- Пиролизный газ — Большая Энциклопедия Нефти и Газа, статья, страница 3
- Что такое пиролизное горение (пиролиз)?
- Пиролизный газ как источник углерода для производства биогаза путем анаэробного сбраживания
- Пиролизный газ как возобновляемый восстановитель для переработки остатков цинка и свинца: отчет о состоянии
Пиролизный газ — Большая Энциклопедия Нефти и Газа, статья, страница 3
Cтраница 3
Газофракционирующий агрегат питается пиролизным газом. [31]
При пиролизе углеводородов получается пиролизный газ, смола и кокс. Пиролизный газ представляет собой смесь этилена, пропилена, водорода, метана, этана, пропана, углеводородов с большим числом атомов углерода. Кроме указанных веществ, пиролизный газ содержит воду, сероводород, сернистые соединения, примеси ацетиленовых соединений, окись и двуокись углерода и кислород. Этилен получают разделением пиролизного газа. После выделения олефинов жидкие продукты пиролиза ( пироконденсат) используются для получения ароматических углеводородов и диенов. [32]
При пиролизе углеводородов получается пиролизный газ, смола и кокс. Кроме указанных веществ, пиролизный газ содержит воду, сероводород, сернистые соединения, примеси ацетиленовых соединений, окись и двуокись углерода и кислород.
Пройдя водяной гидравлик, промытый пиролизный газ поступает в систему очистителей — скрубберов, где производится очистка от оставшейся жидкой смолы и паров. [34]
В отделении газоразделения из очищенного пиролизного газа выделяют метано-водородную фракцию ( используется как топливо для печей пиролиза), этилен, пропилен, этан, пропан, бутилен-ди-винильную фракцию. [35]
При этом исключается разбавление продуктового пиролизного газа и ухудшение его качества. В связи с применением газообразных теплоносителей повышается запыленность продуктового пиролизного газа. В то же время, внутренний обогрев конвекцией позволяет существенно интенсифицировать процесс пиролиза и сократить габариты реакторов по сравнению с внешним обогревом за счет теплопроводности.
Детали, цементированные одним пиролизным газом, наряду с малой глубиной науглероживания, имеют низкую концентрацию углерода в цементированном слое, поэтому цементация одним пиролизным газом не производится. [37]
Характерные для наших опытов выхода пиролизного газа значительно превышают количество газа, полученного И. П. Нихамовым [6] при разложении сходного по составу с применявшимся нами кускового общесыр-товского сланца в стальной реторте с внешним обогревом. [38]
Способ заключается в применении рециркуляции пиролизного газа с вводом его в зону реакции. Некоторое снижение коксообразова-ния достигается также вводом водяного пара в зону реакции. [39]
Для исключения образования взрывоопасной смеси пиролизного газа

Предназначены для обработки содержащего водород неочищенного пиролизного газа в присутствии соединений серы. [41]
Как видно из этих данных, пиролизный газ содержит большое количество предельных и непредельных углеводородов, водорода и малое количество окиси углерода, кислорода и углекислоты. [42]
Как видно из выходных кривых компонентов пиролизного газа ( рис. 49) и данных табл. 44, разделительная способность силикагеля тем больше, чем меньше диаметр его пор. [43]
Метод окислительного пиролиза с последующим сжиганием пиролизных газов универсален в отношении фракционного состава и фазового состояния отходов, их влажности и зольности. Окислительному пиролизу могут быть подвергнуты многие производственные отходы, неудобные для сжигания или газификации. [44]
Смешанный в ретортах крекинга при температуре 960 пиролизный газ с парами воды образует новый газ, крекированный с большим содержанием СО ( до 15 — 20 %), водорода и малым содержанием углеводородов. В полученном газе имеются группы углеводородов, водород, окись углерода, углекислота, кислород и в незначительном количестве азот. Кроме того, в нем содержатся также пары смол, которые частично коксуются еще в реторте.
[45]
Страницы: 1 2 3 4
Что такое пиролизное горение (пиролиз)?
Теплову енергію з деревини навчилися отримувати ще в стародавні часи, але сучасні технології дозволили модернізувати цей процес, зробивши його більш безпечним і економічним. У традиційних печах відбувається горіння деревини, що супроводжується виділенням теплової енергії, при цьому для підтримання температурного режиму в будинку потрібна велика кількість палива. Згоряння деревини відбувається досить швидко, тому необхідно постійна присутність людини для своєчасного видалення золи і закладки нових порцій дров.
