ПАРОВАЯ ТУРБИНА • Большая российская энциклопедия
ПАРОВА́Я ТУРБИ́НА, турбина, в которой в качестве рабочего тела используется водяной пар; служит для преобразования тепловой энергии пара в механич. работу. В отличие от паровой машины, в П. т. используют не потенциальную, а кинетич. энергию пара. Осн. назначение П. т. – привод (первичный двигатель) для генераторов электрич. тока на тепловых и атомных электростанциях. П. т. и электрогенератор составляют турбоагрегат.
Конструкция паровых турбин
Схематический продольный разрез активной паровой турбины с тремя ступенями давления: 1 – кольцевая камера свежего пара; 2 – сопла первой ступени; 3 – лопатки первой ступени; 4 – сопла второй ступени; …
П. т. состоит из двух осн. частей – ротора с лопатками (подвижная часть турбины) и статора с соплами (неподвижная часть). Поток пара, образующийся в паровом котле, под высоким давлением поступает через направляющие (статор с соплами) на криволинейные лопатки турбины, закреплённые по окружности ротора, и, воздействуя на них, приводит ротор, закреплённый на одном валу с электрогенератором, во вращение (происходит преобразование тепловой энергии пара в механич. работу). Каждый ряд направляющих и лопаток называется ступенью турбины (как правило, П. т. имеет неск. ступеней). Корпус П. т. с несколькими ступенями давления разделяют диафрагмами на отд. камеры, в каждой из которых помещён один из дисков с лопатками (рис.). Пар может проникать из одной камеры в другую только через сопла, расположенные по окружности диафрагм. Давление пара снижается после каждой ступени, а скорости истечения пара остаются примерно одинаковыми, что достигается выбором соответствующих размеров сопел.
Роторы П. т., предназначенные для привода электрич. генераторов, работающих на электрич. сеть, имеют фиксированную частоту вращения – 3000 об/мин в России и 3600 об/мин в США и др. странах. Роторы П. т., предназначенных для др. потребителей мощности, могут иметь др. частоту вращения, соответствующую характеристикам оборудования потребителя (напр. , транспортные турбины). Давление и темп-ра пара перед турбиной определяются её назначением.
Мощные П. т. имеют сложную конструкцию и большие размеры (см. рис. к ст. Конденсационная турбина). Длина всего агрегата может достигать 30 м. П. т. располагается на фундаменте, представляющем собой многоопорную жел.-бетон. конструкцию, опирающуюся на общую фундаментную плиту. Конструкция П. т. разделяется на неск. цилиндров (частей) – высокого давления (ЦВД), среднего давления (ЦСД) и низкого давления (ЦНД). Обычно мощная П. т. имеет один ЦВД, один или два ЦСД и неск. ЦНД. Пар поступает в турбину, проходит через ЦВД последовательно все ступени, далее через ЦСД (одним или двумя параллельными потоками), затем, разветвляясь ещё на неск. параллельных потоков, проходит ЦНД и сбрасывается в конденсатор. Разветвление потоков перед конденсатором необходимо для увеличения единичной мощности турбины, т. к. однопоточная турбина может вырабатывать ограниченную мощность, которая зависит от длины рабочих лопаток последней ступени. Для обеспечения надёжной эксплуатации П. т. оснащается системой безопасности, предотвращающей возникновение и развитие аварийных ситуаций. Осн. преимущества П. т.: высокая единичная мощность, широкий диапазон мощностей, высокий ресурс работы. Недостатки П. т.: высокая инерционность (долгое время пуска и останова), дороговизна строительства и ремонта. В П. т., используемых на ТЭС, давление пара может достигать 24 МПа и более, темп-ра – 545–600 °C; мощности П. т., работающих на ТЭС, – до 1200 МВт, АЭС – до 1900 МВт. Кпд современных П. т. достигает 40–42%.
Классификация паровых турбин
По принципу действия выделяют активные турбины и реактивные турбины. По количеству ступеней П. т. подразделяют на одноступенчатые и многоступенчатые турбины. В одноступенчатой П. т. не удаётся достаточно полно использовать энергию пара, поэтому совр. П. т. строят многоступенчатыми. По направлению потока рабочего тела выделяют осевые (аксиальные) П. т. (направление потока совпадает с направлением оси ротора, наиболее распространённый тип П. т., используемых для привода электрогенераторов) и радиальные П. т. (поток осуществляется в радиальном направлении либо от оси ротора к периферии дисков, либо наоборот – от периферии к оси). В зависимости от давления пара П. т. бывают: низкого (не выше 0,9 МПа), среднего (не выше 4 МПа), высокого (9–14 МПа) и сверхкритич. давления (24 МПа и более).
В зависимости от характера теплового процесса П. т. подразделяют на 3 группы: конденсационные турбины, теплофикационные и спец. назначения.
