- Газогенератор на дровах — как сделать своими руками. Жми!
- Газогенератор — Энциклопедия журнала «За рулем»
- Газогенератор
- Типы газогенераторов
- Принцип работы автомобильной газогенераторной установки
- Охлаждение и грубая очистка газа
- Фильтры тонкой очистки
- Вентилятор розжига
- Смеситель
- Методы уменьшения потерь мощности двигателей газогенераторных автомобилей
- Эксплуатация автомобилей с газогенераторными установками
- Дополнительные материалы:
- Газогенератор на дровах своими руками — устройство, схема, сборка
- Автомобиль на дровах? в России — CARobka.ru
- Газогенератор на дровах своими руками — устройство, схема, сборка
- чертежи, устройство, схема, сборка, видео инструкция
- Газогенераторные установки. Переработка отходов в полезную энергию. — Портал-Энерго.ru
- Деревянный генератор на заднем дворе — Возобновляемая энергия
- машин, которые бегают по деревьям» Джона Гудмана (журнал Works That Work)
- Биомасса для производства электроэнергии | WBDG
- Вех в развитии машин: тракторы на древесном топливе — Farmers Weekly
- Газификация древесины — эффективный способ сжигания древесины
- О нас — ВСЕ Power Labs
- Исследование ТЭ (термоэлектрического) генератора, встроенного в многофункциональную дровяную печь
Газогенератор на дровах — как сделать своими руками. Жми!
Сегодня природный газ очень необходим в большинстве домов для их отопления, для приготовления еды и так далее, однако его стоимость с каждым годом увеличивается и платить по счетам становится невыгодно.Поэтому все больше людей предпочитают самостоятельно конструировать и создавать устройства, которые способны выделять газ, превращающийся в различные виды энергии. Преимуществ у такого способа достаточно много. Наибольшее распространение приобрели газогенераторы, работающие на дровах.
Принцип работы
Любой пиролизный газогенератор представляет собой большой металлический резервуар из закаленной стали. В такую печь загружается топливо, то есть дрова.Начинается горение в присутствии небольшого количества кислорода, чтобы дрова не сгорели полностью, так как горение представляет собой процесс взаимодействия с кислородом, благодаря которому выделяется колоссальное количество энергии в виде огня.
В процессе взаимодействия древесины с кислородом образуется:
- углекислый газ или диоксид углерода;
- угарный газ или моноксид углерода;
- чистый водород;
- метан или природный газ, который как раз таки необходим;
- другие углеводородные газы.
Температура в печи должна быть очень высокой и постоянно поддерживаться. После сгорания выделившийся газ направляется на фильтрацию в специальное устройство — циклон, происходит охлаждение, в результате чего различные примеси и мелкие частицы убираются из смеси, в итоге получается практически чистый метан, который затем смешивается с кислородом.
Полученная смесь является необходимым топливом, которое можно использовать для различных целей.
Применение
- Раньше газгены применялись в автомобилестроении, во время Великой Отечественной войны такие генераторы устанавливались на многие легковые автомобили-полуторки и грузовики марки ЗИС. Двигатели внутреннего сгорания, работающие на природном газе, были незаменимы и удобны из-за несложного устройства и дешевизны.
- Сегодня газогенераторные установки применяются для отопления домов и жилищ.
- Для выработки электроэнергии с помощью различных турбинных установок или электрогазогенераторов.
- До сих пор некоторые люди устанавливают на свои жигули подобные агрегаты. Машина при этом совершенно исправна и не требуют больших затрат. Также из-за низкого загрязнения воздуха по сравнению с нефтяным топливом, многие люди все больше переходят на автомобильные газогенераторы для ДВС.
- В промышленности применяются газогенераторы, работающие на каменном угле, который может давать большее количество энергии.
Преимущества и недостатки установки
Основными преимуществами подобного оборудования являются:
- Очень высокий КПД, достигающий 96 %.
- Процесс горения является достаточно длинным, к примеру, древесина может гореть в течение суток, а уголь более недели.
- Полное сгорание всего топлива, в результате чего отсутствует необходимость в частой уборке котлов.
- Возможность полной автоматизации.
- Низкие затраты на выделение энергии.
- Низкие выбросы вредных газов в атмосферу.
- Некоторые люди используют в качестве топлива навоз, который является весьма экологически-чистым и дешевым.
Однако газогенераторные котлы имеют и свои недостатки:
- газогенерация предполагает неизменное взаимодействие с кислородом, из-за чего требуется устанавливать специальные вентиляторы для непрерывной подачи воздуха в печь;
- необходимо безостановочно поддерживать постоянную температуру, чтобы она не падала;
- возможность образования дегтя, загрязняющего печь.
Как соорудить самостоятельно
Схема газогенератора. (Для увеличения нажмите)
Сделать газовой дровяной генератор своими руками не так уж и сложно.
Для начала необходимо разобраться с принципом его работы, устройством, схемой, затем следует начертить чертежи будущего источника энергии и начинать подбор необходимых материалов.
Каждый газовый генератор должен включать в себя:
- опорную конструкцию;
- бункер, в котором будет находиться древесное или другое топливо;
- камерой, где происходит процесс горения;
- фурмы для подачи дутья;
- воздухораспределительные коробки;
- газопровод;
- циклон для фильтрации выходящего газа от пыли и мелких частиц и различных поперечных решеток, используемых для очистки;
- охладитель;
- баллон для сбора газа и его дальнейшего распределения;
- колосниковую решетку для поддержки угля.
Также gazgen можно устанавливать на моторы авто и тракторов, требующие много топлива.
Домашние бытовые мини-теплогенераторы все чаще встречаются в домах из-за простоты устройства и низкой цены монтажа и обслуживания, потому что древесина является очень доступным видом топлива.
Также можно устанавливать небольшие электростанции вместе с парогенераторами, которые будут вращать турбину, для получения электричества. Процесс изготовления самодельных агрегатов не очень трудоёмок.
Советы от мастеров
Мастера, имеющие большой опыт работы с газогенераторами, могут дать несколько важных советов:- Перед установкой необходимо создать чертеж будущей конструкции, оценить примерные затраты. Если они будут больше стоимости промышленного агрегата, то лучше сразу купить готовое устройство.
- Топить можно не только древесиной, но и опилками, старой древесной мебелью, торфом и каменным углем.
- При установке подобного генератора на автомобиль нужно проконсультироваться со специалистом по поводу размеров и автоматизации процессов, происходящих внутри котла.
Смотрите видео, в котором пользователь подробно разъясняет конструкцию газогенератора, сделанного своими руками:
Газогенератор — Энциклопедия журнала «За рулем»
Газогенератор
Газогенератор – это установка для получения горючего газа из твердого топлива. В качестве твердого топлива, как правило, применяются местные ресурсы: уголь, торф, древесина, солома, а так же отходы деревообрабатывающих производств. Превращение твердого топлива в газообразное называется «газификацией» и заключается в сжигании топлива с поступлением количества кислорода воздуха или водяного пара, недостаточном для полного сгорания.
Сегодня газогенераторные установки используют для получения пара, или горячего воздуха для различных технологических процессов, а так же в составе отопительных систем. Однако в 30-е – 40–е годы прошлого века газогенераторы с успехом применяли на транспорте: массовая эксплуатация автомобилей на древесных чурках обещала сберечь жидкое топливо для более важных нужд — тонны сэкономленного бензина можно было направить в вооруженные силы или авиацию.
В 1923 году профессором Наумовым была разработана газогенераторная установка для 3-тонного грузовика, способная работать на древесном угле или на антраците. Установка была испытана в стационарных условиях совместно с 4-цилиндровым бензиновым двигателем Berliet L 14 мощностью 35 л.с. В 1928 году FIAT-15Ter с газогенератором Наумова совершил пробег по маршруту Ленинград – Москва – Ленинград. Первая половина 30-х годов отмечена многочисленными исследованиями, направленными на выявление оптимальной конструкции газогенераторной установки. Статьи об испытательных автопробегах и новых разработках постоянно появлялись в прессе, в том числе и в журнале «За Рулем».
В подавляющем большинстве это были установки для грузового транспорта, что не удивительно – ведь основной транспортной единицей народного хозяйства в период индустриализации являлся грузовик, а не легковой автомобиль. Тем не менее, следует упомянуть созданный в 1935 году ГАЗ-А с газогенераторной установкой Автодор – III, а также ГАЗ-М1 с газогенератором НАТИ-Г12, на котором в сентябре 1938 года был установлен рекорд скорости для газогенераторного автомобиля 60,96 км/ч. Первым серийным газогенераторным автомобилем являлся ЗИС-13, но подлинно массовыми «газгенами» стали ГАЗ-42, ЗИС-21 и УралЗИС-352.
С + О2 = СО2 — это полное сгорание топлива, которое сопровождается выделением углекислого газа СО2;
и С + (1/2)О2 = СО — это неполное сгорание, в результате которого образуется горючий газ – оксид углерода СО.

Оба этих процесса происходят в так называемой «зоне горения» газогенератора.
Оксид углерода СО образуется также при прохождении углекислого газа СО
С + СО2 = 2СО
В процессе участвует часть влаги топлива (или влага, подведенная извне) с образованием углекислого газа СО2, водорода Н2, и горючего оксида углерода СО.
С + Н2О = СО + Н2
СО + Н2О = СО2 + Н2
Зону, в которой протекают три описанных выше реакции называют «зоной восстановления» газогенератора. Обе зоны – горения и восстановления – несут общее название «активная зона газификации».
Примерный состав газа, полученного в газогенераторе обращенного процесса газификации при работе на древесных чурках абсолютной влажностью 20%, следующий (в % от объема):
— водород Н2 16,1%;
— углекислый газ СО2 9,2%;
— оксид углерода СО 20,9%;
— метан СН4 2,3%;
— непредельные углеводороды СnHm (без смол) 0,2%;
— кислород О2 1,6%;
— азот N2 49,7%
Итак, генераторный газ состоит из горючих компонентов (СО, Н2, СН4, СnHm) и балласта (СО2, О2, N2, Н2О)
Топливо для газогенераторов
В качестве твердого топлива в газогенераторных установках могут быть использованы древесные чурки, древесный уголь, торф, бурый уголь, каменный уголь.
На территории СССР наиболее распространенным и доступным твердым топливом была древесина, по этому большую часть газогенераторного транспорта составляли автомобили с установками, работающими на древесных чурках.
Для газификации в автомобильных газогенераторах древесину распиливали на чурки длиной от 4 до 7 см, и шириной и высотой от 3 до 6 см. Абсолютная влажность готового твердого топлива не более 22%.
Менее распространены были древесно-угольные газогенераторные установки. Для их эксплуатации рекомендовалось использовать угли древесины твердых пород. Угли древесины мягких пород, склонные к крошению, допускалось применять с добавлением не менее 50% углей древесины твердых пород.
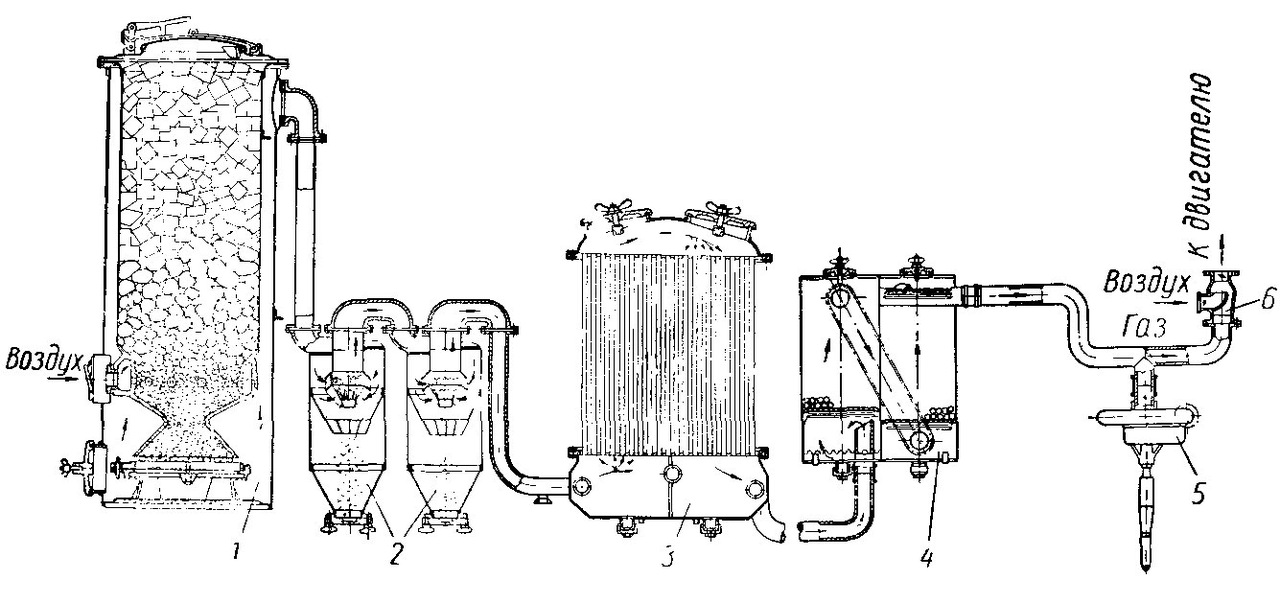
В зависимости от содержания смол и золы твердые сорта топлив для газогенераторов разделяли на смолистые (битуминозные) малозольные (золы до 4%) и многозольные (золы более 4%), а также на безсмольные, или тощие (небитуминозные) малозольные (золы до 4%) и многозольные (золы более 4%). Для разных видов топлива были разработаны газогенераторы соответствующих типов:
— газогенераторы прямого процесса газификации;
— газогенераторы обращенного (обратного, или «опрокинутого») процесса газификации;
— газогенераторы поперечного (горизонтального) процесса газификации.
Типы газогенераторов
Газогенераторы прямого процесса газификации
Основным преимуществом газогенераторов прямого процесса являлась возможность газифицировать небитуминозные многозольные сорта твердого топлива – полукокс и антрацит.
В газогенераторах прямого процесса подача воздуха обычно осуществлялась через колосниковую решетку снизу, а газ отбирался сверху.
Над зоной горения, занимавшей лишь 30 – 50 мм высоты слоя топлива, находилась зона восстановления. Так как восстановительные реакции протекают с поглощением тепла, то температура в зоне восстановления снижалась до 700 – 900 С.
Выше активное зоны находились зона сухой перегонки и зона подсушки топлива. Эти зоны обогревались теплом, выделяемым в активной зоне, а также теплом проходящих газов в том случае, если газоотборный патрубок располагался в верхней части генератора. Обычно газоотборный патрубок располагали на высоте, позволяющей отвести газ непосредственно на его выходе из активной зоны. Температура в зоне сухой перегонки составляла 150 – 450 С, а в зоне подсушки 100 – 150 С.
В газогенераторах прямого процесса влага топлива не попадала в зону горения, поэтому воду в эту зону подводили специально, путем предварительного испарения и смешивания с поступающим в газогенератор воздухом.
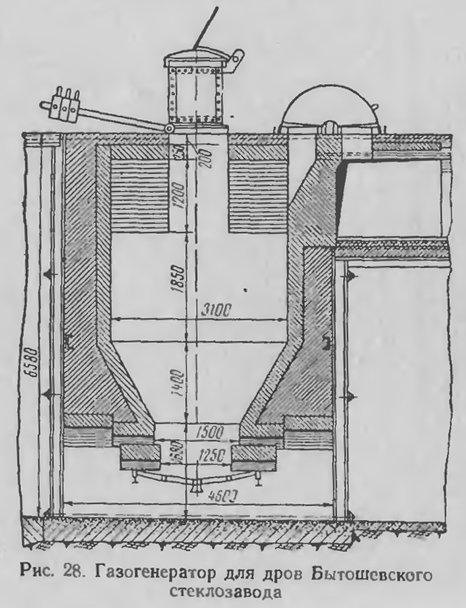
Подача водяного пара в газогенератор должна производиться пропорционально количеству сжигаемого в газогенераторе топлива. Существовало несколько способов регулировки подачи пара в камеру газификации:
— механический способ, когда вода подавалась в испаритель газогенератора с помощью насоса, приводимого в действие от двигателя и имевшего перепускной кран, который был связан с дроссельной заслонкой. Таким образом, количество воды, подаваемой в газогенератор, изменялось в зависимости от числа оборотов и нагрузки двигателя;
— гидравлический способ, когда расход воды регулировался иглой, перекрывавшей сечение жиклера, и связанной с мембраной, на которую действовала разность давлений до и после диафрагмы, установленной в газопроводе, соединявшим газогенераторную установку с двигателем;
— пневматический способ, при котором вода подавалась в испаритель газогенератора вместе с воздухом, засасываемым через обычный карбюратор.

