- Ретортная печь Nabertherm NR (NRA)
- Конструкция ретортных и муфельных печей — Черная и цветная металлургия на metallolome.ru
- Вакуумные печи для отпуска (ретортная печь) — НПО Группа компаний машиностроения и приборостроения
- Ретортные печи | СКБ-4
- Конструкция ретортных и муфельных печей
- Что такое Вращающаяся ретортная печь, определение термина в Металлы и сплавы. Справочник
- Инновационная вращающаяся ретортная печь, рассчитанная на долгий срок службы
- Вакуумные ретортные печи с горячими стенками
- Системы вращающихся ретортных печей — SECO/WARWICK
- Патент США на вращающуюся ретортную печь. Патент (Патент № 4,648,836, выдан 10 марта 1987 г.) печь для непрерывной термической обработки заготовок, включающая в себя ретортный узел, образованный цилиндрическим осевым элементом и спирально навитым трубопроводом, расположенным на внешней поверхности осевого элемента для перемещения заготовки от одного конца ретортного узла к другому концу.
- Серия XLC — L&L Special Furnace Co, Inc.
- Ретортная печь | ONEJOON Kilns & Furnaces
- Процессы
Ретортная печь Nabertherm NR (NRA)
Ретортная печь Nabertherm NR (NRA) — ООО «ГЕФЕСТ»- Главная
- Металлообрабатывающее оборудование
- Термообработка
- Ретортные печи
- Ретортная печь Nabertherm NR (NRA)
Описание
Горизонтальные ретортные печи серии NR/NRA
Горизонтальные ретортные печи предназначены для осуществления операций термической обработки изделий, в зависимости от комплектации, при температурах до 1100⁰С.
Данный тип оборудования обеспечивает возможность проведения следующих технологических операций термической обработки изделий: закалка изделий с имитацией условий охлаждения в среде воздуха, отжиг, отпуск, пайка, спекание, отжиг в среде водорода.
Особенности оборудования:
- при условии нагрева изделий до 600⁰С обработка происходит в условиях вакуума
- при условии нагрева изделий свыше 600⁰С обработка происходит в условиях защитного газа
- прямой или косвенный нагрев изделий (нагревательные элементы располагаются или внутри реторты или на внешней её стороне)
- дверь печи оснащена электромеханическим замком, предотвращающим нарушение герметичности рабочей камеры печи
- русифицированная система управления
- система уплотнений двери печи и воротник реторты оснащены системой водяного охлаждения
- система КИПиА позволяет осуществлять визуальный контроль и отслеживание объёмов расхода газов и воды
- система управления позволяет осуществлять контроль за работой систем оборудования и в случае возникновения неисправности оповещать персонал световым или звуковым сигналом
- система нагрева обеспечивает возможность многозонной схемы
- оборудование соответствует второму классу точности распределения тепловой энергии согласно требованиям стандарта AMS 2750E
- комплектация оборудования вакуумными насосами позволяет обеспечивать уровень вакуума в рабочей камере печи не хуже 5, 5×102 и 5×105 мбар
- обеспечивается обработка изделий при условии парциального (избыточного) давления (значение парциального давления — 50 мбар)
Дополнительное оборудование:
- система обработки изделий в среде чистого водорода
- погрузчики садки
- система конвективного нагрева
- система автоматического регулирования подачи газа
- система выбора рабочего газа
- датчик уровня остаточного кислорода
Модель | Тмакс, ⁰С | Полезные размеры камеры, мм | Объем, л | ||
ш | г | в | |||
NRA 17/.![]() |
650/950/1100 | 225 | 350 | 225 | 17 |
NRA 25/.. | 650/950/1100 | 225 | 500 | 225 | 25 |
NRA 50/.. | 650/950/1100 | 325 | 475 | 325 | 50 |
NRA 75/.. | 650/950/1100 | 325 | 700 | 325 | 75 |
NRA 150/.. | 650/950/1100 | 450 | 750 | 450 | 150 |
NRA 200/.![]() |
650/950/1100 | 450 | 1000 | 450 | 200 |
NRA 300/.. | 650/950/1100 | 570 | 900 | 570 | 300 |
NRA 400/.. | 650/950/1100 | 570 | 1250 | 570 | 400 |
NRA 500/.. | 650/950/1100 | 720 | 1000 | 720 | 500 |
NRA 700/.. | 650/950/1100 | 720 | 1350 | 720 | 700 |
NRA 1000/.![]() |
650/950/1100 | 870 | 1350 | 870 | 1000 |
Основные типы печей:
C прямым нагревом
- Максимальная рабочая температура 650°С.
- Материал реторты жаропрочный сплав.
- Устанавливаемый в реторте вентилятор обеспечивает чёткий контроль за уровнем температуры нагрева начиная от 150°С.
- Система нагревательных элементов расположена с внешней стороны реторты.
C косвенным нагревом
- Максимальная рабочая температура 950°С.
- Материал реторты жаропрочный сплав.
- Устанавливаемый в реторте вентилятор обеспечивает чёткий контроль за уровнем температуры нагрева начиная от 150°С.
- Система нагревательных элементов расположена с внешней стороны реторты.
C косвенным нагревом
- Максимальная рабочая температура 1100°С.
- Материал реторты жаропрочный сплав.
- Система нагревательных элементов расположена с внешней стороны реторты, также осуществляется нагрев внутреннего пространства реторты со стороны двери.
Эти газонепроницаемые ретортные печи в зависимости от температуры оснащаются системой прямого или косвенного обогрева. Они превосходно подходят для разнообразных термических процессов, при которых требуется определенный защитный газ или атмосфера реакционного газа. Также эти компактные модели подходят для термических процессов под вакуумом до 600 °C. Полезное пространство состоит из газонепроницаемой реторты, которая в области двери оснащена водяным охлаждением для защиты специального уплотнения. Ретортные печи, оснащенные соответствующими устройствами безопасности, подходят для применения под реакционными газами, например водородом, а также для инертного выжигания или процессов пиролиза при оснащении пакетом IDB.
Комплектация
Стандартная комплектация:
- Компактный корпус в виде рамной конструкции с использованием стальных листов
- Интегрированные в корпус печи системы управления и подачи газа
- Сваренные подставки для загрузки в реторте и короб воздуховода в печах с атмосферной системой циркуляции
- Навешенная справа поворотная дверь с открытой системой водяного охлаждения
- Многозонное регулирование для версий 950 °C и 1100 °C, отдельно в зависимости от газового пространства печи и двери.
В зависимости от размера газовое пространство печи дополнительно разделено на одну или несколько зон нагрева.
- Управление температурой, осуществляемое при управлении загрузкой с измерением температуры внутри и снаружи реторты
- Система подачи газа для негорючего защитного газа с расходомером и электромагнитным клапаном, включается посредством системы управления
- Возможность вакуумирования до 600 °C, вакуумный насос поставляется опционально
- Возможность подключения вакуумного насоса для холодного вакуумирования
- Управление с помощью программируемого контроллера с сенсорной панелью H 700 для ввода данных (или P 300 для версии 650 °C)
Технологические операции:
- Пайка
- Пайка в среде водорода
- Отжиг
- Отпуск
- Старение
- Спекание
Опции:
- Оснащение для других негорючих газов
- Автоматическая подача газа, включая регулятор массового расхода MFC для изменяющегося объема потока, контролируемый с помощью системы ПЛК-управления с сенсорной панелью H 3700
- Вакуумный насос для вакуумирования реторты до 600 °C, в зависимости от насоса может быть достигнут вакуум до 105 мбар
- Система охлаждения для сокращения времени протекания процессов
- Теплообменник с закрытой системой водяного охлаждения для двери
- Измерительное устройство для определения остаточного содержания кислорода
- Система дожигания паров связующего вещества из рабочей камеры
- Вакуумный насос для обеспечения вакуума не хуже 5×102 мбар
- Погрузчик садки
- Замкнутая система водяного охлаждения
- Столы для подготовки/разборки садки
Поделиться
Назад к списку
Наши специалисты ответят на любой интересующий вопрос по товару
Задать вопрос
Цель нашей компании —
предложение широкого ассортимента товаров и услуг на постоянно высоком качестве обслуживания.
Конструкция ретортных и муфельных печей — Черная и цветная металлургия на metallolome.ru
Главная » Без рубрики
Рубрика: Без рубрики
1. Дистилляционная цинковая печь
2. Печь с вертикальной ретортой
3. Барабанная муфельная печь
4. Вращающаяся вакуумная электропечь для восстановления магния ферросилицием
Дистилляционная цинковая печь
Регенеративная трехрядная дистилляционная цинковая печь с горизонтальными шамотными ретортами показана на рис. 228. Печь отапливается генераторным газом, общее число реторт в ней достигает 216 при общей длине печи вместе с регенераторами 21,5 м. Реторты имеют поперечные размеры 0,2×0,3 м и длину 1,8—2,0 м при толщине стенок 25—50 мм. На открытом конце каждой реторты надет шамотный конденсатор для цинка длиной 0,5—0,9 м, газы из которого выходят через металлическую насадку, называемую алонжем и служащую для улавливания цинка в виде пыли. Реторты обогреваются снаружи в результате сжигания генераторного газа, подводимого по одному из верхних парных каналов. Генераторный газ и воздух после подогрева в регенераторах, расположенных на торцах печи, поступают в печь по левой паре каналов. Продукты горения проходят сначала левую часть печи сверху вниз, переходят в правую часть печи, по которой попадают в правую пару каналов, отводящих их в регенераторы. По мере охлаждения насадки регенераторов через каждые 30 мин перекидываются клапаны, регулирующие движение газов, которое начинает происходить уже в обратном направлении, справа налево. Печь работает по периодическому режиму. Вначале все реторты загружают шихтой, состоящей из обожженных цинковых концентратов, угля и оборотов. После загрузки на реторты надевают конденсаторы и алонжи и начинают разогрев печи до 1300—1400° С. Пары цинка конденсируются в конденсаторе, откуда расплавленный цинк вычерпывают ложкой. После удаления из шихты основной части цинка оставшуюся массу, называемую раймовкой, выгребают из реторт, чистят и ремонтируют печь и далее цикл повторяют. Общая продолжительность одного цикла 24 ч.
В каждую реторту загружают до 100 кг шихты, что при 216 ретортах дает суточную производительность печи по шихте около 20 т (5—6 т цинка). Топлива на обогрев реторт и в шихту дистилляции расходуется до 3 т на 1 т полученного цинка.
Аналогичные ретортные печи, но с металлическими ретортами, работающими под вакуумом, с газовым и электрическим наружным обогревом применяют для восстановления окиси магния в металлургии магния.
Описанная ретортная печь имеет следующие существенные недостатки:
- периодичность работы;
- немеханизированные основные операции обслуживания;
- большой расход топлива и огнеупоров;
- низкое прямое извлечение цинка (80—75%).