Теплофикационные П. т. служат для одноврем. получения электрич. и тепловой энергии. Осн. конечный продукт таких П. т. – теплота. ТЭС, на которых установлены теплофикационные П. т., называются теплоэлектроцентралями. К теплофикационным П. т. относятся турбины с противодавлением, с регулируемым отбором пара, а также с отбором и противодавлением. У турбин с противодавлением отсутствует конденсатор. Отработавший пар, имеющий давление выше атмосферного, поступает в спец. сборный коллектор, откуда направляется к тепловым потребителям для технологич. целей (варка, сушка, отопление и др.). В турбинах с регулируемым отбором часть пара отводится из первой или второй промежуточных ступеней, а остальной пар идёт в конденсатор. Давление отбираемого пара на всех режимах работы турбоагрегата автоматически поддерживается постоянным или же регулируется в заданных пределах, с тем чтобы потребитель получал пар определённого качества.
Существует два вида тепловых потребителей: промышленные, где требуется пар с давлением до 1,3–1,5 МПа (производств. отбор), и отопительные, с давлением 0,05–0,25 МПа (теплофикационный отбор). Если требуется пар как производственного, так и отопит. назначения, то в одной турбине могут быть осуществлены два регулируемых отбора; место отбора (ступень турбины) выбирают в зависимости от нужных параметров пара. У турбин с отбором и противодавлением часть пара отводится из первой или второй промежуточных ступеней, а весь отработавший пар направляется из выпускного патрубка в отопит. систему или к сетевым подогревателям.
П. т. специального назначения обычно работают на отбросном тепле металлургич., машиностроит. и химич. предприятий. К ним относятся П. т. «мятого пара», с промежуточным подводом пара (турбины двух давлений) и предвключённые. П. т. «мятого пара» используют отработавший пар низкого давления после технологич. процессов (пар поршневых машин, паровых молотов и прессов), который по к.-л. причинам не может быть использован для отопит. или технологич. нужд. Давление такого пара обычно несколько выше атмосферного, и он направляется в спец. конденсац. турбину (турбину «мятого пара»). П. т. двух давлений работают как на свежем, так и на отработавшем паре паровых механизмов, подводимом в одну из промежуточных ступеней. Предвключённые П. т. представляют собой турбины с высоким начальным давлением и высоким противодавлением; весь отработавший пар этих П. т. направляют далее в обычные конденсационные турбины.
Историческая справка
Первое устройство, приводимое в движение паром (эолипил), было описано Героном Александрийским. В России П. Д. Кузьминский в нач. 1890-х гг. построил и опробовал судовую П. т. собств. конструкции.
П. т. получила практич. применение лишь в кон. 19 в., когда такие отрасли, как термодинамика, машиностроение и металлургия, достигли необходимого уровня. К. Г. П. де Лаваль (1878) и Ч. А. Парсонс (1884) создали первые промышленно пригодные паровые турбины. В П. т. Парсонса использован принцип поступенчатого расширения пара, который лежит в основе конструкции совр. паровых турбин.
В Европе П. т. получили всеобщее признание в качестве привода электрогенераторов только с 1899, когда на электростанции г. Эльберфельд (Германия) впервые были применены две П. т. Парсонса мощностью по 1000 кВт каждая.
В дореволюц. России строились как стационарные, так и судовые П. т. Особенно большие успехи были достигнуты рос. конструкторами и технологами в 1910–14 в проектировании и изготовлении П. т. для крупных воен. кораблей. Впервые отеч. стационарные П. т. построили на металлич. заводе в С.-Петербурге (позднее Ленингр. металлич. завод, ЛМЗ), на котором в 1907 изготовили П. т. для привода электрогенератора мощностью 200 кВт. В 1937 на ЛМЗ выпущена первая конденсационная двухцилиндровая одновальная турбина мощностью 100 МВт; в 1977 построена и сдана в эксплуатацию самая крупная отеч. конденсационная турбина мощностью 1200 МВт. Начиная с 1964 в СССР освоен выпуск П. т. для АЭС.
Устройство паровой турбины
Вращающейся частью турбины является ротор; по аналогии с электрическими машинами неподвижную часть ее называют иногда статором.
Рассмотрим отдельно устройство и назначение каждой из перечисленных выше частей и механизмов турбины.
фундаментная плита является опорой для корпуса турбины и статора генератора и создает между ними связь при которой правильное взаимное положение их не должно нарушаться.
Ввиду отсутствия в турбогенераторе возвратно-поступательно движущихся частей и связанной с ними неравномерности работы фундаментная плита может быть сравнительно легкой конструкции и обычно выполняется в виде сварной стальной или пустотелой чугунной рамы.
фундаментная плита турбогенератора небольшой мощности представляет собой цельную отливку; при средних и больших мощностях плита выполняется составной из двух и более (до пяти) частей.