В конструкции газогенератора ЦНИИАТ-АГ-2 был использован принцип центрального подвода воздуха и центрального отбора газа. Газогенератор состоял из корпуса, конической камеры газификации и зольника. Верхняя часть корпуса служила бункером для топлива и имела цилиндрический бак для воды. Трубка для подачи воды располагалась внутри газогенератора, бак подогревался теплом сгорающего топлива. Это обеспечивало надежную работу установки в зимнее время. Камера газификации представляла собой горловину конической формы, которая снизу была окружена рубашкой, заполненной водой для образования водяного пара. Необходимый уровень воды в рубашке поддерживался при помощи поплавкового устройства. Количество образовавшегося пара изменялось в зависимости от теплового режима газогенератора.
Воздух, засасываемый в газогенератор через подогреватель, смешивался с паром и поступал в камеру газификации через щель, образованную рубашкой и поворотной плитой. При вращении плиты рукояткой, расположенной снаружи под днищем газогенератора, ребра, имеющиеся на плите, срезали шлак и сбрасывали его в зольник.
Установки прямого процесса газификации не получили распространения, так как, во-первых, были непригодны для газификации самого распространенного твердого топлива — древесины, а во-вторых, потому что приспособления, необходимые для хранения, дозировки и испарения воды существенно усложняли конструкцию газогенератора.
Газогенераторы обращенного (опрокинутого) процесса газификации.
Газогенераторы обращенного процесса были предназначены для газификации битуминозных (смолистых) сортов твердого топлива – древесных чурок и древесного угля.
В генераторах этого типа воздух подавался в среднюю по их высоте часть, в которой и происходил процесс горения. Отбор образовавшихся газов осуществлялся ниже подвода воздуха. Активная зона занимала часть газогенератора от места подвода воздуха до колосниковой решетки, ниже которой был расположен зольник с газоотборным патрубком.
Зоны сухой перегонки и подсушки располагались выше активной зоны, поэтому влага топлива и смолы не могли выйти из газогенератора, минуя активную зону. Проходя через зону с высокой температурой, продукты сухой перегонки подвергались разложению, в результате чего количество смол в выходящем из генератора газе было незначительным. Как правило, в газогенераторах обращенного процесса газификации горячий генераторный газ использовался для подогрева топлива в бункере. Благодаря этому улучшалась осадка топлива, так как устранялось прилипание покрытых смолой чурок к стенкам бункера и тем самым повышалась устойчивость работы генератора.
Газогенератор ГАЗ-42 состоял из цилиндрического корпуса 1, изготовленного из 2-миллиметровой листовой стали, загрузочного люка 2 и внутреннего бункера 3, к нижней части которого была приварена стальная цельнолитая камера газификации 8 с периферийным подводом воздуха (через фурмы). Нижняя часть газогенератора служила зольником, который периодически очищался через зольниковый люк 7.
Воздух под действием разрежения, создаваемого двигателем, открывал обратный клапан 5 и через клапанную коробку 4, футорку 6, воздушный пояс и фурмы поступал в камеру газификации 8. Образующийся газ выходил из-под юбки камеры 8, поднимался вверх, проходил через кольцевое пространство между корпусом и внутренним бункером и отсасывался через газоотборный патрубок 10, расположенный в верхней части газогенератора. Равномерный отбор газа по всей окружной поверхности газогенератора обеспечивался отражателем 9, приваренным к внутренней стенке корпуса 1 со стороны газоотборного патрубка 10.
Для более полного разложения смол, особенно при малых нагрузках газогенератора, в камере газификации было предусмотрено сужение – горловина. Помимо уменьшения смолы в газе, применение горловины одновременно приводило к обеднению газа горючими компонентами сухой перегонки. На величину получаемой мощности влияла согласованность таких параметров конструкции газогенератора, как диаметр камеры газификации по фурменному поясу, проходное сечение фурм, диаметр горловины и высота активной зоны.
Газогенераторы обращенного процесса применяли и для газификации древесного угля. Вследствие большого количества углерода в древесном угле процесс протекал при высокой температуре, которая разрушительно действовала на детали камеры газификации. Для повышения долговечности камер газогенераторов, работающих на древесном угле, применяли центральный подвод воздуха, снижавший воздействие высокой температуры на стенки камеры газификации.
Камера газогенератора НАТИ-Г-15), изготовленная из 12-миллиметровой листовой стали, имела вид усеченного конуса. В средней части газогенератора была смонтирована воздухоподводящая фурма. Она представляла собой чугунную отливку грушевидной формы. Внутри отливки – лабиринт для подвода воздуха в газогенератор. В нижней части камеры газификации располагалась колосниковая решетка, которую вынимали через зольниковый люк при чистке и разгрузке газогенератора. Образовавшийся в камере газификации газ проходил сквозь колосниковую решетку, поднимался вверх между корпусом газогенератора и камерой и отсасывался через газоотборный патрубок. Газогенератор был предназначен для работы на крупном древесном угле, с размером кусков 20 мм – 40 мм.
Газогенераторные установки обращенного процесса газификации, работавшие на древесных чурках, получили наибольшее распространение.
Газогенераторы поперечного (горизонтального) процесса газификации.
В газогенераторах поперечного процесса воздух с высокой скоростью дутья подводился через фурму, расположенную сбоку в нижней части. Отбор газа осуществлялся через газоотборную решетку, расположенную напротив фурмы, со стороны газоотборного патрубка. Активная зона была сосредоточена на небольшом пространстве между концом формы и газоотборной решеткой. Над ней располагалась зона сухой перегонки и выше – зона подсушки топлива.
Отличительной особенностью газогенератора этого типа являлась локализация очага горения в небольшом объеме и ведение процесса газификации при высокой температуре. Это обеспечивало газогенератору поперечного процесса хорошую приспособляемость к изменению режимов и снижает время пуска.
Газогенератор представлял собой цилиндрический бункер, нижняя часть которого, выполненная из листовой стали толщиной 6 – 8 мм, образовывала камеру газификации. В верхней части бункера был расположен люк для загрузки топлива.
Скорость дутья определялась проходным сечением воздухоподводящей фурмы. Фурма служила наиболее ответственной и сложной деталью газогенератора. Она была глубоко погружена в слой топлива и находилась в зоне высокой температуры – непосредственно около носка фурмы температура достигает 1200 – 1300 С. Высокие температурные нагрузки требовали применять водяное охлаждение фурмы. Конструктивно охлаждение фурмы являлось частью системы водяного охлаждения двигателя, или представляло собой самостоятельную систему, питаемую от отдельного бачка.
Воздухоподводящая фурма газогенератора НАТИ-Г-21 состояла из бронзового корпуса 1 и медных трубок 2 и 3 диаметром 20 и 40 мм, образующих водяную рубашку. Тыльная часть наружной трубки 3 была приварена к корпусу 1 фурмы, а носовая часть обварена медью и соединялась с внутренней трубкой 2, свободный конец которой при нагревании фурмы мог перемещаться в сальнике 4. Затяжкой накидной гайки 5 обеспечивалась герметичность водяной рубашки. Вода подавалась через нижний штуцер корпуса фурмы и после прохождения водяной рубашки отводилась через верхний штуцер. Для того чтобы поток воды достиг носка фурмы, к наружной поверхности внутренней трубки параллельно ее оси были приварены две перегородки, направлявшие поток воды к носу фурмы.
Другой важной деталью газогенераторов поперечного процесса газификации служила газоотборная решетка. Газоотборную решетку изготавливали из простой углеродистой или легированной стали толщиной 8 – 12 мм. Ее штамповали в виде изогнутого листа с отбортованными краями или изготавливали в виде плоской пластины. В последнем случае для монтажа решетки в газогенераторе предусматривали специальное гнездо. Отверстия в решетке для прохода газа делали круглыми, диаметром 10 – 12 мм, с раззенковкой со стороны выхода газа. Иногда отверстия делали овальными; в этом случае большая ось овала располагалась горизонтально, что позволяло увеличить проходное сечение без опасности проскакивания за решетку кусков угля (при наклонном расположении решетки).
Этот газогенератор, так же как и газогенератор прямого процесса, был непригоден для газификации топлив с большим содержанием смол. Эти установки применяли для древесного угля, древесноугольных брикетов, торфяного кокса.
Принцип работы автомобильной газогенераторной установки
Автомобильная газогенераторная установка состояла из газогенератора, грубых очистителей, тонкого очистителя, вентилятора розжига и смесителя. Воздух из окружающей среды засасывался в газогенератор тягой работающего двигателя. Этой же тягой выработанный горючий газ «выкачивался» из газогенератора и попадал сначала в грубые очистители охладители, затем – в фильтр тонкой очистки. Перемешавшись в смесителе с воздухом, газо-воздушная засасывалась в цилиндры двигателя.
Охлаждение и грубая очистка газа
На выходе из газогенератора газ имел высокую температуру и был загрязнен примесями. Чтобы улучшить наполнение цилиндров «зарядом» топлива, газ требовалось охладить. Для этого газ пропускался через длинный трубопровод, соединявший газогенератор с фильтром тонкой очистки, или через охладитель радиаторного типа, который устанавливался перед водяным радиатором автомобиля.
Охладитель радиаторного типа газогенераторной установки УралЗИС-2Г имел 16 трубок, расположенных вертикально в один ряд. Для слива воды при промывке охладителя служили пробки в нижнем резервуаре. Конденсат вытекал наружу через отверстия в пробках. Два кронштейна, приваренные к нижнему резервуару, служили для крепления охладителя на поперечине рамы автомобиля.
В качестве простейшего очистителя использовался циклон. Газ поступал в очиститель через патрубок 1, распологавшийся касательно к корпусу циклона. Вследствие этого газ получал вращательное движение и наиболее тяжелые частицы, содержащиеся в нем, отбрасывались центробежной силой к стенкам корпуса 3. Ударившись о стенки, частицы падали в пылесборник 6. Отражатель 4 препятствовал возвращению частиц в газовый поток. Очищенный газ выходил из циклона через газоотборный патрубок 2. Удаление осадка осуществлялось через люк 5.
Чаще всего в автомобильных газогенераторных установках применяли комбинированную систему инерционной очистки и охлаждения газа в грубых очистителях – охладителях. Осаждение крупных и средних частиц в таких очистителях осуществлялось путем изменения направления и скорости движения газа. При этом одновременно происходило охлаждение газа вследствие передачи тепла стенкам очистителя. Грубый очиститель-охладитель состоял из металлического кожуха 1, снабженного съемной крышкой 2. Внутри кожуха были установлены пластины 3 с большим количеством мелких отверстий, расположенных в шахматном порядке. Газ, проходя через отверстия пластин, менял скорость и направление, а частицы, ударяясь о стенки, оседали на них или падали вниз.
Грубые охладители-очистители последовательно соединяли в батареи из нескольких секций, причем каждая последующая секция имела большее количество пластин. Диаметр отверстий в пластинах от секции к секции уменьшался (РИСУНОК 5Г).
Фильтры тонкой очистки
Для тонкой очистки газа чаще всего применяли очистители с кольцами. Очистители этого типа представляли собой цилиндрический резервуар, корпус 3 которого был разделен на три части двумя горизонтальными металлическими сетками 5, на которых ровным слоем лежали кольца 4, изготовленные из листовой стали. Процесс охлаждения газа, начавшись в грубых очистителях – охладителях, продолжался и в фильтре тонкой очистки. Влага конденсировалась на поверхности колец и способствовала осаживанию на кольцах мелких частиц. Газ входил в очиститель через нижнюю трубу 6, и пройдя два слоя колец, отсасывался через газоотборную трубу 1, соединенную со смесителем двигателя. Для загрузки, выгрузки и промывки колец использовали люки на боковой поверхности корпуса.
Применялись конструкции, в которых в качестве фильтрующего материала использовалась вода или масло. Принцип работы водяных (барботажных) очистителей заключался в том, что газ в виде маленьких пузырьков проходил через слой воды и таким образом избавлялся от мелких частиц.
Высота барботажного слоя воды в очистителе установки ЦНИИАТ-УГ-1 повышалась от нуля до максимума (100 мм – 120 мм) по мере увеличения отбора газов. Благодаря этому обеспечивалась устойчивая работа двигателя на холостых оборотах и хорошая очистка газа на больших нагрузках. Предварительно охлажденный газ поступал расположенную по центру очистителя газораздаточную коробку. Боковые стенки коробки имели два ряда отверстий диаметром 3 мм. Отверстия были расположены наклонно от уровня воды до нижнего края стенок, погруженных в воду на 70 мм. Четыре отверстия, расположенные выше уровня воды, служили для обеспечения подачи газа на холостом ходу. С ростом числа оборотов эти отверстия перекрывались водой. В пространстве над газораздаточной коробкой при увеличении нагрузки создавалось разряжение, и уровень воды снаружи коробки повышался, а внутри, соответственно – понижался. При этом газ, поступая внутрь коробки, попадал в отверстия, расположенные над уровнем воды, и уже в виде пузырьков поднимался вверх, сквозь наружный водяной столб. Очистившись в воде, газ проходил через кольца, насыпанные на сетки по обе стороны газораздаточной решетки, и направлялся во вторую секцию очистителя, где вторично пропускался через погруженную в воду гребенку окончательно очищался в слое колец.
Вентилятор розжига
В автомобильных установках розжиг газогенератора осуществлялся центробежным вентилятором с электрическим приводом. При работе вентилятор розжига просасывал газ из газогенератора через всю систему очистки и охлаждения, поэтому вентилятор старались разместить ближе к смесителю двигателя, чтобы процессе розжига заполнить горючим газом весь газопровод.
Вентилятор розжига газогенераторной установки автомобиля УралЗИС-352 состоял из кожуха 6, в котором вращалась соединенная с валом электродвигателя крыльчатка 5. Кожух, отштампованный из листовой стали, одной из половин крепился к фланцу электродвигателя. К торцу другой половины был подведен газоотсасывающий патрубок газогенератора 4. Газоотводящий патрубок 1. Для направления газа при розжиге в атмосферу и при работе подогревателя – в подогреватель к газоотводящему патрубку был приварен тройник 3 с двумя заслонками 2.
Смеситель
Образование горючей смеси из генераторного газа и воздуха происходило в смесителе. Простейший двухструйный смеситель а представлял собой тройник с пересекающимися потоками газа и воздуха. Количество засасываемой в двигатель смеси регулировалось дроссельной заслонкой 1, а качество смеси – воздушной заслонкой 2, которая изменяла количество поступающего в смеситель воздуха.
Эжекционные смесители б и в различались по принципу подвода воздуха и газа. В первом случае газ в корпус смесителя 3 подводился через сопло 4, а воздух засасывался через кольцевой зазор вокруг сопла. Во втором случае в центр смесителя подавался воздух, а по периферии – газ.
Воздушная заслонка обычно была связана с рычагом, установленном на рулевой колонке автомобиля и регулировалась водителем вручную. Дроссельной заслонкой водитель управлял с помощью педали.
Методы уменьшения потерь мощности двигателей газогенераторных автомобилей
Бензиновые двигатели, переведенные на генераторный газ без каких-либо переделок, теряли 40-50% мощности. Причинами падения мощности являлись, во-первых, низкая теплотворность и медленная скорость горения газовоздушной смеси по сравнению с бензовоздушной, а во-вторых, ухудшение наполнения цилиндров как за счет повышенной температуры газа, так и за счет сопротивления в трубопроводах, охладителе и фильтре газогенераторной установки.
Для уменьшения влияния указанных причин в конструкцию двигателей были внесены изменения. В связи с тем что газовоздушная смесь обладает высокой детонационной стойкостью, была увеличена степень сжатия. Сечение впускного трубопровода было увеличено. Для устранения подогрева газовоздушной смеси и уменьшения потерь давления впускной трубопровод устанавливали отдельно от выпускного. Эти меры позволяли сократить потери мощности до 20-30%.
Эксплуатация автомобилей с газогенераторными установками
Эксплуатация автомобилей с газогенераторными установками имела свои особенности. В силу повышенной степени сжатия работа двигателя на бензине под нагрузкой допускалась лишь в крайних случаях и кратковременно: например, для маневрирования в гаражных условиях.
Инструкция категорически запрещала перевозить на газегенераторных автомобилях огнеопасные и легковоспламеняющиеся вещества, и тем более въезжать на территории, где не допускалось пользоваться открытым огнем – например, топливные склады. Разжигать газогенератор разрешалось только на открытой площадке.
Розжиг газогенератора осуществлялся факелом, тягу в при этом создавал электрический вентилятор. Газ, прокачиваемый вентилятором в процессе розжига, через патрубок выходил в атмосферу. Момент готовности газогенератора к работе определяли, поджигая газ у отверстия выходного патрубка – пламя должно было гореть устойчиво. По окончании розжига вентилятор выключали и пускали двигатель.
