Мар 25, 2020
Восстановление сварных соединений трубопроводов.
Наземные сварные соединения наиболее многочисленны. При их ремонте проводят сварочно-ремонтные операции при выявлении в сварных соединениях недопустимых дефектов и эксплуатационных повреждений [1, 2].
Выбор сварочной технологии зависит от типа трубопровода (параметров эксплуатации — давления и температуры, длительности наработки), типоразмера сварного соединения и технологии его изготовления или предыдущего ремонта (способа сварки, сварочного материала, марки стали, вида термообработки), характера и размера повреждения, места и ориентации трещин (поперечные или продольные, по металлу шва или в зоне термического влияния).
Основные положения сварочно—ремонтной технологии включают требования и рекомендации по анализу особенностей и причин повреждения, измерению твердости и химическому анализу металла, организации места ремонта, выбору и прокалке покрытых электродов, удалению поврежденного металла механическим способом с получением углубления — выборки оптимальной чашеобразной формы и размера, многослойному заполнению выборки с подогревом, выполнению при необходимости усиливающих наплавок, проведению послесварочной термообработки, механической обработки и контроля качества отремонтированного сварного соединения [1].
Для сварных соединений технологических трубопроводов химических, газо— и нефтеперерабатывающих и добывающих предприятий ремонт заключается в выполнении подварочных швов в местную выборку. Поверхностный дефект удаляется механическим способом (вырубкой ударным инструментом, фрезерованием, абразивным инструментом) с засверловкой концов трещин. Разделка под сварку подготавливается чашеобразной формы с отлогими стенками без резких переходов по краям разделки. Процесс сварки ведется на спокойном воздухе (без сквозняков) при положительной температуре. При ручной дуговой сварке низко— и легированных сталей, включая высоколегированные аустенитного класса, используются электроды с основным покрытием, при сварке углеродистых сталей — электроды с рутиловым покрытием [1].
Причинами повреждений сварных соединений паропроводов из хромомолибденованадиевых сталей являются технологические, конструкционные и эксплуатационные факторы [1, 2]. К типичным относятся повреждения в виде продольных и поперечных трещин в металле шва и в зоне термического влияния.
Для сварных соединений тепловых сетей горячей воды с температурой эксплуатации до 250° технология ремонта соединений трубопроводов 100 ≤ Дн ≥ 920 мм и с S ≤20 мм проводится путем выполнения подварочных швов в зоне появления свищей или трещин, а также путем переварки поврежденных сварных швов, либо замены разрушившихся сварных деталей на новые [1].
Ремонт сварных соединений магистральных газо- и нефтепроводов проводится несколькими способами, в том числе [1]:
— с применением ручной дуговой сварки. Одним из вариантов технологии является нанесение наплавки при ремонте поверхностных дефектов без прекращения перекачки продукта (нефти, газа) .в трубопроводе. Другим вариантом является замена дефектного участка трубопровода (сварного стыка, трубы) с вваркой нового трубного элемента, что связано с остановкой транспортировки продукта. При любом варианте технологии ремонта принимаются специальные меры по пожаро— и взрывобезопасности;
— с использованием холодной сварки без прекращения транспортировки продукта в трубопроводе. По технологии, разработанной АО «ВНИИСТ», полость поверхностного дефекта заполняется композиционным материалом в виде полимерной основы с дисперсным металлическим наполнителем. В течение короткого времени нанесенный материал твердеет однако по прочности он заметно уступает показателям металла труб, что сдерживает широкое применение этого способа ремонта;
— с применением кольцевых пластиковых муфт (возможно в сочетании с холодной сваркой) без прекращения транспортировки продукта в трубопроводе. Такой способ является эффективным как обеспечивающий несущую способность сварных соединений (или участков труб) с поверхностными дефектами, Кольцевая муфта изготавливается путем многослойной намотки высокопрочной пластиковой ленты на дефектный кольцевой сварной стык трубы без применения электрической дуги или открытого пламени. Целостное сцепление муфты между слоями и с металлом трубы обеспечивается связующим материалом-адгезивом.
Рекомендации по ремонту сварных соединений трубопроводов, включая режимы сварки, даны в [1‚ 2, 3].
Восстановление разъемных соединений трубопроводов.
При ремонте и замене фланцы и крепежные детали технологических трубопроводов независимо от наличия сертификата и заводской маркировки (Pу‚ Dу, марка стали), допускается применять только после проверки марки стали (химический анализ, стилоскопирование и т. п.) [4].
Все детали перед ремонтными работами должны проверяться. Поверхности фланцев, прокладок не должны иметь трещин, раковин, плен, заусенцев и других дефектов, снижающих их прочность и работоспособность.
Маркировка должна соответствовать документации.
Фланцы отбраковываются при:
— неудовлетворительном состоянии привалочных поверхностей;
— наличии трещин, раковин и других дефектов;
— деформации;
— уменьшении толщины стенки воротника фланца до отбраковочных размеров трубы;
— срыве, смятии и износе резьбы в резьбовых фланцах высокого давления, а также при наличии люфта в резьбе, превышающего допустимые пределы.
Крепежные детали отбраковываются:
— при появлении трещин, срыва или коррозионного износа резьбы;
— в случаях изгиба болтов и шпилек;
— при остаточной деформации, приводящеи к изменению профиля резьбы;
— в случае износа боковых граней головок болтов и гаек;
— в случае снижения механических свойств металла ниже допустимого уровня.
Прокладочпый материал для уплотнения соединений фланцев должен соответствовать действующим стандартам.
Прокладки отбраковываются при наличии трещин, забоин, сколов, смятии уплотнительных поверхностей, деформации.
Замена прокладок фланцевых соединении газопровода допустима при условии установки кабельной перемычки между их разъединяемыми частями.
Станции электрохимической защиты при производстве работ выключаются.
При ремонте перед сборкой фланцевых соединений уплотнительные поверхности, а также металлические прокладки и линзы должны промываться и насухо протираться. Торцы труб, соединяемых на фланцах (муфтах), должны быть паралельными в пределах установленных допусков.
На поверхности резьбы крепежных деталей не должно быть следов коррозии, вмятин, надрывов и других дефектов, снижающих прочность.
При сборке фланцев под сварку с различными деталями (патрубками, фасонными частями, бесфланцевой арматурой, компенсаторами и т.п.) следует обеспечивать перпендикулярность и соосность уплотнительной поверхности фланцев к оси смежной детали в соответствии с правилами [4, 5].
При сборке фланцевых соединений деталей трубопроводов и арматуры следует обеспечивать соосность уплотнительных поверхностей фланцев. При сборке фланцев с деталями следует симметрично располагать отверстия под болты и шпильки относительно оси фланцевого соединения. Смещение отверстий двух смежных фланцев не должно превышать половины разности номинальных диаметров отверстия и устанавливаемого болта (или шпильки). При сборке деталей с плоскими приварными фланцами расстояние между уплотнительной поверхностью фланца и торцом трубы (недовод трубы) должно приниматься равным толщине трубы +1 мм или выбираться в зависимости от условного диаметра прохода трубы (табл. 1).
