- Акт гидравлического испытания системы отопления — Офремонт
- Акт гидравлического проверки системы обогрева
- Акт гидравлических испытаний систем теплопотребления
- Акт опрессовки системы обогрева: 4 этапа
- Акт опрессовки системы снабжения воды: как сделать промывку
- Как выполнить правильно: акт опрессовки теплотрассы
- акт гидравлического испытания системы отопления образец заполнения
- Бланк и акт опрессовки системы кондиционирования
- #СантехУчебка №5: Гидравлическое испытание системы отопления в квартире
- Форма акта опрессовки системы обогрева (видео)
- Акт гидравлического проверки системы обогрева и трубо-проводов
- Что такое опрессовка системы обогрева — цели испытаний. Жми!
- Акт гидравлического испытания системы отопления
- Что такое опрессовка системы отопления и какие у нее методы. Жми!
- Опрессовка системы отопления водой и воздухом в частном доме
- Опрессовка системы отопления в Минске и РБ
- Современные методы испытаний внутридомовых сетей отопления
- Испытания холодильных установок — Учебный центр Верконт Сервис
- Пневматические испытания под давлением — Сантехника и HVAC
- 3 Тесты на утечки хладагента кондиционера
- | Обучение работе с вакуумом для кондиционирования воздуха
- Продувка
- Испытание под давлением с использованием сухого газа
- Проверьте свой вакуумный насос (пустое тестирование)
- Примечания по газобалласту (при наличии)
- Evacuation
- Определение разницы между влажностью и утечкой в системе
- Вакуум для чистовой обработки
- Последние мысли
- Советы по проверке кондиционеров | KnowYourParts
- Испытание давления в воздуховодах: взгляд на балансировщик воздуха
- Испытания давлением в изменяющихся условиях окружающей среды
- 5 способов проверить утечку хладагента в домашней системе кондиционирования воздуха
Акт гидравлического испытания системы отопления — Офремонт
Акт гидравлического проверки системы обогрева
Акт гидравлических испытаний систем теплопотребления
Гидравлические проверки — это вид неразрушающего контроля прочности/плотности оборудования. Ведется путем создания лишнего давления водой.
Скачать пустой бланк акта «Гидравлического проверки» (ИТП, СО, трубного змеевика)
Периодичность гидравлического проверки для теплоустановок и тепло магистралей 1 год.
На гидравлике испытаниям у потребителей энергии тепла подвержены:
- теплосети
- тепловые пункты
- системы обогрева
- теплосети калориферов и сами калориферы
- теплообменные аппараты ГВС/теплоснабжения
Гидравлические проверки тепло магистралей
Согласно п. 14.4 ТКП 458-2012 «Гидравлические проверки тепло магистралей выполняются давлением 1,25 рабочего, однако не менее 0,2 МПа. Магистрали из труб выдерживаются под пробным давлением не меньше 10 минут. После снижения давления до рабочего выполняется внимательный осмотр трубо-проводов по всей их длине. Результаты испытаний считаются удовлетворительными,если во время их проведения не случилось падения давления и не обнаружено признаков течи или потения в соединениях сварки и по большей части металле, заметных остаточных деформирований, трещин или признаков разрыва. Для гидравлического проверки должна использоваться вода с температурой не ниже +5С и не выше +40С. Гидравлические проверки трубо-проводов должны выполняться при плюсовой температуре воздуха снаружи»
В вариантах, когда отопление объекта выполняется от тепло магистралей РУП «Минскэнерго» или УП «Минсккомунтеплосети», акты предоставляют перечисленные выше организации.
Внимательно посмотрите на заполнение акта, характеристики тепло магистралей (длинна, диаметр, точка подсоединения), указанные в акте гидравлических испытаний должны отвечать сетям на балансе потребителя согласно акту разъединения балансовой принадлежности тепловые сетей
Пример заполненного акта гидравлического проверки теплосети:
Гидравлические проверки внутренних систем теплопотребления
П.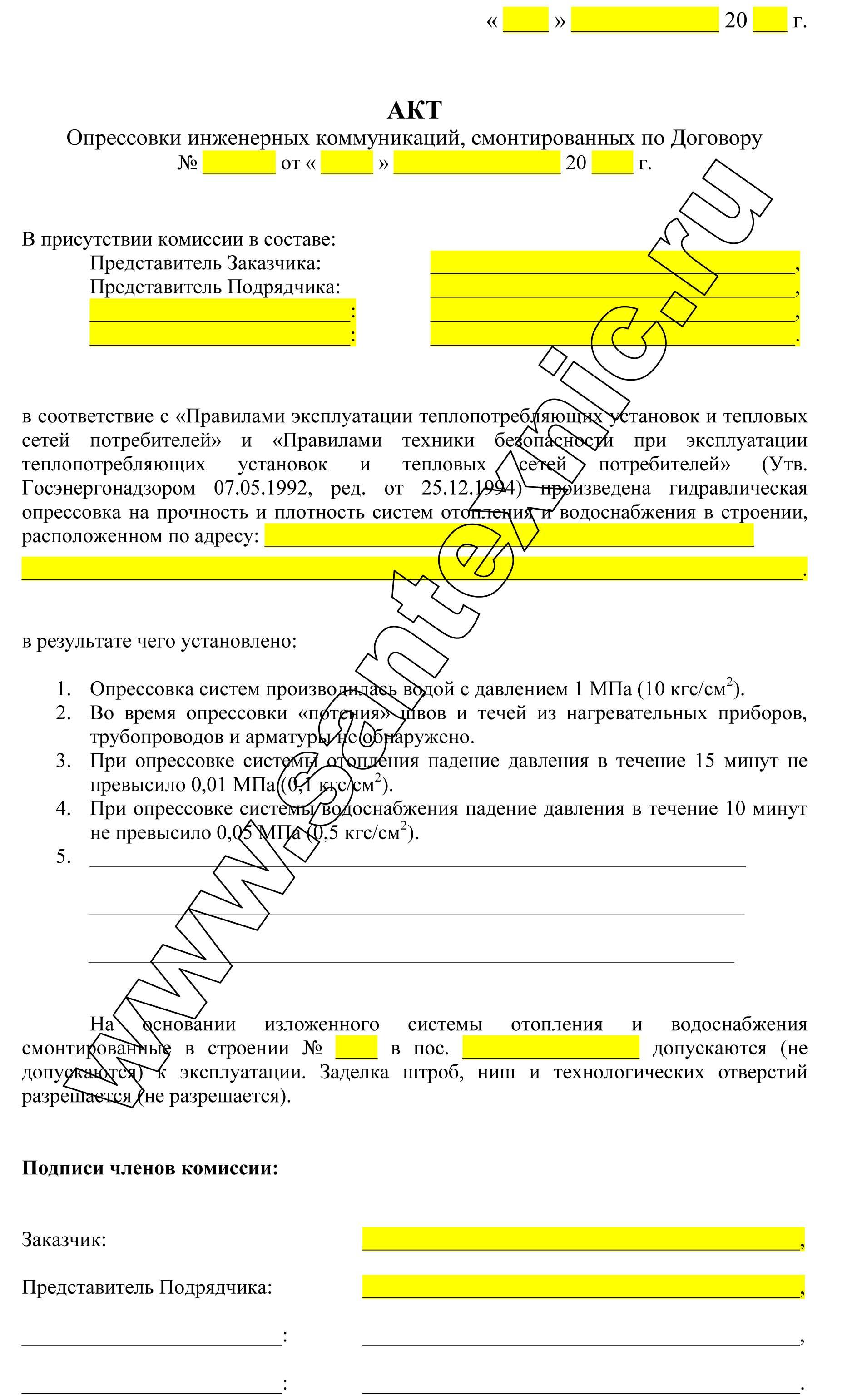
Теплообменные аппараты, будет это системы ГВС или теплоснабжения должны подвергаться опресовке давлением указанным в паспорте, однако не ниже 1 МПа. Очень часто их испытуют на 12,5 ата или 16 ата.
Отопительную систему испытуют на на давление 1,25 рабочего однако не ниже 0,6МПа (6 ата) для отопительных систем с чугунными дизайн радиаторами. системы обогрева с панельного и конвекторного теплоснабжения испытываются на 1МПа (10 ата).
Успешными признаются проверки в ходе которых в течении 10 минут не не случилось падения давления (точнее в п. 20.13 ТКП 458-2012) в испытуемых системах.
Пример заполненного акта гидравлического проверки ИТП, системы обогрева, трубного змеевика:
Акт опрессовки системы обогрева: 4 этапа
Для запуска теплосети или водообеспечения в эксплуатирование нужно испытать конструкциюНикто не может опровергать надобности наличия системы отопления в квартире или доме в наших широтах, когда осень и зима бывают особенно холодными. Самой популярной и наиболее эксплуатируемой считается система обогрева, предусматривающая циркуляцию носителя тепла по трубам. Для работы без разных перебоев системы рассчитано проведение профилактических и контрольных мероприятий, которые смогут помочь проследить за нормальной работоспособностью системы.
Чтобы узнать готовность системы обогрева к работе оборудования и контуров, которые были смонтированы, нужно провести гидравлические проверки. В результате проведения нужной проверки составляют акт опрессовки. Говоря иначе, опрессовка – это комплекс мероприятий по проверке системы, которые формируют, насколько герметична система отопления.
Для обнаружения проблемных участков либо для доказательства работоспособности в рабочем режиме нужно проведение гидравлических испытаний
Когда эксплуатационная система обогрева готова к сдаче, необходимо полностью окончить первый монтаж.
Опрессовку необходимо проводить прежде чем начнется отопительный период. Проверка также нужна, если проводились ремонтные или меры по профилактике на трубопроводах. Чаще всего бывает такое, что трубы «прорывают». Для их ремонта хорошего качества следует определить самые слабые участки системы и разработать план работ по ремонту.
- В систему отопления под большим давлением нагнетают воздух или воду, при этом применяют гидравлический или пневмонасос.
- Этот процесс дает возможность обнаружить место, где была нарушена непроницаемость, что означает попадание воздуха или воды наружу.
- Ненастоящий способ позволяет моделировать ситуации, когда критические величины работают на систему отопления.
- При выполнении проверочных работ исправные системы не подвержены никакому риску.
Что бы проверить независимой системы обогрева в высотном доме очень часто применяют нагнетатель воздуха. Проверку делают с помощью пневматической опрессовки, чтобы вода не просачивалась на этажи, размещенные ниже. Каждая система обогрева уникальна, благодаря этому перед тем как проводить проверочную работу, нужно познакомиться с особенностями характера определенной системы.
Акт опрессовки системы снабжения воды: как сделать промывку
Каждой системе отопления характерны индивидуальные особенности, которые необходимо брать во внимание при выполнении опрессовки. Важно правильно высчитать возможное давление, появившееся во время процедуры опрессовки. Следует хорошо познакомиться с типом разводки системы отопления, характеристикой труб (необходимо брать во внимание их возраст, толщину стен, материал изготовления). Также необходимо принимать во внимание кол-во этажей и характеристики арматуры.
Опрессовка и промывание отопительных систем ведется после выключения всей системы и убирания носителя тепла (воды или антифриза) из нее
Проводить опрессовку необходимо только тогда, когда будут установлены параметры системы обогрева.
В основу контрольно-проверочного мероприятия входит подготовка оборудования, слив старого носителя тепла (если он подлежит замене), пуск в систему проверочного носителя тепла, создание давления. Дефекты системы и повреждённые участки должны подлежать безотлагательному ремонту. Когда обнаруженные повреждения ликвидированы, необходимо сделать повторную опрессовку.
Как выполнить предварительную промывку труб:
- Сделать выключение системы обогрева: необходимо остановить водо подачу, а потом убрать тепловой носитель.
- Если проверки проводят на системе, которой уже пользовались на протяжении длительного времени, нужно вымыть трубы отопительного контура.
- Трубы необходимо высвободить от накипи, убрать из них ржавчину, солевые и иные отложения.
Необходимо заметить, что наличие даже самых тонких наростов говорит про то. То система функционирует неэффективно. Разные загрязнения помогают уменьшению диаметра труб, по которой двигается тепловой носитель. Наросты и коррозия приводят к слишком сильной нагрузки насоса и отопительного котла. Эти все факторы оказывают влияние на то, что система обогрева становится малоэффективной и затратной.
Как выполнить правильно: акт опрессовки теплотрассы
Операция по контролю цельности всей линии теплотрассы именуется опрессовкой. Операцию в большинстве случаев проводят на относительно небольшом участке трубопровода. Данный участок изолируют от ключевой линии, подвергая испытаниям с помощью очень высокого давления, не превышающего возможные границы.
Опрессовка — это комплекс типовых мероприятий что бы проверить оборудования для отопления к работе
Для опрессовки теплотрассы применяют способ закачки большого водного или воздушного объема в отдельную трубу, что делает уровень критического трубопроводного давления.
Система считается пригодной для эксплуатирования, если во время проверки хранит собственную непроницаемость. А вот если система нарушена, и найдено слабенькое место, то весь участок поломанной трубы подлежит ремонту. Опрессовка нужна что бы проверить всех новых водомерных узлов и устаревших систем.
Как делают опрессовку:
- Перекрывают и делают непроницаемым участок, который будут ремонтировать.
- Закрывают опорную арматуру (перекрытие всех вентилей и кранов). Важно сделать это на двоих концах участка.
- Делают подключение источника, который создать нужное давление. Для этого пользуются специализированным опрессовочным насосом или традиционным насосом, отвечающим за циркуляцией носителя тепла в системе.
- Для опрессовки применяют специализированные краны, закрепленные на каждом радиаторе.
- Есть возможность опрессовки водомерного узла сквозь отрезок трубы, где исполняется подключение как горячей, так и холодной воды.
акт гидравлического испытания системы отопления образец заполнения
Многие показатели проверки зависят от того, насколько крепким будет насос. Насос с небольшой мощностью приводит к увеличению времени проверки. Слабый опрессовщик не сумеет быстро справиться с заполнением габаритной трубы нужным воздушным объемом. Скорректировать результаты не в хорошую сторону могут негерметичные стыки.
Бланк и акт опрессовки системы кондиционирования
Система кондиционирования должна быть прочной и герметичной. Для опрессовки системы применяют азот с небольшим количеством примесей. Такой азот находится в баллонах. Что бы проверить нельзя применять сжатый воздух, так как в нем содержится немалое количество влаги.
#СантехУчебка №5: Гидравлическое испытание системы отопления в квартире
Когда опрессовку проводят с использованием азота, баллон подсоединяют к фреоновой магистрали через редуктор, который наблюдает за уменьшением давления.
Если изменяются внешних условий, чтобы провести быструю оценку, можно пользоваться показателем корректировки. Если во время проверки по корректировки режима температур, выявили снижение давления, приступают к проверке потенциально слабых мест: разъемных паяных соединений, заглушек, вальцовок. Утечки можно отыскать с помощью обычного способа обмыливания.
В каких ситуация делают опрессовку:
- Во время установки новой системы;
- После ремонтных работ и перед запуском системы;
- В целях профилактики.
Опрессовка ведется для того, чтобы своевременно обнаружить поломки в системе и решить их. Образец акта опрессовки можно отыскать и скачать в сети интернет. Форма наполнения у всех проверок обычная, но главное не забыть учесть самые лучшие характеристики каждой системы.
Форма акта опрессовки системы обогрева (видео)
Опрессовка системы обогрева – важнейший этап, в процессе какого можно обнаружить поломки и быстро удалить их. Важно выполнять проверку перед запуском системы и после ее ремонта. Очень важно убирать поломки по мере их нахождения.
Акт гидравлического проверки системы обогрева и трубо-проводов
Ни одна отопительная конструкция не может регулярно работать, а это означает давать надежное отопление, без плановых профилактических мероприятий. Среди них — гидравлические проверки системы обогрева. Их целью считается нахождение слабых участков, которые как правило создают проблематику хозяевам недвижимого имущества тогда когда этого совсем не ждешь.
Проведение испытательных мероприятий (называют их еще по другому опрессовкой) – это целый комплекс работ, которые направлены на обнаружение минусов не только в прочности трубопровода, но и всего оборудования для отопления.
Проведения времени гидравлических испытаний
Гидравлическое тестирование трубо-проводов отопительных систем и прочих их компонентов исполняют в таких вариантах:
- при приготовлении конструкции отопления к отопительному периоду;
- при надобности поменять один из участков;
- после окончания работ по ремонту;
- когда выполняется сдача объекта в эксплуатирование.
Успешное окончание гидравлических испытаний считается доказательством герметичности схемы.
Сам процесс состоит из нескольких стадий:
- используя особенное оборудование в магистрали из труб под конкретным давлением поступает воздух или вода;
- обнаружение слабых мест в отопительной системе;
- удаление минусов.
Делаются гидравлические проверки трубо-проводов и дизайн радиаторов при небольшом количестве профессионалов.
Нормы и правила
При выполнении данных планово-профилактических мероприятий пользуются именно разработанным СНиПом, который описывает очередность и рабочие нюансы, зачем в документе есть стандартная инструкция. В нем также содержатся инновационные схемы, учитывающие все специфики проведения действий согласно технике безопасности и нужное оборудование. Любые гидравлические проверки производятся в точном согласии с данным нормативным документом.
Когда ведутся гидравлические проверки системы обогрева – СНиП регламентирует обязательную промывку конструкции, с целью удаления с стен внутри трубо-проводов и отопительных приборов отложения и накипь. Способов ее проведения есть несколько, при этом применяют нагнетатель воздуха и специализированные растворы.
Очень часто в трубопроводах собираются оксиды:
- меди;
- железа:
- серы;
- цинка;
- кальция;
- магния.
Исполнять промывку системы отопления эксперты советуют не реже, чем 1 раз на протяжении пяти лет. В результате обогрев помещений станет более успешным и хорошим. А дело все в том, что во время эксплуатации понижается качество отопления за счёт образования отложений и накипи, которые, собираясь на стенках труб, делают меньше их сечение, после этого циркуляция носителя тепла замедляется. Делать иногда мероприятия по профилактике отопительных систем и технических коммуникаций обязаны рабочие компании, обслуживающие строения. В жилых домах эти работы исполняют работники ЖЭКов или подобных организаций и фирм.