При неисправности вентилятора газогенератор можно было разжечь самотягой. Для этого зольниковый и загрузочный люки газогенератора открывали, а под колосниковую решетку подкладывали «растопку» — стружку, щепу, ветошь. Под действием естественной тяги пламя распространялось по всей камере. После розжига люки закрывали и пускали двигатель.
Розжиг газогенератора при помощи работающего на бензине двигателя допускался инструкцией лишь в аварийных случаях, так как при этом возникала опасность засмоления двигателя.
При движении автомобиля водитель вынужден был принимать во внимание инерцию газогенераторного процесса. Чтобы обеспечить запас мощности, необходимо было поддерживать отбор газа, близкий к максимальному. Для преодоления трудных участков рекомендовалось заранее переходить на понижающие передачи и поднимать обороты двигателя, а так же обогащать газо-воздушную смесь, прикрывая воздушную заслонку смесителя.
В отличие от бензиновых, газогенераторные автомобили требовали более частого пополнения топливом. Догрузку топлива в бункер производили в течение дня во время погрузочно-разгрузочных работ или стоянок.
Обслуживание газогенераторной установки было трудоемким. Чистка зольника газогенератора автомобиля УралЗИС-352 предусматривалась через каждые 250 – 300 км. Через 5000 – 6000 км газогенератор требовал полной чистки и разборки. Трубы охладителя рекомендовалось прочищать раз в 1000 км специальным скребком, входившим в комплект инструмента для обслуживания газогенераторной установки. Нижний слой колец фильтра тонкой очистки необходимо было промывать, выгрузив из фильтра на поддон, через 2500 – 3000 км пробега автомобиля. Верхний слой колец допускалось промывать каждые 10 000 км струей воды через люк в корпусе фильтра.
Оксид углерода СО опасен для человеческой жизни, по этому перед проведением работ по обслуживанию требовалось открыто все люки проветрить газогенераторную установку в течение 5 – 10 минут.
Дополнительные материалы:
За Рулем 1931 № 20 Автомобили на дровах
За Рулем 1933 № 16 Автомобили на дровах
За Рулем 1934 № 17 Газогенератор профессора Карпова
За Рулем 1935 № 1 Пробег газогенераторных автомашин
За Рулем 1935 № 2 Новый четырехосный газогенераторный автобус
За Рулем 1935 № 3 Первый автодоровский газогенератор
За Рулем 1935 № 14 Новый газогенератор для автомобиля ГАЗ-АА
Газогенератор на дровах своими руками — устройство, схема, сборка
7 февраля, 2014. Прочитано 27014 раз(а)
С каждым годом все больше внимания во всех сферах промышленности уделяется разработке и внедрению новых технологий, помогающих сбережению электроэнергии. Сфера производства отопительного оборудования так же не осталась в стороне и провела ряд исследований, позволивших сделать важные открытия и построить газогенератор на дровах. В таком приспособлении в результате сгорания в герметичной камере древесины выделяются газы, которые тоже сгорают, выделяя дополнительное тепло. Таким образом, используемое топливо полностью сжигается с максимальной отдачей тепла. Благодаря высокому коэффициенту теплоотдачи газогенераторного котла на дровах является экономным обогревающим приспособлением.
Газогенераторный котел на дровах можно сделать и собственноручно, однако перед тем как приступить к его изготовлению, необходимо тщательно изучить его принцип работы. Изучив устройство газогенератора на дровах, можно обеспечить наиболее эффективную и безопасную работу котла.
Устройство и схема газогенераторного котла на дровах
Растопка газогенераторного котла аналогична процессу растопки обычной печи – точно так же укладывается топливо, непосредственно выполняется растопка, воздушная заслонка закрывается вполовину для предупреждения поступления кислорода внутрь камеры сгорания.
Устройство и принцип работы газогенератора является весьма простым. Котел состоит из двух камер, размещенных в одном корпусе. Одна камера предназначена для сжигания дров или иного твердого топлива (брикетов, соломы и пр.), другая – для сжигания выделяемого вследствие сгорания дров газа. Температура подымается. Горячий воздух циркулирует по воздухоотводам, захватывая холодный из нижних сопел, который также в процессе топки нагревается и вздымается вверх, что и отображает предоставленная схема газогенератора на дровах.
Благодаря такой конвекции помещение крайне быстро нагревается и длительное время остается теплым.
Изготовление газогенератора на дровах своими руками
Представленная выше схема воспроизводит принцип действия простого котла, поэтому сооружать газогенератор на дровах своими руками необходимо, не только опираясь на данные о работе составляющих элементов приспособления, которые изображены на чертеже, но и подробно ознакомившись с процессом работы уже готового устройства.
Прежде ознакомтесь с видео об устройстве самодельного газогенератора:
В качестве корпуса для будущего газогенератора служит металлическая бочка. В самой верхней части корпуса устанавливается бункер объемом 0,6 – 0,7 м3 для загрузки древесины.
Для расчета габаритов этого бункера, у нас на сайте есть калькулятор расчета бочки и других цилиндрических емкостей.
Также вверху газогенератора располагается юбочка, где изначально находится холодный воздух.
Образующийся в результате горения газ, вдуваясь через фурмы, проходит кольца грубой очистки.
Очищенный газ забирается из юбочки, охлаждается через фильтр охлаждения и выпускается. Фильтр охлаждения представляет собой зигзаг труб с металлическими кольцами, расположенными внутри.
На фильтре устанавливается приспособление с краном для сбора и спуска конденсата, образующегося при использовании сырой древесины.
Если дрова очень влажные, то газ, попадая в юбочку и контактируя с холодным воздухом, оставляет много воды, которая проходит через сепаратор и сливается по ленте слива. Сепаратор изготавливается из трубы, в которую вставляется ребристая пластина.
Если необходим сухой воздушный газ, то вентиль слива перекрывается, а вентиль на газовой трубе, расположенной за сепаратором, открывается. Газ, попадая из маленькой трубы в большую трубу сепаратора, оставляет капли росы и направляется в зону горения.
При желании в нижней части корпуса можно делается емкость для нагрева воды. Такая вода будет нагреваться с помощью обратного горючего газа, который в процессе нагрева будет дополнительно охлаждаться.
При необходимости образующийся в процессе горения газ можно опять-таки использовать как дополнительное горючее для нагрева, повернув определенный вентиль и направив горючий газ в дополнительную зону горения. Тогда выпускаться через фильтр охлаждения будет только оставшийся газ СО2.
Остались вопросы? Создайте тему за 2 минуты у нас на форуме. Получите ответ Прораба и других пользователей. Это бесплатно. Без регистрации.
Рекомендуем вам еще:
Автомобиль на дровах? в России — CARobka.ru
С момента начала производства автомобилей люди начали задумываться о разных источниках энергии. Первые автомобили, ввиду отсутствия альтернатив, работали на пару, затем появились редкие образцы автомобилей, работающие на основе электроэнергии, и только спустя десятки лет был изобретен двигатель внутреннего сгорания.
Однако поиски новых источников энергии для автомобилей не оканчиваются и по сегодняшний день. Инженеры преследуют разные цели: одних заботят экологические аспекты, другие грезят разрушить нефтяную монополию. Но в большинстве своем изобретатели ищут более экономичный вид энергии.
Многократно в различных источниках проскальзывали новости об умельцах из глубинки, которые дорабатывали свои авто для движения на основе спиртосодержащих продуктов или подсолнечного масла. Сегодня же речь пойдет о газогенераторах, основанных на горении. Хотя уже в 30-х годах люди пользовались этой технологией, сегодня находится масса любителей данной альтернативы ДВС.
Как это работает?
В транспортное средство устанавливается специальный газогенератор, в котором под воздействием высокой температуры происходит сложный термохимический процесс, в результате которого топливо расщепляется на простейшие элементы, делящиеся на полезный газ — этилен (C2h5), метан, угарный газ, водород, и бесполезный — азот, двуокись углерода.
После процесса расщепления в топке происходит охлаждение, фильтрация газа и его поступление в ДВС.
Что может быть использовано как топливо?
В основном используются дрова или древесный уголь, но список не ограничивается ими. Пластик, резина, полиэтилен, тряпичная ветошь, различный мусор, помёт и многие другие виды отходов могут войти в состав топлива (конечно, расход топлива и состав газа меняются в зависимости от продуктов сгорания). Любители утверждают, что благодаря работе их автомобилей придорожная полоса оказывается очищенной от разного рода мусора.
Учитывая стоимость дров и древесного угля, нельзя забывать о различных отходах производств, которые могут быть использованы как топливо, — лузга семечек, скорлупа орехов, стержни кукурузы, отработанный кофе после кофемашин, сено, торф, разновидности угля.
Какова реальная экономия, расход топлива?
Пожалуй, самый волнующий вопрос. В среднем при расходе автомобиля 10 л бензина на 100 км потребление газогенератора составляет 20 кг дров. При этом мощность снижается всего на 4% по сравнению с бензином, а значит двигатель также может выдавать необходимую скорость.
Таким образом, 1 литр бензина = 2–3 килограмма дров. Стоимость килограмма дров примерно в 3 раза меньше, чем стоимость литра бензина, поэтому на этапе расчета экономии разница не ощутима. Однако она имеется.
Каково время запуска газогенератора?
На запуск двигателя на древесном угле требуется от 10 до 30 секунд, на дровах (и мусоре) — от 5 до 15 минут.
А не погубит ли такой газ ДВС?
Октановое число газа, получаемого таким способом, — 110–120, что снижает детонацию и в целом менее разрушительно влияет на двигатель. Газ не смывает масляную плёнку, в результате чего работа двигателя становится более тихой и ровной. Однако при неправильно организованной фильтрации газа (изначально в 1м3 газа около 3 грамм пыли) пыль может действовать деструктивно на поршни. Поэтому важнейшими этапами при разработке газогенератора является продуманная система фильтрации и охлаждения (по результатам экспериментов было выяснено, что при увеличении температуры газа с 20 до 70 градусов Цельсия мощность ДВС падает на 25%).
Вредные выхлопы, вырубка леса и прочие вопросы экологии
При сжигании только органических веществ количество вредных выбросов будет стремиться к нулю — в результате работы двигателя ничего, кроме углекислого газа, на выходе не будет. По результатам исследований, проводимых в Европе, такие автомобили в десятки раз экологичнее транспортных средств, движущихся на бензине или газу. Так происходит из-за того, что процесс генерации газа происходит на очень высоких температурах (до 1 000 градусов Цельсия), ввиду чего топливо расщепляется на простейшие элементы.
Вопрос вырубки леса также беспокоит многих, кто сталкивается с газогенераторами. Хочется заметить, что для обеспечения таких автомобилей топливом не обязательно вырубать лес. Многие приверженцы этой технологии пользуются ветками и дровами от умерших деревьев, которых много и в наших лесополосах. Таким образом, бесплатный сухостой и валежник также могут быть использованы как топливо. Кроме того, производство бензина наносит гораздо больший вред окружающей среде, поэтому даже при вырубке леса уровень полезности последнего метода гораздо выше. Конечно, ни на одной заправке вам не предложат отсыпать дров или угля как топлива, поэтому газогенератор подходит далеко не всем.
Кому подходит газогенератор?
В первую очередь жителям глубинки, где сложно найти/дорого стоит топливо (бензин или газ). Однако у жителей городов также часто есть потребность в газогенераторах (по разным причинам).
Например, житель Англии, Колин Дэвисон, с друзьями проехал всю Англию (а это 2 575 км), заправляя свой автомобиль отходами кофе! Маршрут был проложен между 37 кофейными магазинами, в которых они брали отработанное кофе, в результате чего их путешествие было занесено в книгу рекордов Гиннесса. Максимальная скорость — 105 км/час.
Йохан Линель, житель Швеции, проехал всю Швецию (5 420 км) за 20 дней на дровах. Расход топлива составил 7 куб. метров древесины. При этом максимальная скорость составляла до 150 км/час.
Житель Украины, Андрей Лагунов, пошел ещё дальше — он сделал курс «Авто на дровах своими руками», а также собрал множество информации о газогенераторах и их владельцах. Любой желающий, по словам Андрея, может сделать газогенератор своими руками за несколько дней, потратив на его создание менее 50$.
Вывод
Если верить информации, что запасов нефти хватит человечеству на 30–40 лет, то поиск альтернативных видов энергии можно считать оправданным. Количество древесины, необходимой для повсеместного перехода населения на такой метод, невообразимо велико.
В любом случае, главное — чтобы люди использовали новые технологии по мере необходимости и продолжали поиски, ведь любая новая разработка (или улучшение старой технологии) благотворно воздействует на эффективность процессов нашей жизнедеятельности.
А для тех, кто интересуется электромобилями, у нас тоже есть интересная публикация.
Газогенератор на дровах своими руками — устройство, схема, сборка
С каждым годом больше внимания во всех сферах индустрии уделяется разработке и внедрению новых технологий, помогающих сбережению электроэнергии. Сфера производства отопительного оборудования так же не осталась в стороне и провела ряд исследовательских работ, позволивших сделать принципиальные открытия и выстроить газогенератор на дровах. В таком приспособлении в итоге сгорания в герметичной камере древесной породы выделяются газы, которые тоже сгорают, выделяя дополнительное тепло. Таким макаром, применяемое горючее вполне сжигается с наибольшей отдачей тепла. Благодаря высочайшему коэффициенту теплопотери газогенераторного котла на дровах является экономичным обогревающим приспособлением.
Газогенераторный котел на дровах можно сделать и своими руками, но перед тем как приступить к его изготовлению, нужно кропотливо изучить его механизм работы. Исследовав устройство газогенератора на дровах, можно обеспечить более эффективную и неопасную работу котла.
Устройство и схема газогенераторного котла на дровах
Растопка газогенераторного котла подобна процессу растопки обыкновенной печи – точно так же укладывается горючее, конкретно производится растопка, воздушная заслонка запирается вполовину для предупреждения поступления кислорода вовнутрь камеры сгорания.
Устройство является очень обычным. Котел состоит из 2-ух камер, размещенных в одном корпусе. Одна камера создана для сжигания дров либо другого твердого горючего (брикетов, травы и пр.), другая – для сжигания выделяемого вследствие сгорания дров газа. Температура поднимается. Жаркий воздух циркулирует по воздухоотводам, захватывая прохладный из нижних сопел, который также в процессе топки греется и вздымается ввысь, что и показывает предоставленная схема газогенератора на дровах.
Благодаря таковой конвекции помещение очень стремительно греется и долгое время остается теплым.
Изготовка газогенератора на дровах своими руками
Представленная выше схема воспроизводит принцип деяния обычного котла, потому сооружать газогенератор на дровах своими руками нужно, не только лишь делая упор на данные о работе составляющих частей приспособления, которые изображены на чертеже, да и тщательно ознакомившись с процессом работы уже готового устройства.
До этого ознакомтесь с видео об устройстве самодельного газогенератора:
В качестве корпуса для грядущего газогенератора служит железная бочка. В самой высшей части корпуса устанавливается бункер объемом 0,6 – 0,7 м3 для загрузки древесной породы.
Также вверху газогенератора размещается юбочка, где вначале находится прохладный воздух.
Образующийся в итоге горения газ, вдуваясь через фурмы, проходит кольца грубой чистки.
Очищенный газ забирается из юбочки, охлаждается через фильтр остывания и выпускается. Фильтр остывания представляет собой зигзаг труб с металлическими кольцами, расположенными снутри.
На фильтре устанавливается приспособление с краном для сбора и спуска конденсата, образующегося при использовании сырой древесной породы.
Если дрова очень мокроватые, то газ, попадая в юбочку и контактируя с прохладным воздухом, оставляет много воды, которая проходит через сепаратор и соединяется по ленте слива. Сепаратор делается из трубы, в которую вставляется ребристая пластинка.
Если нужен сухой воздушный газ, то вентиль слива перекрывается, а вентиль на газовой трубе, расположенной за сепаратором, раскрывается. Газ, попадая из малеханькой трубы в огромную трубу сепаратора, оставляет капли росы и направляется в зону горения.
При желании в нижней части корпуса можно делается емкость для нагрева воды. Такая вода будет греться при помощи оборотного горючего газа, который в процессе нагрева будет дополнительно охлаждаться.
По мере надобности образующийся в процессе горения газ можно опять-таки использовать как дополнительное горючее для нагрева, повернув определенный вентиль и направив горючий газ в дополнительную зону горения. Тогда выпускаться через фильтр остывания будет только оставшийся газ СО2.
Вам будет любопытно:
- Кран-балка своими руками
- Копалка (картофелекопалка) для мотоблока своими руками
- Минитрактор из мотоблока Нева своими руками: чертежи, фото, видео
- Фрезерный стол для ручного фрезера своими руками
- Станок для профилирования бруса своими руками
Комментирование и размещение ссылок запрещено.
