Паровая турбина — значение слова, определение слова, слово означает
Паровая турбина, первичный паровой двигатель с вращательным движением рабочего органа — ротора и непрерывным рабочим процессом; служит для преобразования тепловой энергии пара водяного в механическую работу. Поток водяного пара поступает через направляющие аппараты на криволинейные лопатки, закрепленные по окружности ротора, и, воздействуя на них, приводит ротор во вращение. В отличие от поршневой паровой машины, П. т. использует не потенциальную, а кинетическую энергию пара. Попытки создать П. т. делались очень давно. Известно описание примитивной П. т., сделанное Героном Александрийским (1 в. до н. э.(наша эра)). Однако только в конце 19 в., когда термодинамика, машиностроение и металлургия достигли достаточного уровня, К. Г. П. Лаваль (Швеция) и Ч. А. Парсонс (Великобритания) независимо друг от друга в 1884—89 создали промышленно пригодные П. т. Лаваль применил расширение пара в конических неподвижных соплах в один приём от начального до конечного давления и полученную струю (со сверхзвуковой скоростью истечения) направил на один ряд рабочих лопаток, насаженных на диск. П. т., работающие по этому принципу, получили название активных П. т. Парсонс создал многоступенчатую реактивную П. т., в которой расширение пара осуществлялось в большом числе последовательно расположенных ступеней не только в каналах неподвижных (направляющих) лопаток, но и между подвижными (рабочими) лопатками. П. т. оказалась очень удобным двигателем для привода ротативных механизмов (генераторы электрического тока, насосы, воздуходувки) и судовых винтов; она была более быстроходной, компактной, лёгкой, экономичной и уравновешенной, чем поршневая паровая машина. Развитие П. т. шло чрезвычайно быстро как в направлении улучшения экономичности и повышения единичной мощности, так и по пути создания специализированных П. т. различного назначения. Невозможность получить большую агрегатную мощность и очень высокая частота вращения одноступенчатых П. т. Лаваля (до 30 000 об/мин у первых образцов) привели к тому, что они сохранили своё значение только для привода вспомогательных механизмов. Активные П. т. развивались в направлении создания многоступенчатых конструкций, в которых расширение пара осуществлялось в ряде последовательно расположенных ступеней. Это позволило значительно увеличить единичную мощность П. т., сохранив умеренную частоту вращения, необходимую для непосредственного соединения вала П. т. с вращаемым ею механизмом. Реактивная П. т. Парсонса некоторое время применялась (в основном на военных кораблях), но постепенно уступила место более компактным комбинированным активно-реактивным П. т., у которых реактивная часть высокого давления заменена одно- или двухвенчатым активным диском. В результате уменьшились потери на утечки пара через зазоры в лопаточном аппарате, турбина стала проще и экономичнее. Классификация паровых турбин. В зависимости от характера теплового процесса П. т. обычно подразделяют на 3 основные группы: чисто конденсационные, теплофикационные и специального назначения. Чисто конденсационные П. т. служат для превращения максимально возможной части теплоты пара в механическую работу. Эти П. т. работают с выпуском отработавшего пара в конденсатор, где поддерживается вакуум. Чисто конденсационные П. т. могут быть стационарными или транспортными. Стационарные П. т. в соединении с генераторами переменного электрического тока (турбогенераторы)— основное оборудование конденсационных электростанций. Чем больше мощность турбогенератора, тем он экономичнее и тем ниже стоимость 1 квт установленной мощности. Поэтому мощность П. т. растет из года в год и к 1974 достигла 1200 Мвт в агрегате [при давлении свежего пара до 35 Мн/м2 (1 нlm2 =10-5кгс/см2) и температуре до 650 °С]. Принятая в СССР частота электрического тока 50 гц требует, чтобы частота вращения П. т., непосредственно соединённой с двухполюсным генератором, равнялась 3000 об/мин. В зависимости от назначения П. т. для электростанций могут быть базовыми, несущими постоянную основную нагрузку; пиковыми, кратковременно работающими для покрытия пиков нагрузки; турбинами собственных нужд, обеспечивающими потребность электростанции в электроэнергии. От базовых П. т. требуется высокая экономичность на нагрузках, близких к полной (около 80%), от пиковых П. т.— возможность быстрого пуска и включения в работу, от П. т. собственных нужд — особая надёжность в работе. Все П. т. для электростанций рассчитываются на 100 тыс. ч работы (до капитального ремонта).Транспортные П. т. используются в качестве главных и вспомогательных двигателей на кораблях и судах. Неоднократно делались попытки применить П. т. на Теплофикационные П. т. служат для одновременного получения электрической и тепловой энергии. К ним относятся П. т. с противодавлением, с регулируемым отбором пара, а также с отбором и противодавлением. У П. т. с противодавлением весь отработавший пар используется для технологических целей (варка, сушка, отопление). Электрическая мощность, развиваемая турбоагрегатом с такой П. т., зависит от потребности производства или отопительной системы в греющем паре и меняется вместе с ней. Поэтому турбоагрегат с противодавлением обычно работает параллельно с конденсационной П. т. или электросетью, которые покрывают возникающий дефицит в электроэнергии. В П. т. с регулируемым отбором часть пара отводится из 1 или 2 промежуточных ступеней, а остальной пар идёт в конденсатор. Давление отбираемого пара поддерживается в заданных пределах системой регулирования. Место отбора (ступень П. т.) выбирают в зависимости от нужных параметров пара. У П. т. с отбором и противодавлением часть пара отводится из 1 или 2 промежуточных ступеней, а весь отработавший пар направляется из выпускного патрубка в отопительную систему. Давление пара П. т. для отопительных целей обычно составляет 0,12 Мн/м2, а для технологических нужд (сахарные, деревообрабатывающие, пищевые предприятия) 0,5—1,5 Мн/м2.П. т. специального назначения обычно работают на отбросном тепле металлургических, машиностроительных, и химических предприятий. К ним относятся П. т. мятого пара, двух давлений и предвключённые (форшальт). П. т. мятого пара используют отработавший пар поршневых машин, паровых молотов и прессов, имеющий давление немного выше атмосферного. П. т. двух давлений работают как на свежем, так и на отработавшем паре паровых механизмов, подводимом в одну из промежуточных ступеней. Предвключённые П. т. представляют собой турбины с высоким начальным давлением и высоким противодавлением; весь отработавший пар этих П. т. направляют в другие П. т. с более низким начальным давлением пара. Необходимость в предвключённых П. т. возникает при модернизации электростанций, связанной с установкой паровых котлов более высокого давления, на которое не рассчитаны ранее установленные на электростанции П. т. П. т. специального назначения не строят сериями, как конденсационные и теплофикационные П. т., а в большинстве случаев изготовляют по отдельным заказам. Все стационарные П. т. имеют нерегулируемые отборы пара из 2—5 ступеней давления для регенеративного подогрева питательной воды. В СССР установлено 4 ступени начальных параметров пара: давление 3,5 Мн/м2, температура 435 °С для П. т. мощностью до 12 Мвт; 9 Мн/м2, 535 °С для П. т. до 50 Мвт; 13 Мн/м2, 565 °С для П. т. до 100 Мвт и 24 Мн/м2, 565 °С для П. т. мощностью 200 и 300 Мвт. Давление отработавшего пара 3,5—5 кн/м2. Удельный расход тепла от 7,6 кдж/(вт×ч) у самых мощных П. т. до 13 кдж/(вт×ч) у небольших конденсационных турбин.Тепловой процесс паровых турбин. Кинетическая энергия, приобретённая паром при его расширении, эквивалентна уменьшению его энтальпии в процессе расширения. Работа пара (в кгс×м, 1 кгс×м = 10 дж) равна: W= 427(i0 — i1 а скорость истечения (в м /сек): , где i0 — начальная, a i1 — конечная энтальпия пара. Мощность (в квт), которую можно получить от турбины при расходе пара D кг/ч, равна:
