- Расстояние между розетками в блоке
- размеры, диаметр коронки, расстояние между розетками, глубина установки
- Установка подрозетников в бетон, гипокартон и дерево.
- Диаметр подрозетника и другие параметры: глубина, межосевое расстояние
- Стандартные размеры подрозетников
- Технические требования к монтажным коробкам
- Монтаж одиночного подрозетника
- Советы
- Монтаж нового подрозетника в старый
- Подготовка стен
- Установка блока подрозетников
- Кто поддерживает горение а кто нет?
- Монтаж на прочие поверхности
- Виды
- Расположение провода в подрозетнике
- Дополнительный видео-инструктаж
- диаметр, глубина, расстояние между центрами
- Стандартные размеры подрозетников
- Диаметр
- Монтаж одиночного подрозетника
- Заготовка раствора и установка в нишу
- Монтаж нового подрозетника в старый
- Подрозетник выскочил из стены
- Установка блока подрозетников
- Максимальная глубина под подрозетник
- Монтаж на прочие поверхности
- Виды и характеристики подрозетников
- Расположение провода в подрозетнике
- Правильный выбор подрозетника для бетонных стен
- Диаметр подрозетника: размеры, глубина, межосевое расстояние
- Прикладные науки | Бесплатный полнотекстовый | Определение остаточных сварочных напряжений в стальном компоненте моста с помощью моделирования методом конечных элементов метода поэтапного сверления отверстий
- Регулируемый шаблон для фрезерования розетки и резонатора
- Сравнение метода кольцевого керна и метода сверления отверстий, используемых для определения остаточных напряжений
- Розетка — Гитары Джеймса Листера
- 404 ОШИБКА WOODWEB
- Экспериментальный анализ остаточных напряжений с помощью сверла
- 1. Введение
- 2. Измерительная система
- описано ниже.
- 3.1 Подготовка поверхности и склеивание
- 3.2 Определение глубины контакта (установка нуля)
- 4. Определение рабочих параметров
- 4.1 Скорость вращения во время сверления
- 4.2 Скорость подачи
- 4.3 Выбор времени задержки
- 4.4 Проверка изменения температуры пластикового компонента
Расстояние между розетками в блоке
Установочная коробка для скрытой установки, предназначенная для крепления в ней розетки, называется подрозетником. Чаще всего подрозетник имеет круглую форму (реже квадратную) и стандартный размер. Главная функция подрозетника — обеспечить жесткое и надежное монтажное место для розетки внутри стены, вблизи плоскости ее поверхности.
Если вам потребовалось установить подрозетник, то вооружившись вполне обычными инструментами (карандаш, уровень, шпатель, кисть, молоток, зубило, дрель с коронкой, алебастр), вы сможете это сделать своими руками. Соблюдайте технику безопасности, предварительно отключите в щитке подачу электричества, аккуратно пользуйтесь инструментом, помните о стандартах — и все получится.
Монтаж подрозетника
Сначала делают разметку относительно провода, идущего к будущей розетке. Проводят горизонтальную линию на небольшом расстоянии от провода — это уровень центра будущей розетки, затем чертят вертикальную линию — это будет край подрозетника (провод должен будет зайти сверху сбоку), наконец прикладывают подрозетник, и обводят его карандашом — обозначают место для сверления.
Стандартный диаметр под сверление коронкой — 68 мм, причем глубина составит примерно 45 мм, это следует учитывать при выборе коронки. Вообще, насадка на дрель так и называется «коронка для подрозетника» (они есть для бетона, для дерева и т. д.), поэтому проблемы с ее приобретением не возникнет. Сверлят по разметке, если нужно, в процессе сверления смачивают насадку водой, чтобы она сильно не перегревалась.
Подрозетник примеряют к отверстию, удаляют при помощи зубила и молотка остатки высверленного материала.
Если подрозетник ставится одиночный, то переходные ушки с его краев срезают, чтобы они не мешали установке в посадочное отверстие, если же розеток будет несколько рядом (блок розеток), то нужные ушки оставляют для скрепления нескольких подрозетников друг с другом.
Если подрозетник легко входит в посадочное отверстие — все хорошо. Провод должен без проблем входить в диагональное отверстие подрозетника, которое находится сбоку возле задней его стенки.
Когда подрозетник нормально входит, подходит по диаметру и глубине, отверстие смачивают водой чтобы лучше приставал алебастр, затем замешивают раствор. Раствор готовят из расчета 4 к 1 — 4 части алебастра к 1 части воды. Наносят раствор на подрозетник со всех контактирующих со стеной сторон.
Осуществляют установку, выставляют подрозетник строго в плоскости стены, чтобы он и не выпирал, и не впадал слишком уж глубоко, края подрозетника должны находиться на одинаковом расстоянии от краев посадочного отверстия. Остатками раствора алебастра маскируют провод, идущий к подрозетнику.
Установка новой розетки в старый подрозетник
Порой, при проведении ремонта в многолетних домах, оказывается, что старый металлический подрозетник намного шире чем нужно, новая розетка в нем болтается как в ведре, лапки не зацепляются. В этом случае можно поставить новый подрозетник прямо внутрь старой коробки.
Жесткая широкая старая коробка без дна потребует применения раствора алебастра, как в случае с установкой подрозетника в стену. Если же коробка прочно удерживает новый подрозетник, то его просто прикручивают на саморезы к старому, помня о том, что провод необходимо завести сзади сбоку, и не повредить его саморезами.
Блок из нескольких подрозетников
Если подрозетников ставится несколько в ряд, то это делают монтируя блок подрозетников. Коронка берется немного большего диаметратра — более 68 мм, вплоть до 80 мм — посадочные отверстия будут объединены между собой, а межосевое расстояние составит минимум 71 мм.
Делают разметку горизонтали относительно провода, который должен будет зайти справа, затем размечают стену под сверление посадочных отверстий с учетом нужного межосевого расстояния или по уже соединенным подрозетникам — просто обводят блок.
Высверливают отверстия, зубилом и молотком устраняют лишнее, убирают перегородки, заводят горизонтально провод. Запас по диаметру поможет ровно сориентировать блок. Переходные ушки выполняют здесь свою функцию — объединяют подрозетники в блок.
Установка подрозетника в гипсокартон
Универсальные подрозетники для гипсокартона имеют специальные распорные ушки, которые облегчают фиксацию, и не нужен с ними алебастр. Сверлится коронкой отверстие под размер подрозетника, производится установка, осуществляется фиксация отверткой — все. Крепежные ушки при закручивании отверткой распираются и хорошо держатся внутри тонкостенных поверхностей типа гипсокартона.
Универсальный подрозетник имеет расстояние между фиксирующими лапками около 83 мм, поэтому если выключатель или розетка отличаются большим чем у обычных расстоянием между креплениями — такие устройства встанут хорошо. Также универсальные подрозетники можно в принципе прикручивать к дереву или ставить в бетон, просто убрав фиксирующие лапки.
Монтаж под штукатурку или плитку
Если стена в дальнейшем будет штукатуриться или покрываться плиткой, то необходимо это учесть при монтаже подрозетника. Сделайте запас на выступ порядка 7 мм (или сколько будет покрытия), чтобы плоскость будущего покрытия стены совпадала с краем устанавливаемого подрозетника. Таким образом, подрозетник нужно оставить выступающим.
Вообще, устанавливая подрозетник в стену заранее, важно брать в расчет тот факт, что возможно глубина будущей розетки (выключателя) и ее диаметр будут отличаться от геометрических параметров подрозетника.
Провод в подрозетнике должен иметь запас
Несмотря на кажущуюся незначительность этого аспекта, предусмотрительный монтажник всегда принимает во внимание тот факт, что вероятно в будущем, при замене розетки или выключателя, потребуется зачистить провод или немного его укоротить. Если провод окажется коротким, то его придется наращивать, а это будет сопряжено с повышенной уязвимостью соединения, оно быстрее окислится и разрушится, будет искрить.
Провод берется с запасом примерно сантиметров 20, аккуратно скручивается в спираль или плавно (не круто) сгибается, и таким образом компактно укладывается внутри подрозетника. Это делается, конечно, для того, чтобы если в будущем хозяева затеют обновление интерьера, они смогли бы легко обновить розетки без лишних заморочек и проблем с наращиванием. Как нарастить короткий провод если стена, скажем, покрыта плиткой или штукатурной? Проще заранее оставить запас.
Делаем шаблон для установки подрозетников
При монтаже современных розеток или выключателей внутренней установки их механизмы должны размещаться в специальной пластиковой коробочке — подрозетнике. На сегодняшний день практически вся электрическая фурнитура выполняется таким образом, что позволяет установить в один ряд несколько розеток или выключателей.
Согласитесь, что одной розетки на кухне уже не хватает, а розетками, установленными на разных концах стены не всегда удобно пользоваться. Поэтому зачастую электрика проектируется таким образом, чтобы в одном месте размещалось несколько точек для подключения бытовой техники. Это очень практично и функционально.
Некоторые мастера по незнанию выполняют сборку не под одну многопостовую рамку, а устанавливают рядом отдельно стоящие розетки. Такая конструкция не создает впечатления единого целого устройства, из-за этого такой монтаж не совсем красиво смотрится.
Профессионалы при монтаже блока розеток всегда используют декоративную рамку на два, три или четыре окна. Но порой бывает так, что на завершающем этапе монтажа розетки с трудом удается установить в коробки, из-за того что они накладываются друг на друга.
Декоративная рамка в этом случае также не стает на свое место. Связано это с тем, что при установке подрозетников не соблюдалось расстояние между их центрами. В идеале расстояние между центрами подрозетников должно составлять 71 мм. А при установке большого числа коробок они начинают смещаться друг относительно друга или деформируются под действием шпаклевочной смеси.
Добрый день дорогие друзья! Я снова рад приветствовать вас на сайте «Электрик в доме». В этой статье поговорим об одной простой и, наряду с тем, полезной штуке для установки подрозетников в стены из кирпича, бетона и газоблоков. Те люди, которые профессионально занимаются электромонтажом, знают, как порой непросто ровно установить блок из пяти розеток.
При помощи несложного приспособления, о котором пойдет речь в данной статье, можно осуществлять установку подрозетников с точностью до миллиметра. Подобные штуки не вырабатываются промышленными предприятиями, поэтому мастера самостоятельно делают подходящие для них самоделки. Данное приспособление на сленге электриков называется шаблон для установки подрозетников. Также встречаются такие названия как кондуктор или макет, но все они выполняют одну и туже функцию.
Планка для установки подрозетников
Большинство пластиковых коробок для монтажа розеток имеют размеры 68 мм в диаметре и глубину порядка 45 мм. Коробки у разных производителей могут немного отличаться между собой по размерам и характеристикам, но функционал у всех одинаковый — будучи собранными в блок, они обеспечивают межцентровое расстояние устанавливаемых механизмов в 71 миллиметр.
Чтобы при монтаже коробки не плясали друг относительно друга их необходимо жестко зафиксировать между собой. Как коробки собираются в блок? Рассмотрим подрозетники фирмы Schneider Electric для внутренней установки. Если внимательно присмотреться на передней части имеются специальные защелки для стыковки нескольких коробок.
Состыковать коробки можно также при помощи специальных соединителей – заглушек .
На первый взгляд, дело кажется простым – после сбора коробок в блок автоматически получаются требуемые межцентровые размеры. Зачем вообще необходим какой-то шаблон для установки подрозетников? Все итак отлично стыкуется.
Однако следует учитывать, что для закрепления подрозетника следует заполнить раствором все пространство между стенками отверстия в стене и самим подрозетником. Поэтому закладка раствора в гнездо осуществляется с избытком. И когда коробку начинаешь вдавливать на место, раствор начнет выходить со всех щелей, заполняя пустоты, в результате чего получается очень прочное фиксирование подрозетника.
Но при вдавливании коробки необходимо приложить изрядное усилие, под действием которого пластиковый подрозетник может попросту лопнуть или изменить форму (стать овальным), а блок из нескольких коробок обязательно расплывется в разные стороны. На финальной стадии установки механизмов розеток и выключателей компенсировать все эти недочеты суппортами невозможно.
Более того коробки при установке должны быть четко установлены по уровню, чтобы торцы не выпирали и небыли утоплены, а находились заподлицо со стеной. При установке блока подрозетников голыми руками такое сделать можно, но на это тратится очень много времени и усилий.
Именно для решения таких задач я сделал себе такое приспособление, как шаблон для установки подрозетников которое позволяет экономить не только время, но и нервы.
Как сделать шаблон для установки подрозетников своими руками
Приступим непосредственно к изготовлению нашего устройства. Для этого я взял алюминиевый уголок размером 40х40 мм. Длина уголка зависит от количества устанавливаемых в блоке подрозетников, плюс необходимые отступы от каждого края для крепления уголка к стене (примерно 10 – 15 см с каждой стороны). Я решил сделать макет для пяти подрозетников поэтому взял уголок длиной 60 см.
Да кстати совсем не обязательно делать шаблон из уголка и тем более из алюминиевого. Можно взять любой жесткий материал произвольной формы, у кого что есть, например трубопрофиль. Удобство шаблона из алюминия в его легкости. Кстати возникали идеи сделать макет из дин-рейки, там и отверстия сверлить не нужно.
Теперь по центру ребра, где будут крепиться коробки необходимо разметить линию. С обеих сторон уголка с помощью рулетки находим центр и отмечаем карандашом линию.
По намеченной линии будем сверлить отверстия для крепления подрозетников с помощью саморезов. Наш шаблон для установки подрозетников практически готов. Приступаем к высверливанию отверстий. Для этого нам в помощь шуруповерт и сверло по металлу размером 3 мм.
Отступаем от края уголка 12 см и сверлим первое отверстие. Чтобы сверло не соскальзывало с намеченного места сверления, рекомендую его накернить.
Затем замеряем расстояние между центрами саморезов подрозетника и переносим его на наш шаблон. У меня получилось 60 мм. Это будет точка для высверливания второго отверстия. Аналогичным образом высверливаем отверстия для всех подрозетников в блоке.
Примеряем коробку на планке
По краям уголка отступаем по 5 см и высверливаем еще два отверстия. При монтаже это поможет прижать к стене всю конструкцию.
Теперь закрепим на готовом макете все подрозетники, получается ровная конструкция, которую удастся вставить в стену без перекосов и изгибов.
Давайте посмотрим, какое расстояние у нас получилось между центрами коробок относительно высверленных отверстий:
Для установки блока подрозетников с помощью шаблона накидываем в отверстие в стене немного раствора, просовываем провода в подрозетники и крепим шаблон к стене. Предварительно нужно пробурить в стене отверстия. Уголок к стене фиксируем дюбелями.
Удобство такой конструкции в том, что все коробки устанавливаются с точным расстоянием друг относительно друга, и нет необходимости постоянно выверять и поправлять каждую коробку до полного высыхания раствора. Также исключается деформация коробок, и все они выставляются заподлицо со стеной.
Можно по краям сделать заточки, чтобы удобно было выставлять шаблон по горизонтали.
Надеюсь, дорогие друзья статья была для вас интересной, и данное устройство поможет вам облегчить и ускорить монтаж. У кого какие мнения? Может уже кто-то пользуется данной конструкцией или есть мнения как ее улучшить. Давайте делиться опытом.
Установка подрозетников
Перед установкой подрозетника (монтажной коробки) нужно в первую очередь подготовить необходимый инструмент и материалы. Если уже проложен провод, он должен быть обесточен или заизолирован.
Установка подрозетников в бетон
Начинаем с разметки. Как правило, розетки располагают на расстоянии 25-30 см от пола, выключатели примерно 90 см от пола. Если розетка устанавливается над рабочей поверхностью кухни, то её расположение должно быть на расстоянии 15-20 см от столешницы.
После того, как расположение электроточки определено, с помощью пузырькового уровня чертим на стене горизонтальную линию и отмечаем на ней расстояние между подрозетниками. Для этого нужно отметить две точки на линии, которые будут центрами будущих углублений. Расстояние между точками 71 мм . Для бурения углублений используется специальная коронка для подрозетников с зубьями из твёрдого сплава. Диаметр коронки по бетону для подрозетника примерно 85 мм. Чтобы ускорить процесс и обеспечить более точное вхождение коронки, предварительно делаем отверстия с помощью перфоратора и бура
диаметром равным диаметру сверла в коронке. От вибрации очень часто у коронки откручивается прижимной болт для сверла. Чтобы этого не происходило, его можно зафиксировать с помощью изоленты. Если Вам нужно пробурить большое количество углублений, лучше использовать мощный перфоратор (лучше SDSmax). Можно использовать и безударное сверление. Для безударного сверления используют алмазные коронки сухого сверления и мощную высоко-оборотистую дрель, желательно от 1.5 кВт и от 3000 об/мин без нагрузки. Диаметры коротких коронок, выпускаемых для сверления отверстий под подрозетники: 68 и 82 мм. Преимущества безударного сверления: малый уровень шума и вибрации, высокая производительность, способность резать армированный бетон. Недостаток такого способа – дороговизна.
После работы коронки, с помощью зубила и молотка или перфоратора с зубилом убираем бетон из углублений. Проверяем, чтобы подрозетники свободно входили в углубления. Для лучшего сцепления строительного гипса и бетона углубления обрабатываем грунтовкой. Можно просто смочить водой. Теперь углубления готовы для установки подрозетников.
Так выглядит подрозетник и соединитель. В продаже существует огромный ассортимент подрозетников: с соединителями и без, округлой и квадратной формы, для установки в гипсокартон и бетонные стены. Перед монтажом необходимо вырезать в подрозетниках отверстия для провода.
Теперь нужно приготовить строительный гипс. Для этого разводим его водой так, чтобы смесь была похожа на густую сметану. Заполняем углубления гипсом примерно на одну треть и размещаем коробки, вдавливая их в раствор заподлицо с поверхностью стены или чуть утопив. Край подрозетника ни в коем случае не должен выступать за поверхность стены. Проверяем положение подрозетников по горизонту, ориентируясь на, ранее сделанную на стене, разметку. С выравниванием подрозетников лучше поторопиться, так как гипс схватывается очень быстро. После частичного схватывания, шпателем, как скребком убираем лишний раствор с поверхности стены и чистим подрозетники от попавшего через щели гипса.
Всё, подрозетники установлены. В стене из кирпича, шлакоблоков, гипсовых плит и газобетона коробки монтируются аналогично.
Установка подрозетников в гипсокартон
В стену из гипсокартона монтаж подрозетников гораздо проще. Для этого существуют специальные подрозетники с «лапками» прижимающими его к листу гипсокартона
с обратной стороны. На стене делается разметка аналогичная предыдущей, с помощью обычной дрели и коронки для гипсокартона делается отверстие. В случае установки двух и более розеток в блоке, расстояние между центрами так же должно составлять 71 мм, только диаметр коронки должен быть равен диаметру подрозетника — 68 мм. Ещё нужно обратить внимание на расстояние между основной стеной и стеной из гипсокартона, чтобы хватило глубины для установки коробки, в противном случае основную стену придётся поддалбливать с помощью перфоратора или зубила. Если гипсокартон смонтирован в два слоя на профиль 60×27 мм, проблем с глубиной возникнуть не должно. Глубина коробки составляет 47 мм.
Установка подрозетников в старом фонде
Теперь рассмотрим сложный случай. Старый фонд с деревянными оштукатуренными перегородками. В таких стенах даже кабель в гофрированной трубке не уложить, толщины штукатурки не хватит, придётся убирать дранку и выпиливать в доске штробу. Для кабеля это конечно не обязательно, его можно и так уложить, а вот коробку для розетки или выключателя всё равно придётся утапливать.
Помочь нам в этом может коронка по дереву и дрель. Цена такого набора коронок невысокая и продаётся она почти в любом строительном магазине. Дрель лучше всего использовать с низкими оборотами с дополнительной рукояткой, это так называемая сверлильная машина. Такие дрели ещё используют с миксером для размешивания растворов. Но можно обойтись и обычной дрелью.
Перед началом работы в месте установки удаляем штукатурку и делаем разметку, как в примере с бетонной и стеной. Дрелью с коронкой сверлим углубление. С помощью стамески и молотка выдалбливаем сердцевину углубления. Если для подрозетника не хватает глубины, повторяем эту процедуру. Углубление делаем немного глубже подрозетника, примерно на 5 мм.
Готовим раствор строительного гипса. Затем шпателем наносим его на заднюю часть монтажных коробок и монтируем их в углубления заподлицо с поверхностью стены. Выравниваем по горизонтали и ждём, когда схватится гипс. После этого, саморезами по дереву прочно крепим их к стене и заштукатуриваем пространство между подрозетниками и стеной.
И наконец, последнее. Если розетки и выключатели устанавливаются во влажных помещениях, без гидроизоляции стен, или вне помещения, вместо гипса желательно использовать ремсостав на цементно-песчаной основе.
Как установить блок розеток в стене – инструкция от А до Я
В чем может быть нюанс
На сегодняшний день стены в доме могут быть бетонными, деревянными, кирпичными либо из гипсокартона. Из-за этого технология монтажа может иметь свои особенности – толи Вы будете штробить бетон в панельном доме, толи просто установите на поверхности накладной блок розеток (наружный) для открытой проводки. Далее мы вкратце расскажем про каждый из вариантов установки, но все же более подробно Вы можете узнать о том, как монтировать подрозетник в бетонной, кирпичной и гипсокартонной стене в соответствующей статье.
Еще один нюанс заключается в том, что сейчас мы рассматриваем только технологию установки и подключения розеточного блока. На сегодняшний день существует еще комбинированный вариант: силовая розетка+выключатель, но о монтаже такой комбинации мы поговорим отдельно.
Инструкция по монтажу
Шаг 1 – Подготовительные работы
Для начала нужно определиться с тем, где Вы хотите поставить розеточную группу в комнате. Если это, кухня, то лучше расположить блок розеток над столешницей, чтобы при подключении мультиварки, микроволновой печи и другой кухонной техники хватило длины шнура. В гостиной либо зале лучше всего установить изделие за телевизором, чтобы большой экран мог спрятать все шнуры. Если Вы решили поставить блок из двух либо трех розеток в ванной комнате, учитывайте важное правило – расстояние от воды должно быть не менее 0,6 метров и при этом корпуса электрических точек должны быть влагозащищенными. Больше советов по поводу данного момента Вы можете получить в статье — высота установки розеток по евростандарту.
Кстати для кухни существует оригинальный вариант исполнения розеточного блока – выдвижной. Врезной корпус в данном случае скрывается в столешнице и открывается при небольшом нажатии. Очень удобно и к тому же безопасно, поэтому при желании рекомендуем установить именно такую модель изделий.