Для облегчения веса агрегата иногда устанавливают общую плиту только под генератор и выпускной конец турбины; передний подшипник ее в этом случае покоиться на особой плите, связанной тягами с основной.
Внутреннее пространство пустотелой плиты иногда используется как резервуар для масла.
На (рис.1) изображена турбинная часть составной плиты; места установки лап корпуса обозначены цифрами 1, стойки переднего подшипника — 2; соединение со второй половиной плиты производится по фланцу 3-3
.
При монтаже турбины фундаментная плита устанавливается на стальные клинья, положенные на заранее приготовленный фундамент (рис. 2). Перемещением клиньев добиваются горизонтальности положения плиты, для проверки чего к обработанным плоскостям последней прикладывают точный уровень (ватерпас). Составная из нескольких частей плита должна быть собрана и крепко стянута болтами еще до установки на клинья. После того как положение плиты точно выверено, фундаментные болты слегка затягивают и устанавливают на плиту стойки подшипников, корпус и ротор турбины. После окончательной выверки плиты, нагруженной этими деталями, ее положение фиксируют подливкой цементного раствора, вытекание которого предупреждается деревянным ограждением(опалубкой).
Перед заливкой нужно заменить клинья толстыми плоскими стальными подкладками, так как клинья имеют тенденцию разъезжаться при вибрации машины.
После затвердения щемента (обычно 5-6 дней) фундаментные болты могут быть затянуты окончательно.
Вместо клиньев для первоначальной выверки турбины иногда пользуются домкратами (джек-болтами).
Корпус турбины
Корпуса турбин почти всех конструкций выполняют разъемным в вертикальной плоскости. Сторона низкого давления крепится к фундаментной плите так, что определенная точка корпуса оказывается неподвижной (мертвой) при тепловых деформациях корпуса; сторона высокого давления обычно подвешена к переднему подшипнику и при удлинении корпуса от нагревания имеет возможность смещаться в осевом направлении по направляющим. Мертвую точку иногда называют фикс-пунктом.
Крепление корпуса к фундаментной плите должно быть выполнено так, чтобы расширение при нагревании происходило свободно, но при этом не нарушалось совпадение геометрических осей турбины и генератора.
Один из методов такого крепления приведен на (рис.3). Корпус опирается на фундаментную плиту стойкой 1 переднего подшипника и боковыми лапами 2, отлитыми вместе с выхлопным патрубком. При удлинении корпуса стойка переднего подшипника может скользить в осевом направлении по плите, причем продольная шпонка
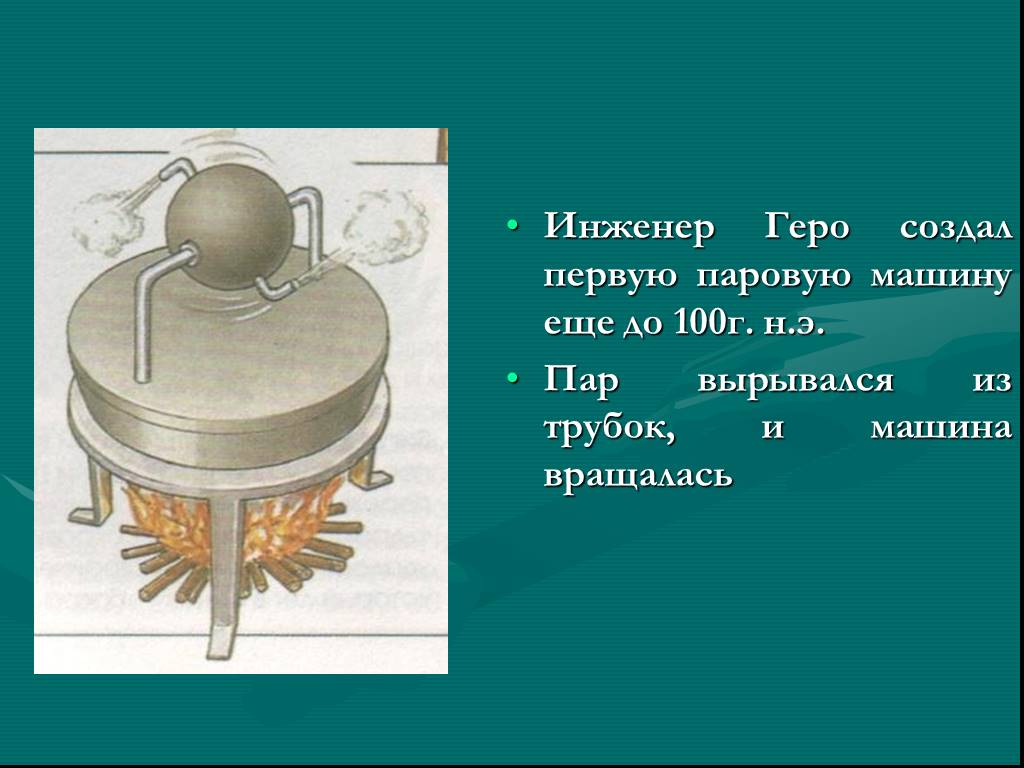
Передней стороной или стороной высокого давления турбины — называют сторону впуска пара
Для того чтобы лапа 2 (рис.4) корпуса могла скользить по плите 4 вдоль шпонок, под головкой болта 3, крепящего лапу, оставляют небольшой зазор; отверстие для болта в лапе делают больше диаметра болта на величину максимального перемещения лапы. Возможность свободного перемещения лапы можно в любой момент проверить по шайбе
1, которая должна свободно вращаться под головкой болта.