а расход пара (в кг/ч) соответственно
Если под i0 — i1 подразумевается адиабатическое изменение энтальпии, то вышесказанное справедливо только для идеальной П. т., работающей без потерь. Действительная мощность на валу реальной П. т. (в квт) равна:
где hое — относительно эффективный кпд(коэффициент полезного действия), представляющий собой отношение действительной мощности, полученной на валу П. т., к мощности идеальной турбины. ‘, где de — расход пара в кг/(квт×ч). Для существующих П. т. удельный расход пара определяется экспериментально, а i0 — i1 находят по i—s диаграмме (см. Энтропия, Энтальпия). В активной П. т. свежий пар с давлением p0 и скоростью c0поступает в сопло и расширяется в нём до давления p1, при этом скорость пара возрастает до c1, с которой поток пара и входит на рабочие лопатки. Поток пара, оказывая давление на лопатки вследствие изменения направления в криволинейных междулопаточных каналах, заставляет диск и вал вращаться. На выходе с лопаток поток пара имеет скорость c2меньшую, чем c1, так как значительная часть кинетической энергии преобразовалась в механическую энергию вращения вала. Давление p1 на входе в канал равно давлению Кинетическая энергия будет полностью использована, если абсолютная скорость пара c2 при выходе с лопаток равна нулю. Это условие соблюдено, если c1 = 2u, где u — окружная скорость. Окружная скорость (в м/сек) равна:
где d — средний диаметр лопаточного венца в м, a n — частота вращения в мин. Следовательно, оптимальная окружная скорость лопаток должна быть . Очевидно, что в реальной турбине c2 не может быть равна 0, т.к. пар должен уходить с лопаток в конденсатор. Однако выходную скорость стремятся получить минимальной, т.к. кинетическая энергия уходящего потока пара представляет собой потерю полезной работы. Отступление от оптимального отношения вызывает сильное снижение кпд(коэффициент полезного действия) турбины. Это делает невозможным создание одноступенчатых турбин с высокими начальными параметрами пара, так как ещё (начало 1970-х гг.) не существует материалов, способных выдержать напряжения от центробежных сил при окружных скоростях, значительно превышающих 400 м/сек. Поэтому одноступенчатые активные турбины применяют только для привода быстроходных вспомогательных механизмов, экономичность которых не имеет решающего значения. Хорошая экономичность П. т., работающей с умеренными окружными скоростями при большом теплопадении, достигается применением ступеней давления. Если разделить располагаемый перепад давления на несколько ступеней с равными перепадами тепла, то в этих ступенях скорость истечения (в м/сек) равна: , где z — число ступеней. Следовательно, в каждой ступени скорость будет в раз меньше, чем в одноступенчатой П. т. Соответственно ниже будет и оптимальная окружная скорость u, то есть частота вращения ротора. Корпус П. т. с несколькими ступенями давления разделяют диафрагмами на отдельные камеры, в каждой из которых помещен один из дисков с рабочими лопатками (рис. 1). Пар может проникать из одной камеры в другую только через сопла, расположенные по окружности диафрагм. Давление пара снижается после каждой ступени, а скорости истечения пара c1 остаются примерно одинаковыми, что достигается выбором соответствующих размеров сопел. Число ступеней давления у мощных турбин с высокими начальными параметрами пара достигает 30—40. Поскольку объём пара по мере его расширения увеличивается, сечения сопел и высоты лопаток возрастают от первой ступени к последней. Последние ступени мощных П. т. обычно выполняют сдвоенными, а у самых больших П. т. — строенными и даже счетверёнными ввиду неприемлемо больших размеров лопаток последних ступеней, которые были бы необходимы для пропуска всего объёма пара через 1 ступень. В ступени давления возможно использовать кинетическую энергию не в одном, а в нескольких венцах лопаток, применив ступени скорости. Для этого на ободе диска размещают 2 (редко 3) венца рабочих лопаток, между которыми установлен венец неподвижных направляющих лопаток. Пар с давлением p0 подводится к соплам (рис. 2) и со скоростью c1 поступает на первый ряд рабочих лопаток, где его скоростной напор частично превращается в работу, а направление потока изменяется. Выйдя со скоростью c2 с первого ряда рабочих лопаток, пар проходит через направляющие лопатки и, снова изменив направление, входит во второй ряд лопаток со скоростью c’1, несколько меньшей, чем c2, вследствие потерь в направляющих лопатках. Второй ряд лопаток пар покидает с незначительной скоростью c’2. Теоретически при 2 ступенях скорости оптимальная окружная скорость u будет в 2 раза меньше, чем для одновенечной ступени, использующей тот же перепад энтальпии. Для z ступеней скорости оптимальная . Однако много ступеней скорости практически не применяют из-за больших потерь в лопатках. Наиболее распространённым типом турбины можно считать активную П. т. с одним двухвенечным диском в первой ступени давления и одновенечными дисками в остальных ступенях. Значение двухвенечного диска в том, что, используя значительную часть располагаемого перепада энтальпии в первой ступени давления, он позволяет понизить температуру и давление в корпусе П. т. и одновременно уменьшить нужное число ступеней давления, то есть укоротить и удешевить П. т. Характерной особенностью реактивных П. т. является то, что расширение пара происходит у них в каналах неподвижных и подвижных лопаточных венцов, то есть как в соплах, так и на рабочих лопатках. Отношение приходящейся на долю рабочих лопаток части располагаемого адиабатического перепада энтальпии h2 к общему адиабатическому перепаду ступени h0 = h1 + h2 (где h1 — теплопадение в направляющих лопатках) называется степенью реактивности . Если , то такую турбину принято называть реактивной. У чисто активной турбины должно бы быть r = 0, но практически активные турбины всегда работают с небольшой степенью реактивности, более высокой в последних ступенях. Это даёт некоторое повышение