Печь с вертикальной ретортой
Более совершенная дистилляционная цинковая печь — печь с вертикальной ретортой (рис. 229) для непрерывного ведения процесса. В ней сохранен принцип косвенного обогрева шихты, характерный для дистилляционных печей с горизонтальными ретортами. Поперечное сечение реторты имеет форму вытянутого прямоугольника с ограниченной шириной 300—330 мм и длиной 1600—1800 мм. Реторта имеет высоту около 8 ж и выполнена из карборундовых плит, отличающихся высокой огнеупорностью и теплопроводностью. Торцы реторты можно собирать из шамотных блоков. Шихту в реторту загружают сверху через герметический затвор, а раймовку выпускают снизу через герметическое выпускное отверстие. Печь отапливается генераторным газом, который подводится через горелки, находящиеся в своде камеры. Для создания равномерной температуры воздух для горения вводят в камеру в нескольких точках по высоте. Отходящие газы направляют в рекуператор для подогрева воздуха. Пары цинка отводят в конденсатор, состоящий из двух частей, работающих в различных температурных условиях. В первой части, выполненной в виде канала из карборундовых блоков, пары цинка быстро охлаждаются, чему способствуют высокая теплопроводность карборунда и турбулентное движение газов вокруг перегородок.
Во второй, зумпфовой, части конденсатора скапливается жидкий металл и во избежание образования большого количества пусьеры газы здесь охлаждаются медленно из-за теплоизоляции этой части конденсатора. Выходящие из конденсатора газы очищают в скруббере и далее сжигают в нагревательных камерах печей.
Нормальная работа печей с вертикальными ретортами возможна только на хорошо подготовленной брикетированной шихте. Шихту для брикетирования составляют из цинкового агломерата, коксующегося угля и связующих веществ. Брикеты после изготовления их на прессах коксуют в шахтных печах, и только после коксования горячие брикеты периодически загружают в верхнюю часть реторты.
В верхней части реторты высотой 2—4 м, выложенной из шамотного кирпича, брикеты нагреваются теплом восходящих ретортных газов. В среднюю, обогреваемую снаружи часть реторты брикеты приходят подогретыми до 1000° С и здесь нагреваются до 1270—1300°С. Продолжительность пребывания брикетов в зоне нагрева около 30 ч, что в сочетании с высокой температурой обеспечивает достаточно полное восстановление окиси цинка.
Цинковые пары и газы, поднимаясь вверх, проходят через столб брикетов и поступают в конденсатор, где цинковые пары конденсируются в интервале температур 850—870° С на входе и 530—560° С на выходе. Для облегчения отвода паров цинка из реторты в нижнюю часть ее вводят небольшое количество воздуха или нейтральных газов. Жидкий металл стекает в зумпф конденсатора и по мере накопления выпускается.
Производительность вертикальной реторты по цинку составляет 3—5 т/сутки. Извлечение металла выше, чем в горизонтальных ретортах, и достигает 90% и более. Кампания вертикальных реторт длится от 3 до 5 лет.
Барабанная муфельная печь
Муфельные печи могут быть барабанные вращающиеся.
На рис. 230 показана вращающаяся барабанная муфельная печь 2,2×14 м, изготовляемая Уральским заводом химического машиностроения. Печь состоит из стального барабана диаметром 2,2 м, футерованного шамотным кирпичом. Внутри этого барабана устроен стальной цилиндрический муфель диаметром 1,4 м и длиной 14,5 м, изготовленный из стали Х23Н18. Этот муфель удерживается внутри барабана на специальных опорах с пружинными амортизаторами и вращается вместе с барабаном печи. Муфель обогревается снаружи дымовыми газами, двигающимися в кольцевом промежутке между наружной поверхностью муфеля и футеровкой барабана.
Максимальная температура газов на входе в печь 950° С, на выходе 350° С. Температура реакционных газов на выходе из муфеля до 600° С. Барабан печи приводится во вращение электромотором 8,5—18 квт при числе оборотов барабана от 0,6 до 2 об/мин. Дымовые газы для обогрева получаются в специальной выносной топке, на рисунке не показанной. Печь можно применять для прокалки, обжига, восстановления различных сыпучих материалов в регулируемой газовой атмосфере.
На рис. 231 приведена вращающаяся муфельная электропечь, применяющаяся для восстановления металлических порошков, а также для обработки различных материалов газами. Печь состоит из металлического вращающегося барабана диаметром 0,46 м и длиной 2,3 м, изготовленного из специального жароупорного сплава. Внутренняя полость барабана для лучшего перегребания материала оборудована лопастями. Барабан нагревается снаружи силитовыми или нихромовыми нагревателями, включенными в электросеть. Обрабатываемый материал в смеси с восстановителем загружают в печь через бункер с помощью уплотненного шнекового питателя. Выгрузка производится также шнековым питателем, служащим одновременно и холодильником. Восстанавливающие или защитные газы — водород, окись углерода и азот — подают в холодильник и в разгрузочную камеру. Печь имеет мощность 60 ква и рабочее напряжение 50—225 в. Нагревательные элементы — 16 силитовых стержней размером 0,025×0,81×1,37 м. Производительность печи по перерабатываемым материалам 1—3 т/сутки. Максимальная рабочая температура 1200° С.
Вращающаяся вакуумная электропечь для восстановления магния ферросилицием
На рис. 232 показана вращающаяся вакуумная электропечь для восстановления магния ферросилицием. Реторта печи имеет цилиндрическую форму и расположена на роликах, позволяющих непрерывно вращать ее для перемешивания шихты.
Реторта состоит из двух сообщающихся частей: реакционной камеры, футерованной кирпичом, и конденсатора из жаропрочной стали. Шихта в реакционной камере нагревается угольными стержнями, расположенными по оси печи и включенными в электрическую сеть. Печь работает периодически по следующему режиму. Реакционную камеру заполняют брикетированной шихтой ниже нагревателей через специальное загрузочное отверстие 7. После уплотнения камеры и конденсатора включают электронагреватели, и печь начинает вращаться, температура в рабочей камере поднимается до 1400—1500° С. Вследствие вращения печи вся шихта равномерно прогревается в течение 4—5 ч. Конденсатор и камера во время работы находятся под глубоким вакуумом, и давление в камере составляет 1—3 мм рт. ст. Пары магния собирают в конденсаторе, где охлаждаются. Полученный металлический магний выплавляют в специальной электропечи. Остатки шихты из реакционной камеры выгружают через то же отверстие, печь снова загружают свежей шихтой и начинают следующую операцию. Печь вмещает одновременно до 2 т шихты и имеет мощность 500 ква. Время обработки одной загрузки 6 ч, что обеспечивает производительность печи по магнию 1 т/сутки. Расход электроэнергии на восстановление и дистилляцию магния составляет 12—14 квт-ч/кг Mg.
Общий расход энергии, включая все побочные операции, 20 квт-ч/кг. Возможно увеличение производительности печей этого типа по магнию до 3 т/сутки.
0 2 194 просмотров
Понравилась статья? Поделиться с друзьями:
Вакуумные печи для отпуска (ретортная печь) — НПО Группа компаний машиностроения и приборостроения
- Навигация
- Производители
- Продукция
- Закупки
- Услуги
0 Войти
Все совпаденияПроизводителиПродукцияУслугиЗакупки
- Главная
- Продукция
- НПО Группа компаний машиностроения и приборостроения
- Вакуумные печи для отпуска (ретортная печь)
Вакуумные печи для отпуска — специализированные устройства, которые выполняют рекристаллизацию сплавов, что приводит к распаду мартенсита (особенная структура, которая характерна закаленным металлам, микроуровень игольчатого или реечного типа). Реторная печь в качестве основы имеет герметичную ретору, снаружи основного элемента расположилось оборудование для нагрева. Внутрь устройства запускается нейтральный газ или же в нем создается разряжение, что зависит от проводимого вида обработки. Конструкция такой печи не предполагает наличия термической изоляции в виде водяной рубашки.
Предлагаем печи с нестандартными габаритами рабочей зоны по спецификации заказчика.
Из-за эффективности и невысокой стоимости печи получили широкое распространение в различных сферах деятельности. Такие печи активно участвуют в производстве изделий, которые в ходе эксплуатации подвергаются высоким нагрузкам. Очень часто такое оборудование встречается в авиационной и автомобильной промышленности. А работу современных металлургических и сталелитейных предприятий сегодня невозможно представить без вакуумных печей отпуска.
https://gkmp32.com/electro/vakuumnye-pechi-dlya-otpuska-retortnye/
Категории
- Специальная техника
- Прочая специальная техника
- Прочая спецтехника
Оставить отзыв
Похожие товары
Установки вакуумного напыления типа МАП-1, МАП-2, МАП-3
НПО ГКМП
Современные технологические процессы требуют современных высокотехнологичных. ..
Установки вакуумного напыления типа УВН-71, УВН-74
НПО ГКМП
Во времена Советского Союза для собственных нужд электронной, авиакосмической,…
Термокопрессионные установки
НПО ГКМП
Термокомпрессия — физический процесс, совмещающий в себе нагрев изделия или…
Термодиффузионные установки
НПО ГКМП
Термическая диффузия — физико-химический процесс, изменяющий структуру…
Конвейерные печи
НПО ГКМП
Конвейерная электропечь — электропечь сопротивления проходного типа с…
Контакты компании
- Телефон: +74832581966
- Почта:
msk@gkmp32.
com
- Сайт: https://gkmp32.com/
Отправить сообщениеЗапросить прайс-лист
B2B каталог для производителей и закупщиков
© «Производитель.рф», 2022
- Производители
- Продукция
- Закупки
- Услуги
- Публикации
- Добавление компаний
- Добавить закупку
- Рубрикатор
- Все производители
- О сайте
- Тарифы
- Техническая поддержка
- Правила сайта
Пользуясь данным сайтом, вы соглашаетесь с пользовательским соглашением и политикой конфиденциальности
Размещенные цены не являются публичной офертой
Ретортные печи | СКБ-4
Ретортные печи используются в случае необходимости изолирования рабочего объема печи от окружающей среды как для защиты от воздействия воздуха (термообработка в защитных газах, вакууме), так и для защиты окружающей среды и персонала от негативного воздействия газовой среды печи (термообработка в присутствии горючих, ядовитых, химически-агрессивных газов).
