- 4.1.2. Паровые турбины — Энергетика: история, настоящее и будущее
- Помогитие написать доклад по физике тема Паровая Турбина
- Паровая и газовая турбины: преимущества и недостатки агрегатов
- Сообщение по физике на тему:»Двигатели внутреннего сгорания. Паровая турбина» в 8 классе.
- Презентация по физике на тему «Паровые и газовые турбины»
- Конспект урока «Паровая турбина. КПД тепловых двигателей»
- Преимущества и недостатки паровых турбин
- Расход и работа паровой турбины
- Паровые турбины — обзор
- Типы паровых турбин — обзор
- Паровые турбины
- Отказ от вибрации ротора паровой турбины: причины и решения
- Конденсатор (паровая турбина) | Проектирование
- Модернизация паровой турбины: Низко висящие плоды
4.1.2. Паровые турбины — Энергетика: история, настоящее и будущее
4.1.2. Паровые турбины
Паровая турбина, как и паровая машина, относится к классу паровых двигателей, но между ними есть существенная разница.
В паровых машинах потенциальная энергия пара преобразуется сразу в механическую работу, а в паровых турбинах – вначале в кинетическую энергию движущегося с большой скоростью пара, а затем эта энергия преобразуется в механическую работу на лопатках турбины.
Карл Густав Патрик де Лаваль (1845–1913) – шведский инженер и изобретатель, по национальности француз – родился в Блазенбурге (Швейцария). Окончил технологический институт и университет в Упсале в 1872 году со степенью доктора философии. Работая на химическом заводе, в 1878 г. сконструировал центробежный сепаратор непрерывного действия для молока. В 1889 г. построил паровую турбину активного типа, где впервые применил гибкий вал, диск равного сопротивления и расширяющиеся сопла. К 1900 г.
Отличительная особенность расширяющегося сопла заключается в том, что давление пара на выходе из сопла может быть доведено до давления среды, в которую он выходит. Расширяющиеся сопла дают возможность использовать любые перепады давлений. Пар, вытекающий из сопла со сверхзвуковой скоростью, идет ровной струей, энергия которой может быть использована для вращения лопаток турбины.
Рис. 4.8. Турбина Лаваля: 1 – рабочий диск; 2 – лопатки; 3 – сопла
Почти через 250 лет после Джовани Бранка инженер Лаваль впервые построил активную турбину промышленного значения.
Турбина Лаваля (рис. 4.8) состояла из рабочего диска 1 небольшого диаметра с одним рядом рабочих лопаток 2, диск с рабочими лопатками размещался в кожухе, по окружности которого устанавливались расширяющиеся неподвижные сопла 3, куда подавался из котла пар. В соплах происходило преобразование кинетической энергии в потенциальную. Турбина вращалась с огромной скоростью до 30000 об/мин. Малая мощность, высокое число оборотов, довольно большой расход пара (8–9 кг/кВт) в турбинах Лаваля ограничивали их применение в промышленности. Они использовались в основном для привода маломощных агрегатов.
Для уменьшения окружной скорости рабочих лопаток турбин американский инженер Чарльз Кертис в 1896 году ввел в практику турбостроения ступени скорости. Принцип ступеней скорости состоит в том, что кинетическая энергия пара преобразуется в механическую на рабочих лопатках не одного ряда, а 2–3 рядов, между которыми стоят неподвижные лопатки для изменения направления движения пара.
Активные турбины со ступенями скорости позволяют уменьшить окружную скорость, но имеют низкий к. п.д., который с увеличением числа ступеней снижается. Поэтому диск Кертиса сохранился в современных турбинах только как первый диск турбины.
Одновенечные высокооборотные турбины для соединения с электрогенератором требовали дорогой зубчатой передачи, а турбины со ступенями скорости имели низкий к.п.д.
Выход из создавшегося положения был предложен еще в 1853 году Турнером, а затем английским инженером Чарльзом Парсонсом, который для уменьшения окружной скорости рабочих лопаток реактивной турбины, а, следовательно, и числа оборотов, предложил общий перепад давления пара использовать не в одной ступени, а разделить на несколько ступеней, то есть применить ступени давления. В 1884 году он получил патент на многоступенчатую реактивную турбину мощностью около 8 кВт при скорости вращения 1000 об/мин. Соединив турбину с валом электрогенератора, Парсонс получил первый турбогенератор для электростанции.
Чарлз Алджернон Парсонс (1854–1931) – английский инженер и предприниматель, член Лондонского королевского общества – родился в Лондоне. Окончил колледж СентДжона Кембриджского университета в 1876 году. С 1877 г. работал на заводе Амстронга инженером в области машиностроения. В 1884–1889 гг. стал партнёром фирмы Амстронга. В 1889 г. основал предприятие по производству паровых турбин своей системы в Хитоне.
Для активных турбин ступени давления впервые были введены в практику французским профессором Огюстом Рато, который в 1900 году построил на французском заводе Соттэ–Гарле первую активную турбину со ступенями давления мощностью 1000 л.с. Увеличивая число ступеней давления, можно уменьшить скорость вращения ротора до необходимых оборотов при соблюдении относительно высокого к.п.д. турбины.
Швейцарский инженер Генрих Целли усовершенствовал турбину Рато, применив в 1903 году насадки (сопла) с косым срезом. За счет этого удалось увеличить скорость пара на выходе из сопла и уменьшить число ступеней давления до 5–8. Одновременно в отличие от турбин Рато, где рабочие диски имели одинаковый диаметр, в его турбине диаметры дисков увеличиваются по мере падения давления пара.
Использование реактивной силы – это второй способ превращения скорости истечения пара – кинетической энергии – в механическую работу.
Реактивное действие пара можно увидеть на примере работы шара, сконструированного выдающимся древнегреческим ученым и инженером Героном Александрийским в Египте (около I века н.э.) (рис. 4.9). Эолипил Герона состоит из полого металлического шара 3, подвижно насаженного на две опоры 2, через которые из резервуара 1 (парового котла) подается к нему пар. Шар имеет две трубочки 4 с загнутыми в противоположные стороны насадками.
Рис. 4.9. Эолипил Герона
Реактивная сила вытекающего из насадок пара возникала из-за перепада давлений пара внутри и вне трубки и приводила шар во вращение.
Реактивные турбины, введенные в практику Парсонсом, выполнялись со ступенями давления и представляли собою чередование неподвижных и подвижных лопаток. Расширение пара совершалось не только до поступления его на рабочие лопатки (как в активной турбине), но и во время прохождения между рабочими лопатками.
Реактивные турбины Парсонса начали широко применяться с 1900 года, когда в Германии на Эльберфельдской электростанции были установлены и испытаны две турбины мощностью по 1000 кВт при 1500 об/мин. Турбины работали при среднем давлении пара 1,05 МПа и температуре 200°С и показали расход пара 8–9 кг/кВт при полной нагрузке.
Таким образом, в конце XIX века были разработаны основные принципы работы и устройства активных и реактивных турбин, которые в ХХ веке стали основными тепловыми двигателями турбогенераторов электростанций.
Помогитие написать доклад по физике тема Паровая Турбина
Паровые турбины работают следующим образом: пар, образующийся в паровом котле, под высоким давлением, поступает на лопатки турбины. Турбина совершает обороты и вырабатывает механическую энергию, используемую генератором. Генератор производит электричество.Электрическая мощность паровых турбин зависит от перепада давления пара на входе и выходе установки. Мощность паровых турбин единичной установки достигает 1000 МВт.
В зависимости от характера теплового процесса паровые турбины подразделяются на три группы: конденсационные, теплофикационные и турбины специального назначения. По типу ступеней турбин они классифицируются как активные и реактивные.
Конденсационные паровые турбины
Конденсационные паровые турбины служат для превращения максимально возможной части теплоты пара в механическую работу. Они работают с выпуском (выхлопом) отработавшего пара в конденсатор, в котором поддерживается вакуум (отсюда возникло наименование). Конденсационные турбины бывают стационарными и транспортными.
Стационарные турбины изготавливаются на одном валу с генераторами переменного тока. Такие агрегаты называют турбогенераторами. Тепловые электростанции, на которых установлены конденсационные турбины, называются конденсационными электрическими станциями (КЭС). Основной конечный продукт таких электростанций — электроэнергия. Лишь небольшая часть тепловой энергии используется на собственные нужды электростанции и, иногда, для снабжения теплом близлежащего населённого пункта.
Частота вращения ротора стационарного турбогенератора связана с частотой электрического тока 50 Герц. То есть на двухполюсных генераторах 3000 оборотов в минуту, на четырёхполюсных соответственно 1500 оборотов в минуту. Частота электрического тока вырабатываемой энергии является одним из главных показателей качества отпускаемой электроэнергии. Современные технологии позволяют поддерживать частоту вращения с точностью до трёх оборотов. Резкое падение электрической частоты влечёт за собой отключение от сети и аварийный останов энергоблока, в котором наблюдается подобный сбой.
В зависимости от назначения паровые турбины электростанций могут быть базовыми, несущими постоянную основную нагрузку; пиковыми, кратковременно работающими для покрытия пиков нагрузки; турбинами собственных нужд, обеспечивающими потребность электростанции в электроэнергии. От базовых требуется высокая экономичность на нагрузках, близких к полной (около 80 %), от пиковых — возможность быстрого пуска и включения в работу, от турбин собственных нужд — особая надёжность в работе. Все паровые турбины для электростанций рассчитываются на 100 тыс. ч работы (до капитального ремонта).
Паровая и газовая турбины: преимущества и недостатки агрегатов
Паровые и газовые турбины используются для приведения в движение генератора, вырабатывающего электрическую энергию. Они отличаются по виду используемого на входе вещества. Объединение преимуществ двух типов агрегатов образует парогазовую установку, позволяющую значительно повысить коэффициент полезного действия.
Назначение энергетических турбин
Энергетическая турбина является приводным механизмом станций по выработке тепла и электроэнергии. Она представляет собой вращающийся вал с лепестками, на которые подается рабочее тело. Вследствие попадания на лопатки вещества под давлением начинает функционировать генератор, соединенный с валом и вырабатывающий энергию.
Турбины делятся на два вида в зависимости от рабочего тела: паровые и газовые.
Отличий в конструкции этих устройств немного. Входящее вещество обеих турбин проходит через камеру сгорания, после чего продукты горения под давлением подаются на лопатки и приводят вал в движение.
Паровая турбина: преимущества и недостатки
В паровой турбине движение вала обеспечивается горячим паром. На входе в систему используется вода.
Преимущества:
- Длительный срок службы – около 20 лет
- Широкий выбор топлива
- Высокий КПД
- Широкий диапазон мощностей
- Отсутствие необходимости подготовки топлива
Рис.1. Паровая турбина
Среди недостатков выделяют долгий запуск агрегата, который может длиться сутками, сложный процесс обслуживания и большое количество вредных выбросов при работе.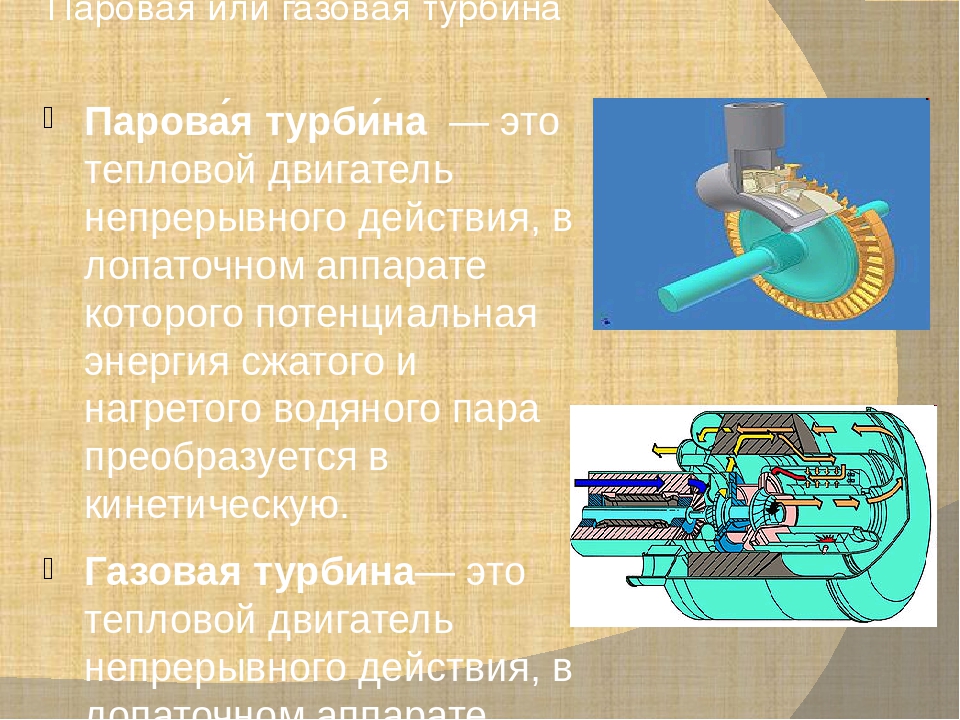
Газовая турбина: преимущества и недостатки
Особенностью газовой турбины является отсутствие изменения агрегатного состояния рабочего тела. Благодаря этому достигается гораздо большая рабочая температура и повышение КПД.
Преимущества газовой турбины:
- Уменьшенные габариты при одинаковой мощности с паровыми
- Быстрый запуск
- Высокая маневренность
- Широкий спектр используемого топлива
- Потребность в охлаждающей жидкости снижена в 5 раз
- Низкие расходы на техобслуживание, небольшой расход смазочных материалов
- Малое количество сопряженных деталей, снижение потерь на трение
- Постоянство электрической частоты
- Снижение уровня шума и вибрации при работе, а также вредных выбросов
Рис.

Обслуживание паровой и газовой турбины
Высокие температуры и нагрузки оказывают значительное влияние на срок службы механизмов турбин. Для обеспечения нормального функционирования детали производятся из жаростойких материалов с повышенной удельной прочностью.
Однако этого бывает мало и детали нуждаются в дополнительной защите, особенно в моменты запуска и остановки агрегатов.
Для этого на этапе производства элементов турбоустановок на наиболее подверженные износу части наносят антифрикционные твердосмазочные покрытия.
Рис. 3. Лопатки турбин до и после нанесения защитного покрытия на хвостовики
Хвостовики лопаток турбин обрабатываются составом MODENGY 1001, подшипники скольжения — MODENGY 1001 и MODENGY 1002, прессовые посадки — MODENGY 1005, ходовые винты — MODENGY 1001, конденсатоотводчики — MODENGY 1001, крепежные изделия — MODENGY 1014.
Парогазовая турбина
В структуре мировой энергетики усиливается удельный вес газовых турбин и парогазовых установок. Последние представляют собой агрегаты с двумя двигателями: паросиловым и газотурбинным.
На входе имеется газ, который расширяется и подается на лопатки газовой турбины. Генератор, прикрепленный к ее валу, начинает вырабатывать электрический ток.
Неиспользованный для этого процесса горячий воздух попадает в котел-утилизатор паросиловой установки, нагревая воду до образования пара.
Горячий пар подается на вторую турбину – паровую. Она приводит в действие второй электрогенератор.