кпд(коэффициент полезного действия), особенно на режимах, отличных от расчётного. Венцы рабочих лопаток реактивной П. т. устанавливают в пазах ротора барабанного типа. В промежутках между ними размещают венцы неподвижных направляющих лопаток, закрепленных в корпусе турбины и образующих сопловые каналы. Профили подвижных и неподвижных лопаток обычно одинаковы. Свежий пар поступает в кольцевую камеру (рис. 3), откуда идёт в первый ряд неподвижных лопаток. В междулопаточных каналах этого ряда пар расширяется, давление его несколько понижается, а скорость возрастает от c0 до c1. Затем пар попадает в первый ряд рабочих лопаток. Между ними пар также расширяется и его относительная скорость возрастает. Однако абсолютная скорость c2 на выходе с рабочих лопаток будет меньше c1, так как за счёт уменьшения кинетической энергии получена механическая работа. В последующих ступенях процесс повторяется. Для уменьшения утечек пара через зазоры между лопатками, ротором и корпусом П. т. располагаемый перепад давлений делят на большое число (до 100) ступеней, благодаря чему разность давлений между смежными ступенями получается небольшой. В СССР не строят стационарных реактивных П. т., но отдельные зарубежные фирмы традиционно продолжают выпускать П. т. с активной частью высокого давления и последующими реактивными ступенями. Конструкция паровых турбин. По направлению движения потока пара различают аксиальные П. т., у которых поток пара движется вдоль оси турбины, и радиальные П. т., направление потока пара в которых перпендикулярно, а рабочие лопатки расположены параллельно оси вращения. В СССР строят только аксиальные П. т. По числу корпусов (цилиндров) П. т. подразделяют на однокорпусные и 2—3-, редко 4-корпусные. Многокорпусная конструкция (рис. 4) позволяет использовать большие располагаемые перепады энтальпии, разместив большое число ступеней давления, применить высококачественные металлы в части высокого давления и раздвоение потока пара в части низкого давления; однако такая П. т. получается более дорогой, тяжёлой и сложной. По числу валов различают одновальные П. т., у которых валы всех корпусов находятся на одной оси, и 2-, редко 3-вальные, состоящие из 2 или 3 параллельно размещенных одновальных П. т., связанных общностью теплового процесса, а у судовых П. т.— также общей зубчатой передачей (редуктором). Неподвижную часть П. т. — корпус — выполняют разъёмной в горизонтальной плоскости для возможности монтажа ротора. В корпусе имеются выточки для установки диафрагм, разъём которых совпадает с плоскостью разъёма корпуса. По периферии диафрагм размещены сопловые каналы, образованные криволинейными лопатками, залитыми в тело диафрагм или приваренными к нему. В местах прохода вала сквозь стенки корпуса установлены концевые уплотнения лабиринтового типа для предупреждения утечек пара наружу (со стороны высокого давления) и засасывания воздуха в корпус (со стороны низкого). Лабиринтовые уплотнения устанавливают в местах прохода ротора сквозь диафрагмы во избежание перетечек пара из ступени в ступень в обход сопел. На переднем конце вала устанавливают предельный регулятор (регулятор безопасности), автоматически останавливающий П. т. при увеличении частоты вращения на 10—12% сверх номинальной. Задний конец ротора снабжают валоповоротным устройством с электрическим приводом для медленного (4—6 об/мин) проворачивания ротора после останова П. т., что необходимо для равномерного его остывания. Лит.: Лосев С. М., Паровые турбины и конденсационные устройства. Теория, конструкции и эксплуатация, 10 изд., М. — Л., 1964; Щегляев А. В., Паровые турбины. Теория теплового процесса и конструкции турбин, 4 изд., М. — Л., 1967. С. М. Лосев. Рис. 2. Схематический разрез активной турбины с двумя ступенями скорости: 1 — вал; 2 — диск; 3 — первый ряд рабочих лопаток; 4 — сопло; 5 — корпус; 6 — второй ряд рабочих лопаток; 7 — направляющие лопатки. Рис. 4. Двухкорпусная паровая турбина (со снятыми крышками): 1 — корпус высокого давления; 2 — лабиринтовое уплотнение; 3 — колесо Кертиса; 4 — ротор высокого давления; 5 — соединительная муфта; 6 — ротор низкого давления; 7 — корпус низкого давления. Рис. 3. Схематический разрез небольшой реактивной турбины: 1 — кольцевая камера свежего пара; 2 — разгрузочный поршень; 3 — соединительный паропровод; 4 — барабан ротора; 5, 8 — рабочие лопатки; 6, 9 — направляющие лопатки; 7 — корпус. Рис. 1. Схематический продольный разрез активной турбины с тремя ступенями давления: 1 — кольцевая камера свежего пара; 2 — сопла первой ступени; 3 — рабочие лопатки первой ступени; 4 — сопла второй ступени; 5 — рабочие лопатки второй ступени; 6 — сопла третьей ступени; 7 — рабочие лопатки третьей ступени. |
vseslova.com.ua
3.2. Основные элементы современных паровых турбин
3.2. Основные элементы современных паровых турбин
Конструкция паровой турбины
Конструктивно современная паровая турбина (рис. 3.4) состоит из одного или нескольких цилиндров, в которых происходит процесс преобразования энергии пара, и ряда устройств, обеспечивающих организацию ее рабочего процесса.
Цилиндр. Основным узлом паровой турбины, в котором внутренняя энергия пара превращается в кинетическую энергию парового потока и далее – в механическую энергию ротора, является цилиндр. Он состоит из неподвижного корпуса (статоратурбины из двух частей, разделенных по горизонтальному разъему; направляющих (сопловых) лопаток, лабиринтовых уплотнений, впускного и выхлопного патрубков, опор подшипников и др.) и вращающегося в этом корпусе ротора (вал, диски, рабочие лопатки и др.). Основная задача сопловых лопаток – превратить потенциальную энергию пара, расширяющегося в сопловых решетках с уменьшением давления и одновременным снижением температуры, в кинетическую энергию организованного парового потока и направить его в рабочие лопатки ротора. Основное назначение рабочих лопаток и ротора турбины – преобразовать кинетическую энергию парового потока в механическую энергию вращающегося ротора, которая в свою очередь преобразуется в генераторе в электрическую энергию. Ротор мощной паровой турбины представлен на рисунке 3.5.
Число венцов сопловых лопаток в каждом цилиндре паровой турбины равно числу венцов рабочих лопаток соответствующего ротора. В современных мощных паровых турбинах различают цилиндры низкого, среднего, высокого и сверхвысокого давления (рис. 3.6.). Обычно цилиндром сверхвысокого давления именуется цилиндр, давление пара на входе в который превосходит 30,0 МПа, цилиндром высокого давления – участок турбины, давление пара на входе в который колеблется в пределах 23,5 – 9,0 МПа, цилиндром среднего давления – участок турбины, давление пара на входе в который около 3,0 МПа, цилиндром низкого давления – участок, давление пара на входе в который не превышает 0,2 МПа. В современных мощных турбоагрегатах число цилиндров низкого давления может достигать 4 с целью обеспечения приемлемой по условиям прочности длины рабочих лопаток последних ступеней турбины.
