- Виды сварных соединений. Описание процесса, преимущества и недостатки
- Основные типы сварных соединений и виды сварных швов
- Сварочные кабельные соединители — Grainger Industrial Supply
- Как подключить электроды для сварки
- SMAW или сварка электродом
- Что такое выводы на сварочном аппарате?
- Шаги по установке проводов для электродуговой сварки
- Три типа сварочных аппаратов: DCEN, DCEP и AC
- DCEP и DCEN: какую полярность следует использовать при сварке?
- Сварка переменным током и сварка постоянным током
- Сварка электродом Поиск и устранение неисправностей сварочных проводов
Виды сварных соединений. Описание процесса, преимущества и недостатки
Терминологию в сфере сварки устанавливают положения ГОСТа 2601-84. Понятию «сварное соединение» в нем дано весьма краткое, но не допускающее двусмысленности определение. Формулировка такая: сварное – это неразъемное соединение, произведенное сваркой. Из всех существующих в настоящее время соединений оно характеризуется самыми высокими показателями надежности и лучшими прочностными качествами. В его основе находится молекулярное сцепление, возникающее между свариваемыми объектами под воздействием высокой температуры. Сами же материалы, из которых они изготовлены, могут быть не только металлами (что встречается чаще всего), но иметь и другую природу, например, полимерную.
Зоны сварного соединения
Сварное соединение состоит из четырех характерных зон.
Зона сварочного шва. Это – область сварного соединения, являющаяся результатом:
-
кристаллизации металлического сплава;
-
сварки давлением, предусматривающей пластическую деформацию;
-
процесса, сочетающего деформацию и кристаллизацию.
Зона наплавленного металла. Здесь находится смесь находящихся в жидком состоянии основного металла и металла используемой для присадки проволоки либо металла электрода.
Зона сплавления. Представляет собой участок с частично сплавившимися зернами, отделяющий шов от основного металла.
Зона термического влияния. Это – область основного металлического сплава, не подвергшаяся плавлению. Но его свойства претерпели изменения под воздействием высокой температуры, при которой проводится сварка либо наплавка.
Плюсы и минусы
Сварные соединения обладают следующими основными преимуществами:
-
возможность проведения работ в автоматическом режиме;
-
невысокий уровень трудоемкости;
-
снижение себестоимости производства сложных деталей мелкими партиями или единичными экземплярами;
-
отсутствие отверстий, ослабляющих конструкцию;
-
соединение получается плотным и абсолютно герметичным.
Из недостатков стоит выделить:
-
качество шва зависит от квалификации исполнителя;
-
неравномерный нагрев деталей в ходе сварки приводит к их короблению;
-
в подвергнутых сварке элементах возникают остаточные напряжения.
Методы выполнения сварных соединений
Сегодня сварку применяют для элементов конструкций, изготовленных из конструкционных сталей всех видов, сплавов высоколегированных, а также из цветных сплавов. Рассмотрим основные способы выполнения этой операции.
Сварка дуговая
Сварка дуговая представляет собой метод соединения металлов посредством сплавления. С этой целью место будущего скрепления нагревается до температуры, достигающей отметки 1500°С. В результате происходит перемешивание расплавленного буферного металла с металлом деталей либо металла только самих деталей.
После охлаждения с последующим застыванием между ними возникает металлургическая связь. Поскольку сформированное таким образом соединение – ни что иное, нежели смесь металлов, ему, как правило, присуща та же прочность, что и металлу скрепляемых объектов. Данный фактор является очевидным преимуществом по сравнению с технологиями, не предусматривающими расплавление кромок деталей (например, пайка). Ведь продублировать механические и физические свойства основных металлов созданные на их основе соединения не могут.
Разновидности
Подразделение дуговой сварки на виды осуществляется по многим критериям. Наиболее часто применяемые – это материал электродов, их количество, а также тип формируемой на основе заготовки и электродов электрической цепи.
-
Сварка электродом неплавящимся. Такой расходник может быть вольфрамовым либо угольным. Соединение образуется за счет плавления только металлов заготовок либо присадочной проволоки.
-
Сварка электродом плавящимся. В данном случае используется метод Славянова. Он предполагает подачу электрода в сварочную ванну в виде жидкого металла.
-
Сварка посредством дуги косвенного действия. Образование электродуги происходит между двумя электродами. Они могут быть как неплавящимися, так и плавящимися. На металл воздействует тепловая энергия электродуги.