Преимущества парогазовых установок:
- Повышение КПД до 60 процентов
- Низкая стоимость единицы получаемой энергии
- Короткие сроки монтажа (до года)
- Повышение экологичности и компактности по сравнению с паровыми турбинами
- Возможность перестройки с паросиловой установки
Рис.
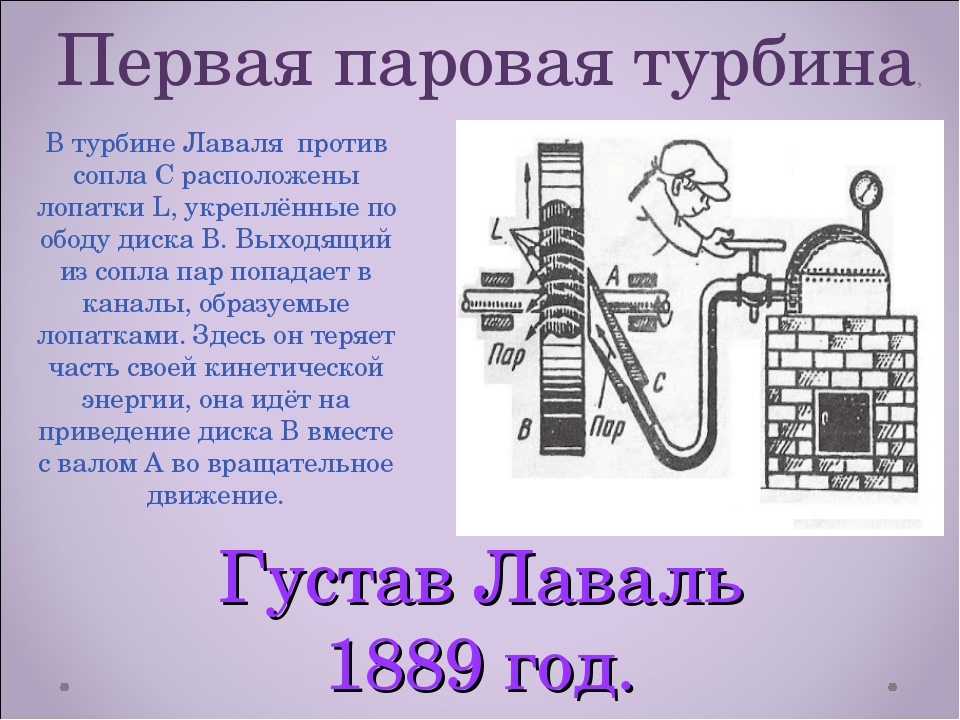
Сообщение по физике на тему:»Двигатели внутреннего сгорания. Паровая турбина» в 8 классе.
МКОУ» Ростошинская СОШ»
СООБЩЕНИЕ
по физике
ТЕМА:
«История изобретения паровых машин».
Подготовила: ученица 8 класса Щурова Ольга Евгеньевна.
Учитель: Стебунова О.А.
История изобретения паровых машин.
Паровая машина — двигатель внешнего сгорания, который преобразовывает энергию пара в механическую работу.
История изобретения паровых машин начинает свой отсчет еще с первого столетия нашей эры. Нам становится известно устройство, описанное Героном Александрийским, и приводимое в действие паром. Пар, выходящий из сопл по касательной, закреплённых на шаре, заставлял двигатель вращаться. Настоящая же паровая турбина была изобретена в средневековом Египте гораздо позднее. Ее изобретателем является арабский философ, астроном и инженер 16 века Таги-аль-Диноме. Вертел с лопастями начинал вращаться благодаря потокам пара, направленным на него. В 1629 г. подобное решение было предложено итальянским инженером Джованни Бранка. Главным минусом этих изобретений было то, что потоки пара были рассеивающимися, а это безусловно приводит к большим потерям энергии.
Дальнейшее развитие паровых машин, не могло происходить без подобающих условий. Необходимо было и экономическое благополучие и необходимость данных изобретений. Естественно этих условий не было и не могло быть до 16 века, в виду столь низкого уровня развития. В конце 17 века была создана пара экземпляров сих изобретений, но серьезно воспринята не была. Создателем первой является испанец Аянс де Бомонт. Эдвард Сомерсет — ученый из Англии в 1663 году опубликовал проект и установил приводимое в движение паром устройство для подъёма воды на стену Большой башни в замке Реглан. Но поскольку все новое трудно воспринимается человеком, то финансировать данный проект никто не решился. Создателем парового котла считается француз Дени Папен. В ходе проведения опытов по вытеснению воздуха из цилиндра, посредством взрыва пороха, он выяснил, что полный вакуум можно получить только с помощью кипящей воды. А чтобы цикл был автоматический, необходимо чтобы пар производился отдельно в котле. Папену приписывают изобретение лодки, которое приводилось в движение посредством реактивной силы в комбинации концепций Таги-аль-Дина и Севери; также его изобретением считается предохранительный клапан.
Все описанные устройства не были использованы и признаны практичными. Даже «пожарная установка», которую в 1698 году сконструировал Томас Севери, прослужила не долго. Из-за высокого давления создаваемого паром в емкостях с жидкостями, они часто взрывались. Поэтому его изобретение посчитали небезопасным. В свете всех этих неудач история изобретения паровых машин могла бы прерваться, но нет.
Презентация по физике на тему «Паровые и газовые турбины»
ПАРОВЫЕ И ГАЗОВЫЕ ТУРБИНЫ
- 1. Паровая турбина
- 1.1 История изобретения
- 1.2 Принцип действия
- 1.3 Применение
- 2. Газовая турбина
- 2.1 История изобретения
- 2.2 Принцип действия
- 2.3 Применение
- 3. КПД паровых и газовых турбин
- 4. Заключение
ПАРОВАЯ ТУРБИНА
сопло
Парова́я турби́на (фр. turbine от лат. turbo вихрь, вращение ) — это тепловой двигатель непрерывного действия, в лопаточном аппарате которого потенциальная энергия сжатого и нагретого водяного пара преобразуется в кинетическую, которая в свою очередь совершает механическую работу на валу.
Поток водяного пара поступает через направляющие аппараты на криволинейные лопатки, закрепленные по окружности ротора, и, воздействуя на них, приводит ротор во вращение.
вал
диск
лопатки
ИЗ ИСТОРИИ
Разработки Густава де Лаваля
Турбина Лаваля представляла собой легкое колесо, на лопатки которого через несколько поставленных под острым углом сопел наводился пар. В 1889 году он значительно усовершенствовал свое изобретение, дополнив сопла коническими расширителями. Это значительно повысило КПД турбины и превратило ее в универсальный двигатель.
ПРИНЦИП ДЕЙСТВИЯ
В соплах потенциальная энергия пара преобразуется в кинетическую; в лопаточном канале под воздействием струи пара возникает центробежная сила, воздействующая на лопатки и вызывающая вращение ротора турбины. При соединении вала с генератором тока механическая энергия преобразуется в электрическую.
ПРИМЕНЕНИЕ
Применяется в качестве привода электрического генератора на тепловых, атомных и гидроэлектростанциях, в качестве двигателей на морском, наземном и воздушном транспорте, как составная часть гидродинамической передачи.
ГАЗОВАЯ ТУРБИНА
Газовая турбина (фр. turbine от лат. turbo вихрь, вращение) — это двигатель непрерывного действия, в лопаточном аппарате которого энергия сжатого и нагретого газа преобразуется в механическую работу на валу. Основными элементами конструкции являются ротор и статор, именуемый сопловым аппаратом.
ИЗ ИСТОРИИ
Норвежец Еджидиус Эллинг построил первую газовую турбину, которая могла выдать больше энергии, чем необходимо для ее работы, что рассматривалось как значительное достижение по тем временам, когда знания о термодинамике были ограничены. Однако только в конце XIX века, когда термодинамика, машиностроение и металлургия достигли достаточного уровня, Густаф Лаваль (Швеция) и Чарлз Парсонс (Великобритания) независимо друг от друга создали пригодные для промышленности газовые турбины.
ПРИНЦИП ДЕЙСТВИЯ
Газ под высоким давлением поступает через сопловой аппарат турбины в область низкого давления, при этом расширяясь и ускоряясь. Далее, поток газа попадает на рабочие лопатки турбины, отдавая им часть своей кинетической энергии и сообщая лопаткам крутящий момент. Рабочие лопатки передают крутящий момент через диски турбины на вал.
ПРИМЕНЕНИЕ
Газовые турбины используются в кораблях, локомотивах и танках. Множество экспериментов проводилось с автомобилями, оснащенными газовыми турбинами. Но чаще всего газовая турбина используется как привод генераторов. Применяются также в составе газотурбинных двигателей, стационарных газотурбинных установок (ГТУ) и парогазовых установок (ПГУ).
КПД ПАРОВЫХ И ГАЗОВЫХ ТУРБИН
КПД паровой или газовой турбины 20–40%. Для повышения КПД на многих электростанциях тепло, отбираемое от паровой турбины, используется для нагревания воды. Горячая вода поступает в систему бытового и промышленного теплоснабжения.
ЗАКЛЮЧЕНИЕ
Поиски оптимального варианта привели к созданию комбинированных активных турбин со ступенями скорости. На ступенях происходит понижение температуры, поэтому лопатки ступеней можно делать из более дешевого материала, что дает экономический выигрыш. Паровые и газовые турбины очень актуальны в наше время и способствуют жизнедеятельности человека. Однако они оказывают вредное влияние на экологию и здоровье людей.
Спасибо за внимание!!!
Конспект урока «Паровая турбина. КПД тепловых двигателей»
План — конспект урока
Паровая турбина. КПД тепловых двигателей
- Организационный момент
Здравствуйте. Садитесь. Проверьте вашу готовность к уроку. Сконцентрируйтесь. Начнем наш очередной урок. Мы заканчиваем изучение темы «Тепловые явления», но вначале давайте вспомним, о чем шла речь на предыдущих уроках.
- Проверка знаний учащихся. Фронтальный опрос:
- Какие двигатели называют тепловыми?
- Какие виды тепловых двигателей вам известны?
- Какие переходы и превращения энергии происходят в них?
- Какой двигатель называют двигателем внутреннего сгорания? (на модели)
- Назовите основные узлы простейшего двигателя внутреннего сгорания.
- Вспомним принцип работы ДВС. Заполните таблицу. Проверяем ваши ответы, отмечаем правильные + и неправильные — .
- Актуализация опорных знаний.
Я неоднократно говорила вам о том, что все физические явления, законы в конечном
итоге находят применение в повседневной жизни человека.
Жизнь людей невозможна без использования различных видов энергии. Источниками
энергии являются различные виды топлива, а также энергия ветра, солнечная энергия,
энергия приливов и отливов.
- 4.
Угадайте, о чем идет речь?
Был водой, теперь летаю.
С виду я туман напоминаю.
Ответ: Пар
Что видно, если ничего не видно?
Ответ: Пар
О чем же сегодня на уроке мы будем говорить?
Тема и Цели урока: Мы познакомимся еще с одним видом тепловых двигателей – паровой турбиной, а кроме этого выясним такой вопрос, что происходит с внутренней энергией в результате ее преобразования в механическую.
Итак, тема нашего урока «Паровая турбина. КПД теплового двигателя». Запишите,
пожалуйста, в ваших рабочих тетрадях число и тему урока.
Изучение нового материала.
В современной технике кроме двигателя внутреннего сгорания широко применяют
другой тип теплового двигателя. В нем пар или нагретый до высокой температуры газ
вращает вал двигателя без помощи поршня, шатуна и коленчатого вала. Такие двигатели
называют турбинами. Схема устройства простейшей паровой турбины приведена на рисунке. На вал 5 насажен диск 4, по ободу которого закреплены лопатки 2. Около лопаток расположены трубы – сопла 1, в которые поступает пар 3 из котла. Струи пара, вырывающиеся из сопел, оказывают значительное давление на лопатки и приводят диск турбины в быстрое вращательное движение.
История изобретения паровой турбины насчитывает не одну сотню лет. Сообщение Шаухиной О.
Физкультминутка.
Модель турбины Герона сейчас может придумать каждый из вас. Вот один из примеров. Объясните опыт. (Опыт)
В современных турбинах применяют не один, а несколько дисков, насаженных на
общий вал. На электростанциях с турбиной соединен генератор электрического тока. Частота вращения вала турбин достигает 30 000 оборотов в минуту, что является очень удобным для приведения в движение генераторов электрического тока. (Слайды 9,10)
Любой тепловой двигатель превращает в механическую энергию только незначительную часть энергии, которая выделяется топливом. Большая часть энергии топлива не используется полезно, а теряется в окружающем пространстве.
При использовании тепловых машин остро встает вопрос загрязнения окружающей
среды.
При сжигании топлива в атмосферу попадает очень много вредных выбросов. К ним
можно отнести углекислый газ СО2, угарный газ СО, различные виды сернистых
соединений, а также соединения тяжелых металлов. Поэтому очень большое внимание следует уделять развитию методов защиты
окружающей среды от этих продуктов сгорания и созданию новых альтернативных
источников энергии.
Тепловой двигатель состоит из нагревателя, рабочего тела и холодильника. Газ или пар, который является рабочим телом, получает от нагревателя некоторое количество теплоты. Рабочее тело, нагреваясь, расширяется и совершает работу за счёт своей внутренней энергии. Часть энергии передаётся атмосфере — холодильнику — вместе с отработанным паром или выхлопными газами.
Очень важно знать, какую часть энергии, выделяемой топливом, тепловой двигатель
превращает в полезную работу. Чем больше эта часть энергии, тем двигатель экономичнее.
Для характеристики экономичности различных двигателей введено понятие
коэффициента полезного действия двигателя – КПД. (Слайд 13)
- Закрепление материала. Решим задачи на определение КПД тепловых двигателей.
- Тепловая машина, получив 4000 Дж тепла, совершила работу в 1 кДж. Определите
КПД машины. (Ответ: КПД = 25%)
- КПД машины 40%. Определите работу, которую совершила машина, если она
получила 6 кДж тепла. (Ответ: А = 2400 Дж)
- Выполняя домашнее задание, ученик записал: «К машинам с тепловым двигателем
относятся: реактивный самолет, паровая турбина, мопед». Дополните эту запись
другими примерами.
- Рефлексия.
Подведение итогов урока. Выставление оценок.
Домашнее задание. п.23-24, итоги гл. 1
Спасибо за урок!
Преимущества и недостатки паровых турбин
Преимущества наших паровых турбин
Ознакомьтесь с преимуществами паровых турбин производства G-Team. К их достоинствам относятся быстрая окупаемость инвестиций и высокая эффективность, так как в турбинах используется избыточное тепло, которое обычно бессмысленно теряется.
Зарабатывайте деньги там, где другие теряют. Создайте новый источник энергии из избыточного пара.
Предложение комплексного решения уменьшает Ваши затраты на установку. Наши турбины просты в эксплуатации и высокоавтоматизированы.