Скользящие опорные поверхности и шпонки во избежание заеданий должны быть перед сборкой тщательно очищены и натерты графитом или смазаны ртутной мазью.
Изображенный на (рис 3) корпус имеет разъем в горизонтальной плоскости и разъем 7 в вертикальной плоскости. Фланцы корпуса в плоскостях разъема стягиваются болтами или шпильками. Затягивание гаек у болтов и шпилек небольшого размера производится ключом, удлиненным трубой до 2 метров длины. У турбин высокого давления затяжка болтов должна быть очень сильной во избежание просачивания пара. Поэтому болты, стягивающие фланцы таких турбин выполняют из хромоникелемолибденовой стали, хорошо переносящей действие высоких температур, располагают их очень близко друг к другу
В настоящее время для прогрева применяют три способа:
1) Автогенной горелкой с длинным не режущим пламенем, которое вводится в отверстие, просверленное в болте (рис .5) .
Гайка болта должна быть предварительно затянута до отказа в холодном состоянии. После прогрева болт удлиняется и гайка может быть повернута еще на 1/10-1/6 оборота в зивисимости от длины болта.
2) Электрическим нагревательным аппаратом (индукционным или с угольным электродом), вставленным в отверстие болта.
3) Паром или горячим воздухом, струя которого направляется в сверление болта.
Между температурами корпуса турбины и болтов или шпилек, стягивающих его фланцы, всегда имеется разность, вызывающая дополнительные напряжения в материале болта или шпильки, особенно большие при пуске турбины. Температура шпилек, имеющих хороший контакт с корпусом по резьбе, всегда ближе к температуре корпуса, чем температуре болтов. С целью снижения разности температур корпуса и стяжных болтов заводы с успехом применяют засыпку алюминиевой пудры в зазоры между болтами. Этим путем удавалось снизить разность температур со 100 до 200 С.
Перед сборкой турбины фланцы горизонтального разъема корпуса тщательно очищают, подшабривают и покрывают мастикой, состоящей из графита на вареном льняном масле; иногда в состав мастики вводят сурик, белила и другие составляющие.
Корпус у турбины стараются придать по возможности простую форму. Размеры корпуса определяются размерами проточной части турбины. Часто корпус в начале имеет большой диаметр, соответствующий диаметру регулирующей ступени, затем, ограничивая камеру регулирующей ступени, он резко уменьшается и далее плавно увеличивается в соответствии с ростом диаметра ступеней турбины по мере расширения пара. Иногда диаметр корпуса, следуя за диаметрами проточной части, изменяется несколькими резко выраженными ступенями.
Во внутреннюю часть корпуса реактивной турбины, в пазы, выполненные обычно прямо в корпусе, устанавливают кольцевые ряды направляющих лопаток, образующие сопла.
В активных турбинах в корпус закладываются диафрагмы, разделяющие его на отдельные камеры, и направляющие аппараты в тех камерах, где есть ступени скорости.
Не редко диафрагмы устанавливаются не в корпус, а в групповые кольцеобразные обоймы, которые затем вставляются в корпус.
Такая конструкция разгружает корпус от напряжений, возникающих при неравномерном расширении диафрагм от нагревания, и упрощает производство при выпуске машин разных мощностей, позволяя пользоваться корпусами одного размера.
Материалом для отливки корпусов паровых турбин служат чугун и сталь. Применение чугуна ограничено областью невысоких температур вследствие склонности чугуна «расти», то есть увеличиваться в объеме при высоких и переменных температурах. «Рост» чугуна неоднократно приводил к авариям вследствие нарушения установленных зазоров между деталями турбины.
С переходами на работу паром очень высокого давления и температуры турбостроение столкнулось с явлением «ползучести» (крипа) стали.
Под одновременным действием высокой температуры и постоянных растягивающих напряжений стальная отливка или паковка с течением времени получает все большую остаточную (пластическую) деформацию – ползет. Пластическая деформация при явлении ползучести возникает при напряжениях, значительно меньших придела текучести.