-
Сварка дугой трехфазной. Подключение металлической обрабатываемой детали и электродов осуществляется к различным фазам 3-фазной цепи. Электродуга образуется между: основным металлом и каждым из двух электродов;обоими электродами.
Методы электродуговой сварки: плюсы и минусы
Электродуговая сварка выполняется несколькими способами. Каждому из них присущи свои преимущества и недостатки.
Ручная электродуговая сварка
Ручная электродуговая сварка является наиболее популярным методом соединения металлических элементов конструкции.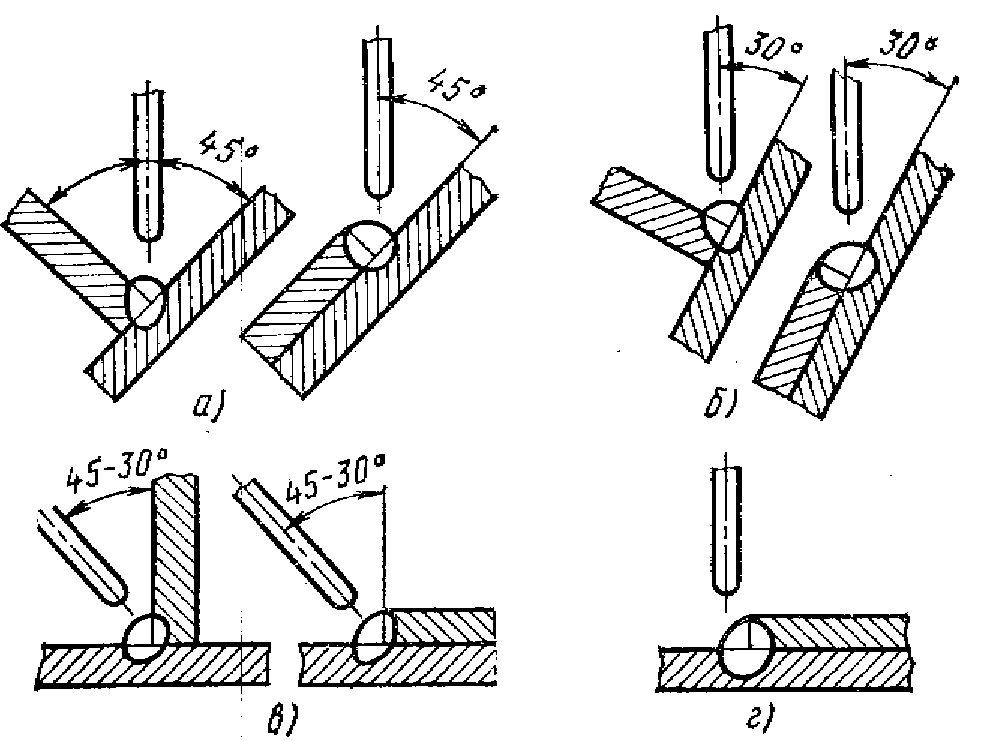
Конструкция плавящегося электрода включает металлический стержень и обмазку. Стержень выполняет две функции:
Функционал обмазки шире. Она:
-
связывает компоненты покрытия стержня;всю массу покрытия с самим стержнем;
-
легирует металл сварного шва, улучшая таким образом его физико-химические характеристики;
-
раскисляет расплавленный металл;
-
защищает сварной шов от внешних негативных воздействий.
Алгоритм ручной электродуговой сварки выглядит так: между металлом заготовки и электродом образуется электродуга. Она обеспечивает размягчение материала, сопровождающееся формированием на его поверхности жидкой ванны. Затем в столб электродуги вводится крайний участок электрода. Там происходит его расплавление. Далее полученный материал смешивается с основным жидким металлом в сформированной ванне.
Сегодня сварка данного вида чаще всего выполняется с использованием сварочных инверторов, имеющих небольшой вес – до 6 кг. Такие устройства представлены на современном рынке в широком разнообразии. Более надежным оборудованием считаются сварочные трансформаторы. Но стоят они намного дороже инверторов, да и весят они заметно больше.
Из преимуществ сварки электродуговой ручной можно выделить:
-
относительно низкая цена сварочного оборудования;
-
возможность работы с различными металлами;
-
сварку можно выполнять в труднодоступных местах;
-
освоение рабочей техники не связано с трудностями.