Таблица 1
Dy трубы, мм | 20 | 20-50 | 70-150 | 200 | 225 | 250-300 | 350-450 |
Недовод, мм | 4 | 5 | 8 | 8 | 9 | 10 | 11 |
Для разъемных соединений трубопроводов при ремонте целесообразна замена их деталей: фланцев, прокладок, крепежа.
ЛИТЕРАТУРА
1. Хромченко Ф.А. Сварочная технология ремонта трубопроводов. М.: ИПК гослужбы, 2004. 92 с.
2. Хромченко Ф.А. Ресурс сварных соединений паропроводов. М.: Машиностроение, 2002. 352 с.
3. Юхин Н.А. Ручная сварка при сооружении и ремонте трубопроводов пара и горячей воды. М.: СОУЭЛО, 2003. 56 с.
4. Правила устройства и безопасной эксплуатации технологических трубопроводов (ПБ 03-585-03). Серия 03. Выпуск 25, 2004. 152 с.
5. Правила устройства и безопасной эксплуатации трубопроводов пара и горячей воды (ПБ 10-573-03). Серия 10. Выпуск 28, 2005. 128 с.
Трубопровод (согласно определению из Википедии) – инженерное сооружение, предназначенное для транспортировки газообразных и жидких веществ, пылевидных и разжиженных масс, а также твёрдого топлива и иных твёрдых веществ в виде раствора под воздействием разницы давлений в поперечных сечениях трубы. В состав трубопровода, помимо труб, входят детали трубопровода, арматура, приборы контроля, опорные конструкции и другие устройства.
Промышленные и магистральные трубопроводы осуществляют транспортировку разного рода сырья – нефти, нефтепродуктов, газов, воды и прочих веществ. Рабочий продукт от производителя или места добычи проходит по всей конструкции трубопровода к местам переработки, к местам промышленного и бытового потребления и прочим объектам.
Трубопроводные конструкции на сегодняшний день занимают важные позиции в инфраструктурах многих стран. Магистральные сооружения оказывают непосредственное влияние на экономику, промышленность и обеспечение жизнедеятельности населения. К показателям надёжности этих конструкций предъявляются повышенные требования безопасности как к важным стратегическим объектам, выполняющим задачи по обеспечению населения энергией, без которой невозможно представить современную жизнь.
В процессе эксплуатации трубопроводы и их элементы (арматура, фланцевые и резьбовые соединения) изнашиваются под воздействием различных факторов, таких как механические нагрузки, температурное воздействие, атмосферные осадки, коррозионный и эрозионный износы, нарушение условий эксплуатации элементов трубопровода, что может привести к серьезным последствиям. Поэтому для предотвращения всевозможных аварий на трубопроводах, продления их срока службы необходимо своевременное проведение превентивных мероприятий – профилактических осмотров, планово-предупредительных ремонтов трубопроводов и арматуры.
Целью ремонта любого трубопровода является поддержание и восстановление первоначальных эксплуатационных качеств в целом или его отдельных участков.
Существует несколько видов ремонтов поврежденных или изношенных участков магистральных и распределительных трубопроводов. По объему и характеру выполняемых работ ремонты подразделяются на текущие (аварийные или внеплановые), средние и капитальные.
При текущем ремонте устраняют дефекты, замеченные во время эксплуатации. Во время текущего ремонта производят частичную замену и (или) восстановление частей оборудования трубопровода.
При среднем ремонте производят восстановительные плановые работы линейной арматуры и оборудования, линий связи, средств электрозащиты, осуществляют работы по очистке внутренней поверхности трубопроводов, обследованию и ремонту водных переходов. На практике текущий и средний ремонт часто объединяют в одно целое, так как их объемы и характер работ схожи.
Капитальный ремонт магистрального трубопровода представляет собой комплекс технических мероприятий, направленных на полное или частичное восстановление линейной части эксплуатируемого трубопровода до проектных характеристик с учётом требований действующих нормативов. Это самый большой по объему и содержанию плановых работ ремонт, который проводят при достижении предельных значений износа в линейных сооружениях. Ремонт связан с полной разборкой, восстановлением или заменой изношенных или неисправных составных частей сооружений.
Основные работы, проводимые при ремонте трубопроводов:
— наружный осмотр трубопровода для выявления дефектов и определения объема работ;
— проверка и подгонка опор и подвесок;
— проверка положения компенсаторов;
— проверка сальников арматуры;
— проверка герметичности арматуры;
— устранение утечек во фланцевых соединениях, обтяжка фланцев, смена прокладок;
— замена изношенных деталей и узлов трубопровода или их восстановление до соответствующих нормативных размеров и допусков;
— изоляция трубопроводов;
— испытание трубопроводов на прочность и плотность;
— окраска трубопроводов.
Эффективное проведение ремонтных работ на трубопроводе зависит от выбора современных технологий ремонта и оборудования, необходимого для проведения восстановительных работ.
Специалистами НПО «ГАКС-АРМСЕРВИС» разработаны различные группы и виды технологического оборудования, необходимого для осуществления основных технологических процессов строительства, облуживания и ремонта трубопроводов различного назначения:
Для диагностики, технологического обслуживания, метрологического обеспечения и ремонта трубопроводной арматуры в НПО «ГАКС-АРМСЕРВИС» разработано следующее оборудование:
Поставляемые предприятием технологическое оборудование и приборы сертифицированы, прошли апробацию и успешно эксплуатируются на различных объектах таких компаний, как Газпром, Роснефть, Русьнефть, ТНК, Лукойл, Татнефть, Атомэнергоремонт и многих других.
- Ремонт трубопроводов.
- РЕМОНТ ТРУБОПРОВОДОВ
- Ремонт трубопроводов методом «труба в трубе»
- Ремонт трубопроводов и арматуры
- Ремонт трубопроводов | Сварка и сварщик
- Устранение дефектов
- Для сварных тройников паропроводов, эксплуатируемых при температуре ниже 510 °С
- Ремонт стыковых соединений паропроводов, эксплуатируемых при температуре 510-560°С
- Ремонт участков паропроводных труб
- REINFORCEKiT ® 4D: КОМПОЗИТНОЕ РЕМОНТНОЕ РЕШЕНИЕ ДЛЯ ПРОЧНОГО ТРУБНОГО Укрепления
- REINFORCEKiT ® 4D SUSBEA (R4D-S): КОМПОЗИЦИОННОЕ РЕМОНТНОЕ РЕШЕНИЕ ДЛЯ РЕМОНТА ПОДВОДНОГО ТРУБОПРОВОДА
- TANKiT ® и REINFORCEKiT ® патч: композитные системы ремонта поврежденного бака
- STOPKiT ® : СИСТЕМА РЕМОНТА АВАРИЙНОЙ ТРУБЫ (EPRS) ДЛЯ ОНЛАЙН-УТЕЧКИ УПЛОТНЕНИЯ
- ROLLERKiT ® : КОМПОЗИТНАЯ СИСТЕМА ДЛЯ ЗАЩИТЫ ТРУБ И ПОДДЕРЖКИ ОТ КОРРОЗИИ
- REFLANGEKiT ® : РЕМОНТ УРОВНЯ УСТАНОВКИ И УСТАНОВКИ ПОД ДАВЛЕНИЕМ ДЛЯ SF6 GAS
- REINFORCEKiT ® Балка: композитный ремонт для поврежденных балок
- DKiT ® : ЗАЩИТА ЛУЧЕЙ ОТ КОРРОЗИИ
Ремонт трубопроводов.