Также на данном этапе Вы должны подготовить инструмент для штробления стен под проводку и подрозетники. Если стена бетонная либо кирпичная, используйте перфоратор со специальной коронкой. Для гипсокартона также существует своя насадка для штробления. Помимо этого подготовьте строительный уровень, маркер и рулетку.
Шаг 2 – Разметка стен
На самом деле очень важный этап, от которого будет зависеть правильность дальнейшей установки и подключения. Вам необходимо нанести разметку на поверхности под установку подрозетников на основании того, сколько электрических розеток будет в блоке. Первое и очень важное правило – расстояние между центрами подрозетников должно быть строго 72 мм. Если Вы допустите погрешность, при установке декоративной крышки она может не стать на свое место. Помимо этого следите за тем, чтобы все круглые штробы были размещены в одной горизонтальной либо вертикальной плоскости. Для этого рекомендуем использовать строительный уровень.
Когда стены будут размечены, можно переходить к штроблению.
Шаг 3 – Создание штроб
Если стены в вашей квартире зашиты листами ГКЛ, тут еще проще — с помощью перфоратора и коронки по гипсокартону вырезаете круглые штробы согласно разметке.
Шаг 4 – Крепление подрозетников
Следующее что Вы должны сделать – установить блок подрозетников. На сегодняшний день существуют специальные пластиковые стаканы, которые могут соединяться между собой. Соединить подрозетники не составит труда даже электрику-новичку.
В кирпичных и бетонных стенах нужно самому вмазать стаканы гипсовым раствором. В гипсокартоне все проще – подрозетники прижимаются к листу специальными лапками по бокам. Опять-таки, увидеть сущность установки подрозетников Вы можете в статье, на которую мы сослались еще в начале.
Шаг 5 – Подключение электрики
Когда раствор застынет (это касается стен из бетона и кирпича), можно переходить к подключению внутреннего блока розеток к сети 220В своими руками. Подключить несколько евророзеток допускается шлейфом от одного вводно кабеля, если Вы не будете подсоединять очень мощную бытовую технику, к примеру, электроплиту.
Итак, для начала отключите электроэнергию на квартирном щитке, после чего заведите в первый подрозетник вводные провода от распределительной коробки: фазу, ноль и заземление. После этого сделайте перемычки для подключения остальных розеток в блоке. Подключение блока из 3 либо 4 розеток нужно производить по данной схеме:
После того как Вы подключите все жилы в соответствующие клеммы, можно самостоятельно фиксировать корпуса евророзеток в подрозетниках и установить декоративную крышку.
Размеры подрозетников
При начале работы с электрикой один из самых частых вопросов — какой размер у подрозетников, на каком расстоянии сверлить отверстия под них?
Стандартные размеры подрозетников
Обычный подрозетник имеет размер 68 мм на 45 мм, где 68 — это диаметр, а 45 — глубина. При установке блоком расстояние между центрами высверливаемых отверстий — 71 мм.
В зависимости от производителя и решаемых задач размеры подрозетников немного варьируются:
- Диаметр может быть 68 мм или 60 мм, в редких случаях — до 72 (это «внешняя» кромка для Легранда, в стандартный цилиндр 68 мм сам подрозетник влезает),
- Глубина зависит от типа устанавливаемой «начинки» и в минимуме составляет 40 мм, в максимуме — может достигать 60 и даже 75−80мм.
Следует также знать, что кроме стандартных компоновок существует подрозетники для гипсокартона — они стоят чуть дороже из-за небольших лапок, закреплённых на болтах. За счёт этих держателей корпус фиксируется на обратной стороне листа ГКЛ.
Подрозетники стандартных размеров 65×45
Размеры инструмента
Места для подрозетников в бетоне сверлятся коронкой на 68 мм — она стандартная. Существуют небольшие цилиндры для 60 мм подрозетников, но брать для дома такую оснастку не стоит — лишний сантиметр несложно закрыть алебастром или штукатуркой, а оказаться в ситуации, что подрозетник не лезет в гнездо не стоит. Для работы с высокопрочными материалами используют алмазные коронки. Расстояние между центрами сверления остаётся 71 мм при любых размерах.
При сверлении в кирпиче и бетоне следует делать отметку глубины на самой коронке, чтобы не пробурить отверстие слишком глубоко. Особенно опасны в этом смысле межкомнатные перегородки, толщина которых может составлять всего 80−90мм.
Для гипсокартона используется отдельная коронка. Сверлить коронкой по бетону в гипсокартоне не следует — материал слишком сильно разрушится. Если нет отдельной оснастки для ГКЛ — лучше воспользоваться ножовкой и вырезать отверстие по разметке.
Подрозетники конкретных производителей
Каждый производитель немного варьирует размеры вокруг стандартных. Если проводится электрика конкретного бренда — то лучше использовать их же подрозетники.
Schneider Electric
Стандартный подрозетник Шнейдер Электрик диаметром 65 мм и глубиной 45 мм. Производится в России, достаточно доступный вариант.
Ещё один русский производитель из Тамбова. Стандартный подрозетник Хегель достаточно крупный — диаметром 68 мм с глубиной 60 мм. Отлично подходит для переключателей и сложных диммеров.
Дорогие подрозетники Легранд французского производства — настоящие гиганты. Внешний диаметр 70 мм и глубина 65 мм. Однако, есть несколько типов подрозетников LeGrand, в том числе стандартные с диаметром 68 мм и двумя глубинами — на 40 и на 60 мм. Для установки групп они подходят лучше.
Заключение
Несмотря на «зоопарк» производителей, в электрике уже сложились свои стандарты, и ошибиться с размерами подрозетников практически невозможно. Даже без купленной фурнитуры можно сверлить места для подрозетников по стандартным расстояниям и не беспокоиться о том, что что-то не уместится.
размеры, диаметр коронки, расстояние между розетками, глубина установки
Электромонтажные коробки используют для установки розеток, распределения проводов при входе в помещение или при опускании кабеля по стене на электроприборы. В распаечных корпусах соединяют провода, отводы снаружи и внутри зданий. При монтаже выдерживают рекомендуемое расстояние между подрозетниками, если собираются устанавливать не одно изделие, а целый блок разъемных устройств.
Содержание
- Размеры подрозетников и коронок
- Диаметр
- Глубина
- Межосевое расстояние и другие параметры
- Правила группировки
- Правила монтажа
- В гипсокартон
- В бетон
- Под штукатурку и плитку
Размеры подрозетников и коронок
В стенах из различных материалов применяют специальные коронки, чтобы просверлить нишу под коробку. Подрозетники бывают открытого и скрытого типа, в первом случае сверление не потребуется. Во втором варианте необходимо узнать диаметр корпуса под розетку, чтобы правильно выбрать размер коронки.
Последствия неправильно выбранного диаметра коронки:
- Если купить инструмент с узким сверлением, дополнительно придется разбивать нишу, чтобы корпус встал на свое место.
- В просторное отверстие нужно монтировать изделие, заделывая пустоты алебастром или другим видом раствора, что приведет к ослаблению крепежа.
Различают конструкции коронок, предназначенных для сверления бетона, кирпича и гипсокартона. По форме они круглые, отличаются диаметром и напайками на режущих гранях.
Коронки для подрозетников бывают разборные и неразборные. В первом случае конструкция подлежит ремонту, если износились или сломались запчасти. Во втором устройства рассматриваются как одноразовые.
Нанимаю специалиста
5. 52%
Сам
90.7%
Зависит от объема работ
3.78%
Проголосовало: 344
Диаметр
Поперечное сечение коробок под монтаж розеток стандартизировано.
Диаметр подрозетника по внутреннему сечению:
- Установочные коробки обычного размера имеют одинаковый диаметр 68 мм. Это объясняется сочетаемостью с конструкцией розеток, выключателей, регуляторов. У этих электроприборов есть крепежные части, размах которых рассчитан на такие размеры.
- Распаечные, распределительные корпуса имеют размеры от 60 до 100 мм.
Для выборки ниш под розеточные корпуса применяют коронки диаметром 70 и 75 мм. Во втором случае потребуется крепление коробки не только метизами, но и слоем алебастра.
Иногда в старых домах стоят подрозетники, установочные размеры которых по ранее действующим нормативам отличаются от действующих в большую сторону. Такие коробки могут быть по ширине 72 – 75 мм. Если подрозетник нужно поставить на это же место, возникает проблема, так как после демонтажа старой коробки остается большая ниша.
Если позволяет глубина старого подрозетника, новый устанавливают непосредственно в него. Обычно такие изделия выполнены из металла и чаще не имеют дна. Новый элемент монтируют с помощью саморезов к стенкам старого. При этом не забывают, что нужно оставить место для бокового выведения кабеля.
Глубина
Кожух с дном под розетку имеет глубину 45 мм. Это стандартная глубина подрозетника, которая не меняется у разных моделей. Для сверления потребуется оснастка, которая может выбирать материал стены на такую глубину.
Иногда встречаются варианты, когда требуется большая глубина:
- используют дополнительный корпус без дна;
- вначале формируют глубокую нишу (по расчету), используя сверлильную коронку несколько раз;
- в отверстие, глубоко утапливая, ставят корпус с дном, закрепляют его метизом (дюбелем) к основанию;
- сверху, ближе к краю устанавливают добавочный кожух, который дна не имеет;
- его также фиксируют к стенкам отверстия, сбоку заводят провода.
Установка корпуса с дном может не понадобиться, если требуемая глубина подрозетника немного превышает размер элемента без дна. В этом случае под деталь формируют нишу требуемой глубины, а подрозетник устанавливают на нужную глубину.
Межосевое расстояние и другие параметры
При монтаже одиночного подрозетника с его боков срезают квадратные ушки, чтобы они не мешали работе по установке. Если ставят несколько кожухов сразу (под пару розеток или выключателей), такие крепежные детали помогут скрепить подрозетники друг с другом. Такие замки удобны, т. к. при их использовании соблюдается межосевой промежуток.
Расстояния, которые нужно выдерживать:
- межосевое расстояние между подрозетниками в блоке должно быть строго 71 мм;
- при фиксации в гипсокартоне отверстие делают точно 68 мм, если сделать больше, крепежные лапки провалятся в материал вместе с кожухами;
- расстояние от оконного откоса до первой электророзетки из общей группы не должно быть меньше 15 – 20 см;
- розетки устанавливают на высоте от пола на 30 см, выключатели — на 90 см, регуляторы — 150 см.
Если ставят подрозеточные коробки без соединительных замков, межосевое расстояние выставляют самостоятельно с помощью рулетки.
Правила группировки
В розеточном блоке допускается ставить несколько приборов, их количество почти ничем не ограничено, но обычно более 6 – 8 штук не монтируют. В блоке, помимо розеток, могут быть выключатели, регуляторы, телевизионные, компьютерные разъемы.
Правила группировки и проведения работ:
- На стене размечают места подрозетников (не выключателей и регуляторов, а кожухов).
- Для формирования выемок используют коронки под розетку диаметром 70 мм, чтобы дать свободу корректировки межосевых расстояний.
- Корпуса регулируют по центрам, выставляют по вертикали и горизонтали.
- Если пренебречь уровнем, все розетки в блоке будут стоять косо (так, как смонтированы коробки под них).
- Принимают во внимание край кожуха.
- Стандартно бортик должен быть в одной плоскости со стеной — тогда розетка с крышкой плотно станет к поверхности.
Валера
Голос строительного гуру
Задать вопрос
После высверливания отверстий в них устанавливают блок для проверки по всем параметрам. Допускается отклонение бортиков блока от оси на 1,5 – 2 мм. Координируют возможность ввода в подрозетники всех проводов, чтобы не мешали друг другу. Слаботочные и силовые разъемы разводят между собой на промежуток, равный еще одному диаметру розетки. Так электромагнитные волны не будут мешать работе устройств.
Правила монтажа
Все установочные подрозетники имеют функциональные элементы для облегчения монтажа.
Конструкция зависит от материала вертикальных ограждений:
- В полые перегородки из гипсокартона коробки ставят с помощью специальной фиксационной системы распорных лапок.
- В пористых материалах стен применяют кожухи упрощенного строения для монтажа в подготовленные ниши при штроблении.
- Для бетонных поверхностей используют гладкие коробки, их надежно фиксируют быстросхватывающимися растворами на основе гипса и алебастра и дюбелями.
Подрозетник сделан в виде пластикового цилиндра в котором предусмотрены отверстия для закручивания саморезов. На внутренних стенках есть наметка для отверстий под провода. При необходимости перфорированные участки вырезают ножом с удобной стороны, в них заводят кабели.
В гипсокартон
Распорные лапки или ушки — основное отличие коробок под розетки для фиксации в гипсокартоне. При таком креплении, если все размечено правильно, алебастр не потребуется.
Правила монтажа подрозетников в гипсокартон:
- Коронкой с зубчатым краем сверлят отверстие в панелях так, чтобы диаметр точно совпадал с размером коробки.
- Саморез фиксируют отверткой, при этом лапки расходятся в стороны, прижимают подрозетник к стене.
- Стандартное расстояние между ушками — 83 мм.
Валера
Голос строительного гуру
Задать вопрос
Для работы не стоит приобретать коронки по гипсокартону китайского изготовления. Товар теряет рабочие параметры после нескольких просверленных выемок (отпадают напайки). Монтажники проводки всегда оставляют запас провода, чтобы в будущем заменить розетку, выключатель, при этом не добавлять недостающие несколько сантиметров.
В бетон
Бетонные стены сверлят перфоратором. Если применять ударную дрель, понадобится в полтора раза больше времени. Обычная дрель не подходит для работы с бетоном.
Сначала на стене делают разметку для основного сверла. Дальнейшие процессы:
- Наконечник вставляют в метку, начинают сверление.
- После достижения граничной глубины убирают коронку.
- Выбивают центральную область в черте реза, применяют перфоратор-отбойник или действуют зубилом и молотком.
Коронки для бетона представляют собой цилиндрическую насадку с алмазным напылением на зубцах.
Сегменты режут бетон с помощью алмазной крошки, появляющейся при работе. Есть разновидности М, С, Т (для обычного, армированного и высокомарочного бетона, соответственно). Такими алмазными коронками можно только сверлить бетонные стены, они не предназначены для ударных и комбинированных режимов. Для удара берут победитовые сверла.
Под штукатурку и плитку
Разводку проводки в доме делают чаще всего до штукатурных работ или перед облицовкой стен плиткой. Этот момент учитывают при сверлении выемок для подрозетников. Края коробок должны быть вровень со штукатурным слоем или плиточным покрытием, чтобы розеточная крышка прилегала к поверхности без щелей.
Варианты установки коробок в таких случаях:
- Край подрозетника выставляют над стеновой поверхностью на 7 — 10 мм (раствор 2 — 5 мм + толщина плитки 5 мм).
- Формируют отверстие под кожух, заводят в него провода, но сам подрозетник не крепят, а монтируют точно по краям после облицовки или штукатурки.
Используют для работы твердосплавные сверлильные коронки (10% кобальта, 90% вольфрама). Такой инструмент работает не слишком долго, является отличным вариантом, если нужно сформировать ниши под розетки в одном жилом строении. Армированных участков лучше избегать, чтобы не повредить напайки. Карбидо-вольфрамовые насадки прочные, выдерживают сверление непосредственно в керамической плитке.
Установка подрозетников в бетон, гипокартон и дерево.
Перед установкой подрозетника (монтажной коробки) нужно в первую очередь подготовить необходимый инструмент и материалы. Если уже проложен провод, он должен быть обесточен или заизолирован.
Установка подрозетников в бетон
Начинаем с разметки. Как правило, розетки располагают на расстоянии 25-30 см от пола, выключатели примерно 90 см от пола. Если розетка устанавливается над рабочей поверхностью кухни, то её расположение должно быть на расстоянии 15-20 см от столешницы.
После того, как расположение электроточки определено, с помощью пузырькового уровня чертим на стене горизонтальную линию и отмечаем на ней расстояние между подрозетниками. Для этого нужно отметить две точки на линии, которые будут центрами будущих углублений. Расстояние между точками 71 мм . Для бурения углублений используется специальная коронка для подрозетников с зубьями из твёрдого сплава. Диаметр коронки по бетону для подрозетника примерно 85 мм. Чтобы ускорить процесс и обеспечить более точное вхождение коронки, предварительно делаем отверстия с помощью перфоратора и бура
диаметром равным диаметру сверла в коронке. От вибрации очень часто у коронки откручивается прижимной болт для сверла. Чтобы этого не происходило, его можно зафиксировать с помощью изоленты. Если Вам нужно пробурить большое количество углублений, лучше использовать мощный перфоратор (лучше SDSmax). Можно использовать и безударное сверление. Для безударного сверления используют алмазные коронки сухого сверления и мощную высоко-оборотистую дрель, желательно от 1.5 кВт и от 3000 об/мин без нагрузки. Диаметры коротких коронок, выпускаемых для сверления отверстий под подрозетники: 68 и 82 мм. Преимущества безударного сверления: малый уровень шума и вибрации, высокая производительность, способность резать армированный бетон. Недостаток такого способа – дороговизна.
После работы коронки, с помощью зубила и молотка или перфоратора с зубилом убираем бетон из углублений. Проверяем, чтобы подрозетники свободно входили в углубления. Для лучшего сцепления строительного гипса и бетона углубления обрабатываем грунтовкой. Можно просто смочить водой. Теперь углубления готовы для установки подрозетников.
Так выглядит подрозетник и соединитель. В продаже существует огромный ассортимент подрозетников: с соединителями и без, округлой и квадратной формы, для установки в гипсокартон и бетонные стены. Перед монтажом необходимо вырезать в подрозетниках отверстия для провода.
Теперь нужно приготовить строительный гипс. Для этого разводим его водой так, чтобы смесь была похожа на густую сметану. Заполняем углубления гипсом примерно на одну треть и размещаем коробки, вдавливая их в раствор заподлицо с поверхностью стены или чуть утопив. Край подрозетника ни в коем случае не должен выступать за поверхность стены. Проверяем положение подрозетников по горизонту, ориентируясь на, ранее сделанную на стене, разметку. С выравниванием подрозетников лучше поторопиться, так как гипс схватывается очень быстро. После частичного схватывания, шпателем, как скребком убираем лишний раствор с поверхности стены и чистим подрозетники от попавшего через щели гипса.
Всё, подрозетники установлены. В стене из кирпича, шлакоблоков, гипсовых плит и газобетона коробки монтируются аналогично.
Установка подрозетников в гипсокартон
В стену из гипсокартона монтаж подрозетников гораздо проще. Для этого существуют специальные подрозетники с «лапками» прижимающими его к листу гипсокартона
с обратной стороны. На стене делается разметка аналогичная предыдущей, с помощью обычной дрели и коронки для гипсокартона делается отверстие. В случае установки двух и более розеток в блоке, расстояние между центрами так же должно составлять 71 мм, только диаметр коронки должен быть равен диаметру подрозетника — 68 мм. Ещё нужно обратить внимание на расстояние между основной стеной и стеной из гипсокартона, чтобы хватило глубины для установки коробки, в противном случае основную стену придётся поддалбливать с помощью перфоратора или зубила. Если гипсокартон смонтирован в два слоя на профиль 60×27 мм, проблем с глубиной возникнуть не должно. Глубина коробки составляет 47 мм.
Также посмотрите видео про установку подрозетников в гипсокартон:
Установка подрозетников в старом фонде
Теперь рассмотрим сложный случай. Старый фонд с деревянными оштукатуренными перегородками. В таких стенах даже кабель в гофрированной трубке не уложить, толщины штукатурки не хватит, придётся убирать дранку и выпиливать в доске штробу. Для кабеля это конечно не обязательно, его можно и так уложить, а вот коробку для розетки или выключателя всё равно придётся утапливать.
Помочь нам в этом может коронка по дереву и дрель. Цена такого набора коронок невысокая и продаётся она почти в любом строительном магазине. Дрель лучше всего использовать с низкими оборотами с дополнительной рукояткой, это так называемая сверлильная машина. Такие дрели ещё используют с миксером для размешивания растворов. Но можно обойтись и обычной дрелью.
Перед началом работы в месте установки удаляем штукатурку и делаем разметку, как в примере с бетонной и стеной. Дрелью с коронкой сверлим углубление. С помощью стамески и молотка выдалбливаем сердцевину углубления. Если для подрозетника не хватает глубины, повторяем эту процедуру. Углубление делаем немного глубже подрозетника, примерно на 5 мм.
Готовим раствор строительного гипса. Затем шпателем наносим его на заднюю часть монтажных коробок и монтируем их в углубления заподлицо с поверхностью стены. Выравниваем по горизонтали и ждём, когда схватится гипс. После этого, саморезами по дереву прочно крепим их к стене и заштукатуриваем пространство между подрозетниками и стеной.
И наконец, последнее. Если розетки и выключатели устанавливаются во влажных помещениях, без гидроизоляции стен, или вне помещения, вместо гипса желательно использовать ремсостав на цементно-песчаной основе.
Диаметр подрозетника и другие параметры: глубина, межосевое расстояние
Такое понятие как диаметр подрозетника не совсем правильное, когда речь идет именно про монтаж. Если размеры розетки и подрозетника подходят друг к другу, то высчитывать надо диаметр отверстия, которое необходимо высверлить в стене. Здесь уже надо смотреть на ее материал (к примеру, есть много нюансов при монтажу на керамическую плитку), какое будет установлено количество розеток и насколько близко они будут располагаться друг к другу.
Стандартные размеры подрозетников
Обычный подрозетник имеет размер 68 мм на 45 мм, где 68 — диаметр, а 45 — его глубина. При установке блоком расстояние между центрами высверливаемых отверстий — 71 мм.
Стандартные размеры подрозетников
Технические требования к монтажным коробкам
Какие-то отдельные нормы и правила для подрозетников, кроме тех, что определены в ПУЭ, отсутствуют, указывается лишь, как правильно установить розетку. Поэтому установка монтажных изделий осуществляется по таким же схемам, как и для распределительных коробок. Рекомендуется учитывать расстояния в помещениях относительно конструктивных элементов, установленных СНИПами, с учетом реальных условий эксплуатации.
В целом, технические требования, предъявляемые к установочным коробкам, затрагивают следующие стороны:
- Достаточная прочность материала, его способность выдерживать определенные нагрузки при регулярных выключениях вилок из розеток. Корпус сначала вставляем, а затем прочно закрепляем в стене, после чего он удерживается сам и удерживает розетку, не боясь нагрузок. Подобный эффект достигается наличием ребер и пазов, расположенных с внешней стороны корпуса.
- Для фиксации коробки используются пастообразные растворы – алебастр, гипс и т.д. Каждый из них целиком заполняет все пазы и щели, а после высыхания надежно удерживает подрозетник в посадочном месте.