Органы парораспределения. Количество пара, поступающего в цилиндр турбины, ограничивается открытием клапанов, которые вместе с регулирующей ступенью называются органами парораспределения. В практике турбиностроения различают два типа парораспределения – дроссельное и сопловое. Дроссельное парораспределение предусматривает подвод пара после открытия клапана равномерно по всей окружности венца сопловых лопаток. Это означает, что функцию изменения расхода выполняет кольцевая щель между клапаном, который перемещается, и его седлом, которое установлено неподвижно. Процесс изменения расхода в этой конструкции связан с дросселированием. Чем меньше открыт клапан, тем больше потери давления пара от дросселирования и тем меньше его расход на цилиндр.
Рис. 3.4. Внешний вид паровой турбины К-300-240
Рис. 3.5. Ротор паровой турбины мощностью 220 МВт
Сопловое парораспределение предусматривает секционирование направляющих лопаток по окружности на несколько сегментов (групп сопел), к каждому из которых организован отдельный подвод пара, оснащенный своим клапаном, который либо закрыт, либо полностью открыт. При открытом клапане потери давления на нем минимальны, а расход пара пропорционален доле окружности, через которую этот пар поступает в турбину. Таким образом, при сопловом парораспределении процесс дросселирования отсутствует, а потери давления сводятся к минимуму.
В случае высокого и сверхвысокого начального давления в системе паровпуска применяются так называемые разгрузочные устройства, которые предназначены для уменьшения начального перепада давления на клапане и снижения усилия, которое необходимо приложить к клапану при его открытии.
В некоторых случаях дросселирование называют еще качественным регулированием расхода пара на турбину, а сопловое парораспределение – количественным.
Система регулирования. Эта система позволяет осуществлять синхронизацию турбогенератора с сетью, устанавливать заданную нагрузку при работе в общую сеть, обеспечивать перевод турбины на холостой ход при сбросе электрической нагрузки. Принципиальная схема системы непрямого регулирования с центробежным регулятором скорости представлена на рисунке 3.7.
С ростом частоты вращения ротора турбины и муфты регулятора центробежная сила грузов увеличивается, муфта регулятора скорости1поднимается, сжимая пружину регулятора и поворачивая рычаг АВ вокруг точки В. Соединенный с рычагом в точке С золотник2смещается из среднего положения вверх и сообщает верхнюю полость гидравлического сервомотора3с напорной линией4через окноa, а нижнюю – со сливной линией5через окноb. Под воздействием перепада давлений поршень сервомотора перемещается вниз, прикрывая регулирующий клапан6и уменьшая пропуск пара в турбину7, что и обусловит снижение частоты вращения ротора. Одновременно со смещением штока сервомотора рычаг АВ поворачивается относительно точки А, смещая золотник вниз и прекращая подачу жидкости в сервомотор. Золотник возвращается в среднее положение, чем стабилизируется переходный процесс при новой (уменьшенной) частоте вращения ротора. Если увеличивается нагрузка турбины и частота вращения ротора падает, то элементы регулятора смещаются в противоположном рассмотренному направлении и процесс регулирования протекает аналогично, но с увеличением пропуска пара в турбину. Это приводит к росту скорости вращения ротора и восстановлению частоты генерируемого тока.
Системы регулирования паровых турбин, применяемых, например, на АЭС, в качестве рабочей жидкости используют, как правило, турбинное масло. Отличительной особенностью систем регулирования турбин К-300240-2 и К-500-240-2 является применение в системе регулирования вместо турбинного масла конденсата водяного пара. На всех турбинах НПО «Турбоатом», помимо традиционных гидравлических систем регулирования, применяют электрогидравлические системы регулирования (ЭГСР) с более высоким быстродействием.
Валоповорот. В турбоагрегатах традиционно применяется «тихоходный» – несколько оборотов в минуту – валоповорот. Валоповоротное устройство предназначено для медленного вращения ротора при пуске и останове турбины для предотвращения теплового искривления ротора. Одна из конструкций валоповоротного устройства изображена на рис. 3.8. Она включает электродвигатель с червяком, входящим в зацепление с червячным колесом1, расположенным на промежуточном валике. На винтовой шпонке этого валика установлена ведущая цилиндрическая шестерня, которая при включении валоповоротного устройства входит в зацепление с ведомой цилиндрической шестерней, сидящей на валу турбины. После подачи пара в турбину частота вращения ротора растет и ведущая шестерня автоматически выходит из зацепления.
Рис. 3.6. Цилиндры высокого, среднего и низкого давления паровой турбины мощностью 300 МВт (нижняя половина)
Рис. 3.7. Принципиальная схема регулирования с однократным усилением: 1 – муфта регулятора; 2 – золотник; 3 – гидравлический сервомотор; 4 – напорная линия; 5 – сливная линия; 6 – регулирующий клапан; 7 – подача пара в турбину
Подшипники и опоры. Паротурбинные агрегаты расположены, как правило, в машинном зале электростанции горизонтально. Такое расположение обусловливает применение в турбине наряду с опорными также и упорных или опорно-упорных подшипников3(см. рис. 3.8). Для опорных подшипников наиболее распространенным в энергетике является парное их количество – на каждый ротор приходится два опорных подшипника. Для тяжелых роторов (роторов низкого давления быстроходных турбин с числом оборотов 3000 об/мин и всех без исключения роторов «тихоходных» турбин с числом оборотов 1500 об/мин) допустимо применение традиционных для энергетического турбиностроения втулочных подшипников. В таком подшипнике нижняя половина вкладыша выполняет роль несущей поверхности, а верхняя половина – роль демпфера любых возмущений, возникающих при эксплуатации. К таким возмущениям можно отнести остаточную динамическую неуравновешенность ротора, возмущения, возникающие при прохождении критических чисел оборотов, возмущения за счет переменных сил от воздействия парового потока. Сила веса тяжелых роторов, направленная вниз, в состоянии подавить, как правило, все эти возмущения, что обеспечивает спокойный ход турбины. А для относительно легких роторов (роторов высокого и среднего давления) все перечисленные возмущения могут оказаться значительными по сравнению с весом ротора, особенно в паровом потоке высокой плотности. Для подавления этих возмущений разработаны так называемые сегментные подшипники. В этих подшипниках каждый сегмент обладает повышенной по сравнению с втулочным подшипником демпфирующей способностью.
Естественно, конструкция сегментного опорного подшипника, где каждый сегмент снабжается маслом индивидуально, значительно сложнее, чем втулочного. Однако резко возросшая надежность окупает это усложнение.