Каталог
Гидравлика и пневматика
Гидравлические узлы
Пневматические узлы
Пневмоинструменты
Гидравлические инструменты
Мониторинг и диагностика
Программное обеспечение
Муфты и приводное оборудование
Уплотнения
Металлические уплотнения
Композитные уплотнения
Неметаллические уплотнения
Станочное оборудование
Намоточные станки
Инструменты
Абразивные инструменты
Алмазные инструменты
Режущие инструменты
Детали и узлы машин и механизмов
Крепежные детали
Механические передачи
Приводные ремни
Поликлиновые ремни
Contitech CONTI-V
Клиновые ремни
Contitech CONTI-V
Зубчатые ремни
Contitech CONTI
Вариаторные ремни
Contitech CONTI-V
Промышленные редукторы
Подшипники
Тормоза
Упругие элементы
Запорно-регулирующее оборудование
Запорная арматура
Защитная арматура
Обратная арматура
Элементы трубопроводов, котлов и сосудов
Фазо – и продукторазделительная арматура
Смесительно-распределительная арматура
Регулирующая арматура
Контрольная арматура
Комбинированная арматура
Компрессорное оборудование
Компрессоры
Воздуходувки
Контрольное, измерительное оборудование
Измерительные инструменты
Измерение геометрических величин
Определение плотности
Измерение давления
Высокоточные преобразователи давления
Манометры
Манометры для систем пожаротушения
Дифференциальные манометры
Цифровые манометры
Промышленные манометры
Измерение времени и частоты
Геофизические измерения
Вторичные приборы для измерительных средств
Виброакустические измерения
Весоизмерительное оборудование
Прецизионные весы
Весы прецизионные 3-й знак
Весы прецизионные 2-й знак
Весы прецизионные 1-й знак
Весы аналитические
Весы начального уровня
Порционные весы
Портативные весы
Платформенные весы
Принадлежности для взвешивания
Измерение механических величин
Гири
Аксессуары для гирь
Радиоэлектронные измерения
Электромагнитные измерения
Экологические измерения
Влагомеры
Физико-химические измерения
Системы измерения характеристик средств транспорта
Системы измерения и контроля вакуума
Радиационные измерения
Поисковое оборудование
Оптические измерения
Медико-биологические измерения
Измерительные системы специализированные
Измерения в системах связи
Измерения в отраслях ТЭК
Измерение уровня
Измерение температуры
Термометры
Биметаллические термометры
Измерение параметров потока
Материалы
Промышленные материалы
Металлопрокат черный и нержавеющий
Металлические изделия
Подъемно-транспортное оборудование
Грузоподъемные машины
Конвейерное оборудование
Транспортирующие машины
Машины напольного транспорта
Пневматические модели Rollers
Пневматические модели Pusher&Puller
Пневматические модели P&P&Litfer
Электрические модели Rollers
Электрические модели Push&Puller
Метрологическое и лабораторное оборудование
Электрохимические измерения
Портативные приборы
Настольные электрохимические приборы
Карманные электрохимические приборы
Электрохимия
Ионселективные электроды и аксессуары
Датчики рН ОВП и температуры
Датчики для кондуктометров
Аксессуары и принадлежности
Five приборы
Кислородные датчики
Кабели и адаптеры
Портативные приборы
Растворы
Электроды и аксессуары
Стационарные приборы
Центрифуги
Титрование
Титраторы
Аксессуары для титраторов
Бюретки, электроды и аксессуары к ним
Автоматические податчики
Принадлежности и расходные материалы
Роторы и адаптеры для центрифуг Frontier
Растворы для электрохимии
Аксессуары
Определение состава
Анализаторы влагосодержания
Весы лабораторные
Ультрамикровесы
Аналитические весы
Весы 10-1 мг (2-3 знак)
Весы 0,1-0,01 мг (4-5 знак)
Дозирование
Пипетки многоканальные
Аксессуары для пипеток
Пипетки одноканальные
Атомная спектроскопия
Лабораторная мебель
Боксы микробиологической безопасности
Изоляторы положительного давления
Шкафы для стерильного хранения
Шкафы вытяжные
Передвижная тележка
Ламинарные укрытия
Инкубаторы
Оборудование для пробоподготовки
Шейкеры
Нагревательные плитки
Магнитные мешалки с нагревом
Диспергаторы
Вортексы
Верхнеприводные мешалки
Магнитные мешалки без нагрева
Оборудование для кристаллографии
Молекулярная спектроскопия
Микроскопия
Лабораторная посуда
Приборы для определения температуры плавления
Аксессуары для MP50 MP70 MP99 DP70 DP90
Фильтры и фильтрующее оборудование
Воздушные фильтры
Промышленная фильтрация воздуха
Фильтровальное оборудование специального назначения
Промышленная фильтрация газов и жидкостей
Фильтры машин и спецтехники
Насосное оборудование
Оборудование для автоматизации
Системы автоматизации специального назначения
Приборы для измерения плотности и показателя преломления
Модули ввода-вывода
Принтеры
Программное обеспечение и кабели
Контроллеры
Аксессуары и комплектующие
Прочее оборудование
Инструментальная техника
Электроинструменты
Бензоинструменты
Ручные инструменты
Промышленное оборудование
Электрооборудование
Смазочное оборудование
Оборудование для судостроения
Оборудование для химического производства
Дорожно-техническое оборудование
Кузнечно-прессовое оборудование
Оборудование для добычи нефти и газа
Оборудование для очистки и переработки
Оборудование для пищевого производства
Оборудование для строительства
Оборудование общего назначения
Оборудование для текстильного производства
Оборудование для физико-механической обработки материалов
Климатическое оборудование
Отопительное оборудование
Оборудование вентиляции и кондиционирования
Испарители
Газовые турбины и двигатели
Турбины
Двигатели
Вакуумная техника
Арматура для вакуумной техники
Расходные материалы для вакуумной техники
Вакуумные насосы
Роторно-платинчатые насосы R5
Кулачковые насосы Mink
Водокольцевые насосы Dolphin LX
Вихревые воздуходувки SAMOS
Вакуумные камеры
Оборудование для сферы услуг
Клеевые машины и оборудование для нанесения клея
Этикетировочное и маркировочное оборудование
Полиграфическое оборудование
Клининговое оборудование
Оптика и фотоника
Базовые элементы перемещений
Поворотные и линейные трансляторы
Рельсы и кронштейны
Оптические столы
Оптические системы
Оптические компоненты и элементы
Оптические держатели
Моторизованные позиционеры
Микрометрические и ультра-точные винты
Лазерные системы
Волоконно-оптические кабели и аксессуары
Базы, крепления оптомеханики
Охрана, защита, пожарная безопасность
Средства защиты информации
Системы охраны и сигнализации
Системы видеонаблюдения
Пожарное оборудование
Защитные конструкции
Аварийно-спасательные средства
Термическое оборудование
Плавильные печи
Шахтные печи
Трубчатые печи
Теплообменное оборудование
Сушильные шкафы
Соляные ванны
Ретортные печи
Печи с циркуляцией воздуха
Печи с выдвижным подом
Печи до 1800 °C
Муфельные печи
Котельное оборудование
Камерные печи
Вакуумные печи
Сантехника, водоснабжение, канализация
Системы водоподготовки
Оборудование дезинфекции и очистки
Электротехника и электроника
Электрощитовое оборудование
Электроустановочные изделия
Генераторы и генераторные установки
Электронные компоненты и аксессуары
Реле
Реле давления
Электромонтажные изделия
Электродвигатели
Трансформаторы и преобразователи
Светотехника
Коммутационно-защитное оборудование
Кабельная продукция и арматура
Источники питания
Заказ оборудованияБесплатная консультация от наших менеджеров
Основной частью конструкции является стальная реторта, с встроенной или внешней системой нагрева. Доступ в реторту осуществляется через фронтальную дверь или откидную крышку. Во время работы печи реторта обеспечивает исключительную герметичность внутреннего объема, доступ к внешнему оборудованию, такому как системы подачи или отвода/утилизации газов, вакуумные насосы, контрольно-измерительное оборудование, осуществляется через вакуумплотные соединения (фланцы).
Базовые модели ретортных печей, подходящие для основных задач термообработки в инертных газах, представлены в нашем каталоге. Дополнительное оснащение для адаптации ретортной печи к технологическому процессу заказчика осуществляется в соответствие с техническим заданием по запросу.
Задачи:
- термообработка в инертной среде до 1100 °С (базовое исполнение)
- термообработка в вакууме до 500-600 °С
- термообработка в горючих газах до 1100 °С
- химико-термическая обработка в газовой среде
- выжигание/удаление связующего
- термообработка в химически агрессивных средах (напр.
пары азотной кислоты)
Использование:
- исследовательские лаборатории
- производство
Конструкция ретортных и муфельных печей
1. Дистилляционная цинковая печь
2. Печь с вертикальной ретортой
3. Барабанная муфельная печь
4. Вращающаяся вакуумная электропечь для восстановления магния ферросилицием
Дистилляционная цинковая печь
Регенеративная трехрядная дистилляционная цинковая печь с горизонтальными шамотными ретортами показана на рис. 228. Печь отапливается генераторным газом, общее число реторт в ней достигает 216 при общей длине печи вместе с регенераторами 21,5 м. Реторты имеют поперечные размеры 0,2×0,3 м и длину 1,8—2,0 м при толщине стенок 25—50 мм. На открытом конце каждой реторты надет шамотный конденсатор для цинка длиной 0,5—0,9 м, газы из которого выходят через металлическую насадку, называемую алонжем и служащую для улавливания цинка в виде пыли. Реторты обогреваются снаружи в результате сжигания генераторного газа, подводимого по одному из верхних парных каналов. Генераторный газ и воздух после подогрева в регенераторах, расположенных на торцах печи, поступают в печь по левой паре каналов. Продукты горения проходят сначала левую часть печи сверху вниз, переходят в правую часть печи, по которой попадают в правую пару каналов, отводящих их в регенераторы. По мере охлаждения насадки регенераторов через каждые 30 мин перекидываются клапаны, регулирующие движение газов, которое начинает происходить уже в обратном направлении, справа налево. Печь работает по периодическому режиму. Вначале все реторты загружают шихтой, состоящей из обожженных цинковых концентратов, угля и оборотов. После загрузки на реторты надевают конденсаторы и алонжи и начинают разогрев печи до 1300—1400° С. Пары цинка конденсируются в конденсаторе, откуда расплавленный цинк вычерпывают ложкой. После удаления из шихты основной части цинка оставшуюся массу, называемую раймовкой, выгребают из реторт, чистят и ремонтируют печь и далее цикл повторяют. Общая продолжительность одного цикла 24 ч.
В каждую реторту загружают до 100 кг шихты, что при 216 ретортах дает суточную производительность печи по шихте около 20 т (5—6 т цинка). Топлива на обогрев реторт и в шихту дистилляции расходуется до 3 т на 1 т полученного цинка.
Аналогичные ретортные печи, но с металлическими ретортами, работающими под вакуумом, с газовым и электрическим наружным обогревом применяют для восстановления окиси магния в металлургии магния.
Описанная ретортная печь имеет следующие существенные недостатки:
- периодичность работы;
- немеханизированные основные операции обслуживания;
- большой расход топлива и огнеупоров;
- низкое прямое извлечение цинка (80—75%).
Печь с вертикальной ретортой
Более совершенная дистилляционная цинковая печь — печь с вертикальной ретортой (рис. 229) для непрерывного ведения процесса. В ней сохранен принцип косвенного обогрева шихты, характерный для дистилляционных печей с горизонтальными ретортами. Поперечное сечение реторты имеет форму вытянутого прямоугольника с ограниченной шириной 300—330 мм и длиной 1600—1800 мм. Реторта имеет высоту около 8 ж и выполнена из карборундовых плит, отличающихся высокой огнеупорностью и теплопроводностью. Торцы реторты можно собирать из шамотных блоков. Шихту в реторту загружают сверху через герметический затвор, а раймовку выпускают снизу через герметическое выпускное отверстие. Печь отапливается генераторным газом, который подводится через горелки, находящиеся в своде камеры. Для создания равномерной температуры воздух для горения вводят в камеру в нескольких точках по высоте. Отходящие газы направляют в рекуператор для подогрева воздуха. Пары цинка отводят в конденсатор, состоящий из двух частей, работающих в различных температурных условиях. В первой части, выполненной в виде канала из карборундовых блоков, пары цинка быстро охлаждаются, чему способствуют высокая теплопроводность карборунда и турбулентное движение газов вокруг перегородок.
Во второй, зумпфовой, части конденсатора скапливается жидкий металл и во избежание образования большого количества пусьеры газы здесь охлаждаются медленно из-за теплоизоляции этой части конденсатора. Выходящие из конденсатора газы очищают в скруббере и далее сжигают в нагревательных камерах печей.