К минусам данного способа сварки эксперты относят:
-
работа ведется во вредных условиях;
-
низкая производительность;
-
качество работ зависит от квалификации исполнителя;
-
сварка листов толщиной до 1,5 мм сопряжена с определенными сложностями.
Сварка полуавтоматическая
Отличительной особенностью сварки данного вида является то, что электродная проволока, а также защитный газ подаются в рабочую область автоматически. Наиболее часто в качестве защитного газа используются аргон (Аr) и углекислый газ (СО2). Они препятствуют воздействию на зону сварки внешних отрицательных факторов.
Популярность полуавтоматической сварки обусловлена ее универсальностью. Данный метод предоставляет возможность обрабатывать и черные, и цветные металлы. Причем толщина пластины (обозначение Т) в данном случае не особо критична. Данный параметр может принимать значения из диапазона 0,5 мм≤Т≤30,0 мм.
Полуавтоматическая сварка обладает следующими основными преимуществами:
-
работы проводятся с высокой скоростью;
-
соблюдение технологии обеспечивает получение качественного и прочного шва;
-
на качество сварки особо не влияет опыт работника;
-
высокая степень концентрации электродуги обусловливает ограничение зоны термического воздействия и минимизирует деформацию обрабатываемых деталей.
Из недостатков можно выделить только один – невысокая мобильность по причине наличия баллона с защитным газом. Но эта проблема решаема путем использования присадочной проволоки, в состав которой входит флюс.
Сварка электрошлаковая
Этот метод соединения изделий основан на разогреве зоны расплавления теплом, продуцируемым шлаковой ванной, нагреваемой электротоком.
Шлак выполняет функцию защиты области кристаллизации от насыщения элементом водород (Н), а также от окисления. Процедура сварки является бездуговой. Здесь плавление металлов – как основного, так и присадочного – осуществляется под воздействием тепловой энергии, выделяющейся, когда электроток протекает по расплавленному электропроводному шлаку.
Потом электрод погружается в шлаковую ванну, дуга гаснет, и электроток начинает протекать через шлак, находящийся в жидком агрегатном состоянии. Сварка осуществляется снизу-вверх. При этом обрабатываемые изделия распложены обычно вертикально, и между ними имеется зазор. По его обе стороны для образования шва устанавливаются ползуны-кристаллизаторы, изготовленные из меди. Они охлаждаются водой. В процессе формирования сварочного шва ползуны-кристаллизаторы передвигаются по направлению сварки.
Этом способу присущи такие плюсы:
К минусам можно отнести:
-
сварочный процесс в обязательном порядке предваряет изготовление с последующей установкой формообразующих элементов и стартового кармана;
-
при минусовых температурах ударная вязкость металла понижается. Обусловлено это крупнозернистой структурой шва и зоны термического воздействия;
-
недопустима приостановка процесса начатой сварки. Причина – возможно появление дефектов. Если же произошел перерыв определенной продолжительности, соединение намеренно разрушают и приступают к его формированию заново.
Электрошлаковую сварку используют при необходимости создания не только прямолинейных швов, но также кольцевых и имеющих более сложную конфигурацию.
Сварка контактная
Этот метод представляет собой процесс формирования сварочного неразъемного соединения нагревом металла путем пропускания через него электротока с последующей пластической деформацией области скрепления под воздействием внешнего усилия, работающего на сжатие.
Используется сварка контактная в массовом и крупносерийном производстве. Особенно востребована эта технология соединения в автопроме, авиастроении и радиоэлектронной промышленности.
Эксперты выделяют следующие преимущества сварки контактной:
-
отсутствие необходимости обеспечения процесса соединения такими расходными материалами, как присадочная проволока, флюс и инертный защитный газ;
-
продолжительный срок эксплуатации контактных электродов ввиду их медленного износа;
-
большая скорость формирования одного соединения.
На это уходит примерно 0,1 сек;
-
простота выполнения работ. Оперативно освоить навыки проведения контактной сварки может даже неопытный человек.
Но и без недостатков здесь не обошлось. Основные из них такие:
Сварка трением
Этот метод является одной из разновидностей сварки давлением. В данном случае нагрев сопрягаемых деталей производится трением. Причем базовый вариант рассматриваемого способа предполагает перемещение одного из компонентов свариваемой конструкции. Следует отметить нюанс, связанный с окончательным формированием соединения. Выполняется оно на заключительной стадии всего процесса путем приложения к зафиксированным образцам (то есть уже неподвижным) проковочного усилия. В целом, соединение данным методом является результатом совместной необратимой пластической деформации скрепляемых сегментов подлежащих сварке заготовок.