Проведение опрессовки
Все работу по опрессовке ведутся силами именно обученного персонала с применением требуемого оборудования. Собственноручно хозяевам квартир либо домов делать эту работу полностью запрещается.
Опрессовку начинают с наполнения теплосети водой, если до этого она была пустой. Выполняется это через обратный трубопровод системы теплопроводов, а точнее через элеватор. С помощью вентилей, размещенных в наиболее высоких точках, стравливают воздух до той поры, пока из них не возникнет тепловой носитель.
При обнаружении утечки воды, систему опорожняют через дренажные вентили. Насос для выполнения опрессовки подсоединяют через узел управления. У лица, ответственного за выполнение работ, есть пустой бланк, который он заполняет в процессе проведения мероприятия. По окончанию выписывают акт гидравлического проверки системы обогрева, как он смотрится видно на фото.
Зачем нужен акт
Дальше составляется акт гидравлического проверки систем отопления. В нем отражают результаты проведенных мероприятий и делают заключение относительно пригодности отопительной конструкции с разрешением эксплуатационного ввода.
Специфики процесса опрессовки
Проверка системы на непроницаемость выполняется под давлением, причем его величина превосходит рабочее в 1,5 раза.
Мероприятия, включающие гидравлические проверки теплообменных аппаратов и иных элементов, исполняют при воплощении следующих условий:
- напор не может быть менее 0,6 бар;
- температура воды неизменная;
- систему следует полностью спасти от воздушных пробок;
- анализ на крепость проводят с использованием приборов для определения величины давления.
Очередность гидравлических испытаний системы обогрева
При опрессовке работа ведется постепенно:
- В начале гидравлических испытаний напор в системе поднимают до установленной величины минимум раза в 2. В большинстве случаев это делают в течении получаса, увеличивая его каждые 10 минут. На протяжении следующих 30 минут давление поддерживают на уровне не менее величины 0,6 бар.
- На втором шаге напор должен составлять не меньше 0,2 бара. При выявлении утечки во фланцевых или резьбовых узлах системы отопления допускается их подтяжка. Когда минусы не получается удалить, это соединение нужно поменять.
Проведение гидравлических испытаний выделяется сложностью, к нему необходимо подходить серьезно. Сделать самостоятельно опрессовку качественно не выйдет. Лучше всего обратиться к услугам специализированных организаций, которые после окончания работы выдадут акт гидравлического проверки системы обогрева и вот тогда с приходом холодов в доме будет уютно и тепло.
Что такое опрессовка системы обогрева — цели испытаний. Жми!
Для запуска теплосети или водообеспечения в эксплуатирование, в результате проведения всех важных работ по монтажу нужно испытать собранную конструкцию.
На этом этапе производятся гидравлические проверки, по результатам которых составляется акт, свидетельствующий о пригодности системы к применению по целевому направлению и ее способности держать гидравлические удары.
Цель испытаний
Проведение гидравлических испытаний – это не каприз и не каприз.
Проверки в первую очередь ведутся после создания новой сети или в результате проведения капремонта, мер по профилактике и реконструкции уже существующей, а еще в первую очередь до начала сезона отопления.
После этого выполняется новое испытание, и так происходит до той поры, пока не будут получены результаты, необходимые норме. Собственно, есть два этапа проведения испытаний: первичные и финальные.
Примите к сведению: ведется опрессовка что бы проверить герметичности и цельности, а еще нахождения предпологаемого брака на каждом участке водомерного узла, включая котлы.
Аналогичные проверки собой представляют довольно популярный процесс опрессовки отопительных систем. Происходит это при помощи имитирования гидравлического удара, когда в системе нагнетается давление, превышающее нормативное во много раз.
Замечание профессионала: весь брак и недоработки, обнаруженные в момент проведения опрессовки, обязаны быть устранены без промедлений и без промедлений.
Все правила проведения проверок аналогичного характера всегда жёстко регламентированы.
Для гидравлических испытаний пользуются нормами. Это два СНиПа: 41-01-2003 и 3.05.01-85, а еще «Правила технической эксплуатации тепловых энергоустановок» от 2003 г.
Процедура тестов достаточно прозрачная и понятна:
Важные тонкости испытаний
Собственно, акт проведения гидравлических испытаний становится доказательством проведенных тестов.
При этом сами проверки могут проводиться одним из 2-ух способов:
Первый способ тестирования предусматривает применение приборов для определения величины давления, которые фиксируют и показывают системное давление.
Нужно обратить внимание: при помощи приборов для определения величины давления устанавливается величина лишнего давления, что дает возможность сделать вывод о достоверности проверки.
Второй способ проверяет настоящую готовность системы к работе путем проверки работоспособности при давлении на 50% больше, чем показатель. Любой тест продолжается не меньше 10 минут, возможный показатель падения давления при опрессовке не больше 0,02 МПа.
Желательно знать: ключевой документ, свидетельствующий про проведение тестов – подходящий акт.
Аналогичный акт обязан быть составлен по форме и подписан всеми ответственными лицами.
Данный документ очень важен, его заполнение и подписание происходит в первую очередь день в день с проведением проверки. Образец бланка приведен в СНиПе 3.05.01-85.
(Форму акта об испытании системы отопления Вы можете скачать тут).
Еще существует ряд жёстких требований к оформлению и структуре этого документа:
- в акте должна обязательно быть указана дата проведения проверки и составления документа;
- обязаны быть перечислены все ответственные лица за проведение опрессовки;
- в первую очередь указание полного название объекта проверки и адреса, по которому он находится;
- достаточно указать параметры теста, место проверки системы;
- приведение показателей давления при тестах: рабочего, проверочного и давления в конце тестов;
- показатели падения давления в системе в течении процесса опрессовки;
- результаты осмотра конструкций, главных составляющих;
- список сделанных работ по ремонту, если они имели место;
- факт приемки и полное заключение про готовность системы к работе;
- подписи всех уполномоченных лиц.
Те либо другие пункты могут несколько различаться в зависимости от характера и трудности объекта, на котором проводились проверки, и причин их проведения.
Посмотрите видео, в котором разъясняются этапы проведения опрессовки системы обогрева:
Акт гидравлического испытания системы отопления
Акт гидравлических испытаний систем теплопотребления
Гидравлические испытания — это вид неразрушающего контроля прочности/плотности оборудования. Проводится путем создания избыточного давления водой.
Скачать пустой бланк акта «Гидравлического испытания» (ИТП, СО, теплообменника)
Периодичность гидравлического испытания для теплоустановок и тепловых сетей 1 год.
Гидравлическим испытаниям у потребителей тепловой энергии подвергаются:
- тепловые сети
- тепловые пункты
- системы отопления
- системы теплоснабжения калориферов и сами калориферы
- теплообменники ГВС/отопления
Гидравлические испытания тепловых сетей
Согласно п. 14.4 ТКП 458-2012 «Гидравлические испытания тепловых сетей осуществляются давлением 1,25 рабочего, но не менее 0,2 МПа. Трубопроводы выдерживаются под пробным давлением не менее 10 минут. После снижения давления до рабочего производится тщательный осмотр трубопроводов по всей их длине. Результаты испытаний считаются удовлетворительными,если во время их проведения не произошло падения давления и не обнаружено признаков течи или потения в сварных соединениях и в основном металле, видимых остаточных деформаций, трещин или признаков разрыва. Для гидравлического испытания должна применяться вода с температурой не ниже +5С и не выше +40С. Гидравлические испытания трубопроводов должны производиться при плюсовой температуре наружного воздуха»
В случаях, когда теплоснабжение объекта осуществляется от тепловых сетей РУП «Минскэнерго» или УП «Минсккомунтеплосети», акты выдают вышеперечисленные организации.
Обращайте внимание на заполнение акта, характеристики тепловых сетей (длинна, диаметр, точка подключения), указанные в акте гидравлических испытаний должны соответствовать сетям на балансе потребителя согласно акту разграничения балансовой принадлежности тепловые сетей
Пример заполненного акта гидравлического испытания тепловой сети:
Гидравлические испытания внутренних систем теплопотребления
П. 20.10 ТКП 458-2012 гласит, что ежегодно перед началом отопительного периода гидравлическим испытаниями подвергаются элеваторные узлы, калориферы, теплообменники на давление 1,25 рабочего но не ниже 1МПа (10 ата). Под элеваторным узлом авторы скорее всего понимают весь тепловой узел, поэтому в связи с установившейся практикой в качестве давление, на которое испытывается тепловой узел принимается 1 МПа(10 ата).
Теплообменники, будь то системы ГВС или отопления должны подвергаться опресовке давлением указанным в паспорте, но не ниже 1 МПа. Зачастую их испытывают на 12,5 ата или 16 ата.
Систему отопления испытывают на на давление 1,25 рабочего но не ниже 0,6МПа (6 ата) для систем отопления с чугунными отопительными приборами. системы отопления с панельного и конвекторного отопления испытываются на 1МПа (10 ата).
Успешными признаются испытания в ходе которых в течении 10 минут не не произошло падения давления (точнее в п. 20.13 ТКП 458-2012) в испытуемых системах.
Пример заполненного акта гидравлического испытания ИТП, системы отопления, теплообменника:
ozp.hdvao.by
Акт опрессовки системы отопления: 4 этапа
Для запуска системы теплоснабжения или водоснабжения в эксплуатацию необходимо протестировать конструкциюНикто не может отрицать необходимости наличия отопительной системы в доме или квартире в наших широтах, когда осень и зима бывают особенно холодными. Самой распространенной и наиболее эксплуатируемой считается система отопления, предусматривающая циркуляцию теплоносителя по трубам. Для бесперебойной работы системы предусмотрено проведение профилактических и контрольных мероприятий, которые помогут проследить за нормальной работоспособностью системы.
Содержание:
Чтобы определить готовность системы отопления к эксплуатации оборудования и контуров, которые были смонтированы, необходимо провести гидравлические испытания. После проведения необходимой проверки составляют акт опрессовки. Иными словами, опрессовка – это комплекс мероприятий по проверке системы, которые определяют, насколько герметична отопительная система.
Для выявления проблемных участков или для подтверждения работоспособности в рабочем режиме необходимо проведение гидравлических испытаний
Когда эксплуатационная система отопления готова к сдаче, следует полностью завершить первоначальный монтаж.
Опрессовку нужно проводить перед тем, как начнется отопительный сезон. Проверка также необходима, если проводились ремонтные или профилактические работы на трубопроводах. Очень часто случается так, что трубы «прорывают». Для их качественного ремонта необходимо определить самые слабые участки системы и составить план ремонтных работ.
Процесс опрессовки:
- В отопительную систему под высоким давлением нагнетают воздух или воду, при этом используют гидравлический или пневматический насос.
- Такой процесс позволяет выявить место, где была нарушена герметичность, что означает попадание воздуха или воды наружу.
- Искусственный способ позволяет моделировать ситуации, когда критические величины действуют на отопительную систему.
- При проведении проверочных работ исправные системы не подвергаются никакому риску.
Для проверки автономной системы отопления в многоэтажном доме чаще всего используют компрессор. Проверку делают при помощи пневматической опрессовки, чтобы вода не просачивалась на этажи, расположенные ниже. Каждая система отопления уникальна, поэтому прежде чем проводить проверочную работу, необходимо ознакомиться с характерными особенностями конкретной системы.
Акт опрессовки системы водоснабжения: как выполнить промывку
Каждой отопительной системе присущи характерные особенности, которые нужно учитывать при выполнении опрессовки. Важно правильно рассчитать возможное давление, образовавшееся во время процедуры опрессовки. Следует внимательно ознакомиться с типом разводки отопительной системы, характеристикой труб (нужно учитывать их возраст, толщину стен, материал изготовления). Также нужно учесть количество этажей и характеристики арматуры.
Опрессовка и промывка систем отопления проводится после отключения всей системы и удаления теплоносителя (воды или антифриза) из нее
Проводить опрессовку нужно только тогда, когда будут определены параметры системы отопления.
В основу контрольно-проверочного мероприятия входит подготовка оборудования, слив старого теплоносителя (если он подлежит замене), запуск в систему проверочного теплоносителя, создание давления. Изъяны системы и поврежденные участки должны подлежать безотлагательному ремонту. Когда обнаруженные повреждения ликвидированы, нужно выполнить повторную опрессовку.
Как сделать предварительную промывку труб:
- Выполнить отключение системы отопления: нужно прекратить подачу воды, а затем убрать теплоноситель.
- Если испытания проводят на системе, которой уже пользовались в течение продолжительного времени, необходимо промыть трубы контура отопления.
- Трубы нужно освободить от накипи, убрать из них ржавчину, солевые и другие отложения.
Следует заметить, что наличие даже самых тонких наростов может говорить о том. То система функционирует неэффективно. Различные загрязнения способствуют уменьшению диаметра труб, по которым циркулирует теплоноситель. Наросты и ржавчина приводят к слишком большой нагрузки насоса и котла отопления. Все эти факторы влияют на то, что система отопления становится неэффективной и затратной.
Как сделать правильно: акт опрессовки теплотрассы
Операция по контролю целостности всей линии теплотрассы называется опрессовкой. Операцию обычно проводят на относительно маленьком участке трубопровода. Этот участок изолируют от основной линии, подвергая испытаниям при помощи повышенного давления, не превышающего допустимые границы.
Опрессовка — это комплекс стандартных мероприятий для проверки отопительного оборудования к эксплуатации
Для опрессовки теплотрассы используют метод закачки большого водного или воздушного объема в отдельную трубу, что создает уровень критического трубопроводного давления.
Система считается пригодной для эксплуатации, если во время проверки сохраняет свою герметичность. А вот если система нарушена, и найдено слабое место, то весь участок неисправной трубы подлежит ремонту. Опрессовка необходима для проверки всех новых водопроводов и старых систем.
Как делают опрессовку:
- Перекрывают и делают герметичным участок, который будут ремонтировать.
- Закрывают опорную арматуру (перекрытие всех вентилей и кранов). Важно сделать это на обоих концах участка.
- Производят подключение источника, который создать необходимое давление. Для этого пользуются специальным опрессовочным насосом или обычным насосом, отвечающим за циркуляцией теплоносителя в системе.
- Для опрессовки используют специальные краны, закрепленные на каждом радиаторе.
- Существует возможность опрессовки водопровода сквозь патрубок, где выполняется подключение как горячей, так и холодной воды.
Многие показатели проверки зависят от того, насколько прочным будет насос. Насос с маленькой мощностью приведет к увеличению времени проверки. Слабый опрессовщик не сможет быстро справиться с заполнением габаритной трубы необходимым воздушным объемом. Изменить результаты не в лучшую сторону могут негерметичные стыки.
Бланк и акт опрессовки системы кондиционирования
Система кондиционирования должна быть прочной и герметичной. Для опрессовки системы используют азот с минимальным количеством примесей. Такой азот находится в баллонах. Для проверки нельзя использовать сжатый воздух, так как в нем содержится большое количество влаги.
Когда опрессовку проводят с применением азота, баллон подключают к фреоновой магистрали через редуктор, который следит за понижением давления.
Если изменяются внешних условий, чтобы провести быструю оценку, можно пользоваться коэффициентом коррекции. Если во время проверки по коррекции температурного режима, обнаружили снижение давления, приступают к проверке потенциально слабых мест: разъемных паяных соединений, заглушек, вальцовок. Утечки можно найти при помощи простого способа обмыливания.
В каких ситуация делают опрессовку:
- При установке новой системы;
- После ремонта и перед запуском системы;
- В профилактических целях.
Опрессовка проводится для того, чтобы вовремя выявить неполадки в системе и решить их. Образец акта опрессовки можно найти и скачать в интернете. Форма заполнения у всех проверок стандартная, но важно учитывать качественные характеристики каждой системы.
Форма акта опрессовки системы отопления (видео)
Опрессовка системы отопления – очень важный этап, в процессе которого можно выявить неполадки и быстро устранить их. Важно проводить проверку перед запуском системы и после ее ремонта. Особенно важно устранять неполадки по мере их обнаружения.
teploclass.ru
Акт гидравлического испытания системы отопления и трубопроводов
Ни одна отопительная конструкция не может постоянно функционировать, а значит обеспечивать надежное теплоснабжение, без плановых профилактических мероприятий. Среди них — гидравлические испытания системы отопления. Их целью является нахождение слабых участков, которые могут создать проблему владельцам недвижимости в самый неподходящий момент.
Проведение испытательных мероприятий (их еще называют опрессовкой) – это целый комплекс работ, направленных на обнаружение недостатков не только в прочности трубопровода, но и всего отопительного оборудования.Время проведения гидравлических испытаний
Гидравлическое испытание трубопроводов систем отопления и других их элементов выполняют в следующих случаях:
- при подготовке конструкции теплоснабжения к отопительному сезону;
- при необходимости заменить один из участков;
- после завершения ремонтных работ;
- когда производится сдача объекта в эксплуатацию.
Удачное завершение гидравлических испытаний является подтверждением герметичности схемы.
Сам процесс состоит из нескольких этапов:
- при помощи специального оборудования в трубопроводы под определенным давлением подается воздух или вода;
- обнаружение слабых мест в системе отопления;
- устранение недостатков.
Выполняются гидравлические испытания трубопроводов и отопительных приборов при минимальном количестве специалистов.
Нормативы и правила
При проведении этих планово-профилактических мероприятий пользуются специально разработанным СНиПом, который описывает последовательность и нюансы работ, для чего в документе имеется типовая инструкция. В нем также содержатся технологические схемы, учитывающие все особенности проведения действий согласно технике безопасности и требуемое оборудование. Любые гидравлические испытания производятся в точном соответствии с этим нормативным документом.