Что касается упорного подшипника, то его конструкция всесторонне рассмотрена еще Стодолой и за истекшее столетие практически не претерпела каких-либо изменений. Опоры, в которых располагаются упорный и опорные подшипники, изготавливают скользящими с «фикспунктом» в районе упорного подшипника. Это обеспечивает минимизацию осевых зазоров в области максимального давления пара, т.е. в области самых коротких лопаток, что в свою очередь позволяет минимизировать в этой зоне потери от утечек.
Рис. 3.8. Продольный разрез турбины К-50-90: 1 – ротор турбины; 2 – корпус турбины; 3 – опорно-упорный подшипник; 4 – опорный подшипник; 5 – регулирующий клапан; 6 – сопловая коробка; 7 – кулачковый вал; 8 – сервомотор; 9 – главный масляный насос; 10 – регулятор скорости; 11 – следящий золотник; 12 – картер переднего подшипника; 13 – червячное колесо валоповоротного устройства; 14 – соединительная муфта; 15 – выхлопной патрубок турбины; 16 – насадные диски; 17 – рабочие лопатки; 18 – диафрагмы; 19 – обоймы диафрагм; 20 – обоймы переднего концевого уплотнения; 21 – перепускная труба (от стопорного к регулирующему клапану)
Типичная конструкция одноцилиндровой конденсационной турбины мощностью 50 МВт с начальными параметрами пара 8,8 МПа, 535°С представлена на рис. 3.8. В этой турбине применен комбинированный ротор. Первые 19 дисков, работающих в зоне высокой температуры, откованы как одно целое с валом турбины, последние три диска — насадные.
Неподвижную сопловую решетку, закрепленную в сопловых коробках или диафрагмах с соответствующей вращающейся рабочей решеткой, закрепленной на следующем по ходу пара диске, называютступенью турбины. Проточная часть рассматриваемой одноцилиндровой турбины состоит из 22 ступеней, из которых первая называетсярегулирующей. В каждой сопловой решетке поток пара ускоряется и приобретает направление безударного входа в каналы рабочих лопаток. Усилия, развиваемые потоком пара на рабочих лопатках, вращают диски и связанный с ними вал. По мере понижения давления пара при прохождении от первой к последней ступени удельный объем пара растет, что требует увеличения проходных сечений сопловых и рабочих решеток и, соответственно, высоты лопаток и среднего диаметра ступеней.
К переднему торцу ротора прикреплен приставной конец вала, на котором установлены бойки предохранительных выключателей (датчики автомата безопасности), воздействующие на стопорный и регулирующие клапаны и прекращающие доступ пара в турбину при превышении частоты вращения ротора на 10–12% по сравнению с расчетной.
Статор турбины состоит из корпуса, в который вварены сопловые коробки, соединенные с помощью сварки с клапанными коробками, установлены обоймы концевых уплотнений, обоймы диафрагм, сами диафрагмы и их уплотнения. Корпус этой турбины, кроме обычного горизонтального разъема, имеет два вертикальных разъема, разделяющих его на переднюю часть, среднюю часть и выходной патрубок. Передняя часть корпуса выполнена литой, средняя часть корпуса и выходной патрубок сделаны сварными.
В переднем картере расположен опорноупорный подшипник, в заднем картере – опорные подшипники роторов турбины и генератора. Передний картер установлен на фундаментной плите и при тепловом расширении корпуса турбины может свободно перемещаться по этой плите. Задний картер выполнен за одно целое с выхлопным патрубком турбины, который при тепловых расширениях остается неподвижным благодаря его фиксации пересечением поперечной и продольной шпонок, образующих так называемыйфикспункттурбины, или мертвую точку. В заднем картере турбины расположено валоповоротное устройство.
В турбине К-50-90 применена сопловая система парораспределения, т.е. количественное регулирование расхода пара. Устройство автоматического регулирования турбины состоит из четырех регулирующих клапанов, распределительного кулачкового вала, соединенного зубчатой рейкой с сервомотором. Сервомотор получает импульс от регулятора скорости и регулирует положение клапанов. Профили кулачков выполнены так, чтобы регулирующие клапаны открывались поочередно один за другим. Последовательное открытие или закрытие клапанов исключает дросселирование пара, проходящего через полностью открытые клапаны при пониженных нагрузках турбины.
Конденсатор и вакуумная система.
Подавляющее большинство турбин, используемых в мировой энергетике для производства электрической энергии, являются конденсационными. Это означает, что процесс расширения рабочего тела (водяного пара) продолжается до давлений, значительно меньших, чем атмосферное. В результате такого расширения дополнительно выработанная энергия может составлять несколько десятков процентов от суммарной выработки.
Конденсатор – теплообменный аппарат, предназначенный для превращения отработавшего в турбине пара в жидкое состояние (конденсат). Конденсация пара происходит при соприкосновении его с поверхностью тела, имеющего более низкую температуру, чем температура насыщения пара при данном давлении в конденсаторе. Конденсация пара сопровождается выделением теплоты, затраченной ранее на испарение жидкости, которая отводится при помощи охлаждающей среды. В зависимости от вида охлаждающей среды конденсаторы разделяются наводяныеивоздушные. Современные паротурбинные установки снабжены, как правило, водяными конденсаторами. Воздушные конденсаторы имеют по сравнению с водяными более сложную конструкцию и не получили в настоящее время широкого распространения.
Рис. 3.9. Схема двухходового поверхностного конденсатора: 1 – корпус конденсатора; 2,3 – крышки водяных камер; 4 – трубная доска; 5 – конденсаторные трубки; 6 – приемный паровой патрубок; 7 – конденсатосборник; 8 – патрубок отсоса паровоздушной смеси; 9 – воздухоохладитель; 10 – паронаправляющий щит; 11 – входной патрубок; 12 – выходной патрубок для охлаждающей воды; 13 – разделительная перегородка; 14 – паровое пространство конденсатора; 15,16,17 – входная, поворотная и выходная камеры охлаждающей воды; А – вход отработавшего пара; Б – отсос паровоздушной смесии; В, Г – вход и выход охлаждающей воды; Д – отвод конденсата
Конденсационная установка паровой турбины состоит из собственно конденсатора и дополнительных устройств, обеспечивающих его работу. Подача охлаждающей воды в конденсатор осуществляется циркуляционным насосом. Конденсатные насосы служат для откачки из нижней части конденсатора конденсата и подачи его в систему регенеративного подогрева питательной воды. Воздухоотсасывающие устройства предназначены для удаления воздуха, поступающего в турбину и конденсатор вместе с паром, а также через неплотности фланцевых соединений, концевые уплотнения и другие места.
Схема простейшего поверхностного конденсатора водяного типа приведена на рис. 3.9.