- Пластик, применяемый для изготовления, должен быть не только прочным и огнеупорным. Он обладает диэлектрическими свойствами, не подвержен разрушительному воздействию влаги и агрессивной среды.
- Современные подрозетники имеют специальные отверстия, предназначенные для винтовых креплений. В новых моделях предусмотрена возможность соединения нескольких коробок, скрепляемых между собой фиксаторами.
Таким образом, может быть собрана конструкция и выполнен монтаж подрозетников под любое количество розеток, запроектированное в данной сети.
Монтаж одиночного подрозетника
Для того чтобы закрепить одну коробку в стене потребуется:
- Уровень,
- Карандаш, кисточка/пульверизатор, маленький шпатель,
- Зубило,
- Молоток,
- Дрель с круглой насадкой, имеющая диаметр 68 мм,
- Алебастр, вода.
Для начала отмечаем по горизонтальному уровню линию, затем от провода вниз чертим еще одну, это будет левая крайняя точка подрозетника. Ориентируясь на вертикальную полоску, горизонтальную линию, обводим заднюю часть элемента, для ориентира.
Диаметр обода 68 мм,установочная внешняя глубина 45 мм, это следует учесть при выборе насадки. Делаем метки, по ним просверливаем отверстия, смачивая насадку водой, чтобы она не перегревалась.
В коробке есть 2 стороны: одна немного уже второй, устанавливаем широкой частью по горизонтали, узкой – по вертикали, иначе коробка может не влезть. Также удаляются «ушки» переходы для монтажа блока подрозетников, они абсолютно не нужны при монтаже одиночного элемента. Если мы их не удалим, коробка не войдет в отверстие и нам придется его расширять.
Мы отметили линию вниз от провода, это наш левый край. Нам необходимо, чтобы провод зашел в диагональное отверстие, не в прямое, а диагональное, потому, что винт для крепления расположен прямо над вертикальным отверстием, он повреждает провод.
После того как мы примеряли подрозетник, убедились что диаметр подходит, нам осталось смочить отверстие и наш элемент для крепления розеток водой, чтобы алебастр лучше держался. Мешаем алебастр с водой в пропорции 1:4, где одна часть воды и четыре алебастра и наносим его на стенку, боковые грани, на дно подрозетника, примыкающее к поверхности.
После установки коробку нужно поправить, добиться строго одного уровня со стеной, чтобы она не выпирала и не была глубоко посажена, все крайние точки имели одинаковое расстояние до стены. Весь лишний алебастр использовать на маскирование провода, идущего к будущей розетке.
Советы
Для того, чтобы процесс монтажа подрозетника в бетонную стену прошел наиболее успешно и не возникли непредвиденные ситуации, квалифицированные мастера по вопросам ремонта дают следующие рекомендации:
- Все работы по высверливанию отверстия для установочной коробки лучше всего проводить до оклейки стен обоями, иначе возникает большая вероятность повредить их структуру, что повлечет необходимость повторного ремонта.
- Выбор коронки необходимо осуществлять исходя из предполагаемого объема работ. Если планируется монтаж одного или двух подрозетников, то покупка дорогой модели будет бессмысленной тратой финансовых средств.
- При подготовке смеси необходимо следить за ее структурой – она не должна быть очень густой, иначе раствор не сможет проникнуть по все щели и отверстия, что не обеспечит достаточной надежности фиксации подрозетника.
Самостоятельный монтаж установочной коробки позволяет сэкономить денежные средства на вызове электрика и оплате его работы. При этом, сам процесс является простым и доступным каждому человеку, если соблюдать все приведенные условия монтажа.
Монтаж нового подрозетника в старый
Часто случается так, что старый, советский металлический подрозетник имеет диаметр больше чем нужно, новые розетки сидят в нем неплотно, болтаются, несмотря на максимально широкий размер между лапками.
Работы нужно совершать в следующем порядке:
- Выключаем свет в щитке.
- Проверяем отсутствие напряжения включением лампочки.
- Снимаем крышку, выкручиваем розетку.
- Отсоединяем провода.
- Смотрим на коробку, если она железная ржавая, без дна, тогда нам понадобится алебастр, чтобы прочно закрепить новую коробку.
Если коробка держится надежно, не вызывает сомнений, у нее есть стенка, тогда можно просто прикрутить новую коробку, к задней стенке старой, с помощью самореза по металлу с буром. Не стоит забывать о расположении коробки узкой частью вертикально, широкой – горизонтально.
Нужно помнить и о проводе, если встарой он идет по центру, тогда следует очень аккуратно закручивать винты, чтобы было оптимальное расстояние и допустимая глубина закручивания шурупов. Если есть возможность, то желательно сточить кончик, чтобы он имел некое расстояние до провода, или был, по крайней мере, неострый, иначе повреждение чревато коротким замыканием.
Подготовка стен
Осуществлять отделку данных поверхностей гипсокартоном многие люди начали массово, поскольку в таком случае удается заметно ускорить проведение ремонтных работ, а также придать им ровности без использования сыпучих материалов, которых при существенных дефектах стен в старых зданиях потребуется задействовать значительное количество.
Произвести монтаж гипсокартонных листов можно на профиль, что имеет ширину в 5 см, оставляя за собой достаточное пространство для дальнейшего помещения утеплителя, звукоизоляции и проводов. При проведении данных работ также возникает потребность в установке подрозетников.
Обратите внимание! Плохо разбираясь в электрике лучше всего прибегнуть к услугам специалистов, которые сумеют качественно проложить электрические кабели, поскольку допущенные в ходе самостоятельной прокладки ошибки могут в будущем стать причиной короткого замыкания, способного привести к возгоранию. Осуществлять приобретение подрозетников желательно вместе с гипсокартоном, так как в этом случае удастся сэкономить значительное количество времени, выполнив подбор подходящих монтажных коробок
Осуществлять приобретение подрозетников желательно вместе с гипсокартоном, так как в этом случае удастся сэкономить значительное количество времени, выполнив подбор подходящих монтажных коробок.
Обыкновенные гипсокартонные листы с легкостью воспламеняются при пожаре. Исключением является лишь пожароустойчивый материал, который в основном имеет розовый или красный окрас и специальную маркировку
По этой причине при приобретении подрозетников также требуется обращать внимание на их пожарные нормы безопасности
Важно! При выборе розеток для установки в гипсокартонных конструкциях необходимо рассматривать лишь те изделия, у которых ободок выполнен из металла, что при чересчур высоком напряжении обеспечит прохождение тока через себя и срабатывание защиты предохранителя в щитке. Помимо этого произойдет отключение электричества, что исключит вероятность возможных отрицательных последствий
Чтобы все же произвести качественный монтаж подрозетника в гипсокартоне требуется осуществить подготовку стен должным образом:
- В первую очередь рекомендуется совершить нанесение шпаклевки, благодаря которой поверхность становится более прочной и начинает отлично удерживать форму во время сверления.
- Далее по окончании застывания шпаклевочного состава необходимо тщательно вскрыть материал грунтовкой. После впитывания нанесенной смеси гипсокартон перестанет крошиться при дальнейшей обработке.
Осуществив указанные действия можно приступать к определению будущих мест монтажных коробок.
Установка блока подрозетников
Для того, чтобы установить сразу блок подрозетников, нам понадобится тот же инструмент и еще более широкая коронка на дрель, диаметр которой 70 – 80мм, если он идет с четырьмя коробками тогда диаметр лучше выбрать на 80.
Размечаем справа от линии, чтобы он вошел в диагональное отверстие, это и экономит время, и шнур фактически не сгибается, не повреждается шурупами. Если блок готовый, тогда там отмерено уже готовое расстояние между коробками, если нет, то нам следует отмерить это вручную.
Отмеряем горизонталь тщательно, на блоке это будет очень хорошо видно невооруженным глазом, после чего также обводим блок, главное, чтобы межосевое расстояние между центрами было не менее 71 мм, это можно сделать и вручную, без обвода.
Затем сверлим отверстия, вынимаем остатки цемента и кладки, выбываем перегородки, заводим провод в элемент, меряем, чтобы он был строго по горизонтали. На блоке этого сложнее добиться, поэтому сверлим с запасом, и большей коронкой, диаметр которой 70-80 мм.
На блоке узкая часть уже установлена вертикально, и специальные переходы между подрозетниками выполняют свою работу. В одиночном они удаляются, чтоб занимать меньше пространства.
Кто поддерживает горение а кто нет?
Все «подопытные» произведены в России или в Украине. А как известно пластик у нас может быть самый разный, и результат непредсказуемый. Я сымитирую нагрев проводки и возгорание.
Для этого достаточно сначала их слегка разогреть и посмотреть, как они себя будут вести под нагревом. А потом подвергнуть их открытому огню. Равномерно прогрев их горелкой буквально 20 секунд, пластик всех корпусов начал плавиться. А еще через 20 секунд легко загорелся.
Горят абсолютно всё. И горят и распространяют огонь прекрасно. Никакие они не самозатухающие. И даже Schneider и Legrand горит. Есть у вас проводка начнет греться, разогреет пластик до возгорания, они прекрасно будут его поддерживать…
Единственное что положительно влияет на время выгорания, так это толщина пластиковой стенки. Те что подороже и потолще – воспламеняются позже остальных и горят дольше. А то что не распространяет горение – не правда. Удивили меня наши производители. Всё горит почти одинаково. Нет никакой разницы.
Остается надеяться что у Вас качественная автоматика, которая сработает раньше, чем прогреется подрозетник до воспламенения. Тут конечно лучше взять толстостенные модели.
Важно: никаких едких запахов при горении не выделяется. Всё горит без запаха. И это еще хуже, т.к. если дело дойдет до пожара – услышать (унюхать) очаг вы сможете уже после того как огонь распространится за пределы розетки.
Монтаж на прочие поверхности
В гипсокартоне задача упрощается, потому что нет необходимости в алебастре. Нужно проделать те же операции, разметка, вырезание определенного размера отверстия, соответствующего с подрозетником, фиксация.
Фиксация коробки в гипсокартоне происходит за счет специальных крепежных лапок, которые прижимаются к гипсокартону при закручивании. Он называется универсальным, его можно крепить к различным тонкостенным поверхностям, в которые входит гипсокартон.
Если коробка, несмотря на плотную фиксацию, сильно выпирает, необходимо снять толщину, и сделать кромки отверстия в гипсокартоне под углом.
Универсальный подрозетник имеет большие размеры, потому что расстояние между лапками составляет 83 мм, что удобно, если у нас имеется розетка либо нестандартный выключатель, у которого расстояние между креплением может быть немного больше.
Аналогично по дереву, если это тонкая деревянная перегородка, но если дом со сруба, тогда возможен вариант прикручивания стенки коробки к срубу на саморезы.
Если куплен универсальный подрозетник для кирпичной стены либо сруба, тогда лапки необходимо выкрутить.
Отверстия в одиночном подрозетнике лучше сделать разогретым ножом, во избежание поломки корпуса. При этом нужно иметь безопасное расстояние от гипсокартона и дерева.
При монтаже на поверхность, которая будет штукатуриться, либо на нее будет ложиться плитка, нет необходимости сверлить отверстия на всю глубину. Следует сделать подрозетник немного выступающим, на 5-7 мм, либо меньше, в зависимости от толщины штукатурки/плитки.
При выборе важно учитывать, что размер глубины розетки может отличаться от глубины подрозетника, также как и диаметр.
Виды
Для правильной работы с бетоном или другим обрабатываемым материалом нужно подобрать соответствующий тип инструмента. При выборе коронки нужно учесть такие условия:
- свойства просверливаемого материала;
- мощность дрели;
- условия работы.
Твердосплавная
Коронки для подрозетников с твердосплавными насадками (наплавками) используются наиболее часто. Они стоят дешевле, чем другие коронки и используются для сверления в обычных условиях, в быту для личного использования.
Такая коронка создана путем нанесения на режущую поверхность инструмента напайки из прочного сплава. Особенностью таких сверл является то, что напайки вылетают во время сверления при попадании в арматуру. Потому для участков бетона с армированием они не подходят.
Алмазная
Прочность такой коронки схожа с алмазным кругом — она так же хорошо режет бетон. Такое изделие наиболее эффективно для сверления бетона, железобетона. Качественный инструмент такого типа имеет высокую цену, но это оправдывается долговечностью, экономией трудозатрат и времени. Такая коронка идеально подходит для выполнения большого объема работ.
Режущая поверхность указанного инструмента имеет напыление из технических алмазов и способна прорезать арматуру. Она подходит для работ на очень сложных участках. При работе с ней все же рекомендуют избегать участков с металлом – это продлит ее трудоспособность.
Карбидо-вольфрамовые
Коронки для подрозетников с карбидо-вольфрамным напылением используют для сверления керамической плитки кроме бетона, камня и кирпича. Этот тип инструмента очень удобен для работы с различными материалами одновременно: его не нужно менять и можно переходить сразу, например, от сверления бетона к созданию отверстий в керамической плитке, а потом к работе с кирпичом или камнем.
Карбидо-вольфрамовая коронка имеет шестигранный хвостовик, он служит для сверления обычной дрелью. Ее мощность должна быть 800 Вт или больше. Единственный существенный недостаток — этот вид коронки выходит из строя при попадании на арматурные стержни или металлические элементы.
Расположение провода в подрозетнике
Конечно, многие не делают на этом особого акцента, но это весьма немаловажная деталь, ведь после каждой замены розетки, выключателя, в коробке, подрозетнике есть вероятность облома кончика провода, либо удаление его и зачистка.
Многие настаивают на том, чтоб запас провода в подрозетнике был 20 см, хуже, если не менее 10 см, но размер провода будет со временем уменьшаться. В худшем случае, при ошибке строителей их наращивают сразу в подрозетнике, такие места окисляются, искрят, и являются у многих проблемным местом.
Провод нужно аккуратно сложить либо по спирали, имеющей большой диаметр, либо с плавным изгибом, ни в коем случае, не допуская резкого изгиба, либо перелома. Такую ошибку делают зачастую неопытные хозяева домов, когда провода укладывают на скорую руку, с надеждой нескоро вновь разбирать розетку.
Так делать не желательно, ведь мы не сможем подтянуть нехватающую длину из штукатурки, нужно стараться делать изгиб менее резким. Особо осторожно следует вести себя со старыми проводами, которым более 20 лет.
Дополнительный видео-инструктаж
Вдоволь налюбовавшись результатом своего труда, можно приступать к подключению механизма розетки. Укрепить его в подрозетнике можно либо посредством раздвижных лапок, либо простыми шурупами, для ввинчивания которых на стенках коробки имеются резьбовые отверстия. Неопытным домашним электрикам лучше воспользоваться шурупами, т. к. фиксация лапками не слишком надежна и может разочаровать азимутальным перекосом. Значит, прикрепим винтами, закроем сверху декоративной крышкой и будем с удовольствием пользоваться установленной собственными силами электрической точкой.
Установка пластиковых окон своими руками — пошаговая технология монтажа в фотографиях
Газовые печи для бань: учимся правильно выбирать + правила самостоятельного монтажа
Установка счетчика электроэнергии: правила и тонкости электромонтажа
диаметр, глубина, расстояние между центрами
Стандартные размеры подрозетников
Обычный подрозетник имеет размер 68 мм на 45 мм, где 68 — диаметр, а 45 — его глубина. При установке блоком расстояние между центрами высверливаемых отверстий — 71 мм.
Стандартные размеры подрозетников
Диаметр
Для круглых коробов под бетон производители разработали иную систему классификации:
- Диаметр подрозетника. Обозначается буквой D.
Самые ходовые параметры: 60, 64, 65, 68, 70 и 75 мм. Чтобы розетка или выключатель идеально поместились внутри кожуха, у них должен быть аналогичный диаметр механизма.
- Глубина. Обозначается буквой H. Типичные размеры: 40, 42, 45, 60 и 62 мм. Бывают изделия с глубиной до 80 мм. Они нужны для внутреннего размещения клеммных колодок, если проводка не оборудована распаечными коробками.
При монтаже овальных и составных подрозетников необходимо учитывать такой параметр, как межцентровое расстояние — «дистанция» между центрами осей.
Это расстояние, которое нужно отсчитать между отверстиями под сверление при установке коробки. По стандарту оно равняется 71 мм, но некоторые в большую или меньшую стороны.
Монтаж одиночного подрозетника
Для того чтобы закрепить одну коробку в стене потребуется:
- Уровень,
- Карандаш, кисточка/пульверизатор, маленький шпатель,
- Зубило,
- Молоток,
- Дрель с круглой насадкой, имеющая диаметр 68 мм,
- Алебастр, вода.
Для начала отмечаем по горизонтальному уровню линию, затем от провода вниз чертим еще одну, это будет левая крайняя точка подрозетника. Ориентируясь на вертикальную полоску, горизонтальную линию, обводим заднюю часть элемента, для ориентира.
Диаметр обода 68 мм,установочная внешняя глубина 45 мм, это следует учесть при выборе насадки. Делаем метки, по ним просверливаем отверстия, смачивая насадку водой, чтобы она не перегревалась.
В коробке есть 2 стороны: одна немного уже второй, устанавливаем широкой частью по горизонтали, узкой – по вертикали, иначе коробка может не влезть. Также удаляются «ушки» переходы для монтажа блока подрозетников, они абсолютно не нужны при монтаже одиночного элемента. Если мы их не удалим, коробка не войдет в отверстие и нам придется его расширять.
Мы отметили линию вниз от провода, это наш левый край. Нам необходимо, чтобы провод зашел в диагональное отверстие, не в прямое, а диагональное, потому, что винт для крепления расположен прямо над вертикальным отверстием, он повреждает провод.
После того как мы примеряли подрозетник, убедились что диаметр подходит, нам осталось смочить отверстие и наш элемент для крепления розеток водой, чтобы алебастр лучше держался. Мешаем алебастр с водой в пропорции 1:4, где одна часть воды и четыре алебастра и наносим его на стенку, боковые грани, на дно подрозетника, примыкающее к поверхности.
После установки коробку нужно поправить, добиться строго одного уровня со стеной, чтобы она не выпирала и не была глубоко посажена, все крайние точки имели одинаковое расстояние до стены. Весь лишний алебастр использовать на маскирование провода, идущего к будущей розетке.
Заготовка раствора и установка в нишу
Следующий этап — установка самих подрозетников в подготовленные ниши. Устанавливать подрозетники можно на алебастр, шпаклевку или гипс.
Время застывания гипса примерно четыре-пять минут. Конечно, за 5 минут закончить работу по установке не проблема. Главная головная боль – это застывание приготовленного раствора в разведенной емкости и невозможность ее использования для других работ.
Поэтому, чтобы гипс не застывал слишком быстро, можно подмешать в него штукатурку (Rotband). Выиграете лишние 10-20 минут. На 3 части гипса добавляйте 2 части шпатлевки.
Просто штукатурка держит гораздо слабее. При застывании цементный раствор дает усадку, а гипс наоборот, немного расширяется и надежно со всех сторон зажимает подрозетник в нише.
Для того чтобы алебастр, гипс прочнее пристал, нишу необходимо увлажнить. Используйте опрыскиватель или брызкалку.
Далее подготавливаются подрозетники. Если они блочного типа, то собираются в блок (2шт и более). Срезается заглушка для входа провода.
Кстати штробу под провод лучше всего делать не по центру, а левее или правее отверстия в стене.
Так как выходное отверстие в самом подрозетнике находится сбоку.
Раствор закидывается в просверленное отверстие ниши.
В нишу вставляется подрозетник.
Все затирается шпателем и снаружи убираются остатки раствора.
Основная задача — выровнять и зафиксировать подрозетник на своем месте. Обратите внимание на то, чтобы его края не выступали из стены.
Как только раствор схватится, можно удалить все лишнее изнутри.
После отделочных работ устанавливаются сами розетки. В этой казалось бы простой работе, также есть свои правила и ошибки, которые могут привести к непоправимым последствиям.
Монтаж нового подрозетника в старый
Часто случается так, что старый, советский металлический подрозетник имеет диаметр больше чем нужно, новые розетки сидят в нем неплотно, болтаются, несмотря на максимально широкий размер между лапками.
Работы нужно совершать в следующем порядке:
- Выключаем свет в щитке.
- Проверяем отсутствие напряжения включением лампочки.
- Снимаем крышку, выкручиваем розетку.
- Отсоединяем провода.
- Смотрим на коробку, если она железная ржавая, без дна, тогда нам понадобится алебастр, чтобы прочно закрепить новую коробку.
Если коробка держится надежно, не вызывает сомнений, у нее есть стенка, тогда можно просто прикрутить новую коробку, к задней стенке старой, с помощью самореза по металлу с буром. Не стоит забывать о расположении коробки узкой частью вертикально, широкой – горизонтально.
Нужно помнить и о проводе, если встарой он идет по центру, тогда следует очень аккуратно закручивать винты, чтобы было оптимальное расстояние и допустимая глубина закручивания шурупов. Если есть возможность, то желательно сточить кончик, чтобы он имел некое расстояние до провода, или был, по крайней мере, неострый, иначе повреждение чревато коротким замыканием.
Подрозетник выскочил из стены
Фиксирующий раствор рассыпался, что привело к выпадению подрозетника
Случается такое, что установочный стакан выпадает из панели. Это происходит по следующим причинам:
- Старая конструкция проводки и давно проведенный ремонт. Вполне вероятно, что фиксирующий раствор просто рассыпался под обоями или другой отделкой.
- Неправильно взятые пропорции воды и порошка для приготовления строительной смеси. В этом случае она недостаточно крепко держит стакан.
Чтобы исправить ситуацию, нужно оценить масштаб проблемы. Если гнездо под подрозетник деформировано сильно, его смещают в сторону и делают новое. Старую лунку замазывают штукатуркой. Установку нового стакана выполняют по приведённому выше алгоритму.
Если речь идет о неправильно приготовленном растворе, его полностью выбирают из гнезда. Готовят новую смесь и устанавливают подрозетник.
Установка блока подрозетников
Для того, чтобы установить сразу блок подрозетников, нам понадобится тот же инструмент и еще более широкая коронка на дрель, диаметр которой 70 – 80мм, если он идет с четырьмя коробками тогда диаметр лучше выбрать на 80.
Размечаем справа от линии, чтобы он вошел в диагональное отверстие, это и экономит время, и шнур фактически не сгибается, не повреждается шурупами. Если блок готовый, тогда там отмерено уже готовое расстояние между коробками, если нет, то нам следует отмерить это вручную.
Отмеряем горизонталь тщательно, на блоке это будет очень хорошо видно невооруженным глазом, после чего также обводим блок, главное, чтобы межосевое расстояние между центрами было не менее 71 мм, это можно сделать и вручную, без обвода.