чертежи, устройство, схема, сборка, видео инструкция
Природный газ – самый дешевый и самый эффективный источник тепла. К сожалению, магистральный газопровод проведен не во все регионы нашей родины, и даже не везде подвозят баллонный. Тем не менее, это не повод отказываться от его использования при отоплении дома с тем лишь исключением, что придется сделать газогенератор на дровах своими руками. Это альтернативный способ отопления, где в качестве базового топлива будут использоваться не только дрова, но опилки, пеллеты, отходы деревообрабатывающей промышленности и т.д.
В статье мы подробно рассмотрим, как правильно сделать такой агрегат, что для этого понадобится, а также разберемся в преимуществах и возможных его недостатках.
Как это работает
Для того, чтобы добыть природный газ, не обязательно искать месторождение и открывать скважину, можно воспользоваться пиролизным котлом. Это особый вид котельного оборудования, где топливо сгорает при минимальном доступе кислорода, распадаясь на древесный остаток (уголь) и горючий газ (пропилен и этилен).
Учитывая то, что одновременно с топливом происходит процесс сгорания пиролизных газов, эффективность котла увеличивается в 1,5-2 раза при одинаковом с обычным котлом расходе топлива.
Медленное сгорание топлива (дров, опилок, пеллет и т.д.) обеспечивает гораздо более длительный процесс горения (12 часов по сравнению с 3-4 часами в обычном).
На схеме видно, по какому принципу работает пиролизный котел и как идет процесс образования горючего (древесного) газа.
Являясь уже, по сути, газогенераторным оборудованием, такой котел выполняет ряд задач, а именно:
- Производит низкомолекудярные олефины в результате сгорания дров и входящей в их состав целлюлозы.
- Очищает олефины от всех сторонних примесей, в результате чего получается чистый горючий газ.
-
Охлаждает газы за счет уменьшения количества энергии при окончательном сгорании топлива.
Пиролизный котел всегда разделен на 2 камеры, в одной из которых сгорает основное топливо при минимальном доступе кислорода, во вторую поступают выработанные газы и при подкачке воздуха происходит их сгорание.
Подобная оптимизация процесса сгорания позволяет решить сразу 2 ключевых задачи – увеличение коэффициента полезного действия котла и возможность организовать водонагревательный котел за счет соединения с водяной рубашкой.
Процесс пиролиза обеспечивает полное сгорание топлива с максимальной отдачей тепла, что на выходе дает более 35% экономии расходов.
Газогенераторный котел на дровах вполне можно сделать и своими руками, но перед этим необходимо понять принцип его работы, устройство камер внутреннего сгорания и технику безопасности, чтобы исключить малейшие нарушения технологии.
Устройство модели на дровах и схема
Данный вид котла растапливается точно по такому же принципу, как и обычный котел на твердом топливе. Дрова, пеллеты, брикеты, опилки и прочие виды топлива закладываются в нижнюю камеру, поджигаются, после чего открывается воздушная заслонка для создания тяги.
Воздушная заслонка должна быть открыта только наполовину, чтобы избежать излишнего поступления воздуха в камеру сгорания.
Устройство самодельного газогенераторного котла очень простое. Основу составляют 2 камеры, закрытые в один корпус. В нижней сгорает твердое топливо, в верхней – дровяной газ. При этом нагреваемый воздух постоянно циркулирует по воздуховодам — теплый поднимается вверх и выходит наружу, холодный подсасывается снаружи нагревается и также выходит. Этот процесс продолжается до той поры, пока в камере тлеет топливо.
Конвекция газогенераторного котла на дровах прогревает помещение достаточно быстро (50 кв.м. за 60-90 минут), при этом тепло сохраняется более длительный период времени.
Как сделать своими руками
На схеме, изображенной выше, видно, как функционирует котел, где и какие камеры расположены, поэтому прежде чем приступать к собственноручной сборке, необходимо разобраться с принципом работы готового котла, а также использовать чертеж котла, работающего на твердом топливе.
На видео вы можете посмотреть, как работает газогенераторный котел:
- Основой котла (корпусом) служит любая металлическая бочка, подойдет даже использованный газовый баллон. Можно сделать такой цилиндр из листа стали 8-10 мм толщиной, для чего сварить его по окружности и приварить дно.
- В верхней части цилиндра делаете камеру минимальным объемом 0,7 куб.м, куда в дальнейшем будет загружаться твердое топливо.
Для того, чтобы рассчитать объем бункера для загрузки топлива, воспользуйтесь таблицей. С ее помощью можно рассчитывать объем любого котла, который вы планируете делать своими руками.
-
На самом верху цилиндра привариваете дополнительный круг стали, из которого будет происходить забор холодного воздуха (юбка).
- Для очистки древесного газа от сторонних примесей используются кольца грубой очистки. Поддув его происходит через фурму.
- Для охлаждения газа из юбки забирается холодный воздух. Он проходит по зигзагу труб, оснащенному несколькими металлическими кольцами, постепенно охлаждаясь.
- Если используется для горения недостаточно сухое топливо, во время работы котла собирается конденсат. Его необходимо регулярно спускать, для чего используется подобный кран.
-
Газогенераторный котел – единственный в линейке отопительного оборудования, который позволяет использовать даже влажные – свежесрубленные – дрова. При контакте с холодным воздухом, поступающим из юбки, образуется слишком большое количество воды, которое необходимо постоянно спускать. Для этой цели используется т.н. сепаратор.
Его изготавливают из трубы диаметром 3-5 мм, куда вставляют пластину с ребрами. Проходя по сепаратору, вода выводится из системы по ленте слива.
- Для повышения мощности газогенераторного котла требуется сухой газ. Для этого достаточно закрыть кран слива конденсата и открыть кран на газовой трубе, которая расположена сразу за сепараторной трубкой. Когда газ поступает из небольшой трубы в большую, он распадается на газообразную и жидкую фракции, после чего переходит в камеру сгорания.
- Для обогрева больших площадей рекомендуется устанавливать водяной контур. Можно даже сделать отдельную камеру в газогенераторном котле, где будет нагреваться с помощью поступающего горючего газа вода. За счет конвекции при нагреве происходит одновременное его охлаждение.
-
При выполнении обвязки котла рекомендуется использовать газ в качестве источника дополнительного горючего.
Для этого достаточно подсоединить контур и открыть вентиль подачи газа в прибавочную зону.
Советы и отзывы специалистов
- Камеры сгорания изготавливают из низкоуглеродистой стали, не подверженной воздействию высоких температур и конденсата.
- Внутри корпуса камеры сгорания закрепляются болтами.
- Крышка корпуса и камеры всегда уплотняется, чтобы исключить неконтролируемое попадание воздуха внутрь. В качестве уплотнителя можно использовать асбестовый шнур.
- Корпус газогенераторного котла лучше всего изготовить из пустого газового баллона. Чтобы исключить риск возгорания остатков газа во время монтажных работ, наполните его до краев водой.
- Обязательно устанавливайте на газогенераторе обратный клапан, который предотвратит выход газа.
- Для нагнетания воздуха можно использовать вентилятор, но в этом случае котел будет энергозависимым.
-
Колосниковая решетка для камеры сгорания твердого топлива изготавливается из чугунных полос.
Для того, чтобы такой агрегат было удобно чистить, сделайте центр колосника подвижным.
- Предусмотрите в загрузочной камере люк – при избытке топлива и газа он позволит сбросить часть балласта.
- Для изготовления газогенераторного котла своими руками обязательно используйте чертежи, а еще лучше – вышедший из строя котел, чтобы в точности соблюсти все пропорции и размеры.
Газогенераторные установки. Переработка отходов в полезную энергию. — Портал-Энерго.ru
На фото газогенераторная устновка AZSD
Газогенераторы — не новое явление в технике. Во время Великой Отечественной Войны топливо поставлялось в основном для фронта. Поэтому грузовые и, даже, легковые машины ездили на дровах. В газогенераторную колонку загружались чурки или деревянные обрезки, газогенератор вырабатывал газ, на котором работал двигатель внутреннего сгорания. Хорошую мощность на таком топливе развить было невозможно, но машины ездили относительно надежно. В настоящее время, в Северной Корее, наши ЗИЛы тоже ездят на дровах.
Сама газификация топлива получила распространение в конце 19 века. В основе газогенерации лежит сжигание твердого топлива в обедненной кислородом среде. Подача воздуха обеспечивается на уровне 30-35% от теоретически необходимого для горения уровня. Поэтому можно говорить скорее об управляемом тлении, чем о горении.
Древесный газогенератор. Принцип работы.
Температура горения 900-1200 градусов. Малое поступление воздуха в топку обеспечивается заслонками и конструктивно, благодаря чему в процессе низкотемпературного пиролиза образуются горючие газы, которые могут отводиться, очищаться и сжигаться в других устройствах. Например, в газопоршневых двигателях, бытовых газовых горелках, удаленных топочных устройствах. Конструктивно печь устроена так, что обеспечивается отделение горючих газов СО, СН4, Н2 от баластных негорючих газов, входящих в состав воздуха. Так же предусматривается подогрев подаваемого в печь воздуха теплом отводимых газов. Применение этих мер обеспечивает КПД газоненераторной установки около 85%. Объем генерируемого горючего газа составляет примерно 2,2 м3 на 1 кг сожженного топлива.
В качестве топлива в газогенераторах используется щепа с размером до 50 мм и, примерно, 20% опилок. Имеются установки с использованием в топливной смеси торфяной крошки, зерновых отходов, пищевой упаковки. Влажность подаваемой смеси до 20%. В то же время, имеются конструкции, предусматривающие влажность топлива до 60% и досушивание смеси в процессе подачи в топку: подача топливной крошки происходит постепенно и просохнуть она успевает до попадания в зону горения. В промышленных газогенераторах подача топлива производится шнеком, вращение которого обеспечивается от электродвигателя с регулируемой частотой вращения. В небольших установках — подача топлива из бункера в зону горения.
Топка конструктивно исполняется в виде футерованной жаростойким кирпичом шахты объемом до от 0,5 до 4,5 кубометров. Установка с тепловой мощностью 50 кВт имеет объем топки 0,65 м3 и вес 320 кг, расход топлива 22 кг в час. Установка с мощностью 1 МВт, имеет топку объемом 4,4 м3 и вес 5 тонн, расход топлива 430 кг в час.
Особенностью газогенераторных установок является отсутствие дымления, поскольку при медленном горении углерод не выносится с отходящими газами, преобразуясь в газовую смесь. Теплотворная способность газовой смеси несколько ниже природного газа, но вполне достаточна для использования такого газа в быту и для привода двигателей внутреннего сгорания.
Газогенераторные установки: экономика эксплуатации
Для средних и малых энергетических предприятий, деревообрабатывающих производств применение газогенераторных установок очень выгодно. Если нет необходимости отделения газовой смеси, газогенераторные установки работают как весьма эффективные теплогенераторы, обеспечивая нужды в тепловой энергии для технологических нужд и в отоплении. Очень эффективно применение газогенераторных установовок на деревобрабытывающих предприятиях для сушки древесины.
При работе газогенератора в составе твердотопливного котла можно сжигать отходы практически любой длины. Одновременно решаются экологические проблемы и проблемы утилизации отходов, снижается себестоимость выпускаемой продукции. Анализ затрат на отопление сушильных камер и промышленных зданий и сооружений, применяющих газогенераторные установки показывает, что затраты на топливо от 3 до 25 раз меньше, чем при традиционном его сжигании в котлах или отоплении электронагревательными установками. При использовании в качестве топлива отходов деревообработки собственного производства экономический эффект возрастает. Опыт эксплуатации отопительного оборудования с использованием газогенераторов в составе сушильных камер показал, что срок их окупаемости находится в пределах от 2-х месяцев до 1 года.
Применение газогенераторных установок для выработки электроэнергии показывает, что экономически они более эффективны, чем остальные объекты малой энергетики. Причиной тому невысокая стоимость оборудования и возможность использования отходов производства, мусора, сорной древесины. В Якутии был произведен подсчет выгоды применения газогенераторных установок взамен дизельных генераторов. Экономия по топливу составила 14 раз, срок окупаемости установок от 1 года до 3 лет. При этом был решен ряд экологических проблем с необходимостью утилизации больного леса и лесных завалов.
Топливо для гезогенераторных установок
Некоторую проблему составляет заготовка топлива и его подготовка для сжигания. Но технически эта проблема легко разрешима. На рынке существует широкое предложение разного рода дробилок и измельчителей, как мобильных, так и стационарных. Если исполнять все требования к вырубкам, то после них на лесосеке не должно оставаться древесных отходов. Мобильные измельчители древесины вполне обеспечивают поставку сырья для газогенераторных установок необходимой кондиции.
Некоторые промышленные предприятия, имеющие газонегераторные установки, не закупают опилки и щепу, а получают деньги за их утилизацию. Учитывая стоимость вывоза мусора на свалку и возможные штрафные санкции, предприятиям выгоднее сдать древесный мусор за небольшие деньги на сжигание. Владелец же газогенераторной установки получает при этом тепло для своих нужд не за деньги, а с доплатой.
Автор: Коваль Сергей Петрович
Деревянный генератор на заднем дворе — Возобновляемая энергия
Иногда трудно решить, что является большим финансовым бременем: расходы на эксплуатацию автомобиля или расходы на обеспечение семьи электроэнергией и теплом. Итак, чтобы уменьшить нагрузку в обоих случаях, ребята из исследовательского центра MOTHER EARTH NEWS потратили последние несколько месяцев на разработку и тестирование различных систем, в которых используются недорогие, а иногда и бесплатные древесные отходы в качестве замены дорогостоящим ископаемое топливо.
В статье «Грузовик на древесном газе: дорожная энергия от газификации древесины» мы подробно рассказали, как сделать газификатор для древесины достаточно маленьким, чтобы приводить в действие автомобиль или пикап, примерно за 125 долларов в деталях и материалах. В этом отчете мы также упомянули, что находимся в процессе адаптации технологии к стационарной генерирующей системе. Что ж, всего за несколько дней до крайнего срока выпуска этого выпуска наша исследовательская группа завершила работу над этим дровяным генератором. И — хотя у нас еще не было возможности посвятить достаточно рабочего времени устройству, чтобы убедить нас в том, что дизайн настолько хорош, насколько мы можем его сделать — наше первоначальное тестирование, похоже, показывает, что он будет работать так же хорошо, как и любые обычные резервный генератор, работающий на топливе, аналогичной мощности в , в дополнение к для обеспечения достаточного количества горячей воды для обогрева дома!
С самого начала этого проекта мы не только хотели создать рабочий демонстрационный образец, который позволил бы посетителям нашей эко-деревни увидеть — и, в некоторых случаях, позже повторить — то, что мы сделали, но также хотели создать безупречный функциональный источник переменного тока, который будет полностью обеспечивать нашу ремонтную мастерскую, тем самым уменьшая нашу зависимость от местных коммунальных услуг.
Как оказалось, мы смогли достичь наших целей … и для этого использовали недорогой лом или запчасти со свалки, которые мы подключили к 10-киловаттному генератору переменного тока на 120/240 В, первоначально приобретенному для гидроэлектростанции. (См. «Материнская гидроэлектростанция». Поскольку напор и сток на нашем гидроэлектростанции имеют потенциал чуть более 2 кВт, мы решили заменить там негабаритный генератор переменного тока более подходящим генератором мощностью 2,5 кВт, таким образом, более крупная установка доступна для использования с древесно-газовой установкой.)
Газификаторы, конденсаторы и фильтры
Система получения электричества из металлолома на удивление проста. Для начала, вместо того, чтобы использовать только один газификатор, мы решили использовать и два , подключенных независимо друг от друга, чтобы двигатель работал без перебоев. (В качестве дополнительного преимущества эта установка также позволяет нам чистить или обслуживать одну камеру, в то время как другая поддерживает работу установки. ) И поскольку в стационарном режиме резервуары с древесным наполнителем не подвержены вибрации и перемещению, которые они могли бы столкновение, если установлено на транспортном средстве, мы пошли дальше и установили электромеханический встряхиватель решетки (сделанный из двигателя автомобильного стеклоочистителя) в каждой топке, чтобы гарантировать, что остатки топлива не накапливаются, и остановить поток горючего «дымового» топлива производится газификаторами.
Когда пар выходит из «используемого» агрегата, он попадает прямо в десятифутовый, слегка наклонный горизонтальный конденсатор, который [1] удаляет большое количество несгоревшего водяного пара и некоторый остаток, и [2] охлаждается и, таким образом, уплотняет топливный заряд, делая его более мощным. Эта «охлаждающая камера» представляет собой не что иное, как ряд труб, заключенных — все, кроме их концов — в «рубашку» трубопровода, которая заполнена водой и подключена к системе охлаждения двигателя.