Нормальная работа печей с вертикальными ретортами возможна только на хорошо подготовленной брикетированной шихте. Шихту для брикетирования составляют из цинкового агломерата, коксующегося угля и связующих веществ. Брикеты после изготовления их на прессах коксуют в шахтных печах, и только после коксования горячие брикеты периодически загружают в верхнюю часть реторты.
В верхней части реторты высотой 2—4 м, выложенной из шамотного кирпича, брикеты нагреваются теплом восходящих ретортных газов. В среднюю, обогреваемую снаружи часть реторты брикеты приходят подогретыми до 1000° С и здесь нагреваются до 1270—1300°С. Продолжительность пребывания брикетов в зоне нагрева около 30 ч, что в сочетании с высокой температурой обеспечивает достаточно полное восстановление окиси цинка.
Цинковые пары и газы, поднимаясь вверх, проходят через столб брикетов и поступают в конденсатор, где цинковые пары конденсируются в интервале температур 850—870° С на входе и 530—560° С на выходе. Для облегчения отвода паров цинка из реторты в нижнюю часть ее вводят небольшое количество воздуха или нейтральных газов. Жидкий металл стекает в зумпф конденсатора и по мере накопления выпускается.
Производительность вертикальной реторты по цинку составляет 3—5 т/сутки. Извлечение металла выше, чем в горизонтальных ретортах, и достигает 90% и более. Кампания вертикальных реторт длится от 3 до 5 лет.
Барабанная муфельная печь
Муфельные печи могут быть барабанные вращающиеся.
На рис. 230 показана вращающаяся барабанная муфельная печь 2,2×14 м, изготовляемая Уральским заводом химического машиностроения. Печь состоит из стального барабана диаметром 2,2 м, футерованного шамотным кирпичом. Внутри этого барабана устроен стальной цилиндрический муфель диаметром 1,4 м и длиной 14,5 м, изготовленный из стали Х23Н18. Этот муфель удерживается внутри барабана на специальных опорах с пружинными амортизаторами и вращается вместе с барабаном печи. Муфель обогревается снаружи дымовыми газами, двигающимися в кольцевом промежутке между наружной поверхностью муфеля и футеровкой барабана.
Максимальная температура газов на входе в печь 950° С, на выходе 350° С. Температура реакционных газов на выходе из муфеля до 600° С. Барабан печи приводится во вращение электромотором 8,5—18 квт при числе оборотов барабана от 0,6 до 2 об/мин. Дымовые газы для обогрева получаются в специальной выносной топке, на рисунке не показанной. Печь можно применять для прокалки, обжига, восстановления различных сыпучих материалов в регулируемой газовой атмосфере.
На рис. 231 приведена вращающаяся муфельная электропечь, применяющаяся для восстановления металлических порошков, а также для обработки различных материалов газами. Печь состоит из металлического вращающегося барабана диаметром 0,46 м и длиной 2,3 м, изготовленного из специального жароупорного сплава. Внутренняя полость барабана для лучшего перегребания материала оборудована лопастями. Барабан нагревается снаружи силитовыми или нихромовыми нагревателями, включенными в электросеть. Обрабатываемый материал в смеси с восстановителем загружают в печь через бункер с помощью уплотненного шнекового питателя. Выгрузка производится также шнековым питателем, служащим одновременно и холодильником. Восстанавливающие или защитные газы — водород, окись углерода и азот — подают в холодильник и в разгрузочную камеру. Печь имеет мощность 60 ква и рабочее напряжение 50—225 в. Нагревательные элементы — 16 силитовых стержней размером 0,025×0,81×1,37 м. Производительность печи по перерабатываемым материалам 1—3 т/сутки. Максимальная рабочая температура 1200° С.
Вращающаяся вакуумная электропечь для восстановления магния ферросилицием
На рис. 232 показана вращающаяся вакуумная электропечь для восстановления магния ферросилицием. Реторта печи имеет цилиндрическую форму и расположена на роликах, позволяющих непрерывно вращать ее для перемешивания шихты.
Реторта состоит из двух сообщающихся частей: реакционной камеры, футерованной кирпичом, и конденсатора из жаропрочной стали. Шихта в реакционной камере нагревается угольными стержнями, расположенными по оси печи и включенными в электрическую сеть. Печь работает периодически по следующему режиму. Реакционную камеру заполняют брикетированной шихтой ниже нагревателей через специальное загрузочное отверстие 7. После уплотнения камеры и конденсатора включают электронагреватели, и печь начинает вращаться, температура в рабочей камере поднимается до 1400—1500° С. Вследствие вращения печи вся шихта равномерно прогревается в течение 4—5 ч. Конденсатор и камера во время работы находятся под глубоким вакуумом, и давление в камере составляет 1—3 мм рт. ст. Пары магния собирают в конденсаторе, где охлаждаются. Полученный металлический магний выплавляют в специальной электропечи. Остатки шихты из реакционной камеры выгружают через то же отверстие, печь снова загружают свежей шихтой и начинают следующую операцию. Печь вмещает одновременно до 2 т шихты и имеет мощность 500 ква. Время обработки одной загрузки 6 ч, что обеспечивает производительность печи по магнию 1 т/сутки. Расход электроэнергии на восстановление и дистилляцию магния составляет 12—14 квт-ч/кг Mg.
Общий расход энергии, включая все побочные операции, 20 квт-ч/кг. Возможно увеличение производительности печей этого типа по магнию до 3 т/сутки.
Что такое Вращающаяся ретортная печь, определение термина в Металлы и сплавы. Справочник
Все словариБольшой юридический словарьОднотомный большой юридический словарьСправочник лекарственных средствЭнциклопедия БиологияФинансовый словарьЭкономический словарьБольшой бухгалтерский словарьМедицинский словарьМорской словарьСоциологический словарьСексологический словарьАстрономический словарьБизнес словарьПолитический словарьСловарь литературных терминовМедицинский большой словарьЭнциклопедический словарьСловарь ЕфремовойЭнциклопедия КольераЭнциклопедия Брокгауза и ЕфронаТолковый словарь УшаковаСловарь ОжеговаСловарь ДаляСловарь наркотического сленгаСловарь воровского жаргонаСловарь молодёжного слэнгаСловарь компьютерного жаргонаМеталлы и сплавы. СправочникТолковый строительно-архитектурный словарьАрхитектурный словарьДжинсовый словарьСловарь по ландшафтному дизайнуАвтомобильный словарьКулинарный словарьСтроительный словарьПолиграфический словарьСловарь модыYoga Vedanta DictionaryСловарь йогиСловарь терминов Йоги и ведантыСозвездия, латинские названияСловарь музыкальных терминовБиографический словарьСловарь эпитетовСловарь курортовСловарь русских технических сокращенийЭтимологический словарь ФасмераСловарь иностранных словСловарь фразеологизмовСловарь географических названийСловарь символовСловарь синонимовСловарь нумизматаСловарь имёнСловарь мерСловарь русских фамилийЭтнографический словарьСловарь лекарственных растенийСловарь народовИсторический словарьРелигиозный словарьСловарь по мифологииБиблейская энциклопедияСловарь по искусствуФилософский словарьСловарь логикиПсихологический словарьВсё о вине, энциклопедический словарьКнига о вкусной и здоровой пищеКулинарный словарьПищевые добавкиСловарь алкогольных напитковЭнциклопедия трезвого образа жизни
-
- Вращающаяся ретортная печь
- Rotary retort furnace — Вращающаяся ретортная печь.
Печь непрерывного действия, работа которой обеспечивается внутренней спиралью, позволяющей осуществить хороший контроль за сохранением температуры в пределах нагретой камеры.
(Источник: «Металлы и сплавы. Справочник.» Под редакцией Ю.П. Солнцева; НПО «Профессионал», НПО «Мир и семья»; Санкт-Петербург, 2003 г.)
.
Ivanov Alex
Выберите букву
А Б В Г Д Е Ж З И К Л М Н О П Р С Т У Ф Х Ц Ч Ш Щ Э
Популярные слова
Капля Биллет (заготовка для выдавливания) Сольвус Газовый карман Валик Лужение Бронза Радиограф Доэвтектический сплав Заэвтектический сплав Отпуск Допрессовка Площадка текучести Баббит Сложные напряжения Двойник Бейлби слой Нагар Молот Стан Стекеля
Инновационная вращающаяся ретортная печь, рассчитанная на долгий срок службы
Когда вы хотите что-то купить в жизни, вы всегда чувствуете себя более комфортно, когда обращаетесь к экспертам. Как производитель промышленных печей, компания Surface Combustion имеет более чем 100-летний опыт работы с системами печей для термической обработки и термообработки. Один из таких специализированных типов оборудования предназначен для очень маленьких заготовок, таких как штифты, звенья цепи или крепежные детали, которые необходимо закалить, закалить и/или отпустить. Тип печи представляет собой вращающуюся реторту, которая представляет собой горизонтально ориентированный барабан с внутренними лопастями, которые при вращении переворачиваются и переносят нагрузку с одного конца на другой. Такое переворачивание обеспечивает равномерный нагрев и распределение технологического газа для очень небольших и плотно упакованных рабочих нагрузок.
Поверхность ® Вращающаяся (также известная как револьверная) реторта сгорания начинается с реторты или барабана из высококачественного сплава, отлитого методом центробежного литья. Барабан устанавливается в изолированную камеру с электрическим или газовым обогревом. Внутри реторты при закалке обычно используется эндотермическая атмосфера. Барабан приводится в движение электрически через цепь или зубчатую рейку. Пакетные стили будут передавать нагрузку (опрокидывание) внутри реторты, двигаясь вперед, а затем в обратном направлении. Груз входит и выходит через одно и то же отверстие. Непрерывные стили входят и выходят через противоположные концы. На выходе для процесса закалки добавляют масло, полимер или воду. Для отпуска закалка не требуется. Можно также проводить традиционное науглероживание. Форсированное диффузионное науглероживание, когда необходимо разделение зон для различных температур стадий процесса или углеродных потенциалов, является проблематичным для вращающейся ретортной печи этого типа. Реторты наших вращающихся ретортных печей могут иметь длину от 2 до 3 футов и длину до 40 футов. Также доступны диаметры до 6 футов. Диапазон рабочих температур, как правило, составляет от 1400°F до 2400°F, так как это теплопроводный способ передачи тепла к нагрузке.
Изоляция, используемая в горячей зоне, может быть кирпичной или волокнистой. Нагревательные элементы традиционно представляют собой изогнутые стержни, которые электрически изолированы от стального корпуса. Модель с газовым нагревом может быть с косвенным нагревом излучающей трубы или горелками с прямым нагревом. В первом случае кольцевое пространство между горячей зоной и внешней поверхностью реторты может продуваться постоянным потоком азота.
Закалка представляет собой капельную закалку, означающую, что небольшое количество деталей сбрасывается в закалку за один раз. Отделение масла от атмосферы печи осуществляется через масляные каскады, которые создают своего рода стену. Типичное перемешивание в этом стиле закалки осуществляется с помощью насосов и форсунок, направленных на поверхность ленты, которая собирает свободно падающие части и поднимает их на поверхность, где они могут быть переданы в систему промывки перед темперированием. Масло можно нагревать с помощью электрических нагревательных элементов байонетного типа, а также охлаждать после закалки, чтобы вернуть температуру масла к заданному значению.