Затем сверлим отверстия, вынимаем остатки цемента и кладки, выбываем перегородки, заводим провод в элемент, меряем, чтобы он был строго по горизонтали. На блоке этого сложнее добиться, поэтому сверлим с запасом, и большей коронкой, диаметр которой 70-80 мм.
На блоке узкая часть уже установлена вертикально, и специальные переходы между подрозетниками выполняют свою работу. В одиночном они удаляются, чтоб занимать меньше пространства.
Максимальная глубина под подрозетник
Иногда приходится сталкиваться с такой проблемой, когда устройство стены имеет рассыпчатую структуру или многослойную, такие стены могут состоять из:
- гипса и доски;
- глины и деревянных перекрытий;
- кирпича и доски.
Такая структура стены находится чаще всего в старых жилых помещениях, толщина первого слоя стены могла достигать 70 мм, дальше шла кирпичная кладка. Изначально для таких стен предназначалась обычная жестяная банка, с прорезанными отверстиями для проводов, она практически утапливалась в стену, прикреплялась на цементно-известковый раствор.
Монтаж таких подрозетников длился более суток, в силу ожидания того, когда застынет раствор, и подрозетник зафиксируется в цементе. Только после этого розетка крепилась к стене.
Вскоре на замену жестяным банкам пришли пластмассовые коробки для розеток. В настоящее время они наиболее востребованы.
Монтаж на прочие поверхности
В гипсокартоне задача упрощается, потому что нет необходимости в алебастре. Нужно проделать те же операции, разметка, вырезание определенного размера отверстия, соответствующего с подрозетником, фиксация.
Фиксация коробки в гипсокартоне происходит за счет специальных крепежных лапок, которые прижимаются к гипсокартону при закручивании. Он называется универсальным, его можно крепить к различным тонкостенным поверхностям, в которые входит гипсокартон.
Если коробка, несмотря на плотную фиксацию, сильно выпирает, необходимо снять толщину, и сделать кромки отверстия в гипсокартоне под углом.
Универсальный подрозетник имеет большие размеры, потому что расстояние между лапками составляет 83 мм, что удобно, если у нас имеется розетка либо нестандартный выключатель, у которого расстояние между креплением может быть немного больше.
Аналогично по дереву, если это тонкая деревянная перегородка, но если дом со сруба, тогда возможен вариант прикручивания стенки коробки к срубу на саморезы.
Если куплен универсальный подрозетник для кирпичной стены либо сруба, тогда лапки необходимо выкрутить.
Отверстия в одиночном подрозетнике лучше сделать разогретым ножом, во избежание поломки корпуса. При этом нужно иметь безопасное расстояние от гипсокартона и дерева.
При монтаже на поверхность, которая будет штукатуриться, либо на нее будет ложиться плитка, нет необходимости сверлить отверстия на всю глубину. Следует сделать подрозетник немного выступающим, на 5-7 мм, либо меньше, в зависимости от толщины штукатурки/плитки.
При выборе важно учитывать, что размер глубины розетки может отличаться от глубины подрозетника, также как и диаметр.
Виды и характеристики подрозетников
Современные розетки по виду и способу монтажа значительно отличаются от тех, которые устанавливались в домах советской эпохи.
Если раньше они просто вмуровывались в стену без возможности замены, то сегодня и установить их, и при необходимости поменять розетку, не представляет особой сложности.
Подрозетник — монтажное приспособление, предназначенное для надежного закрепления электроустановочных изделий скрытой проводки
Независимо от того, проводится ли установка одиночного или группы подрозетников, перед их монтажом проводится штробление стен
При заглублении в кирпичную или бетонную стену эти монтажные коробки или стаканы закрепляются алебастром
Крепление подрозетника в перегородках и фальш-стенах из гипсокартона производится с помощью регулируемых распорных лапок
Практически все стройматериалы и плитные варианты, используемые в черновой обшивке стен, пригодны для установки в них подрозетников
В линейке изделий для скрытой проводки можно найти варианты для обустройства бревенчатых и брусовых построек
Подрозетники применяются для установки единичных выключателей, силовых точек и блоков розеток
В ходе эксплуатации «расшатавшийся» механизм проще подтянуть в подрозетнике. С его применением быстрее и аккуратней производится установка
Выбираем подрозетник по материалу стен
Основным критерием выбора является материал стен, в которые будет производиться монтаж подрозетников.
По этому признаку существует следующая классификация коробок:
- конструкции, предназначенные для установки в стены, выполненные из твердых материалов: бетона, железобетона, газобетона, кирпича;
- стаканы для стен из композитных материалов: гипсокартона, плит из пластика, ДСП, фанеры и других.
В первом случае подрозетник представляет собой круглый стакан, на котором отсутствуют какие-либо дополнительные элементы. Он фиксируется в стене при помощи строительного раствора.
В его стенках или днище имеются монтажные отверстия для подвода электропроводки. При установке подрозетника, достаточно удалить перемычки и выдавить заглушку.
Подрозетники с боковыми стыковочными узлами позволяют быстро и просто осуществить монтаж сразу двух и более розеток
Для монтажа нескольких, расположенных рядом розеток, можно воспользоваться стаканами, сбоку которых находится крепежный механизм. Подрозетники присоединяются друг к другу с помощью специальных пазов и объединяются в блоки.
В коробках для гипсокартона имеются специальные прижимные пластиковые или металлические лапки, предназначенных для закрепления элементов в полых стенах. Зажимы крепятся на винтах, которые вращаясь, регулируют их положение.
При повороте винта происходит подъем или опускание лапки. Вращение по часовой стрелке приближает прижимной элемент к стене, и закрепляет стакан в гипсокартоне
Какой формы выпускаются изделия?
Наибольшее распространение приобрели подрозетники круглой формы. Для них очень просто сделать отверстие в стене при помощи разнообразных приспособлений.
Круглые стаканы можно использовать как для монтажа одиночной розетки или выключателя, так и объединять их в группы, присоединяя друг к другу посредством стыковочных узлов.
Квадратные коробки хоть используются не так часто, но имеют определенные преимущества. Их объем гораздо больше, благодаря чему в них можно спрятать много проводов.
Зачастую их применяют для монтажа элементов системы «умный дом». Есть одиночные и групповые подрозетники квадратной формы, рассчитанные на установку до пяти розеток.
В продаже встречаются и овальные коробки, которые, так же как и квадратные, имеют большое внутреннее пространство. Они удобны тем, что в них можно сразу подключить двойную розетку. Все описанные выше изделия монтируются в стены и используются для проведения скрытой проводки.
Существует еще один вид монтажных коробок, которые стоят несколько особняком — пластиковые накладки или по-другому мультибоксы, предназначенные для открытой установки на плинтус. Они рассчитаны для одной или нескольких розеток и обычно имеют квадратную форму.
Такой тип установки пластиковых накладок может применяться только на разборных плинтусах из пластика
Наружные подрозетники имеют две модификации — конструкции с установкой до середины плинтуса или до пола. Поскольку мультибоксы монтируются сверху плинтуса, их отличительной особенностью является эстетическая привлекательность и оригинальный дизайн.
Размер установочных коробок
Важным параметром подрозетников являются их размеры, которые подбираются исходя из конкретных условий установки. Вилка размеров по диаметру составляет 60-70 мм, по глубине — 25-80 мм.
Стандартные конструкции имеют внешние габариты 45 х 68 мм, при этом нужно учитывать, что внутренняя глубина в этом случае будет 40, а диаметр 65 мм.
При групповой установке нескольких круглых подрозетников, один из них, имеющий увеличенную глубину, может помимо своего основного предназначения, служить в качестве распределительной коробки
Стаканы увеличенных размеров, глубина которых составляет порядка 80 мм, целесообразно применять тогда, когда в электропроводке отсутствует распределительная коробка, а ее функции выполняет сам подрозетник. Что касается квадратных изделий, то, как правило, они имеют размер 70х70 или 60х60 мм.
Материал изготовления монтажных коробок
Самыми популярными являются подрозетники, изготовленные из негорючего пластика. Их можно устанавливать в бетонные стены и конструкции из композитных материалов.
Существуют также металлические коробки, которые в прежние времена применялись повсеместно, но сегодня их практически вытеснили пластиковые изделия.
Подрозетники из металла устанавливаются, как правило, при монтаже электрической проводки в деревянных домах. Они изготавливаются из оцинкованного или цветного металла и не поддаются сварке, поэтому соединение с металлической трубой производится методом пайки.
В целях безопасности и предупреждения возгорания, при монтаже электропроводки в деревянных домах необходимо использовать металлические подрозетники
Расположение провода в подрозетнике
Конечно, многие не делают на этом особого акцента, но это весьма немаловажная деталь, ведь после каждой замены розетки, выключателя, в коробке, подрозетнике есть вероятность облома кончика провода, либо удаление его и зачистка.
Многие настаивают на том, чтоб запас провода в подрозетнике был 20 см, хуже, если не менее 10 см, но размер провода будет со временем уменьшаться. В худшем случае, при ошибке строителей их наращивают сразу в подрозетнике, такие места окисляются, искрят, и являются у многих проблемным местом.
Провод нужно аккуратно сложить либо по спирали, имеющей большой диаметр, либо с плавным изгибом, ни в коем случае, не допуская резкого изгиба, либо перелома. Такую ошибку делают зачастую неопытные хозяева домов, когда провода укладывают на скорую руку, с надеждой нескоро вновь разбирать розетку.
Так делать не желательно, ведь мы не сможем подтянуть нехватающую длину из штукатурки, нужно стараться делать изгиб менее резким. Особо осторожно следует вести себя со старыми проводами, которым более 20 лет.
Правильный выбор подрозетника для бетонных стен
Стакан рядного типа
Если мастер не знает, какой подрозетник лучше для бетонной стены, стоит учитывать такие критерии:
- Толщина стенок стакана. Чем она больше, тем крепче изделие. К тому же, хоть производители и уверяют в пожаробезопасности полимера подрозетника, при сильном возгорании он начнет плавиться.
И тем быстрее, чем тоньше будут его стенки.
- Глубина изделия. Особенно актуален этот параметр, если монтаж подрозетников выполняется в одну стену с двух ее сторон (как в старых панельных домах). Тут лучше купить два изделия по 25 мм и состыковать их, чем прибегать к обрезке коробки, которая будет отличаться по глубине.
- Тип конструкции (одинарный, двойной, блочный). Если нужно смонтировать подряд несколько розеток, можно купить рядные стаканы. Они просто разламываются в месте стыкования. Так можно взять сразу столько штук, сколько нужно.
Для установки подрозетника в гипсокартон нужно брать стакан с фиксирующими лапками. Его крепят просто методом вгона в гнездо. Лапки сами защелкиваются с обратной стороны панели.
Диаметр подрозетника: размеры, глубина, межосевое расстояние
В современной электротехнике широко применяются монтажные или установочные коробки, известные также как подрозетников. Внутри них закрепляется механизм розетки, когда прокладывается скрытая проводка. Чаще всего они выпускаются круглыми с определенной линейкой стандартных размеров. Большое значение имеет диаметр подрозетника, от которого зависит жесткость и надежность крепления внутри стены. Данный параметр привязан не только к розетке, но и к монтажному отверстию, куда он будет установлен.
Содержание
Для чего нужны подрозетники
Поскольку коробки устанавливаются внутрь стены в отверстие под подрозетник. Поэтому многие не знают, что делать с этими изделиями, а иногда даже не подозревают о их существовании. Тем не менее, это наилучшее решение для скрытой электропроводки, без которого невозможен монтаж современных розеток и выключателей. Благодаря несложной конструкции, монтажную коробку вполне возможно установить собственными силами, без привлечения квалифицированных специалистов.
Конфигурация подрозетника выглядит как пластиковый или металлический стакан, устанавливаемый в отверстие, заранее просверленное в стене. Внутри него располагается механизм розетки или выключателя. Сверху закрепляется декоративные рамки, какие делают всю конструкцию невидимой. Для сверления отверстий применяются коронки для подрозетников.
Нередко у хозяев возникает вопрос о возможности как-то делать монтаж без таких коробок и устанавливать механизмы коммутационных приборов напрямую в стену. Чтобы раз и навсегда решить эту проблему, необходимо более подробно рассмотреть основные функции подрозетника и для чего он нужен:
- Гарантируют надежную фиксацию механизмов внутри коробки. Это особенно актуально для группы розеток, их которых регулярно вытаскиваются вилки бытовых устройств. Крепление осуществляется распорными лапками механизмов или с помощью специальных винтов, находящихся в самом подрозетнике.
- Диэлектрическая функция. Пластик обеспечивает надежную изоляцию контактов розетки с материалом стены. В бетоне имеются металлические конструкции, соприкосновение с которыми может вызвать токовые утечки или короткие замыкания.
- Противопожарная функция. Коробки, изготовленные из металла или негорючего пластика, защищают от возгораний, если сделан правильный выбор.
- Нередко подрозетники исполняют роль распределительных коробок, если они не предусмотрены схемой электропроводки.
И, наконец, следует отметить, что экономия на подрозетниках весьма сомнительная, поскольку эти изделия стоят недорого.
Разновидности и классификация
Подрозетники выпускаются в широком ассортименте, включающем в себя большое количество моделей и модификаций, в том числе и углублённый вариант. Человеку, впервые столкнувшемуся с такими изделиями, сложно сразу разрешить проблему, как выбрать подрозетник.
При более внимательном рассмотрении, оказывается, что все виды подрозетников классифицируются всего лишь по нескольким признакам – по материалу, конструкции и размерам. Кроме того, они отличаются цветовой гаммой и дизайнерскими решениями, которые никак не влияют на функциональность коробок.
Наиболее распространенным материалом для изготовления подрозетников, является прочный негорючий пластик. За счет этих качеств монтажные коробки могут устанавливаться в отверстия для подрозетников в гипсокартоне и даже в деревянные конструкции. Они часто используются совместно с такими отделочными материалами, как фанера, ДСП, ДВП, вагонка и другими декорами.
Качественный пластик постепенно вытеснил модели из металла, проводящие электричество. Благодаря этому снизилась вероятность коротких замыканий. Однако металлические подрозетники должно быть очень хорошо зарекомендовали себя в деревянных домах, если они до сих пор применяются на подобных объектах.
Существуют разновидности моделей, которые выбираются по конфигурации и особенностям конструкции. Тем не менее, все типы изделий напоминают стакан цилиндрической формы, закрепляемый в стене раствором из строительного гипса или алебастра. При монтаже по бетону используются модели, не оборудованные дополнительным крепежом. Изделия с крепежными планками применяются в более мягких и пустотелых стенах, где требуется делать надежную фиксацию.
Некоторые модификации коробок для блока розеток могут быть дополнены винтами и другими фиксирующими деталями в виде распорок, регулируемых поворотами винтов. В этом случае крепление в стену осуществляется собственными силами подрозетника, за счет его конструктивных особенностей. Обращаться с креплениями нужно аккуратно, чтобы не испортить посадочное место.
Стандартные размеры подрозетников и коронок
Рассматривая классификацию монтажных коробок, следует более подробно остановиться на их размерах. Стандартные габариты изделия составляют 68х45 мм, и расшифровываются как диаметр подрозетника – 68, глубина – 45 мм. В связи с этим, при разметке отверстий под блок монтажных коробок расстояния между центрами берутся в размере 71 мм.
У разных производителей размеры изделий отличаются в зависимости от предназначения каждого из них. Диаметры находятся в пределах 60-68 мм, максимальное значение составляет 72 мм. Глубина подрозетника выбирается в зависимости от количества элементов, запланированных к установке во внутреннем пространстве. Ее значение начинается от 40 мм, среднее составляет 60 мм, максимальное – 75-80 мм, что означает углубленный подрозетник.
В соответствии с размерами подрозетника выбираются бур и коронка для сверления отверстий. Подбирать инструмент под диаметр отверстия нужно внимательно, иначе коробка просто не поместится внутрь. Железобетон и другие материалы повышенной прочности сверлятся алмазными коронками, а расстояние между подрозетниками в 71 мм сохраняется независимо от их размеров.
Глубина сверления регулируется меткой, наносимой на корпус насадки. За счет этого отверстия получаются не слишком глубокими, что особенно актуально для тонких межкомнатных перегородок.
Выбор диаметра при монтаже в бетонные и кирпичные стены
Проще всего монтируется одиночный подрозетник, размеры которого относятся к стандартным. Разметка коробки совпадает с расположением самой розетки, а все регулировки можно делать в процессе установки. Для ускорения работы рекомендуется использовать перфоратор и специальную коронку или бур для твердых материалов. С их помощью отверстие в бетонной стене просверливается за несколько минут. При отсутствии коронки для одноразового мероприятия вполне подойдет сверло с наконечником из твердого сплава.
Значение имеет правильный выбор диаметра подрозетника. Он выбирается таким образом, чтобы между корпусом и стеной оставался небольшой зазор. То есть, коробка должна свободно заходить на свое посадочное место. При разметке на стене вертикальные и горизонтальные линии должны немного выходить за пределы диаметра окружности. Это даст возможность выровнять подрозетник в том числе и двойной, в процессе его фиксации раствором.
Диаметр коронки для подрозетника при сверлении должен обеспечивать зазор 5-10 мм в который помещается раствор. После застывания он надежно удерживает коробку в гнезде. Во время работы инструмент, в том числе и сверло, нагревается и расширяется, поэтому рекомендуется использовать водяное охлаждение коронки. По достижении нужной глубины бур или коронка вынимается, а само отверстие выравнивается зубилом.
Кирпичную стену можно сверлить точно так же, как и бетон, аналогично выбирается и диаметр отверстия. Глубина высчитывается по-другому, с учетом нанесенной штукатурки, чтобы коробка была на одном уровне с поверхностью. Монтаж проводки в кирпичных стенах выполняется еще до нанесения штукатурки. После высыхания раствора монтируется подрозетник. Ниже линии по кирпичу нужно осторожно просверлить отверстие, после чего пробить канавку и завести провод внутрь коробки.
Особенности монтажа с керамической плиткой
Сверление отверстий в керамической плитке имеет свои особенности. Здесь также нужно рассчитать глубину монтажа подрозетника, чтобы он располагался в одной плоскости с поверхностью стены. Иногда используется усложненный вариант, когда подрозетник изначально монтируется на стену, а уже потом монтируется плитка. В этом случае учитывается несколько параметров, слой клеящего раствора, толщина плитки и размеры подрозетников.
Определенную сложность представляет расчет места расположения отверстия под монтажную коробку. Его необходимо разметить и вырезать непосредственно в плитке и несоответствие в 3-4 мм уже будет критическим и не позволит установить подрозетник на свое место. В таких случаях прорезается новая плитка или вновь сверлится отверстие в самой стене. Нужно учитывать и расстояние между центрами подрозетников.
В более простом варианте делается штроба, после чего провод подводится к отверстию в стене без плитки. Место расположения отверстия и межосевое расстояние подрозетников должны быть размечены, после чего оно закрывается на период выравнивающей штукатурки стен и последующей укладки плитки. После высыхания раствора, на отмеченном месте в плитке прорезается отверстие под коробку.
Для резки плитки используется коронка для подрозетника с алмазным напылением. Такая насадка способна прорезать отверстие не только в плитке, но и в стене.
Диаметр подрозетников при установке в гипсокартон
Для гипсокартонных покрытий совершенно не подходят стандартные подрозетники, в том числе и блочные, используемые в обычных стенах. В этом случае применяются совершенно другие конструкции, в том числе и в блоке. При выборе нужного изделия обязательно учитывается глубина посадки (Н) и наружный диаметр (d2). Стандартная величина диаметра составляет 68 мм, но весь размерный ряд находится в пределах 60-75 мм. По нему следует подбирать и размер коронки.
Глубина посадки изделия тоже может отличаться. Чаще всего встречается высота 40, 42, 45, 60 и 62 мм. Коробки с нестандартными размерами выпускаются редко и применяются в особых случаях. Для сверления отверстий используется коронка для подрозетников по гипсокартону или сверло.
Выбор изделий осуществляется в соответствии с местом будущего монтажа. При наличии благоприятных технических условий, рекомендуется применять размер подрозетника стандартный, высотой 60-62 мм. При таком размере гораздо удобнее сделать разводку проводов. Провода разводятся внутри коробки, и глубокий подрозетник зачастую имеет большое значение. Процесс соединения проводки также существенно упрощается.
Прикладные науки | Бесплатный полнотекстовый | Определение остаточных сварочных напряжений в стальном компоненте моста с помощью моделирования методом конечных элементов метода поэтапного сверления отверстий
1.

Сталь широко используется для строительства самых разных мостов. Сварочные операции обычно используются для соединения элементов конструкции. Остаточные сварочные напряжения возникают в ходе этого производственного процесса, и предполагается, что влияние этих напряжений покрывается коэффициентами безопасности во время проектирования. Распределения остаточных напряжений могут иметь большие градиенты напряжений из-за их неравномерного поведения [1]. В однопроходном сварном соединении остаточные напряжения являются результатом сопротивления металла шва усадке сварного шва. Наличие остаточных напряжений способствует разрушению за счет усталости, водородного растрескивания и коррозии под напряжением [2]. Многочисленные структурные соединения в мостах также требуют многопроходной сварки. На металле шва проводится многократное термоциклирование, вызывающее многорежимную деформацию этого металла шва за счет термической деформации. Многопроходная сварка вводит переменно распределенные поля остаточных напряжений по шву и по толщине [3].
Одним из наиболее важных видов разрушения стальных мостов со сварными элементами конструкции является усталостное разрушение. Усталость является основным видом отказа, и он до сих пор менее изучен, чем любой другой вид отказа, такой как отказ прочности или отказ пригодности к эксплуатации. Для проектирования новых стальных мостов компоненты моста, чувствительные к усталости, требуют точного расчета на усталость, чтобы более точно оценить преждевременное усталостное разрушение [4]. Остаточные напряжения влияют на усталостную прочность сварных соединений мостовых конструкций. В зависимости от знака и величины остаточных напряжений вклад этих напряжений в напряжения нагрузки на элемент конструкции может быть вредным или полезным. Например, усталостная прочность может быть повышена за счет наличия сжимающих остаточных напряжений [5]. Разрушение коррозионного растрескивания под напряжением может быть либо ускорено, либо замедлено наличием остаточных напряжений [6]. Поэтому для точного расчета усталостных элементов моста, чувствительных к усталости, требуется знание распределения остаточных сварочных напряжений. Чтобы оценить влияние остаточных напряжений на конструкцию, необходимо полное понимание остаточных напряжений. Поэтому можно проводить измерение остаточных сварочных напряжений. Улучшение усталостной прочности также может быть достигнуто с помощью механической обработки поверхности, такой как дробеструйная обработка или глубокая прокатка [7].