После прохождения через конденсатор концентрированные газы попадают в вертикальный фильтр, который улавливает любые оставшиеся твердые частицы слоями тканой нити и предотвращает потенциальное обратное пламя от достижения остальной части системы с помощью перфорированных пламегасителей на обоих входах и розетка. И снова конденсатор и фильтр были изготовлены в двух экземплярах, так что были две отдельные и законченные системы производства топлива, каждая из которых подключена к общей питающей трубе, ведущей непосредственно к двигателю.
Силовая установка, генератор и регулятор скорости
При выборе двигателя для нашего завода были приняты во внимание четыре фактора: [1] мощность и крутящий момент при заданных оборотах, [2] рабочий объем, [3] доступность и [4] стоимость.
Из наших приблизительных расчетов мы пришли к выводу, что — после учета потерь эффективности — генератору мощностью 10 кВт для эффективной работы потребуется около 22 лошадиных сил.Однако, поскольку мощность в лошадиных силах является функцией частоты вращения двигателя, было важно, чтобы мы выбрали силовую установку, которая развивает свои «лошадиные силы» в диапазоне средних оборотов, а не на максимальной скорости, поскольку высокоскоростной агрегат будет страдать от плохой экономии топлива и сокращенная продолжительность жизни. Мы также должны были учитывать тот факт, что двигатель, работающий на древесном газе, выдает только от 50 до 65% мощности номинальной мощности , и что медленно горящий газ лучше работает при длинно-тактном, а не коротко-тактном исполнении. .
Объем двигателя — еще один важный фактор.Очевидно, что огромный восьмицилиндровый двигатель потреблял бы больше «дыма», чем требует скромная четырехцилиндровая машина. И в интересах экономии мы не видели смысла в использовании слишком крупногабаритного двигателя для выполнения относительно небольшой задачи по обеспечению единственного здания электричеством и теплом.
Также важны доступность и стоимость. Мы посчитали, что лучше использовать недорогой утилизированный двигатель, близкий к нашим потребностям, чем покупать идеально подобранный, но дорогой — новый силовой агрегат .
К счастью, наш выбор оказался удачным. При обыске на местной свалке был обнаружен (за 75 долларов) четырехцилиндровый двигатель Pontiac Tempest 1961 года выпуска. Это длинноходная модель объемом 195 кубических дюймов, которая фактически является правой половиной General Motors V-8. Мы оснастили блок поршнями с соотношением сторон 11: 1 и распределительным валом с малым перекрытием, затем установили самодельную систему карбюратора, аналогичную той, что используется на нашем пикапе с древесным газом, и немного увеличили угол опережения зажигания. (Эти модификации были экспериментальными.Система определенно будет работать вполне адекватно с двигателем «коробчатого типа».) Мы также заменили традиционный выпускной коллектор на морской агрегат с водяным охлаждением и построили водяную рубашку вокруг открытой выхлопной трубы, чтобы отводить отработанное тепло для использования система хранения тепла.
В нынешнем состоянии двигатель производит на больше, чем на мощности, достаточной для оптимальной скорости генератора — 1800 об / мин — для эффективного выполнения своей работы. Насколько мы можем догадаться, крепкий маленький четырехцилиндровый двигатель, изначально рассчитанный на 110 л. с. при 3800 об / мин, на этой скорости вытесняет почти 70 «пони» на своей газовой диете… что означает подачу около 30 лошадиных сил на генератор переменного тока при 1800 оборотах в минуту (и это также скорость, с которой силовая установка развивает свой максимальный крутящий момент). Кроме того, эти обстоятельства позволяют нам использовать экономичную муфту с прямым приводом, а не более сложную и энергосберегающую систему понижающей передачи для установки.
Само генераторная установка представляет собой стандартный генератор с самовозбуждением Kamag 14 мощностью 10 кВт в непрерывном режиме.Он обеспечивает либо одну 240-вольтную, либо две 120-вольтовые 60-тактные цепи и предназначен для включения при 210 вольт, чтобы установка могла выйти на рабочую скорость без нагрузки. Точно так же он включает в себя регулятор превышения скорости, который отключает устройство при напряжении 270.
Поскольку изменение требований к нагрузке напрямую влияет на скорость вращения двигателя / генератора переменного тока и, таким образом, влияет на циклическое переключение мощности, нам пришлось полагаться на регулятор скорости, чтобы поддерживать 60 циклов последовательно. Но вместо того, чтобы использовать шкив с регулируемой шириной, который изначально поставлялся с генератором, мы использовали только его датчик скорости и серводвигатель, а затем подключили последний компонент непосредственно к дроссельной заслонке двигателя. Этот макет гораздо менее громоздкий и сложный, чем «зажим для шкива», хотя нам нужно будет провести гораздо больше испытаний — и, возможно, внести некоторые изменения — прежде чем мы сможем полностью поручиться за его эффективность.
Система когенерации обеспечивает тепло
Система предназначена не только для производства электроэнергии для нашей ремонтной мастерской, но и для обеспечения этой конструкции теплом.Вы не поверите, но только около одной трети энергии данного топлива выполняет какую-либо полезную работу, поскольку оно сжигается в двигателе. Остальное, как правило, тратится в виде тепла, когда оно выбрасывается из выхлопной трубы или забирается из радиатора. Итак, чтобы воспользоваться этим растраченным ресурсом, мы направили систему охлаждения силовой установки вместе с «рубашкой», окружающей ее выпускной коллектор, в 15-галлонный «замкнутый контур» . .. который, в свою очередь, сбрасывает тепловую энергию в систему Резервуар на 500 галлонов, который через насос и 1 1/2 «линию соединен со вторым контейнером равного объема.
Для наших летних демонстраций мы подключили небольшой водонагреватель к первичному контуру двигателя. Однако осенью мы планируем расширить ее до полномасштабной гидронной системы, установив обогреватели плинтуса в конструкции площадью 1200 квадратных футов, которая должна полностью использовать воду с температурой 170 ° F, которую обеспечивает двигатель.
и многое другое!
Наши эксперименты на этом не заканчиваются . Как только мы будем полностью удовлетворены производящей электричество частью нашей установки, мы собираемся прикрутить воздушный компрессор к вспомогательному кронштейну в передней части двигателя, обвязать его ремнем и провести пневматическую линию в закопанный резервуар для хранения воздуха рядом с магазином.Холодная земля поможет сконденсировать любую влагу, а сжатую «атмосферу» затем можно будет использовать для привода инструментов или распыления краски.
На самом деле, когда дело доходит до придумывания новых задач для нашего генератора, мы ограничены только нашим воображением. Похоже, что в двигателе достаточно избыточной мощности, чтобы позволить нам работать даже с автомобильным компрессором кондиционера, который должен обеспечивать охлаждение небольшого дома. По крайней мере, один из наших научных сотрудников считает, что можно разработать механизм для измельчения древесины / шнековой подачи, приводимый в действие коленчатым валом двигателя, который мог бы преобразовывать большие куски древесины в куски «размером с укус» и подавать их в газифицирующую среду. камеры!
В любом случае, мы чувствуем, что сделали ряд заслуживающих внимания открытий в ходе нашего небольшого исследования, не последним из которых является тот факт, что домашние электрические потребности могут быть удовлетворены за счет газификации древесины.Вклад нашей лилипутской коммунальной службы — не считая рабочей силы — составил примерно 6000 долларов, включая ее «корпус», который состоит из плиты и защитной крыши. Конечно, эту стоимость можно было бы существенно снизить, если бы использовались подержанный генератор переменного тока и немодифицированный двигатель. И не требуется очень острого карандаша, чтобы понять, что домашнему хозяйству или ферме, которые ежегодно потребляют около 1500 долларов покупной энергии (во многих областях, которые можно было бы считать скромной цифрой ), придется работать с автономным всего четыре года — при условии, что топливо утилизируется — чтобы окупить вложения.
Но мы еще не закончили. Следите за будущими выпусками, чтобы получать больше отчетов о нашей когенерационной системе, потому что мы будем держать вас в курсе нашего прогресса по мере продвижения.
«машин, которые бегают по деревьям» Джона Гудмана (журнал Works That Work)
автор: Джона Гудман (3044 слова)
Машины, работающие на дровах, могут показаться фантастикой в стиле стимпанк или одержимостью на заднем дворе какого-то сумасшедшего мастерицы, но в какой-то момент они были обычным явлением во многих частях Европы, и технология, на которой они работают, все еще находит практическое применение сегодня.
Фото на обложке: Иоганн Линелл на Volvo, который он и двое друзей установили газогенератором. За 20 дней 2007 года они проехали 5420 километров по Швеции на энергии, вырабатываемой семью кубометрами древесины. (Фотография любезно предоставлена Иоганном Линеллом.)
В глубине лесов континентальной Швеции Йохан Линелл останавливается, его двигатель не работает. Он и двое друзей выходят из машины и идут веером через деревья, возвращаясь с руками, полными еловых шишек и мертвого дерева. В задней части машины Линелл снимает с петель верх высокого стального ящика, который возвышается над отверстием в багажнике.Дым поднимается вверх, и пламя следует за ним, когда он сбрасывает вырубленную древесину внутрь. Из нижней части заляпанной смолой стопки толстые сварные трубы карабкаются по кузову автомобиля и змеятся к переднему бамперу, где они входят в двигатель, как трубки для кормления пациента. В считанные минуты машина оживает, плавно движется по массивной древесине.
На короткое время, 70 лет назад, почти все гражданские автомобили в Европе работали таким образом. По мере того как Вторая мировая война затягивалась, а бензина становилось все меньше, древесина стала основным альтернативным топливом для транспортных средств.К 1945 году около миллиона европейских автомобилей работали на газификации древесины с использованием модификаций, аналогичных модификациям Volvo Линелла. Принцип работы удивительно прост: сжигая бочку из дерева или угля до тех пор, пока она не достигнет внутренней температуры от 900 ° до 1200 ° C (от 1650 ° до 2200 ° F), а затем ограничивая подачу воздуха в огонь, газификаторы производят горючий углерод. монооксид, который можно охлаждать, фильтровать и направлять непосредственно в двигатель обычного автомобиля.
Автомобиль с приводом от дерева был изобретен в 1905 году английской автомобильной компанией Thornycroft, но прошло еще 20 лет до того, как французский химик Жорж Имбер сделал практическую возможность путешествия на древесном газе. Благодаря переработанной камере сгорания, в которой использовалось всасывание от двигателя для втягивания газа вниз через горячую сердцевину горящих поленьев, его модель могла создавать намного больше оксида углерода, чем предыдущие версии. Это также обеспечивало устойчивое горение, так как гравитация и вибрация транспортного средства вытряхивали золу из кучи, оседая на месте новое топливо. К 1930-м годам четыре европейских правительства активно исследовали газификаторы Имберта с целью их использования в общественном транспорте: политически нейтральные Швеция и Финляндия стремились достичь топливной автономии в нестабильном регионе; Италия Муссолини, находящаяся под торговым эмбарго Лиги Наций после вторжения в Эфиопию, искала источник топлива, альтернативный нефти; а нацистская Германия готовилась к войне.
Даже автомобили, работающие на древесном газе, нуждаются в инфраструктуре снабжения: в 1945 году в Финляндии было 70 деревообрабатывающих заводов, а в Германии — тысячи складов древесины, предназначенных специально для автомобильного топлива.Из 17 мест, где Линелл и его друзья останавливались за дровами во время поездки, только в четырех были готовые к употреблению, предварительно порубленные дрова.
Падение Германии в пропасть сюрреалистично задокументировано в сохранившихся экземплярах спонсируемого государством автомобильного журнала Motor Schau . И пронацистское пропагандистское, и банальное автомобильное издание, в его выпусках 1939 года представлены автогонщики с символикой СС, мотоциклы, тестирующие вермахт, и украшенные свастикой митинги, посвященные автомобилю Kraft durch Freude или Volkswagen Beetle.В 1940 году, когда каждый ежемесячный выпуск объявляет о падении еще одной европейской столицы, начинают появляться статьи о транспортных средствах на древесном газе, рекламируя технологию как топливо национальной гордости, которое освободит Германию от зависимости от иностранных поставщиков. В период с 1941 по 1942 год, когда потребности военных привели к сокращению поставок нефти для гражданского населения Германии более чем на 50%, страницы Motor Schau заполнены растущей рекламой газификаторов, а также крепких алкогольных напитков.
«Древесный газ дешев, экономичен и избавляет вас от зависимости от бензина, сырой нефти и нефти.Так читает объявление Motor Schau , автомобильного журнала нацистской эпохи. Транспорт, работающий на древесном газе, особенно привлекает тоталитарных режимов, стремящихся к независимости от мировой торговли, и до сих пор используется в Северной Корее. (Из журнала Motor Schau , 1941 г.)
К 1943 году характерные высокие цилиндрические печи были обязательными на большинстве транспортных средств в странах, оккупированных нацистами, поскольку ресурсы жидкого топлива направлялись прямо в вооруженные силы, особенно в Люфтваффе.В 2013 году греческий механик Александрос Топалоглоу сказал исследователю Алексии Папазафейропулу, что, несмотря на ограничения военного времени, греки поддерживают активный рынок бензина на черном рынке, обманывая чиновников, зажигая газификаторы на своих автомобилях непосредственно перед приближением к немецким контрольно-пропускным пунктам. Когда Германия начала терять территорию в 1944 году, по крайней мере пятьдесят танков Tiger были модернизированы установками для сжигания древесного газа, и наказания за езду на бензине без письменного разрешения регионального генерала — даже для военных — стали жесткими.
Адольф Гитлер осматривает автомобиль, работающий на древесном газе. Изначально опубликованное в выпуске 1941 года в журнале Motor Schau за 1941 год, изображение располагалось над цитатой из нацистского лидера: «Эти автомобили по-прежнему будут иметь особое значение после войны, потому что рост автомобилизации будет означать, что у нас никогда не будет достаточно масла, что оставляет нас. зависит от импорта. Это родное топливо полезно для экономики страны ». (Из журнала« Motor Schau », 1941 г.)
Личные взгляды Гитлера на автомобили, работающие на древесном газе, можно прочесть в номере журнала Motor Schau за 1941 год, рядом с веселыми фотографиями Дер Фюрера на демонстрации газификаторов Mercedes-Benz. «Это автомобили, которые будут иметь особое значение после войны», — сказал он. «Нефть поступает из-за границы, но это топливо нашей родины». Четыре катастрофических года спустя автомобили с газификатором в Берлине действительно приобрели мрачный символизм. В суровую зиму 1946 года они бесполезно ржавели на улицах, когда берлинцы крушили мебель и вырывали деревья с корнем, отчаянно ища дрова в развалинах немецкой столицы.
Кажется, вам нравятся хорошие истории
Подпишитесь на нашу нечастую рассылку, чтобы получать больше историй прямо на свой почтовый ящик. В начале 2000-х, когда Линелл решил сделать свой собственный автомобиль на дровах и газе, он видел только один раз. Транспортные средства на древесном газе в Европе являются исключительной прерогативой любителей, и его единственным источником запчастей и информации было местное радио-шоу под названием Serk I Fin , или «Найди и найди». В эфире Линелл изложил свой план, и его сравнили с Инге Найман, пожилой слушательницей, которая пережила Вторую мировую войну и все еще имела элементы газогенератора, оставшиеся с того периода. Это был прорыв, поскольку, как это ни удивительно, в наличии было немного другого, хотя в 1945 году в Швеции было более 60 000 транспортных средств на дровах, включая лодки, автобусы, тракторы и четверть мотоциклов страны.
(Фото любезно предоставлено Иоганном Линеллом)
Сегодня любители делятся советами в Интернете, а современные технологии позволяют «лесорубам» во всем мире извлекать выгоду из опыта таких авторитетов, как финский Веса Микконен и голландский псевдоним «Датч Джон». Однако создаваемые ими газификаторы по-прежнему имеют много общего со своими предшественниками времен Второй мировой войны и отличаются особой привередливостью, требующей глубокого знания своей конструкции, причуд и темперамента.По словам Датча Джона, «единственный человек, который может водить машину, работающую на древесном газе, — это человек, который ее сделал».
Даже серийно выпускаемые версии 1940-х годов, такие как немецкий 3TO Opel Blitz Lastwagen 1943 года, поставлялись с толстыми иллюстрированными руководствами по эксплуатации, в которых подробно описывается, как каждую неделю Lastwagen необходимо очищать и тщательно промывать, а также каждый месяц его неплотный пробковый газовый фильтр. должен быть удален, очищен и переустановлен. Запуск двигателя, хотя и занимает 20 минут, в основном включает в себя поднесение спички к дровам, но контроль потоков газа и воздуха вокруг двигателя, что имеет решающее значение для таких задач, как движение в гору, пересечение долины или остановка более чем на три часа. , требует освоения сочетаний четырех рычагов и ручки.В результате газификации образуется значительное количество азота, инертного газа, который разбавляет топливную смесь, в результате чего автомобили, работающие на древесном газе, имеют малую мощность, и извлечение из них наилучшего — путем разумной регулировки клапанов и вентиляционных отверстий — такое же искусство как наука.