- Особенности
- Процессы
- Промышленность
- Материал/Компонент
- Сопутствующее оборудование
Установки поставляются с одинарными и двойными ретортами футов
Нормальная нагрузка (в зависимости от максимальной рабочей температуры) может достигать насыпной плотности 300 фунтов/фут³
Устройства рассчитаны на максимальную рабочую температуру 1950°F
Gas-fired and electrically heated units available
Batch and continuous designs available
Wide range of available companion equipment to meet your needs
Annealing
Austempering
Carbonitriding
Carburizing
Hardening
Marquenching
Temper
Показан частичный список процессов. Ищете что-то конкретное, свяжитесь с нами.
Автомобильная промышленность
Подшипники
Коммерческая термообработка
Крепеж
Государственный поставщик печей
Внедорожник/горнодобывающая промышленность/Раскопки
Боеприпасы
Спортивные товары
Показан неполный список отраслей. Ищете что-то конкретное, свяжитесь с нами.
Подшипники
Чугун
Цепь
Крепежи
Нержавеющая сталь
Штамповки
Сталь
Стальная дробь
9000 Неполный перечень материалов и компонентов. Ищете что-то конкретное, свяжитесь с нами.Показан неполный список вспомогательного оборудования. Ищете что-то конкретное, свяжитесь с нами.
СВЯЖИТЕСЬ С НАМИ СЕГОДНЯ, и позвольте нам показать вам Ценность Surface™- Новые клиенты
- Существующие клиенты
y 901 Приступить к работе?
Пожалуйста, позвоните нам, когда вы будете готовы обсудить новую печь или обслуживание, модернизацию или замену вашей печи или любой ее части. В Surface мы с нетерпением ждем возможности помочь вам с любыми потребностями в термической обработке.
Call Surface со следующей информацией, готовой инициировать решение вашей печи.
- Цикл
- Операция
- часов в год
- Доступное пространство
- Диапазон рабочих температур
- Тепловой источник
Позвоните нам на звонок
(800) 537-8980100100
99999999. Необходимость.
Пожалуйста, позвоните нам, когда вы будете готовы обсудить новую печь или обслуживание, модернизацию или замену вашей печи или любой ее части. В Surface мы будем рады помочь вам с любыми потребностями в термической обработке.
В разделе «Запчасти и обслуживание» по возможности укажите одну или несколько следующих сведений о вашей печи:
- Серийный номер
- Номер чертежа
- Фотографии вашей печи или деталей для замены
- Список запасных частей
- История восстановления печи
Позвоните нам
(800) 537-8980
Вакуумные ретортные печи с горячими стенками
Вакуумные печи могут быть как с горячей стенкой (рис. 1), так и с холодной стенкой (рис. 2). Между ними есть заметные различия, и каждый из них имеет свои преимущества и ограничения. В этой и следующей статьях мы рассмотрим эти различия и опишем, какие приложения лучше всего подходят для каждого из них.
Конструкции с горячей стенкой
В начале истории вакуумных печей были доступны только конструкции с горячими стенками. В этих печах, как и в современных, используется реторта (также известная как муфель), в которую помещается загрузка. Затем реторта запечатывается. Насос вакуумирует реторту, и процесс проходит либо под вакуумом, либо при определенном (отрицательном или положительном) давлении после достижения начального уровня вакуума.
Преимущества использования реторты заключаются в том, что печь, окружающая реторту, может работать на газе или электричестве, а реторта может быть быстро откачана. Конструкции с горячими стенками, как правило, дешевле в производстве, чем их аналоги с холодными стенками. Кроме того, поскольку объем внутри реторты относительно невелик, насосы меньше, и для достижения необходимого уровня вакуума для процесса требуется меньше времени, чем в печи с холодными стенками сопоставимого размера (рис. 3).
Примечания:
- Синяя заштрихованная область представляет собой объем, который необходимо откачать.
- На рисунке слева показана прямоугольная горячая зона. Цилиндрические конструкции сегодня более распространены.
В конструкциях с горячими стенками источник нагрева расположен вне реторты, но внутри самой печи. Напротив, в конструкциях с холодными стенками источник нагрева находится в горячей зоне печи (рис. 4). Определяющей характеристикой конструкции с горячей стенкой и ее основным ограничением является необходимость использования реторты.
При нормальной работе внутри реторты перед нагревом создается вакуум. После достижения заданного уровня вакуума процесс может продолжаться в вакууме или при парциальном или избыточном давлении, если вводится инертный (или горючий) газ. Вентиляторы часто поставляются внутри реторты для обеспечения циркуляции атмосферы. Чтобы нагреть загрузку, нагреватели должны сначала нагревать реторту снаружи, а затем реторта передает или излучает тепло к загрузке внутри.
Если реторта подвергается атмосферному давлению снаружи и определенному уровню вакуума внутри, конструкция реторты должна быть такой, чтобы предотвратить разрушение реторты. Поскольку все материалы в той или иной степени подвержены снижению прочности при повышенной температуре (рис. 5) и усталости после многократного циклирования, материалы конструкции и конструкция реторты должны учитывать эти факторы. Таким образом, блоки с горячими стенками по своей природе имеют более низкую максимальную рабочую температуру, чем конструкции с холодными стенками. Конструкции с горячими стенками обычно ограничиваются максимальной температурой 1100°C (2000°F). Кроме того, реторты также могут быть изготовлены из керамики или кварца, которые имеют более высокие максимальные температуры, но могут быть подвержены тепловому удару при нагревании и охлаждении. Преимущество этих материалов в том, что они меньше загрязняют технологический вакуум, и используются в основном в приложениях с высокой степенью чистоты, например, в полупроводниковой промышленности.
Конструкция реторты может быть D-образной, цилиндрической или прямоугольной. Реторты также часто гофрируют для придания дополнительной прочности. Поскольку атмосферное давление немного выше 10 000 кг/м2 (14,7 фунтов/дюйм2), реторта под вакуумом испытывает силу в десятки тысяч килограммов, пытаясь ее разрушить. Эту сжимающую силу можно продемонстрировать, откачав воздух из барабана или стального резервуара и отметив, как внезапно и резко резервуар разрушается (рис. 6). В результате все реторты должны быть соответствующим образом усилены.
Принудительное охлаждение в вакуумных печах с горячими стенками
Ретортные вакуумные печи с горячими стенками часто нуждаются в принудительном охлаждении для достижения приемлемого времени технологического цикла . Это можно сделать, либо вынув реторту из печи, либо циркулируя охлаждающий воздух вокруг реторты снаружи.
Другой метод охлаждения включает удлиненную реторту (рис. 7). Реторта удлиняется так, что выходит за пределы нагревательной камеры, а внешняя часть обернута водяной рубашкой для охлаждения. Подвижная решетка, несущая загрузку, перемещается в печь и из нее с помощью толкателя, проходящего через уплотнение в конце реторты. По окончании нагрева решетка, удерживающая лоток с деталями, вытягивается из нагретой части реторты и помещается в водоохлаждаемую часть реторты. Груз все время находится под вакуумом.
Другой способ охлаждения загрузки в вакуумных печах с горячими стенками заключается в нагнетании окружающего воздуха в печь снаружи реторты (рис. 8). Показанная печь предназначена для создания вакуума с последующей засыпкой инертным газом.
Рисунок 8 | Схематический трехмерный вид печи с горячими стенками 6На этом изометрическом разрезе показаны следующие элементы печи:
- Реторта (поз. 1)
- Нагревательные элементы (поз. 2)
- Изоляция печи (поз. 3)
- Система управления газом (поз. 4)
- Вакуумный насос (поз. 5)
- Охлаждающий вентилятор (поз.
6)
- Выходной тракт охлаждающего воздуха (поз. 7).
- Газоотвод (поз. 8)
- Вентилятор циркуляции газов для циркуляции инертной атмосферы после засыпки (поз. 9)
- Нагрузка (поз. 10)
- Бак аварийной продувки (поз. 11)
Технологические приложения
Вакуумные печи с горячими стенками используются для различных процессов, включая отпуск, пайку, нанесение покрытия, отверждение, удаление примесей и цементацию (азотирование, нитроцементация, сульфонитридирование).
Каталожные номера
- Kanthal (www.kanthal.com)
- Справочник по термической обработке стали, Джордж Э. Тоттен и Морис А. Х. Хоуз (редакторы), Marcel Dekker, Inc., 1997.
- Разработка сплавов (www.alloyengineering.com)
- Национальная корпорация Вабаш (www.wabashnational.com)
- Вакуумная технология: практическая термообработка и пайка, Роджер Фабиан (ред.), ASM International, 1993.
- Набертерм (www.nabertherm.com)
- Directindustry.com
Системы вращающихся ретортных печей — SECO/WARWICK
Вращающиеся ретортные печи SECO/WARWICK специально разработаны для непрерывного производства и равномерной термообработки мелких деталей, таких как монеты, мелкие скобяные изделия, гвозди, подшипники, компоненты цепей и крепежные детали, такие как гайки, болты и винты.
Вращающаяся ретортная печь предназначена для повышения производительности и поддержания стабильных характеристик термообработки и закалки, необходимых для высокопроизводительных мелких деталей, таких как подшипники и крепежные детали. Он обеспечивает гибкость процесса, которую можно использовать для производственных сред с одним или несколькими приложениями, а также небольшими или большими партиями. Клиенты SECO/WARWICK выбирают системы с вращающимися ретортами, чтобы сэкономить время и деньги на техническое обслуживание и эксплуатационные расходы при оценке общей стоимости владения по сравнению с традиционными системами с сетчатым ремнем или системами периодического действия.
- Обзор
- Особенности
- Преимущества
- Процессы
- Материалы
Вращающиеся ретортные печи используются для обработки исключительно широкого спектра мелких деталей, включая винты, гайки, болты, гвозди, шайбы и монеты. Вращающаяся ретортная печь особенно подходит для операций закалки в контролируемой атмосфере, нитроцементации и науглероживания в диапазоне температур от 1550 до 1750°F (от 840 до 955°C).
Whirl-A-Way Quench™
Закалка Whirl-A-Way представляет собой систему быстрой однородной закалки, обеспечивающую большую глубину гильзы. Закалка Whirl-A-Way предназначена для обеспечения превосходных результатов закалки деталей из черных и цветных металлов после того, как они достигнут температуры в печи. Детали выгружаются в охлаждающую среду через несколько секунд после достижения температуры и переносятся на вращающийся разгрузочный конвейер движением охлаждающей жидкости. Это движение позволяет мгновенно стереть пароизоляцию каждой детали, что приводит к превосходным характеристикам закалки. При входе в закалочный барабан детали транспортируются к месту разгрузки вращательным движением скребков барабана. Закалочной жидкостью может быть масло, вода или синтетическая среда. Запатентованная система Whirl-A-Way предназначена для предотвращения загрязнения атмосферы в печи. Система способна работать с широким спектром конфигураций деталей, постоянно поддерживая индивидуальные результаты закалки, обеспечивая как большую глубину корпуса, так и однородность
/ Заводская сборка — Все оборудование полностью собрано на заводе, подключено к трубопроводу, подключено и механически протестировано перед отправкой, чтобы свести к минимуму время и затраты на установку. Обеспечено быстрое подключение к инженерным сетям.
/ Бункер/загрузчик – Бункер/загрузчик предназначен для загрузки в печь заданного количества деталей при каждом обороте реторты. Детали, хранящиеся в бункере, автоматически передаются в загрузочный ковш по прибытии его в нижнее положение элеватора. Затем загруженная корзина поднимается, и детали автоматически помещаются в печь.