Для измерения остаточных напряжений были разработаны различные методы. Существуют три основные категории, к которым можно отнести измерения остаточных напряжений: неразрушающие, полуразрушающие и разрушающие методы измерения. Как для полуразрушающих, так и для разрушающих методов исходное напряженное состояние определяется путем частичного или полного снятия напряжения за счет удаления материала, и измеряются деформации, вызванные этим освобождением. Методы неразрушающего контроля измеряют параметр, связанный с остаточным напряжением, без повреждения образца [8].
Рентгеновская и нейтронная дифракция являются широко используемыми неразрушающими методами измерения. Расстояние между атомными плоскостями измеряется с помощью электромагнитного излучения. Рентгеновская дифракция измеряет расстояние между атомными плоскостями, вызванное напряжением материала. Это измерение используется для расчета общего напряжения в материале. Однако рентгеновская дифракция не является наиболее практичным методом определения остаточных напряжений в больших сварных швах, поскольку на большинстве рентгеновских дифрактометров имеется лишь ограниченное пространство. Это требует, чтобы материал был разрезан на более мелкие части для оценки напряжений. Геометрия измеряемого образца также имеет большое значение, поскольку рентгеновские лучи должны попадать в область измерения, но также должны дифрагировать к детектору, не мешая другим материалам [8].
Метод нейтронной дифракции аналогичен рентгеновской дифракции, поскольку для расчета остаточного напряжения также определяется расстояние между атомными плоскостями. Можно получить большую глубину проникновения по сравнению с дифракцией рентгеновских лучей, поскольку нейтрон может проникать в материал на несколько сантиметров. Однако относительная стоимость метода нейтронной дифракции выше [8].
Метод разрезания — это разрушающий метод, который можно использовать для определения остаточных напряжений. Разрез производится через материал без внесения какой-либо пластичности или тепла на поверхность материала. В процессе резки высвобождаются деформации, которые измеряются тензодатчиками. Эти деформации используются для определения остаточных напряжений [8].
В этой статье ортотропный стальной настил используется для измерения остаточного напряжения вблизи сварного соединения, а также используется полуразрушающий метод измерения. Метод пошагового сверления используется для измерения остаточных напряжений в сварных стальных компонентах. Этот метод предпочтительнее, потому что измерения можно легко выполнить на площадке моста, не влияя на его производительность. Небольшое отверстие просверливается с возрастающим числом шагов, и соответствующие деформации измеряются с помощью розеток тензодатчиков на поверхности. Остаточные напряжения рассчитываются с этими измеренными деформациями, и получается распределение остаточных напряжений по глубине материала [1].
При оценке высоких остаточных сварочных напряжений вблизи отверстия вводятся пластические релаксационные деформации. Это пластическое поведение может привести к значительным ошибкам в расчете остаточных напряжений, поскольку метод сверления отверстий применяется только тогда, когда поведение материала остается линейно-упругим [9,10].
В этой статье метод поэтапного бурения моделируется с помощью моделирования методом конечных элементов (МКЭ) с моделью материала, включающей пластичность. Во-первых, моделируется равномерное остаточное напряжение по глубине и проводится сравнение между калибровочными коэффициентами, указанными Американским обществом по испытаниям и материалам ASTM E837-13a, и рассчитанными коэффициентами, включая влияние пластичности из модели конечных элементов. После этого исследуют неравномерные остаточные напряжения по глубине путем оценки экспериментальных значений остаточных напряжений ортотропного стального настила.
2. Метод поэтапного сверления отверстий
Остаточные напряжения, возникающие при сварке ортотропного стального настила, оцениваются методом поэтапного сверления отверстий. В испытуемом материале просверливается небольшое отверстие через центр тензометрической розетки [10]. Эти тензометрические розетки используются для измерения снятой поверхностной деформации, вызванной введением отверстия, которое образуется путем сверления в несколько небольших шагов. Остаточные напряжения можно рассчитать с помощью измеренных деформаций и калибровочных коэффициентов в соответствии с принципами расчета, указанными в ASTM E837-13a. Надежные измерения достигаются только при ограничении остаточных напряжений до 80% от предела текучести материала [11]. Однако значения остаточного напряжения могут достигать предела текучести материала путем сверления отверстия, и может быть достигнут предел упругости материала. Эта пластическая область присутствует вблизи нижней окружности отверстия и распространяется по направлению к тензорезисторам тензометрической розетки за счет увеличения глубины отверстия [10]. Черные зоны на рисунке 1 указывают на эту пластическую область, где отверстие, просверленное до глубины 1 мм, моделируется для четверти стального листа качества S235 толщиной 6 мм с использованием линейно-упругого закона материала. На рисунке также указаны два тензорезистора тензометрической розетки.
Остаточные сварочные напряжения, создаваемые сварным соединением плиты настила с продольным элементом жесткости настила из ортотропной стали, оцениваются с помощью фрезерного шаблона RS-200 (рис. 2). Для установки тензометрической розетки необходима гладкая поверхность. Однако подготовка поверхности перед приклеиванием тензометрической розетки не должна создавать значительных остаточных напряжений [10]. Слой краски с настила из ортотропной стали удаляли шлифовальным инструментом. После обработки первых измерений было замечено, что приповерхностные напряжения очень велики. При использовании шлифовального круга с менее грубой наждачной бумагой можно уменьшить приповерхностные напряжения. Чтобы обнажить материал поверхности, необходимо просверлить только материал розетки тензодатчика, а не материал испытуемого образца, чтобы установить правильную нулевую глубину [10,12]. На практике эта нулевая глубина устанавливается очень медленным продвижением фрезы на 0,02 мм и полным вращением сверлильного станка. Деформации тензометрической розетки регистрируются и остаются постоянными, пока резец еще не достиг поверхности испытания. Когда регистрируемые деформации меняются, резец просверлил материал розетки тензодатчика и достиг поверхности испытуемого материала. Эта глубина резца указывает на первое измерение розетки тензодатчика. Нулевая глубина – это глубина фрезы перед этим первым измерением.
Для измерений на ортотропном стальном настиле используется только один тип тензометрической розетки. Поэтому в данной статье будет рассматриваться только этот тип тензометрической розетки. Тензометрическая розетка с геометрией Рендлера и Вигнесса [13]. Тензометрическая розетка типа СЕА-06-062УЛ-120 используется для экспериментальных измерений на ортотропном стальном настиле. Геометрия схематически представлена на рис. 3а, а деталь одного тензодатчика на розетке — на рис. 3б. Размеры используемой тензометрической розетки приведены в таблице 1, диаметр отверстия 2 мм и максимальная глубина сверления 1 мм [10].
Большие тензометрические розетки могут использоваться для получения остаточных напряжений в большей глубине испытательной поверхности. Таким образом, могут быть устранены неопределенные приповерхностные остаточные напряжения из-за подготовки поверхности для розеток тензодатчиков. В будущих исследованиях эти более крупные тензометрические розетки могут использоваться для получения результатов более глубоко в материале [11].
3. Трехмерная модель конечных элементов
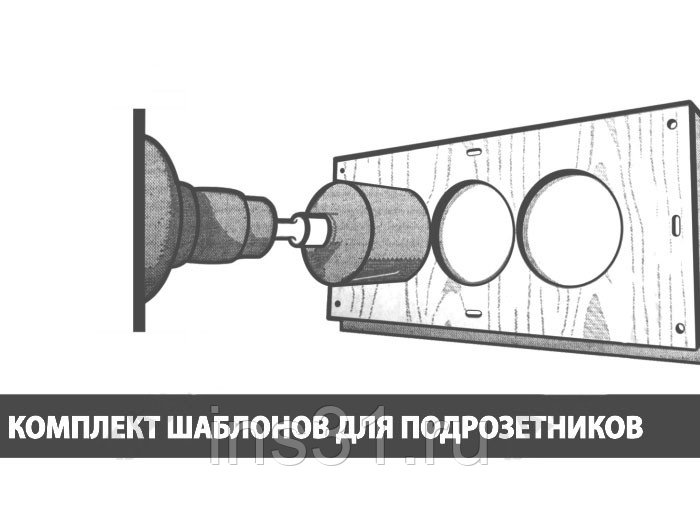
Сверление дополнительных отверстий для метода сверления отверстий моделируется путем деактивации слоя элементов с функцией рождения/смерти элемента. Для каждого удаленного слоя к сторонам модели, содержащей отверстие, прикладывается давление в соответствии с принципом Сен-Венана, и регистрируются деформации, которые используются для расчета остаточных напряжений в соответствии с ASTM E837-13a. Интерес представляют только нормальные напряжения x и y, поэтому для оценки остаточных напряжений учитываются только радиальные деформации 1 и 3 (рис. 3а) [10].
3.1. Геометрия, свойства материалов, ограничения и условия нагружения
Плоская пластина толщиной 6 мм используется для имитации сверления отверстий. Исследовано увеличение толщины пластины, влияние на результаты которого практически отсутствует (менее 1%). Из-за симметрии приходится рассматривать только четверть всей пластины. Пластина представляет собой толстую пластину в соответствии с ASTM E837-13a, поскольку толщина пластины больше, чем средний диаметр розетки тензодатчика. Ширина модели в 15 раз больше диаметра отверстия [10]. Толщина моделируемой пластины также равна толщине продольного элемента жесткости ортотропного стального настила. Марка стали ортотропного стального настила моста S235. Этот материал также используется для моделирования, в результате чего параметры материала указаны в таблице 2.
Ограничения симметрии необходимы, поскольку для моделирования методом конечных элементов рассматривается только четверть пластины. Эти ограничения применяются к сторонам, где расположено отверстие. Смещения по осям x и y вдоль этих сторон равны нулю. Для нижней поверхности смещение по оси z принимается равным нулю [10].
Различия в поведении материалов указываются при задании другой кривой напряжения-деформации. Линейная кривая напряжение-деформация используется для линейно-упругого поведения материала с пределом текучести в качестве верхнего предела (рис. 4). Билинейная кривая напряжение-деформация (рис. 5) задается при упругопластическом поведении материала и использовании модели изотропного пластического упрочнения [10].
Для поведения линейно-упругих напряжений и деформаций программа конечных элементов следует той же линейной кривой для посткритических напряжений и деформаций. Для упругопластического напряженно-деформированного состояния закритическое поведение определяется второй ветвью кривой, где она следует той же тенденции.
Как однородные (рис. 6а), так и неоднородные (рис. 6б) поля остаточных напряжений по глубине будут оцениваться с линейно-упругим и упруго-пластическим поведением напряжения-деформации. Наличие поля остаточных напряжений имитируется путем наложения зависящих от времени однородных или неравномерных распределений давления на сторонах, не содержащих просверленное отверстие.
3.2. Mesh Sensitivity Study
Эффект измельчения сетки в области просверленного отверстия изучается для изучения размеров элементов. Поэтому по всей толщине пластины прикладывается равномерное распределение давления по сторонам, не содержащим просверленного отверстия, и предполагается линейно-упругое поведение напряжения-деформации. Деформации, полученные с помощью этой модели, сравнивают с теоретически рассчитанными деформациями в соответствии с ASTM E837-13a. Сетка уточняется до тех пор, пока результаты модели не будут хорошо согласованы с теоретическим результатом.

3.3. Расчет остаточного напряжения
Для равномерного распределения остаточных напряжений по глубине главные остаточные напряжения σ x и σ y можно рассчитать, используя калибровочные коэффициенты a и b, измеренные релаксационные деформации ϵ 1 и ϵ 3 , коэффициент Пуассона ν и модуль Юнга E материала [11]. Применяются следующие соотношения:
Коэффициенты калибровки зависят от глубины отверстия, типа тензометрической розетки и диаметра просверленного отверстия. Известное равномерное распределение напряжения применяется к сторонам, где отверстие не расположено, и релаксирующие деформации оцениваются для расчета этих калибровочных коэффициентов [9].,10].
При неравномерном распределении остаточных напряжений связь между остаточными напряжениями и ослабленными деформациями более сложная по сравнению с равномерными распределениями. Стандартные ошибки векторов комбинированных деформаций также следует учитывать для определения основных остаточных напряжений. Для неоднородных полей остаточных напряжений расчетные релаксационные деформации 3D-модели будут сравниваться с теоретически определенными релаксирующими деформациями в соответствии с ASTM E837-13a ортотропного мостового полотна. Эти деформации используются для определения распределения остаточных напряжений в ортотропном настиле моста.
4. Равномерное поле остаточных напряжений по глубине
Однородное поле остаточных напряжений по глубине моделируется путем приложения известного равномерного давления к сторонам модели. Сверление отверстия происходит с разным временным шагом и для каждого удаляемого слоя прикладывается давление одинаковой высоты на сторону. Во-первых, для определения калибровочных коэффициентов будет применяться линейно-упругое поведение материала. Затем применяется упрощенная пластичность материала и проводится сравнение результатов двух разных законов материала.
4.1. Свойства линейно-упругих материалов
Сначала процесс сверления отверстий подвергается численной калибровке с использованием образца, на который воздействует однородное поле остаточных напряжений по глубине в 50 МПа, и определяются калибровочные коэффициенты. Однородное поле остаточных напряжений делится на равнодвуосное (σ x = σ y = 50 МПа) и девиаторное (σ x = −σ y = 50 МПа) поля остаточных напряжений и линейно-упругое. рассматривается материальное право. Оцениваются две трехмерные модели с линейно-упругим поведением материала. Известное равнодвуосное поле напряжений применяется к первой модели, а вторая модель оценивается путем применения девиаторного поля напряжений. Модель с равнодвуосным полем остаточных напряжений используется для определения калибровочного коэффициента а. Поле девиаторных остаточных напряжений дает калибровочный коэффициент b. Для обеих моделей оцениваются десять приращений глубины по 0,1 мм, пока не будет достигнута окончательная глубина отверстия 1 мм.
Коэффициенты калибровки при моделировании методом конечных элементов с линейно-упругим поведением материала должны быть равны коэффициентам, указанным в ASTM. Однако коэффициенты, рассчитанные с помощью 3D-модели, в среднем на 4% меньше, чем коэффициенты из ASTM. При увеличении глубины отверстия разница также увеличивается, поскольку увеличивается расстояние до тензометрической розетки на поверхности. Вклад релаксированной деформации меньше при увеличении глубины отверстия, поскольку увеличивается расстояние до поверхности розетки тензодатчика. Геометрические переменные, такие как диаметр отверстия, толщина листа и глубина сверления, влияют на определение калибровочных коэффициентов. Ошибки измерения деформации, глубины отверстия и геометрии вызывают разницу между калибровочными коэффициентами, определенными с помощью моделирования методом конечных элементов, и указанными в ASTM. Исследования, проведенные Aoh и Wei [16], показывают, что калибровочный коэффициент a становится хуже обусловленным быстрее, чем калибровочный коэффициент b, и это также можно заметить в таблице 3.9.0005
Также проведено сравнение с коэффициентами из других исследований [16], и при экспериментальной калибровке наблюдаются аналогичные частоты ошибок и тенденции. Поэтому делается вывод, что калибровочные коэффициенты трехмерного моделирования методом конечных элементов согласуются с обычными коэффициентами метода пошагового сверления отверстий, указанного в ASTM. Эта модель конечных элементов используется для моделирования пошагового бурения скважины для определения остаточных напряжений в ортотропном настиле моста [10].
4.2. Свойства упруго-пластического материала
Сравниваются калибровочные коэффициенты, определенные с помощью линейно-упругой и упруго-пластической моделей конечных элементов, и это показано на рисунке 9. Коэффициенты поведения упруго-пластического материала меньше, только для первой глубины отверстия калибровочный коэффициент б крупнее. Разница между поведением двух материалов также увеличивается с увеличением глубины отверстия. Меньший калибровочный коэффициент означает, что остаточные деформации и соответствующие им напряжения ниже теоретических. Следовательно, линейно-упругое поведение материала дает завышенную оценку остаточных напряжений. Эффект пластичности более выражен для девиаторных полей остаточных напряжений [10].
5. Неравномерное поле остаточных напряжений по глубине настила ортотропного моста
Неравномерное поле остаточных напряжений по глубине настила ортотропной стали моделируется приложением неравномерного давления на стороны модели без просверленного отверстия. Неравномерное поле остаточных напряжений получают измерениями при сверлении отверстий. Результаты моделирования методом конечных элементов будут сравниваться с экспериментальными результатами измерений при сверлении отверстий.
5.1. Измерения экспериментального сверления отверстий
Экспериментальные измерения остаточного напряжения на ортотропном стальном настиле выполняются с помощью процедуры поэтапного сверления отверстий в соответствии со стандартом ASTM. Полномасштабный испытательный образец, использованный для измерений, показан на рисунке 10 [17]. Продольные ребра жесткости приварены к плите настила моста двухпроволочной сваркой под флюсом. Сварку можно выполнять только снаружи ребра жесткости, поскольку сварочная горелка не может добраться до внутренней части. Параметры процедуры сварки предоставляются производителем. Диаметр электродов 2 мм, а удлинение одного электрода 30 мм. Сварку выполняют током оп 780 А и напряжением 29 В.V. Скорость подачи сварочных горелок 950 мм в минуту. Сварочный ток течет от электрода к основному металлу.
Оцениваются места на верхней и нижней части плиты настила и на продольном элементе жесткости. Деформации измеряют с увеличением глубины 0,05 мм, пока не будет достигнута окончательная глубина отверстия 1 мм. Одно репрезентативное значение остаточного напряжения выбирается для каждой тензометрической розетки в распределении остаточного напряжения по глубине этой конкретной тензометрической розетки. На приповерхностные напряжения воздействует шлифовальный диск, который используется для подготовки поверхности к установке тензометрической розетки. Считается, что остаточное напряжение на конечной глубине отверстия 1 мм минимизирует влияние подготовки поверхности на значение остаточного напряжения. Распределение остаточного напряжения в продольном и поперечном направлениях может быть установлено в зависимости от расстояния до сварного шва. Расположение различных розеток тензодатчиков показано на рис. 11.
Значение остаточного напряжения присваивается каждой измеренной тензометрической розетке в поперечном и продольном направлениях. Это значение остаточного напряжения представляет собой расчетное напряжение на конечной глубине отверстия в соответствии с принципами расчета стандарта ASTM для обоих направлений. Поскольку значения остаточных напряжений различны для соседних тензометрических розеток, проводится различие между значениями остаточных напряжений сжатия и растяжения. Измеренные места сгруппированы в зоны сжатия и растяжения. Значения остаточных напряжений, присвоенные этим зонам, рассчитываются путем усреднения остаточных напряжений розеток тензометрических датчиков, присутствующих в рассматриваемой зоне. Положительные значения указывают на растягивающие остаточные напряжения, а отрицательные значения указывают на сжимающие напряжения. В продольном направлении на верхней части плиты настила имеются зоны растягивающих и сжимающих остаточных напряжений. Зона растяжения имеет значение 64% от предела текучести (f y ), а зона сжатия достигает предела текучести. В нижней части плиты настила имеется зона растягивающих остаточных напряжений (0,5 × f y ), присутствующая в продольном направлении. На элементе жесткости вблизи сварного шва имеется небольшая зона предела текучести при растяжении, за которой следуют зона сжатия (0,17 × f y ) и зона растяжения (0,13 × f y ).
В поперечном направлении в верхней части плиты настила выделяются две зоны растяжения и зона сжатия. Между двумя сварными стенками ребра жесткости существует среднее остаточное растягивающее напряжение 67 МПа. Вблизи места сварки на плите палубы имеется зона сжатия со средним остаточным напряжением, равным 0,42×f и . Другая зона остаточного напряжения при растяжении существует с правой стороны от зоны сварки на плите настила. На нижней стороне плиты настила существует среднее остаточное растягивающее напряжение, равное 70% предела текучести. Для продольного элемента жесткости вблизи сварного шва присутствует зона растягивающих остаточных напряжений. Эти общие распределения остаточных напряжений, полученные с помощью экспериментальных результатов, показаны на рисунке 12.
Остаточные напряжения самоуравновешиваются, поскольку они остаются в материале даже после устранения первоначальной причины напряжений (сварки). Следовательно, сумма всех напряжений в локальной области создает нулевую результирующую силу и нулевой импульс. Для проверки саморавновесия необходимы дополнительные измерения сверления отверстий по всей стальной палубе. Однако распределение остаточного напряжения на верхней части плиты настила в поперечном направлении указывает на хороший баланс.
5.2. Результаты моделирования методом конечных элементов
Процедура сверления отверстий экспериментальной установки для ортотропного стального настила моделируется методом конечных элементов. Отверстие просверливают с шагом 20 глубин по 0,05 мм, пока не будет достигнута окончательная глубина отверстия 1 мм. На каждом этапе материал удаляется и снимается напряжение. Чтобы компенсировать это удаление материала, по бокам модели применяется соответствующее давление. Таким образом, внешний силовой баланс напряжений остается в равновесии. Приложенные давления соответствуют экспериментально полученным результатам, и остаточные напряжения могут быть рассчитаны для каждой глубины сверления. Это позволяет сравнивать полученные результаты с экспериментальными измерениями и моделированием методом конечных элементов.
5.2.1. Верхняя боковая пластина настила
На верхней стороне настила исследуются в общей сложности 11 тензометрических розеток. Измеренные остаточные напряжения для каждой из этих тензометрических розеток при 20 шагах по глубине 0,05 мм применяются к трехмерной модели на границах, не содержащих отверстия, и моделируется процедура сверления отверстия. Дополнительные деформации, полученные с помощью 3D-модели, используются для расчета остаточных напряжений. Для каждой розетки тензодатчика используется репрезентативное значение остаточного напряжения на конечной глубине отверстия 1 мм, чтобы получить распределение остаточного напряжения в зависимости от расстояния до края сварного шва. Определенное экспериментально распределение остаточного напряжения сравнивается с измеренным распределением остаточного напряжения из конечно-элементной модели как в поперечном, так и в продольном направлениях. Это сравнение показано на рис. 13. По горизонтальной оси отложено расстояние до края шва, начало координат соответствует краю шва, в то время как положительные расстояния находятся с правой стороны края шва, а отрицательные расстояния — с левой стороны.
Значения остаточного напряжения, полученные с помощью упруго-пластического анализа, приводят к более высоким растягивающим и более низким остаточным напряжениям при сжатии по сравнению с ожидаемыми на основе экспериментальных измерений в соответствии со стандартом ASTM. Однако общий тренд напряжений в зависимости от расстояния до края шва остается прежним.