В піролізних котлах традиційне горіння палива відсутній — його замінює процес тління, який називається піролізом. Що ж таке піролізне горіння? В звичайних умовах під впливом високих температур деревина починає горіти, однак горіння неможливо при відсутності або нестачі кисню. В піролізних котлах доступ повітря до палива обмежений, а температура досить висока, тому замість горіння деревина починає розкладатися на летючий газ і тверді відходи. Цей процес і називається піролізом.
Звідки ж береться теплова енергія для обігріву житла? Гарячий деревний газ змішується з повітрям, що запускає процес горіння і призводить до нагрівання теплоносія. Різниця між звичайним і піролізного горіння полягає в наступному. Температура горіння деревного газу набагато перевершує температуру при звичайному горінні деревини, тому при піролізі згорають багато гази і шкідливі домішки, які у звичайних дров’яних печах йдуть в димар і забруднюють навколишнє середовище. При піролізі утворюється набагато менше сажі та золи, що дозволяє очищати котел всього кілька разів в тиждень, а не після кожної згорілої порції палива.
Перший етап роботи піролізного котла нагадує роботу звичайних дров’яних печей. В завантажувальній камері підпалюється невелика кількість деревини. При досягненні температури 450°C починається виділення деревного газу. У цей момент слід провести повну дозагрузку палива і перекрити доступ повітря з допомогою шиберних заслінок. Щоб направити летючі гази в нижню камеру, де відбуватиметься їх згоряння, застосовують нагнітаючий вентилятор.
В форсунку, через которую древесный газ попадает в камеру сгорания, подводят воздух, и при температуре 560°C начинается горение смеси пиролизного газа с кислородом. Максимальная температура в камере сгорания может достигать 1100 °C, и вся эта тепловая энергия уходит на нагрев теплоносителя, что значительно повышает КПД отопительного оборудования. Продолжительность пиролизного горения превышает время обычного сгорания дров в несколько раз, что снижает расход топлива за одну и ту же единицу времени.
Управление пиролизным процессом осуществляется системой шиберов, а кроме того, пиролизные котлы оборудованы автоматикой, что позволяет полностью исключить присутствие человека для обеспечения работы котла. С помощью автоматических систем можно настроить работу котла на необходимый температурный режим в зависимости от погодных условий. Применение пиролиза позволяет использовать все энергетические резервы древесного топлива, существенно снижает затраты на отопление жилища, облегчает эксплуатацию отопительной системы, делает её более эффективной, безопасной и надёжной.
На сайті компанії DM-Stella представлений широкий модельний ряд твердопаливних піролізних котлів різної потужності, з допомогою яких можна забезпечити обігрів приміщень будь-якої площі — від приватних будинків до великих виробничих цехів або складських приміщень.
Пиролизный газ как источник углерода для производства биогаза путем анаэробного сбраживания
Принадлежности автора
* Соответствующие авторы
и Государственная ключевая лаборатория по переработке тяжелой нефти, Пекин Ключевая лаборатория по переработке биогаза, Институт новой энергии, Китайский нефтяной университет в Пекине (CUPB), Пекин, КНР
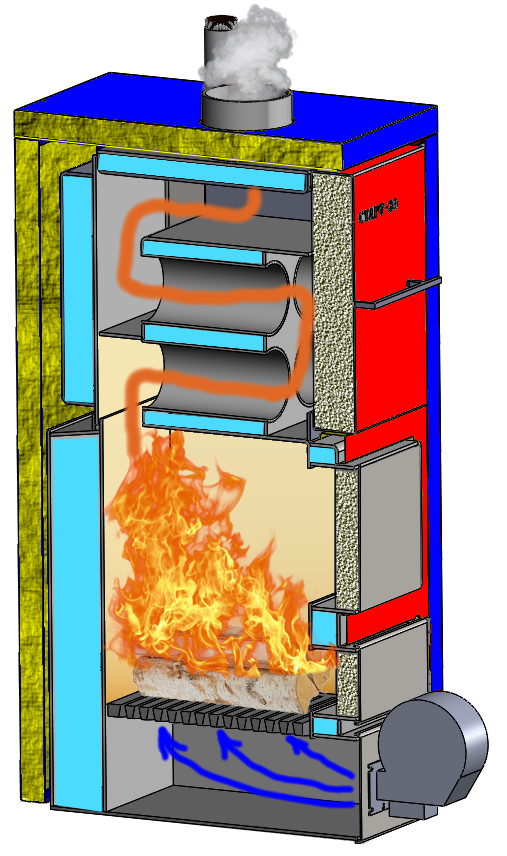
б Факультет сельскохозяйственных наук и наук об окружающей среде Ростокского университета, Юстус-фон-Либих-Вег 6, 18059Росток, Германия
д Факультет химического машиностроения, Университет Западной Вирджинии, США
Аннотация