При текущем ремонте устраняются дефекты замеченные во время эксплуатации. Трубопроводы, которые во время работы на технологических установках закоксовываются или подвергаются коррозии, обязательно проверяются и очищаются.
В объем ремонтных работ входит:
проверка и ремонт всех опор и подвесок;
устранение утечки во фланцевых соединениях, обтяжка фланцев, смена прокладок;
проверка положения компенсаторов;
проверка сальников арматуры;
проверка герметичности арматуры;
замена изношенных трубопроводов.
Ремонтируемые трубопроводы должны быть полностью освобождены от продукта.
Пропуски в действующих трубопроводах определяют визуально, по потекам, запаху или изменению режима перекачки. Пропуски по телу трубы или в сварных швах можно ликвидировать наложением хомутов, которые изготовляют по форме трубы. Устанавливают таким образом, чтобы при стягивании прокладка (асбест, поранит резина, свинец, фторопласт ) оставалась зажатой между трубой и хомутом и заполняло неплотности. Хомут должен обладать достаточной прочностью и жесткостью для большей прочности хомут приваривают к трубе. Материал прокладок зависит от условий работы трубопровода. Прокладка не должна растворяться или разрушаться средой при длительной эксплуатации в рабочих условиях. Обычную резину можно применять при температуре не выше 50 градусов. В трубопроводах для пара, газа, нефтепродуктов, горячей воды и других жидкостей, при давлении до 40 ат. и температуре до 400 градусов, устанавливают прокладки из паранита.
Аварию, вызванную разрывом сварочного шва, устраняют, удаляя дефектный участок с последующей заваркой. Если участок большой — его заменяют. Для этого трубопровод освобождают от продукта и участок, длиной равной не менее одному диаметру трубы, вырезают. Вместо него заваривают кусок трубы.
Испытание трубопроводов.
По окончании монтажа, и периодически после ремонта трубопроводы проходят гидравлическое испытание на прочность и плотность, затем промываются и продуваются, и дополнительно испытываются на герметичность воздухом или инертным газом.
Для чего, трубопровод с обоих концов заглушатся приварными заглушками с кранами для выпуска воздуха, всю установленную арматуру полностью открыть, на месте регулирующих клапанов и измерительных устройств установить монтажные катушки, штуцера для КИП заглушить. Разрешается испытание с тепло- и антикоррозионной изоляцией.
Трубопровод заполняется водой с температурой 5-40 градусов, но чтоб не вызывала появления потения. Если температура ниже 0, то принимаются меры против замерзания.
Поршневым насосом создают необходимое давление опрессовки 1,25-1,5 от рабочего, но не менее 2 ат.
Напорные нефтяные трубопроводы должны быть подвергнуты гидравлическому испытанию при пробном давлении, превышающее в полтора раза рабочее.
При заполнении водой полностью вытеснить весь воздух.
Давление повышать плавно. Скорость подъёма давления должна быть указана в проектной документации. Использовать для подъёма давления сжатый воздух или газ, не допускается.
Отключают трубопровод от насоса.
Выдерживают 10 мин (испытание на прочность) и проверяют: отсутствие потеков, выпучен и порывов.
Давление должно контролироваться двумя манометрами, классом точности не ниже 1,5, с диаметром не менее 160 мм и шкалой 4/3 от измеряемого. Один устанавливается возле агрегата, другой в отдаленной точке.
После чего снижают давление до рабочего и проводят тщательный осмотр сварных швов (испытание на плотность). Во время осмотра допускается обстукивание молотком массой не более 1,5 кг. При пневматическом испытании обстукивание не допускается.
По окончании осмотра давление вновь повышают до испытательного и выдерживают ещё 5 минут, после чего снова снижают до рабочего и вторично тщательно осматривают трубопровод.
Продолжительность испытания на плотность определяется временем осмотра и проверки герметичности разъёмных соединений.
Затем открывают воздушники и опорожняют трубопровод через дренажи.
Результаты удовлетворительные если не произошло разрывов, видимых деформаций, падения давления по манометру, не обнаружено течи и запотевания. Подчеканка сварных швов запрещается.
При неудовлетворительных результатах дефекты устраняются, а испытания повторяются. Результаты оформляются актом или заносятся в паспорт трубопровода.
Допускается замена гидравлического испытания на пневматическое в случаях:
если опоры не рассчитаны на вес воды;
при Т ниже 0 и опасности промерзания;
если применение жидкости не допустимо.
При условии контроля испытания методом акустической эмиссии и положительной температуре воздуха.
Пневматическое испытание на прочность и плотность производится воздухом или инертным газом. Поднимать давление плавно со скоростью 5 % от Рпр в мин., но не более 2 ат в минуту с периодическим осмотром трубопровода при давлениях до 2-х ат два раза, более 2-х – 3. во время осмотра подъём давления прекратить.
Места утечки определяются по звуку и мыльной эмульсией.
На время испытаний обозначить флажками охранную зону 10 м при подземной прокладке и 25 – при надземной, в обе стороны и выставить через 200 м посты. Во время подъёма давления пребывание людей в охранной зоне запрещается.
Компрессоры и манометры располагать вне охранной зоны.
После окончания гидравлического испытания трубопровод опорожняется и продувается воздухом до полного удаления воды. Затем дополнительно проводятся пневматические испытания на герметичность воздухом или инертным газом под рабочим давлением в течении 24 часов новых и не менее 4-х часов ремонтируемых.
Определяется скорость падения давления после выдержки для выравнивания температуры. Температуру контролируют по термометрам на разных концах трубопровода.
Падение давления должно быть не менее 0,2 % за час.
32
РЕМОНТ ТРУБОПРОВОДОВ
В процессе эксплуатации трубопроводы и их элементы изнашиваются. Характер износа определяется условиями эксплуатации, свойствами материала, из которого выполнен трубопровод, его конструктивными особенностями, качеством изоляции и т.д. В основном трубопроводы подвержены коррозионному износу, а нарушение условий эксплуатации трубопровода приводит к разрыву трубы, отрыву фланца, выбиванию прокладки, ослаблению болтовых соединений.