К преимуществам сварки трением можно отнести:
-
отсутствие необходимости в присадочных материалах;
-
на подготовительные работы уходит немного времени.
Не нужно зачищать свариваемые поверхности и удалять с них пленки оксидов;
-
работы проводятся в условиях менее вредных по сравнению с другими способами сварки. Отсутствуют: явление разбрызгивания расплавленного металла; выделения вредных для здоровья человека газов; яркий ослепляющий свет;
-
высокий уровень производительности. Продолжительность цикла сварки составляет всего несколько секунд либо считаные минуты. Точная цифра определяется габаритами заготовок.
Основные недостатки сварки трением такие:
-
процесс не универсален. Свариваются детали из неширокой номенклатуры размерных позиций;
-
громоздкость и дороговизна используемого оборудования;
-
применение сварки данного вида, так сказать, в «полевых условиях» невозможно.
Оборудование не мобильно, а стационарно.
Сварка специальных видов
Сегодня разработаны специальные технологии сварки. Ниже коротко описаны лишь некоторые из них.
Сварка диффузионная
В основу данного метода заложено явление диффузии, происходящее даже не на молекулярном, а на атомарном уровне между поверхностями свариваемых элементов конструкции. Процесс сварки предваряет обработка поверхности деталей по шестому классу шероховатости с финишным обезжириванием ацетоном. После этого свариваемые изделия нагреваются и подвергаются воздействию давления. Все это происходит в защитной среде.
Разогреваются детали до температуры, изменяющейся в диапазоне от 0,5×Тр. до 0,7× Тр. где Тр. – температура плавления сплава, из которого они произведены. Это обеспечивает повышение пластичности металла и значительную скорость процесса диффузии. Уровень давления в камере, где выполняется диффузионная сварка, не превышает отметку 10-2 миллиметров ртутного столба. Другой вариант – в камере при обычном давлении присутствует какой-то инертный газ либо водород.
Сварка лазерная
Здесь источником энергии служит лазер. Принцип действия данной сварки следующий: монохромное излучение направляется в систему фокусировки. Там оно преобразуется в световой поток с меньшим сечением. Попав на подлежащие сварке детали, лазерное излучение:
Процесс его поглощения сопровождается нагревом металла и его расплавлением. В результате формируется сварочный шов.
Сфера применения данного метода – сварка в технологических процессах микроэлектроники как идентичных, так и несходных по структуре материалов, толщина которых может составлять до 10 микрон.
Сварка радиочастотная
Данный метод представляет собой разновидность сварки давлением. Нагрев скрепляемых поверхностей осуществляется с использованием токов высокой частоты. Подвод такого тока к свариваемым деталям может выполняться двумя способами:
-
подключение при помощи проводников к источнику тока.
Это – кондуктивный способ;
-
индуктированием в соединяемых элементах конструкции высокочастотного тока при помощи индуктора, представляющего собой токопроводящий виток. Этот метод подвода энергии получил название индукционный.
Второй способ нашел наибольшее применение для радиочастотной сварки продольных швов трубных изделий. Описывая его и особо не вдаваясь в законы физики, скажем, что плотность тока в приповерхностном слое детали превышает значение данного показателя в ее толще. Таким образом, внешняя часть активно нагревается. Но наиболее сильно проявляется это явление в месте, расположенном именно под индуктором. И ток как-бы следует за ним при его перемещении. В результате нагрева кромки соединяемых элементов конструкции расплавляются. Далее они сжимаются под высоким давлением до формирования сварочного шва.
Сварка ультразвуковая
В качестве источника энергии в данном методе сварки используются ультразвуковые колебания. Сфера применения сварки этого типа – соединение металлических изделий, пластмассовых деталей, стекла с металлом и даже тканевых и кожаных материалов
Частота ультразвука (обозначение ω) – генерируется он непрерывно – изменяется в пределах 18 кГц≤ ω ≤180 кГц. Его мощность принимает значения от 0,01 Вт до 10,0 кВт. Для сварки скрепляемые элементы конструкции подвергаются одновременному воздействию:
Высокочастотные колебания приводят к сухому трению поверхностей. Под его воздействием происходит разрушение присутствующих на них пленок. Затем на смену сухому приходит чистое трение. Оно обеспечивает образование узлов схватывания. Формируются общие зерна, являющиеся общими компонентами обеих соединяемых поверхностей. Кроме того, образуется общая граница, разделяющая приповерхностные зерна. Это – заключительный этап ультразвуковой сварки.