rsc.org/schema/rscart38″> Углерод является важным ресурсом для анаэробов для увеличения производства биогаза. В данном исследовании изучалась возможность использования имитации пиролизного газа (СПГ) в качестве источника углерода для производства биогаза. Влияние скорости перемешивания (SS), времени удержания газа (GHT) и H 2 добавление к биометанированию SPG. Разнообразие и структура микробных сообществ также были проанализированы на платформе Illumina MiSeq. Результаты показали, что при GHT 14 ч и SS при 400 об/мин SPG с содержанием CH 4 до 64,7% может быть биомодернизирован до биогаза. Ограничением для биометанирования СПГ является газожидкостный массоперенос. Впервые было замечено, что добавление H 2 может биомодернизировать SPG до высококачественного биогаза (с 91,1% CH 4 ). Methanobacterium считался ключевым фактором во всех реакторах. Это исследование предлагает идею и альтернативный способ преобразования лигноцеллюлозной биомассы и твердых органических отходов в энергию (
Пиролизный газ как возобновляемый восстановитель для переработки остатков цинка и свинца: отчет о состоянии
Введение
В настоящее время выделение возобновляемых ресурсов для различных применений является большой проблемой. Особенно в металлургии существует широкий спектр первичных ресурсов, используемых для производства различных металлов или продуктов. В большинстве случаев в качестве источника энергии или восстановителя используется углеродный носитель, что сопровождается образованием углекислого газа. Что касается высокой стоимости сертификатов на выбросы углекислого газа, то 5 или 6 лет назад были начаты различные исследования с целью поиска возобновляемых восстановителей и энергетических ресурсов для сокращения выбросов углекислого газа и снижения затрат на необходимые сертификаты на выбросы углекислого газа. Одной из многообещающих возможностей было использование сельскохозяйственных отходов или древесины в процессе карбонизации для получения древесного угля в качестве носителя углерода, нейтрального по отношению к двуокиси углерода. Такой процесс используется, но для использования древесного угля в металлургии требуются некоторые особые характеристики. При пиролизе биомассы или древесины в качестве побочного продукта образуется так называемый пиролизный газ. Он состоит из горючих соединений, двуокиси углерода и конденсируемых смол.1 В промышленных пиролизных установках этот газ используется для нагрева самой пиролизной установки, но его также можно использовать в качестве восстановителя для металлургических применений. Идея использования возобновляемых источников энергии или восстановителей в металлургии была проверена в концепции переработки для переработки содержащих цинк и свинец технологических отходов.
Одним из вариантов использования древесного угля в металлургии является утилизация пыли металлургического производства. Вельц-процесс, который представляет собой установку с вращающейся печью, в настоящее время является самой современной технологией для переработки цинка в виде вельц-оксида из пыли сталелитейного производства. В этом процессе возможно, что древесный уголь смешивается с другими исходными материалами из вельц-печи, и, следовательно, этот углеродный носитель используется для восстановления соединений цинка до металлического цинка, который испаряется и поступает в поток отходящих газов для отделения его от шлаковая масса. Недостатком этого процесса является большое количество оставшегося вельц-шлака, который по-прежнему содержит цинк и свинец, а элюирование этого остаточного шлака препятствует его использованию в качестве вторичного ресурса в других целях.
В целях предотвращения демпинга в будущем планируется провести дополнительную обработку образующегося вельц-шлака. Одной из возможностей может быть так называемая вертикальная реторта, в которой низкая температура испарения металлического цинка используется для концентрирования цинка в отходящих газах в виде оксида цинка. Для этого материал нагревают в вертикальной реторте в диапазоне 1050–1150°С, а пиролизный газ древесноугольного производства для вельц-печи протекает через массив твердого вельц-шлака. Для полученного шлака остается два варианта, которые описаны далее.