«Когда вы едете медленно, вы видите больше», — говорит Линелл. «Это похоже на то, как будто страна преображается в зависимости от вашей машины. Я почувствовал то же самое годом ранее, когда проехал 500 км (311 миль) на мопеде, который я переоборудовал для работы на этаноле.Вы видите совершенно новый мир ».
Однако нет причин, по которым технология газификации должна оставаться в прошлом веке. Именно поэтому финский энтузиаст древесного газа Юха Сипиля построил самый передовой в мире автомобиль на древесном газе, El Kamina, модифицированный грузовик с полностью автоматизированным система газификации, управляемая компьютером, встроенным в ее приборную панель. Хотя это всего лишь прототип, это автомобиль на древесном газе, которым может управлять кто угодно. Сипиля — больше, чем просто любитель; он твердо верит в возобновляемые источники энергии и в то, что люди могут жить «вне сети».Он также является основателем Volter Oy, энергетической компании, занимающейся исследованиями газификации древесины, а также создателем десятиэтажного экологического поселка Кемпеле, а с мая 2015 года — премьер-министром Финляндии.
В 2010 году финское общество провело бурную общественную дискуссию о возможном возвращении к заменителям топлива военного времени, особенно к газификации древесины. В 1945 году 80% автомобилей в Финляндии — 46 000 — работали на газогенераторах, и только в 1944 году было потреблено более 2 000 000 м 3 (70 630 000 футов 3) древесины.Полный переход на систему транспортировки древесины произошел всего за два года. Теперь такие инновации, как El Kamina, показывают, что многие недостатки процесса можно преодолеть с помощью новых технологий. Что самое убедительное, Финляндия — одна из немногих стран в мире, где деревья могут быть действительно устойчивым источником топлива, с 23 миллионами гектаров (88 800 квадратных метров) бореальных круглых лесов и населением всего 5,5 миллиона человек.
Йохан Линелл чистит охладитель своего Вольво, работающего на древесном газе, который он сделал из старого стального дизельного бака.Охлаждение газа делает его более плотным и конденсирует воду из топливной смеси, так что на двигатель передается больше мощности. После использования Йохан обнаружил, что внутренняя часть кулера будет покрыта загадочным кремообразным веществом. «Это напомнило мне вазелин». (Фото любезно предоставлено Иоганном Линеллом)
Ярно Хаапакоски, генеральный директор Volter Oy с 2011 года, объясняет, что семье из шести человек, живущей в образцовой деревне Кемпеле, которая получает энергию и обогревается от большой установки по газификации древесины, требуется всего 20 м³ (706 футов³) древесины в год. .По данным Metla, Финского института лесных исследований, в финских лесах ежегодно производится 104,5 миллиона кубометров новой древесины, что почти достаточно для удовлетворения энергетических потребностей всех жителей Финляндии. Более того, сжигание деревьев — это «замкнутый углеродный цикл»: углекислый газ, выделяемый деревьями при сжигании, примерно равен углекислому газу, который они вытягивают из воздуха в процессе роста.
Есть и обратная сторона. Древесный газ — это в первую очередь окись углерода, а окись углерода не имеет запаха, легче воздуха и исключительно ядовита.При атмосферной концентрации всего 0,5% он может убить, а всего 0,03% достаточно, чтобы вызвать потерю сознания. В одном из инцидентов в Хельсинки во время войны были замечены пассажиры, садившиеся в ожидающее такси холодным днем. Через десять минут такси не двинулось с места, прохожие открыли двери и обнаружили пассажиров без сознания, отравленных утечкой газа в закрытый отсек автомобиля. Треть из примерно 25 000 жертв отравления угарным газом в военное время в Финляндии пострадали во время вождения своих автомобилей, что часто приводило к плачевным результатам, а подходы к обнаружению угарного газа во время войны зачастую были грубыми.Дания, например, установила мышей или канареек в клетках возле газогенераторов для проверки на наличие смертельных газов. Но сегодня Хаапакоски не беспокоится. По его словам, детекторы намного сложнее, и горелки могут быть построены с системами аварийной защиты и сигнализации.
И это не первое возрождение древесного газа. В период между возрождением в Финляндии 21-го века и расцветом в Европе военного времени интерес к технологиям резко вырос в 1970-х годах после глобального нефтяного кризиса. Некоторые из этих интересов были оборонными, например, Швеция, которая разработала три типа аварийных газогенераторов, готовых к серийному производству во время кризиса.Но большая часть интереса возникла в развивающихся странах с наиболее острой потребностью: в сельских районах Азии, Африки и Латинской Америки.
Потенциал оказался огромным. Любые углеродосодержащие отходы могут быть газифицированы, будь то рисовая шелуха, пшеничная мякина, скорлупа грецких орехов, семена фруктов, опилки, солома, торф или кукурузные початки. Фильтры могут быть изготовлены из масла, угля, пробки, воды, ткани, фарфоровой крошки или сизаля. А при наличии необходимого опыта эффективные газификаторы для автомобилей или электрогенераторов могут быть построены из бочек с нефтью и ржавых труб.Крупные газифицирующие электростанции были эффективны в определенных местах, таких как лесопилки в Сапире, Парагвае и Восточном мысе Южной Африки, сушилка для кокосовых орехов в Шри-Ланке, работающая на газифицированной кокосовой скорлупе, или несколько сотен небольших электростанций, работающих на газификации рисовой шелухи. заводы в Китае. Аварийные установки, такие как Power Pallet, генератор газификатора, разработанный в Калифорнии, недавно показали себя многообещающими в качестве средства оказания помощи при бедствиях в Либерии. Но в наши дни производство метана из сточных вод оказалось гораздо более успешным в качестве автономного альтернативного источника энергии.В бедных странах горючие твердые вещества, такие как скорлупа орехов и солома, все еще могут быть товаром, даже если они дешевы, в то время как метан создается из отходов.
Йохан Линелл и его друзья Микаэль Андерберг и Мартин Йоханссон начали строительство своего Volvo, работающего на древесном газе, в начале 2007 года. К июлю он был готов, и они отправились в путешествие на дровах протяженностью 5420 км. Швеция. Поездка заняла 20 дней, несмотря на то, что максимальная скорость автомобиля составляла 90 км / ч (56 миль / ч), потому что остановки каждые 50 км (31 миль) для дозаправки их оригинального бака газификатора 1942 года замедляли прогресс.
Отчасти их маршрут был продиктован необходимостью найти лес. Собирать еловые шишки и поваленные ветром деревья можно только в экстренных случаях. Для эффективной газификации древесина должна состоять менее чем на 20% из воды, а это означает, что древесину необходимо тщательно высушить, прежде чем ее можно будет использовать. Влажная древесина не только снижает мощность двигателя за счет добавления пара в смесь и использования тепла для испарения; он также может вызвать «зависание древесины» из-за того, что горение будет настолько медленным, что древесина не сможет попасть в горелку. «Это похоже на мост и не упадет туда, где огонь», — объясняет Линелл.«В центре становится холодно, процесс образования газа останавливается». Он также может распространять сильное тепло в неправильные части системы. «Если вам не повезло, — говорит Линелл, — это их плавит». А если вы вынуждены собирать корм, вы не можете просто использовать что-либо. «Если вы найдете немного засохшее мертвое дерево, вы можете использовать его, но это не может быть сосна, — говорит он, — это должна быть ель. Большая мертвая рождественская елка. Не то, что у тебя дома. Большой ». Газификаторы также не могут сжигать топливо всех форм и размеров.Куски дерева одинакового размера обеспечивают постоянную скорость горения, необходимую для предотвращения «падения давления», внезапной потери мощности. Во время путешествия по Швеции Линелл и его друзья буксировали трейлер с импровизированной машиной для рубки древесины, состоящей из бензопилы, поршня и двигателя старого автомобиля.
(Фото любезно предоставлено Иоганном Линеллом)
Поездка покинула Линелла с вопросами: «Я подумал:« Могу ли я что-нибудь сделать с этими знаниями? Могу ли я получить прибыль? Начать бизнес? » Я мог видеть, что газификация не для автомобилей.Он функционирует, но требует больших затрат. В современном образе жизни слишком много работы, слишком много времени и слишком грязно. Даже если бы у вас была инфраструктура, я не думаю, что люди будут ею пользоваться ». Однако сельскохозяйственные приложения выглядели многообещающими, главным образом потому, что« вы более стационарны — у вас может быть своя куча дров ». Линелл применил свои навыки, чтобы 68-летний трактор и переделали его для работы по деревьям, поваленным ветром. Он решил провести весь 2008 год, проживая самодостаточную, углеродно-нейтральную жизнь на своей семейной ферме в Даларне, Швеция, выращивая картофель, морковь, свеклу, репу и салат на своей новой машине.В конце концов, бизнес-плана не было, и он не получил прибыли. «Я просто взял старый трактор и немного дров в лесу и принялся за работу».
Биомасса для производства электроэнергии | WBDG
Введение
Внутри этой страницы
ЭТА СТРАНИЦА ПОДДЕРЖИВАЕТСЯ
Биомасса используется для отопления помещений, производства электроэнергии и комбинированного производства тепла и электроэнергии. Термин «биомасса» охватывает большое количество разнообразных материалов, включая древесину из различных источников, сельскохозяйственные остатки, а также отходы животных и человека.
Биомассу можно преобразовать в электроэнергию несколькими способами. Наиболее распространенным является прямое сжигание материала биомассы, например сельскохозяйственных отходов или древесных материалов. Другие варианты включают газификацию, пиролиз и анаэробное сбраживание. Газификация производит синтез-газ с полезным содержанием энергии за счет нагрева биомассы меньшим количеством кислорода, чем необходимо для полного сгорания. Пиролиз дает бионефть за счет быстрого нагревания биомассы в отсутствие кислорода. При анаэробном сбраживании образуется возобновляемый природный газ, когда органические вещества разлагаются бактериями в отсутствие кислорода.
Различные методы работают с разными типами биомассы. Обычно древесная биомасса, такая как древесная щепа, пеллеты и опилки, сжигается или газифицируется для выработки электроэнергии. Остатки кукурузной соломы и пшеничной соломы упаковываются в тюки для сжигания или превращаются в газ с помощью анаэробного варочного котла. Очень влажные отходы, такие как отходы животных и человека, превращаются в газ со средним содержанием энергии в анаэробном варочном котле. Кроме того, большинство других типов биомассы можно превратить в бионефть путем пиролиза, которое затем можно использовать в котлах и печах.
В Вудленде, Калифорния, электростанция использует древесину из сельскохозяйственной промышленности.
Источник: NREL
В этом обзоре основное внимание уделяется древесной биомассе, используемой для выработки электроэнергии на промышленных предприятиях, а не в проектах коммунальных предприятий. Тепло биомассы и биогаз, включая анаэробное сбраживание и свалочный газ, рассматриваются на других страницах технологических ресурсов в этом руководстве:
По сравнению со многими другими вариантами возобновляемой энергии, биомасса имеет преимущество диспетчеризации, что означает, что она управляема и доступна при необходимости, подобно системам выработки электроэнергии на ископаемом топливе.Однако недостатком биомассы для производства электроэнергии является то, что топливо необходимо закупать, доставлять, хранить и оплачивать. Кроме того, при сжигании биомассы образуются выбросы, которые необходимо тщательно контролировать и контролировать в соответствии с нормативными требованиями.
В этом обзоре представлены конкретные детали для тех, кто рассматривает системы выработки электроэнергии на биомассе как часть крупного строительного проекта. Дополнительную общую информацию можно получить в Управлении энергоэффективности и возобновляемых источников энергии (EERE) Министерства энергетики США (DOE). Основы технологии биомассы.Подробную информацию об использовании биомассы для комбинированного производства тепла и электроэнергии можно получить в Партнерстве по комбинированному производству тепла и энергии Агентства по охране окружающей среды США (EPA).
Описание
На большинстве биоэлектростанций используются системы сжигания прямого сжигания. Они сжигают биомассу напрямую, чтобы произвести пар высокого давления, который приводит в действие турбогенератор для производства электроэнергии. В некоторых отраслях промышленности, связанных с биомассой, отведенный или отработанный пар электростанции также используется для производственных процессов или для обогрева зданий.Эти системы комбинированного производства тепла и электроэнергии (ТЭЦ) значительно повышают общую энергоэффективность примерно до 80% по сравнению со стандартными системами, работающими только на биомассе, с эффективностью примерно 20%. Сезонные потребности в отоплении повлияют на эффективность системы ТЭЦ.
Простая система выработки электроэнергии на биомассе состоит из нескольких ключевых компонентов. Для парового цикла это включает в себя комбинацию следующих элементов:
- Оборудование для хранения и транспортировки топлива
- Камера сгорания / печь
- Котел
- Насосы
- Вентиляторы
- Турбина паровая
- Генератор
- Конденсатор
- Градирня
- Контроль выхлопа / выбросов
- Система управления (автоматизированная).
Системы прямого сжигания подают сырье биомассы в камеру сгорания или печь, где биомасса сжигается с избытком воздуха для нагрева воды в бойлере и образования пара. Вместо прямого сжигания некоторые развивающиеся технологии газифицируют биомассу для получения горючего газа, а другие производят пиролизные масла, которые можно использовать для замены жидкого топлива. Котельное топливо может включать древесную щепу, пеллеты, опилки или биотопливо. Затем пар из котла расширяется через паровую турбину, которая вращается, чтобы запустить генератор и произвести электричество.
В целом, все системы, работающие на биомассе, требуют места для хранения топлива и некоторого типа оборудования для обработки топлива и средств контроля. Система, использующая древесную щепу, опилки или гранулы, обычно использует бункер или силос для краткосрочного хранения и внешний склад для хранения топлива для более крупных хранилищ. Автоматизированная система управления транспортирует топливо из внешней зоны хранения с использованием некоторой комбинации кранов, штабелеукладчиков, регенераторов, фронтальных погрузчиков, ремней, шнеков и пневматического транспорта. Ручное оборудование, такое как фронтальные погрузчики, можно использовать для переноса биомассы из штабелей в бункеры, но этот метод потребует значительных затрат на рабочую силу и эксплуатацию оборудования и техническое обслуживание (O&M).Менее трудоемким вариантом является использование автоматических штабелеукладчиков для создания штабелей и регенераторов для перемещения щепы из штабелей в бункер или бункер для щепы.
В электроэнергетических системах, работающих на древесной стружке, обычно используется одна сухая тонна на мегаватт-час производства электроэнергии. Это приближение типично для систем с влажной древесиной и полезно для первого приближения требований к потреблению и хранению топлива, но фактическое значение будет зависеть от эффективности системы. Для сравнения, это эквивалентно 20% эффективности HHV с 17 MMBtu / т древесины.
Большая часть древесной щепы, производимой из сырых пиломатериалов, будет иметь влажность от 40% до 55% на влажной основе, что означает, что тонна зеленого топлива будет содержать от 800 до 1100 фунтов воды. Эта вода снизит содержание извлекаемой энергии в материале и снизит эффективность котла, так как вода должна испаряться на первых этапах сгорания.
Самые большие проблемы с установками, работающими на биомассе, связаны с обработкой и предварительной обработкой топлива. Это относится как к небольшим установкам с колосниковым обогревом, так и к большим установкам с подвесным обогревом.Сушка биомассы перед сжиганием или газификацией повышает общую эффективность процесса, но во многих случаях может быть экономически невыгодной.
Выхлопные системы используются для вывода побочных продуктов сгорания в окружающую среду. Средства контроля выбросов могут включать в себя циклон или мультициклон, рукавный фильтр или электрофильтр. Основная функция всего перечисленного оборудования — это контроль твердых частиц, и она указана в порядке увеличения капитальных затрат и эффективности. Циклоны и мультициклоны могут использоваться в качестве предварительных коллекторов для удаления более крупных частиц перед рукавным фильтром (тканевым фильтром) или электростатическим фильтром.
Кроме того, может потребоваться контроль выбросов несгоревших углеводородов, оксидов азота и серы в зависимости от свойств топлива и местных, государственных и федеральных нормативных актов.
Как это работает?
В системе прямого сжигания биомасса сжигается в камере сгорания или печи для получения горячего газа, который подается в котел для выработки пара, который расширяется через паровую турбину или паровой двигатель для производства механической или электрической энергии.
В системе прямого сжигания переработанная биомасса является котельным топливом, который производит пар для работы паровой турбины и генератора для производства электроэнергии.