Для обычных углеродистых сталей ползучесть наблюдается начиная с температуры 380-400
Так как скорость ползучести для данного материала определяется температурой и напряжениями, то задачей конструктора является назначение таких размеров детали, при которых напряжения в ней будут таковы, что деталь может проработать заданный срок службы не выходя за установленные пределы деформации.
Задаваясь сроком службы детали, например 100 000 ч. И максимальной допустимой деформацией, например 0,5% длины детали, конструктор находит по результатам испытания металла на ползучесть то напряжение, при котором скорость ползучести не превышает 5*10-8мм/мм*ч.
Сопротивляемость стали ползучести зависит от химического состава металла и от технологии его обработки. Из присадок, вводимых в сталь, наиболее эффективно повышает сопротивление ползучести молибден
, содержание которого в количестве 0,4-0,6% дает возможность применять сталь для температур до 550о С при приемлемых значениях рабочих напряжений.Другое явление, с которым приходится встречаться в турбинах высокого давления, это релаксация деталей то есть самопроизвольное падение первоначально созданных напряжений в деталях (например, при затяжке болтов), которое заметно проявляется при длительном воздействии высоких температур. Процесс релаксации протекает при неизменной общей деформации напряженной детали. В результате деформации снижается натяг болтов, стягивающих фланцы корпусов турбин или фланцевые соединения паропроводов, и болты приходится периодически подтягивать.
В турбине, рассчитанной на высокие параметры пара, в наиболее тяжелых условиях находится корпус высокого давления.
Наибольшая трудность заключается в достижении длительной плотности стыка между половинами корпуса и в устройстве рациональной связи корпуса со стойками подшипников.
С возрастание параметров свежего пара быстро увеличивается толщина фланцев, необходимая для обеспечения плотности в разъеме корпуса высокого давления.
Для того чтобы обеспечить правильное взаимное положение подшипников и корпуса при удлинении последнего, точки опоры корпуса расположены на высоте его продольного разъема и насколько возможно близко к середине подшипников. Корпус с обоих концов опирается лапами на стойки подшипников и может скользить в вертикальных и горизонтальных направляющих стоек, что обеспечивает свободное расширение его в радиальных направлениях от центра вала без нарушения правильности совпадения осей турбины и генератора.
При проектировании турбин, рассчитанных на сверхвысокие параметры пара, толщина фланцев корпуса в.д. и диаметры стяжных болтов и шпилек могут получиться неприемлемо большими. В таких случаях хорошим конструктивным решением является применение корпусов с двойными стенками. В этом случае между внутренним корпусом, заключающем в себе проточную часть в. д., и наружным корпусом, обеспечивающим отсутствие утечек пара наружу, находится пар, отработавший в проточной части в. д. и имеющий значительно пониженный по сравнению со свежим паром давление.
Диафрагмы
Диафрагмы отливают из чугуна или отковывают из стали (для давлений выше 20 ата и температуре выше 250о С). Как правило, диафрагмы делают разъемными на две части; каждая половина устанавливается в соответствующую выточку корпуса турбины или в обойму.
Диафрагмы закрепляют в корпусе таким образом, чтобы они могли при нагревании свободно расширяться в радиальном направлении, не оказывая давления на стенки корпуса. Для этого их вставляют в выточки стенок корпуса с небольшими зазорами, обычно составляющими от 0,003 до 0,004 от диаметра диафрагмы в радиальном направлении и от 0,1 до 0,3 мм в осевом направлении.
Обода диафрагм перед установкой их в корпус необходимо смазать графитом.
Положение половинок диафрагмы фиксируется установкой шпонок 1 (рис. 9). Верхние половинки закрепляют так, чтобы можно было поднять верхнюю часть корпуса вместе с ними; это достигается установкой с каждой стороны шпонок 3, удерживающих диафрагмы от выпадения. Нижние половины диафрагм при удаленном роторе обычно свободно вынимаются из корпуса 2 кверху.
На (рис. 10) изображен вид снизу верхней части (крышки) корпуса небольшой турбины; цифрой 2 отмечены диафрагмы, 1 – секция направляющего аппарата, 3 – закрепляющие винты диафрагм, 4 – уплотнение диафрагм, 5 – шпоночные канавки для шпонок, соединяющие верхнюю и нижнюю половины диафрагм.
Впуск пара в первых ступенях часто бывает парциальным, соответственно этому диафрагмы имеют сопла только в части своей окружности.
В последних ступенях подвод пара всегда полный – по всей окружности, на (рис. 11) изображены диафрагмы с парциальным и полным впуском пара.
Во избежание утечек пара вдоль вала в тех местах, где он проходит сквозь диафрагмы, последние снабжают лабиринтовыми уплотнениями, принцип действия и устройство которых рассмотрен ниже.
Вследствие большой поверхности диафрагмы полное давление пара на нее достигает очень большой величины даже при небольшой разности давлений между соседними камерами: естественно, что конструкция диафрагмы, особенно в первых ступенях, где температура и разность давлений сравнительно высоки, должна быть очень солидной, тем более, что даже небольшой прогиб диафрагмы может повлечь за собой серьезную аварию турбины.