Когда проводятся гидравлические испытания системы отопления – СНиП регламентирует обязательную промывку конструкции, чтобы удалить с внутренних стен трубопроводов и радиаторов отложения и накипь. Способов ее проведения существует несколько, при этом используют компрессор и специальные растворы.
Чаще всего в трубопроводах собираются оксиды:
- меди;
- железа:
- серы;
- цинка;
- кальция;
- магния.
Выполнять промывку отопительной системы специалисты рекомендуют не реже, чем один раз в течение пяти лет. В результате обогрев помещений будет более эффективным и надежным. Дело в том, что в процессе эксплуатации понижается качество теплоснабжения за счет образования отложений и накипи, которые, собираясь на стенках труб, уменьшают их сечение, после чего циркуляция теплоносителя замедляется. Производить периодически мероприятия по профилактике систем отопления и инженерных коммуникаций обязаны эксплуатационные компании, обслуживающие здания. В жилых домах данные работы выполняют работники ЖЭКов или аналогичных организаций и предприятий.
Проведение опрессовки
Все работы по опрессовке проводятся силами специально обученного персонала с использованием необходимого оборудования. Собственноручно владельцам домов или квартир делать данную работу категорически запрещено.
Опрессовку начинают с заполнения системы теплоснабжения водой, если до этого она была пустой. Делается это через обратный трубопровод теплосети, а конкретнее через элеватор. При помощи вентилей, расположенных в наиболее высоких точках, стравливают воздух до тех пор, пока из них не появится теплоноситель.
В случае обнаружения утечки воды, систему опорожняют через дренажные вентили. Насос для выполнения опрессовки подключают через узел управления. У лица, ответственного за проведение работ, есть пустой бланк, который он заполняет в процессе проведения мероприятия. По завершению выписывают акт гидравлического испытания системы отопления, как он выглядит видно на фото.
Для чего нужен акт
Когда производится монтаж или ремонт отопительной конструкции, по окончанию работ обязательно проводят испытания, для того, чтобы убедиться в качественном функционировании схемы. Проверяются на прочность и надежность трубопровод и различные элементы системы.Дальше составляется акт гидравлического испытания систем теплоснабжения. В нем отражают результаты проведенных мероприятий и делают заключение относительно пригодности отопительной конструкции с разрешением ввода в эксплуатацию.
Особенности процесса опрессовки
Проверка системы на герметичность производится под давлением, причем его величина превышает рабочее в 1,5 раза.
Мероприятия, включающие гидравлические испытания теплообменников и других элементов, выполняют при соблюдении следующих условий:
- напор не может быть менее 0,6 бар;
- температура воды постоянная;
- систему необходимо полностью избавить от воздушных пробок;
- анализ на прочность проводят с применением манометров.
Последовательность гидравлических испытаний системы отопления
При опрессовке работа проводится поэтапно:
- В начале гидравлических испытаний напор в системе поднимают до установленной величины минимум раза в два. Обычно это делают на протяжении получаса, повышая его каждые 10 минут. В течение следующих 30 минут давление поддерживают на уровне не меньше величины 0,6 бар.
- На втором этапе напор должен составлять не менее 0,2 бара. При обнаружении утечки во фланцевых или резьбовых узлах отопительной системы допустима их подтяжка. Когда недостатки не удается устранить, это соединение необходимо заменить.
www.trmc.ru
Что такое опрессовка системы отопления — цели испытаний. Жми!
Для запуска системы теплоснабжения или водоснабжения в эксплуатацию, после проведения всех необходимых монтажных работ необходимо протестировать готовую конструкцию.
На данном этапе производятся гидравлические испытания, по итогам которых составляется акт, свидетельствующий о пригодности системы к использованию по прямому назначению и ее способности выдерживать гидравлические удары.
Цель испытаний
Проведение гидравлических испытаний – это не каприз и не прихоть.
Испытания обязательно проводятся после создания новой сети или после проведения капитального ремонта, профилактических работ и реконструкции уже существующей, а также обязательно до начала отопительного сезона.
После чего производится новое тестирование, и так происходит до тех пор, пока не будут получены результаты, соответствующие норме. Собственно, существует два этапа проведения испытаний: предварительные и окончательные.
Примите к сведению: проводится опрессовка для проверки герметичности и целостности, а также обнаружения возможного брака на любом участке водопровода, включая котлы.
Подобные проверки представляют собой наиболее популярный процесс опрессовки систем отопления. Происходит это посредством имитации гидроудара, когда в системе нагнетается давление, превышающее нормативное в несколько раз.
Замечание специалиста: весь брак и недоделки, обнаруженные в момент проведения опрессовки, должны быть устранены незамедлительно и без задержек.
Все правила проведения проверок подобного характера всегда жёстко регламентированы.
Для гидравлических испытаний пользуются нормативными документами. Это два СНиПа: 41-01-2003 и 3.05.01-85, а также «Правила технической эксплуатации тепловых энергоустановок» от 2003 г.
Процедура тестов достаточно прозрачна и понятна:
Важные нюансы испытаний
Собственно, акт проведения гидравлических испытаний становится свидетельством проведенных тестов.
При этом сами проверки могут проводиться одним из двух способов:
- манометрическим;
- гидростатическим.
Первый способ тестирования предполагает использование манометров, которые фиксируют и демонстрируют давление в системе.
Обратите внимание: с помощью манометров определяется величина избыточного давления, что позволяет сделать вывод о достоверности испытания.
Второй способ проверяет реальную готовность системы к работе путем проверки работоспособности при давлении на 50% выше, чем норматив. Любой тест длится не менее 10 минут, допустимый показатель падения давления при опрессовке не более 0,02 МПа.
Полезно знать: основной документ, свидетельствующий о проведении тестов – соответствующий акт.
Подобный акт должен быть составлен по форме и подписан всеми ответственными лицами.
Этот документ крайне важен, его заполнение и подписание происходит обязательно день в день с проведением проверки. Образец бланка приведен в СНиПе 3.05.01-85.
(Форму акта об испытании отопительной системы Вы можете скачать здесь).
Также существует ряд жестких требований к оформлению и структуре данного документа:
- в акте обязательно должна быть указана дата проведения испытания и составления документа;
- должны быть перечислены все ответственные лица за проведение опрессовки;
- обязательно указание полного наименование объекта проверки и адреса, по которому он находится;
- необходимо указать параметры теста, место проверки системы;
- приведение показателей давления при тестах: рабочего, пробного и давления в конце тестов;
- показатели падения давления в системе на протяжении процесса опрессовки;
- результаты осмотра конструкций, основных составляющих;
- перечень проведенных ремонтных работ, если они имели место;
- факт приемки и полное заключение о готовности системы к эксплуатации;
- подписи всех уполномоченных лиц.
Те или иные пункты могут несколько различаться в зависимости от характера и сложности объекта, на котором проводились испытания, и причин их проведения.
Смотрите видео, в котором разъясняются этапы проведения опрессовки системы отопления:
teplo.guru
Что такое опрессовка системы отопления и какие у нее методы. Жми!
Одним из необходимых этапов на пути ввода в эксплуатацию отопительной системы является её опрессовка.Важность подобной процедуры заключается в том, чтобы проверить насколько качественно был осуществлен монтаж, понять насколько работоспособными являются её элементы и выявить скрытые дефекты, чтобы в дальнейшем их устранить.
Когда подобная процедура заканчивается, и все работает должным образом, выдается соответствующий документ, который и называется акт опрессовки отопления.
При этом важно понимать, что это только один из видов необходимых испытаний для ввода в эксплуатацию системы теплоснабжения, который осуществляют:
- в случае завершения монтажа новой отопительной системы;
- по завершении ремонтных работ;
- если в здании проводились какие-либо строительные работы;
- до наступления отопительного сезона.
Разновидности действий при опрессовке
Прежде всего стоит отметить, что подобное испытание системы теплоснабжения проводится под повышенным давлением, которое создают, используя для этого воду или воздух.Исходя из этого, такая процедура может быть:
- Пневмоопрессовкой. Главной целью такого способа считается проверка на герметичность как отдельных соединений, так и всей системы в общем. Для её осуществления используются электрические, а также ручные пневмонасосы, которые дают возможность заполнить все элементы сжатым воздухом. При этом необходимо внутри системы поддерживать нужный уровень кондиционирования, чтобы получить точные результаты.
[advice]Совет специалиста: проведение пневматической проверки отопительной системы является весьма опасным. Дело в том, что в случае наличия дефектов воздух будет быстро высвобождаться через них, за счет чего может нанести большие повреждения. Именно поэтому давление выше отметки в 0.15 МПа не стоит увеличивать.[/advice]
- Гидроопрессовкой. Проводится такое исследование также для проверки прочности системы. Чтобы создать нужное давление, применяются обычные гидравлические насосы подходящей мощности. Обычно для проведения такой опрессовки давление в теплотрассе выше нормативного рабочего в среднем на 30%, в то время как при воздушной проверке этот показатель выше допустимого на 50%.
Подробнее о монтаже системы отопления в доме можно прочитать здесь: https://teplo.guru/elementy/truby/montazh-otopleniya-v-dome.html
Этапы проведения
Для проверки уровня давления в системе во время гидроиспытаний используются обычные манометры.Осуществляется данная процедура поэтапно:
- Сначала проверяются все соединения, а также работоспособность запорных элементов. Визуально оценивается их состояние.
- После этого от системы отключается не только котел, но даже расширительный бак. Это необходимо, чтобы осуществить полную промывку трубопровода и радиаторов от возможного наличия в них мелкого мусора.
- Далее начинается сама опрессовка. Для этого в систему заливается вода из водопровода и к сливному крану подключают компрессор и давление постепенно повышают, пока оно не достигнет нужной величины. В случае, если не происходит никаких изменений в показателях в меньшую сторону – это свидетельствует о том, что система полностью герметична, и её можно вводить в эксплуатацию. В случае наличия пробоины в тепловом узле труб произойдет резкое падение давления в системе.
[warning]Примите к сведению: среднее время проведения гидроопрессовки составляет один час, в то время как для пневматической проверки хватает и 20 минут.[/warning]
- Если были обнаружены неисправности, их устраняют и повторно осуществляют процедуру.
- Когда система по результатам проверки подтвердила герметичность, составляют акт опрессовки.
[advice]Обратите внимание: нельзя осуществлять подобную процедуру одному, ведь подобный процесс требует наличия специальных навыков, а также знаний. При этом важно правильно соблюдать все меры безопасности.[/advice]
Выдача документовИмея на руках документ, подтверждающий осуществление проверки отопительной системы, в случае аварий он будет являться основанием для обращения с требованием возмещения ущерба к проверяющим. (Образец акта опрессовки системы отопления можно скачать здесь)Какую систему отопления выбрать: открытую или закрытую, подскажет данная статья: https://teplo.guru/sistemy/zakrytaya-i-otkrytaya-sistemy.html
После окончания работ оформляется акт опрессовки, который имеет юридическую силу.
Такого рода документ будет являться подтверждением того, что:
- проверка на герметичность отопительной системы была проведена в соответствии со всеми нормами;
- все оборудование находится в исправном состоянии, поэтому готово к использованию;
- если после выдачи такого документа случаются аварии, то вся ответственность будет ложиться на тех, кто осуществлял проверку.
Ответственные за проведение данной процедуры, а также её результаты, могут назначаться:
- Представители организации, которая осуществляет теплоснабжение (это мастер, инспектор или даже инженер и техник). Они должны иметь при себе все соответствующие документы, оборудование, а также бланки выдаваемых актов.
- Представители самого объекта, где проводили опрессовку. Так, в многоквартирных домах таковыми являются сотрудники управляющих организаций, в частных домах – их владельцы, а если процедура осуществляется в административных или же социальных объектах – это могут быть руководители, а также сотрудники надзорных организаций.
- В тех случаях, когда опрессовку делали в новостройке, которая только сдается в эксплуатацию, добавляться в состав комиссии должны представители подрядчика.
Определиться с выбором труб для отопления поможет данный материал: https://teplo.guru/elementy/truby/vybor-trub-dlya-otopleniya.html
Таким же способом проверяется и система водоснабжения. Когда все краны в ней закрыты, повышают давление до необходимого уровня и смотрят на наличие пробоин. Все коммерческие объекты проверяются исключительно на платной основе, за счет чего стоимость работ всегда включают в смету. Поэтому нужно заранее узнать, сколько будет стоить такая процедура.
Смотрите видео, в котором специалист подробно рассказывает что такое опрессовка системы отопления, для чего выполняется и где проводится:
Опрессовка системы отопления водой и воздухом в частном доме
Эффективным методом проверки функционирования контура отопления является его гидравлические или пневматические испытания (опрессовка). По сути — это контроль герметичности и правильности монтажа всех его элементов. Проводится проверка работоспособности отопительной системы путем опрессовки бойлеров, нагревательных составляющих, расширительных баков, коммуникаций и запорной арматуры. Для этого искусственно создается избыточное давление в контуре, приближающееся к предельно возможным расчетным нагрузкам. Неисправные узлы и функциональные элементы выходят из строя, а остальные сохраняют работоспособность.
Испытания организуют перед началом отопительного сезона, после замены отдельных участков трубопроводов, установки или ремонта контролирующих приборов, их сервисного обслуживания. Грамотно проведенная опрессовка системы отопления позволяет своевременно выявить наиболее слабые и проблемные участки и устранить все неисправности.
Оглавление:
- Основные этапы
- Правила проведения испытаний
- Цены
Отработанная методика и современное оборудование дают возможность выполнять опрессовку быстро и с минимальным привлечением персонала. Осуществлять ее должны специалисты с соответствующей квалификацией. Проверка отопления жилых домов поручается работникам коммунальных хозяйств, а производственные и административные здания испытывают представители ответственных за них служб. В холодную пору года опрессовка воздухом системы отопления более предпочтительна, так как вода в трубопроводах может замерзнуть.
Порядок проведения мероприятий
Организационно гидравлические испытания представляют стандартизированный набор действий:
- Внешний осмотр всех элементов системы отопления.
- Заполнение контура теплоносителем (водой, антифризом).
- Создание опрессовочного давления и контроль его уровня измерительной техникой.
- Визуальное исследование коммуникаций, запорных элементов и нагревательных приборов на предмет герметичности и правильной работы.
- Ликвидация выявленных протечек и повторная проверка.
- Составление актов о пригодности оборудования к эксплуатации.
Обычно опрессовка отопления производится после отключения системы от централизованной подачи теплоносителя. Если требуется проводить испытания работающего оборудования, то его останавливают, охлаждают и сливают жидкость. Удаление воды, как и последующее заполнение ею системы, выполняется через специальный спусковой вентиль, который находится в тепловом (элеваторном) узле на обратном трубопроводе. При таком нижнем подключении жидкость, постепенно заполняющая контур, выдавливает из него воздушные пробки. Перед подсоединением компрессора надо рассчитать величину допустимого опрессовочного давления. Во время вычислений важно учесть:
1. Сроки эксплуатации. В новых домах опрессовка труб систем кондиционирования и отопления может проводиться давлением, в 2 раза превышающим рабочее. В старых — увеличенным лишь на 15–50 %.
2. Тип установленных в помещении отопительных приборов. Для проверки конвекторов допустимо поднимать давление до 10 атм, а для чугунных радиаторов — не более чем до 6.
3. Технические характеристики трубопроводов и запорной арматуры (толщина и прочность материала).
4. Использованный тип разводки.
5. Этажность здания и его назначение.
Автоматический компрессор или ручной насос (пресс) подключается к спусковому вентилю. С его помощью давление в системе отопления увеличивается до опрессовочного уровня и поддерживается в течение 15 минут. При снижении показаний более, чем на 0,1 атм (фиксируется манометром), принимается решение о разгерметизации и начинаются поиски мест утечки теплоносителя.
В зданиях небольшой этажности обычно поддерживается невысокое давление жидкости (до 2 атм), поэтому опрессовка отопительной системы в частном доме может осуществляться без помощи компрессора (насоса), простым подключением к водопроводной сети. Если испытания проводятся водой, то места разгерметизации визуально находят по следам протечек теплоносителя. Антифриз обладает большей текучестью, поэтому точки его выхода на поверхность обнаружить проще.
При продувке воздушным компрессором сомнительные участки покрывают мыльным раствором и наблюдают за его вспениванием. Наибольшее внимание следует уделить осмотру запирающей арматуры, радиаторов, резьбовых и сварных соединений и прокладок, а также скрытых в стенах и полу частях трубопроводов.
После устранения проблем производится повторная опрессовка системы квартирного отопления. Неизменные показания манометра в течение контрольного времени свидетельствуют о ее исправности. После этого давление снижается до рабочего, а компрессор отсоединяется от контура. Качественная опрессовка закрытой системы отопления с принудительной циркуляцией в частном доме или коттедже займет не более двух часов. По окончанию гидравлических испытаний составляется акт выполненных работ, в котором указывается дата, расчетная величина опрессовочного давления, продолжительность контрольного мероприятия и его результаты.
Требования к проверкам
В нормативных документах, регламентирующих обслуживание внутренних санитарно-технических сетей и тепловых систем, указан порядок проведения контрольных испытаний. Прежде всего, отопительный контур надо промыть холодной хозяйственно-питьевой водой. Целью является удаление с внутренних стенок трубопроводов накипи, различных химических соединений и солевых отложений (оксидов железа, магния, кальция, меди, цинка и серы), которые уменьшают их сечение и нарушают циркуляцию жидкости. Система промывается гидропневматическим методом до появления на ее выходе чистой воды, после чего немедленно заполняется штатным теплоносителем (водой, антифризом). Оставлять контур пустым запрещается.
Согласно СНиП, при испытаниях следует придерживаться требований:
- Тепловые элеваторы и контуры отопления проверяются не реже раза в год, но не одновременно.
- Расчетное давления при опрессовке каждого типа системы надо снимать с наивысшей точки трубопровода.
- Из контуров удаляют весь воздух.
- Температура теплоносителя не должна превышать 45 ºС.