Тщательная ревизия трубопроводов осуществляется при плановых ремонтах. Пропуски в действующих трубопроводах определяют визуально, по появлению запаха или изменению режима перекачивания (например, снижению давления в трубопроводе, изменению количества принимаемого и расходуемого продукта и т.д.).
На ответственных трубопроводах, работающих при высоком давлении, практикуется система “сверления безопасности”, при которой на участках трубопроводов, где износ наиболее вероятен, до пуска в эксплуатацию высверливают несквозные отверстия. Остаточная толщина труб должна обеспечивать безаварийную работу. По мере износа трубопровода в процессе эксплуатации наиболее вероятен пропуск продукта через эти ослабленные сверлением стенки трубопровода. Отверстия забивают пробкой и накладывают хомут, трубопровод тщательно ремонтируют при первом плановом ремонте.
Во время ревизии трубопроводов проводят контрольную сквозную засверловку с измерением остаточной толщины стенки. Дефекты могут быть обнаружены при измерении толщины стенки ультразвуковыми дефектоскопами. Ликвидация пропусков на поверхности трубы или в сварных швах на действующем трубопроводе возможна наложением хомутов или скоб с накладками. Их ставят на дефектный участок так, чтобы при стягивании хомутов или скоб прокладка (поранит, резина, свинец, фторопласт и др.) оставалась зажатой между трубой и хомутом (накладкой) и заполняла неплотности в трубе или сварном шве.
Хомут и накладка должны обладать достаточной жесткостью и прочностью, в соответствии с этим выбирается их толщина.
При разрыве сварного шва шов вырубается и после зачистки заваривается вновь.
Если участок дефекта большой или образовавшийся дефект нельзя устранить наложением хомутов (например, разрыв трубы по образующей), такой участок заменяют.
Плановый ремонт трубопроводов предусматривает замену определенных участков с трубами, фланцами и крепежными деталями. Трубы отбраковывают, если их толщина в результате износа более не обеспечивает заданные параметры эксплуатации. Для каждого трубопровода должны быть установлены отбраковочные нормы. Технологические трубопроводы диаметром более 75 мм при остаточной толщине 2 мм и менее бракуются без предварительного расчета. При плановых ремонтах проверяют опоры и подвески трубопроводов; плотность прилегания трубы к подушке, подвижность опор, целостность поверхностей скольжения и т.д.
Пропуски во фланцевых соединениях являются результатом плохой подгонки соприкасающихся поверхностей, поврежденности этих поверхностей, некачественной прокладки и недостаточной подтяжки болтов и шпилек. Для ликвидации пропуска сначала подтягивают болты (особенно это эффективно для горячих трубопроводов, где регулярная подтяжка является обязательной). Если таким способом пропуск не устраняется, меняют прокладку.
За 2-3 ч до разборки фланцевых соединений трубопроводов резьбовую часть крепежных деталей необходимо смочить керосином. Отворачивание гаек проводится в два приема: сначала все гайки ослабляются поворотом на 1/8 оборота, затем отворачиваются полностью в любой последовательности. При разборке трубопроводов с целью замены прокладок весьма трудоемка раздвижка фланцев. Винтовое приспособление для раздвижки фланцев показано на рис. 11.1. Для раздвижки фланцев на трубопроводах высокого давления используется приспособление с гидроцилиндром (рис. 11.2).
Для вырезки прокладок используются разнообразные приспособления. Вариант простейшего из них показан на рис. 11.3. Конус 1 имеет сквозные отверстия, в которых стопорными болтами крепятся четырехгранные ножи 2. Приспособление вставляется в патрон сверлильного станка.
|
|
| ||||
При ремонте технологических трубопроводов изношенные участки заменяются новыми, дефектные сварные стыки удаляются, а взамен их ввариваются катушки. Перед удалением участка трубопровода необходимо закрепить разделяемые участки так, чтобы предупредить их смещение. Участок, подлежащий удалению, крепится в двух местах.
После демонтажа участка трубопровода свободные концы оставшихся труб необходимо закрыть пробками или заглушками. При установке нового участка его сначала укрепляют на опорах, а затем сваривают.
При ремонте фланцевых соединений зеркало фланца, находившегося в эксплуатации, очищается от старой прокладки, следов коррозии, графита и проверяется на отсутствие на них раковин и забоин. Если фланцы имеют дефекты, они должны быть заменены.
Приспособление для контроля приварки нового фланца к трубопроводу показано на рис. 11.4.
При ремонте межцеховых трубопроводов замена изношенных участков надземных трубопроводов может осуществляться потрубно. Возможна также сборка участков из секций, которые собирают и сваривают из отдельных труб и их элементов вблизи трассы или в трубозаготовительной мастерской.
|
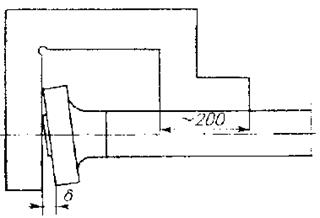
При замене участков трубопроводов, работающих при высокой температуре, а также при прокладке дополнительных линий проводится растяжка компенсаторов температурных удлинений. Величину растяжки можно найти по формуле
l = a×t×L,
где l — удлинение трубопровода; a — коэффициент линейного удлинения; t — температура среды; L — длина трубопровода.
Линзовые компенсаторы ставятся на трубопроводах, имеющих продольное и поперечное перемещения. Для предотвращения разрыва линз при сдвиге трубопровода в поперечном направлении на компенсаторах ставятся стяжки (рис. 11.5). Линзовые компенсаторы растягиваются на половину их компенсирующей способности.
Основным видом ремонта подземных трубопроводов является замена изношенного участка новым. При этом способе извлеченный из траншеи трубопровод разрезается на отдельные части и увозится на ремонтную базу. Новая секция вваривается в коллектор.