/ Стандартное оборудование — . Линии печей имеют стандартные размеры и номинальную мощность от 500 фунтов (225 кг) до 1000 фунтов (450 кг). Они могут быть изготовлены, доставлены и установлены быстро. Были предоставлены специально спроектированные системы с производительностью до 4000 фунтов (1800 кг) в час.
/ Electric Design – конструкция с электрическим нагревом оснащена байонетными нагревательными элементами, которые можно легко заменить снаружи печи.
/ Газовая конструкция – Конструкция с газовым обогревом оснащена радиационными трубами из центробежнолитого сплава и полной системой сгорания
.
/ Реторта — Консольная цельная литая реторта поддерживается на одном конце и герметизируется на входном конце печи. В горячих зонах или на нагнетательном конце отсутствуют уплотнения или подшипники.
/ Вращающийся механизм – Скребки шнека плавно и бесшумно перемещают детали через печь. Вращение реторты имеет широкий диапазон регулировки скорости для обеспечения полной гибкости временных циклов обработки.
/ Атмосферонепроницаемый – Реторта опирается на герметичный подшипник, а закалочная камера крепится фланцем к печи. Только малая загрузочная дверца открывается на мгновение при каждом обороте реторты.
/ Низкие эксплуатационные расходы — Корзины и лотки не требуются. Реторта является единственной движущейся частью, подвергающейся нагреву.
/ Автоматизация — Термическая обработка выполняется полностью автоматически после загрузки деталей.
/ Без котлованов – система не требует котлованов или специальных фундаментов; он предназначен для установки на уровне пола.
/ Superior Material Handling – Транспортировка внутренних лопастей через реторту печи и транспортировка жидкости без механизма через закалочную ванну сводит к минимуму потери, перепутывание или повреждение деталей.
/ Нитроцементация,
/ Закалка,
/ Науглероживание.
/ Винты,
/ Гайки,
/ Болты,
/ Гвозди,
/ Шайбы и монеты.
Патент США на вращающуюся ретортную печь. Патент (Патент № 4,648,836, выдан 10 марта 1987 г.) печь для непрерывной термической обработки заготовок, включающая в себя ретортный узел, образованный цилиндрическим осевым элементом и спирально навитым трубопроводом, расположенным на внешней поверхности осевого элемента для перемещения заготовки от одного конца ретортного узла к другому концу.
Вращающиеся ретортные печи использовались в течение многих лет для непрерывной обработки различных мелких металлических заготовок или деталей, таких как болты, гайки, винты, заклепки, штифты, шарики, пружины, зажимы, шпильки, гвозди, шайбы и т. как. В этих печах предшествующего уровня техники реторты используются для непрерывной обработки небольших пакетов таких деталей и транспортировки их от одного конца реторты к другому концу, когда она вращается в окружающей нагревательной камере. Такие предшествующие реторты, как правило, имеют цилиндрическую форму и обычно представляют собой толстостенные литые реторты с грубыми стенками и внутренними литыми спиралями (скребками) или реторты, изготовленные из деформируемых материалов с внутренней спиралью, приваренной непосредственно к цилиндрической оболочке. Реторты, изготовленные из кованых материалов, имеют ряд присущих им проблем. Одна из проблем заключается в том, что изготовление внутренних скребков очень дорого из-за высоких требований к допускам при размещении и креплении внутренних скребков в тесном контакте с боковыми стенками реторты. В противном случае обработанные детали будут иметь тенденцию застревать между пролетом и боковинами. Если такие детали, подлежащие обработке за одну операцию, застревают в промежутках между пролетами и боковыми стенками реторты и впоследствии попадают или смешиваются с другими комплектами термообрабатываемых деталей, это может оказаться весьма обременительной и дорогостоящей задачей. для сортировки частей.
Смешение частей недопустимо. Если время выдержки регулируется очень точно, то смешивание частей либо продлит, либо уменьшит время выдержки. Другая проблема изготовленных реторт из кованых материалов заключается в том, что прочность используемых материалов не может легко выдерживать циклические физические и термические нагрузки, которые могут быть присущи вращающимся печам при высоких температурах.
Несмотря на то, что литые реторты намного лучше справляются с высокотемпературными нагрузками, они не лишены проблем. Например, поскольку стенка литых реторт намного толще, чем в кованых ретортах, требуется гораздо более высокая тепловая среда для компенсации температурного градиента в стенке реторты для достижения тех же внутренних температур. Кроме того, из-за процесса литья внутренние поверхности значительно шероховатее, чем у кованых реторт, что приведет к накоплению клинкера (режущей стружки и смазочно-охлаждающих масел), ограничивая прохождение деталей и вызывая снижение скорости теплообмена и возможное повреждение. сами части.
Поскольку вращающиеся ретортные печи часто используются с контролируемой атмосферой для создания нейтральных (не окисляющих) условий или для создания термохимической комбинации, необходимой для термической обработки деталей, важно свести к минимуму количество газа или газов, используемых в печи. печь. В предшествующих конструкциях вращающихся печей непрерывного действия значительные объемы газа используются из-за конфигурации реторты и расположения небольших пакетов деталей таким образом, чтобы гарантировать, что достаточное количество регулируемой атмосферы подается на все части и в течение достаточного времени. предоставляется для получения желаемого лечения. Однако объем используемых газов относительно высок, что увеличивает эксплуатационные расходы.
Другая проблема, связанная с этими вращающимися печами предшествующего уровня техники, заключается в термических напряжениях, возникающих во внутренней камере и корпусе реторты из-за того, что заготовки поступают в печи в чрезвычайно холодном состоянии по отношению к температуре печи. Степень напряжения зависит от величины перепада температур. Эта разница температур может быть весьма существенной, поскольку тепловложения, подводимые к входу в печь, очень велики. В результате наличие этого и других типичных условий может привести к преждевременному выходу из строя реторты из-за растрескивания, возникающего вблизи пересечения скребков и корпуса, что требует дорогостоящей замены или ремонта скребка и/или корпуса реторты. Еще одним недостатком, который до сих пор традиционно встречался в этих ретортных печах, является то, что тепло, передаваемое частям, ограничивалось главным образом излучением с некоторой передачей тепла за счет теплопроводности частям, прилегающим к боковым стенкам реторты.
СУЩНОСТЬ ИЗОБРЕТЕНИЯ
Соответственно, общей целью настоящего изобретения является создание усовершенствованной вращающейся ретортной печи, имеющей ретортный узел, образованный осевым элементом и спирально навитым трубопроводом, расположенным на внешней поверхности осевого элемента. элемент, который относительно прост и экономичен в изготовлении и сборке, но при этом преодолевает недостатки ретортных печей предшествующего уровня техники.
Целью настоящего изобретения является создание вращающейся ретортной печи, которая включает в себя цилиндрический вращающийся осевой элемент и спирально закрученный трубопровод, расположенный на внешней поверхности осевого элемента для перемещения заготовок с одного конца осевого элемента на другой. конец.
Еще одной целью настоящего изобретения является создание вращающейся ретортной печи, имеющей ретортный узел, который включает в себя спирально закрученный трубопровод, образованный множеством полых спиральных вращающихся секций для постепенной транспортировки деталей, подлежащих нагреву, через печь.
Еще одной целью настоящего изобретения является создание вращающейся ретортной печи, которая включает в себя ретортный узел и загрузочно-разгрузочное устройство для транспортировки деталей, подлежащих термообработке, в спиральный канал ретортного узла.
В соответствии с этими целями и задачами настоящее изобретение касается создания непрерывной вращающейся ретортной печи, которая включает в себя внешний кожух, имеющий первый и второй концы. Узел реторты проходит через отверстия в первом и втором концах. Узел реторты поддерживается опорными элементами на обоих концах снаружи кожуха. Узел реторты образован осевым элементом и спирально навитым трубопроводом, расположенным на внешней поверхности осевого элемента. Узел привода соединен с опорным устройством рядом с первым концом для вращения узла реторты.
КРАТКОЕ ОПИСАНИЕ ЧЕРТЕЖЕЙ
Эти и другие цели и другие преимущества настоящего изобретения станут более очевидными из подробного описания при чтении вместе с прилагаемыми чертежами с одинаковыми ссылочными позициями, обозначающими соответствующие части, на которых:
РИС. 1 представляет собой вид сверху вращающейся ретортной печи, построенной в соответствии с принципами настоящего изобретения;
РИС. 2 — вид сбоку печи по линиям 2-2 на фиг. 1;
РИС. 3 — вид с торца загрузочного конца печи по линиям 3-3 на фиг. 2;
РИС. 4 представляет собой вид сбоку, частично в разрезе, для иллюстрации узла реторты по настоящему изобретению;
РИС. 5 представляет собой вид печи в разрезе по линиям 5-5 на фиг. 4;
РИС. 6 представляет собой вид сбоку, показывающий детали узла загрузки-разгрузки для использования с узлом реторты по настоящему изобретению; и
РИС. 7 показано альтернативное расположение для загрузки и выгрузки деталей в спирально закрученный трубопровод.
ОПИСАНИЕ ПРЕДПОЧТИТЕЛЬНЫХ ВАРИАНТОВ ВОПЛОЩЕНИЯ
Обращаясь теперь к различным видам чертежей, на фиг. 1, 2 и 4 показана вращающаяся ретортная печь непрерывного действия согласно настоящему изобретению, которая в целом обозначена ссылочной позицией 10. Печь имеет удлиненный внешний кожух 12, облицованный втягивающим материалом 14, и снабжен центральной полостью 16. Кожух 12 печи состоит из пола 17, боковых стенок 18 и 20, торцевых стенок 22 и 24 и крыши или капота 26, которые предпочтительно являются съемными для облегчения доступа для любого необходимого технического обслуживания внутри оболочки. В крыше 26 расположено множество выпускных отверстий 28, обеспечивающих выход газов, используемых во время работы печи.
Печь 10 включает узел вращающейся реторты 29, состоящий из цилиндрического вращающегося осевого элемента 30 и спирально навитого канала 32, расположенного на внешней поверхности осевого элемента 30. Осевой элемент проходит в продольном направлении через отверстия 34, 36 в соответствующих в стенах 22, 24 и поддерживается снаружи на обоих своих концах подшипниками с возможностью вращения вокруг оси осевого элемента 30. Оболочка 12 поддерживается над землей с помощью конструкционной металлической рамы в сборе 38. Рама в сборе 38 также обеспечивает опора для привода в сборе 39для узла реторты, включающего в себя гидравлический двигатель 40. Подшипник 42 на приводном конце 44 осевого элемента 30 жестко прикреплен к нему для поддержки осевого элемента в фиксированном положении. Подшипник 46 на выпускном конце 48 осевого элемента 30 опирается на колонный элемент 50. Подшипник 46 допускает тепловое расширение осевого элемента. Во время работы печи как осевой элемент 30, так и спирально закрученный трубопровод 32 будут увеличиваться из-за теплового расширения. Рост спирально намотанного канала 32 обычно происходит в радиальном направлении, а рост осевого элемента 30 обычно происходит в продольном направлении. Из-за спиральной конфигурации ретортного узла термические напряжения, которые обычно возникают, не возникают из-за пружинящего действия трубопровода.