- Создается рабочее давление воды на время, необходимое для визуальной оценки отсутствия протечек (10 минут), после чего его увеличивают для проведения испытаний (не менее 15).
- Для контроля показаний используются пружинные манометры соответствующего класса точности, прошедшие плановую поверку в текущем году.
Стоимость гидропневматической проверки
С учетом дополнительных условий, цены на опрессовку отопления в квартирах и частных домах составляют:
Наименование работ | Минимальная цена, рубли | Дополнительные условия, влияющие на стоимость |
Опрессовка контуров | 45 за 1 м. погонный | Диаметр трубопровода |
Испытание отдельных элементов системы | 6 000 | Конструктивные особенности |
Ликвидация аварийных ситуаций (свищей, протечек) | 5 000 | Стандартная процедура |
7 000 | Использование газосварочного оборудования | |
Промывание трубопроводов | 130 за 1 м. погонный | Протяженность трубопровода и его диаметр |
Промывка радиаторов отопления и конвекторов | 700 за шт | Особенности отопительных устройств |
Гидропневматическая чистка котлового теплообменника | 21 000 за шт | Разновидности контуров |
Промывка теплообменника котла с применением химреактивов | 5 000 за шт | Конструктивные характеристики |
Очистка отопительного контура здания (гидропневматическая) с применением химреактивов | Определяется после визуального осмотра и составления сметы |
Опрессовка системы отопления в Минске и РБ
Опрессовка системы отопления
300.00 Br
Опрессовка системы отопления в Минске и РБ. Опыт работы с любыми системами: опрессовка труб отопления, теплового пункта, котлов и теплообменников и др. Вызываем представителя энергоснабжающей организации и составляем акт. При необходимости выполняем восстановительные работы.
Для расчета актуальной цены введите данные в форму Калькулятора. Затем нажмите на кнопку «Получить предложение», чтобы Калькулятор отправил коммерческое предложение с уникальной скидкой на e-mail.
Рассчитать цену онлайн
Заказать обратный звонокЗаказать обратный звонок
Описание
Проводим опрессовку систем отопления в Минске, Бресте, Витебске, Могилеве, Гомеле и других городах РБ
Наши опытные специалисты проведут опрессовку системы отопления в самые сжатые сроки. Мы проверим на целостность и прочность систему отопления, по результатам опрессовки составим акт.
Опрессовка любых систем
- Опрессовка трубопровода
- Опрессовка теплового пункта
- Опрессовка радиаторов системы отопления и теплоснабжения
- Опрессовка системы ГВС
- Опрессовка пластинчатых теплообменников
- Опрессовка паяных теплообменников
- Опрессовка кожухотрубных теплообменников
- Опрессовка котлов
- Опрессовка тепловых сетей (теплотрассы)
- Опрессовка калориферов системы вентиляции
Как известно, в процессе эксплуатации в системе отопления могут появляться дефекты. Для того чтобы они не дали знать о себе в самое неподходящее время, проблемные участки следует выявить в межотопительный период. Если при проведении опрессовки обнаруживаются участки разгерметизации, мы проводим ремонтно-восстановительные работы.
Внимание!
Замена не прошедших испытания участков трубопроводов и запорной арматуры, ремонт теплообменников производится за дополнительную плату.
В составе отдела главного энергетика работают 14 инженеров-энергетиков, которые общаются с представителями энергоснабжающей организации и составляют акты. На выполнение самих работ по опрессовке системы отопления назначаются сантехники из хорошо укомплектованного штата специалистов. На сегодняшний день в компании задействованы 83 сантехника.
Этапы проведения опрессовки системы отопления
Первый этап выполняется нашими специалистами без вызова представителя энергосберегающей организации. Перекрывается запорная арматура, проверяемый контур отключается от общей отопительной системы. В гидравлическую систему, заполненную теплоносителем, прессом накачивается необходимое давление (обычно на 25% выше, чем рабочее). Специалисты внимательно наблюдают за показателями манометра.
Если стрелка манометра сдвигается, если давление падает при закрытых задвижках, значит, где-то есть утечка. В таком случае составляется дефектный акт, выполняются восстановительные работы. Когда система успешно проходит опрессовку, можно вызывать представителя энергоснабжающей организации.
Второй этап – проведение опрессовки в присутствии представителя энергоснабжающей организации. Лишь убедившись в полной работоспособности системы при повышенном давлении, обходчик подписывает акт. Напоминаем, акт опрессовки системы отопления — один из ключевых документов, необходимых для получения паспорта готовности объекта к ОЗП.
Сервис Бай с 2010 года оказывает услуги по опрессовке системы отопления на самых разных объектах: начиная от многоквартирных жилых домов, заканчивая промышленными предприятиями. Мы также можем опрессовать систему отопления в частном доме. Узнать, сколько стоит опрессовка отопления вашего объекта очень просто – позвоните нам и вы получите квалифицированную консультацию.
А бонусы есть?
Конечно! Заключая с нами годовой договор на техобслуживание, вы получаете услуги по опрессовке системы отопления совершенно бесплатно! Выбирайте долгосрочное и взаимовыгодное сотрудничество!
Современные методы испытаний внутридомовых сетей отопления
Современные методы испытаний внутридомовых сетей отопления.
В разгар лета по всей нашей огромной стране кипит работа на муниципальных и внутридомовых теплосетях. К началу следующего отопительного сезона предстоит провести большой объём ремонтно-профилактических процедур: промывку трубопроводов, проверку запорной и регулирующей арматуры, выявление и ликвидацию протечек и т.п. Одним из важнейших этапов, позволяющих выявить все «слабые места» систем отопления и увеличить их надёжность, являются гидравлические испытания.
Гидравлический тест на выносливость
Согласно «Правилам технической эксплуатации тепловых энергоустановок» гидравлические испытания на внутридомовой сети жилых многоэтажных домов обязательны после ремонтных работ и замены участков трубопровода, запорной арматуры, приборов отопления. Опыт показывает, что проведение опрессовки позволяет выявить допущенные при монтаже скрытые дефекты, что является лучшей гарантией безаварийной работы оборудования в следующем отопительном сезоне.
Ответственные собственники проводят гидравлические испытания сразу после окончания отопительного сезона. Это позволяет своевременно устранить неполадки, а затем произвести повторную опрессовку. Таким образом, проверка герметичности производится в два этапа.
На первом этапе трубопроводы и батареи в многоэтажных домах заполняются холодной водой. Для систем отопления с чугунными и стальными отопительными приборами давление при испытании должно быть 0,6 МПа (6 бар), а в системах конвекторного отопления – 1 МПа (10 бар), но не менее 1,25 рабочего давления теплоносителя. При этом давление за первые 30 минут не должно упасть более чем на 0,06 МПа.
После проведения опрессовки проводится визуальный осмотр всей системы отопления. Именно на этом этапе обнаруживаются все дефекты, которые предстоит устранить за лето. Если нигде не обнаружено свищей, течей со стояков отопления и радиаторов, считается, что система выдержала гидравлическое испытание. После этого составляется акт, который подписывают представители потребителя и теплоснабжающей организации.
Второй раз отопительный контур тестируется непосредственно перед началом обогревательного сезона. Теплоноситель подаётся под максимальным рабочим давлением для данной системы – опять же с контролем образования течей.
Поскольку чаще всего систему заполняют водой из городского водопровода с небольшим давлением (от 2 до 5 бар), для проведения гидравлических испытаний в многоэтажных домах приходится использовать те или иные виды гидропрессов.
Так, для отопительных систем небольшого объёма подходят ручные агрегаты, для которых не нужен источник электропитания. Заполнение системы теплоносителем и непосредственно опрессовка осуществляются движениями рукояти. Аппарат очень прост в использовании, надёжен, невосприимчив к грязи и ударам. Благодаря малому весу и компактности его легко переносить. Подобное оборудование могут использовать не только коммунальщики, но и строительно-монтажные организации, занимающиеся опрессовкой спринклерных установок, систем кондиционирования и т.п.
Если же речь идёт об испытаниях отопительной системы большого многоэтажного дома, где объём теплоносителя может составлять десятки кубометров, то больше подойдёт высокопроизводительный электрический опрессовщик. Благодаря быстроразъёмной системе контрольный блок и манометр могут оставляться на испытательном контуре. А насос тем временем может использоваться для опрессовки другого контура с дополнительным контрольным блоком.
Для организаций, производящих ремонтно-профилактические работы на системах отопления, важно выполнить все процедуры за минимальное время и при этом соблюсти все требования, прописываемые регламентами. Поэтому важно, чтобы рабочие бригады были снабжены современным производительным оборудованием.
Испытание температурой
Некоторые специалисты считают, что прописанные в регламентах методики гидравлических испытаний не достаточны для выявления всех слабых мест в теплосетях. Доказательством этому является тот факт, что даже проведённая самым тщательным образом опрессовка не спасает от образования течей в отопительный период.
В регулируемых системах теплоснабжения температура теплоносителя изменяется в зависимости от текущей погоды до 40 раз за отопительный сезон. При этом цикличные изменения длины трубопроводов составляют от 10 мм, что можно сравнить с мехами гармошки. Это может приводить к разрушению ветхих труб и нарушению герметичности резьбовых, фланцевых и сварных соединений.
В качестве альтернативы эксперты предлагает метод испытаний, имитирующий поведение системы в течение отопительного периода: в конце отопительного сезона в течение одной смены 5-6 раз резко (на 30-40°С) при рабочем давлении и циркуляции воды поднять и понизить температуру воды в сети.
Будут ли эффективны и найдут ли широкое применение в нашей стране новые методы тестирования трубопроводов, покажет время. Как минимум, тут предстоит ещё прописать соответствующую нормативную базу, легализующую такого рода испытания. Пока же для российских коммунальных служб более актуальна задача обновить парк инструментов для опрессовки, которые позволяли бы проводить гидравлические испытания в полном соответствии с регламентами. Уже этого будет достаточно, чтобы многократно снизить аварийность в отопительный период.
По материалам сайта http://www.c-o-k.ru/market_news/sovremennye-metody-ispytaniy-vnutridomovyh-setey-otopleniya
Испытания холодильных установок — Учебный центр Верконт Сервис
Необходимость испытаний холодильной системы на прочность определяется организацией-разработчиком холодильного оборудования, при этом возможны испытания как отдельных элементов, так и всей холодильной установки.
Ниже приведена последовательность действий при испытании на прочность установки в целом. Отличие испытания всей установки от испытаний отдельных элементов приведены ниже.
Давление для проведения испытаний на прочность указывается в технической документации конкретной холодильной установки и зависит от области её применения и типа хладагента.
При испытаниях холодильной установки на прочность используется следующее оборудование:
- Манометры (2 шт.) класса точности не ниже 1,5 с диаметром корпуса не менее 160 мм и шкалой с максимальным значением, равным 4/3 измеряемого давления;
- баллоны с азотом;
- редуктор с предохранительным клапаном, предназначенный для работы с азотом.
Испытания холодильного контура на прочность проводятся путем заполнения магистралей сухим (точка росы не выше -40 °С) азотом под давлением.
Испытания необходимо проводить в следующей последовательности:
- Установить один манометр после запорного вентиля у источника давления, а второй—в самой удаленной точке системы.
- В холодильном контуре открыть запорные вентили и при необходимости—электромагнитные клапаны—так, чтобы каждый участок контура имел возможность подачи и сброса азота.
- Отключить от контура все приборы КИПиА, а также другие элементы, не рассчитанные на давление испытания.
- Поднять давление в контуре до величины давления испытания. Подъем давления следует осуществлять со скоростью не выше 1 бар в минуту. При достижении давления, равного 0,3 и 0,6 давления испытания, а также при давлении испытания, необходимо прекратить повышение давления и провести промежуточный осмотр и проверку наружной поверхности контура.
- Под давлением испытания система должна находиться не менее 10 мин, после чего давление следует постепенно снизить до расчетного, также указанного в документации. Затем следует осмотреть наружную поверхность сосудов, аппаратов, трубопроводов, арматуры с проверкой герметичности швов и разъемных соединений мыльным раствором.
- Результаты признаются удовлетворительными, если во время испытаний не произошло разрывов, видимых деформаций, падения давления по показаниям манометра.
- При обнаружении утечек, деформаций, разрывов необходимо сбросить давление из контура, выполнить работы по устранению неисправностей и повторить предыдущие операции.
Испытания отдельных элементов холодильного контура проводятся в последовательности, указанной выше, но с учетом следующих мероприятий: - испытываемый элемент холодильного контура (сосуд, аппарат, трубопровод) должен быть отсоединен от других элементов с использованием металлических заглушек с прокладками, имеющими хвостовики, выступающие за пределы фланцев не менее, чем на 20 мм. Толщина заглушки указывается в документации.
- места расположения заглушек на время проведения испытания должны быть отмечены предупредительными знаками, и пребывание около них людей не допускается.
- использование запорной арматуры для отключения испытуемого сосуда (аппарата), трубопровода не допускается.
Контрольные вопросы:
- Кто принимает решение о проведении испытаний на прочность?
- Кто назначает давление для проведения испытаний на прочность?
- В какой последовательности проводятся испытания на прочность?
- Какие особенности существуют при испытании отдельного элемента холодильного контура?
Испытания системы на плотность.
Проверка холодильного контура на плотность (опрессовка) проводится в обязательном порядке для обнаружения мест возможных утечек хладагента, а также после завершения ремонтных работ, связанных с разгерметизацией холодильного контура.
Испытания на плотность проводятся раздельно по сторонам высокого и низкого давления. При равенстве давлений испытания для стороны высокого и низкого давления, например, для установок с воздухоохладителями, допускается проводить испытание на плотность всей системы.
Давление для проведения испытаний на плотность назначается организацией-разработчиком и указывается в технической документации. Оно зависит от области применения установки и типа хладагента.
При испытаниях холодильной установки на плотность используется следующее оборудование:
- Манометры (2 шт.) класса точности не ниже 1,5 с диаметром корпуса не менее 160 мм и шкалой с максимальным давлением, равным 4/3 измеряемого давления;
- баллоны с азотом;
- редуктор с предохранительным клапаном, предназначенный для работы с азотом.
Испытания холодильного контура на плотность проводятся путем заполнения магистралей сухим (точка росы не выше минус 40 °С) азотом под давлением.
При равенстве давлений испытания для стороны высокого и низкого давлений, последовательность испытаний такова:
- Установить один манометр был установлен после запорного вентиля у источника давления, а второй—в самой удаленной точке системы.
- В холодильном контуре открыть запорные вентили и, при необходимости, электромагнитные клапаны так, чтобы каждый участок контура имел возможность подачи и сброса азота.
- Поднять давление в контуре до величины давления испытания. Подъем следует осуществлять со скоростью не выше 1 бар в минуту. При достижении давления, равного 0,3 и 0,6 давления испытания, необходимо прекратить повышение давления и провести промежуточный осмотр и проверку наружной поверхности контура.
- Не производить никаких манипуляций с установкой в течение не менее 3 часов для выравнивания температур внутренней и наружной среды. Зафиксировать давление в контуре и температуру окружающей среды.
- Выдержать установку под давлением не менее 12 часов. По прошествии данного времени проверить давление в контуре. Изменений давления, кроме вызванных колебаниями температуры окружающей среды, быть не должно. Эти изменения определяются следующей зависимостью:
P1/P2=T1/T2,
где P1, P2 – абсолютные значения давления газа в контуре, бар, T1, T2 – термодинамическая температура газа в контуре, К.
- Если во время испытаний не произошло разрывов, видимых деформаций, падения давления по показаниям манометра, их результаты признаются удовлетворительными,.
- При обнаружении утечек, деформаций, разрывов необходимо сбросить давление из контура, выполнить работы по устранению неисправностей и повторить предыдущие операции.
Контрольные вопросы:
- В каких случаях проводят испытания на плотность?
- Кто назначает величину давления для проведения испытаний?
- Какова последовательность действий при проведении испытаний на плотность?
Испытание на вакуум (вакуумирование холодильного контура)
Вакуумирование холодильного контура проводится для удаления воздуха из агрегатов и трубопроводов и осушения холодильного контура после завершения ремонтных работ, а также после проведения испытаний на прочность и/или плотность.
Вакуумирование проводится до восстановления теплоизоляции, нарушенной при проведении ремонтных работ.
Использовать для вакуумирования компрессор холодильной установки категорически запрещено. Подавать напряжение на компрессор и проверять целостность его цепей в процессе выполнения работ по вакуумированию запрещено.
Исходное состояние холодильной установки перед вакуумированием зависит от вида выполненного ремонта и характеризуется изолированностью участка холодильного контура, на котором выполнялись ремонтные работы, от остальной схемы холодильной установки. В этой связи выбор сервисных штуцеров для подключения вакуумного оборудования, используемого в процессе вакуумирования, производится оператором в зависимости от участка, который требуется вакуумировать.
Для проведения вакуумирования применяют следующее оборудование:
- манометрический коллектор*;
- комплект гибких шлангов*;
- вакуумный насос;
- вакуумметр.
Оборудование, помеченное *, должно быть предназначено для работы с применяемыми в установке хладагентом и маслом и иметь соответствующую маркировку.
Порядок действий при ваккумировании:
- Произвести сборку схемы вакуумирования с таким расчетом, чтобы расстояние между вакуумным насосом и холодильной установкой было как можно меньшим, а диаметр соединительных шлангов как можно большим.
- Подключить манометрический коллектор к контуру и убедиться в отсутствии избыточного давления. При наличии избыточного давления, понизить его до атмосферного и проконтролировать его рост.
- Подключить вакуумный насос к сервисным штуцерам вакуумируемого участка холодильного контура.
- Подключить вакуумметр в наиболее отдаленной от места установки вакуумного насоса точке.
- Открыть вентиль перед вакуумным насосом и, при необходимости, электромагнитные клапаны так, чтобы каждый участок подлежащего вакуумированию контура имел возможность подключения вакуумного насоса.
- Включить насос и отвакуумировать холодильный контур до остаточного давления
- Остаточное давление следует принять 1 кПа (8 мм рт.ст.).