- Минимальные установочные размеры
- Высокая тепловая эффективность в диапазоне 85-93,5 %
- Минимальный срок службы 25 лет
Быстрая окупаемость
Период окупаемости, как правило, до 2 лет
Срок окупаемости зависит от мощности паровой турбины, ее расположения в системе и других личных предпочтений, которые могут у Вас возникнуть. Однако, мы всегда можем гарантировать Вам хорошее соотношение цены и выгоды
Эффективность
Возможность использования даже самых малых источников пара
Малые паровые турбины используют энергию избыточного пара, которая в противном случае теряется, таким образом, зарабатывая деньги с помощью производства электроэнергии.
Низкая стоимость установки
По сравнению с нормальными ЕРС единицами, стоимость нашей поставки значительно ниже.
Благодаря комплексному решению, нет лишних затрат на строительство для добавления дополнительных устройств. Затраты могут быть дополнительно снижены, в зависимости от простоты установки, которая отражает ваши индивидуальные потребности.
Простота
Наши турбины легко настроить и просто использовать.
- простое конструктивное решение
- комплектная поставка с фундаментальной рамой и маслом
- нет необходимости в дополнительных поставщиках второстепенных услуг
- нет необходимости в установке дополнительных устройств для обработки пара
- незначительные ремонтные работы достаточно просты, чтобы Ваш технический отдел мог сам справиться с ними
Высокая автоматизация
Благодаря высокой автоматизации, эксплуатация и техническое обслуживание паровой турбины весьма просты.
Расход и работа паровой турбины
Паровые турбины — одна из старейших и наиболее универсальных технологий первичных двигателей, остающихся в общем использовании. Они приводят в движение бесчисленное количество машин и производят электроэнергию на многих заводах по всему миру. Паровые турбины использовались более 120 лет, когда они заменили поршневые паровые двигатели из-за их более высокой эффективности и более низкой стоимости. Мощность паровой турбины может варьироваться от 20 киловатт до нескольких сотен мегаватт (МВт) для больших водителей.
Паровая турбина используется для выработки максимального количества механической энергии с использованием минимального количества пара в компактном приводе, обычно в конфигурации с прямым приводом. Возможности изменения или регулировки скорости также важны для паровых турбин. В настоящее время паровые турбины широко используются в различных приводах для механических приводов и энергоблоков и производят почти 1 миллион (МВт) мощности по всему миру.
Ротор паровой турбины — это вращающийся элемент, к которому прикреплены колеса и лопасти.Лезвие — это компонент, который извлекает энергию из пара.
Конструкции и типы паровых турбин
Доступны два основных типа конструкций паровых турбин. Один из них — это импульсная конструкция, в которой ротор вращается в результате воздействия пара на лопасти. Другой является реактивной конструкцией, и он работает по принципу, согласно которому ротор получает вращающую силу от пара, покидающего лопасти.
Пар обычно входит в один конец, движется в одном направлении к другому концу секции и выходит из обсадной колонны для повторного нагрева или передачи в следующую секцию.Однако в двухпоточной паровой турбине пар входит в середину и течет в обоих направлениях к концам секции. Двухпоточные устройства были популярны много лет назад. За исключением особых обстоятельств, они не рекомендуются для современных приложений.
Конденсатор
Основным типом паровой турбины является конденсационная паровая турбина, которая использовалась для больших приводов с превышением определенного предела номинальной мощности (скажем, как очень грубое указание, выше 8 МВт).Эти паровые турбины выпускаются непосредственно в один или несколько конденсаторов, которые поддерживают условия вакуума на выходе из паровой турбины. Массив трубок с охлаждающей водой конденсирует пар в воду (жидкость) в конденсаторе.
Вакуум в конденсаторе возникает, когда охлаждающая вода из окружающей среды конденсирует пар (выхлоп турбины) в конденсаторе. Поскольку известно, что небольшое количество воздуха просачивается в систему, когда давление ниже атмосферного, для удаления неконденсируемых газов из конденсатора обычно используется относительно небольшой компрессор.Неконденсирующиеся газы могут включать воздух, небольшое количество побочного продукта коррозии, вызванной реакцией вода-железо, и водород.
Процессы конденсационной паровой турбины производят максимальную механическую мощность и эффективность от подачи пара. Однако выходная мощность конденсационных паровых турбин чувствительна к температуре окружающей среды. Конденсационные паровые турбины дорогие, большие, сложные и менее пригодны для применения с механическим приводом. Паровые турбины, особенно для машин малого и среднего размера, пропускают пар вокруг рядов лопаток и через торцевые уплотнения. Когда конец находится под низким давлением, как в случае с конденсационными паровыми турбинами, воздух может просочиться в систему. Утечки вызывают меньшую мощность, чем ожидалось.
Противодавление
Другой тип паровой турбины — это паровая турбина с противодавлением, которая является наиболее подходящим оборудованием для приложений с механическим приводом, таких как приводы компрессоров или насосов. Термин противодавление относится к паровым турбинам, которые выпускают пар с давлением выше атмосферного.Давление нагнетания обычно определяется конкретным применением пара в установке. Более низкие давления часто используются в малых и больших приложениях низкого давления (НД), таких как системы отопления, а более высокие давления часто используются при подаче пара в промышленные процессы.
Промышленные процессы часто включают дальнейшее расширение для других меньших механических приводов с использованием небольших паровых турбин для приведения в действие вращающегося оборудования (например, насосов смазочного масла), которое непрерывно работает в течение длительных периодов времени. Значительная способность к выработке механической энергии приносится в жертву, когда пар используется при значительном давлении, а не расширяется до вакуума в конденсаторе. Выпуск пара в парораспределительную систему при избыточном давлении 10 бар (изб.) Может принести в жертву примерно половину мощности, которая могла бы быть произведена при условиях пара на входе около 50 бар изб. И 420 ° C, что типично для малых и средних паровых турбин.
Между выходной механической мощностью конденсационной паровой турбины и комбинацией мощности и пара паровой турбины с противодавлением может быть обеспечено практически любое соотношение выходной мощности к теплу.Паровые турбины с противодавлением могут иметь множество различных противодавлений, что дополнительно увеличивает изменчивость отношения мощности к теплу.
Добыча
Третий тип паровых турбин — это паровые турбины с отжимом. Отборная турбина имеет одно или несколько отверстий в корпусе для отбора части пара при некотором промежуточном давлении. Отобранный пар можно использовать в технологических целях. Давление отбора пара может регулироваться или не регулироваться автоматически в зависимости от конструкции паровой турбины.
Регулируемый отбор позволяет лучше регулировать поток пара через паровую турбину для выработки дополнительной механической энергии в зависимости от рабочих сценариев. В некоторых специальных паровых турбинах могут быть предусмотрены несколько точек отбора, каждая из которых имеет разное давление, соответствующее разной температуре, при которой на установке необходимы услуги отопления (или другие услуги).
Конкретные потребности предприятия в паре и электроэнергии с течением времени определяют степень отбора пара.В больших, часто сложных установках, дополнительный пар может поступать (поступать в корпус и увеличивать поток в паровом тракте) к паровой турбине. Часто это происходит, когда несколько котлов и паропроизводящих систем используются при разном давлении из-за сложности установки и необходимости достижения максимальной тепловой эффективности или ее исторического существования (в сложных установках, которые подвергались нескольким реконструкциям и расширениям). Эти паровые турбины называются паровыми турбинами с впуском.Производители адаптировали запросы клиентов к дизайну, изменяя площадь проходного сечения на ступенях и степень, в которой пар извлекается (или удаляется из пути потока между ступенями), чтобы соответствовать техническим требованиям. В местах отбора и впуска пара клапаны управления потоком пара обычно увеличивают стоимость пара и системы управления.
Когда пар расширяется за счет высокого давления, как в больших паровых турбинах, пар может начать конденсироваться в турбине, когда температура пара падает ниже температуры насыщения при этом давлении.Если в паровой турбине образуются капли воды, может произойти эрозия лопаток, когда капли ударяют по лопаткам. На этом этапе расширения пар иногда возвращается в котел и повторно нагревается до высокой температуры, а затем возвращается в паровую турбину для дальнейшего (безопасного и надежного) расширения. В некоторых крупных паротурбинных установках сверхвысокого давления также могут быть установлены системы двойного перегрева.
Паровые турбины с отбором и впуском являются специальными машинами, и их следует использовать только в тех случаях, когда они действительно необходимы, поскольку их работа и управление всей системой сложны и иногда могут приводить к эксплуатационным проблемам.Паровые турбины с отбором и впуском представляют собой сложные турбомашины со сложным управлением и эксплуатацией, которые должны одновременно управлять паровыми турбинами (часто с переменной нагрузкой) с различными регуляторами расхода пара в зависимости от других агрегатов и требований системы. Их следует использовать только в специальных крупных установках, в которых другие более простые паровые турбины не могут быть коммерчески конкурентоспособными по своим мощностям, тепловому КПД или другим соображениям. Обычно использование сложной паровой турбины с отбором и впуском не оправдано для работы с мощностью в несколько мегаватт и сложных схем работы паровой турбины с переменной нагрузкой и скоростью.
Расход пара, работа и конструкция
Пар сначала нагревается в системе генерации пара (например, в котлах или системах утилизации отходящего тепла), где он достигает высокой температуры, примерно от 400 ° C до 600 ° C. Первый клапан, с которым сталкивается пар, когда он движется из системы генерации пара в паровую турбину, — это главный запорный клапан (главный отключающий или отключающий клапан), который либо полностью открыт, либо полностью закрыт. Этот клапан часто не контролирует поток пара, кроме как полностью его остановить.
Рис. 2. Показан еще один пример паровой турбины с внутренними устройствами, компонентами и подсистемами.
Регулирующие или дроссельные клапаны в различных устройствах и конфигурациях также используются для управления впуском пара. Также распространены комбинированные триггерные и дроссельные клапаны. Во многих паровых турбинах должны быть предусмотрены как минимум два независимых отключающих клапана для надлежащего резервирования. Эти клапаны расположены непосредственно перед паровой турбиной и предназначены для выдерживания полной температуры и давления пара.Эти клапаны необходимы, потому что при потере механической нагрузки паровая турбина быстро разгонится и разрушится. Это случается нечасто. Причиной этого может быть необычная первопричина, например, отказ муфты. Возможны и другие несчастные случаи, из-за которых требуется два или три независимых запорных клапана, которые обеспечивают безопасность и надежность, но увеличивают стоимость системы.
Приводы паровых турбин оснащены дроссельными клапанами или регуляторами сопел для регулирования потока пара и обеспечения работы с переменной скоростью.Привод паровой турбины может выполнять ту же функцию, что и привод электродвигателя с регулируемой скоростью. Паровые турбины обычно могут работать в широком диапазоне скоростей и не выходят из строя при перегрузке. Они также создают высокий пусковой крутящий момент, необходимый для нагрузок с постоянным крутящим моментом, например, для поршневых насосов или компрессоров.
Пар ударяет по первому ряду лопастей при таком высоком давлении, что он может создавать крутящий момент с небольшой площадью поверхности. Воздействие пара заставляет ротор вращаться. Однако по мере продвижения ступеней паровой турбины пар теряет давление и энергию, поэтому требуются все более большие площади поверхности. По этой причине размеры лопастей увеличиваются с каждой ступенью. Когда пар выходит из турбины, его температура падает, и он теряет почти все свое повышенное давление. Некоторое падение давления также происходит на диафрагме, которая является компонентом между внешней стенкой и внутренней перемычкой. Перегородки диафрагмы направляют пар к вращающимся лопастям.
Пар должен ударить по лопастям под определенным углом, чтобы максимизировать полезную работу давления пара. Здесь в игру вступают сопла. Между лопастными колесами размещены неподвижные кольца форсунок, чтобы «повернуть» пар под оптимальным углом для удара лопастей. Упорный подшипник установлен на одном конце главного вала для сохранения его осевого положения и предотвращения столкновения движущихся частей с неподвижными частями. Опорный подшипник поддерживает главный вал и не позволяет ему выскакивать из корпуса на высоких скоростях.
Вытяжной колпак направляет пар из последней ступени паровой турбины, и он спроектирован так, чтобы минимизировать потерю давления, которая снизила бы тепловой КПД паровой турбины. После выхода из выхлопной секции пар поступает в конденсатор, где охлаждается до жидкого состояния. В процессе конденсации пара обычно создается вакуум, который затем вводит больше пара из паровой турбины. Вода возвращается в систему производства пара, повторно нагревается и используется повторно. Регулятор — это устройство, которое регулирует скорость турбины.Современные паровые турбины имеют электронный регулятор, который использует датчики для контроля скорости, проверяя зубья ротора.
Чтобы спроектировать более эффективную паровую турбину, следует использовать кожух с соответствующими соплами и лопатками для удержания пара и клапаны для управления подачей пара к соплам. Толстостенные отливки, используемые для секций турбин, работающих под давлением, называются кожухами и обычно изготавливаются из материалов из легированной стали. Некоторые конструкции включают внутреннюю и внешнюю оболочки, которые служат для уравновешивания перепада давления и уменьшения толщины оболочки при тепловом напряжении, запуске и нагрузке.Многоступенчатые конструкции используются для повышения эффективности. Тип и количество ступеней турбины, а также форма и размер лопаток различаются. Они определяются на основе давления и температуры пара, давления выхлопных газов и скорости.
Когда ротор паровой турбины неподвижен, пар, проходящий через сопло, ударяет по лопаткам с полной силой, создавая наибольший крутящий момент. Однако, поскольку это происходит при остановленном роторе, выполняемая работа равна нулю.С другой стороны, если скорость ротора равна скорости пара, пар не будет иметь компоненты скорости относительно лопастей, и лопасти не будут вращаться. Следовательно, этот случай приводит к нулевому крутящему моменту и, опять же, нулевой работе. Максимальный КПД находится между этими двумя крайностями. Для достижения идеальных условий эксплуатации и максимальной эффективности необходимо провести надлежащую оптимизацию.
Из-за высокого давления, используемого в паровых турбинах, корпус достаточно толстый, и, следовательно, паровые турбины обладают большой тепловой инерцией.Их следует медленно нагревать и охлаждать, чтобы свести к минимуму дифференциальное расширение между вращающимися лопастями и неподвижными компонентами. Для разогрева больших паровых турбин может потребоваться от пяти до девяти часов. В то время как агрегаты меньшего размера имеют более быстрое время запуска, паровые турбины заметно отличаются от поршневых двигателей, которые запускаются быстро, и от газовых турбин, которые могут запускаться за умеренное время и с разумной скоростью следовать за нагрузкой.
Применения паровых турбин обычно работают непрерывно в течение продолжительных периодов времени, даже несмотря на то, что пар, подаваемый в агрегат, и передаваемая механическая мощность могут изменяться в течение таких периодов непрерывной работы.Поскольку большинство паровых турбин выбираются для применений с высокими коэффициентами нагрузки, характер их применения часто учитывает необходимость только медленных изменений температуры во время работы, и можно допустить длительное время запуска. Паровые котлы также имеют длительное время запуска.
Поток, износ и деградация
Примеси в паре могут вызывать отложения, накипь и коррозию в паровых турбинах, что отрицательно сказывается на их работе. Три наиболее важных механизма отказа в любой паровой турбине низкого давления, связанные с коррозией, — это точечная коррозия, коррозионная усталость и коррозионное растрескивание под напряжением.Местная паровая среда определяет, возникают ли эти механизмы повреждения на поверхностях лезвий и дисков.