Типы сварных соединений
Основной критерий, по которому сварочные соединения подразделяются на типы –пространственное расположение скрепляемых элементов конструкции.
-
Соединения угловые. В данном случае торцы элементов конструкции располагаются под некоторым углом. Сварка выполняется на всех примыкающих кромках деталей.
-
Соединения тавровые. Такой вариант предусматривает примыкание торца одного элемента в плоскости другого тоже под углом (чаще всего – под прямым).
-
Соединения стыковые. Детали стыкуются одна к другой плоскими торцами. Если у них толщина разная, торцы могут сместиться относительно друг друга по вертикали. То есть одна кромка будет выше другой.
-
Соединения нахлесточные. Подлежащие свариванию элементы конструкции расположены параллельно с частичным/полным перекрытием поверхностей.
-
Соединения торцовые. Здесь сопрягаемые детали совмещаются параллельно, а сварочный шов проделывается по торцам.
Заключение
Несколько слов о дефектах в сварных соединениях. К таковым относятся любые отклонения параметров сопряжений от установленных действующими стандартами, возникновение которых является следствием невыполнения требований к:
-
собственно, процессу сварочных работ;
-
механической, а также термической обработке скреплений, произведенных сваркой;
-
сборке конструкции;
-
сварочным материалам.
Интересную информацию опубликовало общество инженеров-механиков (сокращенное название АSМЕ), президиум которого работает Нью-Йорке. Причины дефектов сварочных соединений распределяются так: 10% — некорректный подбор сварочных материалов; 12% – сварочное оборудование функционировало со сбоями;32% – исполнитель допустил ошибки; 45% – неправильный выбор сварочной технологии. В оставшийся 1% входят прочие причины.
Please enable JavaScript to view the comments powered by Disqus. comments powered by Disqus
Основные типы сварных соединений и виды сварных швов
Соединение металлических деталей сварки давно и прочно вошло в производство, широко применяется в быту и продолжает развиваться в направлениях повышения качества и снижения себестоимости. У этой популярности есть свои плюсы и минусы. Плюс в доступности технологии для широких народных масс. Минус в том, что большое количество непрофессионалов вносит неопределенности в терминологию и описание сварочных процессов. Действующий ныне ГОСТ 5264 – 80 говорит о характеристиках и типах сварных соединений, а также видах сварных швов.
1 / 1
Содержание:
- Назначение кислородного редуктора
- Что представляет собой сварочное соединение
- Типы сварных соединений
- Классификация сварных швов
- Требования к сварным швам
- Что влияет на качество сваривания
Что представляет собой сварочное соединение
Прежде всего, это неразъемное соединение, которое выполняется сваркой. Существует множество способов выполнения таких работ. Их популярность легко объясняется отличным качеством и высокой прочностью. Низкая стоимость и высокая скорость выполнения позволили этой технологии проникнуть во все сферы народного хозяйства. При этом интерес к сварке не снижается и множество ученых и инженеров продолжают работать над усовершенствованием процесса.
Типы сварных соединений
В сварочной технологии рассматривают следующие типы:
-
стыковое – этот тип соединения предполагает сваривание торцевых поверхностей деталей;
-
нахлесточное – в этом случае детали располагают параллельно, с частичным заходом одной на другую;
-
угловое – детали устанавливают под углом и сваривают вдоль линии примыкания;
-
тавровое – торец одной детали приваривают к боковой поверхности другой детали;
-
торцевое – сваривание производится по примыкающим боковым поверхностям.
Наибольшее распространение имеет стыковое. Оно не требуют высокой квалификации сварщика, отличается надежностью и качеством. Выполняются с разделкой кромок или без, в зависимости от толщины металла.
Преимущество нахлесточного соединения состоит в том, что отпадает необходимость подготовки свариваемой поверхности. Этот тип наиболее актуален для листов толщиной 8 – 12 мм. Чаще всего встречается при точечной, контактной и роликовой сварке.