Вакуумирование рекомендуется проводить при нормальных температурных условиях в помещениях (20°С), в крайнем случае, при температуре в помещениях с холодильным оборудованием не ниже 5°С.
При низких температурах (ниже 2°С) рекомендуется проводить обогрев помещения, в которых размещен вакуумируемый участок контура.
При протяженных трассах трубопроводов рекомендуется разбить подлежащий вакуумированию участок на несколько подучастков (с помощью запорных вентилей) и проводить вакуумирование по подучасткам.
Запрещается подогревать участки холодильного контура открытым пламенем.
После достижения величины остаточного давления, следует продолжить вакуумирование в течении 18 часов. После этого следует закрыть вентиль и выключить вакуумный насос.
Если при низких температурах не удается достичь необходимой величины остаточного давления, то процесс вакуумирования следует чередовать с процессом наддува сухим азотом (отсоединяя насос) до абсолютного давления 2…3 бар.
При проведении испытаний холодильная установка должна находиться под вакуумом в течении 18 часов, при этом изменение давление в контуре должно фиксироваться не реже, чем через 1 час. Допускается повышение давления до 50% за первые 6 ч. В остальное время давление должно оставаться постоянным.
Если по окончании вакуумирования заправка установки хладагентом не планируется, то установку необходимо заполнить сухим азотом до абсолютного давления 2…3 бар.
Если в первые 3 часа выдержки под вакуумом давление резко повышается до уровня давления насыщенных паров воды, соответствующего температуре окружающей среды в помещении, а затем стабилизируется, то, значит, система герметична, но не достаточно осушена. Необходимо продолжить вакуумирование.
Если за 18 часов рост давления превысил 500 Па (5 мбар), давление не стабилизируется на уровне давления насыщенных паров воды при температуре окружающей среды и продолжает расти, то установка негерметична. Следует произвести поиск и устранить причину негерметичности контура. После этого повторить работы по вакуумированию.
Ниже приведена таблица зависимости давления насыщенных паров воды от температуры окружающей среды.
T,°C | 0 | 4 | 8 | 12 | 16 | 20 | 24 | 28 | 32 |
Р, Па | 610 | 812 | 1072 | 1401 | 1817 | 2337 | 2982 | 3778 | 4753 |
Контрольные вопросы:
- В каких случаях проводят вакуумирование холодильного контура?
- Какова последовательность действий при вакуумировнии?
- Какова величина остаточного давления при вакуумировании?
- Какова допустимая величина остаточного давления после завершения испытаний? В каких случаях оно превышает необходимую величину?
Заправка маслом
Большинство герметичных компрессоров не имеют средств определения уровня масла. Такие типы компрессоров проектируются для установки в системах, заправляемых определенным количеством масла при сборке на заводе. В случае небольшой утечки, когда количество потерянного масла может быть рассчитано, недостающее масло заправляется в компрессоре. При утечке большого количества масла компрессор должен быть демонтирован из системы, использованное масло необходимо слить и добавить строго определенное количество нового.
Слив масла из
герметичного компрессора
Полугерметичные и открытые (сальниковые) компрессоры оснащаются смотровыми окнами на картерах; во время работы уровень масла должен находиться в центре или немного выше центра смотрового окна. Низкий уровень масла может привести к недостаточному смазыванию деталей; а высокий – к масляным пробкам, повреждениям клапанов компрессора или переизбытку масла в системе.
Уровень масла может существенно варьироваться при запуске, когда жидкий хладагент находится в картере, поэтому проверять уровень масла следует во время работы компрессора после выхода холодильной установки на режим.
Некоторые виды хладагентов поглощаются маслом, и, чтобы избежать выделения хладагента, следует установить нагреватель масла или применять устройство для слива хладагента перед сливом масла.
Рекомендуется провести следующие процедуры:
- Закрыть запорные вентили на компрессоре,
- Включить нагреватель масла,
- Откачать газообразный хладагент (с помощью устройства слива хладагентов)
- Слить масло в специальные промаркированные емкости (при необходимости—с помощью азота.)
Заправка масла в герметичный компрессор
Перед заправкой масла компрессор необходимо отключить от системы с помощью запорных вентилей, масло должно быть удалено из отверстия на линии всасывания путем наклона компрессора. Перед процедурой следует точно отмерить необходимое количество масла. Тип и количество заправляемого масла можно узнать из инструкции по эксплуатации. Чтобы избежать чрезмерного поглощения хладагента маслом или выпускания хладагента, следует установить нагреватель для масла.
Заправка масла в полугерметичные и открытые (сальниковые) компрессоры
Метод для открытой системы
Если компрессор оснащен отдельным отверстием для заливки масла в картер, самый удобным способом заправки масла является отключение компрессора от системы и залив в картер необходимого количества масла. При отсутствии хладагента в холодильной системе, или если компрессор открыт для проведения ремонта, не требуется специальных мер предосторожности. После залива масла в картер, компрессор должен быть отвакуумирован во избежание попадания грязи и влаги в масло.
Пример масляного насоса
При наличии хладагента в компрессоре, следует закрыть всасывающий клапан компрессора и снизить давление в картере до уровня немного менее 0 бар. Затем отключить компрессор и закрыть его запорные вентили.
Существуют небольшие насосы для закачки масла в компрессоры. При необходимости закачка в работающий компрессор осуществляется через рабочее отверстие; можно использовать насос для заливки масла напрямую в картер, где не всегда возможна подача самотёком. Во время работы компрессора обратный клапан насоса препятствует утечке хладагента, позволяя создать достаточное давление для преодоления давления всасывания и закачать масло. В ситуации, когда отсутствует масляный насос и невозможно произвести заправку масла в картер, масло можно залить в компрессор с помощью сервисного клапана на линии всасывания.
Необходимо соблюдать максимальную осторожность, чтобы в компрессор не попал воздух.
Метод с применением азота и вакуума
Другим методом замены масла при ремонте, обслуживании или монтаже компрессора является использование азота и вакуумного насоса для заливки масла. Далее следует описание этого метода:
Замена масла (слив):
- Проверить систему на наличие утечек и при необходимости устранить их.
- Отключить компрессор от холодильного контура, используя функцию откачки или закрыв запорные вентили.
- При необходимости откачать оставшийся хладагент, используя подходящий метод откачки.
- Открыть отверстие картера для залива масла.
- Вставить 6-миллиметровую трубку из мягкой меди и опустить ее до дна картера.
- Заклеить отверстие клейкой лентой и придерживать медную трубу.
- Запустить в картер небольшое количество азота под низким давлением.
- Масло переместится в отдельную емкость.
- Утилизировать масло в соответствии с правилами по защите окружающей среды.
Замена масла (заправка):
- Подключить вакуумный насос к запорному вентилю или к сервисному штуцеру компрессора.
- Вставить свободный конец 6-миллиметровой медной трубы и/или шлангового соединения в канистру с маслом
- Включить насос.
- Масло поступит в компрессор через картер благодаря низкому давлению.
- Следить за уровнем масла в смотровом окне.
- Прекратить подачу масла.
- Измерить количество заправленного масла.
- Отвакуумировать компрессор
- Открыть запорные вентили компрессора
- Запустить компрессор
- Проверить уровень масла в смотровом окне
- Проверить систему на наличие утечек.
Примечание: Так как масла (особенно полиэфирные) поглощают влагу, необходимо использовать малые емкости с маслом. Запрещается хранить в открытом состоянии канистры с полиэфирными маслами, предназначенными для дальнейшего использования. |
Контрольные вопросы:
- Как заправлять масло в герметичный компрессор?
- Как производится заправка в полугерметичный и открытый (сальниковый) компрессоры?
Заправка хладагентом и хладоносителем
Заправка хладагентом.
В зависимости от установки, заправку холодильным агентом производят из цистерн или баллонов. Для этого в системе предусматриваются заправочный коллектор, специальный вентиль или ниппель. Заправку производят в линейный ресивер, жидкостный ресивер или в конденсатор.
Чиллеры, сплит-системы и моноблоки обычно заправляются маслом и холодильным агентом на заводе. Для проверки заправки, следует присоединить к ниппелю манометр и, учитывая температуру окружающего воздуха, проверить давление в системе. Установка находится при температуре окружающего воздуха, поэтому холодильный агент внутри находится при температуре окружающего воздуха. Температурная шкала соответствующего хладагента на манометре должна показать температуру окружающего воздуха. Если значения температуры, отличаются, то машина либо не заправлена, либо заправлена инертным газом.
Перед заправкой необходимо проверить, все ли манометры и приборы автоматизации на месте, сняты ли заглушки на сторонах нагнетания и всасывания компрессора. Смесевые неазеатропные и псевдоазеатропные холодильные агенты (R404A) заправлять можно только в жидкой фазе, баллон подключают к жидкостному ресиверу и установку заправляют жидким холодильным агентом.
Холодильные агенты, являющиеся моновоеществами (R134A, R22), и азеатропные смеси (R507) можно заправлять в жидкой и газовой фазах. При этом баллон присоединяют к всасывающей линии работающей холодильной установки, и компрессор отсасывает из баллона пары агента в систему.
Запрещается для ускорения заправки греть баллон газовой горелкой или ставить баллон в горячую воду. Холодильные установки заправляют по массе, для чего используют весы или, что менее предпочтительно, зарядные цилиндры. В документации по оборудованию должна быть указана масса заправки.
Для заправки из баллона, на резьбовой штуцер навинчивают заправочный шланг, второй конец шланга присоединяют к системе, но гайку до конца не завинчивают и ставят баллон на весы. Перед заправкой необходимо продуть шланг от воздуха, для чего открывают на баллоне вентиль, и воздух выдавливается холодильным агентом из шланга, после чего гайку завинчивают. Заправочные вентили или ниппели на холодильной установке открывают, и по шлангу холодильный агент перетекает из баллона в систему, по весам контролируют массу заправленного агента. Более грамотно использовать заправочный коллектор и заправочные весы.
При заправке большого количества хладагента массу заправки контролируют приблизительно. Например, если необходимо заправить 500 кг хладагента, то общую массу заправки делят на массу хладагента в баллоне и получают необходимое количество баллонов. При этом считается, что если заправлены все баллоны, то масса заправки составляет требуемую величину.
Примерная схема заправки выглядит следующим образом:
Перед заправкой хладагента необходимо поместить баллон на весы для контроля массы заправки хладагента
Заправка хладагента (жидкого и газообразного) в систему, находящуюся под вакуумом | |
---|---|
A,B,C,D | Закрыты |
1,2,4 | Подключить согласно изображению |
3 | Подключить к H или R |
L, H или R | Открыть (в среднем положении), L для заправки в газообразной фазе, R для заправки в жидкой фазе |
B | Открыт (вентиль баллона открыт) |
D | Открыт для заправки в жидкой фазе |
C | Открыт для заправки в газообразной фазе |
Запустить компрессор системы | |
Прекратить заправку | |
B, C, D | Закрыты (вентиль баллона закрыт) |
Проверить давление в системе | |
H, R | Открытое положение (сервисные порты отключены) |
D, C | Открыты |
Выравнивание давлениия | |
L | Открытое положение (сервисные порты отключены) |
D, C | Закрыты |
При заправке хладагентом удобно пользоваться линейкой для перевода значений давления в температуру насыщения хладагента.
Заправка хладоносителем.
Заправку систем хладоносителем производят через специально предназначенные для этого штуцеры или в бак хладоносителя. В крупных установках предусматривают специальные станции по приготовлению хладоносителя – баки объемом до 5 м3, оборудованные стационарными насосами для перекачивания хладоносителя в систему.
Приходящий в бочках гликоль следует наливать в указанной в технической документации пропорции во временную чистую емкость (бочку, бак). Затем на бочку навинчивают специальный ручной бочковой насос (например «Biltema») или используют обычный бытовой насос типа «Малыш», который применяют для добавки в емкость чистой воды, хорошо размешивают и тем же насосом по шлангам заправляют в систему. При необходимости добавки ингибиторов, их необходимо внести в раствор, строго следуя указаниям технической документации.
При разведении гликолей следует руководствоваться следующими правилами:
- нельзя закачивать в систему гликоль, а потом воду, закачивать можно только готовый раствор;
- необходимо предусмотреть меры по защите площадки от проливов гликолей, не допускать проведения работ вблизи открытого пламени и курения, приготовить средства пожаротушения,
При заправке системы растворами солей, таких как СаС12 , следует соблюдать следующие правила: - Приготовленному раствору необходимо дать отстояться;
- Отбор готового раствора не следует делать из нижней точки во избежание попадания загрязнений, оставшихся после отстаивания.
- Насос для заполнения требуется обеспечить фильтром на всасывании.
- Необходимо применять насос, пригодный для работы с агрессивной средой.
Контур оборотного водоснабжения заполняют из водопровода по подпиточной трубе. Как правило, на трубопроводе подпитки устанавливается система водоподготовки. При заполнении в зимнее время системы оборотного водоснабжения обогреватели поддонов конденсаторов и градирен, встроенных в испарительные конденсаторы насосов, необходимо включить заранее.
Контрольные вопросы:
- Как производится заправка холодильной системы хладагентом?
- Как производить заправку системы хладоносителем?
Литература
- Полевой А. А. Монтаж холодильных установок: Учеб. Пособие для вузов. – СПб.: Политехника, 2005. – 259 с.: ил.
Проверка электрооборудования.
После завершения монтажа электрооборудования необходимо проверить правильность подключения согласно технической документации.
Проверка осуществляется методом прозвонки. Как правило, данную проверку осуществляют два человека – один устанавливает временную перемычку в щите управления, второй, находясь непосредственно у компонента, проверяет, замкнуты ли кабели. В случае, если кабели подключены от соответствующего агрегата или прибора в нужные клеммы, временную перемычку снимают и переходят к следующим кабелям.
После проверки правильности подключения, проверяют правильность направления вращения валов трехфазных электродвигателей. У крупных компрессорных агрегатов в щитах предусмотрена защита от неправильного направления вращения, но на этом этапе муфты компрессора и электродвигателя разъединены, электродвигатель запускают отдельно. В документации изготовителя оборудования всегда указано правильное направление вращения электродвигателя, в случае, если при пробном запуске двигатель крутится в обратную сторону, следует перекинуть фазы в щите или в клеммной коробке электродвигателя и внести изменения в монтажную документацию. Направление вращения особенно важно для винтовых и спиральных компрессоров, для поршневых компрессоров направление вращения не имеет значения.
Направление вращения вентиляторов определяется при кратковременном пуске, для определения направления вращения электродвигателя герметичного насоса необходимо снять пластиковую защитную муфту в месте стыковки вала насоса и электродвигателя. Кратковременный пуск без среды не повредит центробежному насосу. Подав напряжение, по вращению вала определяют, крутится ли двигатель в направлении, указанном производителем насоса.
При проверке направления вращения полугерметичного винтового компрессора следует руководствоваться следующей последовательностью действий:
- Установить манометры на всасывании и нагнетании.
- Замкнуть магнитный пускатель (контактор) компрессора вручную и удерживать не более 2 с. Если после ручного отключения катушки контактора компрессор продолжает работать, немедленно отключить питание установки.
- Во время краткого пуска контролировать давление по манометрам. Если давление по манометру всасывания падает, а по манометру нагнетания увеличивается, то компрессор подключен правильно. В противном случае необходимо поменять направление вращения.
Контрольные вопросы:
- Какие проверки электрооборудования необходимо проводить?
Пневматические испытания под давлением — Сантехника и HVAC
В новой системе или при ремонте / обновлении стыки остаются неокрашенными до завершения испытания под давлением.
Грег Скривнер
Пневматические испытания под давлением проводятся на холодильных системах и оборудовании на заводе, где они производятся, при установке и в любое время в течение их срока службы, когда открыт трубопровод хладагента. Значит, сделано много.
Почему мы это делаем?
Предпочтительный метод испытания компонентов давлением — гидростатический с использованием воды.Фактически, большинство холодильных емкостей испытывают на заводе под гидростатическим давлением, а затем сушат (надеюсь) перед установкой в систему охлаждения. Это связано с тем, что гидростатические испытания менее опасны и часто могут быть выполнены более точно. Пневматическое испытание под давлением создает ситуацию, когда во время испытания в системе трубопроводов накапливается значительное количество энергии.
В полевых условиях испытание холодильных систем гидростатическим давлением невозможно, поскольку влажность очень вредна для работы и эффективности системы.Достаточно сложно удалить влагу, которая попадает в наши системы из воздуха во время установки, не говоря уже о намеренной заливке воды в трубопровод для проверки.
Несмотря на этот факт, у меня было два случая в моей жизни, когда должностное лицо кодекса было довольно непреклонно категорически запрещало пневматические испытания. В настоящее время в Альберте вы должны предоставить письмо в орган, описывающее вашу процедуру тестирования и причину, по которой требуется пневматическое испытание.
Почему это опасно?
Когда газ сжимается, вся энергия, используемая для его сжатия (за вычетом некоторых потерь, таких как трение), сохраняется в системе трубопроводов.Это может быть большое количество энергии, и в случае разрыва или большого отказа эта энергия может быть высвобождена очень быстро.
Это повторное расширение в некоторой степени отличается от того, что происходит при утечке хладагента, поскольку утечки хладагента имеют самоограничивающееся качество. При быстром выпуске хладагента жидкость быстро испаряется и охлаждает оставшуюся жидкость, что снижает давление в системе. Это не означает, что разрывы холодильной системы не опасны, но следует проявлять особую осторожность при проведении пневматических испытаний.
Существует два типа рисков, которые следует учитывать, и оба четко определены в стандарте Американского общества инженеров-механиков (ASME) PCC-2 «Ремонт оборудования трубопроводов под давлением». Это может быть взрыв, вызванный быстрым расширением газа, и могут быть фрагменты материала, брошенные в результате разрушения.
PCC-2 предоставляет методы для расчета расстояний радиуса взрыва и выброса осколков, как показано на рис. 1.