Зона фазового перехода, где расширение и охлаждение пара приводит к конденсации, особенно важна. Ряд процессов, происходящих в этой зоне, таких как осаждение химических соединений из перегретого пара, осаждение, испарение и высыхание жидких пленок на горячих поверхностях, приводят к образованию потенциально коррозионных поверхностных отложений.
Чистота пара и условия отключения — два параметра, которые приводят к коррозионным повреждениям.Еще одним важным фактором могут быть условия окружающей среды, возникающие во время останова. Это условия, которые возникают во время незащищенного останова, когда насыщенные кислородом влажные и жидкие пленки образуются на поверхностях паропровода в результате гигроскопических эффектов. Эти пленки непосредственно вызваны ненадлежащими методами останова, принятыми группой по эксплуатации / техническому обслуживанию паровых турбин или всей командой. Они могут привести к питтингу, который чаще всего является предвестником механизмов коррозии.
Соответствующие свойства материала (такие как состав, структура и внутренние напряжения) и конструкция (температура, напряжения и щели) также играют важную роль.Точечная коррозия может также возникать во время работы в щелях, например, в местах крепления лезвий. Чистота пара контролирует большинство процессов коррозии и жизненно важна для надежности паровой турбины.
Механические блокировки могут возникать в результате отложений. Блокировки в чувствительных местах, хотя и встречаются редко, обычно имеют серьезные последствия. Например, даже небольшие отложения на штоке обратного клапана паровой турбины могут нарушить его работу. В случае отключения паровой турбины неисправный обратный клапан может привести к продолжению потока пара и некоторому повреждению турбины.Кроме того, отложения на неподвижных частях, если они достаточно толстые и сильные, могут препятствовать движению лезвия, представляя особый риск механического повреждения небольших лезвий.
Закупорка парового тракта изменяет соотношение давлений в паровой турбине таким образом, что может вызвать осевое смещение вала. Это может привести к контакту между вращающимися и неподвижными частями, что может привести к серьезному повреждению. Такие условия часто обнаруживаются и избегаются путем контроля давления в паровой турбине.
Более частым, но менее значимым результатом блокировки потока пара является снижение пропускной способности (поглощающей способности) паровой турбины и изменение эффективного профиля потока пара на лопатках паровой турбины. Эти изменения приводят к уменьшению расхода пара, снижению выходной мощности и снижению эффективности турбины. Распространенными примерами являются отложения меди и алюминия в паровых турбинах высокого давления и отложения кремнезема в турбинах среднего и низкого давления.
Амин Алмаси — старший консультант по вращающемуся оборудованию в Австралии. Он является дипломированным профессиональным инженером Engineers Australia и IMechE и имеет степени бакалавра и магистра в области машиностроения и RPEQ. Он является активным членом Engineers Australia, IMechE, ASME и SPE и является автором более 100 документов и статей, посвященных вращающемуся оборудованию, мониторингу состояния, оффшорным, подводным и надежности.
Паровые турбины — обзор
Общие цели управления и защиты линии
Таблица 5.В 10.1 представлены общие цели управления и защиты поездов.
Таблица 5.10.1. Общие цели управления / защиты линии
|
Независимо от типа приводного оборудования, цель системы управления и защиты — обеспечить непрерывную подачу необходимого количества продукта или генерируемой энергии, поддерживая максимально возможную общую эффективность поезда и надежность.
На рис. 5.10.1 представлена технологическая схема компрессорной линии с приводом от паровой турбины.
Рисунок 5.10.1. Полный контроль поезда.
В зависимости от выбранной переменной процесса и местоположения любой PIC или FIC будет непрерывно контролировать выбранную переменную процесса, посылая свой сигнал в качестве входного сигнала на регулятор скорости турбины.Для этого примера предположим, что уставка — это регулятор расхода, расположенный в нагнетательной линии турбокомпрессора ( FIC D ). Показаны требования к напору (энергии) технологической системы A, B, C. Эти различные потребности в энергии могут отражать либо повышенные требования к соотношению давлений (блокировка теплообменника всасывающего фильтра Δ P и т. Д.), Либо изменения плотности газа (M.W. P или T ). По мере того, как требования к напору (энергии) увеличиваются от A до B до C, переменная входящего потока будет уменьшаться, если скорость турбокомпрессора не изменится.Однако, как только контролируемая переменная процесса, FIC D уставка расхода, выход регулятора скорости турбины откроет впускные дроссельные клапаны турбины, чтобы обеспечить большую мощность турбины для увеличения напора (энергии), производимого компрессором, до соответствовать дополнительным требованиям к головке технологической системы и, следовательно, поддерживать желаемую производительность.
Регулировка скорости приводимого оборудования является наиболее эффективным методом управления, поскольку в системе не требуются регулирующие клапаны.Поэтому турбокомпрессор производит только точное значение напора, требуемое технологической системой.
Также на рис. 5.10.1 отмечены две основные системы защиты компрессора и паровой турбины, системы защиты от перенапряжения и защиты турбины от превышения скорости. Система помпажа обсуждалась ранее, система превышения скорости турбины будет рассмотрена позже в этой главе. В дополнение к двум основным системам защиты, упомянутым выше, другими типичными системами защиты для вращающегося оборудования являются:
- ■
Вибрация вала
- ■
Вибрация опоры подшипника
- ■
Осевое усилие рабочий объем
- ■
Температура подшипника
- ■
Температура технологического газа
- ■
Давление смазочного масла
- ■
6
- Высокий уровень жидкости во всасывающем барабане (компрессоры)
Control
Регулятор турбины — это регулятор скорости.Важные факты, касающиеся регуляторов турбодетандера, показаны в Таблице 5.10.2.
Таблица 5.10.2. Управление
|
Независимо от типа, все контроллеры имеют три идентичных параметра:
- ■
Вход
- ■
Уставка
- ■
Выход
Некоторые известные контроллеры:
Температура
Помпаж
Скорость
В качестве примера см. Рис.5.10.2, который может быть вам знаком.
Рисунок 5.10.2. Аналогия с системой управления.
(A) Круиз-контроль. (B) Регулятор паровой турбины.
В обоих случаях изменение нагрузки обратно пропорционально изменению скорости. Контроллер сравнивает ввод с уставкой и соответствующим образом изменяет вывод.
На рис. 5.10.2 мы сравниваем автоматический «круиз-контроль» с регулятором паровой турбины (типичный одноступенчатый механический / гидравлический). Оба являются контроллерами скорости и имеют:
- ■
Вход
- ■
Уставка
- ■
Выход
В таблице ниже показано сравнение этих параметров.
Параметр | C.C. (Круиз-контроль) | T.G. (Регулятор турбины) |
---|---|---|
Ввод | Фактическая скорость от спидометра | Фактическая скорость от набора скорости |
Уставка | Выбирается водителем | Выбирается оператором |
Выход Кому Система управления подачей топлива | К дроссельному клапану подачи пара |
Рис.5.10.3 — схема системы регулятора паровой турбины.
Рисунок 5.10.3. Управление паровой турбиной.
(любезно предоставлено M.E. Crane, консультантом)Обратите внимание, что уставка может быть либо ручной уставкой, подобно тому, как водитель устанавливает «скорость» в системе круиз-контроля, либо переменной процесса. Примеры уставок переменных процесса:
- ■
Давление
- ■
Расход
- ■
Уровень (приложения с насосом)
Существует множество конструкций контроллеров.Исторически первые контроллеры были полностью механическими. Пример механического регулятора скорости показан на рис. 5.10.4.
Рисунок 5.10.4. Система механического регулятора.
Обычно называемый «Fly Ball Governors», входной вал от привода будет вращать грузы через зубчатую передачу. Когда грузы вращаются, центробежная сила будет перемещать грузы наружу, сжимая пружину и, таким образом, перемещая рычажный механизм на выходе . Натяжение пружины от переключателя скорости (заданное значение) будет управлять скоростью как точкой равновесия входных и заданных значений.
Многие механические регуляторы все еще используются на старых небольших одноклапанных паровых турбинах. Выходная сила механического регулятора ограничена и приводит к созданию механического гидравлического регулятора, изображенного на рис. 5.10.5.
Рисунок 5.10.5. Система механического гидравлического регулятора.
Механико-гидравлический регулятор использует тот же механический механизм для определения выходного сигнала. Однако выходной вал перемещает пилотный клапан, который позволяет гидравлической жидкости (обычно маслу) подавать выходной сигнал на дроссельную заслонку (клапаны).Обычный Вудворд «T.G.» и «П.Г.» регуляторы являются примерами механических / гидравлических регуляторов. Эти регуляторы имеют внутренние масляные насосы прямого вытеснения, приводимые в действие входным валом регулятора.
Для всех механико-гидравлических регуляторов требуется гидравлическая жидкость, и методы профилактического обслуживания на объекте должны включать эти регуляторы. Они снабжены смотровым окном для индикации рабочего уровня гидравлической жидкости. Типичными используемыми жидкостями являются турбинное масло и жидкость для автоматических трансмиссий «ATF».Для получения информации о конкретных гидравлических характеристиках необходимо обращаться к руководству по эксплуатации регулятора. В более крупных системах резервуар для гидравлической жидкости регулятора может быть недостаточно большим для обеспечения достаточного количества жидкости для заполнения всех маслопроводов регулятора скорости.
Читатели предупреждены о том, что может потребоваться дополнительная гидравлическая жидкость во время первоначального запуска и всякий раз, когда выполнялись работы с системой регулятора во время ремонта.
На рис. 5.10.6 представлена механико-гидравлическая система регулятора для многоклапанной паровой турбины.
Рисунок 5.10.6. Типовой механико-гидравлический регулятор для турбинного привода.
(любезно предоставлено Elliott / Woodward)Система показывает Woodward «P.G.–P.L.» система губернатора. Эти системы, распространенные в 1960-х и 1970-х годах, используются до сих пор и обеспечивают чрезвычайно надежное обслуживание. Однако как механические, так и механико-гидравлические регуляторы получают свой входной сигнал через зубчатую передачу. Поэтому их нельзя ремонтировать или снимать во время работы турбины. В течение 1970-х годов мощности нефтеперерабатывающих, нефтехимических и газовых заводов значительно выросли.В результате упущенная выгода от продукта из-за однодневного простоя для ремонта регулятора стала очень большой (обычно от 500 000 до более чем 1 000 000 долларов!). Следовательно, возникла острая необходимость в системе регулятора, которую можно было бы обслуживать без остановки турбины. Электрогидравлический регулятор удовлетворил эту потребность. В таблице 5.10.3 представлены важные факты, касающиеся этой системы.
Таблица 5.10.3. Электрогидравлические регуляторы
с тройным резервированием им не требовался механический входной сигнал (зубчатая или валковая передача), th Эти регуляторы можно было менять, в то время как операторы держали турбину в ручном режиме.По аналогии, замена автоматических регулирующих клапанов — это та же процедура. В этом случае оператор поддерживает технологические условия, вручную дросселируя байпасный клапан, в то время как автоматический регулирующий клапан подвергается ремонту.Первые электронные регуляторы аналогового типа требовали значительного обслуживания для замены карт. Цифровые регуляторы были представлены в конце 1970-х годов и являются единственным типом управления скоростью, используемым сегодня. По мере того, как микропроцессоры стали популярными, цифровые регуляторы также предложили большое преимущество избыточности.Резервные и тройные резервные регуляторы стали очень популярными, потому что регуляторы теперь могли автоматически переключаться в оперативный режим, позволяя поддерживать управление, в то время как другому регулятору требовалось техническое обслуживание. Помощь оператора больше не требовалась. На рис. 5.10.7 представлена блок-схема электрогидравлической системы регулятора.
Рисунок 5.10.7. Блок-схема электрогидравлического регулятора.
(Предоставлено консультантом M.E. Crane)В 1990-х годах была тенденция контролировать все процессы и функции оборудования через централизованную распределенную систему управления предприятием.Новый химический завод в Южной Америке в настоящее время проектирует D.C.S. система, которая будет управлять всеми критическими функциями системы:
- ■
Управление скоростью турбины
- ■
Управление процессом
- ■
Защита от перенапряжения
- ■
E. системы
- ■
Мониторинг в режиме онлайн
- ■
Автозапуск аварийного насоса
В этой конструкции все критические функции активируются на основе двух систем голосования из трех.
Как обсуждалось ранее, экстракционные турбины используются для оптимизации парового баланса завода и общей эффективности парового цикла. В таблице 5.10.4 определены функции системы управления паровой турбиной с отбором газов.
Таблица 5.10.4. Управление вытяжкой
|
Функция: удовлетворяет требованиям к управлению приводным оборудованием и обеспечивает необходимое количество отбираемого пара при желаемом расходе или давлении Система управления вытяжкой состоит из нескольких регуляторов с обратной связью |
Как механико-гидравлические, так и электрические -гидравлические системы управления вытяжкой успешно работают на месторождении.Любая конструкция включает два или более регуляторов, работающих вместе для достижения целей системы управления. Каждый выход регулятора управляет определенным набором дроссельных заслонок. Кроме того, каждый регулятор в системе отбора или впуска непрерывно получает входной сигнал от других регуляторов в системе. Каждый регулятор будет реагировать на этот входной сигнал в соответствии со всеми задачами управления системой регулятора.
Механико-гидравлические системы всасывания или впуска зарекомендовали себя как требующие значительного объема регулировки и обслуживания из-за высокого трения в системах.См. Рис. 5.10.8, на котором показана механико-гидравлическая система регулятора одинарной вытяжки.
Рисунок 5.10.8. Механическое / гидравлическое управление вытяжкой.
(любезно предоставлено Elliott / Woodward)В результате все новые системы включают электрогидравлический регулятор, как показано на рис. 5.10.9.
Рисунок 5.10.9. Электрогидравлическая система контроля и защиты вытяжки.
(любезно предоставлено M.E. Crane, консультантом)В сочетании с резервными функциями эти системы обеспечивают высокую надежность и эффективное управление процессами.Независимо от типа используемого регулятора, механико-гидравлические и электрогидравлические регуляторы должны быть снабжены надежной системой управления маслом. В таблице 5.10.5 представлены функции и часто встречающиеся проблемные области гидравлических систем управления.
Таблица 5.10.5. Система контрольного масла
Функция: Постоянно подавать холодное, чистое контрольное масло в систему управления и защиты при надлежащем давлении, скорости потока и температуре Частые проблемные области:
|
Обычно гидравлическая система управления встроена в систему смазки.Типичные диапазоны рабочего давления для этих систем:
Низкое давление | 276–690 кПа (40–100 PSI) |
Среднее давление | 827–4137 кПа (120–600 PSI) |
Высокое давление | Выше 4137 кПа (600 фунтов на квадратный дюйм) |
В таблице 5.10.6 приведена диаграмма применения, показывающая тип классификации регулятора, регулировку скорости и тип используемого регулятора.