5.2.2. Нижняя боковая пластина настила
На нижней стороне настила оцениваются в общей сложности 4 розетки тензометрических датчиков. Ожидаемое экспериментально распределение остаточного напряжения и распределение остаточного напряжения, рассчитанное с помощью модели конечных элементов с упруго-пластическим поведением материала, в зависимости от расстояния до края шва показаны на рис. 14.
Опять же, распределение остаточного напряжения из трехмерной конечно-элементной модели (FEM) показывает аналогичную тенденцию по сравнению с экспериментальными измерениями в соответствии с ASTM. Для нижней стороны плиты настила имеются только растягивающие остаточные напряжения, которые выше для результатов моделирования методом конечных элементов.
5.2.3. Продольный элемент жесткости
Наконец, 4 розетки тензодатчиков, расположенные на продольном элементе жесткости, оцениваются с помощью модели конечных элементов. Результаты показаны на рисунке 15.
Снова наблюдаются те же тенденции. Распределение остаточных напряжений по 3D-модели показывает более высокие растягивающие и более низкие сжимающие остаточные напряжения по сравнению с результатами ASTM. Ход остаточных напряжений в зависимости от расстояния до края шва остается одинаковым для экспериментальных и численных результатов моделирования методом конечных элементов.
5.3. Распределение остаточных напряжений ортотропного стального настила
Остаточные напряжения из экспериментальных измерений реализованы в модели конечных элементов, и результаты показаны в разделе 5.2. Эти результаты остаточного напряжения являются более репрезентативными, поскольку в модели конечных элементов используется модель упруго-пластического материала, которая более реалистична, чем упругое поведение экспериментальной установки. Общее распределение остаточных напряжений устанавливается по отношению к расстоянию до сварного шва, которое можно сравнить с рисунком 12. Здесь также проводится различие между зонами остаточных напряжений сжатия и растяжения, и учитываются как продольное, так и поперечное направление. Значения остаточных напряжений, присвоенные этим зонам, рассчитываются путем усреднения остаточных напряжений розеток тензометрических датчиков, присутствующих в рассматриваемой зоне. Это распределение остаточного напряжения показано на рисунке 16а для продольного направления и на рисунке 16b для поперечного направления.
В продольном направлении на верхней части плиты настила имеются зоны растягивающих и сжимающих остаточных напряжений. Зона растяжения имеет значение 51% предела текучести (f y ), в то время как зона сжатия достигает предела текучести. В нижней части плиты настила имеется зона растягивающих остаточных напряжений размером 0,74 × f y в продольном направлении. На элементе жесткости вблизи сварного шва имеется небольшая зона предела текучести при растяжении, за которой следуют зоны сжатия и растяжения. В поперечном направлении в верхней части плиты настила выделяются две зоны растяжения и зона сжатия. Между двумя сварными стенками элемента жесткости существует среднее остаточное растягивающее напряжение 133 МПа, что соответствует 56% предела текучести. Вблизи места сварки на плите палубы имеется зона сжатия со средним остаточным напряжением, равным 0,23 × f и . Другая зона остаточного напряжения при растяжении со средним значением 53% от предела текучести существует с правой стороны области сварки на настиле. На нижней стороне плиты настила существует среднее остаточное растягивающее напряжение, равное 0,88 × f y . Для продольного элемента жесткости вблизи сварного шва имеется небольшая зона предела текучести при растяжении, за которой следуют очень небольшие остаточные напряжения сжатия, близкие к нулю. Дальше от сварного шва находится зона остаточного напряжения при растяжении, составляющая 80 % имеющегося предела текучести.
При сравнении результатов моделирования методом конечных элементов (рис. 16) с остаточными напряжениями экспериментальных измерений (рис. 12) можно установить общее распределение остаточных напряжений ортотропного стального настила. Результаты МКЭ более репрезентативны, поскольку в них используется более реалистичная модель материала. Сначала обсуждаются результаты продольного направления. Между двумя сварными стенками элемента жесткости на верхней части плиты настила имеется зона сжатия. Эта зона сжатия равна половине предела текучести материала по результатам МКЭ. Это на 10% меньше по сравнению с результатами экспериментальной установки. Вблизи области сварки на верхней части плиты настила присутствуют остаточные напряжения текучести при растяжении. На нижней стороне плиты настила имеется зона растяжения с 74% предела текучести, представленного в результатах моделирования методом конечных элементов. Это на 24 % больше, чем значение из экспериментальных результатов. Для элемента жесткости рядом со сварным швом имеется небольшая зона текучести при растяжении, за которой следует небольшая зона сжатия с пределом текучести 23%. Эта зона сжатия меньше по размеру по сравнению с зоной из экспериментальных измерений и на 6% больше. Наконец, вдоль остальной части элемента жесткости существует зона растяжения со значением 32% от предела текучести материала. это 19% больше по сравнению с экспериментальными данными. Для продольного направления можно сделать вывод, что аналогичные зоны остаточных напряжений присутствуют как для МКЭ, так и для экспериментальных результатов. Сжимающие остаточные напряжения остаются неизменными в пределах примерно 10 %. Растягивающие остаточные напряжения, как правило, на 20% больше для результатов МКЭ.
В поперечном направлении на верхней части настила можно различить три различные зоны. Зона растяжения с пределом текучести 56 % между сварными стенками элемента жесткости, за которой следует зона сжатия с пределом текучести 23 % вблизи области сварки и снова зона растяжения с пределом текучести 53 % материала. Растягивающие остаточные напряжения соответственно на 28% и 35% больше для результатов МКЭ. Значения остаточных напряжений сжатия составляют 19% меньше. На нижней стороне плиты настила имеется зона растягивающих остаточных напряжений со значением 88% от предела текучести. Это приводит к остаточным напряжениям, которые на 18% больше по сравнению с экспериментальными результатами. Для продольного элемента жесткости по результатам МКЭ наблюдается совершенно другое поведение остаточных напряжений. Результаты экспериментальных данных показывают растягивающие остаточные напряжения, равные 69% предела текучести по всей длине элемента жесткости. Однако результаты МКЭ показывают зону текучести при растяжении вблизи сварного шва, за которой следует небольшая зона сжатия, где остаточное напряжение близко к нулю, и снова зона растягивающего напряжения с 80% предела текучести. В поперечном направлении аналогичные зоны остаточных напряжений выделены для плиты настила. Продольный элемент жесткости показывает другое поведение остаточных напряжений. В целом можно сделать вывод, что значения остаточных напряжений растяжения больше для результатов МКЭ по сравнению с экспериментальными результатами, а остаточные напряжения сжатия меньше.
Моделирование методом конечных элементов метода сверления отверстий для ортотропного стального настила дает эффект остаточных напряжений, включая более реалистичную модель материала. Это приводит к большим остаточным напряжениям растяжения и меньшим напряжениям сжатия. Следовательно, можно сделать вывод, что экспериментальные результаты метода сверления отверстий, рассчитанные в соответствии со стандартом ASTM, занижают остаточные напряжения растяжения и завышают остаточные напряжения сжатия. Поскольку большие растягивающие остаточные напряжения более вредны для усталости сварного компонента моста, лучше учитывать реальные свойства материала с упруго-пластическим поведением. В этом случае очень ценна проверка результатов сверления отверстий методом конечных элементов.
6. Выводы
Метод пошагового сверления может быть использован для оценки высоких остаточных сварочных напряжений в сварных мостовых конструкциях. Этот метод применяется только в том случае, когда поведение материала является линейно-упругим, и поэтому влияние учета реальных свойств материала с упруго-пластическим поведением на остаточные напряжения, рассчитанные в соответствии с ASTM E837-13a, изучается с помощью трехмерного моделирования методом конечных элементов. Процедура сверления отверстий моделируется с помощью расчетного программного обеспечения. Во-первых, выполняется линейно-упругий анализ для определения калибровочных коэффициентов, аналогичных тем, которые указаны в ASTM E837-13a для однородных остаточных напряжений по глубине. Для равномерного по глубине поля остаточных напряжений выполняется суперпозиция равнодвуосных и девиаторных полей остаточных напряжений, приложенных к сторонам модели. Затем определяется влияние пластичности на равномерные остаточные напряжения по глубине путем применения закона упруго-пластического материала к той же трехмерной модели. Сделан вывод, что остаточные напряжения, полученные в предположении, что поведение материала является линейно-упругим, являются завышенными. Пластичность вызывает релаксацию материала, и если ее игнорировать, остаточные напряжения будут завышены из-за определения линейно-упругого поведения материала.
Влияние упругопластического поведения материала на неравномерные остаточные напряжения по глубине также изучается путем сравнения экспериментально определенных радиальных деформаций с расчетными деформациями из упругопластического анализа ортотропного стального настила. Аналогичное поведение остаточных напряжений было замечено. Однако остаточные напряжения, полученные при упругопластическом анализе конечно-элементной модели, больше для растягивающих и меньше для сжимающих остаточных напряжений.
Точный расчет на усталость, включая остаточные сварочные напряжения, очень важен, поскольку усталостное разрушение является одним из наиболее важных видов разрушения стальных мостов со сварными элементами конструкции. Моделирование методом конечных элементов показало более высокие растягивающие остаточные напряжения по сравнению с анализом по ASTM. Более высокие растягивающие остаточные напряжения ускоряют коррозионное растрескивание под напряжением, что приводит к более раннему усталостному разрушению компонента. Поэтому очень важно учитывать эти более высокие растягивающие остаточные напряжения при расчете усталостной прочности сварного компонента.
Определенные экспериментально значения остаточного напряжения ортотропного стального настила в соответствии со стандартом ASTM основаны на линейно-упругом поведении материала. Моделирование методом конечных элементов показало, что включение модели упругопластического материала приводит к большим растягивающим и меньшим сжимающим остаточным напряжениям. Такое поведение более невыгодно, так как приводит к преждевременному усталостному растрескиванию. Поэтому очень важно проверить экспериментальные результаты сверления отверстий с помощью моделирования методом конечных элементов, включая упруго-пластическое поведение материала.
Вклад авторов
Концептуализация: E.V.P., W.N. и HDB; Курирование данных: E.V.P.; Формальный анализ: E.V.P.; Расследование: EVP, WN и HDB; Методология: Э.В.П. и В.Н.; Администрация проекта: E.V.P., K.S. и HDB; Ресурсы: К.С. и HDB; Программное обеспечение: E.V.P. и В.Н.; Руководство: К.С. и HDB; Валидация: EVP, ZU-A и WN; Визуализация: E.V.P. и В.Н.; Написание — первоначальный вариант: E.V.P. и HDB; Написание — обзор и редактирование: EVP, ZU-A и HDB.
Финансирование
Это исследование не получило внешнего финансирования.
Конфликт интересов
Авторы заявляют об отсутствии конфликта интересов.
Ссылки
- Schajer, G.S. Практические методы измерения остаточного напряжения; John Wiley & Sons Ltd.: Чичестер, Великобритания, 2013 г. [Google Scholar]
- Huang, C.C.; Пан, Ю.К.; Чуанг, Т.Х. Влияние послесварочной термической обработки на остаточное напряжение и механические свойства стальных листов SAE 4130, сваренных электронной сваркой. Дж. Матер. англ. Выполнять. 1997 , 6, 61–68. [Google Scholar] [CrossRef]
- Гангули, С.; Суле, Дж.; Якубу, М.Ю. Расчет напряжений многопроходных сварных швов конструкционной стали для повышения структурной целостности. Дж. Матер. англ. Выполнять. 2016 , 25, 3238–3244. [Google Scholar] [CrossRef]
- Чжао З.; Халдар, А .; Брин, Ф.Л. Оценка усталостной прочности стальных мостов. Дж. Структура. англ. 1994 , 120, 1608–1623.
[Google Scholar] [CrossRef]
- Sonsino, C.M. Влияние остаточных напряжений на усталостные характеристики сварных соединений в зависимости от условий нагружения и геометрии шва. Междунар. Дж. Усталость 2009 , 31, 88–101. [Google Scholar] [CrossRef]
- Prevéy, P.S.; Мейсон, PW; Хорнбах, ди-джей; Молкентин, Дж. П. Влияние предварительной механической деформации на развитие растягивающих остаточных напряжений в ядерных компонентах, изготовленных сваркой. Дж. Матер. англ. Выполнять. 1996 , 5, 51–56. [Google Scholar] [CrossRef]
- Зинн, В.; Шолтес, Б. Механическая обработка поверхности легких материалов — влияние на усталостную прочность и приповерхностные микроструктуры. Дж. Матер. англ. Выполнять. 1999 , 8, 145–151. [Google Scholar] [CrossRef]
- Россини, Н.; Дассисти, М .; Беньюнис, К.; Олаби, А. Методы измерения остаточных напряжений в компонентах. Матер. Дес.
2012 , 35, 572–588. [Google Scholar] [CrossRef]
- Бегини М.; Бертини, Л.; Сантус, К. Процедура оценки высоких остаточных напряжений с использованием метода бурения вслепую, включая влияние пластичности. Дж. Анальный штамм. англ. Дес. 2010 , 45, 301–318. [Академия Google] [CrossRef]
- Ван Пюимбрук, Э.; Надь, В .; Де Бакер, Х. Влияние пластичности на остаточные напряжения, полученные методом пошагового сверления с 3D-моделированием МКЭ. Матер. Рез. проц. 2016 , 2, 235–240. [Google Scholar]
- ASTM International. Стандартный метод испытаний для определения остаточных напряжений скважинно-тензометрическим методом; АСТМ Е837-13а; ASTM International: West Conshohocken, PA, USA, 2015. [Google Scholar]
- Vishay Measurements Group. Руководство по фрезерованию модели RS-200 Инструкция по эксплуатации Версия 2.0; Micro-Measurements: Malvern, PA, USA, 2011. [Google Scholar] «> Рендлер, Нью-Джерси; Вигнесс, И. Метод измерения остаточных напряжений с помощью тензорезистора. Эксп. мех. 1966 , 6, 577–586. [Google Scholar] [CrossRef]
- Нау, А.; Шолтес, Б. Оценка техники высокоскоростного бурения методом пошагового бурения. Эксп. мех. 2013 , 53, 531–542. [Google Scholar] [CrossRef]
- Бегини, Л.; Бертини, Л. Последние достижения в методе сверления отверстий для измерения остаточного напряжения. Дж. Матер. англ. Выполнять. 1998 , 7, 163–172. [Google Scholar] [CrossRef]
- Аох, Дж. Н.; Вэй, К. С. Об улучшении калибровочных коэффициентов для интегрального метода сверления отверстий: часть I — анализ калибровочных коэффициентов, полученных с помощью трехмерной модели конечных элементов. Дж. Инж. Матер. Технол. 2002 , 124, 250–258. [Google Scholar] [CrossRef]
- Nagy, W.; Ван Пуимбрук, Э.; Шотте, К.; Ван Богарт, П.; Де Бакер, Х.
Измерение остаточных напряжений в ортотропных стальных настилах с использованием метода пошагового сверления отверстий. Эксп. Тех. 2017 , 41, 215–226. [Google Scholar] [CrossRef]
Рис. 1. Зона пластичности введена путем сверления отверстий.
Рисунок 1. Зона пластичности введена путем сверления отверстий.
Рисунок 2. Фрезерная направляющая RS-200 (, левая, ) и розетка с просверленными отверстиями (, правая, ).
Рисунок 2. Фрезерная направляющая RS-200 ( левая ) и розетка тензодатчика с просверленными отверстиями ( правая ).
Рисунок 3. Схематическая геометрия розетки тензодатчика ( a ) и деталь одного тензодатчика ( b ).
Рисунок 3. Схематическая геометрия розетки тензодатчика ( a ) и деталь одного тензодатчика ( b ).
Рисунок 4. Линейно-упругое напряжение-деформация.
Рисунок 4. Линейно-упругое напряжение-деформация.
Рисунок 5. Упругопластическое напряженно-деформированное состояние.
Рисунок 5. Упругопластическое напряженно-деформированное состояние.
Рисунок 6. ( a ) Однородное по глубине и ( b ) неоднородное по глубине поле остаточных напряжений.
Рисунок 6. ( a ) Однородное по глубине и ( b ) неоднородное по глубине поле остаточных напряжений.
Рисунок 7. Конечно-элементная модель с просверленным отверстием.
Рисунок 7. Конечно-элементная модель с просверленным отверстием.
Рисунок 8. Исследование чувствительности сетки.
Рисунок 8. Исследование чувствительности сетки.
Рисунок 9. Сравнение линейно-упругого и упруго-пластического поведения материала по 3D-моделям.
Рис. 9. Сравнение линейно-упругого и упруго-пластического поведения материала по 3D-моделям.
Рисунок 10. Образец для испытаний в натуральную величину ( a ), вид сверху; ( b ) поперечное сечение; ( c ) вид снизу между двумя продольными ребрами жесткости.
Рис. 10. Образец для испытаний в натуральную величину ( a ), вид сверху; ( b ) поперечное сечение; ( c ) вид снизу между двумя продольными ребрами жесткости.
Рисунок 11. Расположение измеряемых тензометрических розеток (размеры в мм).
Рисунок 11. Расположение измеряемых тензометрических розеток (размеры в мм).
Рисунок 12. Распределение общего остаточного напряжения ортотропного стального настила по результатам экспериментальных измерений (f y = предел текучести) для продольного направления ( a ) и поперечного направления ( b ).
Рисунок 12. Общее распределение остаточного напряжения ортотропного стального настила по экспериментальным измерениям (f y = предел текучести) в продольном направлении ( a ) и поперечном направлении ( b ).
Рисунок 13. Сравнение распределения остаточного напряжения на верхней части плиты настила между ASTM и 3D-моделью в продольном ( а ) и поперечном ( b ) направлениях.
Рис. 13. Сравнение распределения остаточного напряжения на верхней части плиты настила между ASTM и 3D-моделью в продольном ( a ) и поперечном ( b ) направлениях.
Рисунок 14. Сравнение распределения остаточного напряжения на дне плиты настила между ASTM и 3D-моделью в продольном ( a ) и поперечном ( b ) направлениях.
Рис. 14. Сравнение распределения остаточного напряжения на дне плиты настила между ASTM и 3D-моделью в продольном ( a ) и поперечном ( b ) направлениях.
Рисунок 15. Сравнение распределения остаточного напряжения на продольном элементе жесткости между ASTM и 3D-моделью в продольном ( a ) и поперечном ( b ) направлениях.
Рис. 15. Сравнение распределения остаточного напряжения на продольном элементе жесткости между ASTM и 3D-моделью в продольном ( а ) и поперечном ( b ) направлениях.
Рисунок 16. Распределение остаточного напряжения ортотропного стального настила согласно МКЭ для ( a ) продольного и ( b ) поперечного направлений.
Рис. 16. Распределение остаточного напряжения ортотропного стального настила согласно МКЭ для ( a ) продольного и ( b ) поперечного направлений.
Таблица 1. Размеры тензометрической розетки в мм; D: круг калибра диаметра; GL: длина линий сетки; GW: ширина линий сетки; р 1 : радиус 1; R 2 : радиус 2.
Таблица 1. Размеры тензометрической розетки в мм; D: круг калибра диаметра; GL: длина линий сетки; GW: ширина линий сетки; R 1 : радиус 1; R 2 : radius 2.
Rosette Type | D | GL | GW | R 1 | R 2 |
---|---|---|---|---|---|
CEA-06-062UL-120 | 5,13 | 1,59 | 1,59 | 1,77 | 3,36 |
Таблица 2. Свойства материала.
Таблица 2. Свойства материала.
Material Properties S235 | |
---|---|
Mass density ρ | 7.85 × 10 −6 kg/mm 3 |
Young’s modulus E | 210,000 MPa |
Poisson’s ratio ν | 0,3 |
Shear modulus D | 81,000 MPa |
Yield stress σY | 235 MPa |
Ultimate tensile strength σT | 360 MPa |
Table 3. Калибровочные коэффициенты.
Таблица 3. Калибровочные коэффициенты.
Глубина отверстия (мм) | ASTM E837-13a (линейно-упругое поведение материала) | Линейно-упругое поведение материала FEM | FEM Elastic-Plastic Material Behavior | ||||||||||
---|---|---|---|---|---|---|---|---|---|---|---|---|---|
Hole Depth (mm) | Calibration Coefficient a | Calibration Coefficient b | Calibration Coefficient a | Calibration Coefficient b | Calibration Coefficient a | Calibration Coefficient b | |||||||
0,1 | 0,015 | 0,028 | 0,016 | 0,028 | 0,013 | 4 99399 0,0497 0,0134 98397 0,0160476 | 0.![]() | 0.036 | 0.066 | 0.037 | 0.065 | 0.029 | 0.078 |
0.3 | 0.059 | 0.110 | 0.058 | 0.108 | 0.043 | 0.119 | |||||||
0.4 | 0.083 | 0.155 | 0.079 | 0.153 | 0.056 | 0.157 | |||||||
0.![]() | 0.104 | 0.200 | 0.097 | 0.197 | 0.068 | 0.191 | |||||||
0.6 | 0.124 | 0.242 | 0.113 | 0.238 | 0.079 | 0.223 | |||||||
0.7 | 0.140 | 0.280 | 0.125 | 0.276 | 0.089 | 0.252 | |||||||
0.![]() | 0.154 | 0.314 | 0.135 | 0.309 | 0.099 | 0.280 | |||||||
0.9 | 0.165 | 0.343 | 0.143 | 0.338 | 0.109 | 0.306 | |||||||
1 | 0.173 | 0.370 | 0.148 | 0.363 | 0.119 | 0.331 |
© 2019 авторами.

Регулируемый шаблон для фрезерования розетки и резонатора
Перейти в конец галереи изображений
Перейти в начало галереи изображений
расширение роутера. Универсальный инструмент для мастеров!
Надставка изготовлена из высококачественного прозрачного плексигласа для оптимального обзора вашего проекта. Он поставляется с предварительно просверленными отверстиями для обычных оснований фрезеров, таких как Bosch, Makita и Dremel. С помощью прилагаемого внутреннего компонента вы можете легко просверлить дополнительные отверстия для другого основания, если это необходимо.
Радиус круга задается бесступенчато на пинхоле. Для больших кругов его легко перевернуть, чтобы получить диаметр от 6 до 32 см и все, что между ними. Поставляется с булавкой 5 мм для размещения в центральной точке вашего круга.
Мы также добавили съемную опору по высоте для оптимальной устойчивости при использовании этого приспособления в сочетании с приспособлением для подготовки розетки и приспособлением для фрезерования
Детали
Используйте:
Загрузите эти рекомендации для настройки шаблона или когда вы хотите отрегулировать другую базу фрезера.