Расчет диафрагм на прочность может быть произведен только с приближенной точностью. Поэтому новые конструкции диафрагм обычно испытывают на прогиб гидравлическим прессом на турбинных заводах.
Сопла первой ступени, чаще всего изготавливаются в виде составных фрезерованных сегментов (рис. 13) или сегментов, состоящих из лопаток, приваренных между отрезками бандажа и обоймы.
Сопла в чугунных диафрагмах образуются посредством заливки в тело диафрагмы соответственно изогнутых стальных лопаток (рис. 11). Сопла получают при этом трапецеидальное сечение и могут быть устроены расширяющимися или суживающимися в зависимости от расчетной скорости истечения пара.
Неточная пригонка стыка лопаток в разъеме диафрагмы может вызвать вибрацию рабочих лопаток, так как в таком случае правильная форма соплового канала нарушается и каждая рабочая лопатка, проходя мим стыка, получает толчок. Ввиду большой трудности получения правильных стыков в диафрагмах с залитыми лопатками применяют диафрагмы с косыми стыками, так что разрезанные лопатки в разъемах отсутствуют.
В современных конструкциях турбин высокого давления чаще всего применяются сварные диафрагмы (рис. 16).
Направляющие лопатки 1, образующие сопла, закрепляются в двух полукольцевых бандажах – внутреннем 2 и наружном 3, в отверстия которых входят шипы лопаток, после чего привариваются к бандажам. Затем собранное полукольцо сопел приваривается к наружному ободу 4 и телу диафрагмы 5.
Сварные диафрагмы по своей жесткости превосходят диафрагмы с приклепанными лопатками, но уступают им в точности изготовления, что может вызвать небольшое увеличение расхода пара турбиной.
Сопловые венцы, набранные из фрезерованных лопаток, позволяют получить наиболее точные профили и гладкие поверхности сопловых каналов, что обеспечивает высокую экономичность турбины, но обходится дороже в изготовлении.
Далее ► ► ► Наверх Главная страница
Основы проектирования и анализа паровых турбин
Перейти к основному содержанию
Вы здесь
- Главная
- Публикации
- КЭП
- Август 2018
- Основы проектирования и анализа паровых турбин
Назад к основам
Август
Джимми Д. Кумана
Эффективное проектирование, анализ и интеграция паровых турбин могут помочь оптимизировать надежность подачи пара и общую энергоэффективность предприятия.
Паровые турбины являются важными компонентами инженерных систем технологических установок. Они предлагают возможности для оптимизации надежности подачи пара, а также энергоэффективности в масштабах всей площадки. Наиболее распространены паровые турбины в нефтеперерабатывающей, аммиачно-карбамидной, метанольной, этиленовой и целлюлозно-бумажной промышленности, где их мощность обычно составляет 10–60 МВт. Хорошие экономические показатели также возможны при меньших размерах до 2 МВт, которые более распространены в пищевой промышленности и производстве напитков, а также на малых и средних предприятиях химической промышленности (CPI).
Достижение благоприятной экономической эффективности паровой турбины зависит от выбора правильного типа турбины ( например, противодавление по сравнению с конденсационной) нужного размера, а также от правильной интеграции ее с сетью теплообменников (HEN) в соответствии с соответствующим размещением Принцип пинч-анализа.
В этой статье рассматриваются термодинамические соотношения и уравнения, связывающие условия расхода пара и выходную мощность, которые полезны для предварительной оценки экономических показателей новых турбин и анализа производительности существующих агрегатов.
Основы
Любое устройство, которое преобразует химическую энергию, содержащуюся в топливе, в механическую энергию ( т. е. работа вала) посредством сгорания, называется тепловым двигателем. Тепловые двигатели обычно классифицируют в соответствии с термодинамическим циклом, которому они следуют. Наиболее распространенными тепловыми двигателями в промышленности являются паровые турбины (цикл Ренкина), газовые турбины (цикл Брайтона) и двигатели внутреннего сгорания (цикл Отто).
Хотя газовые турбины также могут играть важную роль в экономической оптимизации комбинированных теплоэлектроцентралей (ТЭЦ) на производственных предприятиях, эта статья посвящена исключительно паровым турбинам. Паровые турбины имеют четыре типичных режима работы:
▲ Рисунок 1. Паровые турбины бывают разных конфигураций, включая (а) турбины с противодавлением (BPST), работающие в режиме когенерации, и (b) конденсационные турбины (CST) для производства электроэнергии. Гибридные конфигурации, такие как (в) экстракционные турбины и (г) асинхронные турбины, менее распространены.