Он состоит из корпуса, торцевые стороны которого закрыты трубными досками с конденсаторными трубками, выходящими своими концами в водяные камеры. Камеры разделяются перегородкой, которая делит все конденсаторные трубки на две секции, образующие так называемые «ходы» воды (в данном случае – два хода). Вода поступает в водяную камеру через патрубок и проходит по трубкам, расположенным ниже перегородки. В поворотной камере вода переходит во вторую секцию трубок, расположенную по высоте выше перегородки. По трубкам этой секции вода идет в обратном направлении, совершая второй «ход», попадает в камеру и через выходной патрубок направляется на слив.
Пар, поступающий из турбины в паровое пространство, конденсируется на поверхности конденсаторных трубок, внутри которых протекает охлаждающая вода. За счет резкого уменьшения удельного объема пара в конденсаторе создается низкое давление (вакуум). Чем ниже температура и больше расход охлаждающей среды, тем более глубокий вакуум можно получить в конденсаторе. Образующийся конденсат стекает в нижнюю часть корпуса конденсатора, а затем в конденсатосборник.
Удаление воздуха (точнее, паровоздушной смеси) из конденсатора производится воздухоотсасывающим устройством через патрубок8. В целях уменьшения объема отсасываемой паровоздушной смеси ее охлаждают в специально выделенном с помощью перегородки отсеке конденсатора – воздухоохладителе.
Для отсоса воздуха из воздухоохладителя устанавливается трехступенчатый пароструйный эжектор – основной. Помимо основного эжектора, который постоянно находится в эксплуатации, в турбоустановке предусмотрены эжектор пусковой конденсатора (водоструйный) и эжектор пусковой циркуляционной системы. Эжектор пусковой конденсатора предназначен для быстрого углубления вакуума при пуске турбоустановки. Эжектор пусковой циркуляционной системы служит для отсоса паровоздушной смеси из циркуляционной системы конденсатора. Конденсатор турбоустановки снабжен также двумя конденсатосборниками, из которых образующийся конденсат непрерывно откачивается конденсатными насосами.
На переходном патрубке конденсатора размещены приемно-сбросные устройства, цель которых – обеспечить сброс пара из котла в конденсатор в обход турбины при внезапном полном сбросе нагрузки или в пусковых режимах. Расходы сбрасываемого пара могут достигать 60% полного расхода пара на турбину. Конструкция приемносбросного устройства предусматривает, помимо снижения давления, снижение температуры сбрасываемого в конденсатор пара с соответствующим ее регулированием. Она должна поддерживаться на 10–20°С выше температуры насыщения при данном давлении в конденсаторе.
Промежуточный перегрев и регенерация в турбоустановках. В теплоэнергетической установке с промежуточным перегревом пар после расширения в цилиндре высокого давления (ЦВД) турбины направляется в котел для вторичного перегрева, где температура его повышается практически до того же уровня, что и перед ЦВД. После промежуточного перегрева пар направляется в цилиндр низкого давления, где расширяется до давления в конденсаторерк.
Экономичность идеального теплового цикла с промежуточным перегревом зависит от параметров пара, отводимого на промежуточный перегрев. Оптимальную температуру параТ1опт, при которой он должен отводиться на промежуточный перегрев, можно ориентировочно оценить как 1,02–1,04 от температуры питательной воды. Давление пара перед промежуточным перегревом обычно выбирают равным 0,15—0,3 давления свежего пара. В результате промперегрева общая экономичность цикла возрастет. При этом благодаря уменьшению влажности пара в последних ступенях турбины низкого давления возрастут относительные внутренние к.п.д. этих ступеней, а следовательно, увеличится и к.п.д. всей турбины. Потеря давленияΔрппв тракте промежуточного перегрева (в паропроводе от турбины к котлу, перегревателе и паропроводе от котла к турбине) снижает эффект от применения промперегрева пара и поэтому допускается не более 10% потери абсолютного давления в промежуточном перегревателе.
Система регенерации в турбоустановках предполагает подогрев конденсата, образовавшегося в конденсаторе, паром, который отобран из проточной части турбины. Для этого основной поток конденсата пропускают через подогреватели, в трубную систему которых поступает конденсат, а в корпус подается пар из отборов турбины. Для подогрева основного конденсата применяют подогреватели низкого давления (ПНД), подогреватели высокого давления (ПВД) и между ними – деаэратор (Д). Деаэратор предназначен для удаления из основного конденсата остатков воздуха, растворенного в конденсате.
Идея регенерации в ПТУ возникла в связи с потребностью снижения потерь теплоты в конденсаторе. Известно, что потери теплоты с охлаждающей водой в конденсаторе турбины прямо пропорциональны количеству отработавшего пара, поступающего в конденсатор. Расход пара в конденсатор можно значительно уменьшить (на 30–40%) путем отбора его для подогрева питательной воды за ступенями турбины после того, как он произвел работу в предшествующих ступенях. Такой процесс называют регенеративным подогревом питательной воды. Регенеративный цикл по сравнению с обычным имеет более высокую среднюю температуру подвода теплоты при неизменной температуре отвода и обладает поэтому более высоким термическим к.п.д. Повышение экономичности в цикле с регенерацией пропорционально мощности, вырабатываемой на тепловом потреблении, т. е. на базе теплоты, переданной питательной воде в системе регенерации. Путем регенеративного подогрева температура питательной воды могла бы быть повышена до температуры, близкой к температуре насыщения, отвечающей давлению свежего пара. Однако при этом сильно возросли бы потери теплоты с уходящими газами котла. Поэтому международные нормы типоразмеров паровых турбин рекомендуют выбирать температуру питательной воды на входе в котел равной 0,65–0,75 температуры насыщения, отвечающей давлению в котле. В соответствии с этим при сверхкритических параметрах пара, в частности при начальном давлении егор0=23,5 МПа, температура питательной воды принимается равной 265–275°С.
Рис. 3.10. Тепловая схема турбинной установки с использованием утечек пара концевых уплотнений и уплотнений штоков клапанов турбины в системе регенерации: Т – турбина; Г – генератор; К – конденсатор; КН – конденсатный насос; ЭЖ – основной эжектор; ОЭ – охладитель основного эжектора; ЭУ – эжектор уплотнений; ОЭУ – охладитель пара эжектора отсоса уплотнений; СП – сальниковый подогреватель; П1–П4 – подогреватели; ОК – охладитель конденсата; Д – деаэратор; ПН – питательный насос
Регенерация положительно влияет на относительный внутренний к.п.д. первых ступеней благодаря повышенному расходу пара через ЦВД и соответствующему увеличению высоты лопаток. Объемный пропуск пара через последние ступени турбины при регенерации уменьшается, что снижает потери с выходной скоростью в последних ступенях турбины.
В современных паротурбинных установках средней и большой мощности в целях повышения их экономичности применяют широко развитую систему регенерации с использованием пара концевых лабиринтовых уплотнений, уплотнений штоков регулирующих клапанов турбины и др. (рис.3.10).