При подъеме и опускании трубопровода в траншею наиболее напряженные сварные стыки усиливают муфтами или планками. При усилении планками (рис. 11.6) используется угловой или полосовой профиль. Для лучшего прилегания планок к трубопроводу в середине планок делается выгиб. При усилении муфтами (рис. 11.7) их длина принимается равной 300 мм для труб диаметром 200-377 мм и 350 мм для труб диаметром 426-529 мм. Диаметр муфты принимается на 50 мм больше диаметра трубопровода. Толщина стенки муфты и трубопровода должны быть одинаковы. Допускаемый зазор между муфтой и трубой d = 2 мм.
| |||
| |||
При ремонте иногда нужно подключиться к действующим трубопроводам соседних цехов. Такая необходимость возникает и при подключении нового аппарата к действующим цеховым трубопроводам. Подобные врезки чаще всего осуществляются в период остановочных ремонтов. Врезка в действующий трубопровод проводится с использованием приспособления, представленного на рис. 11.8. К трубопроводу 1 в месте врезки подгоняется и приваривается патрубок 5 с фланцем 6. К этому фланцу на шпильках присоединяется задвижка 8 требуемой серии. К задвижке на фланце 9 крепится приспособление, состоящее из сверла 2 и коронки 4, на которой укреплены резцы 3, штока 7, сальника 10, грундбуксы 11, упорного шарикоподшипника 12 и штурвала 13. Вращением коронки 4 при помощи штурвала 13 в стенке основного трубопровода вырезается отверстие требуемого диаметра. После этого шток 7 с коронкой 4 поднимается выше клина задвижки и последняя закрывается. Затем с задвижки снимается приспособление, и к отводящему патрубку присоединяется новый трубопровод.
|
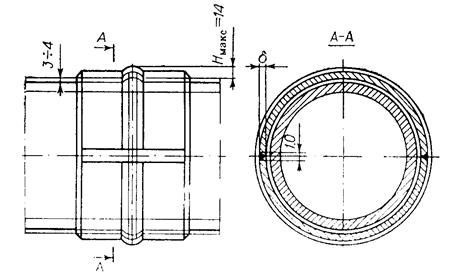
|
После окончания капитального ремонта трубопроводов проводится проверка качества работ, промывка или продувка, а затем испытание на прочность и плотность. Технологическая аппаратура перед испытанием отключается, концы трубопровода закрываются заглушками. Заглушаются все врезки для контрольно-измерительных приборов. В самых низких точках ввариваются штуцеры с арматурой для спуска воды при гидравлическом испытании, а в самых высоких — воздушки для выпуска воздуха. В начальных и концевых точках трубопровода, а также на насосах и компрессорах устанавливаются манометры с классом точности измерения не ниже 1,5.
Гидравлическое испытание на прочность и плотность обычно проводится до покрытия тепловой и антикоррозионной изоляцией. Величина испытательного давления должна быть равна 1,25 максимального рабочего давления, но не менее 0,2 МПа для стальных, чугунных, винипластовых и полиэтиленовых трубопроводов.
РЕМОНТ АРМАТУРЫ
Арматурой называют устройства, предназначенные для управления потоками жидкостей и газов, движущихся по трубопроводам. В зависимости от назначения различают: арматуру запорную, предназначенную для полного перекрытия потока, и регулирующую, предназначенную для регулирования расхода или давления передаваемой среды; клапаны предохранительные и перепускные, служащие для выпуска избытка среды при повышении давления, и обратные, назначение которых — не допускать движения среды в обратном направлении; специальную арматуру — указатели уровня, конденсатоотводчики, пробно-спускные краны и др.
Основные параметры арматуры — условный диаметр прохода Dу и условное давление Ру. Арматуру устанавливают на трубопроводах, непосредственно на аппаратах, в некоторых случаях она является неотъемлемой составной частью аппарата. По способу соединения с трубопроводом или аппаратом различают фланцевую, приварную, муфтовую и цапковую арматуру, а по способу приведения в действие — приводную с ручным или механическим приводом и самодействующую, приводимую в действие перемещаемой средой.
Запорная арматура является наиболее применяемой на предприятиях нефтепереработки и нефтехимии.
В зависимости от принципа действия и формы запорного устройства различают вентили, краны и задвижки.
Вентили (рис. 12.1) применяют для самых различных сред в широком диапазоне давлений и температур. Рабочим элементом в вентилях является клапан, совершающий возвратно-поступательное движение и имеющий сравнительно небольшой ход для его полного открытия. Недостаток вентилей — дополнительное гидравлическое сопротивление. Их не следует применять при работе с загрязненными средами. Вентили устанавливают так, чтобы движение среды происходило “под клапан”, обратное направление нежелательно. Обычно на корпусе вентиля имеется стрелка, показывающая нормальное направление движения среды.
Похожие статьи:
Ремонт трубопроводов методом «труба в трубе»
13 мая 2016 г.
Учитывая имеющиеся недостатки жестких металлических, полиэтиленовых и эластичных труб при ремонте трубопроводов по методу «труба в трубе», предлагается использовать в качестве ремонтных труб гибкие металлические рукава (ГМР) сварной конструкции (рисунок ниже), сваренные в «плеть» и образующие гибкие металлические трубопроводы (ГМТ) необходимой длины (рисунок ниже).
Применение для ремонта трубопровода сваренных в «плеть» гибких высокопрочных металлических рукавов позволяет быстро и без дополнительного оборудования произвести протаскивание рукава в трубу, сматывая его, например, с бобины, барабана, и дает перед другими известными способами следующие преимущества:
1. исключается необходимость в прижатии его к стенкам трубы либо в заполнении межтрубного пространства затвердевающими композициями (например цементным гелем), поскольку такой рукав сам имеет возможность воспринимать внутреннее давление транспортируемой рабочей среды;
Рукав сварной конструкции
Гибкий металлический трубопровод
1 — ГМР; 2 — гофрированная оболочка; 3 — проволочная оплетка; 4 — концевая арматура
2. значительно упрощается и ускоряется способ ремонта;
3. появляется возможность ремонта высоконапорных трубопроводов;
4. появляется возможность увеличить расстояние от места повреждения до мест начала и конца протаскивания ГМТ из-за их большой осевой и радиальной прочности;
5. уменьшается величина котлованов, необходимых для протаскивания и приварки ГМТ к ремонтируемому трубопроводу из-за малой допустимой величины радиуса их изгиба, что очень важно при производстве ремонтных работ в стесненных городских условиях, в мерзлых грунтах, болотистой и горной местностях;
6. снижаются сроки ремонта трубопроводов за счет резкого снижения количества манипуляций, совершаемых с ГМТ при его монтаже в ремонтируемую трубу в экстремальных природных и техногенных условиях, а также исключения дополнительных устройств, обеспечивающих эти манипуляции;
7. при благоприятных условиях возникает возможность:
■ изъятия ГМТ из ремонтируемого участка трубопровода;
■ ремонта трубопровода одним из известных способов;
■ при положительных результатах ревизии вынутого ГМТ — возможность повторного его использования для ремонта.
Это и делает предлагаемый способ привлекательным для производства ремонтных работ, особенно срочных.
Технология ремонта по методу «труба в трубе» следующая (рисунок ниже).
В качестве ремонтной трубы используют герметичный высокопрочный металлический трубопровод 1, представляющий собой гибкую гофрированную оболочку 2 с предохранительной силовой оплеткой 3. Характерным признаком рукава 1 является высокая несущая способность, он обладает достаточной кольцевой прочностью (до 5 МПа), что дает ему возможность выдерживать наружное давление грунта, воздействию которого он может быть подвергнут при его попадании в сквозное повреждение трубопровода, а также выдерживать внутреннее рабочее давление. Другим характерным признаком такого трубопровода является гибкость, позволяющая производить предварительную его намотку на отдельную бобину с последующей транспортировкой бобины к месту ремонта.