Паровые турбины с противодавлением (BPST) производят отработавший пар низкого давления (НД), который можно использовать для одного или нескольких процессов нагрева (рис. 1a). Цели состоят в том, чтобы обеспечить процесс паром в количестве и под давлением, требуемом для процесса, при этом вырабатывая максимальное количество энергии, чтобы уменьшить потребность в покупной энергии. Поскольку BPST совместно генерируют два энергетических продукта ( , т. е. пар и мощность) одновременно, они имеют эффективную тепловую мощность 4 500–5 500 БТЕ/кВтч, что представляет собой энергоэффективность в два-три раза лучше, чем у конденсационной турбины, даже с учетом как котла, так и турбины. потери энергии. (Теплопроизводительность — это количество топлива, которое тепловой двигатель преобразует в полезную мощность — чем меньше число, тем лучше. Минимально возможная теплотворная способность составляет 3413 БТЕ/кВтч, что соответствует 100-процентному преобразованию энергии топлива в мощность.)
Чистые BPST используются в основном на промышленных объектах, которые работают непрерывно, где целью является высокая термодинамическая эффективность и относительно стабильные потребности в энергии. Обычно они рассчитаны на мощность от 3 до 60 МВт.
Конденсационные паровые турбины (CST) выбрасывают пар в конденсатор при атмосферном давлении или минимально возможном давлении, при котором он может быть сконденсирован с помощью имеющейся системы охлаждения (рис. 1b). В местах с готовым водоснабжением охлаждение обычно осуществляется через замкнутый контур, который циркулирует через испарительную градирню. В засушливых регионах, таких как Ближний Восток, Северная Африка и юго-запад США, теплообменники с воздушным охлаждением обычно более практичны, чем мокрые градирни.
Коммунальные электростанции используют CST исключительно потому, что их цель состоит в том, чтобы максимизировать выработку электроэнергии, а отработанное тепло от BPST не используется в цикле выработки электроэнергии Ренкина. CST электростанций обычно имеют мощность более 100 МВт и теплопроизводительность 11 000–16 000 БТЕ/кВтч, в зависимости от таких факторов, как давление и температура пара на входе, температура охлаждающей среды и изоэнтропическая эффективность турбины.
Экстракционно-конденсационные турбины (ЭКТ) представляют собой гибриды, в которых часть выхлопного пара извлекается при достаточно высоком давлении для технологического нагрева (режим когенерации), а остальная часть конденсируется с помощью охлаждающей установки для выработки электроэнергии (режим без когенерации) (рис. 1с). ECT менее распространены в промышленности, потому что их дороже покупать и обслуживать, и их сложнее контролировать.
Индукционные турбины представляют собой гибриды, обеспечивающие очень высокую эффективность системы, поскольку они извлекают энергию из пара, который в противном случае должен был бы снижаться под давлением через дроссельный клапан (рис. 1d). Как правило, они получают два источника пара на входе с разным давлением ( например, высокое давление и среднее давление) и выхлоп при одном более низком давлении ( например, давление окружающей среды или вакуум).
На рис. 1d показан простой случай, когда подошла бы асинхронная турбина. Процесс является экзотермическим и генерирует больше пара низкого давления, чем необходимо для технологического нагрева, но для других высокотемпературных режимов требуется пар высокого давления (ВД). Только с двумя уровнями давления пара требуемое количество пара высокого давления направляется прямо в процессы, которые в нем нуждаются, в то время как избыточный выхлоп из турбины конденсируется охлаждающей установкой для дополнительной выработки электроэнергии (режим без когенерации). Индукционные турбины еще менее распространены, чем экстракционные, потому что их дороже покупать и обслуживать, а также сложнее контролировать.
Проектные и расчетные расчеты
Процесс расширения, происходящий в правильно изолированной паровой турбине, по существу является адиабатическим процессом. Разница энтальпий между входным и выходным паром (без учета потерь на трение) почти полностью преобразуется в механическую энергию, которую затем можно использовать для привода насоса, компрессора или электрогенератора.
▲ Рис. 2. Адиабатическое расширение пара в турбине удобнее всего представить на энтальпийно-энтропийной (H-S) диаграмме Молье. Точка 1 = вход в турбину, точка 2 = выхлоп низкого давления для технологического нагрева (режим когенерации), точка 3 = выхлоп в конденсатор общего назначения (режим выработки электроэнергии).
Этот процесс можно проследить на энтальпийно-энтропийной (H-S) диаграмме, известной как диаграмма Молье. На приведенной в качестве примера диаграмме (рис. 2) путь от точки 1 к точке 2 представляет типичную операцию BPST на химическом, целлюлозно-бумажном, нефтеперерабатывающем или пищевом предприятии; перегретый пар с давлением 600 фунтов на кв. дюйм при температуре 700°F (точка 1) расширяется при прохождении через турбину и выходит при давлении 50 фунтов на кв. дюйм (точка 2). Путь от точки 1 до точки 3 представляет собой работу CST с целью максимального производства электроэнергии, чтобы свести к минимуму потребность в импортируемой мощности при нормальной работе или компенсировать временную потерю импортируемой мощности из сети. Пар высокого давления выпускается в условиях вакуума и конденсируется на охлаждающем устройстве.