Виды технологий и стоимость технологий
Есть множество компаний, в основном в Европе, которые продают маломасштабные двигатели и комбинированные теплоэнергетические системы, которые могут работать на биогазе, природном газе или пропане. Некоторые из этих систем доступны в Соединенных Штатах с мощностью от примерно 2 киловатт (кВт) и примерно 20 000 британских тепловых единиц (БТЕ) в час тепла до нескольких мегаватт (МВт). Кроме того, в настоящее время в Европе доступны маломасштабные (от 100 до 1500 кВт) паровые двигатели / генераторные установки и паровые турбины (от 100 до 5000 кВт), которые работают на твердой биомассе.
В США прямое сжигание является наиболее распространенным методом производства тепла из биомассы. Установленная стоимость малых электростанций, работающих на биомассе, составляет от 3000 до 4000 долларов за кВт, а приведенная стоимость энергии — от 0,8 до 0,15 доллара за киловатт-час (кВтч).
Двумя основными типами систем прямого сжигания щепы являются камеры сгорания со стационарной и подвижной решеткой, также известные как топки с неподвижным слоем и камеры сгорания с атмосферным псевдоожиженным слоем.
Стационарные системы
Существуют различные конфигурации систем с неподвижным слоем, но общей характеристикой является то, что топливо тем или иным образом доставляется на решетку, где оно вступает в реакцию с кислородом воздуха.Это экзотермическая реакция, при которой образуются очень горячие газы и пар в секции теплообменника котла.
Системы с псевдоожиженным слоем
В системе с циркулирующим псевдоожиженным слоем или с барботажным псевдоожиженным слоем биомасса сжигается в горячем слое взвешенных негорючих частиц, таких как песок. По сравнению с колосниковыми камерами сгорания, системы с псевдоожиженным слоем обычно производят более полное преобразование углерода, что приводит к снижению выбросов и повышению эффективности системы.Кроме того, котлы с псевдоожиженным слоем могут использовать более широкий спектр исходного сырья. Кроме того, системы с псевдоожиженным слоем имеют более высокую паразитную электрическую нагрузку, чем системы с неподвижным слоем, из-за повышенных требований к мощности вентилятора.
Системы газификации биомассы
Небольшая модульная система биоэнергетики от Community Power Corporation
Хотя системы газификации биомассы встречаются реже, они аналогичны системам сжигания, за исключением того, что количество воздуха ограничено и, таким образом, вырабатывается чистый топливный газ с полезной теплотворной способностью в отличие от сжигания, при котором отходящий газ не имеет теплотворная способность.Чистый топливный газ обеспечивает возможность приводить в действие множество различных типов газовых первичных двигателей, таких как двигатели внутреннего сгорания, двигатели Стирлинга, термоэлектрические генераторы, твердооксидные топливные элементы и микротурбины.
На эффективность системы прямого сжигания или газификации биомассы влияет ряд факторов, включая влажность биомассы, распределение и количество воздуха для горения (избыток воздуха), рабочую температуру и давление, а также температуру дымовых газов (выхлопных газов).
Приложение
Тип системы, наиболее подходящей для конкретного применения, зависит от многих факторов, включая доступность и стоимость каждого типа биомассы (например, щепа, пеллеты или бревна), стоимость конкурирующего топлива (например, мазут и природный газ), пиковые и годовые электрические нагрузки и затраты, размер и тип здания, доступность помещений, наличие рабочего и обслуживающего персонала, а также местные нормы выбросов.
Проекты, которые могут использовать как производство электроэнергии, так и тепловую энергию из энергетических систем, работающих на биомассе, часто являются наиболее рентабельными.Если место имеет предсказуемый доступ к круглогодичным доступным ресурсам биомассы, то некоторое сочетание производства тепла и электроэнергии из биомассы может быть хорошим вариантом. Транспортировка топлива составляет значительную часть его стоимости, поэтому в идеале ресурсы должны быть доступны из местных источников. Кроме того, на предприятии обычно необходимо хранить сырье для биомассы на месте, поэтому доступ на площадку и хранение являются факторами, которые следует учитывать.
Как и в случае с любой другой технологией производства электроэнергии на объекте, система производства электроэнергии должна быть подключена к коммунальной сети.Правила присоединения могут быть другими, если система является комбинированной теплоэнергетической системой, а не только для производства электроэнергии. Возможность использования чистого измерения также может иметь решающее значение для экономики системы.
Руководство Федеральной программы энергоменеджмента (FEMP) по интеграции возобновляемых источников энергии в федеральное строительство содержит дополнительную информацию о требованиях к межсетевым соединениям и чистому измерению.
Экономика
Основные статьи капитальных затрат для энергосистемы, работающей на биомассе, включают в себя хранение топлива и оборудование для обработки топлива, камеру сгорания, котел, первичный двигатель (например,грамм. турбина или двигатель), генератор, элементы управления, дымовая труба и оборудование для контроля выбросов.
Стоимость системы имеет тенденцию к снижению по мере увеличения размера системы. Для паровой системы, работающей только на электроэнергии (не комбинированной), мощностью от 5 до 25 МВт, затраты обычно составляют от 3000 до 5000 долларов за киловатт электроэнергии. Нормированная стоимость энергии для этой системы будет составлять от 0,08 до 0,15 доллара за кВтч, но она может значительно возрасти с расходами на топливо. Для больших систем требуется значительное количество материала, что приводит к увеличению расстояний транспортировки и затрат на материалы.Небольшие системы имеют более высокие затраты на эксплуатацию и техническое обслуживание на единицу произведенной энергии и более низкую эффективность, чем большие системы. Следовательно, определение оптимального размера системы для конкретного приложения — это итеративный процесс.
Существует множество стимулов для производства энергии из биомассы, но они различаются в зависимости от политики федерального законодательства и законодательства штата. База данных государственных стимулов для возобновляемых источников энергии и эффективности® перечисляет стимулы для биомассы. Сроки программ стимулирования часто позволяют меньше времени на строительство, чем необходимо для проектов по биомассе.Кроме того, федеральные агентства часто не могут напрямую воспользоваться финансовыми стимулами для возобновляемых источников энергии, если они не используют другую структуру собственности.
РуководствоFEMP по интеграции возобновляемых источников энергии в федеральное строительство содержит дополнительную информацию о финансировании проектов в области возобновляемых источников энергии.
Интересно, что штат Массачусетс недавно исключил электричество, работающее на биомассе, из своего Стандарта портфеля возобновляемых источников энергии, поскольку официальные лица штата не считали, что биомасса обеспечивает явное сокращение выбросов парниковых газов.Таким образом, проекты, связанные с использованием биомассы, больше не имеют права на получение сертификатов возобновляемой энергии, которые засчитываются для целей или финансирования возобновляемых источников энергии Массачусетса.
Оценка доступности ресурсов
Наиболее важными факторами при планировании энергетической системы на биомассе являются оценка ресурсов, планирование и закупки. В рамках процессов отбора и анализа осуществимости критически важно определить потенциальные источники биомассы и оценить необходимое количество топлива.
Если возможно, детально определите способность потенциальных поставщиков производить и поставлять топливо, отвечающее требованиям оборудования для биомассы.Это может быть немного интенсивный процесс, так как он включает определение нагрузки, которая будет обслуживаться, выявление возможных производителей или поставщиков оборудования, работу с этими поставщиками для определения спецификации топлива и связь с поставщиками, чтобы узнать, могут ли они соответствовать спецификации — и какая цена. Также необходимо оценить ежемесячные и годовые потребности в топливе, а также пиковое потребление топлива, чтобы помочь при обращении с топливом и выборе размеров оборудования для хранения топлива.
Поскольку на большей части территории Соединенных Штатов нет установленной системы распределения древесной щепы, иногда бывает трудно найти поставщиков.Одно из предложений — связаться с региональной лесной службой США и государственной лесной службой. К другим ресурсам, с которыми можно связаться, относятся ландшафтные компании, лесопилки и другие переработчики древесины, свалки, лесоводы и производители деревянной мебели.
Оценки ресурсов биомассы на уровне округа также доступны в режиме онлайн с помощью интерактивного инструмента картографии и анализа. Инструмент оценки биомассы был разработан Национальной лабораторией возобновляемых источников энергии (NREL) при финансовой поддержке EPA. Раньше оценка ресурсов обычно была статической и не позволяла пользователям анализировать данные или манипулировать ими.Этот новый инструмент позволяет пользователям выбрать местоположение на карте, количественно оценить ресурсы биомассы, доступные в пределах заданного пользователем радиуса, и оценить общую тепловую энергию или мощность, которая может быть произведена путем восстановления части этой биомассы. Инструмент действует как предварительный источник информации о сырье биомассы; однако он не может заменить оценку сырья на месте.
Доступные ресурсы биомассы в США.
Источник: NREL
Необходимо разработать процесс приема поставок биомассы и оценки свойств топлива.По состоянию на июль 2011 года национальных спецификаций по древесной щепе нет, но разрабатываются региональные спецификации. Наличие спецификации помогает сообщать и обеспечивать выполнение требований к микросхеме. Спецификация должна включать физические размеры, диапазон содержания влаги в топливе, энергосодержание, содержание золы и минералов, а также другие факторы, влияющие на обращение с топливом или его сжигание. Для обеспечения справедливой стоимости контракты на закупку топлива должны масштабировать закупочную цену обратно пропорционально содержанию влаги, поскольку более высокое содержание влаги значительно снижает эффективность сгорания и увеличивает вес транспортируемого материала.
Вопросы закупок
Следующие ниже рекомендации имеют решающее значение для успеха любого проекта по производству энергии из биомассы.
- Полностью вовлекайте лиц, принимающих решения, и широкую общественность на этапах планирования и по мере достижения прогресса, особенно если система будет установлена в общественном здании.
- Тесно сотрудничать с производителем или поставщиком оборудования, работающего на биомассе, для совместной работы над проектированием зданий и требованиями к оборудованию.
- Согласовать календарное планирование строительства с поставкой оборудования.Например, легче доставить и установить оборудование, если кран имеет доступ к месту установки.
- Определите маршрут доставки топлива, чтобы грузовики могли легко добраться до места хранения и при необходимости развернуться.
Эксплуатация и обслуживание
Затраты на эксплуатацию и техническое обслуживание энергетических систем, работающих на биомассе, в основном состоят из затрат на топливо и рабочую силу. В остальном эти системы аналогичны другим системам производства электроэнергии на базе котлов. Эксплуатация осуществляется непрерывно, поэтому затраты на эксплуатацию, а также на покупку и хранение топлива необходимо оценивать вместе с общими затратами по проекту.
Особенности
Ниже приведены важные особенности электрических систем, работающих на биомассе.
Экологическая экспертиза / разрешение
Основной проблемой NEPA и выдачей разрешений для энергетической системы на биомассе являются выбросы от сжигания. Следовательно, следует пересмотреть местные требования. Выбросы в атмосферу из системы биомассы зависят от конструкции системы и характеристик топлива. При необходимости можно использовать системы контроля выбросов для уменьшения выбросов твердых частиц и оксидов азота.Выбросы серы полностью зависят от содержания серы в биомассе, которое обычно очень низкое.
Хранение щепы требует внимательности, подготовки и внимательности. Когда стружка хранится в здании, существует вероятность скопления пыли от стружки на горизонтальных поверхностях и попадания внутрь оборудования. Обеспокоенность вызывает способность древесной щепы самовоспламеняться или самовоспламеняться при хранении в течение длительного времени, хотя встречается редко. Для получения дополнительной информации см. Информационный бюллетень OSHA по безопасности и охране здоровья Горючая пыль в промышленности: предотвращение и смягчение последствий пожара и взрывов.
Это происходит из-за цепочки событий, которая начинается с биологического разложения органического вещества и может привести к тлею кучи. Критический диапазон влажности, поддерживающий самовозгорание, составляет примерно от 20% до 45%. Вероятность самовозгорания также увеличивается с увеличением размера кучи из-за увеличения глубины.
Чтобы помочь с этой проблемой, Управление пожарной охраны в Онтарио, Канада предоставляет следующие рекомендации:
Место хранения должно быть хорошо дренированным и ровным, с твердым грунтом или вымощенным асфальтом, бетоном или другим твердым материалом.На поверхности земли между сваями не должно быть горючих материалов. Сорняки, трава и подобная растительность должны быть удалены со двора. Переносные горелки с открытым пламенем для сорняков нельзя использовать на площадках для хранения щепы. Сваи не должны превышать 18 м (59 футов) в высоту, 90 м (295 футов) в ширину и 150 м (492 футов) в длину, если временные водопроводные трубы со шланговыми соединениями не проложены на верхней поверхности сваи.
Между штабелями щепы и открытыми конструкциями, дворовым оборудованием или инвентарём должно сохраняться пространство, равное (а) двойной высоте сваи для горючего материала или зданий или (b) высоте сваи для негорючих зданий и оборудования.
В местах скопления щепок курение запрещено.
Возгорание древесной стружки может быть вызвано другими факторами, такими как удары молнии, тепло от оборудования, искры от сварочных работ, лесные пожары и поджоги. Эти пожары иногда называют поверхностными пожарами, потому что они возникают и распространяются по внешней стороне сваи.
При хранении очень важно поддерживать чистоту щепы. Когда щепа хранится на земле или гравии, часть этого материала часто собирается вместе со щепой и попадает в камеру сгорания.
21 февраля 2011 года EPA установило нормы выбросов Закона о чистом воздухе для больших и малых котлов и инсинераторов, сжигающих твердые отходы и осадки сточных вод. Эти стандарты охватывают более 200 000 котлов и инсинераторов, выбрасывающих опасные загрязнители воздуха (HAP), также известные как токсичные вещества. Новые стандарты EPA должны соблюдаться при планировании проекта любого котла для сжигания топлива.
EPA также приняло Закон о чистом воздухе, разрешающий выбросы парниковых газов 2 января 2011 года.Этот процесс, также называемый «правилом адаптации», требует разрешения на производство парниковых газов, но не распространяется на более мелкие предприятия. Ожидается, что окончательные правила будут разработаны в течение трехлетнего исследовательского периода, но федеральные предприятия, использующие производство электроэнергии из биомассы в рамках нового строительного проекта, могут захотеть убедиться, что размер объекта, работающего на биомассе, не вызывает эти требования.
В 2009 году штат Массачусетс издал документ под названием , озаглавленный «Нормы безопасности и выбросов котлов и печей на биомассе в северо-восточных штатах».Несмотря на то, что в этом документе содержится обзор существующих правил в этом регионе, он может быть полезной справочной информацией для других частей страны.
Дополнительные ресурсы
Следующие дополнительные ресурсы могут предоставить более подробную информацию о производстве электроэнергии из биомассы.
Электроресурсы биомассы
Публикации
Вех в развитии машин: тракторы на древесном топливе — Farmers Weekly
Это может показаться немного дурацким, но тракторы могут работать на дереве, что было доказано несколькими изобретениями в сельском хозяйстве за последние годы.
Топливо для трактора, производимое из древесины, представляет собой газ, выделяющийся при нагревании древесины до 700 ° C или более в специально разработанном контейнере, прикрепленном к трактору. Он называется «генераторный газ» или древесный газ и представляет собой смесь азота, окиси углерода, двуокиси углерода и небольшого количества водорода.
Дровяной огонь в основании контейнера нагревает небольшие куски дерева, которые заполняют оставшееся пространство в контейнере, и при этом выделяется газ.
Когда дрова нагревают на открытом огне, доступен кислород для сжигания газа пламенем для получения тепла.
Но в баллоне с газом-генератором огонь в основании использует доступный кислород, а газ, произведенный из нагретой древесины, не горит и не выделяет энергию, пока не достигнет камеры сгорания двигателя.
Промышленный газ может использоваться в качестве топлива для широкого спектра энергоблоков, включая газовые турбины, топливные элементы, двигатели с искровым зажиганием и дизели.
Трактор Fendt G25 времен Второй мировой войны с газогенератором EG60 и двухцилиндровым дизельным двигателем
Большая часть коммерческой продукции генераторного газа поступает от статических установок, вырабатывающих газ для использования в качестве топлива для производства электроэнергии или для сжигания для обеспечения тепла для производственных процессов, и это по-прежнему важно в странах, где имеется много древесины, но есть другие энергоресурсы. не хватает.
См. Также: Вехи машиностроения: Полноприводные тракторы
Электрооборудование
Промышленная добыча газа имеет долгую историю. Его сжигали, чтобы обеспечить тепло для небольших промышленных процессов в начале 1800-х годов, особенно в сельских районах с изобилием древесины.
Гусеничный комбайн Renault, переоборудованный для производства древесного газа
Переносные газовые генераторы, которые можно было использовать в транспортных средствах, включая тракторы, появились в конце Первой мировой войны.
Была нехватка топлива на нефтяной основе, следовательно, был гораздо больший всплеск интереса, когда нехватка моторного топлива снова стала серьезной проблемой в Великобритании и большей части Европы во время Второй мировой войны.
Важность использования тракторов для поддержания производства продуктов питания была признана в конце 1930-х годов, когда Великобритания и другие европейские страны были готовы к войне.