Таблица 5.10.6. Схема применения системы регулятора паровой турбины
Оборудование, приводимое в действие приложениями | Регулирование скорости% | Тип системы регулятора |
---|---|---|
Запасной насос | NEMA A ± 10% | 16 Механическое (более раннее механическое) 906 (гидравлический) Электрогидравлический (опция) * Без резервирования |
Вентилятор (ы) | NEMA A ± 10% | Механический (старая гидравлика) Механический гидравлический |
Насос смазочного / уплотнительного масла ( с) | NEMA A ± 10% | Механический / гидравлический |
Турбокомпрессор | NEMA D ± 0.5% | Электрогидравлический (после 1980 г.) Без резервирования Дополнительный с тройным резервированием |
Генератор | NEMA D ± 0,5% | Изохронный (падение 0%) Механический / гидравлический Присутствует Электро -гидравлический |
Как правило, регуляторы NEMA A используются в приложениях общего назначения (резервные), а регуляторы NEMA D используются в приложениях специального назначения (не связанных).
Защита
По опыту авторов, функция системы защиты паровой турбины часто путается с системой управления.Эти две системы полностью разделены. Система защиты срабатывает только при превышении любого из заданных параметров системы управления, и паровая турбина будет повреждена, если продолжит работу. В таблице 5.10.7 определены типичные методы защиты.
Таблица 5.10.7. Защита
Система защиты контролирует общие параметры паровой турбины и обеспечивает безопасность и надежность с помощью следующих действий:
|
Схема многоклапанной многоступенчатой системы защиты турбины показан на рис.5.10.10.
Рисунок 5.10.10. Типовая защита паровой турбины.
(Предоставлено Elliott Co.)Эта система включает в себя механическое устройство превышения скорости (отключающий штифт) для отключения турбины при превышении скорости (на 10% выше максимальной продолжительной скорости). Центробежная сила, возникающая из-за высокой скорости вала, заставляет рычаг отключения, который позволяет подпружиненной рукоятке перемещаться внутрь. Когда это происходит, порт в штоке рукоятки позволяет давлению управляющего масла стечь и упасть до 0. Высокоэнергетическая пружина в расцепителе и дроссельной заслонке, обычно противодействующая давлению управляющего масла, внезапно закроется (менее 1 с) .В этой системе есть два других средства отключения турбины (снижение давления управляющего масла до 0):
- л
Ручное нажатие на пружинную ручку
- л
Открытие электромагнитного клапана
Электромагнитный клапан открывается по команде при превышении любого заданного значения параметра отключения. Электромагнитные клапаны предназначены для закрытия при нормальном напряжении.
В последние годы в промышленности потребовалось параллельное и последовательное расположение электромагнитных клапанов для обеспечения повышенной надежности паротурбинного агрегата.
На рис. 5.10.11 показаны два популярных метода защиты от превышения скорости, которые использовались в прошлом.
Рисунок 5.10.11. Обнаружение превышения скорости.
(любезно предоставлено Elliott Co.)Сегодня в большинстве систем скоростного отключения используются входные магнитные сигналы скорости, и два из трех голосующих обеспечивают повышенную надежность. В таблице 5.10.8 представлены устройства, отключающие турбину изнутри. То есть они напрямую снижают давление управляющего масла, вызывая закрытие клапана отключения без необходимости использования соленоидного клапана (метод внешнего отключения).
Таблица 5.10.8. Внутренняя защита
|
Показаны два популярных типа запорных клапанов паровых турбин на рис.5.10.12.
Рисунок 5.10.12. Запорная арматура паровых турбин.
(A) Отключение и дроссельная заслонка. (B) Поездка.
(Часть A: Предоставлено Gimple Corp. Часть B: Предоставлено Siemens)В обоих типах используется высокое усилие пружины, которому противодействует давление управляющего масла во время нормальной работы, чтобы быстро закрыть клапан при потере давления масла в системе управления.
Очень важно отметить, что управляющий клапан закроется только в том случае, если пружина имеет достаточную силу для преодоления трения штока клапана. Скопление твердых частиц в паровой системе, которое увеличивается с давлением в системе (когда паровые системы не обслуживаются должным образом), может помешать закрытию управляющего клапана.
Чтобы убедиться, что шток управляющего клапана может свободно перемещаться, все управляющие клапаны должны проверяться вручную на линии. Рекомендуемая частота — один раз в месяц.
Все клапаны отключения турбины должны быть снабжены ручными тренажерами, чтобы эта функция была возможна. В Таблице 5.10.9 представлены сведения о ручном испытании турбины в рабочем состоянии.
Таблица 5.10.9. Онлайн-ручное упражнение управляющего клапана
|
Философия систем защиты имеет тенденцию к географическому различию в зависимости от поставщиков паровых турбин.В таблице 5.10.10 представлены эти факты.
Таблица 5.10.10. Философия системы защиты
|
- B.P. 5.11:
Динамическое давление вакуума конденсатора сальника парового уплотнения в DCS.
Очень важно, чтобы конденсатор сальника на турбинах специального назначения (или общего назначения, если он оборудован конденсатором сальника) поддерживался ниже атмосферного давления, чтобы гарантировать, что пар всасывается, а не направляется к подшипниковому узлу. .
Анализируя давление вакуума, пользователь может увидеть, с какой скоростью изнашивается система уплотнения сальника (обычно обучающая) и которую необходимо отремонтировать. Для обеспечения оптимальной надежности парового уплотнения настоятельно рекомендуется использовать два эдуктора (один в качестве резервного, который можно переключить в оперативный режим) в сочетании с этой передовой практикой.
Для этого мониторинга необходимо установить передатчик, но он определенно стоит небольших дополнительных затрат заранее, учитывая головные боли и отказы, которые могут возникнуть из-за чрезмерного загрязнения водой в масляной системе.
- L.L. 5.11:
Отсутствие контроля и изменения разрежения в конденсаторе сальника на паровых турбинах специального назначения (без запасных частей) привело к сильному загрязнению масляных систем и сокращению срока службы подшипников.
Типы паровых турбин — обзор
14.2.2 Вращающееся щеточное уплотнение
Конструкция барабанного ротора типична для реактивного типа паровой турбины. В секциях турбин ВД и ПД предпочтительны турбины реактивного типа из-за их высокого КПД. В конфигурации барабанного ротора пространство для межступенчатого корневого уплотнения очень ограничено. В отличие от традиционной конфигурации колеса и диафрагмы, в конструкции ротора барабана нет места для колеса ротора. В результате нельзя применять обычные подпружиненные уплотнения. Вместо этого зубья уплотнения часто прикрепляются к ротору или обрабатываются как неотъемлемая часть ротора для образования уплотнения.Преимущество зубьев ротора заключается в том, что на неподвижный компонент можно надежно нанести истираемое покрытие, чтобы обеспечить плотный зазор и избежать образования грибовидных грибов на зубьях уплотнения при трении. Пожалуй, наиболее эффективным лабиринтным уплотнением является J-образное уплотнение с истираемым покрытием. На рис. 14.6 показано типичное истираемое J-образное уплотнение в местах расположения корня сопла.
Рисунок 14.6. J-образные уплотнения внутренней крышки форсунки с истираемыми материалами.
J-образные уплотнения способны очень хорошо истирать и разрезать истираемые покрытия. Однако они не соответствуют требованиям.Очень узкий зазор может затруднить запуск турбины и поворотного механизма. После трения во время переходных процессов рабочий зазор может быть большим. Следовательно, податливые и плотные уплотнения необходимы в конфигурации ротора барабана больше, чем в конфигурации колеса и диафрагмы.
Щеточные уплотнения снова являются хорошим решением для уплотнения корневой части форсунки, они соответствуют требованиям и работают более плотно, чем лабиринтные уплотнения. Однако есть несколько факторов, которые ограничивают применимость традиционных щеточных уплотнений в местах расположения корней форсунок.Одной из проблем, особенно в паровых турбинах, является нагрев от трения из-за трения щетины о ротор. Помимо износа щетинок, этот нагрев может также привести к неравномерному тепловому росту ротора, вызывая роторную динамическую нестабильность [7,8]. Кроме того, для конфигурации турбины с ротором барабана применимость стандартных щеточных уплотнений в месте расположения основания сопла ограничена пространственными ограничениями и методами конструкции сопла.
Традиционные щеточные уплотнения прикрепляются к стационарному компоненту турбомашины, где только гибкие кончики щетинок щеточного уплотнения входят в зацепление с ротором во время работы турбомашины, образуя динамическое уплотнение.Традиционные щеточные уплотнения также обычно включают щетинки, расположенные под углом по окружности относительно ротора. Во вращающемся щеточном уплотнении, как показано на рис. 14.7, набор щетинок прикреплен к ротору турбомашины и трется о статические компоненты. Щетинки расположены под углом, по существу, в осевом направлении и поддерживаются конической задней пластиной. Неподвижный конец вращающейся щетины прикрепляется к боковой пластине с помощью сварки или механического крепления, например зажима. Затем узел уплотнения закрепляется в кольцевой канавке ротора [8].
Рисунок 14.7. Вращающееся щеточное уплотнение у основания сопла.
Помимо экономии места на статоре, преимущество вращающегося щеточного уплотнения состоит в том, что тепло, выделяемое щеточным уплотнением, будет оказывать меньшее влияние на изгиб ротора, чем обычные щеточные уплотнения, поскольку кончики щетинок скользят по неподвижному компоненту. Тепло, выделяемое при трении кончиков набора щетинок о неподвижный компонент, частично переходит в неподвижный компонент, а частично отводится за счет утечки через набор щетинок, при этом меньше тепла передается в ротор.Напротив, в обычных щеточных уплотнениях кончики щетинок трутся о поверхность ротора, что непосредственно нагревает ротор. Этот нагрев ротора может привести к изгибу ротора и дальнейшему увеличению нежелательного неравномерного нагрева.
Подобно стандартным щеточным уплотнениям, вращающееся щеточное уплотнение состоит из набора щетинок и при установке образует кольцо. Однако вращающееся щеточное уплотнение прикреплено к ротору, а не к статору. Кроме того, набор щетинок наклонен по существу в осевом направлении, а не в основном по окружности, относительно оси вращения.Уплотнение дополнительно включает коническую заднюю пластину, которая частично поддерживает набор щетинок.
На рис. 14.7 показан пример того, как фиксированный конец набора щетинок может быть установлен или прикреплен к ротору. Коническая опорная пластина и фиксированный конец набора щетинок могут быть вставлены в канавку и прикреплены к ротору с помощью гребня, установочных винтов, ласточкин хвоста или комбинации этих методов.
В дополнение к характеристикам герметичности конструкция вращающегося щеточного уплотнения должна соответствовать требованиям к напряжению, жесткости и гибкости.Эти показатели зависят от комплексного взаимодействия зависит от давления между щетинками сил, центробежными сил и сил трения между опорной пластиной и пакетом щетинок, а также геометрией уплотнения. Во вращающихся щеточных уплотнениях дополнительные конструктивные параметры, такие как наклон щетинок в двух разных плоскостях, а также скорость ротора, усложняют эти взаимодействия. Поэтому для успешного проектирования вращающихся щеточных уплотнений необходимо строгое понимание физических факторов.
Вращающееся щеточное уплотнение — все еще относительно новая технология уплотнения. Соотношение выгод и затрат, долговечность уплотнения и удобство обслуживания еще предстоит доказать. Тем не менее, он действительно открывает пространство для применения щеточных уплотнений в турбомашинном оборудовании, включая уплотнения вала лонжерона в авиационных двигателях и промежуточные ступени в газовых турбинах.
Паровые турбины
Большая паровая турбина General Electric |
Паровые турбины встречаются повсюду на планете и используются для вращения
генераторы и производят электричество или создают двигательные установки для кораблей, самолетов,
ракеты.
Они преобразуют тепловую энергию в виде паров воды в движение, используя давление на вращающиеся лезвия. Это похоже на то, как турбины гидроэлектростанции за исключением того, что пар движется намного быстрее, а лезвия и устройство очень разные.
Паровые турбины используются со многими источниками энергии:
Ядерная энергия
Уголь
Ископаемое топливо / природный газ
Геотермальная энергия
Инженеры улучшили каждый миллиметр паровой турбины и это один из самых сложных предметов для проектирования и изготовления.Там это лишь несколько мест в мире, где производятся большие паровые турбины.
Крупные производители паровых турбин:
General Electric. Schenectady, NY
Siemens, Германия
Weir Allen Steam Turbines, Brazil
Elliot Group, Sodegaura Japan, Jeanette PA
Строящийся ротор большой паровой турбины в Скенектади, Нью-Йорк (фото: General Electric) |
История:
Идея паровой турбины возникла примерно в 100 году нашей эры.Современный пар турбины, разработанные на основе поршневого парового двигателя, типичного для 19 век. Первые новаторы, такие как Джордж Вестингауз знал, что возвратно-поступательное движение поршневых паровых машин потрачено впустую много энергии, и что если бы пар можно было направить в узкое пространство и давление, используемое для вращения вала, это приведет к максимальная энергоэффективность.
Хронология:
1712 — Паровая машина с поршнем, разработанная Томасом Ньюкоменом
1781 — Джеймс Ватт разрабатывает первую паровую машину, которая производит непрерывный вращательное движение
1831 — ДеВитт Клинтон запускает первое регулярное железнодорожное сообщение в Северной Америке. Олбани — Скенектади, штат Нью-Йорк, работает на поршневом паровом двигателе. После этого использование паровой машины возрастает. и официально начинается область машиностроения.
1884 — Сэр Чарльз Парсонс строит первую настоящую паровую турбину.
Знания, необходимые для его создания, были получены от
1885 — Джордж Вестингауз покупает патенты на паровые турбины и начинает улучшения.
1896 — Чарльз Кертис разрабатывает турбину, которая весит 1/8 от
существующих турбин и составлял 1/10 размера при той же мощности
1903 — Кертис и Уильям
Ле Рой Эммет разработал вертикальную турбину мощностью 5000 кВт для General Electric,
эта турбина создавала огромное количество энергии только в компактном пространстве.
25 футов в высоту.В то время все крупные электростанции США хотели этого.
1900-е годы — Паровые турбины становились все меньше и меньше, а мощность увеличивалась.
Некоторые турбины вырабатывают до 500 000 кВт.
Ниже: видео из Технического центра Эдисона о ранней истории паровых турбин с историком Джорджем Уайзом:
Как это работает:
Паровые турбины пропускают пар высокого давления через многоступенчатые роторы, что означает многие наборы лезвий извлекают всю возможную энергию из давления.
Подробнее см. TurbineGenerator.org>
CO-Generation:
Турбины Cogen имеют два отдельных поколения в одном потоке энергии, это извлекает максимум энергии из горячего потока пара. Они может иметь КПД более 80% по сравнению с обычной паровой турбиной растения, у которых около 40%.
Связанные темы:
Газовые турбины
Hydro (водяные турбины)
Связанные темы:
Источники:
Wabash Power Equipment Company
General Electric
Siemens
Turbocam International
Википедия
Эллиотт Групп
ASME
Музей Скенектади
Отказ от вибрации ротора паровой турбины: причины и решения
Роторы паровой турбины изгибаются во время работы, но подшипники и опоры сконструированы таким образом, чтобы удерживать статические и динамические силы под контролем.Однако изгиб может вызвать столкновение между неподвижными и вращающимися частями — часто каскадные удары. Оператор многих паровых турбин для коммунальных предприятий делится своим обширным практическим опытом в определении первопричин отказов, а также успешных решений.