Паровые турбины обычно вращаются со скоростью 3 000–15 000 об/мин. На такой скорости могут образовываться капли воды, которые разбалансируют лопасти турбины, вызывая серьезные механические повреждения. BPST обычно могут безопасно работать при влажности до 3% (, т. е. , минимальное качество пара 97%). CST, специально разработанные для электростанций коммунального масштаба, могут выдерживать влажность до 10–12%. Технологические установки должны избегать нормальной работы в этих ограничивающих условиях и должны стремиться к тому, чтобы температура точки росы отработанного пара была как минимум на 20°F выше.
Эти эксплуатационные ограничения необходимы для эффективного анализа выходной мощности турбины, будь то расчет конструкции или расчет мощности. Чтобы определить выходную адиабатическую мощность примера BPST (точки 1-2, рис. 2), мы сначала определяем изменение общей энтальпии для изоэнтропического расширения до давления выхлопа 50 фунтов на квадратный дюйм (от точек 1 до точек 2*). Затем мы применяем изэнтропический КПД (η T ), который является комбинированным показателем оригинальной конструкции машины и ее настоящего механического состояния:
, где H 1 — энтальпия входящего пара высокого давления (БТЕ/фунт), H 2 — фактическая энтальпия выхлопного пара НД (БТЕ/фунт), а H 3 * — энтальпия выхлопного пара НД при изоэнтропическом расширении (БТЕ/фунт).
Затем адиабатическая выходная мощность может быть рассчитана по формуле:
, где Вт — рабочая мощность (кВт), M — массовый расход пара (фунт/час), а 3,412 — приблизительный коэффициент преобразования БТЕ в кВтч.
Изэнтропический КПД не может быть точно определен, но его можно довольно точно оценить с помощью эмпирических корреляций, основанных на историческом опыте работы в отрасли, которые обычно можно получить у поставщиков паровых турбин. При закупке паровой турбины рекомендуется требовать от всех участников торгов предоставления значений η T для каждой машины в диапазоне ожидаемых условий нагрузки. Мониторинг потери эффективности существующей турбины может обеспечить заблаговременное предупреждение о надвигающихся проблемах с турбиной.
Ссылка 1 содержит некоторые данные о реальной работе турбины, но набор данных слишком мал, чтобы делать общие выводы. Наиболее надежные и полезные корреляции для новых турбин можно найти в [1]. 2. η T для паровой турбины можно определить итеративно, используя:
, где a и b являются функциями W (таблица 1). Определение значений a и b из табл. 1 требует итеративного расчета разницы между температурой насыщения на входе ( T sat,i ) и выход ( T sat,o ) в градусах Цельсия (Δ T ).
Таблица 1. Эмпирические… |
Разрешения на авторское право
Хотите повторно использовать материалы из журнала CEP? Легко запросить разрешение на повторное использование контента. Просто нажмите здесь, чтобы мгновенно подключиться к службам лицензирования, где вы можете выбрать из списка варианты повторного использования желаемого контента и завершить транзакцию.
Паровая турбина— Factorio Wiki
Паровая турбина потребляет пар для выработки электроэнергии. Обычно используется вместе с теплообменниками и ядерным реактором.
Несмотря на то, что турбины рассчитаны на пар ядерного реактора с температурой 500°C, их все же можно подключать к котлам для использования в традиционной паровой энергетике с температурой 165°C. На этом режиме паровая турбина действует как две отдельные паровые машины мощностью 1800 кВт и потреблением 60 пар/сек. Однако фактическое производство электроэнергии основано на температуре пара, а не на самом здании. Это означает, что использование паровой турбины не более экономично, чем использование двух паровых двигателей. Если не экономить место в большой сборке, нет необходимости использовать более дорогие турбины для котлового пара.
Выходная мощность
Каждая паровая турбина потребляет максимум 60 единиц пара с температурой 500°C в секунду и производит 5,82 МВт электроэнергии; 5,8 МВт, указанные во всплывающей подсказке, округлены.
- Теплообменник нагревает воду с температурой 15°C до пара с температурой 500°C;
- Требуется 0,2 кДж энергии горелки, чтобы поднять 1 воду на 1°C;
- Пар потребляется паровыми турбинами со скоростью 60 единиц в секунду;
- (500°C — 15°C) × 0,2 кДж × 60 единиц = 5820 кВт или 5,82 МВт.
- С другой стороны, расчет пара, вырабатываемого котлом: (165°C — 15°C) × 0,2 кДж × 60 единиц = 1800 кВт или 1,8 МВт.