Приводной узел 39 включает в себя приводную цепь 52, приводимую в движение двигателем 40 через редуктор 54, который входит в зацепление с ведущей звездочкой 56. Ведущая звездочка 56 установлена на валу 58 зубчатого механизма 54 и соединена посредством приводную цепь 52 к ведомой звездочке 60, жестко закрепленной на внешнем конце аксиального элемента 30. Средства привода реторты 29, конечно, могут быть различными, например, с помощью электродвигателя с фиксированной скоростью или реверсивного электродвигателя с регулируемой скоростью. мотор по желанию. Проиллюстрированный гидравлический двигатель 40 и редукторный механизм 54 предоставлены просто как пример одной практической формы силового привода.
Как лучше всего видно на ФИГ. 4 и 5, нижняя часть реторты 29 всегда погружена в источник 62 нагрева жидкости. Источник 62 нагрева жидкости может состоять либо из среды с псевдоожиженным слоем, либо из ванны с расплавленной солью, либо из ванны с расплавленным свинцом. В предпочтительном варианте осуществления настоящего изобретения предпочтительно использовать псевдоожижающую среду. Среда псевдоожиженного слоя может быть нагрета путем погружения или путем нагревания снаружи реторты, которая может быть газовой или электрической, например, с помощью электрических нагревательных элементов 64.
Поскольку детали (пакеты шихты) 66, подлежащие термической обработке, поступающие в печь, будут попадать в первый виток спирального трубопровода 32, который все время погружен в псевдоожиженный слой, детали 66 подвергаются воздействию высокотемпературного источника в исходное состояние, чтобы обеспечить высокую скорость теплопередачи. Эта повторная теплопередача обусловлена еще и тем, что детали полностью окружены источником нагрева и находятся чрезвычайно близко по всем своим поверхностям к источнику нагрева. Таким образом, детали можно быстро нагреть до соответствующей температуры. Кроме того, из-за того, что спирально закрученный трубопровод 32 погружен в псевдоожиженный слой с постоянной температурой по всей его длине, будет меньше перепад температур и, таким образом, будут уменьшены напряжения. Кипящий слой также обеспечивает эффект плавучести, который способствует поддержанию реторты в сборе 29.по всей длине, что продлевает срок службы.
Обычно требуется контролируемая атмосфера вокруг зарядного пакета 66 во время термохимической обработки во всех случаях и во время термической обработки в большинстве случаев. В случае термической обработки обычно желательно иметь нейтральную атмосферу, такую как азот или специальную смесь экзотермического газа или эндотермического газа. В случае термохимической обработки контролируемой атмосферой будут смеси азота, аммиака, природного газа или богатые смеси экзотермического газа или эндотермического газа. В любом случае регулируемая атмосфера для термообработки вводится рядом с приводным концом 44 в осевой элемент 30 под давлением через впускное отверстие 68. Затем такие газы подаются в ретортный блок 29.где газы проходят через спирально закрученный трубопровод 32 и выходят на выпускном конце 48 осевого элемента.
Как указывалось ранее, ретортный узел 29 состоит из цилиндрического вращающегося осевого элемента 30 и спирально-навитого трубопровода 32. Осевой элемент 30 изготавливается предпочтительно из жаропрочной высоколегированной стали, которая изготавливается либо литьем, либо изготовлением . Спирально закрученный трубопровод 32 включает в себя множество полых спиральных вращающихся секций 32а для постепенной транспортировки загрузочных пакетов или частей 66, подлежащих термообработке, через вращающийся узел 29 реторты.. Один конец спирального трубопровода 32 соединен с осевым элементом 30 через загрузочный желоб 32b, а конец трубопровода соединен с осевым элементом через разгрузочный желоб 32с. Хотя полые секции 32а проиллюстрированы круглыми по площади поперечного сечения, следует четко понимать, что площадь поперечного сечения полых секций может иметь любую требуемую конфигурацию, например квадратную, овальную, прямоугольную или многоугольную.
Конкретная конфигурация может быть разработана на основе отношения объема (массы) пакета заряда, подлежащего термообработке, к площади открытой поверхности спирального канала 32, чтобы максимизировать теплопередачу. Проиллюстрированная конкретная спиральная конфигурация упоминается как конфигурация с одним каналом и одним проходом. Также предполагается, что может быть использовано любое количество других устройств, таких как одинарный трубопровод с двойным и/или тройным проходом или двойной или тройной трубопровод с одним проходом. Кроме того, для простоты иллюстрации изображено только выбранное число оборотов спирального трубопровода 32; однако должно быть очевидно, что число оборотов в типичной ретортной печи может быть всего от половины оборота до любого желаемого максимума в зависимости от физических ограничений используемого материала. Расчетные критерии числа оборотов также будут основываться на объемной плотности деталей, подлежащих термической обработке, продолжительности времени, в течение которого детали должны находиться в печи, и производительности (вес на часовую производительность), требуемой от печь.
Таким образом, ретортный узел 29 по настоящему изобретению имеет преимущества обеспечения относительно быстрого нагрева деталей на начальном входе и тесного контакта контролируемой атмосферы с деталями. Поскольку площадь, в которой должны проходить контролируемые газы, проходит через все детали, подлежащие термообработке, объем используемых газов будет равен площади трубопровода 32, а не площади реторты в обычных печах. Кроме того, реторта в сборе имеет меньшую длину, чем реторта в обычных вращающихся ретортных печах, что значительно снижает затраты на производство и техническое обслуживание. Поскольку детали, подлежащие термообработке, проходят в виде ряда зарядных пакетов 66, которые все содержатся внутри спирального трубопровода 32 без какого-либо другого соединительного прохода, проблема предшествующего уровня техники, связанная с пересечением деталей в соседних зонах прохода, вызывающая их смешивание, была полностью устранена. Кроме того, благодаря тому факту, что спиральный канал 32 опирается на внешнюю поверхность осевого элемента 30, канал 32 может быть изготовлен с очень тонкой конструкцией, тем самым уменьшая количество подводимого тепла и тем самым уменьшая термические напряжения.
Обратимся теперь к фиг. 6 показан узел загрузки/выгрузки 70, используемый для загрузки и выгрузки деталей в спиральный трубопровод 32 узла реторты. Зарядно-разрядный узел 70 включает в себя загрузочный стакан или емкость 72 цилиндрической формы и разгрузочный стакан или емкость 74 цилиндрической формы, соединенные с емкостью 72 посредством удлиненного элемента или стержня 76. Зарядно-разрядный узел заключен в корпус. внутри осевого элемента 30. Емкость 72 для заряда также соединена со стержнем 78, который соединен с горизонтальным исполнительным средством (фиг. 4), таким как гидравлический цилиндр 79.для горизонтального перемещения узла 70 загрузки/выгрузки внутри осевого элемента 30 из положения загрузки (сплошные линии) в положение разгрузки (пунктирные линии). В положении разгрузки контейнеры 72 и 74 поворачиваются на 180 градусов с помощью вращающихся исполнительных средств, таких как поворотный привод 80, который также соединен со штоком 78.
Теперь будет описана работа зарядно-разгрузочного узла 70. Предположим вначале, что контейнеры 72 и 74 находятся в крайнем правом положении, как показано сплошными линиями на фиг. 6. Отверстие контейнера 72 для заряда находится в положении верхней мертвой точки, чтобы быть выровненным по вертикали с загрузочным желобом 82 (фиг. 4). Загрузочный желоб 82 пропускает контролируемый объем деталей, подлежащих термообработке, из загрузочного механизма 84 (фиг. 3) в загрузочный контейнер 72. Разгрузочный контейнер 74 имеет свое отверстие в положении верхней мертвой точки, чтобы быть выровненным по вертикали с разгрузочный желоб 32с спирального трубопровода 30. Разгрузочный желоб пропускает предварительно контролируемый объем деталей, которые были перемещены по трубопроводу, от последнего витка спирали к разгрузочному контейнеру 74. Контейнеры 72 и 74 затем перемещаются горизонтально на гидроцилиндр 79в крайнее левое положение, как показано пунктирными линиями на фиг. 6. Затем контейнеры 72 и 74 поворачиваются на 180 градусов поворотным приводом 80 так, чтобы их соответствующие отверстия находились в положении нижней мертвой точки. В результате загрузочный контейнер становится выровненным по вертикали с загрузочным желобом 32b спирального канала для подачи контролируемого объема деталей в первый спиральный виток. Одновременно разгрузочный контейнер 74 выровняется по вертикали с желобом 85 для закалки для подачи ранее контролируемого объема деталей в обычную систему 86 для закалки. перемещается горизонтально назад в крайнее правое положение гидроцилиндром 79. Затем этот цикл повторяется непрерывно. Закалочная система 86 включает в себя закалочную ванну 88 с любой обычной средой, такой как масло и т.п., и транспортное средство 90 для перемещения деталей из закалочной ванны.
Альтернативное расположение для загрузки и выгрузки деталей в спиральный канал 32 показано на фиг. 7. В этом устройстве используется наклонный скользящий загрузочный желоб 92 для подачи деталей в первый виток 94 спирального канала 96 и наклонный скользящий разгрузочный желоб 9.8 для подачи деталей с последнего витка 100 трубопровода. Загрузочный желоб 92 выполнен за одно целое со спиральным каналом и соединен с загрузочным концом осевого элемента 101. Разгрузочный желоб 98 также выполнен за одно целое со спиральным трубопроводом и соединен с выпускным концом осевого элемента 101. устройство позволяет загружать и выгружать детали в трубопровод 96 и из него под действием силы тяжести без использования узла загрузки/выгрузки 70. Другим альтернативным устройством может быть использование шнека (не показан) для загрузки деталей в спиральный трубопровод. и наклонный скользящий желоб, аналогичный желобу 98 для выгрузки деталей из спирального канала.
Обратимся теперь к загрузочному механизму 84, показанному на ФИГ. 1, 2 и 3 имеется бункер 102, в который детали, подлежащие термической обработке, транспортируются любым подходящим средством, таким как вилочный погрузчик, ленточный конвейер или ручная загрузка. Бункер 102 подает деталь к дозирующему загрузчику 84, который включает в себя ковши и транспортные средства для доставки контролируемого объема (веса) деталей через загрузочный желоб 82 с регулируемым объемом. в зарядный контейнер 72.
Вращающаяся ретортная печь по настоящему изобретению имеет следующие преимущества по сравнению с печами предшествующего уровня техники:
(а) она требует использования меньшего объема газов в контролируемой атмосфере;
(b) обеспечивает плотный контакт деталей, подлежащих термообработке, с контролируемой атмосферой, чтобы облегчить контакт деталей с равномерной атмосферой;
(c) устраняет проблему пересечения частей в смежных зонах полета, вызывающую смешивание частей; и
(d) он представляет собой относительно легкую реторту в сборе, которая менее затратна в производстве и обслуживании.
Из вышеприведенного подробного описания видно, что в настоящем документе предлагается усовершенствованная вращающаяся ретортная печь непрерывного действия, имеющая ретортный узел, образованный цилиндрическим вращающимся осевым элементом и спирально навитым трубопроводом, расположенным на внешней поверхности осевого элемента для перемещения части, подлежащие термообработке, от одного конца реторты до другого конца. Кроме того, предусмотрено устройство загрузки/выгрузки для использования при загрузке и выгрузке деталей, подлежащих термической обработке, в спирально закрученный трубопровод ретортного узла.