Свежий пар из котла поступает в турбину по главному паропроводу с параметрамир0,t0. После расширения в проточной части турбины до давленияркон направляется в конденсатор. Для поддержания глубокого вакуума из парового пространства конденсатора основным эжектором (ЭЖ) отсасывается паровоздушная смесь. Конденсат отработавшего пара стекает в конденсатосборник, затем конденсатными насосами (КН) подается через охладитель эжектора (ОЭ), охладитель пара эжектора отсоса уплотнений (ОЭУ), сальниковый подогреватель (СП) и регенеративные подогреватели низкого давления П1, П2 в деаэратор Д. Деаэратор предназначен для удаления растворенных в конденсате агрессивных газов (О2и СО2), вызывающих коррозию металлических поверхностей. Кислород и свободная углекислота попадают в конденсат из-за присосов воздуха через неплотности вакуумной системы турбинной установки и с добавочной водой. В деаэраторе агрессивные газы удаляются при нагревании конденсата и добавочной воды паром до температуры насыщения греющего пара. В современных паротурбинных установках устанавливают деаэраторы повышенного давления 0,6—0,7 МПа с температурой насыщения 158–165°С. Конденсат пара на участке от конденсатора до деаэратора называют конденсатом, а на участке от деаэратора до котла – питательной водой.
Питательная вода из деаэратора забирается питательным насосом (ПН) и под высоким давлением (на блоках со сверхкритическими и суперсверхкритическими параметрами пара до 35 МПа) подается через подогреватели высокого давления ПЗ, П4 в котел.
Пар концевых лабиринтовых уплотнений турбины отсасывается из крайних камер уплотнений, где поддерживается давление 95—97 кПа, специальным эжектором и направляется в охладитель эжектора отсоса, через который прокачивается основной конденсат. Часть пара повышенного давления из концевых лабиринтовых уплотнений направляется в первый и третий регенеративные отборы. С целью предотвращения присоса воздуха в вакуумную систему через концевые уплотнения турбины в каждой предпоследней камере концевых уплотнений поддерживается небольшое избыточное (110—120 кПа) давление с помощью специального регулятора, установленного на подводе уплотняющего пара к этой камере из деаэратора.
Питательная установка. Питательная установка турбоагрегата состоит из главного питательного насоса с турбинным приводом, пускорезервного питательного
насоса с электроприводом и бустерных насосов с электроприводом. Питательная установка предназначена для подачи питательной воды из деаэратора через подогреватели высокого давления в котел. Насос включается в работу при нагрузке блока 50–60% и рассчитан на работу в диапазоне 30–100%. Пускорезервный питательный насос ПЭН приводится во вращение асинхронным электродвигателем.
Сборка паровой турбины на испытательном стенде
energetika.in.ua
Паровая турбина Википедия
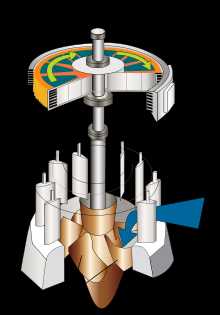
Парова́я турби́на — тепловой двигатель, в котором энергия пара преобразуется в механическую работу.
В лопаточном аппарате паровой турбины потенциальная энергия сжатого и нагретого водяного пара преобразуется в кинетическую, которая в свою очередь преобразуется в механическую работу — вращение вала турбины.
Пар от парокотельного агрегата поступает через направляющие аппараты на криволинейные лопатки, закрепленные по окружности ротора, и воздействуя на них, приводит ротор во вращение.
Паровая турбина является одним из элементов паротурбинной установки (ПТУ).
Паровая турбина и электрогенератор составляют турбоагрегат.
Основные конструкции паровых турбин[ | ]
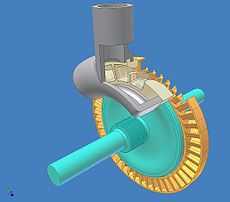
Паровая турбина состоит из двух основных частей. Ротор с лопатками — подвижная часть турбины. Статор с соплами — неподвижная часть.
По направлению движения потока пара различают аксиальные паровые турбины, у которых поток пара движется вдоль оси турбины, и радиальные, направление потока пара в которых перпендикулярно, а рабочие лопатки расположены параллельно оси вращения.
По числу цилиндров турбины подразделяют на одноцилиндровые и двух—трёх-, четырёх-пятицилиндровые. Многоцилиндровая турбина позволяет использовать бо́льшие располагаемые тепловые перепады энтальпии, разместив большое число ступеней давления, применить высококачественные материалы в частях высокого давления и раздвоение потока пара в частях среднего и низкого давления. Такая турбина получается более дорогой, тяжёлой и сложной. Поэтому многокорпусные турбины используются в мощных паротурбинных установках.
По числу валов различают одновальные, двувальные, реже трёхвальные, связанных общностью теплового процесса или общей зубчатой передачей (редуктором). Расположение валов может быть как соосным, так и параллельным — с независимым расположением осей валов.
- Неподвижную часть — корпус (статор) — выполняют разъёмной в горизонтальной плоскости для возможности выемки или монтажа ротора. В корпусе имеются выточки для установки диафрагм, разъём которых совпадает с плоскостью разъёма корпуса турбины. По периферии диафрагм размещены сопловые каналы (решётки), образованные криволинейными лопатками, залитыми в тело диафрагм или приваренными к нему.
- В местах прохода вала сквозь стенки корпуса установлены
ru-wiki.ru
Тепловой расчет паровой турбины
Введение
Тепловой расчет турбины выполняется с целью определения основных размеров и характеристик проточной части: числа и диаметров ступеней, высот их сопловых и рабочих решеток и типов профилей, к.п.д. ступеней, отдельных цилиндров и турбины в целом. Тепловой расчет турбины выполняется на заданную мощность, заданные начальные и конечные параметры пара, число оборотов; при проектировании турбины с регулируемыми отборами пара, кроме того, на заданные давления и величину отборов. В данном курсовом проекте произведен тепловой расчет турбины Р-40-130/31.Даны все нужные исходные данные. Целью курсового проектирования является закрепление, расширение и углубление теоретических знаний по дисциплине “Паровые и газовые турбины”. Курсовой проект включает проведение большого объёма расчётных работ, поэтому при его выполнении нужно максимально использовать ЭВМ, что существенно повысит качество проекта.
Паровая турбина является двигателем, в котором потенциальная энергия перегретого пара преобразуется в кинетическую энергию и , затем в механическую энергию вращения ротора.
Для турбин типа Р за расчетный расход пара принимается расход пара на турбину при режиме номинальной мощности.
1 .Основная часть
1.1 Построение рабочего процесса турбины и определение расхода пара на турбину
Процесс расширения начинают строить с состояния пара перед стопорным клапаном турбины (рис.1) определяемого начальными параметрами P0 , t0 . Состояние пара перед соплами первой ступени определяют с учётом его дросселирования в клапанах
P’0 = (0,95¸0,97)·P0 .