В настоящей статье описаны некоторые фундаментальные основы вельц-процесса и процесса удаления цинка через отходящие газы. Это согласуется с опубликованными результатами вышеупомянутой концепции реторты. Параметры такого процесса уже определены в ходе лабораторных и технических испытаний и опубликованы2, в то время как в этой статье описываются исследования на пилотной установке для обработки вельц-шлака.
Производство вельц-шлака
В настоящее время преобладающим процессом переработки пыли сталеплавильного производства является вельц-процесс, при котором цинксодержащие материалы, особенно пыль из колошников черной металлургии, смешивают с различными добавками и восстановителями на основе углерода. Рабочая температура составляет около 1100°C. В результате восстановления цинксодержащих соединений углеродом или монооксидом углерода образующиеся пары цинка повторно окисляются воздухом, подаваемым в верхнюю часть печи, и затем собираются в рукавном фильтре; можно отделить цинк от остального загруженного материала.
Вельц-технологический маршрут5
Изображение полного размера
Основной реакцией извлечения цинка является восстановление оксидных соединений цинка с помощью CO. Из-за низкой температуры улетучивания образовавшийся металлический цинк испаряется при 907°C. Для накопления цинка и управления разделением массы необходимо провести повторное окисление в надводном слое вельц-печи, что связано с выделением значительного количества тепловой энергии. Эта энергия используется для нагрева подаваемого материала, поступающего в печь в верхней части. Остальную массу образует оставшийся шлак, который покидает топку в нижней части печи и охлаждается в воде.
Основные реакции в вельц-печи
Изображение полного размера
Был разработан или используется в промышленных масштабах широкий спектр различных технологий переработки пыли сталелитейного производства, но в настоящее время вельц-процесс самая высокая доля рынка и около 30–35 единиц находятся в эксплуатации по всему миру, не включая Китай. Несмотря на низкое качество продукта и большое количество вновь образующихся отходов, вельц-печь представляет собой простой процесс с хорошо известным принципом, с одной стороны, и низким потреблением энергии по сравнению с альтернативами, с другой.7,8,9
Теоретические принципы и основы использования пиролизного газа при извлечении цинка
Извлечение цинка из различных шлаков изучалось в прошлом. Одним из процессов, реализуемых в промышленных масштабах для извлечения цинка из жидкого шлака, является процесс выпаривания шлака, осуществляемый совместно с печами первичного свинца. При этом жидкий шлак переносится в дымовую печь, а цинк может быть извлечен путем добавления воздуха и угля или кокса через фурмы в нижней части реактора. При 1300–1500°С добавленный углерод восстанавливает оксид цинка. При таком подходе цинк отделяется от жидкого шлака за счет испарения металлического цинка с последующим повторным окислением в потоке отходящих газов. Достижимое содержание остаточного цинка составляет около 2 % масс. Обзор происходящих реакций представлен на рис. 3.10,11,12.
Реакционная система, протекающая в процессе выкуривания шлака13
Изображение полного размера
На рис. 3 показан газовый пузырь с частицей полукокса в середине. Углерод реагирует с образованием CO с кислородом в пузырьке, в результате чего создается восстановительная атмосфера для восстановления оксида цинка из массы шлака. Что касается температуры процесса, то парообразный цинк накапливается в газовом пузыре. При этом восстановлении образуется CO 2 , который реагирует с твердым углеродом с образованием CO посредством реакции Будуара. Восстановительные условия могут быть сохранены и достигнута высокая степень извлечения цинка. Во время этих реакций пузырек поднимается в ванне, так как выталкивающая сила пузырька выше силы его веса. Когда цинк покидает объем шлака газовым пузырем, он повторно окисляется из O 2 или CO 2 на оксид цинка. Таким образом, можно собрать оксид цинка из системы отходящих газов в рукавном фильтре. Обычные выходы извлечения цинка составляют около 87,5%. В зависимости от условий процесса из шлака также выделяют оксид свинца. При низкой концентрации свинца в шлаке свинец накапливается в виде оксида свинца в пыли. Если концентрация достаточно высока, пары свинца накапливаются в пузырьках восстановительного газа, конденсируются там и образуют капли свинца, которые затем опускаются на дно печи и создают свинцовую ванну.