Рис. 1: Пример результатов расчета PCC-2.
Доступны и другие методы. Затем во время испытания под давлением из опасной зоны проводится эвакуация, чтобы никого не травмировать. Возникают две проблемы: во-первых, на больших системах расстояния могут быть большими (нам пришлось закрыть дороги!), А эвакуация — это неприятность. Во-вторых, как найти утечку, если нельзя подойти к системе?
Процедуры и проблемы
Испытания под давлением обычно проводятся с использованием сухого азота или другого инертного газа. Воздух иногда используется в больших системах, особенно в системах с аммиаком, когда проблемы с влажностью не столь заметны.Однако для систем с галогенуглеводородом и CO2, где критически важно минимизировать содержание влаги в системе, воздух не является хорошим выбором.
О том, сколько времени нужно оставить для испытания под давлением, идет много споров. ASME B31.5, стандарт для трубопроводов под давлением основного хладагента, требует всего 15 минут при давлении на 10 процентов выше расчетного. CSA B52, канадский код безопасности холодильного оборудования, требует двух часов работы при расчетном давлении. Верно, что чем дольше проводится испытание под давлением, тем больше вероятность обнаружения небольших утечек.Однако верно и то, что чем дольше вы покидаете испытание под давлением, тем больше вероятность того, что вас введут в заблуждение какие-либо мелкие изменения.
Существует миф о том, что давление азота во время опрессовки не зависит от внешних факторов. Это просто неправда. На азот, как и на другие газы, влияет температура. Это может быть незначительно, но учтите, что это часто будет меняться.
Рис. 2 иллюстрирует этот момент, показывая, как давление азота зависит от температуры в фиксированном объеме.При начальном испытательном давлении 300 фунтов на квадратный дюйм при 75 ° F давление упадет примерно до 280 фунтов на квадратный дюйм при 40 градусах F.
Рис. 2: Изменение испытательного давления при изменении температуры.
Это изменение явно немаловажно. Однако вы можете использовать закон идеального газа, чтобы оценить или предсказать, какое изменение будет, и, поскольку объем не изменится, вы можете использовать упрощенную версию закона ниже.
Хотя это определенно может помочь, я могу засвидетельствовать тот факт, что не всегда так легко определить, какая температура на самом деле.Для небольшой системы это можно сделать. Но представьте себе большую сложную сеть трубопроводов, в которой часть трубопроводов находится на открытом воздухе, часть находится в отапливаемом здании, часть — в морозильной камере, а часть — в безусловном пространстве. Какая температура?
Теперь, когда мы понимаем, что эти испытания под давлением имеют ограничения, особенно при попытке использовать небольшие изменения давления для определения утечки, возникает вопрос: сколько времени достаточно для испытания?
Существует реальный риск признания теста недействительным, если вы не выполняете его надолго.Раньше я рекомендовал длительные испытания под давлением, но за последние несколько лет я несколько изменил свой подход, и хотя в некоторых случаях 15 минут могут быть слишком короткими, обычно этого достаточно, чтобы найти утечку. Двухчасовое испытание под давлением, необходимое для CSA B52, можно использовать для завершения обязательной проверки на герметичность (см. Ниже).
В отношении последнего утверждения есть предостережение, поэтому, прежде чем вы будете слишком взволнованы тем, что можете спешить через испытание под давлением, вспомните, что 15-минутное испытание под давлением должно проводиться при давлении от 110 до 120 процентов от расчетного.Для хладагента R410A это означает, что испытание должно проводиться под давлением почти 500 фунтов на квадратный дюйм. Более высокое давление означает, что предохранительные устройства и некоторые компоненты необходимо снять, а затем повторно установить в системе после завершения испытания.
В этом проекте трубопровод изолируется после завершения испытания под давлением.
Испытание на герметичность и давление
Другим требованием ASME B31.5 является испытание на герметичность, которое существенно отличается от испытания под давлением. Проверка на герметичность может представлять собой проверку мыла или использование течеискателя с индикаторным газом в азоте.Необходимо проверить каждое соединение в системе, а это означает, что изоляция не может быть завершена на 100 процентов до завершения испытаний.
Последний интересный момент касается трубопроводных сетей и сосудов, испытываемых давлением зимой, особенно тех, в которых используется сталь (почти все сосуды высокого давления). Если температура окружающей среды ниже минимальной расчетной температуры металла (MDMT) стали, она не должна находиться под расчетным давлением. В некоторых случаях это означает, что необходимо накапливать и нагревать трубопроводы для испытаний.Если вы вспомните подобное обсуждение в статье давным-давно, этот обогрев также необходим для эффективной эвакуации.
При проведении испытаний на пневматическое давление есть о чем подумать, больше, чем большинство из нас когда-либо учили в школе!
3 Тесты на утечки хладагента кондиционера
3 Тесты на утечки хладагента кондиционераВаша местная компания по ОВК в Мур, штат Оклахома-сити
Автор: администратор, После того, как технический специалист ОВК проверил вашу систему, он обнаружил, что хладагента недостаточно .Следует ли утилизировать систему и купить новую? Когда возникает такая ситуация, A-Better Heat and Air Conditioning рекомендует эти 3 теста на утечку хладагента, чтобы решить проблему. Посмотрите, как проверка утечки хладагента может помочь вам сэкономить копейки.- Проверка красителя
- Электронное обнаружение утечек
- Тест на утечку азота и пузырьков
| Обучение работе с вакуумом для кондиционирования воздуха
Правильная установка и опорожнение системы кондиционирования воздуха начинается с качественной установки и надлежащей практики прокладки трубопроводов.
Получите комплект!
Короткое замыкание во время установки комплектов медных линий приводит к потере времени во время откачки, потенциальным утечкам хладагента, плохому возврату масла, загрязнению системы и избыточному времени, необходимому для откачки.
Надлежащая эвакуация после первоначальной установки или после обслуживания, если система была открыта в атмосферу критично для правильной работы система кондиционирования воздуха. Эвакуация — это двухэтапный процесс: дегазация и обезвоживание.Дегазация удаляет неконденсируемые вещества, которые вызывают повышенное давление напора и увеличивают эксплуатационные расходы. Там, где часто бывают высокие температуры, неконденсирующиеся вещества в сочетании с влагой также вызывают появление масла. отказ, снижение производительности и повышенный износ компрессора и потенциал отказ. Потери, связанные с неправильной эвакуацией, могут быть очень высокими.
Влага — вторая проблема. Влага тормозит масло POE в HFC системы (например, R410a), вызывающие преждевременный выход из строя масла. Потому что POE выходит из строя на его основные компоненты, он может засорить дозирующее устройство и загрязнять наборы линий.Это может привести к необходимости полной системы замена. Влага хладагента и минеральных масел образуют кислоты, которые вызвать отказ системы из-за медного покрытия и повреждение компрессора обмотки.
Вакуумметр используется для определения уровня атмосферы (дегазации и обезвоживания) в системе.
Быстрое и глубокое вакуумирование кондиционера или холодильной системы просто сводится к правильным действиям, включая правильную установку и сборку, предотвращение попадания влаги во время изготовления и, конечно же, правильные шланги и датчики для измерения уровня дегазации и обезвоживания.Когда влага (жидкость) попадает в систему или конденсируется, единственный способ ее удаления — это пар. Когда дело доходит до вакуумирования системы, таким способом можно удалить лишь небольшое количество влаги. «Нецелесообразно удалять большие количества воды с помощью вакуумного насоса, так как кипящая вода производит большое количество водяного пара. Один фунт воды (около 1 пинты) производит около 867 кубических футов водяного пара при температуре 70 ° F». (1) Поэтому, как сказал Дэвид Бойд из Appion, «Держите его чистым, сухим и плотным».
- Трубки должны быть чистыми и сухими на протяжении всей установки, влажность, грязь и другие загрязнения могут нарушить работу системы и значительно увеличить время, необходимое для вакуумирования.
- Стержни клапанов следует снимать с помощью инструмента для прокладки стержней, рассчитанного на вакуум, чтобы обеспечить продувку системы азотом и возможность закрытия системы, когда это возможно, во время установки трубопровода.
- Трубогибы следует использовать для минимизации количества фитингов и уменьшения внутренних ограничений. Фитинги требуют резки труб, очистки, удаления заусенцев, сборки, пайки, продувки азотом и проверки на герметичность. Лучше всего полностью исключить фитинги.Хороший набор трубогибов окупится в кратчайшие сроки.
- Обрезанные трубы следует развернуть или удалить заусенцы. Внутренние ограничения могут вызвать эрозию трубопровода, снижение скорости всасываемого газа и плохой возврат масла. Даже несколько неправильно смонтированных фитингов могут снизить качество установки.
- Азот следует продувать через трубопровод во время установки и во время пайки, чтобы избежать попадания загрязнений и влаги в трубопровод, а также во избежание образования оксидов меди во время пайки.Используйте откалиброванный расходомер, чтобы избежать избытка азота. Промывание системы азотом во время установки значительно сократит время вакуумирования.
- Установите фильтр-осушитель для удаления следов влаги после вакуумирования. Небольшое количество влаги может скапливаться под компрессорным маслом или, в случае POE, связываться с самим маслом. Осушитель, оснащенный индикатором влажности, установленным непосредственно перед дозирующим устройством, эффективно удаляет следы влаги и помогает быстро выявить потенциальные проблемы с влажностью.Установка осушителя внутри рядом с испарителем лучше защитит дозирующее устройство, обеспечит визуальное присутствие 100% жидкости и предотвратит преждевременное ржавление осушителя.
Продувка
После установки трубопроводов и различных компонентов необходимо убедиться в наличии потока через всю систему путем продувки сухим газом, например, сухим азотом, из линии жидкости на сторону всасывания. система. При промывке не только удаляются мелкие капли воды (если они есть), но и собирается часть влаги из системы.
Испытание под давлением с использованием сухого газа
Испытание под давлением используется для проверки герметичности с использованием сухого газа, например, сухого азота. Мы никогда не надеемся найти утечки в вакууме. (Хотя это действительно происходит.) Когда воздух просачивается внутрь, появляется влага, на удаление которой могут уйти часы, если количество слишком велико. Испытание давлением с температурной компенсацией, подобное тому, которое имеется в цифровых коллекторах серии Testo, сделает процесс быстрым и эффективным. Однако, если вы используете цифровой коллектор, такой как Fieldpiece SMAN, утечки также будут очевидны просто из-за высокого разрешения датчиков давления.При установке типичной жилой системы тест можно выполнить и проверить примерно за 15 минут. Выполнение этого теста снова приведет к накоплению некоторой дополнительной влаги, которую не нужно будет удалять во время процесса вакуумирования. При выпуске этого газа под высоким давлением не сбрасывайте давление полностью до атмосферного. Понизьте его примерно до 1 фунта на кв. Дюйм. поэтому воздух не может попасть обратно в систему.
Проверьте свой вакуумный насос (пустое тестирование)
Присоедините микронный манометр непосредственно к вакуумному насосу через соединение 1/4 «и убедитесь, что насос способен достигать уровня вакуума 100 микрон или меньше.Насос хорошего качества легко достигнет уровня ниже 50 микрон. Заглушки насоса печально известны утечками, поэтому не полагайтесь на одну из них для изоляции вакуумного насоса. Используйте основные инструменты, чтобы изолировать насос и шланги, тем самым минимизируя вероятность проникновения газа через шланги. Помните, что даже самые лучшие вакуумные шланги будут протекать, поэтому изоляция необходима. Если ваша помпа не может достичь 100 микрон или меньше, замените масло на высококачественное масло с низким давлением паров, такое как Appion Tezom.Часто требуется несколько замен масла для удаления значительного количества влаги из мокрого насоса. По сравнению с поломкой системы масло дешево меняют часто. Если насос по-прежнему не создает глубокого вакуума, возможно, пришло время заменить или отремонтировать.
Примечания по газобалласту (при наличии)
Воду можно удалить из системы только в виде пара. Если атмосфера, которую вы удаляете из холодильной системы, насыщена влагой, когда эта влага попадает в насос, она находится в форме пара, то есть находится в состоянии равновесия с воздухом в системе.Это состояние равновесия и подразумевается под термином «балласт». (что-то, что дает стабильность)
Балласт, когда он открыт, вводит свободный воздух в насос во время такта нагнетания, чтобы поддерживать эту влажность в равновесии. Если газовый балласт закрыт, давление, создаваемое во время такта нагнетания, будет конденсировать водяной пар и сбрасывать влагу в масло. Открытие балласта во время первоначального опускания влажной системы поможет предотвратить конденсацию внутри насоса.(держите его открытым, пока не достигнете 15 000–10 000 микрон)
Влага убивает масло в вакуумном насосе. Когда масло влажное, давление пара увеличивается до точки, при которой невозможно создать глубокий вакуум. (Влажное масло — это белое масло). Если масло влажное, дешевле и быстрее заменить масло, чем позволить газовому балласту отработать это. Эта влага также повредит ваш насос, если ее оставить, поэтому всегда меняйте масло, если вы работаете с влажной системой. Причина, по которой я рекомендую всегда менять масло, заключается в том, что через маленькое неосвещенное смотровое стекло трудно увидеть, насколько оно мутное.
Открытый балласт газа не позволяет насосу достичь предельного уровня вакуума и должен быть закрыт после достижения 15 000–10 000 микрон. Используемый газовый балласт используется только во время черновой обработки и необходим только при наличии влаги в системе.
Одна из наиболее важных вещей, которую вы можете сделать, — это всегда продувать азотом или продувать систему перед выполнением вакуумирования. Это означает проталкивание азота через систему с одной стороны на другую, БЕЗ значительного повышения давления в системе.Это вытолкнет пары влаги, но не попадет в систему в жидком виде.
Если вы производите продувку во время сборки и продуваете систему азотом перед откачкой, вам, скорее всего, вообще не потребуется использовать газовый балласт. Газовый балласт эффективен только для удаления небольшого количества влаги, поэтому очень влажная система потребует частой замены масла, если вы хотите быстро выполнить работу.
Evacuation
Системы кондиционирования и охлаждения предназначены для работы только с маслом и хладагент, протекающий через них.Когда обычная система установлена и / или обслуживается, воздух и влага попадают в систему. Кислород, азот и влага (все это составляет наш воздух или атмосферу) вредна для работы системы. Удаление воздуха и других неконденсируемых веществ называется дегазацией и обезвоживанием влаги. Удаление обоих обычно называют эвакуацией.
Предполагая, что стержни клапанов сняты, подсоедините шланги большого диаметра, рассчитанные на разрежение, к задней части стержневых инструментов (не используйте боковые порты стержневого инструмента для вакуумирования) как на верхней, так и на нижней стороне системы, чтобы обе стороны могли быть сняты одновременно.Хотя сначала может показаться нелогичным использование шлангов большого диаметра, ценность быстро становится очевидной после начала откачки. Шланги 1/2 дюйма сокращают время, необходимое для откачки, в 16 раз по сравнению с типичными шлангами диаметром 1/4 дюйма, используемыми в большей части промышленности. Шланги большего размера уменьшают трение и, следовательно, увеличивают скорость проводимости. Скорость проводимости шланга 1/4 дюйма настолько мала, что его никогда не следует использовать для откачивания. По возможности избегайте шлангов диаметром 1/4 дюйма для откачивания, поскольку они требуют слишком много времени и затрат, чтобы быть эффективными.Подсоедините шланги непосредственно к вакуумному насосу с помощью латунного тройника с развальцовкой или вакуумного коллектора. Не используйте коллекторы, не оборудованные кольцевыми уплотнениями, поскольку набивка часто удерживается под давлением, но протекает в вакууме. Сведите к минимуму количество подключений, а количество точек доступа — по максимуму. Другими словами, подключайтесь к как можно большему количеству мест в системе, но исключите ненужные шланги или фитинги. Если доступны только две точки доступа, подключайтесь напрямую к вакуумному насосу, устраняя необходимость в коллекторе.
Установите высококачественный вакуумметр с медной линией или латунным соединителем непосредственно на сердечник, установленный на всасывающей линии. Это позволит полностью изолировать эвакуационную установку (шланги и фитинги) от системы во время «испытаний на постоянное давление», во время которых будет измеряться качество вакуума.
Начните со свежего и сухого масла для вакуумного насоса. Масло для вакуумного насоса чрезвычайно гигроскопично (впитывает влагу), поэтому использование свежего масла значительно ускорит процесс. Если ваш насос оборудован газовым балластом, открывайте балласт до достижения уровня 10 000 микрон.В узких пределах целью вакуумного балласта является предотвращение конденсации водяного пара в насосе во время такта нагнетания. Вообще говоря, лучше и быстрее заменить масло, чем ждать, пока газовый балласт удалит лишнюю влагу из масла во время работы насоса. Влага разрушает масло вакуумного насоса, увеличивая давление пара настолько, что невозможно создать высокий уровень вакуума. Насос не может создавать более высокий вакуум, чем давление пара его герметика.Если сомневаетесь, замените!
1-е испытание на стойкость
Создайте вакуум до тех пор, пока не будет достигнут уровень 1000 микрон (при использовании шлангов большого диаметра и основных инструментов откачка линии и змеевика испарителя займет менее 15 минут для типичной жилой системы с повышенным давлением). до 5 тонн). Изолируйте вакуум с помощью стержневых инструментов, чтобы насос продолжал работать, и запишите скорость утечки (примерно после 5-минутного периода стабилизации), показанную вакуумметром, если таковой имеется. Скорость утечки просто определяется падением вакуума за единицу времени и обычно отображается в микронах в секунду.Повышение давления после короткого периода стабилизации указывает на то, что в системе все еще присутствует влага или имеется небольшая утечка в системе.
2-е испытание на стойкость
Откройте основные инструменты и позвольте системе продолжить процесс вакуумирования до тех пор, пока уровень вакуума не достигнет 500 микрон или меньше. Затем повторите «испытание стоя», чтобы определить, произошло ли уменьшение скорости утечки после стабилизации вакуума. Если утечки нет, то при 2-й скорости утечки в системе скорость утечки должна быть значительно меньше первой, что указывает на прогресс в работе по обезвоживанию.