Изгиб ротора, который приводит к преждевременному выходу из строя лопаток паровой турбины и других внутренних компонентов, является одной из наиболее серьезных проблем, возникающих при эксплуатации электростанций. Проблемы часто снижают эксплуатационную готовность завода из-за ограничения выработки и увеличения затрат на эксплуатацию и техническое обслуживание.Проблемы с экстремальным изгибом ротора часто связаны с взаимодействием между ротором турбины и неподвижными частями. Изгиб ротора может быть вызван множеством статических и динамических факторов, многие из которых будут рассмотрены в этой статье.
Начнем с механических факторов, связанных с ротором, самым большим вращающимся узлом в турбине. Далее, работая изнутри, мы рассмотрим проблемы с балансировкой ротора, за которыми следуют проблемы несоосности ротора и корпуса, а также проблемы, вызванные корпусом. Обсуждение основано на опыте авторов на шестиблочной электростанции Рамин мощностью 1890 МВт, расположенной в Ахвазе, Иран.Агрегаты введены в эксплуатацию с 1980 по 1985 год.
Избегайте трения ротора
Само собой разумеется, что трение лабиринтов или диафрагм, вызванное недостаточным зазором, нарушает торцевое уплотнение ротора. Эта ситуация обычно возникает, когда ротор с большой массой на рабочей скорости входит в контакт с неподвижной поверхностью, как правило, из-за слишком малого зазора между лабиринтными или мембранными сальниками и ротором. Во-вторых, может наблюдаться локальное повышение температуры в точке контакта, вызывающее повышение температуры металла в точке контакта из-за трения.
Силы, возникающие в результате удара большой вращающейся массы ротора с плохо функционирующими неподвижными уплотнениями, часто вдавливают слой металла на поверхность ротора. Трение может вызвать упругую деформацию ротора в месте удара и временный изгиб вала ротора. Изгиб вала обычно вызывает повышенный уровень вибрации (Рисунок 1).
1. При трении лезвия возникает изгиб. Трение уплотнения ротора высокого давления блока 300 МВт привело к изгибу этого ротора и истиранию кончика лопасти. Предоставлено: Ahwaz Power Generation Management Co. |
Неравномерное охлаждение ротора, особенно после останова, также приводит к контакту ротора с неподвижными частями. После отключения установки относительно высокотемпературный ротор может изгибаться исключительно из-за массы ротора и расстояния между опорами подшипников, если его оставить в неподвижном положении для охлаждения. Эта ситуация может привести к необратимому изгибу вала.
Эффект постоянного изгиба вала, вызванного неравномерным охлаждением, сразу же проявляется в виде сильной вибрации ротора при следующем запуске.Вибрация вызвана недостаточным зазором между неподвижными и вращающимися частями, а также валом, расположенным не по центру подшипника. Даже если изменение зазора невелико, ротор может сильно потирать, что приведет к его повреждению. И снова трение вызывает трение между неподвижными и вращающимися частями, локальный нагрев металла ротора в точке контакта и изгиб вала.
Кроме того, неравномерный нагрев вала, вызванный трением между вращающимися и неподвижными частями, может вызвать дальнейший изгиб вала в том же направлении, что и существующая дуга, и вызвать дополнительный контакт с неподвижными частями, увеличивая температуру и, следовательно, вызывая больший изгиб.Эффект каскадируется, если ему позволено продолжаться. Если позволить изгибу продолжаться, возможно, что предел текучести металла может быть превышен, что вызовет необратимую деформацию вала. Допустимый изгиб в турбинах на 3000 об / мин составляет до 0,02–0,03 мм в каждой секции. При токарной передаче предел составляет 0,05 мм.
Чтобы избежать изгиба ротора во время охлаждения, поставщики турбин предоставляют очень конкретные инструкции по допустимой скорости охлаждения. Например, турбина должна оставаться включенной, пока температура цилиндра высокого давления (ВД) не опустится ниже 150 ° C, а температура масла не опустится ниже 75 ° C.Производитель турбины также определяет скорость вращения поворотного механизма.
Предотвращение перекоса ротора и корпуса
Несоосность муфты между двумя валами или между валом и подшипником может вызвать изгиб в системе. Несоосность двух валов интегрированного ротора может вызвать эксцентриситет центра масс ротора, и этот эксцентриситет при высокой скорости вращения будет создавать центробежную силу в радиальном направлении, вызывая изгиб ротора.Несоосность оси вращения и оси вала также может вызвать изгиб ротора. Существует шесть основных факторов, которые могут вызвать смещение.
Одной из причин является плохое соединение между корпусом турбины и опорными подушками на фундаментной раме. Если колодка испытывает повышенное трение или перестает скользить во время теплового расширения (обычно во время запуска) в осевом направлении, результатом является опрокидывающий момент на обсадной колонне. Этот крутящий момент может вызвать смещение между корпусом и поверхностью подшипника, вызывая вибрацию в переднем конце турбины, деформацию опоры поверхности рамы фундамента и срыв подушки подшипника.
Также обратите особое внимание на фундаментную раму, включая болты, шпонки и подушки, чтобы было возможно свободное движение опорных поверхностей, особенно при запуске и изменении нагрузки. Степень продольного и поперечного теплового расширения центров отверстий цилиндров и хода колодок должны быть записаны для будущих сравнений. Этот процесс должен быть частью плановых проверок оборудования для технического обслуживания.
Еще один фактор — сложность сборки переднего подшипника турбины ВД.В то время как вал вращается в своем журнале подшипник, вал толкает масло из нижней части подшипника, в результате чего толщина масляной пленки к изменению. Когда это происходит, центральная линия вала перемещается вверх и в одну сторону. Для учета этого движения вала, сегментированный подшипник должен автоматически регулировать и контактная поверхность подшипника журнала будет оставаться в хорошем состоянии. Если поверхность контакта слишком велика, трение на поверхности подшипника будет увеличиваться, вызывая повышенное трение и коррозию поверхности подшипника, а также увеличивая вибрацию и эксцентриситет ротора.Результатом будет утечка масла из подшипников и трение уплотнительных сальников. С другой стороны, если площадь контакта подшипника уменьшается, масляная пленка вызовет неравномерное движение ротора внутри сегментированного подшипника, и масляная пленка не образуется, что также приведет к увеличению вибрации (Рисунок 2).
2. Вал должен оставаться в центре. Смещение центра вала в сегментированном подшипнике во время вращения может вызвать вибрацию. Предоставлено: Ahwaz Power Generation Management Co. |
Не упускайте из виду соосность ротора с отверстиями и муфтами. Правильная центровка ротора теряется, когда ось одного ротора не непрерывна с ротором в следующем корпусе, в паровых турбинах с несколькими корпусами. Индивидуально подключенные трансмиссии должны работать как одна длинная непрерывная, но гибкая трансмиссия. После капитального ремонта паровой турбины важно подтвердить центровку ротора относительно муфт, а также любые другие факторы, которые могут вызвать изменение первичного положения отдельных корпусов, подшипников и роторов.Если во время технического обслуживания наблюдается истирание торца или промежуточного уплотнения ротора или эксцентриситет муфт, необходимо отрегулировать трансмиссию, чтобы избежать сильной вибрации турбины, контакта и трения сальников или лабиринтных уплотнений и т. Д. (Рисунок 3) .
3. Правильно выровняйте диафрагмы. Мембраны должны быть тщательно выровнены по осевой линии вала внутри корпуса этой турбины мощностью 315 МВт, чтобы избежать контакта с лопастями ротора. Предоставлено: Ahwaz Power Generation Management Co. |
Помните, что ось от центра отверстия сальника должна совпадать с осью ротора турбины при нормальных температурах, возникающих во время работы турбины. Кроме того, очень важно быстро идентифицировать любые потери в уплотнительных зазорах во время прогрева паровой турбины. Во время нагрева могут возникнуть изменения зазора, которые могут вызвать изгиб цилиндров из-за разницы температур между верхней и нижней секциями цилиндра (Рисунок 4).
4. Требуется точное выравнивание. На этой фотографии показан расширительный ключ верхней половины цилиндра низкого давления. Предоставлено: Ahwaz Power Generation Management Co. |
Наконец, обратите особое внимание на возможность контактного трения кончиков лопастей о стенки цилиндра на реактивных стадиях. Трение может вызвать повышенную вибрацию изгиба лезвия, обычно у основания лезвия (Рисунок 5).
5. Избегайте трений, вызванных выдавливанием шипов. Это пример экструзии шипа в лопастях ротора высокого давления. Предоставлено: Ahwaz Power Generation Management Co. |
Дисбаланс ротора увеличивает вибрацию
Кривизна вала также смещает ось вращения вала, перемещая центр масс ротора, создавая вибрацию. Эта вибрация влияет на лезвия тремя значительными способами.
Во-первых, вибрация вызывает проблемы с конструкцией лезвия. Центробежные силы, возникающие во время работы, значительны, вызывая увеличение растягивающих усилий в поперечном сечении лопасти и, если центр масс не находится на радиальной линии, также возникают напряжения изгиба. Кроме того, изгибающие напряжения создаются в соединениях лопаток под действием давления пара высокого давления, протекающего в осевом направлении через цилиндр турбины. Величина этих напряжений зависит от расхода пара, перепада температуры на ступени лопастей, скорости вращения лопастей и веса лопасти.Температура пара, перегретого на первой ступени и насыщенного на конечных ступенях, будет влиять на механические свойства и коррозию материалов лопаток (рис. 6).
6. Коррозия вызывает дисбаланс. Отказ этой ступени управления ротором высокого давления был вызван неравномерным распределением пара из-за коррозии. Предоставлено: Ahwaz Power Generation Management Co. |
Во-вторых, вибрация лопасти может быть вызвана внешними средствами, такими как неудовлетворительная динамическая балансировка ротора, несоответствие проходов диафрагмы, отклонение шага лопастей, неправильно смонтированное соединение между двумя полумембранами или коррозия вечный край неподвижных лезвий.
В-третьих, размеры поворотных лопастей и способ их установки на роторы могут быть разными. После капитального ремонта необходимо тщательно поддерживать одинаковый вес и материалы всех ножей, особенно когда заменяется только несколько ножей. Даже небольшое изменение веса лопасти или центра тяжести может вызвать дисбаланс и вибрацию ротора (Рисунок 7).
7. Неисправности могут быть вызваны плохим обслуживанием. Диск снят с ротора неправильно, в результате на валу появились глубокие царапины.Ремонт потребует переделки и повторной балансировки вала, чтобы предотвратить дисбаланс, который может вызвать вибрацию. Предоставлено: Ahwaz Power Generation Management Co. |
8. Пар может отводить болты. Большие болты, вставленные в отверстия, используются для плотного закрепления большого горизонтального соединительного фланца в этом цилиндре высокого давления. Отверстия под болты — это места, где может образоваться утечка паровой струи из-за деформации цилиндра и изменения давления в воздуховоде. Предоставлено: Ahwaz Power Generation Management Co. |
Корпус также является важным фактором вибрации ротора
Колебания температуры корпуса могут вызывать вибрацию паровой турбины разными способами. Проблемы с обсадной колонной могут вызывать перекосы по разным причинам, в основном связанные с расширением и сжатием из-за колебаний температуры.
Во-первых, цилиндр турбины может иметь температурное расслоение, вызванное недостаточной теплоизоляцией от корпуса и / или слабой изоляцией в других областях.Нарушение теплоизоляции может быть вызвано плохой изоляцией в местах соединений между соединениями и трубами с кожухом, обычно в нижней части турбины. Плохая изоляция корпуса в нижней части, например, может вызвать температурный градиент сверху вниз корпуса, что может привести к деформации корпуса и упругому изгибу ротора. Поставщик определяет допустимый градиент температуры обсадной колонны. По нашему опыту, градиент не должен превышать 60 ° C. Новые турбины высокого давления особенно чувствительны к градиентам температуры корпуса.
Далее, если турбина запускается из горячего состояния до того, как она вернется в пределы кривизны, вращающиеся лопасти и неподвижные диафрагмы могут протираться и вызывать повреждение уплотнений и сальников диафрагмы. По мере увеличения веса вала увеличиваются размеры ротора турбины, цилиндра турбины и тепловая инерция вала. Эффект состоит в том, что между запусками (и при повороте механизма) требуется более длительный период времени, поэтому любая кривизна ротора устраняется перед следующим запуском.
Изгиб цилиндра можно оценить, зная его размеры и материалы, из которых он изготовлен.Изгиб цилиндра (мм) можно найти по выражению α Δt L 2 / 8D, где Δt — разница температур между верхом и низом цилиндра (C), L — длина цилиндра (мм), D — внешний диаметр оболочки, усредненный по ее длине (м), а α — коэффициент линейного теплового расширения, обычно около 13,6 мм / мм-С, или любой другой согласованный набор единиц. Величина допустимого изгиба цилиндра определяется минимальным допуском между диафрагмой и концевыми сальниками.Например, если размеры цилиндра высокого давления составляют l = 3620 мм и D = 1840 мм, а максимальный допуск сальника диафрагмы составляет 0,6 мм, допустимая разница температур от верха до низа цилиндра составляет 50 ° C.
Также можно определить влияние теплового изгиба ротора на корпус. Когда верхняя часть кожуха более горячая, чем нижняя, кожух имеет тенденцию изгибаться вниз. Если температурный градиент постоянен от верха обсадной колонны к низу и по ее длине, то максимальное напряжение изгиба возникает в середине обсадной колонны по вертикали и между опорами обсадной колонны по горизонтали.Изгиб или прогиб в этих условиях можно определить как α Δt (LZ — Z 2 ) x 10 3 / 2D, где L — длина обсадной колонны между опорами (м), Z — расстояние от передней опоры обсадной колонны до интересующее местоположение (m), а другие переменные остаются такими, как определено выше. Предполагая, что используется средняя точка длины обсадной колонны, L / 2 может заменить Z, чтобы найти максимальное отклонение.
Температурный градиент по лопастям и диафрагмам также необходимо учитывать во время горячего пуска.При запуске горячей турбины, если пар относительно холодный, температура металла диафрагмы и лопатки будет ниже, чем у ротора. В этом случае диаметр отверстий диафрагмы будет увеличиваться быстрее, чем диаметр ротора, вызывая радиальный люфт и уменьшая зазоры между лопатками и диафрагмой. Используя типичный коэффициент линейного теплового расширения, диаметр уплотнения диафрагмы 500 мм будет увеличиваться на 0,3 мм на каждые 100 ° C разницы температур между ротором и диафрагмой.
Таким образом, если ротор имеет более высокую кривизну, чем нормальный диапазон, и если регулирование пути потока пара не было выполнено тщательно во время горячего запуска, следует ожидать трения.
Расчеты с использованием этих формул и опыт применения говорят нам, что разница температур между верхней и нижней частью цилиндра высокого давления не должна превышать определенный нормальный предел во время запуска паровой турбины. Если этот предел разницы температур превышен, радиальные расстояния в сальнике переднего конца значительно уменьшатся, вызывая трение с последующим изгибом ротора возле ступени управления.
Опыт многих компаний по ремонту паровых турбин показывает, что причиной изгиба цилиндра высокого давления является конденсация пара внутри горячего цилиндра турбины при остановке. Высокотемпературная теплопередача для испарения этого конденсата охлаждает нижнюю часть цилиндра, в то время как верхняя часть цилиндра остается относительно горячей. В результате цилиндр изгибается вниз, а верх корпуса в большинстве случаев остается прямым.