По обеим сторонам ремонтируемого участка трубы 5 отрывают котлованы 6 и вскрывают трубопровод по длине L, определяемой из условия допускаемого радиуса R изгиба рукава (обычно R > 5d, где d — диаметр протаскиваемого гибкого трубопровода). При необходимости внутреннюю поверхность рукава очищают от отложений и ржавчины любыми известными способами. Далее через трубопровод 5 пропускают трос 7, который одним концом закрепляют к съемной головке 8, а второй его конец присоединяют к тяговому устройству, например лебедке. Тяговым устройством при помощи троса 7 гибкий трубопровод 1 меньшего диаметра протаскивают внутрь трубопровода 5, сматывая его с бобины (на схеме не показано). При этом оплетка 3, кроме всего прочего, надежно защищает гофрированную оболочку от возможных повреждений при трении о стенки трубопровода 5 в момент протаскивания. Способ позволяет также на практике применить использование отдельных предварительно подготовленных плетей трубопровода с суммарной длиной, равной длине ремонтируемого участка трубопровода, с последующим соединением их известными методами по мере втягивания в ремонтируемый трубопровод.
Схема ремонта трубопровода методом «труба в трубе»
1 — ГМТ; 2 — гофрированная оболочка; 3 — проволочная оплетка; 4 — ремонтируемый трубопровод; 5 — поврежденный участок трубопровода; 6 — котлованы; 7 — трос; 8 — съемная головка; 9 — кольцо; 10 — направляющий лоток
Давление транспортируемой среды, воздействуя на гофры ГМТ, заставляет его увеличить свою длину, что, в свою очередь,будет оказывать силовое воздействие на концы ремонтируемого трубопровода, к которым приваривается ГМТ.С целью снятия недопустимых осевых нагрузок на ремонтируемый трубопровод необходимо концевые участки разрушенной части трубопровода жестко соединить с концевыми участками неразрушенной части ремонтируемой трубы. Чтобы не повредить ГМТ о неровные края ремонтируемого трубопровода, проводят обработку кромок ручным слесарным инструментом или шлиф-машинкой.
Для исключения низкопроизводительной операции — подготовки кромки ремонтируемого трубопровода — защиту внешней поверхности протаскиваемой трубы предлагается производить путем установки защитного футляра на кромки ремонтируемого трубопровода. Футляр представляет собой устройство, состоящее из двух коаксиально соединенных основаниями цилиндров 1, надеваемое на концы ремонтируемого трубопровода с натягом или прижимаемое к наружной поверхности трубопровода хомутом 2 (рисунок ниже).
Футляр для малых (а) и больших (б) диаметров
1 — защитный материал; 2 — хомут; 3 — распорное кольцо; 4 — труба
При ремонте трубопроводов больших диаметров с целью снижения габаритов футляров они выполняются в виде листов из эластичного материала, что особенно удобно при их транспортировке и хранении. В этом случае лист вставляется в ремонтируемый трубопровод и прижимается к внутренней поверхности трубопровода распорным кольцом 3, затем лист загибается, прижимается и закрепляется на наружной поверхности ремонтируемого трубопровода хомутом 2. Причем со стороны приема вставляемой трубы футляр может не крепиться к внутренней поверхности ремонтируемого трубопровода.
Использование предлагаемых футляров эффективно при полном разрыве трубопроводов, особенно подводных переходов.
Ремонт трубопроводов и арматуры
В трубопроводах в процессе эксплуатации могут возникнуть трещины и свищи, течь хладагента и рассола во фланцевых соединениях, изломы и трещины в кронштейнах.
Трещины и свищи устраняют газовой сваркой, электросваркой или вырезают поврежденные участки и вваривают новые. Эти работы выполняют с соблюдением правил техники безопасности, т. е. после отключения ремонтируемого участка трубопровода от системы холодильной установки, освобождения его от хладагента, рассола или воды и последующей продувки.
При ремонте трубопроводов применяют труборез, позволяющий резать трубы в труднодоступных местах без демонтажа. Труборез (рис. 166) состоит из корпуса (5) в виде фигурного стакана, конического сердечника (4), рукоятки (6) и кронштейнов (3) с насаженными на них дисковыми ножами (2). Конический сердечник ввинчивают в корпус, при этом упирающиеся в его поверхность плечи кронштейнов раздвигаются, а дисковые ножи, находящиеся на противоположных плечах, прижимаются к разрезаемой трубе (1). Вращая корпус с помощью рукоятки (6), в которой смонтирован механизм с трещоткой, поворачивают кронштейны с ножами, а следовательно, и разрезают трубу. Вертикальная подача ножей на глубину резания производится дальнейшим ввинчиванием конического сердечника. Положение ножей под наклоном к оси трубы обеспечивает получение фаски в месте реза.
Рис. 166 – Схема трубореза
При разъединении фланцев труб не следует вынимать все болты. Два болта оставляют на месте и вынимают после установки остальных проверенных болтов. Для облегчения разъединения фланцев используют специальное приспособление (рис. 167). Лапки захватов (3), шарнирно закрепленные в корпусе (2), вводят в отверстия фланцев (6), распорный клин (4) направляют в зазор между фланцами и поджимают винтом с рукояткой (1). Вращением рукоятки винта разжимают фланцы на необходимое расстояние, после чего старую прокладку (5) можно удалить и на ее место поставить новую. Вращением рукоятки в обратную сторону клин освобождают, в результате чего фланцы сходятся. При сближении фланцев необходимо следить, чтобы прокладка не выпала и не перекосилась.
Рис. 167 – Приспособление для разъединения фланцев
Для изготовления прокладок используют листовой паронит толщиной 2…3 мм для аммиачных трубопроводов и 0,5…2 мм для хладоновых. Прокладки для аммиачных трубопроводов смазывают графитовой пастой (графит, разведенный в машинном масле), для хладоновых трубопроводов – глицерином. Прокладки рассольных трубопроводов изготовляют из листовой резины толщиной 3…5 мм. В соединениях водяных трубопроводов можно использовать прокладки из паронита, резины или специального картона.
Процесс ремонта запорной арматуры предусматривает очистку вентилей и задвижек от загрязнений, проточку седел и опорных гнезд, шабрение и протирку клапанов, замену сальниковых уплотнений, восстановление или замену поврежденных или изношенных шпинделей и гаек.