Определение разницы между влажностью и утечкой в системе
Если скорость утечки не уменьшилась, могут произойти две вещи:
1) Система все еще загрязнена влагой. (Возможно, застрял под компрессорным маслом.)
2) В системе есть небольшая утечка, которая не была обнаружена при первоначальном испытании под высоким давлением. (Некоторые утечки более очевидны под вакуумом, чем под давлением.)
Высококачественный вакуумметр с высоким разрешением, подобный тем, что можно найти на этой странице «Измерение вакуума», может указать на утечку намного быстрее, чем манометр, из-за чувствительности прибора.Хотя микронный манометр вполне подходит, проверка на утечку в вакууме не является приемлемой практикой по сравнению с испытанием под давлением, поскольку влага втягивается в систему во время процесса вакуумирования. Если вы обнаружите утечку под вакуумом, прервите вакуум с помощью сухого азота и попытайтесь найти утечку под давлением. ЗАПРЕЩАЕТСЯ открывать систему в атмосферу под вакуумом! Это отнимает у вас все время и усилия до этого момента.
Если в системе есть утечка, вакуумметр будет продолжать подниматься до тех пор, пока не будет достигнуто атмосферное давление.Однако, если система герметична, но все еще содержит влагу, повышение будет выравниваться, когда давление пара в системе выровняется, как правило, между 20 000 и 25 000 микрон в диапазоне от 72 до 80º F. В этот момент показания вакуума станут стабильными. (Примечание: система, которая продолжает выравниваться на уровне 3500-4500 микрон, возможно, превратила влагу в систему в лед. В этом случае, возможно, придется повысить температуру системы с помощью внешнего источника тепла, чтобы удалить влагу из системы.)
Если система показывает влажность, многократная откачка с продувкой азотом значительно снизит количество влаги в системе.Чтобы выполнить эту процедуру, уменьшите давление в системе до 1000–2500 микрон. Изолируйте вакуумный насос с помощью основных инструментов и отсоедините вакуумный шланг от стороны низкого давления системы. Прервите системный вакуум с помощью азота, введенного в боковое отверстие стержневого инструмента. Прервите вакуум азотом до давления, эквивалентного атмосферному давлению (760 000 микрон), затем продуйте систему азотом под давлением 1–3 фунта на квадратный дюйм. от верхней к нижней стороне, позволяя ей выходить через открытый порт стержневого инструмента.Не создавайте давление в системе, так как это не приведет к удалению влаги. Нет необходимости создавать давление в системе, если вы не выполняете проверку на утечку. Повышение давления в системе фактически вызовет выпадение воды из азота, подобно тому, как это происходит в сжатом воздухе в воздушном компрессоре. Азот не поглощает воду, но увлекает ее и помогает ей выйти из системы, позволяя жидкой воде нагреваться, испаряться и увеличивать давление водяного пара без введения дополнительной влаги в систему.Если система высыхает, вы заметите, что быстро достигается более глубокий уровень вакуума, что указывает на прогресс в работе по обезвоживанию. При желании или необходимости повторите этот процесс, пока влага не будет удалена. Обычно требуется не более трехкратного вакуумирования с зачисткой. Если заметного прогресса не достигнуто во время этого процесса, повторите продувку азотом для удаления жидкой влаги, которая может присутствовать. Если обнаружена утечка, ее необходимо устранить до завершения эвакуации.
После второго испытания на падение проверьте состояние масла в вакуумном насосе.Масло молочного цвета содержит влагу и не позволяет достичь окончательного вакуума из-за увеличения давления пара и потери герметичности, вызванной влажностью масла. Если масло влажное, замените его чистым сухим маслом. Если сомневаетесь, замените!
Вакуум для чистовой обработки
После второго испытания на стойкость дайте вакуумному насосу поработать до тех пор, пока в системе не станет предпочтительно менее 200 микрон. (С хорошим насосом 50–100 микрон легко достижимо.) Изолируйте вакуумную установку с помощью основных инструментов и дайте системе постоять в течение 15–30 минут.Если уровень в микронах не превышает 500 микрон, откачивание завершено. Если давление поднимется выше 500, снова откройте керновые инструменты и дайте возможность продолжить откачку. Опыт и / или микронный манометр с высоким разрешением позволят сократить время оценки.
После завершения вакуумирования, если вы работаете с новой установкой, держите насос изолированным и откройте (взломайте) линию всасывания, пропуская небольшое количество хладагента в систему, медленно доводя систему до положительного давления.(Примечание: когда вакуумметр показывает «высокое давление», вы превышаете 20 000 микрон, но все еще находитесь под отрицательным давлением.) Поскольку манометр может выдерживать давление до 500 фунтов на квадратный дюйм, вам не нужно беспокоиться о повреждении микронного манометра из-за избыточного давления. Когда всасывающая линия полностью откроется, откройте сервисный клапан для жидкости, установите стержни клапана на место и снимите вакуумметр и инструменты для стержней. (Примечание: хладагент может привести к срабатыванию вакуумного датчика, если он находится под вакуумом, или может работать неустойчиво после удаления до тех пор, пока пары хладагента не выйдут из датчика.Датчик откалиброван для воздуха, и атмосфера хладагента будет влиять на показания.) После установки стержней и снятия стержневых инструментов прочистите шланги коллектора и установите датчики, чтобы завершить ввод системы в эксплуатацию.
При обслуживании и существующей установке устраните вакуум с помощью необходимого системного хладагента перед снятием основных инструментов, затем продолжите процедуру ввода в эксплуатацию, как того требует производитель.
Последние мысли
Мы рекомендуем Accutool BluVac по нескольким причинам.Он имеет ряд преимуществ по сравнению со всеми другими вакуумметрами. Проблемы с загрязнением масла, калибровкой в полевых условиях и рабочим процессом были решены. При разрешении 0,1 микрона вы можете легко увидеть, набирает ли популярность вакуумный насос, нужно ли менять масло в вакуумном насосе, а когда манометр изолирован, падение вакуума и предельное давление в системе. Из-за разрешающей способности BluVac мы настоятельно рекомендуем вам использовать инструменты и шланги для работы в вакууме. Все шланги протекают, и при разрешении 0,1 микрона это будет очень заметно.
Для правильного выполнения эвакуации также обратите внимание на комплект RapidEvac от TruTech Tools. При использовании, как показано, он сократит время эвакуации в 16 раз из шлангов 1/4 дюйма. Экономия рабочей силы при использовании этого комплекта очень значительна и сократит потребность в рабочей силе и время простоя обслуживаемого оборудования.
Ищете идеальную вакуумную установку? Не смотрите дальше, у нас это есть. ВАКУУМНАЯ УСТАНОВКА
Ссылки:
(1) Холодильная техника кондиционирования воздуха, 5-е издание Авторские права 2005
(2) Обзор вакуума для инженеров по обслуживанию 1988
Советы по проверке кондиционеров | KnowYourParts
Лучший способ начать любой ремонт кондиционера — это тщательно осмотреть его компоненты, поскольку проблема может возникать по разным причинам.После проверки таких компонентов, как ремни, шланги и соответствующие соединения, следующим шагом является визуальный осмотр компрессора кондиционера. Для некоторых транспортных средств это может быть непросто, потому что их можно хорошо спрятать.
Так что вы хотите искать? Что ж, вам нужно проверить отсутствие утечек масла и проверить сцепление и подшипник на предмет хорошего состояния.
Примечание : Для выполнения подробных проверок вам может потребоваться приобрести гибкое автомобильное зеркало для осмотра, которое позволит вам заглянуть в некоторые из этих труднодоступных мест и узнать, что происходит в той или иной конкретной области.
Далее проверьте саму муфту компрессора. Вы обнаружите, что есть воздушный зазор между муфтой компрессора и поверхностью подшипника. Проверьте рекомендуемый зазор в воздушном зазоре муфты. Чтобы измерить воздушный зазор, вам нужно вставить щуп между муфтой компрессора и поверхностью подшипника. Убедитесь, что он не тоньше 0,014 дюйма и не больше 0,030 дюйма.
Знаете ли вы… Большинство отказов компрессора вызвано потерей смазочного материала и / или хладагента.Повторные отказы обычно возникают из-за загрязнения системы (шлам или металлические частицы от предыдущего отказа компрессора).
Денежный тест
Если вам просто нужно провести быструю пробную проверку, а у вас нет доступа к служебной информации, попробуйте денежный тест. Это старое эмпирическое правило — использовать никель и десять центов. Если воздушный зазор тоньше десятицентовика, значит, он слишком тонкий. Если вы обнаружите, что никель легко входит и выходит из воздушного зазора, вы можете держать пари, что сцепление полностью изношено. Хотя это простой и быстрый тест, чтобы получить наилучшие результаты, вы всегда хотите использовать соответствующую служебную информацию и проверять ее так, как того хочет производитель автомобиля.
В муфте
Компрессоры с ременным приводом имеют магнитную муфту на входном валу, которая включает и выключает компрессор для управления охлаждением. При необходимости сцепление можно заменить отдельно. Если компрессор вышел из строя, заменяемый блок может поставляться или не поставляться с установленным новым сцеплением. Мы рекомендуем заказать новое сцепление, если оно не входит в комплект.
Проблемы со шлангами
Одна из проблем, с которыми сталкиваются технические специалисты, — это проблема замены шлангов кондиционера после отказа компрессора.
Металлический мусор, который попадает в систему кондиционирования при выходе из строя компрессора, может заблокировать диафрагмы и, возможно, повредить новый компрессор при его установке. Поэтому важно удалить весь мусор из системы, чтобы новый компрессор не постигла та же участь.
Хотя большая часть мусора попадает в конденсатор, некоторые могут перемещаться отсюда в другие части системы или отбрасываться назад во всасывающий шланг из впускного отверстия компрессора.
Конденсаторы змеевикового типа с трубками большого диаметра обычно можно очистить путем промывки одобренным промывочным химическим средством.Но конденсаторы с параллельным потоком или конденсаторы с очень маленькими трубками может быть невозможно очистить, требуя замены для устранения возможных загрязнений.
Что касается шлангов хладагента, замена всасывающего и нагнетательного шлангов не требуется, если их можно тщательно промыть и очистить. Однако шланги, которые содержат глушители или диафрагмы, обычно не подлежат очистке и должны быть заменены. Установка защитного экрана на конце всасывающего шланга, который присоединяется к компрессору, и / или установка встроенного фильтра для улавливания любого остаточного мусора, который мог быть пропущен, также рекомендуется для дополнительной защиты от будущего отказа компрессора.Шланг высокого давления находится между компрессором и конденсатором. Для более поздних моделей автомобилей с системами кондиционирования R-134a требуются «барьерные» (нейлоновые) шланги с гофрированными концевыми фитингами. В старых автомобилях с системами R-12 можно использовать шланги без футеровки с зазубринами на концах. При замене шлангов кондиционера всегда используйте новые уплотнительные кольца или уплотнения.
Проверка радиатора
После проверки кондиционера муфты компрессора и компрессора, которые кажутся в хорошем состоянии, проверьте переднюю часть конденсатора на предмет любого типа воздушного потока, мусора или чего-либо, что может ограничить возможность воздуха, проходящего через конденсатор в радиатор.Для визуального осмотра радиатора и конденсатора следует использовать подходящее освещение для магазинов. На большинстве автомобилей это означает снятие пластикового кожуха на передней части радиатора и затем просмотр между компонентами. Любой автомобиль с пробегом на радиаторе более 100 000 миль является идеальным кандидатом для проверки и оценки радиатора. Если охлаждающая жидкость слишком ржавая или сердцевина радиатора сильно повреждена дорожным мусором, пора подумать о замене радиатора.
Технический совет: Продолжение проверки — Как определить тип утечки хладагента для точной диагностики
При диагностике утечки хладагента полезно знать, какой тип утечки присутствует в системе кондиционирования воздуха.Утечки хладагента бывают двух типов — активные и пассивные. Активную утечку легче обнаружить, чем пассивную. Знание типа утечки, с которой вы имеете дело, поможет определить тип прибора для обнаружения утечки хладагента, который будет использоваться для определения места утечки.
Утечка активного хладагента
Утечка активного хладагента — это постоянная утечка, поэтому электронный детектор утечки обнаружит ее эффективно.
Существует ряд распространенных причин активных утечек в системе кондиционирования, в том числе:
• Коррозионная пористость на линии хладагента, испарителе или конденсаторе
Примечание. Отслоение краски из стальной линии хладагента или конденсатора — это нормальное явление, которое происходит со временем и не всегда является признаком утечки хладагента.Однако наличие масла вокруг ржавой или покрытой чешуей краски линии хладагента указывает на наличие утечки.
• Компрессор
— Трещина в корпусе компрессора.
— Ослабленные стяжные болты компрессора.
— Уплотнение вала компрессора.
— Уплотнения корпуса компрессора.
• Трубопровод хладагента
— Повреждение из-за изгиба трубопровода во время ремонта системы хладагента.
— Удар, вызвавший деформацию лески.
• Кольцо круглого сечения или уплотнительная шайба
— Мусор застрял между уплотнительным кольцом, уплотнительной шайбой или стыковой поверхностью.
— Уплотнительное кольцо или уплотнительная шайба неправильного размера используются на стыке или сопрягаемой поверхности.
— Прокатное уплотнительное кольцо.
— Отсутствует уплотнительное кольцо или уплотнительная шайба.
• Компоненты с ненадлежащим моментом затяжки.
— Избыточный или недостаточно затянутый трубопровод хладагента, соединение компонентов или фитинг компонентов.
— Реле давления с недостаточным крутящим моментом или циклический переключатель.
— Неплотная крышка сервисного порта
• Пористость отливки компонентов
— Пористость из-за неправильно изготовленной детали, такой как корпус компрессора или корпус терморасширяющего клапана (TXV).
• Сервисный клапан или реле давления
— Шток смещен по центру и неправильно установлен
— Ослаблен стержень клапана
Утечка пассивного хладагента
Пассивная утечка — это тип утечки хладагента, который возникает периодически и вызван изменения давления, температуры или вибрации.
Использование ультрафиолетового красителя для обнаружения утечек будет более эффективным при обнаружении утечки, чем использование электронного течеискателя. В зависимости от серьезности утечки и стиля вождения вашего клиента может потребоваться от нескольких минут до нескольких дней, чтобы найти утечку.Перед добавлением дополнительного красителя в систему проверьте, не установлен ли краситель от производителя транспортного средства.
Ниже приведены некоторые примеры того, как может происходить пассивная утечка:
• Давление
— Расширение и сжатие линии хладагента с недостаточным крутящим моментом, соединения компонентов или фитингов компонентов во время работы кондиционера.
— Негерметичность уплотнения вала компрессора.
• Вибрация
— Трещина пайки на конденсаторе или испарителе от линии хладагента, которая не поддерживается должным образом.
• Температура
— Корпус компрессора или уплотнительное кольцо передней головки.
Испытание давления в воздуховодах: взгляд на балансировщик воздуха
Испытания на утечку в воздуховодах путем создания избыточного давления в воздуховодах можно проследить до стандартов SMACNA на герметичность воздуховодов, опубликованных в 1960-х годах. Испытания на герметичность в коммерческих каналах под давлением в течение десятилетий процветали как метод проверки одного из многих факторов производительности системы HVAC. К сожалению, сегодня испытание под давлением водяных воздуховодов в жилых помещениях принимается как отдельная гарантия того, что система отопления, вентиляции и кондиционирования воздуха в жилых помещениях достигла максимальной эффективности государственными и коммунальными программами по всей стране.
Теоретически, если система воздуховодов герметична, все БТЕ, генерируемые безупречно работающим оборудованием, будут доставлены в оболочку здания. Таким образом, в настоящее время существует практика проверки герметичности системы воздуховодов, чтобы гарантировать гражданам максимальную энергоэффективность. Но на самом деле шансы на то, что все другие факторы, определяющие эффективность системы, невелики, автоматически функционируют должным образом.
Давайте вернемся на 50 лет назад и посмотрим на полный объем испытаний, которые использовались и продолжают использоваться для документирования характеристик установленной системы HVAC.Мы сопоставим старый способ, который выдержал испытание временем, с тем, что принято сегодня.
Тестирование герметичности коммерческих воздуховодов
В процессе строительства, когда воздуховод доступен до установки решеток и оборудования, каждое намеренное отверстие в системе воздуховодов герметично закрывается пластиком и лентой. Затем в системе воздуховодов создается высокое давление, и измеряется воздушный поток, проходящий через вентилятор. Воздушный поток вентилятора интерпретируется как утечка в воздуховоде.Если уровень утечки не соответствует требованиям, негерметичный воздуховод ремонтируется, а затем испытание повторяется. Процесс продолжается до тех пор, пока не будут достигнуты приемлемые результаты.
В коммерческих испытаниях используется вентилятор мощностью от 5 до 10 лошадиных сил для проведения испытаний на герметичность и для обеспечения эффективности до 7 дюймов. давления не требуется. Эта мощность вентилятора в 70 раз превышает давление, которое используется сегодня при проверке воздуховодов в жилых помещениях. Более высокое давление необходимо для создания адекватного давления в системе воздуховодов и получения точных результатов.
Более высокое давление имеет решающее значение для обеспечения того, чтобы давление на вентиляторе было равно давлению во всей системе воздуховодов. Только в этом случае давление на вентиляторе можно интерпретировать как точное представление об утечке воздушного потока через систему.
Один из множества тестов
В коммерческих целях испытание воздуховода под давлением является первым из множества тестов, необходимых для проверки фактических характеристик установленной системы. Понятно, что создание давления в воздуховоде — это «мертвое» испытание, потому что на данный момент оборудование, включая вентилятор, системы отопления и охлаждения, еще не работает.Таким образом, сам по себе этот тест отображает только одну небольшую часть картины производительности системы.