Кроме того, недостаточные зазоры в рамах цилиндров низкого (LP) и промежуточного (IP) давления в многоцилиндровых турбинах могут возникать при неправильной установке распорных болтов и шайб.Дистанционные болты используются для крепления рам корпуса LP и IP к фундаменту. Во время работы и при номинальной нагрузке, если давление конденсатора (вакуум) и температура конденсата находятся в пределах нормального диапазона, то зазор должен быть таким, как это предусмотрено. Но если давление в конденсаторе (вакуум) ненормальное, а температура конденсата высокая, то баллон низкого давления нагревается выше допустимого предела, вызывая большее расширение объема в конденсаторе. В результате зазор между болтами уменьшается или становится равным нулю.Если проектные зазоры не соблюдаются, вибрация турбины может увеличиться, и ее нагрузку необходимо уменьшить.
Затем не забудьте о болтах, шпильках и других соединениях корпуса. Кожухи для турбин высокого давления имеют толстые стенки, а также большие фланцы с горизонтальным соединением, для которых требуются болты и шпильки. Бывают случаи, когда нагрузки турбины быстро меняются или фланец корпуса и стенки нагреваются неравномерно во время пуска или останова агрегата. Разница температур между верхом и низом кожухов высокого и низкого давления (обычно от 50 ° C до 70 ° C) и фланцевых штифтов (максимум от 15 ° C до 25 ° C) может вызвать утечку пара через горизонтальное соединение корпуса.
Наконец, нескомпенсированное движение паропроводов, соединенных с обсадной колонной, может вызвать смещения обсадной колонны и вибрацию ротора. Это особенно актуально для труб большого диаметра с толстыми стенками. Когда турбина работает, ротор совершает осевое движение, как и корпус турбины. Тепловое расширение системы учтено в конструкции турбины. Силы и моменты, которые эти большие трубы прилагают к корпусу, также учитываются при проектировании турбины. Чрезмерные нагрузки на соединение труб могут вызвать деформацию корпуса, а изгибающие моменты, приложенные к фланцам корпуса, также могут вызвать смещение и перемещение цилиндра внутри корпуса, что может увеличить вибрацию ротора.
— Фаршад Шаморади (fshamoradi@yahoo.com) — менеджер инструментального отдела, Насер Мохаммади — менеджер инженерного отдела и Махди Хейдари Какеш — менеджер по общему техническому обслуживанию в Ramin Power Завод, Ahwaz Power Generation Management Co.
Конденсатор (паровая турбина) | Проектирование
Конденсатор здесь означает кожухотрубный теплообменник, установленный на выходе каждой паровой турбины на тепловых электростанциях коммунальных предприятий.Эти конденсаторы представляют собой теплообменники, которые переводят пар из газообразного в жидкое состояние, также известное как фазовый переход. При этом скрытая теплота пара отводится внутри конденсатора.
Цель состоит в том, чтобы конденсировать выходящий (или выхлопной) пар из паровой турбины для достижения максимальной эффективности, а также для получения конденсированного пара в форме чистой воды, иначе известной как конденсат (конденсат — не путать с использованием слово конденсат в конденсате природного газа в нефтяной промышленности), обратно в парогенератор или (котел) в качестве питательной воды для котлов.
Сама паровая турбина представляет собой устройство для преобразования тепла пара в механическую энергию. Разница между теплотой пара на единицу веса на входе в турбину и теплотой пара на единицу веса на выходе из турбины представляет собой выделяемое тепло (или падение тепла) в паровой турбине, которое преобразуется в механическую мощность. Падение тепла на единицу веса пара также измеряется словом «падение энтальпии». Следовательно, чем больше тепла на фунт (или кг) пара преобразуется в механическую мощность в турбине, тем лучше ее рабочие характеристики или, иначе говоря, КПД.За счет конденсации выхлопного пара турбины давление выхлопных газов понижается ниже атмосферного по сравнению с давлением выше атмосферного, увеличивая перепад давления пара между входом и выходом паровой турбины. Это дальнейшее снижение давления выхлопных газов дает больше тепла на единицу веса пара, подаваемого в паровую турбину, для преобразования в механическую мощность. Большая часть тепла, выделяемого за счет конденсации, т. Е. Скрытой теплоты пара, уносится циркулирующей водой внутри трубок.
На соседнем чертеже показана типичная конструкция конденсатора мощностью около 200 МВт, и он описан здесь. Описание предназначено для двухкомпонентного и однопроходного конденсатора. Возможны вариации в конструкции изготовления в зависимости от производителей, размера паротурбинной установки, а также некоторых требований, продиктованных условиями площадки.
Оболочка[править | править источник]
Кожух — это самый внешний корпус конденсатора, обеспечивающий возможность установки трубок.Корпус изготовлен из довольно толстых пластин из углеродистой стали. Из-за большого размера оболочка достаточно усилена или усилена изнутри пластинами из углеродистой стали, чтобы обеспечить достаточную жесткость самой оболочки. Кожух также поддерживает ряд промежуточных опорных пластин для длинных трубок в зависимости от размера конденсатора. Эти промежуточные опорные пластины для труб также помогают избежать провисания труб большой длины. Эти опорные пластины имеют достаточное количество отверстий подходящего диаметра, просверленных с помощью зажимного приспособления в подходящем сверлильном станке, чтобы облегчить простую нарезку резьбы в каждой трубе во время установки или во время замены.В то же время промежуточные опорные пластины для труб обеспечивают свободное перемещение труб во всех направлениях, особенно в продольном направлении, из-за расширения и сжатия, возникающих во время работы.
Кожух соединяется с выпускным отверстием (выхлопом) паровой турбины с помощью компенсатора, выполненного, как правило, из нержавеющей стали, с фланцами на обоих концах. Весь конденсатор поддерживается тяжелыми пружинами, установленными на стальных опорных плитах в подходящих местах на бетонном основании, обычно с небольшим наклоном к выпускному водяному баку, чтобы способствовать полному дренажу водяного бака.Внизу кожуха, где конденсат может собираться, предусмотрен отстойник. Этот поддон является общим для обеих половин, но разделен перегородкой посередине до высоты нижнего ряда труб. Это необходимо для облегчения измерения проводимости конденсата с обеих сторон независимо. Это необходимо для определения загрязнения конденсата и с какой его половины.
На каждой стороне отстойника предусмотрено соединение трубы с фланцем для подключения к внешнему насосу для непрерывного удаления конденсата при нормальной работе.Эта небольшая труба также снабжена компенсатором на стороне отстойника, чтобы избежать движения конденсатора от жестко установленных насосов.
Внутри кожуха и снаружи трубок в целом сохраняется вакуум при нормальных условиях эксплуатации. Внутри трубок проходит охлаждающая или циркулирующая вода.
Воздушная зона [править | править источник]
Внутри корпуса центральная или боковая часть в продольном направлении разделена внешним экраном, за исключением нижней части.Эта перегородка называется воздушной зоной. Эта воздушная зона присутствует во всех конденсаторах независимо от производителя и размера. Все газы, выделяющиеся в конденсаторе из-за охлаждения, выводятся через эти трубки воздушной зоны.
Из подходящей части этой воздушной зоны внутри кожуха вынимается воздуховыпускная труба и выводится из кожуха для подсоединения к устройству вытяжки воздуха.
Трубные листы [править | править источник]
На каждом конце кожуха предусмотрена трубная решетка достаточной толщины, обычно сделанная из мунц-металла, с отверстиями для вставки и прокатки труб.Однако на впускном конце каждая трубка также имеет раструб для обтекаемого входа воды. Это сделано для того, чтобы избежать завихрений на входе в каждую трубку, вызывающих эрозию. Некоторые производители также рекомендуют пластиковые вставки на входе в трубки, чтобы избежать эрозии входного конца водоворотами. В небольших установках некоторые производители используют манжеты для уплотнения концов трубок вместо катания. Для обеспечения продольного расширения труб в некоторых конструкциях между кожухом и трубной решеткой имеется компенсатор, позволяющий последней перемещаться в продольном направлении.В небольших установках трубам придается некоторый прогиб, чтобы компенсировать расширение труб, при этом водяные камеры обоих концов жестко прикреплены к кожуху.
Ящики для воды [править | править источник]
Трубная решетка на каждом конце с закрученными концами труб для каждой половины конденсатора заключена в сборную коробку, известную как водяная камера, с фланцевым соединением с трубной решеткой. Крышка водяного бака имеет как минимум два человека на откидных крышках.
Эти водяные камеры на впускной стороне также будут иметь фланцевые соединения большого размера для впуска охлаждающей воды на нижнем уровне для дроссельных заслонок, небольшую вентиляционную трубу с ручным клапаном для выпуска воздуха на более высоком уровне и ручной сливной клапан внизу для слива воды. ящик для обслуживания.Точно так же на выпускной водяной камере соединение охлаждающей воды будет иметь большие фланцы, но на более высоком уровне для дисковых затворов, выпускное соединение также на более высоком уровне, а сливное соединение на более низком уровне. Аналогично расположены карманы для термометров на впускном и выпускном патрубках для локальных измерений температуры охлаждающей воды.
В небольших установках мощностью около 5 кВт некоторые производители изготавливают кожух конденсатора, а также водяные камеры из чугуна.
Обычно трубы изготавливаются из латуни, алюминиевой латуни, медно-никелевого сплава или титана в зависимости от требований к надежности в рабочих условиях.Длины фиксированы на уровне около 20 футов, в зависимости от размера конденсатора, который основан на возможности транспортировки с завода-изготовителя и возможности монтажа на месте. Наружный диаметр ограничен максимум одним дюймом для простоты использования и простоты вставки через отверстия в кожухе и прокатки с обоих концов.
Почему возникает коррозия? [Править | править источник]
Трубки, трубные решетки и водяные камеры изготовлены из материалов разного состава. Эти материалы всегда контактируют с циркулирующей водой.Циркуляционная вода, в зависимости от ее химического состава, будет действовать как электролит между трубками и водяными камерами. Это вызовет электролитическую коррозию, которая в первую очередь начнется с анодных материалов. Трубки конденсатора, являющиеся самыми низкими в серии из анодных материалов, будут произведены в первую очередь. Это приводит к тому, что концы трубки конденсатора съедаются первыми.
Конденсаторы на основе морской воды, особенно когда морская вода содержит химические загрязнители, имеют наихудшие коррозионные характеристики.Речная вода, содержащая загрязняющие вещества, также нежелательна для охлаждающей воды конденсатора.
Однако из-за того, что для больших конденсаторов требуется большой расход воды, необходимо допускать коррозионное воздействие морской или речной воды, и на практике следует применять соответствующие методы.
Концентрация нерастворенных газов над трубками воздушной зоны высокая. Поэтому эти трубы подвержены более высокой скорости коррозии. Иногда эти трубы подвергаются коррозионному растрескиванию под напряжением, если изначально напряжение не снимается полностью во время производства.Чтобы преодолеть эти эффекты коррозии, некоторые производители предлагают в этой области трубы с более высокой коррозионной стойкостью.
Эффекты коррозии [править | править источник]
Поскольку концы трубок корродируют, существует вероятность утечки охлаждающей воды на сторону пара, загрязняющей сконденсированный пар или конденсат, что вредно для парогенераторов. Другие части водяных камер также могут быть повреждены в долгосрочной перспективе, что потребует ремонта или замены, включая длительные остановки.
Защита от коррозии [править | править источник]
Катодная защита используется для решения этой проблемы. Расходные аноды из цинковых пластин (самые дешевые) устанавливаются в подходящих местах внутри водяных камер. Эти цинковые пластины будут корродированы первыми, находясь в самом низком диапазоне анодов. Следовательно, эти цинковые аноды требуют периодической проверки и замены. Это требует сравнительно меньшего времени простоя. Водяные ящики из стальных пластин также защищены внутри эпоксидной краской.
РУКОВОДСТВО ДЛЯ ИНЖЕНЕРОВ-МЕХАНИКОВ КЕНТА. Дизайн. Магазинная практика. ОДИННАДЦАТОЕ ИЗДАНИЕ, СЕРИЯ СПРАВОЧНИКОВ WILEY ENGINEERING, НЬЮ-ЙОРК: JOHN WILEY & SONS, INC. ЛОНДОН: CHAPMAN & HALL, LIMITED.
Модернизация паровой турбины: Низко висящие плоды
В 1500 году Леонардо да Винчи нарисовал эскизы устройства, которое вращалось, когда горячий воздух, поднимающийся по дымоходу, проходил через набор лопастей, похожих на вееры. Леонардо назвал свое изобретение «домкратом для дымохода», и, хотя оно превратило всего лишь вертел для жарки, оно породило идею установки лопастей на вал для преобразования тепловой энергии в механическую.Усовершенствования концепции сэром Чарльзом Парсонсом привели к получению патента на первую многоступенчатую реактивную турбину в 1884 году и прототипа мощностью 4 кВт в следующем году. Спустя столетие технология была усовершенствована до такой степени, что эффективность современных сверхсверхкритических заводов приблизилась к магическому 50% -ному барьеру.
В США рыночные силы побудили некоторых владельцев заводов продолжать эксплуатировать агрегаты, показатели тепла которых считаются посредственными. Лучшие в своем классе паровые электростанции, которым уже 50 лет и которые при вводе в эксплуатацию обеспечивали тепловую мощность в диапазоне 9000 БТЕ / кВт · ч, сегодня продолжают работать с аналогичной эффективностью для удовлетворения краткосрочных потребностей.Ключевым моментом, конечно же, является то, что стоимость эксплуатации завода растет с возрастом и становится менее надежной (рис. 1).
1. Старшие моменты. Номинальная частота вынужденных отключений типичной паровой электростанции со временем будет увеличиваться. Источник: журнал POWER
.Поддержание любого завода в рабочем состоянии и прибыльности требует постоянных инвестиций. Не обязательный вид — например, установка или модернизация систем контроля выбросов для соответствия более строгим стандартам, — а дискреционные инвестиции. Разумно вкладывать средства только в те области, где окупаемость инвестиций будет наибольшей, например, в модернизацию рабочей лошадки завода, его паровой турбины (рис. 2).Деньги значительны: повышение тепловой мощности базовой угольной электростанции мощностью 500 МВт на 100 БТЕ / кВтч могло бы сэкономить до 10 миллионов долларов в год только на расходах на топливо.
2. На полукорпусе. Компания Dairyland полностью заменила всю турбину высокого / среднего давления на своей станции J.P. Madgett, чтобы улучшить производительность и надежность установки. Предоставлено: Энергетический кооператив Dairyland, станция Джона П. Мэджетта
Вперед. . . мышление
Dairyland Power Cooperative (DPC) и Siemens Power Generation (Орландо, Флорида.) недавно завершила модернизацию паровых трактов высокого давления (HP), среднего давления (IP) и низкого давления (LP) блока 1 станции JP Madgett в Dairyland в Алме, штат Висконсин. Станция Madgett работает на угле. докритическая паровая установка, введенная в эксплуатацию в 1979 году, с номинальной мощностью 365 МВт. Вывести подразделение на пенсию было нельзя, потому что специалисты по планированию ресурсов ЦОД понимали, что им нужны его мощности сейчас и еще на 30 лет. Модернизация паровой турбины была единственно возможной стратегией. DPC инициировал проект модернизации, преследуя три важные цели: повысить эффективность установки во всем диапазоне нагрузок, увеличить мощность агрегата и продлить период технического обслуживания турбины до 10 лет.