Наиболее ответственные операции при ремонте запорной арматуры – восстановление седел и уплотняющих поясков у клапанов и золотников вентилей. Изношенные уплотняющие баббитовые пояски клапанов запорных аммиачных вентилей восстанавливают перезаливкой с последующей проточкой на станке или опиловкой вручную. Незначительно изношенные уплотняющие детали золотниковых вентилей ремонтируют путем притирки пояска золотника к опорному кольцу седла вручную или с помощью специального приспособления. Шпиндели с изгибом или повреждением резьбы восстанавливают или заменяют.
Большое значение имеет правильная набивка и затяжка сальника. Кольца для набивки сальников аммиачных вентилей изготовляют из прожированного хлопчатобумажного шнура квадратного сечения с размерами сторон 10, 12 или 16 мм. Для сальников рассольных и водяных вентилей применяют пропитанный специальным составом хлопчатобумажный шнур или пеньковую набивку, для сальников хладоновых вентилей – асбестовый шнур, пропитанный графитом с глицерином. Чтобы стыки сальниковых колец были плотными, отмеренные куски шнура отрезают острым ножом под углом 45°. При установке в сальник стыки колец располагают вразбежку.
После ремонта проверяют герметичность арматуры при рабочем давлении. Если арматура демонтировалась для ремонта, то ее герметичность перед монтажом в вагон проверяют на специальном стенде воздухом при рабочем давлении.
По окончании ремонта трубопровод хорошо очищают и высушивают. Участки, работающие при низкой температуре, покрывают гидро- и теплоизоляцией, а затем окрашивают масляной краской.
Ремонт трубопроводов | Сварка и сварщик
Повреждения трубопроводов пара и горячен воды происходят как в сварных соединениях, так и в наружных поверхностях трубных элементов. Ремонту подлежат сварные соединения паропроводных труб равной толщины. Его выполняют тремя способами.
1. Удаление поврежденного участка без подварки мест выборки возможно при следующих условиях:
- повреждение развивалось снаружи сварного соединения;
- толщина ремонтируемого участка соединения в зоне выборки равна или больше минимально допустимой толщины трубного элемента;
- на поверхности выборки отсутствуют макродефекты, не допустимые по РД 153-34.1-003-01.
Поверхностный металл удаляют только механическим способом (вышлифовкой). Края выборки следует сглаживать с радиусом скругления не менее 30 мм.
2. Подварка места выборки с термической обработкой возможна при условиях:
- трещины развивались с наружной поверхности сварного соединения:
- протяженность местной выборки составляет не более 1/3 периметра трубы, а глубина — не более 50% расчетной толщины стенки трубы;
- кольцевая выборка по всему периметру стыка имеет глубину до 25% расчетной толщины стенки трубы;
- поверхность металла выборки соответствует требованиям РД 153-34.1-003-01 но макродефектам и микроповреждениям.
Поврежденный металл удаляют механическим способом (вышлифовкой). Заполняют выборку многослойной наплавкой кольцевыми валиками.
Термообработку после подварки ведут по режиму высокого отпуска 720-750 °С с выдержкой 1-5 ч (РД 153-34.1-003-01).
Для сварных соединении трубопроводов с температурой эксплуатации ниже 510°С удалению подлежит только поврежденный металл, а участок подварки может ограничиваться одной-двумя зонами соединения. например, металлом шва или участком шва с одной из прилегающих зон термического влияния (ЗТВ).
3. Переварке подлежат сварные соединения с трещинами, которые развивались с внутренней поверхности. Переварку выполняют в следующей последовательности: вырезают патрубок — устанавливают новый патрубок — выполняют сварку — термическую обработку.
Устранение дефектов
Для паропроводов, эксплуатируемых при температуре ниже 510°С
Дефект | Форма выборки | Рекомендации* |
Несквозные трещины в металле шва | Выборка вышлифовкой с плавными радиусами переходов | Выборку заваривают многослойными швом |
Несквозная трещина в зоне термического влияния | Выборка — по шву и в основном металле | Заварка выборки с плавным переходом к металлу старого шва и основному металлу |
Сквозная трещина в зоне тремического влияния | Глубина выборки на 2-3 мм меньше толщины стенки | Подварочный шов многослойный, с тщательной зачисткой поверхности предыдущего слоя |
*Обозначения: СШ — старый шов, ПШ — подварочный шов.
Для сварных тройников паропроводов, эксплуатируемых при температуре ниже 510 °С
Кольцевая трещина в зоне термического влияния
Поврежденный (металл удаляют шлифовкой абразивным инструментом. Многослойная сварка валиками толщиной 5 — 8 мм и шириной 12 — 20 мм
Кольцевая трещина на штуцере
Края выборки допускается оставлять на старом шве. Подварка — электродом диаметром 3 — 4 мм
Поперечные трещины в металле шва
Ширина выборки может быть ограничена размерами поврежденного металла
Ремонт стыковых соединений паропроводов, эксплуатируемых при температуре 510-560°С
Поверхностные трещины в металле шва и в зоне термического влияния
Поврежденный металл удаляют не менее чем на 5 мм глубже вершины самой удаленной трещины. Выборку заполняют кольцевыми валиками толщиной 5-8 мм и шириной 10-20 мм (при любом S/Dн).
Поверхностная трещина глубиной более четверти толщины металла
Выборку делают на глубину более 1/4 толщины стенки и дополнительно вышлифовывают кольцевое углубление глубиной 8-10 мм но периметру шириной, равной ширине выборки.
Сквозная трещина в зоне термического влияния
Перед сваркой в трешиис но концам и длине просверливают отверстия диаметром 2-3 мм для устранения ее развития, проверки глубины дефекта и лучшей переплавки поврежденного металла.
Ремонт участков паропроводных труб
![]() | ![]() |
Валиками толщиной 6-10 мм, шириной 20 — 30 мм, длиной 100 — 150 мм обратноступенчатым способом. Заплавленная выборка должна иметь выпуклость 3 — 5 мм с шириной перекрытия 8-10 мм по всему контуру в сторону основного металла наружной поверхности трубы.
Композитные материалы для ремонта трубопроводов
Многочисленные государственные и частные исследования, выполненные за последние 20 лет, исследовали потенциальные выгоды от использования композитного ремонта для структурного усиления трубопроводов. Эти исследования показали, что, когда составные ремонтные системы спроектированы и установлены правильно, они могут восстановить структурную целостность трубопровода для широкого спектра аномалий и областей применения — даже до такой степени, что уровень производительности поврежденной трубы равен уровню производительности оригинальной труба.
Исследования также показали, что плохо спроектированная или неправильно установленная композитная система не принесет никакой пользы. Это означает, что приемлемая производительность составного ремонта критически зависит от трех основных компонентов: (1) анализ неисправности, подлежащей ремонту, (2) правильная конструкция и (3) правильная установка ремонтной системы.
Большая часть исследований, связанных с композитными ремонтными системами, была сосредоточена на коррозии в трубопроводах высокого давления. Однако недавние исследования также проводились для оценки усиления более широкого диапазона аномалий трубопровода, включая изгибы морщин, ответвления, колена / изгибы, плоские дефекты и кольцевые швы.