12,13,14,15,16,17, 18
Этот процесс связан с экстракцией цинка из жидкого шлака твердым восстановителем. В прошлом процесс первичного извлечения цинка осуществлялся в так называемых «муфельных» печах, где концентрат цинка смешивался с углеродным носителем и нагревался в муфеле, представляющем собой закрытый реактор с круглым или овальным поперечным сечением. . Удаление жидкого цинка проводили через определенные промежутки времени. Также была разработана муфельная печь непрерывного действия для повышения производительности. С тех пор эти процессы были заменены гидрометаллургическим процессом извлечения в производстве первичного цинка.3 Для извлечения цинка из промышленных остатков гидрометаллургический метод был бы очень дорогим и сложным из-за широкого спектра различных металлов и соединений в остатках. В эти времена очень дорогого CO 2 , производство возобновляемых источников энергии или восстановителей имеет важное значение. Общей темой исследования был пиролиз биомассы или древесины для получения древесного угля. В зависимости от используемых условий обработки могут быть затронуты характеристики полученного древесного угля. При переработке биомассы или древесины происходит массовое уменьшение оставшегося твердого древесного угля. В качестве побочных продуктов (жидкости) возникают смолы и пиролизный газ. Из-за состава пиролизного газа, в основном состоящего из СО, Н 2 , CO 2 и CH 4 , его можно использовать в качестве энергетического ресурса или газа-восстановителя в металлургических целях. Это привело к разработке специального процесса «вертикальной реторты» для обработки вельц-шлака, остатка от переработки пыли сталелитейного производства, для извлечения оставшегося цинка и получения инертного шлака, чтобы избежать сброса. Опубликованы основы такого подхода, а также первоначальные практические результаты.2 В следующем разделе описывается текущий уровень развития экспериментальной испытательной установки.
Пиролизный газ для обработки вельц-шлака
Ранние исследования по использованию пиролизного газа для извлечения цинка из вельц-шлака показали возможность извлечения цинка с помощью специальной вертикальной реторты с непрямым нагревом. Для достижения лучшего выхода извлечения цинка следует учитывать реформинг пиролиза. Фундаментальное описание получения пиролизного газа наряду с практической реализацией в технических масштабах исследований показано в первой публикации по этой теме исследования.2
Идея состоит в том, чтобы производить чистый водород из пиролизного газа в процессе паровой конверсии, аналогично тому, как это делается с природным газом. Для существующей системы реакции твердое тело–газ в вертикальной реторте водород является эффективным восстановителем. Возможная схема процесса риформинга показана на рис. 4.19.
Рис. 4Возможный процесс риформинга пиролизного газа для получения водорода следующий шаг. После этого первого шага происходит подача энергии через горелку и добавление воды. В присутствии катализатора протекает следующая реакция20:
$$ {\text{CH}}_{4} + {\text{H}}_{2} {\text{O}} \leftrightarrow 3{\text{H}}_{2} + { \text{CO}} $$
(1)
Для уменьшения количества монооксида углерода в газе водород образуется в результате реакции конверсии вода–газ20:
$$ {\text{CO}} + { \text{H}}_{2} {\text{O}} \leftrightarrow {\text{H}}_{2} + {\text{CO}}_{2} $$
(2)
Одновременно происходит расщепление длинноцепочечных углеводородов на монооксид углерода и водород, и в результате реакции конверсии вода-газ образующийся монооксид углерода реагирует на водород и диоксид углерода. 20
Чтобы отделить водород от других газов, используются различные адсорбционные свойства отдельных газов при более высоком давлении. Образовавшийся чистый водород можно использовать в качестве восстановителя.19
Восстановление вельц-шлака с помощью пиролизного газа
Тенденция к производству возобновляемой энергии и восстановителей привела к различным разработкам в области пиролиза из биомассы. В случае рециркуляции пыли сталелитейного производства по вельц-процессу в этом исследовании учитываются стоимость сертификатов на двуокись углерода и экологические аспекты. Общая идея заключалась в том, чтобы создать пригодный для металлургии древесный уголь в специальном реакторе при заранее определенных условиях, чтобы использовать его в качестве носителя углерода в вельц-печи. В качестве побочного продукта возникает пиролизный газ, состоящий в основном из СО, СН 4 , H 2 и CO 2 . Значения различных газовых соединений зависят от температуры пиролиза. Одна из возможностей состояла в том, чтобы также использовать этот газ в качестве восстановителя; поэтому были начаты исследования по переработке вельц-шлака в вертикальной реторте для извлечения цинка из этого остатка и получения шлака, который не нужно вывозить на свалку.