Тягач Renault 304 серии с газогенератором
Правительство Германии организовало исследовательский проект по разработке нового газогенератора специально для тракторов.
Генератор EG60, он был более компактным и удобным в использовании, чем предыдущие модели, и когда во время войны нехватка топлива стала все более серьезной, немецким тракторным компаниям не разрешалось продавать новые тракторы, которые не были оснащены утвержденным газогенератором.
Комплекты производственного газа использовались в большом количестве на тракторах во Франции, Нидерландах и других странах Европы во время войны, меньшее количество — в Великобритании, но комплекты не ограничивались Европой.
Некоторые фермеры в Австралии оборудовали свои тракторы для сжигания древесины из-за опасений военного времени, что японский флот может заблокировать импорт нефти.
Парафин и дизельное топливо
Хотя комплекты для сжигания дров обеспечивали трактору необходимую мощность для поддержания производства продуктов питания во время чрезвычайной ситуации военного времени, они никогда не пользовались популярностью.
Вскоре после того, как война закончилась, и керосин и дизельное топливо снова стали доступны, продажи новых тракторов, оборудованных для сжигания дров, в Европе резко прекратились, и тракторы, ранее оснащенные такими комплектами, были вскоре переведены на обычное топливо.
Единственные тракторы в Германии, в которых сохранилось газогенераторное оборудование, находятся в музеях или принадлежат энтузиастам.
Экспериментальный газогенератор, установленный на Fordson Major E27N примерно 1949 года выпуска
Одним из возражений против заправки тракторов газом-генератором была потеря мощности, обычно около 15-20% по сравнению с парафином и даже выше для дизельных двигателей.
Заполнение генератора небольшими деревянными брусками, а затем зажигание огня и ожидание достаточного количества тепла для начала производства газа могло занять 15-20 минут, и этот процесс нужно было повторять каждые два или три часа, чтобы поддерживать подачу газа, пока трактор работал. работает непрерывно.
Также существовала потенциальная опасность пожара, если нужно было удалить золу от предыдущего пожара, особенно когда трактор работал в поле с сеном или соломой.
Большой размер генератора также был недостатком, поскольку он закрыл обзор с места водителя. Некоторые из самых больших генераторов имели мощность 300 литров или более, но немецкая версия EG60 была 230 литров и была разработана с более низким, менее заметным профилем.
Строгие правила
Существовали также строгие правила выбора, подготовки и хранения древесины для генератора EG60.Бук был первым в списке рекомендованных, за ним следуют береза и другие лиственные породы.
Древесина из хвойных пород была менее подходящей, а чрезмерное содержание смол могло повлиять на работу двигателя и увеличить требования к обслуживанию.
Для достижения наилучших результатов древесину нужно было разрезать на небольшие блоки размером примерно 7 см, и хранение в сухом состоянии было важным, поскольку предпочтительное содержание влаги для генерирования газа составляло 15% или меньше.
Иногда использовались более высокие уровни влажности, в некоторых случаях до 40%, но эффективность добычи газа была намного ниже.
Переносные генераторы для производства газа, оставившие работать многие тысячи тракторов во время Второй мировой войны, вскоре после окончания войны исчезли с ферм в Европе, и на данном этапе перспективы их возрождения невелики.
Газогенератор Martezo французской конструкции конца 1970-х годов
Рост цен на нефть в 1970-х и 1980-х годах побудил к поиску альтернативных видов топлива, но наибольший интерес для двигателей тракторов вызвали такие виды топлива, как биодизель, метан и, в последнее время, электричество, причем генераторный газ редко упоминался.
Несмотря на это, рост цен на нефть способствовал кратковременному оживлению спроса на комплекты для производства газа для тракторов в некоторых странах Африки и Азии, где стоимость топлива имела большое значение.
Новые и улучшенные комплекты газогенераторов были разработаны во Франции для поставок на новые рынки, но продажи были неутешительными, и вскоре спрос иссяк, что, вероятно, стало последним актом в истории тракторов, работающих на дровах.
Газификация древесины — эффективный способ сжигания древесины
Котел для газификации древесины.Древесина сжигается в топке (вверху), а газы движутся вниз и сжигаются при температуре от 1800 до 2000 F в керамической камере внизу. Затем горячие газы проходят через жаротрубный теплообменник для передачи тепла воде, хранящейся в большом резервуаре. Температура дымовых газов обычно ниже 350 F, креозот отсутствует. Древесина должна быть сухой (желательно двухлетней). Из Руководства по установке, эксплуатации и техническому обслуживанию Eko-Vimar Orlanski, https://www.newhorizoncorp.com/PDF/ekomanual.pdf; используется с разрешения. |
Использование опоры для резки позволяет быстро и эффективно раскряжевать множество бревен и веток небольшого диаметра одновременно.Этот метод рекомендуется только тем, кто обучен технике безопасности с бензопилой и имеет опыт работы с бензопилой. Будьте предельно осторожны, обрезая маленькие ветки, и кладите самые большие сверху, так как маленькие кусочки могут быть выброшены в сторону пилорама. Держите пилу на повышенной скорости, так как медленная цепь может зацепиться за мелкую древесину и толкнуть ее в сторону пилорама. Фотографии любезно предоставлены автором |
Бен Хоффман
Правильно высушенная и обожженная древесина является отличным зеленым топливом для отопления сельских районов.Поскольку свежепиленная древесина может на 60 процентов состоять из воды, ключ к минимизации резки, раскалывания и штабелирования древесины — дать ей высохнуть в течение как минимум года. Если вы этого не сделаете, около 40 процентов вашей древесины будет сжигаться только для того, чтобы отогнать воду — никакого нагрева. Большинство печей работают с КПД от 40 до 60 процентов, дровяные котлы, работающие на открытом воздухе, обычно получают от 30 до 50 процентов, а газогенераторы древесины — от 80 до 92 процентов, но главное — это сухая древесина. Через год влажность древесины может составить от 20 до 35 процентов; через два года — от 10 до 20 процентов.В моем газогенераторе для максимальной эффективности требуется влажность от 15 до 25 процентов, поэтому я сушил древесину в течение двух лет и недавно завершил установку солнечной сушилки для древесины, чтобы сократить время сушки.
При газификации дрова сначала сжигаются в обычной топке, затем газы направляются в керамическую камеру сгорания, где температура достигает 1800–2000 F. Все газы и смолы сжигаются, дым не выходит из дымохода, и дымоход остается чистым. Несмотря на высокие температуры в камере газификации, к тому времени, когда газы пройдут через жаротрубный теплообменник котла, температура дымовых газов может достигнуть 350 F.У меня температура дымовых газов обычно ниже 250, что указывает на эффективность теплообменника с дымовыми трубами. Если древесина слишком влажная, огонь охлаждается и из дымохода выходит белый пар. Поскольку котлы с газификацией древесины серийно производятся в Европе, они намного дешевле отечественных моделей. Моя изготовлена в Польше. Теперь я обогреваю свой дом площадью 1400 квадратных футов, подвал и бытовую воду с осени до поздней весны примерно на 3-1 / 2 шнурах. До установки котла мой дом был площадью 1000 квадратных футов, и с дровяной печью для отопления я сжег 3-1 / 2 шнура плюс от 150 до 200 галлонов масла для горячего водоснабжения.
В холодную погоду я разводил один костер в день и держу его около восьми часов. Ключ к эффективности — сухая древесина и быстрое горячее горение. Мой небольшой котел на 85000 БТЕ нагревает воду, хранящуюся в пропановом баке на 500 галлонов, и эта вода циркулирует по запросу для обогрева жилых помещений и бытовой воды. С древесиной годичной давности мой бак достиг максимальной температуры 170 градусов, но с действительно сухой древесиной она достигает 180, что значительно увеличивает БТЕ. Один пожар хорош в течение дня зимой в штате Мэн, но мягкой осенью 2015 года он продолжался два-три дня.Когда цены на нефть упали, летом я сжигал нефть, а не дрова; один пожар может обеспечить горячее водоснабжение на неделю, но большая часть тепла из резервуаров будет потеряна в подвал. Большая семья, принимающая много душа и много стирающая, скорее всего, выиграет от еженедельного ожога.
Древесина — идеальное топливо для отопления сельской местности в штате Мэн, особенно если у вас есть лесной участок. Заготовки дров — это возможность улучшить лес за счет удаления мертвых, умирающих, больных и плохо сформированных деревьев, позволяя остаточным деревьям расти быстрее, производить больше кислорода и использовать больше парниковых газов CO2.Если вы садовод, древесная зола добавляет в почву кальций, калий, другие питательные вещества и биоуглерод (но применяйте ее только после и в соответствии с рекомендациями теста почвы, поскольку древесная зола может быстро и чрезмерно повысить pH почвы). С точки зрения энергии покупать древесину у местного поставщика намного лучше, чем покупать пеллеты издалека, и сводит к минимуму потребление моторного топлива. Он также обеспечивает местную занятость и сохраняет деньги в местной экономике.
Я вырезал примерно половину своей древесины из крошечного лесного массива и использую верхушки и ветки примерно 1-1 / 2 дюйма в диаметре для кухонной плиты.Ветви и дерево менее 4 дюймов эффективно раскряжевываются в «стойке для резки», сделанной несколько лет назад одним другом.
О нас — ВСЕ Power Labs
– Если бы вы могли постоянно превращать много органического материала в биоугля, вы могли бы со временем обратить вспять историю последних двухсот лет … Мы можем буквально начать всасывать часть углерода, который наши предшественники выливали в сквозь наши сорняки и стебли проникает атмосфера, и воткнуть ее обратно в землю. Мы можем запустить фильм в обратном направлении.Мы можем добыть часть угля, немного разбурить нефть ».
Билл Маккиббен
МОЩНОСТЬ ПОСЛЕДНЕГО ПОКОЛЕНИЯ
Представляем новейшую генераторную установку Power Pallet, работающую на биомассе, новую PP30. Теперь с постоянной мощностью 25 кВт при 60 Гц. Мы также включаем функции параллельного подключения к электросети, комбинированного нагрева и мощности и шумоподавляющий кожух двигателя, а также средства контроля выбросов в качестве стандартного оборудования.
Это наш самый продвинутый поддон Power Pallet из когда-либо существовавших, обеспечивающий беспрецедентную максимальную эффективность 80% тепловой + электрической энергии.Мы достигаем этого с помощью нашей уникальной трехступенчатой системы ТЭЦ, а также нашей и без того беспрецедентной выработки — более одного киловатт-часа электроэнергии на килограмм биомассы.
Мы также модернизировали двигатель и систему фильтрации PP30, теперь используя 4,0-литровый двигатель Heavy Duty Ashok Leyland и рукавный фильтр с возможностью очистки на месте, который стал еще более эффективным и долговечным благодаря точному контролю температуры для дегтя и водяной росы. точечное управление.
All Power Labs — мировой лидер в области маломасштабной газификации.Мы производим генераторы-газификаторы биомассы, готовые к повседневной работе, для удовлетворения реальных потребностей в распределенной энергии.
Наши Power Pallet и Powertainer — это новая категория энергетических устройств. Они сочетают в себе лучшие эксплуатационные характеристики дизельных генераторов с экологически чистым использованием типичных возобновляемых источников энергии с потенциалом отрицательного воздействия углерода.
Наш проект начался в 2008 году с открытого набора Gasifier Experimenter’s Kit (GEK), поддерживающего исследования, обучение и самодельные взломы в области термического преобразования биомассы.Спустя более десяти лет GEK превратился в Power Pallet, полное решение для коммерческого производства электроэнергии из биомассы. Сегодня наши системы работают в десятках стран по всему миру и поддерживают исследования в более чем 50 университетах.
С помощью продуктов APL вы можете вырабатывать электроэнергию по требованию за 1/4 эксплуатационных расходов дизельного топлива при 1/2 капитальных затрат на солнечную энергию. И, экономя деньги, вы можете сократить свой углеродный след и внести позитивный вклад в глобальные усилия по борьбе с изменением климата.
Правильная энергетика и климат
Ставка на правильное использование энергии и климата устрашающая. Огромный объем углерода, который мы выкопали из древних резервуаров со времен индустриализации и вернули в современную циркуляцию, трудно осознать — мы собрали здесь некоторые детали. До сих пор нам в основном удавалось игнорировать последствия этого ограбления могил, поскольку повышение температуры из-за накопления СО2 отстает на десятилетия, если не столетия.
APL Углеродноотрицательное оборудование: сегодня и будущее
Процесс газификации является неполным, и оставшиеся «отходы», производимые нашим оборудованием при производстве энергии, представляют собой стабильную форму углерода, известную как «биоуголь».«Секвестрация этого углерода — вот что делает газификацию биомассы чистой углеродно-отрицательной энергией.
Хотя современные APL Power Pallets производят относительно небольшое количество побочного продукта биоугля (около 5% от исходной массы), этого все же достаточно для углеродного отрицательного заряда в топливном цикле. Круглое эмпирическое правило:
.- Из 1 тонны сухой биомассы производится около 1 МВт / ч электроэнергии и 50 кг побочного продукта углерода.
- 50 кг сырого углерода после рекомбинации с O2 эквивалентны 185 кг CO2 в атмосфере.(масса C x 3,67 = масса CO2)
- 1 тонна биомассы, поступающая в газогенератор, может улавливать почву, эквивалентную 0,185 тонны CO2 в атмосфере.
- Выбросы CO2, которых удалось избежать в результате отказа от сжигания ископаемого топлива, добавляются к вышеупомянутым результатам.
Будущие машины APL, включая наш новый пиролизатор Chartainer Biochar, представят функции, которые позволят увеличить выход биоугля до 15-20% от исходной массы, при одновременном совместном производстве электроэнергии и / или тепла. Наш пилотный Chartainer производит 40кр / час высококачественного, высокотемпературного, геопроводящего биоугля!
На данный момент мы просто используем закалочную обугливание с 5% -ным вводом в нашей работе с нашим проектом по снижению выбросов: Local Carbon Network.Мы обнаруживаем, что влияние этого биоугля, особенно когда он компостируется и используется в органическом сельском хозяйстве, гораздо более значимо, чем мы ожидали. Мы наблюдаем значения до 40 кг CO2-экв на 1 кг биоугля! Ознакомьтесь с превосходным анализом Остина Лю на сайте LCN.
Подробнее о нашем анализе углерода можно узнать здесь. Вы также можете прочитать фантастические репортажи о подготовке к COP21 в The Guardian. А если взглянуть на это неординарным инсайдером, то нам действительно нравится блог Джереми Леггетта «Победа в углеродной войне».
ПО ТРЕБОВАНИЮ, ДОСТУПНАЯ, ОТРИЦАТЕЛЬНАЯ ЭНЕРГИЯ УГЛЕРОДА
https://www.facebook.com/tr?ev=6028954195142&cd[value visible=0.00&cd[currencypting=USD&noscript=1
Чтобы узнать о том, как наши машины помогают решить глобальный кризис, связанный как с доступностью энергии, так и с изменением климата, посетите нашу страницу проектов. или щелкните один из различных сценариев использования ниже
Исследование ТЭ (термоэлектрического) генератора, встроенного в многофункциональную дровяную печь
Abstract
Замена традиционных открытых топок, характеризующихся низкой эффективностью, на более совершенные, является важной задачей для развивающихся стран.Добавление ТЭ (термоэлектрических) генераторов может обеспечивать электричество, которое позволяет не только использовать электрический вентилятор, увеличивая соотношение воздуха к топливу для достижения полного сгорания в печах, но также удовлетворять основные потребности: свет, телефоны и другие электронные устройства. Представлен обзор существующих генераторов ТЭ для печей. Для тестирования ТЕ-модулей в нашей лаборатории была проведена экспериментальная установка, в которой газовый обогреватель имитирует печь. Описана генераторная установка, включая импульсный электрический регулятор, который стабилизирует колебания напряжения от модулей и накапливает энергию в батарее.Производительность генератора в основном зависит от теплопередачи через модули и особенно от теплового контактного сопротивления. Первые эксперименты показывают влияние давления на эти сопротивления. Затем исследование температуры и измерения электрической мощности сравнивается с теоретическим анализом с использованием ТЕ и уравнений теплопередачи. Очень разумное значение полученных контактных сопротивлений показывает, что механическая конструкция генератора практически оптимизирована. Генератор TE произвел до 9.5 Вт.
Особенности
► ТЭ (термоэлектрический) генератор мощностью 9,5 Вт для печи на биомассе. ► Производительность генератора TE во многом зависит от сопротивления теплового контакта. ► 500 кПа (5 бар) — разумное значение для минимизации контактного сопротивления модулей TE. ► Одномодульный генератор TE может производить около 7,6 Вт стабилизированной электроэнергии с экономическими затратами, конкурентоспособными с солнечными батареями.