Приспособление для фрезерования розетки и звукового отверстия
Нарисуйте центральную точку звукового отверстия или розетки и просверлите отверстие диаметром 5 мм.
Определите нужный диаметр (указанный радиус x2). Расстояние от оси до оси. Пожалуйста, помните о диаметре вашего сверла.
Установите расстояние, ослабив внешние болты, и двигайте их до тех пор, пока центральная линия не достигнет нужного значения. Безопасный. Если вы хотите большего диаметра, открутите и переверните.
Снимите опору по высоте, отвинтив черные винты с шестигранной головкой. Установите приспособление на основание фрезера, поместите фрезу и установите высоту.
Вставьте 5-миллиметровый штифт в отверстие шаблона.
Удерживая фрезер над поверхностью, дайте штифту войти в отверстие, пока фреза все еще находится немного над поверхностью.
Включите фрезер и дайте ему двигаться прямо вниз, пока шаблон не станет плоским на поверхности.
Двигайтесь с легким нажимом в форме круга, пока не станете полностью круглым.
В сочетании с подготовкой Rosette и шаблоном для фрезера
Определите нужный диаметр (указанный радиус x2). Расстояние от оси до оси. Пожалуйста, помните о диаметре вашего сверла.
Установите расстояние, ослабив внешние болты, и двигайте их до тех пор, пока центральная линия не достигнет нужного значения. Безопасный. Если вы хотите большего диаметра, открутите и переверните.
Убедитесь, что прилагаемая опора по высоте расположена для дополнительной поддержки при фрезеровании.
Установите приспособление на основание фрезера, поместите фрезу для деталей и установите высоту, учитывая, что у фрезера есть дополнительная высота.
Вставьте 5-миллиметровый штифт в отверстие приспособления.
Удерживая фрезер над поверхностью, дайте штифту войти в центральное или смещенное от центра отверстие приспособления для подготовки до тех пор, пока фреза не будет находиться немного над поверхностью.
Включите фрезер и дайте ему двигаться прямо вниз, пока шаблон не станет плоским на поверхности.
Двигайтесь с легким нажимом в форме круга, пока не станете полностью круглым.
Как удлинитель маршрутизатора
Снимите опору по высоте, открутив винты с черным шестигранным ключом. Установите приспособление на основание маршрутизатора.
Дополнительная информация
Артикул | 116028 |
---|---|
Марка | Гитарные товары TLC |
Размер | 235x130x21 мм |
Тип | Розетка |
Материал | Оргстекло |
Вес | 179 г |
Товарная единица | Шт.![]() |
отзывов
Напишите свой отзыв
Вы пишете отзыв о: Фрезерный шаблон Rosette and Soundhole, регулируемыйПсевдоним
Резюме
Обзор
Доставка
В Guitar Goods мы делаем все возможное, чтобы все было максимально просто и весело, например:
Быстрая доставка Все, что заказано до 12:00 по центральноевропейскому времени, отправляется в тот же день. Мы держим собственный склад. Если чего-то, к сожалению, нет в наличии, вы можете нажать кнопку с товаром, и мы отправим вам электронное письмо, когда он появится в наличии.
Бесплатная доставка при заказе на сумму 110 евро в Нидерландах, или скидка 5,50 евро при доставке за границу. При меньшей сумме заказа стоимость доставки составляет 5,50 евро в Нидерландах. Тарифы для других стран указаны в обзоре заказа перед оплатой.
14 дней на месте для оценки вашей покупки. Если передумаете, не беда! Заполните форму возврата и верните товары в их первоначальном состоянии. Подробности нашей политики можно найти здесь. Пользовательские товары или товары, настроенные для вас, не могут быть возвращены.
Шоппойнты предоставляются при каждом заказе просто потому, что мы довольны вами. Вы можете потратить свои баллы на следующий заказ, чтобы оплатить (часть) вашего следующего заказа. Сладкий!
Пользовательские опции . В качестве стандарта мы предлагаем несколько пользовательских опций, таких как полноцветные, черные, белые, серебряные и золотые наклейки, а также индивидуальные вставки в вашем дизайне, гравировку на металле или пластике или как насчет лазерного рисунка на дереве! если есть что-то еще, что вы ищете, пожалуйста, свяжитесь с нами. Мы всегда заинтересованы и поможем вам, где мы можем.
Сравнение метода кольцевого керна и метода сверления отверстий, используемых для определения остаточных напряжений
1. Введение
Остаточные напряжения [4] – это напряжения, существующие в объектах без внешней нагрузки. Эти напряжения создаются технологическими процессами или предыдущим нагружением. В принципе все технологические процессы – прокатка, формовка, термическая обработка и т.д. создают в изготавливаемых изделиях остаточные напряжения. Остаточные напряжения играют в прочности конструкции ту же роль, что и обычные механические напряжения, но если напряжения от внешних нагрузок можно рассчитать с определенной точностью, то остаточные напряжения трудно предвидеть, и поэтому очень важно иметь надежный метод, позволяющий измерять их непосредственно в конструкции с минимальным ущербом для нее.
Методы кольцевого керна и сверления отверстий являются полуразрушающими методами, используемыми для количественного определения основных остаточных напряжений в пределах заданной глубины материала. Оба метода являются относительно быстрыми и удобными на практике. Образец не разрушается полностью во время измерения и во многих случаях может быть использован для другого применения.
2. Метод сверления отверстий
Наиболее широко используемым полуразрушающим методом измерения остаточного напряжения является метод сверления отверстий.0532 [1] . Принцип этого метода заключается в наложении тензометрической розетки на верхнюю часть исследуемой детали и последовательном сверлении отверстия в центре розетки. Эта процедура нарушает внутреннее равновесие сил и моментов и вызывает искажения вблизи просверленного отверстия, которые измеряются розеткой тензодатчика. Оцениваются измеренные деформации и с использованием полученной теории определяются ход и величина остаточных напряжений. Этот метод считается полудеструктивным, так как просверливаемое отверстие (диаметром 2-4 мм на глубину 2-4 мм) незначительно и легко поддается коррекции, например, ввинчиванием шурупа, штифта, сваркой и т. д. Небольшой нарушение поверхности не влияет на функциональность компонентов. Теория метода сверления отверстий основана на решении пластины со сквозным отверстием. Для определения остаточных напряжений методом сверления отверстий можно использовать, например, Систему СИНТ — МТС 3000, отображающую прогресс в определении остаточных напряжений методом сверления отверстий Рисунок 2 [6, 8] .
Рис. Ур 1 . Принцип метода сверления отверстий
Рисунок 2. Система СИНТ-МТС 3000
3. Метод кольцевого керна
Метод кольцевого керна, несомненно, менее распространен, чем метод сверления отверстий. Помимо того, что он является более «разрушающим», тот факт, что фактическое выполнение теста является более сложным, ограничивает развитие метода. Он имеет значительное сходство с методом сверления отверстий, фактически эти два метода дополняют друг друга, поскольку они основаны на одних и тех же математических уравнениях для расчета остаточных напряжений на основе измеренных деформаций, хотя методы явно имеют совершенно разные калибровочные константы и кривые.
Метод кольцевого сердечника можно использовать для определения однородных и неоднородных остаточных напряжений. Принципы этого метода основаны на методе сверления отверстий, но вместо сверления отверстия через середину тензометрической розетки вокруг розетки [2, 3] фрезеруется насечка, имеющая размеры примерно: D= 18 мм, d = 14 мм, h = от 4 до 5 мм Рис. 3. Это означает, что метод кольцевого керна является более разрушительным, чем метод сверления отверстий, но все же является полуразрушающим.
Небольшая кольцевая канавка на поверхности образца фрезеруется концентрически вокруг тензометрической розетки, оставляя верхнюю часть сердечника отделенной от окружающего материала. Это разделение вызывает релаксацию остаточных напряжений, присутствующих в сердечнике, что выражается в деформации сердечника. Эти деформации могут быть измерены тензорезисторами, предназначенными для измерения ослабленных деформаций по методу Ring-Core. Кольцевая канавка может быть обработана подходящей фрезой, такой как кольцевая пила.
Этот метод менее чувствителен к ошибкам, связанным с позиционированием режущего инструмента относительно тензорезистора, и позволяет более точно измерять напряжение вплоть до предела текучести материала.
Рисунок 3. Метод кольцевого ядра
Фрезерование производится для выбранных шагов, и на каждом шаге записываются измеренные значения. Процесс повторяется, обычно на глубину до 4 мм. Полученные данные обрабатываются в подходящей процедуре оценки (например, интегральный метод, инкрементальный метод и т. д.). Кольцевой метод позволяет проводить измерения на большей глубине за счет снятия фрезерованного кольца. Затем на поверхность наклеивается новая тензометрическая розетка и фрезеруется новое кольцо. Это может продолжаться до глубины 25 мм.
Предположения, li имитации и применимость R ing- C рудные методы:
Остаточными напряжениями в направлении, перпендикулярном поверхности материала, пренебрегают.
Остаточные напряжения постоянны по всей глубине или шагам фрезерования.
В процессе фрезерования не допускается придание исследуемому материалу дополнительных остаточных напряжений.
Материал имеет однородную структуру и линейно-упругий.
Разгруженная поверхность материала (возникает плоскостное поверхностное натяжение).
Поверхность исследуемого материала плоская.
Влияющие факторы:
Размеры образца достаточно велики, чтобы толщина материала позволяла создать глухую канавку.
Точка измерения должна располагаться на достаточном расстоянии от геометрических характеристик (прилегающих отверстий, радиуса).
Центр тензометрической розетки должен совпадать с геометрическим центром паза.
Цилиндричность и перпендикулярность сердечника относительно плоскости поверхности
Тип тензометрической розетки — геометрия и размер измерительных решеток тензометра.
Тип метода, который используется для оценки остаточных напряжений.
Основные этапы определения остаточных напряжений методом R ing- C руды:
провода под пайку).
Защитите розетку тензодатчика и провода.
Поместите механическую часть инструмента на нужную область.
Отцентрируйте коронную фрезу и розетку тензодатчика.
Установите нулевую глубину.
Кольцевая канавка вокруг тензометрической розетки с шагом в глубину, и на каждом шаге значения деформации измеряются по трем сеткам.
Предыдущий шаг повторяется для достижения минимальной глубины 4 мм.
Полученные штаммы обрабатываются наиболее подходящим методом [4] .
Примером системы, используемой для определения остаточных напряжений методом кольцевого сердечника, является система MTS3000 Ring-Core, рис. 4.
Рисунок 4. Система SINT MTS 3000 Ring-Core
4. Сравнение метода кольцевого керна и метода сверления отверстий
Метод кольцевого керна моложе, но с точки зрения теоретического и практического применения аналогичен методу сверления отверстий. Основное различие между этими двумя методами показано на рис. 5. В первом случае мы просверливаем отверстие через центр тензометрической розетки, а во втором случае делаем годовую канавку вокруг приклеенной тензометрической розетки.
Рисунок 5. Разница между полуразрушающими методами
Метод кольцевого керна более чувствителен по сравнению с методом сверления отверстий, так как предполагает почти полное снятие поверхностных напряжений. Однако размер кольцевой канавки относительно велик, что приводит к гораздо большему повреждению, чем метод сверления отверстий, который позволяет более локализовать остаточное напряжение. Несмотря на потенциальные недостатки, метод сверления отверстий является наиболее распространенным выбором. Метод хорошо отработан экспериментально и теоретически.
Различие между этими двумя методами также заключается в используемой тензометрической розетке. Эти методы обычно используются для измерения остаточных напряжений в металлах, но они также полезны для других материалов, например керамики, полимеров и т. д. [7] .
В следующих таблицах (таблица 1, таблица 2, таблица 3, таблица 4) обобщены основные различия между методом кольцевого керна и методом сверления отверстий.
Таблица 1. Сравнение метода Ring-Core и метода сверления отверстий (общая характеристика)
Таблица 2. Для равномерных остаточных напряжений
Таблица 3. Для неравномерных остаточных напряжений
Таблица 4. Сравнение чувствительности, измеримости и влияния температуры
Преимущества метода кольцевого керна:
Возможность измерения остаточного напряжения на большей глубине.
Подходит для измерения крупнозернистых материалов.
Менее чувствителен к ошибкам, вызванным неточным расположением фрезы относительно середины тензометрической розетки.
Измерение возможно до величины предела текучести материала.
В процессе фрезерования вводимые дополнительные остаточные напряжения не оказывают такого большого влияния на измерение остаточных напряжений, как при сверлении отверстий.
Измеренный сигнал как минимум больше, чем при методе сверления отверстий.
Недостатки метода Ring-Core :
Необходимость определения калибровочных коэффициентов в зависимости от механических свойств материала, геометрии фрезерованного стержня, общей глубины кольца, типа тензометрической розетки.
Метод кольцевого керна не стандартизирован, в отличие от метода сверления отверстий.
Ограничения применимости метода и необходимость учитывать факторы, влияющие на точность.
Длительный процесс измерения.
4.1. Тензометрические розетки, используемые для измерения остаточных напряжений
При сверлении отверстий и методе кольцевого керна используются различные типы тензометрических розеток. Сравнивая эти два метода, становится очевидным, что в методе сверления отверстий мы сверлим до середины тензометрической розетки, а в методе Ring-Core мы фрезеруем вокруг тензометрической розетки. Компания по производству тензометрических розеток, например, Hottinger Baldwin Messtechnik GmbH (HBM), производит тензометрические розетки для обоих методов. Различные типы, используемые в этих методах от компании HBM, показаны и описаны в следующем разделе 9.0532 [9] .
Тензометрические розетки, используемые для метода кольцевого сердечника Рис. 6:
XY 51:
Мы используем эту тензометрическую розетку, когда знаем направление главных напряжений.
Размеры: a = 5 мм, b = 2,5 мм, c = 12 мм, сопротивление 350 Ом.
Размеры: a = 5 мм, b = 2,5 мм, c = 12 мм, сопротивление 350 Ом
Рисунок 6 . Розетки тензодатчиков, используемые для метода кольцевого сердечника
Тензометрические розетки, используемые для метода сверления отверстий :
Для метода сверления отверстий мы можем использовать три основных типа тензометрических розеток, определенных в ASTM E 837 [9] .
Тип A:
Тензодатчик для общего применения, например. RY61 производства HBM (рис. 7 а)
Размеры: a = 1,5 мм, b = 0,8 мм, d = 12 мм, сопротивление 120 Ом
Рисунок 7 . Тензорезисторы для метода сверления отверстий
Тип B:
Все сетки расположены в одном направлении (рис. 7b).
Мы используем эту тензометрическую розетку для бурения вблизи препятствий.
Тип C:
Для измерения деформации с высокой чувствительностью и в тех случаях, когда требуется высокая температурная стабильность (рис. 7 c).
Имеет три пары решеток, расположенных друг напротив друга, которые соединены полумостовыми схемами.
5. Заключение
В этой статье мы кратко упомянули о возможности определения остаточных напряжений полуразрушающими методами, особенно с использованием метода сверления отверстий и метода кольцевого керна. Это краткое изложение результатов может помочь экспериментатору правильно решить, какой из этих двух методов в его случае более уместен.
Благодарность
Работа выполнена при поддержке Министерства образования Фонда Словакии в рамках гранта VEGA № 1/0289/11, VEGA № 1/0937/12 и АПВВ-0091-11.
Ссылки
[1] | Стандарт ASTM E837-08. | ||
In article | |||
[2] | Civín, A: Komplexní teoretická analýza metody sloupku pro zjišťováni zbytkových napätí, Rigorózni práce, 2010. | ||
In article | |||
[3] | Civín, A, Vlk, M: Theoretical Analysis of Ring-core Method for Residual Strees Detemination, ANSYS 2009. | ||
In article | |||
[4] | Валентини Э.![]() | ||
0498 | |||
[5] | Требуня Ф., Шимчак Ф.: Приручка экспериментальной механики, Кошице 2007, ул. | ||
в статье | |||
[6] | TREBUňA, F, FKAN. | ||
В статье | |||
[7] | SINT TECHNOLOGY, Ring-core operating and maintenance, Manual, Callenzo — Italia, 2012. | ||
In article | |||
[8] | SINT TECHNOLOGY — Центр передового опыта в области измерений [онлайн], http://www.![]() | ||
в статье | |||
[9] | Hottinger Baldwin Messtechnik Gmbhh..com. | ||
в статье | |||
Розетка — Гитары Джеймса Листера
9
. Розетка на изображении ниже имеет центральный рисунок «концевого зерна», несколько линий шпона и две линии полуелочки (или веревки). Некоторые мастера сооружают всю розетку на приспособлении, а затем вставляют ее в деку целиком, но в описанном здесь методе каждый компонент вставляется отдельно, начиная с рисунка торцевых волокон в центре розетки.
.
Узор торца
Узор торца состоит из квадратных полос разного цвета толщиной 1 мм, склеенных вместе в виде узора. В более детализированных розетках для создания более тонкого рисунка используется шпон толщиной 0,6 мм (или тоньше), но для их изготовления требуется гораздо больше работы. Полосы толщиной 1 мм склеиваются в два этапа, образуя «бревно», из которого будут вырезаться отдельные «плитки» и вкладываться в деку.
Шаблон состоит из плиток размером 3 x 4 квадрата размером 1 мм. Сначала склейте вместе каждый ряд из 4 линий. Длина линий должна быть не менее 300 мм. Используйте две 300-миллиметровые линейки (обернутые лентой и/или бумагой, чтобы защитить их от клея), чтобы скрепить линии вместе, и закрепите их малярным скотчем, пока клей не высохнет (около 30 минут должно быть достаточно). После высыхания соскребите излишки клея, прежде чем склеивать 3 части вместе, чтобы сформировать бревно. Убедитесь, что части склеены в правильном порядке и точно выровнены. Это может помочь сделать небольшое приспособление, чтобы выровнять детали во время их склеивания. Оставьте бревно сохнуть на ночь.
Теперь бревно нужно разрезать на плитки толщиной примерно 2,5 мм каждая. Используйте пилу с мелкими зубьями и приспособление, чтобы разрезы были ровными, а все плитки были одинаковой толщины. Храните плитки в безопасном месте, пока не будете готовы вставить их в деку.
.
Линии шпона
По обеим сторонам торцевого рисунка и на каждом краю розетки есть группы из 5 линий шпона. Вы можете выбрать разные цвета для этих линий, но старайтесь выбирать цвета, которые будут сочетаться с общим дизайном гитары, т. е. сочетаться со шпоном, используемым в пластике, и верхней отделкой. Линии шпона легче укладывать, если они склеены попарно или по трое. Отдельные линии довольно хрупкие, но больше 3 или 4 будет трудно согнуть. Так как в каждой группе 5 линий, лучше всего склеить их парой и группой из 3. Склейте полоски шириной около 25 мм и длиной 400 мм. После высыхания можно отрезать полоски необходимой ширины 2,5 мм. Используйте гибочное железо, чтобы согнуть склеенные вместе линии шпона в круги примерно подходящего диаметра для их положения в розетке.
.
Елочка
Последним компонентом, который нужно сделать, является половинка елочки (или веревка). Они изготовлены из шпона толщиной 0,6 мм, и, опять же, вы можете выбрать цвет/древесину, которую используете.
Вы будете использовать приспособление для изготовления елочки, которое предназначено для изготовления елочки такой длины, чтобы ее можно было пройти по всей розетке без каких-либо соединений, что значительно упрощает процесс. Для этого нужно использовать всю длину приспособления.
Приклейте шпон выбранных вами цветов в правильной последовательности. Полоски должны быть шириной 30 мм, а общая длина должна быть около 1 м (это можно сделать из 2 или 3 более коротких полос). Используйте клей Blue Titebond, который обладает чуть лучшей термостойкостью при изгибе.
Когда клей высохнет, обрежьте полоски шириной 25-28 мм. Затем полоски следует разрезать на короткие отрезки – они должны быть нарезаны как можно более точно под прямым углом и одинаковой длины. Точная длина будет зависеть от угла, который вы хотите для елочки, и количества шпона (цвета), который вы использовали, но она должна быть где-то около 30-35 мм. Если все кусочки не будут точно одинаковой длины, то более короткие кусочки не будут удерживаться достаточно плотно, и у вас будут пробелы в готовой елочке.
Затем установите ширину шаблона «елочка». Точная ширина зависит от длины полосок, на которые вы нарезали полоски, и от угла, под которым они сплетаются в елочку, но она должна быть от 8 до 12 мм. Помните, что чем меньше угол (то есть чем меньше зазор), тем легче будет согнуть елочку, не сломав ее. Убедитесь, что кондуктор установлен так, чтобы зазор был одинаковым по всей длине.
Теперь вам понадобятся два клина, чтобы удерживать елочку на концах приспособления. Клинья должны плотно входить в зазор приспособления, а угол должен соответствовать углу, необходимому для елочки.
Вставьте первый клин в один конец приспособления – при необходимости зафиксируйте его.
Плотно прижмите первую часть елочки к клину, затем нанесите клей на одну поверхность следующей детали. Плотно прижмите склеенную сторону к первой части. Каждую часть нужно очень плотно прижать к последней части, чтобы не было зазоров.
Повторяйте, пока не будут использованы все детали или пока не дойдете до другого конца приспособления.
Сильно прижмите второй клин к последнему кусочку елочки и при необходимости зажмите его.
НЕ НУЖНО зажимать приспособление. В этом нет необходимости, если вы сделали все части одинаковой длины и плотно прижали каждую часть к последней. Зажатие зажимного приспособления может привести к его поломке!
Оставьте клей сохнуть на ночь.
После высыхания осторожно снимите с приспособления. Зачистите края рубанком – полоса должна быть шириной около 25 мм.
Теперь аккуратно сошлифуйте одну поверхность елочки, пока она не станет идеально плоской и квадратной. Вы можете легко увидеть, не является ли поверхность квадратной, так как соединения между разными цветами не будут квадратными с краями.
Когда вы довольны этой стороной, вам нужно выровнять, отшлифовать и/или очистить другую сторону, чтобы достичь желаемой толщины. Если у вас все еще есть 5 мм или больше, вероятно, стоит сначала обрезать его на ленточной пиле или даже разрезать на две части, если он достаточно толстый. Окончательная толщина должна быть около 2,5 мм. Сконцентрируйтесь на том, чтобы получить одинаковую толщину по всей длине и ширине елочки.
Теперь вы можете разрезать елочку на полоски толщиной 2,5 мм, чтобы вставить их в деку.
Будьте очень осторожны, сгибая полоски елочкой, так как их очень легко сломать! В общем, если вы делаете елочку с очень малым углом (скажем, 10–15 градусов), вероятность того, что она сломается при изгибе, гораздо меньше, чем если бы угол был больше (30–40 градусов).