Компания «Сименс» предоставила пакет модернизации, который включал новые роторы, внутренние кожухи и высокоэффективные лопатки ротора и статора, а также услуги по проектированию и установке. Осенью 2004 года было запланировано отключение на 50 дней для завершения работ по модернизации параллельно с капитальным ремонтом котла, модернизации системы управления до современной распределенной системы управления и замены главного трансформатора для обеспечения ожидаемой более высокой выходной мощности.
Пакет модернизации турбины HP / IPBB44FA (полная дуга) компании Siemens предназначен для существующего парка турбин Westinghouse Building Block (BB) 44 с давлением на входе до 2400 фунтов на кв. Дюйм и температурой на входе 1000F.Турбины BB44 имеют мощность от 350 МВт до 680 МВт. Используя этот пакет, инженеры могут добавить полную дугу к впускной впускной секции, исключить поворот пара на 180 градусов на траектории лопастей высокого давления, исключить ступень импульсного управления, добавить полностью интегрированный внутренний кожух и улучшить паронепроницаемость (рис. ).
Все внутренние стационарные компоненты были помещены в единый, полностью интегрированный корпус — конструкция, которая сводит к минимуму количество деталей и сокращает время установки и продолжительность отключений в будущем.Конструкция BB44FA дублирует профиль ответных фланцев существующих агрегатов, что позволяет повторно использовать внешний кожух и все точки крепления. Это иллюстрирует философию проектирования Siemens для пакета модернизации: сделать его полностью «подключи и работай».
Конструкция ротора HP / IP включает полностью цельную конструкцию без отверстия для поковки, что сокращает время запуска и увеличивает усталостную долговечность. Подобно внешнему корпусу и точкам крепления, подшипники можно использовать повторно, поскольку новый ротор соответствует весу старого, что снижает затраты и время установки.Конструкции лопастей со встроенными кожухами были выбраны для оптимизации термодинамических характеристик. Конструкция кожуха имеет два преимущества: кожух создает периферийную границу для парового тракта, позволяя модернизировать более эффективные уплотнения, и обеспечивает отдельные опоры для наконечников лопастей между соседними лопастями. Конструкция лопаток высокого и низкого давления первой ступени снижает температуру на входе в ротор, обеспечивая при этом благоприятные условия потока на выходе.
Старая пятиступенчатая турбина низкого давления блока 1была заменена новой семиступенчатой конструкцией, в которой отсутствуют заклепанные кожухи на передних лопастях и заклепанные кожухи и крепежные тросы на более крупных лопастях низкого давления (рис. 3).В комплект дооснащения входит единый внутренний кожух с функциями отвода влаги. Турбина низкого давления была спроектирована как «вставляемая» замена, позволяющая повторно использовать многие точки соединения внутреннего и внешнего цилиндра. Другие особенности пакета включают в себя моноблочную поковку ротора без сквозного канала, реактивные передние лопасти со встроенными кожухами, 37,7-дюймовые отдельно стоящие лопасти последнего ряда и единый внутренний кожух с улучшенным выпускным диффузором.
3. Новая аренда на жизнь. В замененной турбине низкого давления Siemens Power Generation используется улучшенная конструкция лопаток и увеличенная площадь кольцевого зазора для повышения производительности.Предоставлено: Энергетический кооператив Dairyland, станция Джона П. Мэджетта
Модернизированная турбина была успешно установлена во время планового 50-дневного простоя станции Дж. П. Мэджетт. Результаты испытаний были исключительными: КПД турбины высокого давления увеличился на 8–10% в диапазоне нагрузок, а КПД секции ПД увеличился на 2–4%. Общая мощность станции увеличилась с 20 до 27 МВт. Большая часть измеренного прироста производительности от 7 до 8 МВт в секции низкого давления была приписана улучшенной конструкции лопастей переднего конца, увеличению площади кольцевого пространства на 25% и повышению эффективности последних трех ступеней секции низкого давления.
Покажите мне улучшения
Завод LabadieAmerenUE, расположенный в 35 милях к западу от Сент-Луиса, был признан Агентством по охране окружающей среды США и штата Миссури за его исключительные экологические характеристики. Но руководство станции также хорошо известно своим стремлением постоянно улучшать производственную статистику четырех угольных блоков Labadie мощностью 600 МВт (номинальная).
За последние несколько лет персонал станции — с помощью Alstom Power (Виндзор, Коннектикут) — увеличил максимальную единицу мощности не менее чем на 10% (с 580 МВт до 630 МВт), одновременно увеличивая свою готовность (POWER, июль). / Август 2003 г., стр.58–61). Помимо усовершенствований котла, вызванных его переходом на уголь бассейна Паудер-Ривер (PRB) в конце 1990-х годов, на заводе в Лабади были также установлены горелки с низким уровнем выбросов NOx, воздушная система перегрева и передовые компьютерные средства управления для повышения производительности агрегата и значительного сокращения выбросов.
Одно из самых значительных достижений Labadie в производительности произошло за счет модернизации всех четырех паровых турбин. Четыре агрегата были спроектированы в конце 1960-х годов и начали коммерческую эксплуатацию в период с 1971 по 1974 год.Westinghouse поставила турбогенераторы конструкции BB44 для блоков 1 и 2; Компания General Electric разработала проект G-2 для блоков 3 и 4. Каждый турбогенератор представляет собой тандемно-составную установку с двумя двухпоточными секциями низкого давления. Программа модернизации рассчитана на несколько лет; турбины HP / IP на установках Westinghouse были заменены в 2002 году, а новые турбины HP / IP и LP для агрегатов GE были введены годом позже.
Рекорды производительности HP / IP блоков 1 и 2 за первые 30 лет службы были неутешительными.Интервалы между капитальным обслуживанием оставались стабильными и составляли около четырех лет, эффективность агрегатов продолжала снижаться, время ввода в эксплуатацию продолжало расти, а количество и серьезность эксплуатационных проблем росли. Эффективность турбины повысится после капитального ремонта, но никогда не вернется к проектному уровню и быстро ухудшится между капитальными ремонтами. Внутренние проблемы турбины, такие как сколы на сопловом блоке и деградация парового уплотнения, оказалось трудно исправить навсегда. Другие механические проблемы включали неравномерное проскальзывание роторов, вызывающее их прогиб и дальнейшее увеличение времени запуска и интервалов простоя.Конечный результат — меньшее количество проданных мегаватт-часов — диктовал не что иное, как замену турбин HP / IP на обоих блоках.
ВАмеренУЭ было принято решение заменить турбины в виде модулей новыми установками с низкореагирующими (импульсными) лопатками и полным подводом дуги. Это стоило дороже, но давало инженерам больше свободы для максимизации производительности, не ограниченной существующим внешним кожухом агрегатов (хотя внешний кожух также был заменен во время модернизации, чтобы устранить другие проблемы с обслуживанием). Модульный подход также упростил расстановку сцен.Поскольку впускные отверстия новых секций ВД / ВД находятся в центре турбины (наряду с однопоточными расширениями ВД и ВД), большой балансировочный поршень больше не требуется для компенсации осевого усилия, которое давала старая турбина реактивной конструкции. используется для производства. Удаление поршня уменьшило количество внутренних путей утечки с пяти до одного.
Дальнейшее улучшение рабочих характеристик стало результатом пересмотренного устройства парового уплотнения, которое более чем значительно снижает утечку. Он также использует холодный пар вторичного нагрева, а не основной пар, для герметизации турбины.Благоприятный эффект «просачивания» распространяется на уменьшение перетекания пара сальника и снижение тепловой нагрузки конденсатора.
Обе модификации турбины дали желаемые результаты. На энергоблоках 1 и 2 (где были заменены только турбины ВД / ВД) КПД высокого давления увеличился на 7%, а КПД низкого давления — на 5%. Общее увеличение мощности каждого блока было продемонстрировано на 27 МВт только за счет повышения эффективности.
Вышеупомянутые проблемы с эксплуатацией и техобслуживанием также вынудили Ameren произвести оптовую замену турбин энергоблоков 3 и 4.В этом случае цели заключались в повышении эффективности установки и производительности установки, а также в увеличении интервалов технического обслуживания турбины (Рисунок 4). Тандемно-составная турбина ВД / ПД была заменена турбиной аналогичной конструкции с низкой реакцией (Рисунки 5 и 6). В замене внешнего кожуха не было необходимости, что позволило сэкономить капитальные затраты и сократить необходимость в ремонте трубопроводов и изоляции.
4. Вид с высоты птичьего полета. Узел 3 Лабади для чистовой обработки ротора турбины высокого и среднего давления. Предоставлено: AmerenUE
.5.Вы звоните. Сравните новые и старые турбины высокого давления (ВД) на блоках 3 и 4 Лабади. В старой секции HP (слева) на две строки меньше, чем в новой (справа). Тестирование показало, что новый дизайн на 7% эффективнее. Предоставлено: AmerenUE
.6. Что бы вы хотели? Слева — старая конструкция лопатки / кожуха турбины среднего давления блоков 3 и 4. Справа — современная конструкция. Предоставлено: AmerenUE
.Две двухпоточные турбины низкого давления с 30-дюймовыми лопастями L-0 были заменены, поскольку коррозионное растрескивание под напряжением в области «ласточкин хвост» колеса L-1 ускорилось достаточно, чтобы потребовать капитального ремонта или замены лопаток.Проведя подсчеты, Ameren выбрала вариант замены, который повлек за собой использование современных 34-дюймовых лопастей L-0 и меньшего пути лопастей (рис. 7). Это увеличило единицу мощности на 10 из 14 МВт.
Возможно, самым важным уроком, извлеченным Амереном, стала необходимость рассматривать проекты модернизации целостно и координировать их выполнение с другими запланированными изменениями на заводе. Внутри подразделения любое изменение, внесенное в любую систему, почти всегда приводит к изменениям в другом месте. Например, установка нового экономайзера и подогревателя воздуха снижает перепад давления в газовом тракте, уменьшая уровень необходимой мощности вентилятора.В Labadie это сэкономило от 3 до 6 МВт и дало дополнительное преимущество: улучшенные характеристики электрофильтра за счет более низкой температуры газа на входе. Аналогичным образом, модификация разделительных панелей перегревателя устранила ряд ограничений по потоку газа и отказов труб из-за усталости, что позволило операторам увеличить максимальную мощность агрегата еще на 12 МВт. Инженеры АмеренУЭ позаботились о том, чтобы у новой паровой турбины был запас, чтобы воспользоваться преимуществами других улучшений производительности завода.
7. Почти закончено. Удлинение лопаток турбины низкого давления 3-го блока с 30 до 34 дюймов увеличило КПД секции низкого давления на 5%. Предоставлено: AmerenUE
.Excelsior ever upward вместимостью
Проект, аналогичный модернизации завода в Лабади, был недавно завершен на четырехблочной электростанции Northport мощностью 1520 МВт на Лонг-Айленде. В Нортпорте есть паровые турбины производства General Electric 1960-х и 1970-х годов. Осенью 2004 года настала очередь 3-го энергоблока мощностью 375 МВт.Основной проблемой надежности турбины блока 3 была утечка внутреннего уплотнения, которая снижала пиковую мощность блока и увеличивала его тепловую мощность.
KeySpan обычно регулярно тестирует свои устройства и ремонтирует их примерно каждые семь лет. Блок 3 Northport не подвергался ремонту с 1997 года. До планового капитального ремонта турбины в 2004 году блок 3 не работал должным образом. Например, испытания показали, что в 2003 и начале 2004 года нагрузка на блок была ограничена его питающим насосом основного котла мощностью 15 МВт.Температура основного пара также была ограничена увеличением температуры горячего повторного нагрева и постоянным падением давления первой ступени с момента последнего капитального ремонта агрегата. Из-за этих и многих других проблем скорректированная нагрузка энергоблока 3 упала на 20–30 МВт ниже ожиданий. Все признаки указывают на повышенную утечку HP / IP недопустимого уровня.
Когда в 2004 году начался капитальный ремонт, операторы отметили, что две горизонтальные шарнирные шпильки с правой стороны внутреннего кожуха HP были полностью ослаблены, когда кожух был снят.Обе шайбы были разрезаны и сняты без снятия гаек. Проверка контакта внутреннего полусоединения обечайки в средней зоне пролета высокого и низкого давления выявила значительный путь утечки. GE подтвердила и оценила утечку на уровне более 18 000 фунтов / час, снижая мощность на 470 кВт и тепловую мощность на 7,9 БТЕ / кВтч.
Предпроектные оценки обещали рекуперацию 4 МВт и снижение расхода тепла на 257 БТЕ / кВтч за счет повышения эффективности ступени турбины и снижения утечки от ВД до ВД с 11% до 4% потока пара. Первым шагом была отправка корпуса турбины для обработки стыковочного узла на 0.031 дюйм, чтобы придать плоскостность дизайну.
Пакет оптимизации парового уплотнения, выбранный KeySpan, был получен от TurboCare Inc. (Чикопи, Массачусетс). В нем были стандартные лабиринтные упаковочные кольца, выдвижные уплотнительные кольца, щеточные уплотнения, а также обычные уплотнения с лопастями и наконечниками щеток — все размеры соответствовали турбине блока 3. Трение уплотнения не является редкостью в паровых турбинах, и особенно часто встречается в конструкциях HP / IP с одним корпусом, в которых используется сальниковая коробка для герметизации потока между секциями HP и IP.
Относительно длинный пролёт подшипника часто вызывает трение в зоне уплотнения посередине пролета. Обычная набивка может открыться после нескольких первых запусков турбины, в результате чего уплотнения на концах лопаток имеют зазор от 0,025 до 0,040 дюйма в течение многих лет после первых нескольких перезапусков после капитального ремонта. Выдвижная набивка, входящая в комплект TurboCare, выдерживает 0,015 дюйма. зазора с помощью пружин, чтобы отодвинуть сегменты уплотнительного кольца от вала во время запуска. Для уплотнений вала между ступенями к корпусу выдвижной набивки были добавлены щеточные уплотнения, уменьшающие зазор почти до нуля (рис. 8).
8. Плотно закрыто. Установка нового щеточного уплотнения (слева) и уплотнения кончика щетки (справа) значительно снизила утечку парового уплотнения в турбине блока Northport 3. Предоставлено: TurboCare Inc.
Конструкция парового уплотнения — это не только наука, но и искусство. На турбине блока 3 щеточные уплотнения были проанализированы в широком диапазоне рабочих условий, чтобы определить влияние на них износа. Хорошая практика проектирования турбин требует, чтобы ротор высокого давления выдерживал вдвое превышающую ожидаемую дестабилизирующую силу от уплотнений в качестве наихудшего условия устойчивости.Поскольку оригинальные уплотнения не соответствовали этому условию, новые уплотнения включали в себя три конструктивных элемента, предотвращающих завихрение, в промежуточном уплотнении высокого давления (кольца N2) и на ступенях 2 и 3 секции высокого давления.