При необходимости сваривания деталей под некоторым углом применяют угловые соединения. Надежный провар соединения возможен только при наличии скосов кромок. Выполнение скосов более трудоёмкая операция, чем сама сварка.
Тавровое соединение требует выполнения скосов и большого количества наплавляемого металла, что увеличивает расход электродов и себестоимость изделия. Его форма повторяет литеру «Т». Без разделки торцов можно выполнять односторонние швы на металле толщиной не более 4 мм.
Классификация сварных швов
Чаще всего встречается следующая классификация сварных швов:
-
по положению в пространстве;
-
по конфигурации;
-
по степени выпуклости;
-
по количеству проходов;
-
по направлению действующего усилия и вектору действия внешних сил;
-
по виду сварки;
-
по протяженности.
От пространственного положения шва зависит технология и сложность его выполнения. По этому признаку выделяют следующие виды сварных швов:
-
нижние,
-
горизонтальные,
-
вертикальные,
-
потолочные.
Нижние – это азбука всех сварщиков. Они наиболее просты в исполнении и не требуют высокой квалификации сварщика. Самый сложный вид – потолочный. Кроме сложности он неудобен и опасен, возможностью попадания на сварщика капель расплавленного металла.
Разделение по конфигурации не требует особых разъяснений и не отличается особыми приемами. По этому признаку их делят на следующие виды:
-
прямолинейные,
-
криволинейные,
-
кольцевые.
Сварные швы получаются вогнутыми, выпуклыми или плоскими. На этом признаке создали еще одно разделение: по степени выпуклости. Этот признак имеет существенное значение потому, что от него зависят физико-механические свойства. Плоские и вогнутые более гибкие и экономные, по сравнению с выпуклыми. А выпуклые более прочные, но при чрезмерной выпуклости склонны к концентрации напряжений.
С количеством проходов и вектором действия внешних сил все понятно, а вот по виду сварки сварные соединения разделяют по методу:
-
дуговой сварки;
-
автоматической и полуавтоматической сварки под флюсом;
-
дуговой сварки в защитных газах;
-
электрошлаковой сварки;
-
электрозаклепочные;
-
контактной электросварки;
-
паяных соединений.
По признаку протяженности различают сплошные и прерывистые швы. У прерывистых есть свои преимущества – сниженное тепловложение и низкая стоимость. Они, в свою очередь, делятся на цепные и шахматные. Встречаются крайне редко в связи с тем, что не имеют должной прочности и непроницаемости. На стороне сплошных главные козыри – качество, прочность и непроницаемость.
Требования к сварным швам
К разным швам предъявляют разные требования, но есть и общие положения, применимые ко всем. Швы должны обладать определенными механическими свойствами и соответствовать их основным показателям:
-
относительное удлинение в пределах 14 – 16%;
-
предел прочности не менее чем у свариваемого металла;
-
показатель твердости не менее чем у свариваемого металла.
Технологические требования сводятся, в основном, к обеспечению полного провара. Иначе трудно гарантировать надежную работу изделия. От внешнего вида шва требуется отсутствие прожогов, наплывов, непроваров и подрезов. Также требуют наличие плавных переходов к основному металлу.
Что влияет на качество сваривания
На этот вопрос можно ответить легко и сложно одновременно. Простым ответом может быть слово «всё». Возьмите любой из множества параметров технологического процесса сваривания, нарушьте его и вы не получите приемлемого качества.
Единственно верным подходом для получения надежной сварки можно считать следующий: технологи готовят полноценное технологическое описание процесса, менеджеры обеспечивают условия, материалы, специалистов, в соответствии с описанием; а сварщики выполняют работу без отклонения от техпроцесса. Только так можно получить изделие, которому можно доверять.
Сварочные кабельные соединители — Grainger Industrial Supply
Сварочные кабельные соединители
19 изделия
Сварочные кабельные соединители предназначены для быстрого соединения удлинителей проводов, ремонта изношенных кабелей или соединений электродов. Соединители стандартизируют типы соединений, позволяя пользователям подключать провода к источникам питания для повышения эффективности.
Соединители сварочных кабелей Tweco
Наборы соединителей сварочных кабелей Tweco
Dinse-Style Welding Cable Connectors
Tweco-Style to Dinse Connector Adapters
Cam-Lok to Dinse Connector Adapters
Tweco-Style Welding Cable Connectors
Loading.![]() |
0003
Loading… |
Dinse-Style Welding Cable Connectors
Загрузка.![]() |