Вопросы ремонта трубопровода
Компания Stress Engineering Services разработала методологию, которая помогает операторам трубопроводов оценивать степень серьезности аномалий трубопровода в рамках их общих программ управления целостностью. Эта методология — Инженерная программа управления целостностью (EB-IMP ® ) — объединяет существующие знания, аналитические методы, экспериментальные методы и инженерную строгость для разработки инструментов для обеспечения целостности трубопровода.
Аналогичный подход можно использовать при оценке методологий ремонта трубопровода. По мере того, как усложняется ремонт, возрастает и уровень оценки. Наличие набора конкретных требований, которые могут быть выполнены с помощью документации и проверки, имеет решающее значение для обеспечения надлежащего выполнения комплексного ремонта.
, 3X ENGINEERING, является лидером компании по обслуживанию трубопроводов с использованием композитных технологий.
В основном мы работаем в нефтегазовой отрасли, и наша экспертиза включает также электростанции и строительный сектор. Уже более 25 лет 3X разрабатывает широкий спектр продуктов для ремонта / защиты трубопроводов и выполнила множество успешных ремонтных работ по композитным трубам по всему миру. В 3X мы не только производим и продаем наши собственные продукты, но мы также предлагаем полный комплекс услуг по ремонту трубопроводов, от проектирования ремонта до монтажа на месте.
Сегодня, в лице более 40 дистрибьюторов по всему миру, мы можем быстро работать на суше, на море и под водой, чтобы укреплять и восстанавливать трубопроводы, страдающие от коррозионных дефектов и механических повреждений.
Продукты3X проходят строгие программы аттестации и тестирования, чтобы гарантировать, что они соответствуют поставленным целям в соответствии с международными стандартами. Все возможности продуктов сертифицированы третьей стороной, такой как ABS, Bureau Veritas, TUV, Lloyd’s Register … и более 10 патентов находятся на рассмотрении или одобрены во всем мире.
REINFORCEKiT ® 4D: КОМПОЗИТНОЕ РЕМОНТНОЕ РЕШЕНИЕ ДЛЯ ПРОЧНОГО ТРУБНОГО Укрепления
Разработанный в соответствии с международными стандартами ISO 24.817 и ASME PCC-2, R4D представляет собой композитную систему для ремонта обвязки трубопроводов и трубопроводов, имеющих различные дефекты (внешняя коррозия, внутренняя коррозия, сильное истирание, эрозия, точечная коррозия, механические повреждения, вмятины, трещины, утечка, сквозные дефекты стенки, дефект сварного шва, прокол …).Изготовленное из ленты Kevlar® и эпоксидной смолы, это решение разработано для восстановления первоначальной целостности труб без остановки. Это альтернатива металлическому зажиму, сварной втулке или замене трубы. R4D используется для ремонта газопроводов, ремонта нефтепроводов и водопроводов (наземных / морских / подводных).
REINFORCEKiT ® 4D SUSBEA (R4D-S): КОМПОЗИЦИОННОЕ РЕМОНТНОЕ РЕШЕНИЕ ДЛЯ РЕМОНТА ПОДВОДНОГО ТРУБОПРОВОДА
R4D-S — это система постоянного ремонта подводных труб.Основанный на технологии R4D и использующий эпоксидную смолу подводного отверждения Kevlar ® и армированную керамикой эпоксидную смолу, этот продукт укрепляет подводную трубу и стояк. Это относится как к внешней, так и к внутренней коррозии, вмятинам и утечкам в подводной среде.
TANKiT ® и REINFORCEKiT ® патч: композитные системы ремонта поврежденного бака
TANKiT ® и REINFORCEKiT ® PATCH — это две композитные системы ремонта патчей для поврежденных резервуаров и сосудов, которые подвержены внутренней или внешней коррозии и дефектам утечки.
TANKiT ® — это экстренное решение, готовое к использованию в особых случаях. REINFORCEKiT ® PATCH — это решение для прочного усиления резервуара, которое можно применять в любых условиях после проектирования и расчетов.STOPKiT ® : СИСТЕМА РЕМОНТА АВАРИЙНОЙ ТРУБЫ (EPRS) ДЛЯ ОНЛАЙН-УТЕЧКИ УПЛОТНЕНИЯ
STOPKiT ® — единственная в мире эффективная система ремонта труб, способная устранить утечку в режиме онлайн за несколько минут (применение под давлением до 80 бар, отключение не требуется).STOPKiT ® используется для ремонта газопровода, ремонта нефтепровода и ремонта водопровода (наземного / морского / подводного).
ROLLERKiT ® : КОМПОЗИТНАЯ СИСТЕМА ДЛЯ ЗАЩИТЫ ТРУБ И ПОДДЕРЖКИ ОТ КОРРОЗИИ
ROLLERKiT ® — это не только система предотвращения коррозии под опорой (CUS), но и лечебная система, которая ремонтирует опору трубопровода благодаря комбинации трех компонентов (прокладка, стекловолокно и эпоксидная смола).
ROLLERKiT ® можно устанавливать как на опоре (любой вид опоры трубы), так и на трубе (диаметры от 4 ’’ до 56 ’’), независимо от того, являются ли они новыми или старыми установками.REFLANGEKiT ® : РЕМОНТ УРОВНЯ УСТАНОВКИ И УСТАНОВКИ ПОД ДАВЛЕНИЕМ ДЛЯ SF6 GAS
REFLANGEKiT ® — это метод герметизации SF6 для фланцев, применяемый онлайн.Концепция основана на двойной оболочке, которая герметизирует протекающий фланец. Эта система неинвазивна и легко снимается без повреждений.
REINFORCEKiT ® Балка: композитный ремонт для поврежденных балок
REINFORCEKiT ® BEAM — это композитная ремонтная система, которая укрепляет конструкции (балки, опоры, опоры контактной сети …), подверженные коррозии.Изготовленная из металлических вставок, ленты Kevlar ® и эпоксидной смолы, эта технология может применяться без остановки производства или движения.
DKiT ® : ЗАЩИТА ЛУЧЕЙ ОТ КОРРОЗИИ
DKiT ® — это многослойное покрытие, предназначенное для защиты конструкций от коррозии. Это предотвращает проникновение воды, защищает от климатических воздействий и воздействий и, таким образом, обеспечивает целостность и устойчивость конструкции.
BRISTLE BLASTER ® : ПОВЕРХНОСТЬ ВЗРЫВА
3X является эксклюзивным французским дистрибьютором продукции Bristle Blaster ® . Эта технология MONTI используется для удаления коррозии и покрытий, очистки поверхности и создания шероховатой текстуры поверхности. Достигнутое качество поверхности сопоставимо с таковым при использовании других традиционных методов пескоструйной обработки