Непрерывно образующийся вельц-шлак следует обрабатывать непосредственно после выхода из вельц-процесса, чтобы снизить количество энергии, необходимой для нагрева до температуры, необходимой в ретортном процессе. Возможная промышленная процедура для этой комбинации процессов показана на рис. 5.
Рис. 5Реалистичная промышленная технологическая схема обработки вельц-шлака2 (Авторские права 2015 г. Общества минералов, металлов и материалов. Используется с разрешения)
Изображение в натуральную величину Вельц-шлак поступает в пустую реторту, которая нагревается косвенно. Идея горячей зарядки состоит в том, чтобы избежать значительной потери температуры. На этапе 2 верхняя часть реторты закрывается для сбора возникающих газовых потоков, а пиролизный газ (обозначенный как «синтез-газ» на рис. 5) сжигается для непрямого нагрева, а для проведения восстановления оксида цинка пиролизный газ также протекает через объем шлака. Шаг 3 иллюстрирует текущие реакции в массе шлака. Благодаря соединениям свинца с галогенами свинец вместе с оксидом цинка удаляется при очистке и образует товарный продукт фильтровальной пыли. Для выполнения шага 4 доступны две разные возможности. Рекуперация тепла, аналогичная технологии SDHL5,21, из вельц-печи возможна путем пропускания воздуха через восстановленный шлак вместо азота. Присутствующее металлическое железо реагирует с кислородом; это экзотермическая реакция. Генерируемая энергия поглощается потоком газа и может использоваться для нагрева на этапе 1. Наконец, шлак не должен содержать цинка и свинца, чтобы использовать шлак для дальнейшего использования, но не для захоронения. Другой вариант заключается в использовании азота вместо воздуха для получения продукта, аналогичного железу прямого восстановления, для применения в черной металлургии. В этом случае следует учитывать примеси через различные компоненты шлака.
Применение ретортного процесса в пилотном масштабе
Предварительные результаты лабораторных и технических испытаний опубликованы в Ref. 2 и послужил основой для следующего масштабирования до периодического процесса с 250 кг обработанного материала на испытание. Чтобы получить общее представление об истории испытаний, на рис. 6 представлены различные масштабы исследования.
Рис. 6Различные масштабы испытаний по восстановлению вельц-шлака
Изображение в полный размер
Первые испытания проводились в самой маленькой реторте с 2,5 кг шлака на партию для определения некоторых параметров. Во время этих исследований восстановления вельц-шлака исследовательская группа также располагала экспериментальной установкой для пиролиза биомассы, что позволяло использовать эти два процесса одновременно. Накопленный пиролизный газ собирали и направляли в объем вельц-шлака из реторты, где происходило восстановление с использованием предварительного нагрева газа в замкнутой системе трубопроводов. В следующем типоразмере с емкостью 25 кг вельц-шлака было невозможно объединить пиролизную установку с ретортой, поскольку необходимое количество газа было слишком большим и не могло быть обеспечено из пиролизной установки в требуемое время. В качестве альтернативы для проведения большого количества испытаний использовались синтетические газовые смеси. Состав синтез-газа был адаптирован к результатам, полученным на установке пиролиза биомассы, также использовался чистый водород.
После этих первых двух этапов разработки можно констатировать, что гранулометрический состав в объеме вельц-шлака не оказывает существенного влияния на достижимый выход цинка. Можно было удалить цинк и свинец из вельц-шлака с помощью пиролизного газа от производства древесного угля, но использование чистого водорода привело к лучшим результатам. После детальной интерпретации результатов было принято решение провести испытания с 250 кг вельц-шлака на партию и водородом в качестве восстановительного газа при температуре 1100°C.
Пилотная реторта (вместимость 250 кг) аналогична меньшему устройству на 25 кг. Реторта реакционная изготовлена из жаропрочной стали. Отличие заключается в блоке предварительного подогрева газа, который является специальной разработкой для данной исследовательской установки и имеет разные зоны нагрева для достижения заданной температуры газа, а также отличается типом комплектации (рис. 6). Сама реакционная комната косвенно обогревается сопротивлением. В верхней части происходит дожигание, при котором металлический цинк в отходящем газе повторно окисляется, а все еще присутствующие горючие соединения сгорают. Оксид цинка собирается в рукавном фильтре. Практическое устройство можно увидеть на рис. 7.