После того, как система завершена, начинается настоящее тестирование. Воздушный поток — это основная работа, которая должна быть завершена до того, как начнутся все остальные. Поскольку воздух является жидкостью, которая нагревает или охлаждает все здание, его поток, температура, скорость, потери, прирост и энтальпия должны проверяться во многих точках системы, чтобы ее можно было эффективно диагностировать и оценить производительность.
Воздушный поток — это жизненная сила системы, от которой зависят все остальные компоненты и схемы. Воздух так же важен для системы, как и мощность вентилятора. Без проверки воздушного потока во всей системе невозможно эффективно проверить эффективность нагрева и охлаждения.
Статическое давление
Статическое давление для врача похоже на артериальное давление и является начальным тестом, который используется для получения общего представления о системе. Это следующий тест, который следует добавить к диагностике герметичности жилого воздуховода.Научившись точно измерять общее внешнее статическое давление, воздушный поток вентилятора можно точно отобразить в таблицах производительности вентиляторов производителя.
Последний выпускник NCI позвонил, чтобы сообщить о 5-тонной системе, в которой было только шесть 6-дюймовых. приточные каналы. Система успешно прошла обязательное испытание на герметичность воздуховода и имела «проверенное» изменение охлаждения, но ее статическое давление в три раза превышало номинальную мощность вентилятора. Его оценка доказала, что эта «проверенная» система работала менее чем на 40% от номинальной мощности оборудования.Не редкость.
Мы обнаружили, что на национальном уровне среднее общее внешнее статическое давление превышает 0,76 дюйма. для вентиляторов с номиналом 0,50 дюйма. или менее. Не очень красивая картинка.
Падение давления
Причина высокого статического давления определяется путем измерения падения давления на многих компонентах системы. Падение давления над любым одним компонентом можно разделить на общее внешнее статическое давление системы, чтобы определить процент падения давления в системе, вызванный этим одним компонентом.Измерение перепада давления — отличная диагностика.
Воздушный поток вентилятора
Тестирование хорошей производительности системы подтверждает общий воздушный поток вентилятора, определяемый статическим давлением или выполнением пересечения воздушного потока в соответствующей точке воздуховода рядом с вентилятором. Падение возвратного воздуха или комбинация показаний воздушного потока в магистральном воздуховоде обычно достаточно. Этот тест также определяет потери воздушного потока в вентиляционном оборудовании. Это действительно сочная цифра, и она варьируется от производителя к производителю, но это уже другая статья.
Тест производительности вентилятора
Для дальнейшей проверки производительности вентилятора, а также для проверки работы оборудования, измерьте частоту вращения вентилятора и двигателя, а также потребляемую мощность двигателя вентилятора. Сравните эти числа с номинальными характеристиками оборудования в качестве дополнительных факторов проверки производительности.
Поток воздуха в помещении
Просто потому, что «воздушный поток через змеевик внутри помещения» может быть достаточным, абсурдно предполагать, что этот воздушный поток адекватно распределяется внутри и по всему зданию.Основная цель наших систем — обеспечить комфорт, и комфорт не может быть гарантирован, если воздушный поток в каждой комнате не измеряется и не проверяется в соответствии с вашими ручными расчетами ACCA для каждой комнаты. Если воздух не попадает в каждую комнату, БТЕ ни за что не попадут туда.
Температурное испытание
Бывают случаи, когда воздух попадает в комнату, но БТЕ теряются по пути. Многие коммерческие отчеты о балансе воздуха, которые просто совпадают с числами расхода воздуха инженером, не позволяют проверить доставку в БТЕ путем проверки дельта-Т между воздухом в помещении и приточным воздухом.CFM, умноженное на дельта-T, умноженное на соответствующий коэффициент BTU, равняется доставленному BTU.
Температурные испытания можно использовать для проверки производительности каждой комнаты, системы и даже оборудования, если известен расход воздуха в каждом из них. Точность имеет решающее значение и требует понимания процедур тестирования, которые до сих пор не распространены в отрасли.
Как только известен расход воздуха, мы можем проверить работу контуров охлаждения и сгорания систем, которые мы измеряем, с помощью температуры.Еще раз, воздушный поток — единственная жидкость, которая циркулирует по всему зданию. Попытка проверки производительности системы путем измерения одной из второстепенных цепей системы даст худшие результаты, и мы обнаружили, что это частичное тестирование системы часто оказывает отрицательное энергетическое воздействие на систему.
Потери температуры в воздуховоде
Когда воздуховоды расположены в некондиционных помещениях, потери температуры через изоляцию воздуховода могут быть очень высокими. Во многих частях страны температура чердаков достигает 150 ° F — изоляция R-4, R-6 или даже R-8 просто не справляется со своей работой в таких условиях.И помните, что в те дни, когда в помещении больше всего нужны кондиционирование и отопление, это время наиболее экстремальных температур.
Измеряя разницу температур от одной точки воздуховода к другой, можно определить и изолировать температурные потери или повышения. Как только станут известны источники потерь и прибылей, эти недостатки системы можно будет устранить.
Проверка общей производительности системы
Плохая новость заключается в том, что для проверки общей производительности системы необходимо собрать и записать более 200 точек данных по всей системе.Хорошая новость заключается в том, что с использованием новых процедур тестирования и диагностических приборов HVAC в сочетании с возможностями онлайн-проверки подрядчики теперь могут завершить этот процесс всего за 90 минут. Часто это меньше времени, чем требуется для проведения качественного испытания герметичности жилого воздуховода.
В любом методе тестирования есть преимущество, которое сделает вас лучшим подрядчиком и подтолкнет вас и ваши системы к повышению эффективности.
Как технический специалист или подрядчик, вы всегда будете тем, кто решает, как вы будете проверять, работает ли система с максимальной загрузкой.Ваша задача — найти то, что хочет ваш клиент и что позволит вам превзойти своих конкурентов.
Роб «Док» Фалке работает в отрасли в качестве президента National Comfort Institute, обучающей компании, специализирующейся на измерении, оценке, улучшении и проверке производительности систем HVAC. Если вы подрядчик или технический специалист по ОВКВ, заинтересованный в Таблице уровней и симптомов отравления CO, свяжитесь с Доком по адресу [email protected] или позвоните ему по телефону 800 / 633-7058. Перейдите на сайт NCI www.nationalcomfortinstitute.com, где вы найдете бесплатную информацию, технические статьи и файлы для загрузки.
Испытания давлением в изменяющихся условиях окружающей среды
В данном руководстве описывается безопасный метод испытания на герметичность трубопроводов RACHP с использованием бескислородного азота (OFN) при высоком давлении; с особым упором на изменение давления, вызванное изменением температуры окружающей среды во время испытания на герметичность.
Это требование Регламента по фторсодержащим газам (EC517 / 2014, ст.3) что установщики систем RACHP и связанных трубопроводов и компонентов
«должны принимать меры предосторожности для предотвращения утечки» хладагентов, которые должны содержаться в системах.
Также требуется, чтобы регулярные проверки на утечки, выявляющие утечку, «ремонтировались без неоправданной задержки», а точка утечки
снова проверялась «в течение одного месяца».
На практике это означает:
• Для новых систем это означает немедленное повторное тестирование, чтобы убедиться в отсутствии утечек в системе, прежде чем система будет введена в эксплуатацию или хладагент
будет введен в трубопровод.
• Для существующего оборудования, тестируемого в рамках плановой плановой проверки на утечки, требуемой в соответствии с нормативными актами, это означает:
— система снова проверяется на герметичность после ремонта, не позднее, чем через один календарный месяц после ремонта, но в идеале как можно скорее после ремонта, чтобы убедиться, что ремонт прошел успешно.
ОЦЕНКА РИСКОВ И СООБРАЖЕНИЯ БЕЗОПАСНОСТИ
Прежде чем приступить к работе, необходимо провести оценку рисков.При оценке риска следует учитывать ручное обращение со сжатыми газами и их использование, а также соблюдение обычного использования СИЗ (средств индивидуальной защиты) при выполнении этого вида работ: защитные перчатки, обувь и очки, а также любые соображения, необходимые для работы на месте. местные условия.
Тип хладагента должен быть известен и на основании этого должно быть определено максимально допустимое давление в системе и давление испытания на герметичность.
Коллекторы хладагента со смотровыми стеклами, как известно, выходят из строя и вызывают травмы из-за неправильного обращения и повреждения стеклянного кожуха.Использование стандартных коллекторов должно использоваться только после утвержденного набора регуляторов, а процедура испытания под давлением должна гарантировать, что давление в системе медленно повышается без резкого повышения давления в какой-либо части системы. Газообразный азот обладает удушающим действием — при высоких концентрациях он задыхается. Испытания под давлением с применением ОФН следует проводить только в хорошо вентилируемых помещениях.
ПРОЦЕДУРА ИСПЫТАНИЯ
- Убедитесь, что баллон с азотом закреплен или расположен в таком положении, чтобы он не упал.
- Перед установкой на цилиндр убедитесь, что регулирующий клапан полностью выкручен (против часовой стрелки).
- Подсоедините манометры к тестируемой системе и подсоедините шланг общего коллектора к регулятору OFN.
- Используйте клапан на стороне высокого давления и манометр коллектора для проверки, чтобы избежать повреждения манометра на стороне низкого давления (при использовании составных манометров).
- Откройте вентиль баллона OFN и начните медленно заводить регулятор (по часовой стрелке) с шагом не более 45 фунтов на квадратный дюйм (3 бара) за раз.
- На каждом этапе прислушивайтесь к звуковой утечке и проверяйте падение давления на манометре.
- Когда будет достигнут уровень испытания под давлением, клапан баллона OFN должен быть закрыт и записаны время, температура и давление в системе.
- Регулирующий клапан должен быть снова полностью намотан (против часовой стрелки) и общий шланг снят с цилиндра.
- Новая система должна быть испытана на герметичность, по крайней мере, в течение ночи, а при проверке на следующий день снова должны быть записаны давление и температура.
Примечание. Давление в системе могло измениться из-за изменения температуры, а не из-за утечки.
ГАЗОВЫЙ ЗАКОН GAY-LUSSAC
Этот газовый закон гласит, что если вы измените температуру газа в контейнере с фиксированным объемом (например, в системе RACHP), давление внутри фиксированного объема изменится прямо пропорционально изменению температуры.
(P1 / T1) = (P2 / T2)
Где: P — абсолютное давление газа в барах (манометрическое давление +1)
T — температура газа в Кельвинах (° C + 273)
P1 и T1 — давление и температура при начало теста, а P2 и T2 — давление и температура в конце теста.
Этот закон затем говорит нам, что при тестировании с помощью OFN, если температура тестового газа изменится, то
изменится и давление. Мы можем предсказать, каким должно быть давление, используя следующее уравнение:
P2 = (P1 X T2) / T1
Например: если вы испытываете давление в системе R410A при расчетном испытательном давлении 33 бар манометрического ( 34 абс.), А температура в начале составляет 20 ° C, но когда вы вернетесь на следующий день, чтобы проверить результаты теста, температура упала до 15 ° C, тогда ожидаемое давление будет 32.Манометр 4 бара (33,4 бара абс.):
[(34 X 288) / 293] = 33,4
Падение давления на 0,6 бар ман. (Прибл. 8 фунтов на кв. Дюйм) произошло из-за падения температуры, а НЕ из-за утечки.
Обратите внимание: этот документ основан на знаниях, доступных на момент публикации, и предназначен для общих целей, а не для уверенности в отношении конкретных технических или юридических вопросов, и в этом случае вам всегда следует обращаться за независимой консультацией.Авторы или другие лица, участвующие в его публикации (включая Ассоциацию инженерных служб зданий), не принимают никакой ответственности за любые травмы, смерть, потерю, ущерб или задержку, как бы они ни были вызваны в результате использования советов и рекомендаций, содержащихся в настоящем документе. .
5 способов проверить утечку хладагента в домашней системе кондиционирования воздуха
Система кондиционирования воздуха в вашем доме чрезвычайно важна в жаркие месяцы года, поскольку она помогает поддерживать прохладную температуру в помещении.Однако, когда в нем происходит утечка хладагента, он не может подавать достаточно холодного воздуха; оставляя вас горячим и вспотевшим и стоившим вам тонны счетов за электроэнергию.
Если вы не хотите, чтобы в жаркие летние месяцы вам приходилось сталкиваться с палящими температурами, важно знать, как проверить на утечку фреона домашнюю систему кондиционирования.
Заявление об ограничении ответственности: Обращение в компанию по ремонту кондиционеров — лучший способ решить проблемы с кондиционерами, включая утечки хладагента. Если у вас нет опыта в ремонте переменного тока, не рискуйте причинить еще больший ущерб.Мы не несем ответственности за информацию, представленную ниже, и настоятельно рекомендуем позвонить профессионалу.
Один из наиболее эффективных способов проверить утечку хладагента в системе кондиционирования воздуха — это провести тест на краситель. Этот процесс включает отправку флуоресцентного красителя в вашу систему отопления, вентиляции и кондиционирования воздуха. По прошествии достаточного времени для циркуляции краситель вытечет через любые имеющиеся утечки.
Затем с помощью лампы обнаружения вы можете просканировать систему отопления, вентиляции и кондиционирования воздуха и определить место утечки красителя.Весь этот процесс не должен занять у вас больше нескольких минут, но он требует инвестиций в специализированное оборудование. Если у вас нет времени, денег или опыта для выполнения этого теста на краситель, вам следует обратиться в профессиональную компанию по ремонту кондиционеров. Они могут выполнить этот тест на краситель быстро и безопасно.
Этот тест с красителем имеет много преимуществ по сравнению с другими методами тестирования. Во-первых, вы можете быстро определить каждую утечку в вашей системе HVAC. Утечки также можно обнаружить на расстоянии, если достаточно света от лампы обнаружения.Кроме того, этот тест на окрашивание можно проводить, когда ваш блок переменного тока работает или нет.
Еще один полезный и простой метод обнаружения утечек, который вы можете попробовать, — это использование электронного устройства. Это позволяет сканировать компоненты холодильного оборудования за пределами вашего дома. При обнаружении утечки это электронное устройство подает сигнал тревоги, который легко распознать.
Единственным недостатком этого метода является то, что утечки могут быть обнаружены только в определенных областях, где электронный течеискатель касается компонентов хладагента.Эти электронные устройства обнаружения утечек также могут быть дорогими, и вам потребуется пройти краткое обучение, чтобы научиться правильно ими пользоваться. Еще одна вещь, которую вы должны учитывать, — это убедиться, что электронный детектор совместим с хладагентом, который вы используете. В противном случае детектор не сработает при обнаружении утечки.
Опять же, если вы хотите избавить себя от необходимости вкладывать деньги в одно из этих устройств, вы всегда можете обратиться в сервисную и ремонтную компанию переменного тока для проведения этого теста.Они могут выполнить это рентабельно и избавить вас от дорогостоящего ремонта переменного тока.
Существует множество тестов на обнаружение утечек, которые любят использовать домовладельцы и техники HVAC, но тест детектора утечек азота является одним из самых популярных. Это может стоить больше, чем другие методы, но дает точные результаты, на которые вы можете положиться.
Во-первых, необходимо удалить оставшийся фреон в вашей системе. Затем азот закачивается обратно в вашу домашнюю систему кондиционирования.Поскольку азот находится под более высоким давлением, чем хладагент, он будет издавать слышимые звуки в местах утечки.
Затем все, что требуется, — это прислушиваться к звукам и затем отмечать эти области. Вы также узнаете, есть ли утечки, если будете контролировать азот с помощью манометров. Если эти манометры показывают значительные изменения давления, вы знаете, что есть утечка.
Если вы планируете протестировать свою систему отопления, вентиляции и кондиционирования воздуха без профессиональной помощи, одним из лучших способов является испытание мыльных пузырей.Этот тест выполнить довольно просто. Все, что вам нужно сделать, это смешать немного мыла с теплой водой. Затем вам нужно будет перемешивать этот раствор в течение нескольких минут.
После того, как он будет достаточно перемешан, отправьте его через систему хладагента переменного тока. Если в вашей системе есть утечки, будут видны пузырьки воздуха. Затем вы можете пометить эти области, чтобы техник HVAC точно знал, где требуются исправления.
Крайне важно, чтобы вы не добавляли никаких коррозионных элементов в эту воздушно-пузырьковую смесь.Если вы это сделаете, эти элементы могут привести к износу компонентов хладагента и потребовать дорогостоящего ремонта. Вы также должны быть осторожны, чтобы не использовать достаточное количество пузырьков воздуха, потому что, как только этот раствор попадает в систему, может быть трудно определить, откуда именно появляются пузырьки воздуха.
Опять же, если вы не знакомы или не имеете опыта в ремонте кондиционеров, мы настоятельно рекомендуем обратиться в ремонтную компанию для проверки утечек хладагента.
Если в вашей системе кондиционирования имеется утечка хладагента, иногда происходит утечка масла.Это вещество довольно просто обнаружить, учитывая его густую темную консистенцию. Он также имеет сильный запах, который легко различить, даже если вы находитесь далеко.
Если вы подозреваете утечку в вашей системе, начните прощупывать различные компоненты переменного тока. При выполнении этого шага рекомендуется надевать защитные перчатки, чтобы не испачкать руки и не порезать их острыми предметами.
Осматривайте различные компоненты и постоянно проверяйте перчатки на предмет видимых следов масла.Если область производит много, есть вероятность, что есть утечка, которую необходимо немедленно устранить. Если у вас нет защитных перчаток, можно также использовать ткань. Убедитесь, что он светлый, чтобы его было видно при наличии масла.
Устранение утечек хладагента переменного тока может вызвать стресс, поскольку они мешают вашей системе отопления, вентиляции и кондиционирования воздуха работать на оптимальном уровне. Если вы думаете о том, как найти утечку в домашней системе переменного тока, вам не нужно впадать в безумие. Вам просто нужно попробовать метод обнаружения утечек, который подходит для вашего бюджета, или вы можете попробовать комбинацию методов, чтобы убедиться, что все утечки обнаружены.