Теперь у вас должны быть все компоненты, необходимые для розетки.
.
Вставка компонентов розетки
Рекомендуется прикрепить деку к толстой плоской опорной доске и удерживать ее прижатой к этой доске, пока розетка не будет завершена. Просверлите отверстие диаметром ¼ дюйма в опорной доске для круглого штифта. Совместите это отверстие с отверстием в деке, вставьте штифт, чтобы зафиксировать его на месте, затем зажмите конец деки с помощью 2 зажимов и плоского уплотнителя.
Первой частью для инкрустации будут торцевые плитки. Сначала вычислите радиус внутренней кромки конечного узора волокон. На чертеже Торреса это 11,5 мм от внутреннего края розетки. Вам нужно добавить к этому радиус звукового отверстия (43 мм) и зазор между краем звукового отверстия и розеткой (3 мм). Отметьте это расстояние (57,5 мм) от центра резонаторного отверстия на центральной линии деки, где она будет закрыта накладкой грифа.
Установите круглую фрезу на этот радиус, убедившись, что скос лезвия направлен в сторону отходов разреза. Лезвие необходимо перевернуть, чтобы сделать надрез по внешнему краю канала, как показано ниже:
Лезвие круглого резака должно выступать на 2,0 мм из основания круглого резака. Первый разрез должен быть сделан очень легко, с достаточным усилием, чтобы разрезать волокна на поверхности деки. Постепенно режьте глубже, пока не достигнете максимальной глубины (2,0 мм).
Если лезвие достаточно острое, вы сможете получить чистый срез по всей окружности в одном направлении, но иногда безопаснее резать только по направлению волокон. Для этого вам нужно разделить круг на 4 квадранта и сделать четыре отдельных разреза для каждого края, причем в направлениях, показанных на схеме ниже.
Теперь отметьте ширину торцевых плиток от края, который вы только что обрезали, снова по центральной линии, где она будет закрыта накладкой грифа. Вы можете использовать эту область, чтобы сделать пробные пропилы, чтобы получить точную ширину канала, прежде чем делать пропил по всему периметру. Прорежьте на полную глубину на небольшом расстоянии от центрального соединения и удалите отходы между двумя разрезами с помощью долота или ручного фрезера. Возьмите одну из плиток и проверьте ее посадку в канале. Если он слишком тугой или свободный, отрегулируйте радиус круговой фрезы по мере необходимости и сделайте еще один короткий разрез. Снова проверьте соответствие плитки. У вас должно быть место в области, которая будет закрыта грифом, чтобы сделать 4 пробных разреза. Когда вы довольны тем, что подходит идеально, продолжайте резать по кругу, снова начиная с очень легкого разреза и медленно продвигаясь до максимальной глубины.
Ручной фрезер является идеальным инструментом для удаления отходов из канала, но можно использовать и долото. Будьте осторожны, чтобы не прорезать слишком глубоко или не прорезать края канала. Старайтесь резать по зерну, чтобы не вырвать дно канала. Глубина канала должна быть чуть меньше 2 мм — если вы попытаетесь пройти на ту же глубину, что и установка лезвия круглой фрезы, будет трудно удалить отходы материала в углах. Глубина должна быть не менее 1,5 мм.
Плитки большего размера рекомендуется начинать укладывать с центрального соединения деки в нижней части розетки, чтобы рисунок розетки был симметричным, но с маленькими плитками, используемыми для этого дизайна, лучше менее важно. Если у вас достаточно плиток, вы можете укладывать их по всему каналу, но не обязательно размещать плитки в области, которая будет закрыта накладкой грифа. Нанесите клей в канал и начните укладывать плитки, убедившись, что они плотно прилегают друг к другу, чтобы не было зазоров. Когда все плитки будут приклеены, оставьте на ночь, чтобы клей высох.
После полного высыхания выровняйте и/или соскребите плитку вровень с декой. Это будет проще, если все плитки будут нарезаны одинаковой толщины. Если вы используете рубанок, убедитесь, что он острый и установлен достаточно точно, так как вы будете строгать по торцевым волокнам, и есть риск выдергивания плитки, если рубанок затупится или установлен слишком грубо. При необходимости обработайте шлифовальным блоком.
Следующими компонентами для вставки являются линии шпона. Установите диаметр кругового фрезы так, чтобы он едва касался внешней кромки торцевых плиток, убедившись, что скос лезвия находится на стороне отходов (от плитки). Глубина по-прежнему должна быть 2 мм. Разрежьте со всех сторон, начиная с очень легкого разреза, как и раньше. Отметьте другую сторону канала на правильной ширине для 5 линий шпона, которая должна быть около 3 мм, но сверьтесь с фактическими компонентами. Переверните лезвие круглого резака так, чтобы скос находился на стороне отходов для второго реза. Как и прежде, вы можете использовать область, которая будет закрыта накладкой грифа, чтобы сделать пробный разрез, чтобы проверить соответствие 5 линий шпона (одна деталь с 2 шпонами, а другая с 3). Прилегание должно быть плотным, без зазоров, но не настолько плотным, чтобы виниры не могли войти в канал после нанесения клея.
Если вы довольны подгонкой, продолжайте резать по кругу. Удалите отходы долотом или ручным фрезером на глубину чуть менее 2 мм. Проверьте соответствие линий шпона в канале и обрежьте их до нужной длины. Если они слишком тугие, вы можете немного сжать линии шпона полировщиком (или паста-машиной, если она у вас есть!). Это поможет им легче установиться, и они снова расширятся, чтобы соответствовать каналу, когда наносится клей.
Нанесите клей по всему периметру желоба и маленькой кистью нанесите клей на углы. НЕ наносите клей на виниры — в этом нет необходимости, и это затруднит их установку в канал. Вставьте линии шпона в канал, убедившись, что они полностью вдавлены. Оставьте сохнуть на ночь.
После высыхания выровняйте и соскребите линии шпона заподлицо с декой. Теперь повторите процесс для линий шпона на другой стороне торцевых плиток. Оставшиеся каналы можно вырезать по 2 за раз, поэтому затем вы можете вырезать оба канала для полу-елочки. Снова используйте область под грифом для пробных надрезов и вклейте компоненты «елочкой» в каналы.
Последние два набора линий шпона образуют внешний и внутренний края окончательной розетки, поэтому важно сделать эти разрезы как можно более чистыми. Убедитесь, что лезвие кругового резака острое, и сделайте эти окончательные надрезы очень осторожно, вырезая вдоль волокон деки, в квадрантах, как показано на диаграмме выше. После того, как окончательные компоненты установлены и клей высох, выровняйте, соскребите и отшлифуйте розетку заподлицо с декой. После окончательной шлифовки края должны быть чистыми и острыми, без следов засохшего клея на деке или розетке.
Теперь отшлифуйте всю верхнюю поверхность деки. Прежде чем приступить к утолщению деки, вы должны убедиться, что на верхней поверхности нет надрывов, следов от плоскости или других дефектов, которые впоследствии нужно будет отшлифовать.
404 ОШИБКА WOODWEB
404 ОШИБКА WOODWEB Поиск по всему сайту
Поиск в каталоге продуктов
Поиск в базе знаний
Поиск по всем форумам
Поиск по биржевому оборудованию
Поиск биржи пиломатериалов
Поиск вакансий
Поиск объявлений
Новости отрасли
Поиск Аукционы, распродажи и специальные предложения
Календарь событий поиска
————————
Поиск отдельных форумов
Клеи
Архитектурная мастерская
Бизнес
Изготовление шкафов
САПР
ЧПУ
Пыль/Безопасность/Завод
Отделка
Лесное хозяйство
Мебель
Монтаж
Ламинат/твердая поверхность
Распиловка и сушка
Обработка массивной древесины
Добавленная стоимость Древесина Прод.![]() |
Главная || Новые посетители | Карта сайта |
Извините… введенный вами адрес недоступен. Скорее всего, вы ввели неверный адрес (URL) Список ссылок для навигации по сайту Все комментарии направляйте по адресу: [email protected] Тип ошибки: 404 Ресурсы Главная Программное обеспечение и мобильные приложения Аукционы, Распродажи и специальные предложения — Знак оповещения о продажеПромышленность Новости Деревообработчики Каталог Пиление и Справочник по сушке Wood Doctor Книжный магазин Пиломатериалы/древесина/разное КалькуляторыМедиа-кит О WOODWEB Пользовательское соглашение и условия
использования Стать
Член Каталог продукции Каталог продукции Работа Возможности и услуги по деревообработке Ламинирование и наплавка Пиломатериалы
и Фанера Машины Молдинги
и столярные изделия Электроинструменты Планы и публикации Завод Техническое обслуживание и управление Распиловка и сушка Поставщики Инструменты Шпон Токарная обработка дерева ГалереиПроект ГалереяГалерея лесопилки Магазин Галерея Галерея оборудования Последние изображения Галерея ФорумыПоследние сообщения со всех форумовКлеи Архитектура Деревообработка Бизнес и управление Монтаж столярных и столярных изделий Изготовление столярных изделий CAD Коммерческая сушка в печи ЧПУ Сбор пыли, Безопасность и завод Эксплуатация Профессиональная отделка Лесное хозяйство Профессиональная мебель Изготовление Ламинирование и Наплавка массива Распиловка и Сушка Заводское строительство Оборудование Массивная древесина Механическая обработка Обработка древесины с добавленной стоимостью Шпон WOODnetWORK Последние обменыСообщения со всех биржВакансии и Services Exchange – Job-GramLumber Exchange — Lumber-GramОбмен машин — Machinery-GramБиржа объявлений База знанийБаза знаний: Поиск или просмотрКлеи, склеивание и ламинирование – Клеи и склеиваниеАгенты – Склеивание и зажимное оборудованиеАрхитектурное оборудование Столярные изделия – Пользовательские Столярные изделия— Двери иОкна – Полы– Общие– Столярные изделия Установщик— Токарный станок Токарная обработка– Погонаж– Столярные работыРеставрация — Лестницы— Наличие на складеПроизводство Бизнес Изготовление шкафов Отделка Лесное хозяйство Мебель Ламинирование
и Solid Surfacing Пиломатериалы
и Фанера Обработка Дерево
Инженерное дело |
Экспериментальный анализ остаточных напряжений с помощью сверла
В этой статье описывается применение автоматической системы измерения остаточного напряжения путем сверления отверстий в полимерных молдингах . Аксессуар был разработан для Рестан МТС3000, автоматической измерительной системы, по существу состоящей из тихоходного электродвигателя и электронной системы управления .
1. Введение
За последние пятьдесят лет индустрия пластмасс значительно развилась, опередив сталелитейную промышленность, в том числе и в технических приложениях. Это привело к новым синтетическим веществам , постепенно заменяющим традиционные материалы, и к формальному переосмыслению структур, эргономичных форм и производственных процессов.
Использование этих материалов стало настолько распространенным, так это то, что они дешевы, легки, просты в обработке и их можно 0190 разработать желаемые механические свойства . Поэтому требуется все более точная и всесторонняя механическая характеристика, и именно в этом контексте возникает необходимость знать и изучать значение остаточных напряжений , вызванных процессами механической обработки в этих материалах.
Течение расплава полимера, распределение давления, неравномерное температурное поле и распределение плотности вызывают остаточные напряжения в полимерных литьевых формах и эти напряжения влияют на механические свойства пластиковых деталей , могут изменить окончательную форму и значительно сократить ожидаемый срок службы изделия , в дополнение к увеличению вероятности нестабильности размеров и растрескивания под воздействием окружающей среды . Хотя остаточные напряжения обычно обнаруживаются в пластмассах, их величину трудно предсказать, поскольку она зависит от широкого диапазона переменных, включая конструкцию пресс-формы, материал и параметры обработки. Следовательно, важно иметь надежный метод оценки напряжений, существующих в пластмассовых компонентах .
Метод тензорезистора со сверлением отверстий позволяет измерять остаточное напряжение в широком диапазоне пластиковых отливок . Его преимущество состоит в том, что измерений могут быть выполнены на меньшей площади . Специальная тензометрическая розетка приклеивается к поверхности образца, и отверстие просверливается точно через центр розетки . Деформации, измеренные на поверхности, соответствуют напряжения ослабли в процессе бурения. Используя измеренные деформации и соответствующие модели (например, ASTM E837), можно рассчитать напряжений вдоль двух главных осей и их направление .
2. Измерительная система
Рис. 1.: a) модифицированная система MTS3000 для измерения остаточных напряжений в пластмассахb) специально разработанный сверлильный инструмент
c) сверло с 2 режущими кромками
Механическая установка системы сверления показан на рис. 1а . Он основан на консолидированной системе Рестан — МТС 3000 , разработанной SINT Technology и продаваемой в сотрудничестве с HBM.
На рис. 1b показан специально разработанный сверлильный инструмент , который позволяет сверлить отверстия со скоростью менее 200 об/мин . Эта скорость сводит к минимуму местный нагрев и остаточные напряжения , возникающие в анализируемом материале. Режущий инструмент показан на рисунок 1с . Это спиральное сверло с двумя режущими кромками диаметром 1,6 мм, перпендикулярными направлению движения, которое производит отверстия с плоским дном при небольшой подаче.
Система бурения приводится в действие и автоматически управляется электронной системой управления и программным обеспечением для управления бурением, что делает процесс бурения полностью автоматизированным . Весь измерительный прибор может управляться дистанционно: этот вариант целесообразен, так как позволяет свести к минимуму внешние воздействия оператора в процессе измерения.
На рис. 2 показана трехэлементная розетка тензометрического датчика предварительно смонтированного типа, которая предпочтительнее для испытаний, поскольку она не только ускоряет ее установку, но и предотвращает выделение тепла при сварке проволоки . Остаточные напряжения, существующие в испытуемом компоненте, определяют, исходя из значений деформации, измеренных сетками тензодатчика, наклеенными на поверхность компонента.
Полученные данные были обрабатывал с использованием специальной версии программного обеспечения EVAL, разработанного SINT Technology srl, специально для обработки деформаций в пластиковых материалах. В этой версии применяется исходная оптимизированная полиномиальная интерполяция измеренных деформаций . Измерения деформации обрабатываются в соответствии с положениями стандарта ASTM E837.
Рисунок 2. Розетка: HBM K-RY61-1.5/120R-3, предварительно смонтированная
описано ниже.
- Очистите поверхность с помощью подходящего чистящего средства для удаления любой грязи, которая может препятствовать прилипанию тензорезисторов к поверхности полимера.
- Прикрепите тензорезисторы к поверхности полимера с помощью клея , который не влияет на свойства полимера.
Цианоакрилатный клей подходит для многих применений.
- Насколько это возможно, используйте предварительно смонтированные тензометрические розетки . Они исключают влияние тепла сварщика на распределение остаточных напряжений в полимере. Если это невозможно, рекомендуется использовать подложку и минимизировать время сварки.
- Закрепите систему сверления на образце и убедитесь, что ось сверления перпендикулярна поверхности.
- С помощью оптического микроскопа совместите перекрестную сетку так, чтобы она находилась точно в центре розетки.
- Замените микроскоп сверлильным инструментом и просверлите точно через центр розетки.
- Установите токопроводящую ленту заданной толщины на тензорезистор, следя за тем, чтобы не закрыть все контрольные метки.
- Продвигайте сверлильный инструмент до тех пор, пока он не достигнет поверхности токопроводящей ленты.
Снова запустите резак и продвигайте его, пока он не прорежет токопроводящую ленту и материал подложки розетки. Эта точка соответствует «нулевой» глубине резца.
- Запишите показания каждого тензодатчика с резцом на поверхности после ожидания, достаточного для стабилизации сигнала (время задержки).
- Установите установленную скорость подачи, максимальную глубину, количество шагов сверления и время задержки в автоматической системе. Отверстия обычно делаются с шагом ок. 0,05 мм в соответствии с положениями стандарта ASTM E837.
- Показания тензодатчика t и глубина отверстия записываются для каждого шага сверления.
- Замените систему сверления микроскопом и измерьте диаметр отверстия и эксцентриситет , выполнив четыре перемещения по двум перпендикулярным осям.
3.1 Подготовка поверхности и склеивание
Химическое сродство каждого пластикового материала с растворителями и клеями , используемыми при установке, необходимо проанализировать и принять во внимание. Неподходящие связующие вещества могут фактически повредить установку тензодатчика или даже анализируемый компонент. Для очистки поверхности рекомендуется метод механической обработки поверхности .
Исключительно в качестве примера, таблица 1 указывает требования для правильной установки тензорезистора на пластиковый материал .
Таблица 1 . Подготовка к установке тензорезисторов на некоторые пластмассовые материалы.3.2 Определение глубины контакта (установка нуля)
Определение начальной глубины является ключевым аспектом правильного измерения остаточных напряжений методом сверления отверстий.
Эта точка определяется в металлических материалах электрическим контактом . Полностью автоматически система MTS3000 останавливает фрезу, когда сверло достигает поверхности детали после прорезания полиамидной основы розетки тензодатчика.
В то время как нулевая точка в пластиковых материалах не может быть определена простым электрическим контактом, поскольку они не допускают электропроводности. Тем не менее некоторые операции можно использовать для определения «нулевой» точки.
Принципиально возможна работа либо:
- Определение «нулевой» глубины вручную , остановка фрезы, когда она начинает производить резку пластика ( рис. 3 , слева), либо
- С помощью специального алюминиевого клейкая лента , чтобы «нулевая» глубина определялась автоматически. После определения «нулевой» точки необходимо перевести систему на расстояние, равное сумме толщин тензометрической розетки и специальной алюминиевой ленты. ( рис. 3 , справа).
4. Определение рабочих параметров
Измерение остаточных напряжений в пластиковых материалах методом сверления отверстий включает в себя очень разные аспекты от применения того же метода до металлические материалы . В пластмассовых материалах модуль упругости ниже , и поэтому измеренные деформации намного выше при той же нагрузке, и материал более чувствителен к операции удаления материала. Скорость резания , скорость подачи и время задержки при получении показаний деформации должны быть выбраны соответствующим образом.
4.1 Скорость вращения во время сверления
Скорость сверления , несомненно, является одним из параметров, которые больше всего влияют на измерение остаточных напряжений в пластиковых материалах методом сверления отверстий. Высокоскоростное сверление с помощью воздушной турбины, которое является методом, обычно используемым для измерения остаточных напряжений в металлических материалах, не может применяться, так как выделяемое тепло приводит к плавлению пластмассы и значительному повышению температуры в зонах деформации. применяются манометры.
В качестве примера на рис. 4a показано отверстие, сделанное в пластике с помощью высокоскоростной системы сверления с использованием воздушной турбины: отчетливо видно плавление пластика по краям отверстия. Снижение давления сжатого воздуха и связанное с этим замедление воздушной турбины могут только уменьшить этот эффект, но, конечно, этого недостаточно для его устранения.
Скорость резания , следовательно, должна быть очень низкой . На рис. 4b можно увидеть качество отверстия, выполненного с помощью низкоскоростной сверлильной системы (до 200 об/мин), предназначенной для измерения остаточных напряжений в пластмассовых материалах.
Рисунок 4: а) отверстие, выполненное с помощью турбины, питаемой воздухом, сжатым до давления 4 барб) отверстие, выполненное с помощью электродвигателя на низкой скорости
в) тензодатчик в процессе сверления
4.2 Скорость подачи
Поскольку пластмассы очень чувствительны к механическим нагрузкам, были проведены различные экспериментальные испытания сверления для определения оптимальной скорости подачи .
Результаты испытаний показали, что буровой инструмент должен продвигаться медленнее , чтобы сократить время нестабильности после сверления. Уменьшение скорости подачи означает увеличение времени, необходимого для измерения остаточных напряжений : правильный компромисс между этими двумя аспектами привел к определению оптимальной скорости сверления отверстий в пластиковых материалах.
Таблица 2 показывает время, необходимое для сверления, и среднее время стабилизации для каждой анализируемой скорости подачи: наилучший компромисс достигается при скорости подачи 0,1 мм/мин .
Таблица 2. Время, необходимое для измерения остаточных напряжений в пластиковых материалах.4.3 Выбор времени задержки
Время задержки позволяет получить показания деформации, когда образец возвращается в состояние теплового и механического баланса после того, как отверстие просверлено. Испытания показали, что тепловой баланс, на который влияет процесс бурения, достигается с задержкой в несколько секунд.
Для оценки времени, необходимого для достижения механического баланса компонента, необходимо провести испытания для измерения тренда деформаций на протяжении всего этапа сверления пластмассового материала.
Таким образом, с помощью усилителя QuantumX и программного обеспечения для сбора данных Catman производства HBM стало возможным измерить тенденцию деформации, измеренную в течение всей операции бурения: результаты показаны на рисунок 5 , показать, что система механически нестабильна в процессе бурения и что необходимо подождать прибл. 90 секунд, прежде чем система вернется к стабильной работе. При достаточном времени задержки можно наблюдать обычные кривые зависимости деформации от глубины для каждой сетки тензодатчиков. Кривые относятся к испытаниям со скоростью подачи 0,2 мм/мин.
Те же экспериментальные испытания были повторены также при сверлении металлических материалов (сталь и алюминий: результаты показали поведение системы, но с более быстрым временем стабилизации (3-5 секунд). Через На рисунках 6 и 7 можно детально наблюдать тенденции деформации в металлическом материале (сталь) и пластиковом материале (поликарбонат).
Рис. 5. Слева: приобретение штаммов во времени. Справа деформации в зависимости от глубины сверления.4.4 Проверка изменения температуры пластикового компонента
После проектирования системы сверления была измерена температура t пластикового (поликарбонатного) компонента в процессе сверления. 9 глубиной 2 ммЗатем было сделано отверстие 0190, и температуры на образце были зарегистрированы с помощью термопары типа K , установленной на том же расстоянии от отверстия, что и сетки тензодатчиков, расположенные напротив сетки 2 (или B).
На рис. 8 показана зависимость температуры от глубины отверстия . Двадцать секунд были установлены в качестве времени задержки между этапами сверления, и для испытания была выбрана скорость подачи 0,2 мм/мин (стандартная скорость для испытаний на металлических материалах, таких как сталь).
Результаты показывают, что буровой инструмент не вызывает чрезмерного нагрева на сетках тензометрических датчиков. Максимальное зарегистрированное изменение температуры приходится на конец этапа сверления и составляет менее 1°C.
Кроме того, в течение времени задержки наблюдается быстрое снижение температуры компонента и возврат к исходной температуре . Действительно, через 20 секунд видно, что температура достигает начальных значений: максимальное отклонение, измеренное по отношению к начальной температуре, составляет 0,24°С.
Рис. 6. Тенденция деформации при сверлении металлического материала.Рис.