Рис. 7Реторта, использованная для испытаний в пилотном масштабе
Изображение в полный размер
Что касается больших усилий для каждого испытания, только два испытания с определенными условиями процесса были успешно выполнены, но для оценки воспроизводимости оба испытания были повторены четыре раза. раз в тех же условиях. Технологические условия для испытаний в 250-килограммовой реторте были определены в соответствии с опытом проведенных испытаний меньшего масштаба. В таблице I представлен обзор параметров, использованных для испытаний.
Полноразмерный стол
Эти испытания проводились с тем же материалом образца, что и предыдущие исследования. Результаты обобщены на рис. 8.
Рис. 8Результаты экспериментальной реторты
Изображение в полный размер
Столбцы на рис. 8 представляют собой средние арифметические значения различных испытаний, проведенных в одних и тех же условиях. Для интерпретации учитывали металлизацию железа и выход цинка и свинца. Можно было удалить до 90 мас.% цинка из вельц-шлака. Удаляемость свинца при этом типе обработки ниже, но значения содержания свинца в шлаке, использованном для испытания, также намного ниже по сравнению с содержанием цинка. Для достижения таких высоких скоростей удаления цинка также имело место восстановление железа. При температурах выше 1100°С можно снизить степень восстановления железа, но при имевшемся ретортном оборудовании работать при более высоких температурах не представлялось возможным по причинам термодинамических основ, подробно описанных в [11]. 2.
Сравнивая два испытания, RG1 и RG2, можно заметить, что большее количество доступного восстановителя приводит к гораздо лучшим результатам, но коэффициент использования газа намного ниже. Для экономичной и экологичной работы становится необходимой очистка отходящих газов и повторное использование процесса.
Подводя итог, можно оценить три основных параметра: температуру, размер зерна и восстановительный газ. Для высокого извлечения цинка и более низкого восстановления железа температура в используемом оборудовании должна быть максимально высокой. Ограничением является температура спекания, так как это может снизить газопроницаемость, и тогда процесс будет невозможен. Определенная температура для удаления цинка с приемлемым поведением при спекании составляет около 1150°C. Образующийся шлак вельц-процесса не является типичным шлаком, известным из процесса в жидком состоянии, поскольку он не плавится в вельц-печи, а только агломерируется в рассыпчатый материал, который можно использовать непосредственно в ретортном реакторе для дополнительного восстановления. . Чтобы определить влияние различных размеров частиц, были проведены испытания с различными категориями зерен. Разница при сравнении этих испытаний была незначительной. Эти испытания продемонстрировали возможность использования пиролизного газа непосредственно из установки пиролиза для рециркуляции цинка из вельц-шлака. Для лучших результатов необходимо провести риформинг и использовать полученный водород в качестве восстановителя. Еще одним преимуществом такого подхода является расщепление углеводородных цепочек, образующихся при пиролизе биомассы или древесины.
Заключение
В настоящей статье описывается возможная обработка вельц-шлака пиролизным газом, который образуется в результате металлургического производства древесного угля из биомассы или древесины и содержит огромное количество горючих компонентов. В вертикальной реторте пиролизный газ проходит через косвенно нагретый объем вельц-шлака, и в процессе цинк восстанавливается и отделяется от остального объема шлака посредством испарения. Металлический цинк в отходящих газах повторно окисляется вне реторты кислородом в подаваемом воздухе и может быть собран в рукавном фильтре системы отходящих газов. Свинец или некоторые соединения свинца также следуют за цинком в газовую фазу. Образовавшееся металлическое железо также остается в твердом материале. Эти исследования проводились в разных масштабах, от лабораторных испытаний до так называемых пилотных, с 250 кг обработанного материала на партию. В проведенных испытаниях были определены различные параметры, и, в конце концов, можно было оценить такой процесс переработки вельц-шлака с разных точек зрения.
Используемая очистная установка в настоящее время не является современным процессом или технологией, поэтому доступна лишь ограниченная информация о производительности такой технологии в промышленных масштабах.