Несмотря на то, что было проиллюстрировано и описано то, что в настоящее время считается предпочтительным вариантом осуществления настоящего изобретения, специалистам в данной области будет понятно, что могут быть сделаны различные изменения и модификации, а эквиваленты могут быть заменены его элементы, не выходя за рамки истинного объема изобретения. Кроме того, можно сделать множество модификаций, чтобы адаптировать конкретную ситуацию или материал к идеям изобретения, не выходя за его основной объем. Следовательно, предполагается, что это изобретение не ограничивается конкретными вариантами осуществления, раскрытыми как наилучший предполагаемый способ осуществления этого изобретения, но что изобретение будет включать все варианты осуществления, подпадающие под объем прилагаемой формулы изобретения.
Серия XLC — L&L Special Furnace Co, Inc.
Описание:
Атмосферные ретортные печи серии XLC представляют собой передовую конструкцию, в которой особое внимание уделяется качеству процесса и контролю, а также безопасности оператора. Система управления, реторта сплава и проточная система полностью интегрированы в единую систему. Любое приложение, требующее 100% водорода или смеси водорода, окиси углерода, природного газа или любой другой горючей атмосферы (а также любой чисто инертной атмосферы), может использоваться в серии XLC. Типичными примерами являются водородная пайка и отжиг нержавеющей стали. Любой периодический процесс, который не переносит кислород или требует высокой степени надежности атмосферы, воспроизводимости и низкой точки росы, является кандидатом для этой печи. Максимальная температура составляет 2200°F (1200°C), хотя для увеличения срока службы реторты рекомендуются более низкие максимальные температуры. В зависимости от чистоты используемого газа эти печи могут поддерживать точку росы на уровне -60°F.
Источник питания:
Electric
Нагрузка:
Фронт
Атмосфера:
Контролируемый или водород или инертный/сжигаемый или азот/эндотермический или нитроген/метанол или азот/метанолол/атён/метанолол/метанолол/атёнолол/атён -атён/метанооловый/метанооловый/метанооловый/метанооловый/метанооловый/метанооловый/сжитый
Футеровка:
Кирпич с волокнистой крышей
Ниже перечислены самые популярные размеры наших моделей. Обсудите индивидуальное решение, которое точно соответствует вашим потребностям, связавшись с нашим отделом продаж сегодня.
Модель № | Внешние размеры Ш В Г | Внутри реторты W H D | Максимальная нагрузка (фунты) | Вес корабля (фунты) | Максимальная температура (°F) | Стандартная мощность (кВт) | Высокая мощность (кВт) |
---|---|---|---|---|---|---|---|
XLC524 | 34 57 64 | 10 10 22 | 905:501500 | 2200 | 13,5 | 18 | |
XLC824 | 37 60 64 | 905:501800 | 2200 | 17 | 22 | ||
XLC836 | 37 60 76 | 905:502100 | 2200 | 22,5 | 29 | ||
XLC848 | 37 60 88 | 905:502400 | 2200 | 27 | 36 | ||
XLC244 | 43 66 64 | 905:502600 | 2200 | 24 | 35 | ||
XLC246 | 43 66 76 | 905:503000 | 2200 | 31,5 | 41 | ||
XLC248 | 43 66 88 | 905:503500 | 2200 | 38 | 49,5 | ||
XLC272 | 43 66 112 | 905:504000 | 2200 | 51 | 68 | ||
XLC3348 | 49 68 88 | 905:503800 | 2200 | 48,5 | 65 | ||
XLC3372 | 49 68 112 | 905:505500 | 2200 | 66,5 | 88,5 | ||
XLC3448 | 55 62 88 | 905:504000 | 2200 | 48 | 64 | ||
XLC3472 | 55 62 112 | 905:506000 | 2200 | 66 | 88 | ||
XLC3648 | 55 74 88 | 905:504800 | 2200 | 56 | 66,5 | ||
XLC3672 | 55 74 112 | 905:507000 | 2200 | 82 | 109 |
Запросить цену
Наверх
Ретортная печь | ONEJOON Kilns & Furnaces
Промышленные печи Для сложных атмосфер (Sih5, h3, Mg, вакуум) и самых высоких требований к однородности температуры в периодическом процессе
- Печи и печи
- Ретортная печь
Печи непрерывного действия для осаждения газовой фазы (CVD )
неметаллических порошков и восстановление металлических порошков
Ретортная печь ONEJOON является идеальным решением для процессов со сложными атмосферами, такими как силаны (Sih5), водород (h3), газообразный магний (Mg), вакуум и многие другие. более.
Типичным применением ретортной печи является химическое осаждение из паровой фазы в неметаллические порошки, а также кислородное восстановление металлических порошков для получения металла высокой чистоты.
Ретортная печь с уникальной циркуляцией технологического газа, состоящей из высокой скорости технологического газа и оптимального направления технологического газа непосредственно над продуктом, обеспечивает однородный поток через всю структуру продукта, что, в свою очередь, обеспечивает превосходную однородность атмосферы и температуры. Благодаря высокой циркуляции технологического газа возможны очень короткие скорости нагрева и охлаждения без ущерба для однородности атмосферы и температуры.
Для экономии дополнительного технологического газа и минимизации времени цикла обмен технологического газа осуществляется путем вакуумирования технологической камеры и последующей подачи технологического газа.
Поскольку ретортная печь представляет собой печь периодического действия, для нее требуется мало места, а компоновка компактна.
Контакт Матиас Мук Старший эксперт Промышленные печи и технологии +49 551 820 830 — 300 [email protected]
Процесс
Производство оборудования
Наши услуги
Справочные материалы
Процесс
Процессы ретортной печи
С помощью ретортных печей ONEJOON можно картировать различные процессы.
К ним относятся, например:
- осаждение из паровой фазы (химическое осаждение из паровой фазы)
- восстановление кислорода
- удаление связующего и предварительное спекание
- специальные процессы
Процессы
- Химическое осаждение из газовой фазы
- Восстановление
Производство установок
Ретортная печь в деталях
Материалы
- Неметаллические порошки
- Металлические порошки
Описание системы
Как работает ретортная печь
Правильная термообработка высокоэффективной керамики2 Наполнение изготовленных изделий
900 транспортируется на под печи и поднимается вверх через подъемный портал.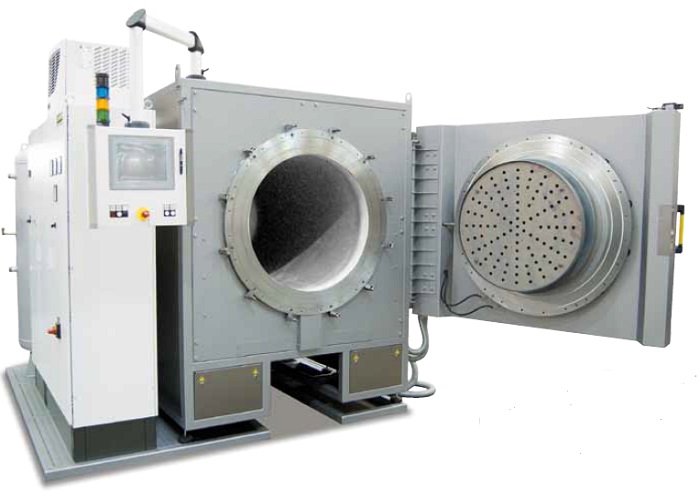
Во время фазы выжигания (до 500 °C) загрузка печи нагревается циркулирующим горячим воздухом, предварительно подогретым внешним нагревателем. Отходящие газы, загрязненные связующим, очищают в установке термического дожигания. В конце фазы выжигания осуществляется дальнейший нагрев электрическими нагревательными элементами в печи.
Технологический газ также можно поддерживать в циркуляции при повышенных температурах до 800 °C. Это способствует оптимальной однородности температуры в процессе нагрева. Циркуляция технологического газа заканчивается при температуре выше 800 °С.
Также на последующих этапах процесса циркуляция газа или воздуха не происходит до тех пор, пока не будет достигнута максимальная температура. Это связано с тем, что турбулентность в атмосфере печи часто очень важна для процессов спекания и кристаллизации. В конце процесса заготовки охлаждаются закаленным воздухом или газом. Для этого внешняя система обогрева заранее регулирует температуру охлаждающей среды до того, как она достигнет носителей продуктов и продуктов. После охлаждения до ок. 250 °C пол печи перемещается из подъемного портала в камеру охлаждения, где изделия окончательно охлаждаются до комнатной температуры.
Схема с потоком рециркуляционного газа, впрыском свежего технологического газа, выпуском отработавших газов, а также входом и выходом охлаждающего воздуха для охлаждения внешнего муфеля
Ретортные печи от ONEJOON
Краткий обзор преимуществ:
- сложные атмосферы (Sih5, h3, Mg и т. д.)
- отличная однородность атмосферы и температуры
- очень короткие скорости нагрева и охлаждения
- быстрая и простая загрузка и разгрузка
- оптимизированное время цикла
- мало места, компактная компоновка
Технические особенности:
- вакуумно-плотная реторта с внутренним муфелем
- прямой впрыск технологического газа
- оптимизированная циркуляция технологического газа с вентилятором горячего газа до 1000 °C
- 16 мощный непрямой 9 охлаждение
- зарядная стойка для быстрой загрузки и разгрузки
- CFD-моделирование для оптимизации потока технологического газа
Услуги
Наши услуги
Консультации, сервис, строительство печей и многое другое.
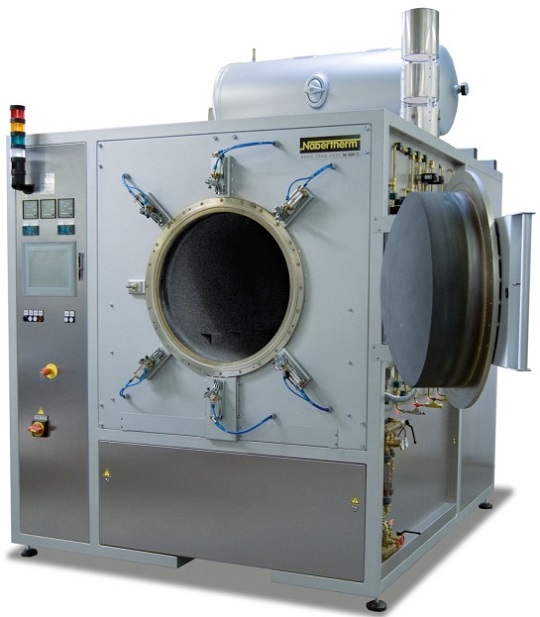
Просто потому, что у каждого клиента есть особые требования.
Вместе с вами мы разработаем оптимальное решение для вашего запроса.
- определение объема поставки
- проектирование системы на основе ваших спецификаций
- конфигурация системы из стандартизированных компонентов, адаптированные под клиента
- презентация концепции установки
- подготовка предложения
- проектирование, производство и испытание системы на нашем заводе
- отгрузка, сборка, ввод в эксплуатацию и приемка установки в вашем регионе по всему миру
- подготовка документации по установке и декларации соответствия CE
- производственная поддержка
- услуги: техническое обслуживание, запасные части, ремонт, измерения
- сеть для смежных процессов
Мы с нетерпением ждем вашего запроса, свяжитесь с нами сегодня!
Референции
Избранные референции
Довольные клиенты — лучшее доказательство успешного сотрудничества.