Идеей этой разработки было использование возобновляемых источников энергии или восстановителей в металлургии и стоимость сертификатов CO 2 . В настоящее время эти сертификаты не являются решающим фактором для производителей вельц-шлаков, поэтому многие исследования по этой теме прекращены. Более того, исследования по получению древесного угля с помощью специальной пиролизной установки были остановлены, и поэтому пиролизный газ, который можно было бы использовать для такой концепции реторты, не образуется.
Для проведения такого процесса необходимо провести риформинг пиролизного газа, что влечет за собой дополнительные затраты на операцию. Из-за цен на доступные первичные ресурсы любая операция слишком дорога. Также необходима комплексная установка дополнительной газоочистки для увеличения заполняемости газа.
Остаток после восстановления состоит в основном из металлического железа. Из-за большого количества примесей его нельзя использовать в качестве железа прямого восстановления в черной металлургии, и его также приходится выбрасывать.
По обсуждаемым причинам исследовательский проект был остановлен на этапе пилотных испытаний, и потребуются некоторые оптимизации, чтобы иметь возможность выполнять такой процесс в промышленных масштабах. В случае обработки вельц-шлаков исследования будут продолжены путем проведения полного восстановления в жидком состоянии вместе с другими цинк- и свинецсодержащими остатками.
Ссылки
P. Basu, Газификация биомассы и пиролиз , 1-е изд. (Берлингтон: Academic Press, 2010).
Google ученый
C. Pichler and J. Antrekowitsch, JOM 67, 2038 (2015).
Артикул Google ученый
Ф. Павлек, Metallhüttenkunde , 1-е изд. (Берлин: Вальтер де Грюйер, 1983).
Книга Google ученый
«>Э. Сааге и У. Хаше, World Metall. ERZMETALL 57, 138 (2004).
Google ученый
П.А. Козлов, Вельц-процесс , 1-е изд. (Москва: Издательство «Руда и металлы», 2003).
Google ученый
J. Rütten, Семинар «Сетевое взаимодействие между цинком и сталью », 3-е изд. (Клаусталь-Целлерфельд, Германия: GDMB Society for Mining, Metallurgy, Resource and Environment Technology e. V., 2011), с. 77.
Google ученый
Л. М. Саутвик, Извлечение цинка из электродуговой печи (ЭДП) Пыль (Лиссабон: Международная исследовательская группа по свинцу и цинку, 2015 г.).
Google ученый
«>Хил К., Бот О., Климчук К., Риу Д., Металлургия цинка и свинца , изд. Л. Сентомо (Wiley-VCH, Weinheim, 2008), с. 53.
Хил К., Бот О., Климчук К., Риу Д., Металлургия цинка и свинца , изд. А. Зигмунд (Wiley-VCH, Weinheim, 2010), с. 1087.
Харалампиев Г. и Попов Н., кан. Металл. Q. 38, 1 (1999).
Google ученый
Р. Пюлленберг и Р. Хён, Schriftenreihe der GDMB-Gesellschaft für Bergbau. Металл. Рост. Umwelttech 83, 81 (1999).
Google ученый
«>К. Кох, Schlacken in der Metallurgie , 1-е изд. (Дюссельдорф: Verl. Stahleisen, 1984).
Google ученый
Э. Джак и П. Хейс, Кан. Металл. Вопрос 42, 163 (2002).
Артикул Google ученый
E. Worrell and M.A. Reuter, Handbook of Recycling , 1st ed. (Уолтем: Elsevier, 2014), с. 121.
Google ученый
W. Snelgrove and JC Taylor, Can. Металл. Q. 20, 231 (1981).
Артикул Google ученый
B.V. HyGear, Генераторы водорода . http://hygear.
J. Rütten, C. Frias, G. Diaz, D. Martin и F. Sanchez, Proceedings of EMC 2011 , vol. 1673 (2011).
H. Bartusch, F. Alcalde, A. María и M. Fröhling, Erhöhung der Energie- und Ressourceneffizienz und Reduzierung der Treibhausgasemissionen in der Eisen-, Stahl- und Zinkindustrie , 1st ed. (Карлсруэ: Научное издательство КИТ, 2013).
Google ученый
В. Гао, К. Ван, Ф. Инь, Ю. Ченг и В. Ян, Adv. Матер. 24, 581 (2012).
Артикул Google ученый