P’0 = (0,96)·P0 =0,96*12,75=11,97 МПа
Рисунок 1- Процесс расширения пара в турбине с промперегревом в i-s–диаграмме
Внутренний КПД регулирующей ступени и отдельных частей турбины принимается по аналитическим зависимостям или по опытным данным, полученным в результате испытаний однотипных турбин.
Для турбин с n = 50 сек-1 КПД регулирующей ступени зависит в основном от площади сопловой решётки, пропорциональной объёмному расходу пара.
В турбинах типа Р в качестве регулирующей ступени устанавливают до мощности 40 МВт включительно как одновенечные, так и двухвенечные ступени, выше 50 МВт – одновенечные. Одновенечные — hорс =95 кДж/кг.
Располагаемый теплоперепад в турбине определяем по формуле:
H0 = h0 – hк =3490 – 3080= 410 кДж/кг
От точки Ро/ по изоэнтропе откладывается выбранный тепловой перепад на регулирующую ступень hорс (рис.3.1). Изобара Р2рс , проведенная через точку С конца отрезка hорс , соответствует давлению за регулирующей ступенью. Для того, чтобы на этой изобаре найти точку начала процесса в нерегулируемых ступенях, необходимо учесть потери в регулирующей ступени.
КПД одновенечной регулирующей ступени можно найти по формуле
(1)где ku/с — коэффициент, учитывающий отклонение отношения скоростей u/сф от оптимального значения;
Р0 ,v0 — давление, Па, и удельный объём, м³/кг, перед соплами регулирующей ступени;
D — расход пара через ступень, кг/с.
Величину D можно принять равной расходу пара на турбину, найденному для её прототипа или приближённо оценить из выражения
(2)где kрег – коэффициент регенерации, учитывающий увеличение расхода пара из-за регенеративных отборов, kрег =1,15…1,30;
Нi – действительный теплоперепад конденсационного потока пара;
ηм , ηг – механический КПД турбины и КПД электрогенератора, принимаемые для турбин мощностью более 50 МВт, соответственно 0,99 и 0,997;
Dп , Dт – расходы пара на производственные нужды и теплофикацию;
yп , yт – коэффициенты недовыработки мощности паром промышленного и отопительного отборов.
КПД групп ступеней ЧНД, работающих на перегретом пареКак правило, наибольшее значение имеет КПД ЧСД турбины, где высота лопаток достигла значительной величины, нет регулирующей ступени и отсутствуют потери энергии от влажности.
Расход пара на ЦНД:
Т.к. ЦНД выполнен однопоточным, то расход пара на один поток G1 = 118 кг/с.
1.2 Выбор и расчёт регулирующей ступени
Первая ступень в турбинах с сопловым парораспределением работает с переменной парциальностью при изменении расхода пара и называется регулирующей. В турбинах с дроссельным парораспределением регулирующая ступень отсутствует.
В качестве регулирующей ступени может быть использована одновенечная ступень или двухвенечная ступень скорости. Выбор типа регулирующей ступени производится с учетом ее влияния на конструкцию и экономичность турбины. Использование теплоперепад в одновенечной (80…120 кДж/кг), что приводит к сокращению числа нерегулируемых ступеней и снижению металлоемкости и стоимости турбины. При этом уменьшится температура и давление пара перед нерегулируемыми ступенями, а это позволит применить более дешевые, низколегированные стали для их изготовления, снизить утечки пара через переднее концевое уплотнение и увеличить высоту лопаток первой нерегулируемой ступени. Расчет регулирующей ступени сводится к определению ее геометрических размеров, выбору профилей сопловых и рабочих лопаток, нахождению мощности и КПД ступени. Поскольку характеристики этой ступени оказывают существенное влияние на конструкцию, число ступеней и КПД всей турбины, то необходимо стремиться спроектировать эту ступень с высоким КПД. Исходными данными для расчета регулирующей ступени являются частота вращения ротора турбины, расход пара на турбину
и параметры пара перед ступенью. В качестве определяющего размера принимают средний диаметр ступени d. Расчет одновенечной регулирующей ступени (рис.2) производят в следующей последовательности.Находят окружную скорость ступени
и выбирают степень реактивности ρ на среднем диаметре в пределах 0,03-0,08. Такая величина ρ исключает возможность появления отрицательной реактивности у корня лопаток на нерасчетных режимах.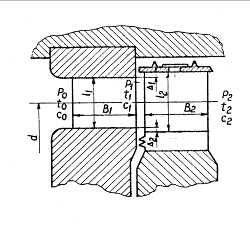
Рисунок 2 — Ступень турбины
Большое влияние на характеристики ступени оказывает характеристический коэффициент
. В первом приближении его можно принять равным , обеспечивающим максимум лопаточного КПД , (3)где
— фиктивная скорость пара;φ — коэффициент скорости сопловой решетки;
— угол выхода пара из сопловой решетки;Предварительно можно принять
, φ=0,95 с последующим уточнением по формуле (4)Действительное отношение
рекомендуется принять меньше оптимального для увеличения теплоперепада на регулирующую ступень.Фиктивная скорость на выходе из сопловой решетки
позволяет определить располагаемый теплоперепад, срабатываемый в ступени .С учетом принятой степени реактивности ρ находят располагаемый теплоперепад в сопловой
и рабочей решетках, а так же теоретичmirznanii.com
Паровая турбина
Паровая турбина — вид двигателя, в котором энергия пара преобразуется в механическую работу.
Паровая турбина состоит из двух основных частей — ротор с лопатками (подвижная часть турбины) и статор с соплами (неподвижная часть).
В паровой турбине потенциальная энергия сжатого или нагретого пара (обычно водяного) преобразуется в кинетическую, которая в свою очередь преобразуется в механическую через вращение вала турбины — пар, вырабатываемей паровым котельным аппаратом, поступает (через специальные направляющие) на лопатки турбины, закрепленные по окружности ротора, и приводит к его вращению.
Турбины бывают:
- Конденсационные – предназначены для преобразования максимально возможной части тепла пара в механическую энергию. Бывают стационарными и транспортными.
- Теплофикационные — предназначены для получения электрической и тепловой энергии.
- Специального назначения — работают на уходящем тепле от предприятий различного вида (пар, выхлопы и т.д.).
Паровые турбины, как и поршневые двигатели, используются в качестве приводов для различных устройств:
- Стационарные паровые турбины обычно используют как привода турбогенераторов – устанавливаются на одном валу с генераторами. В качестве конечного продукта системы рассматривается, главным образом, электроэнергия. Тепловая энергия используется лишь в небольшой части. Паровые турбины для электростанций имеют назначенный ресурс в 270 тыс. ч. с капитальным ремонтом в период около 4 лет.
- Теплофикационные паровые турбины предназначены для одновременного получения как электрической, так и тепловой энергии (по аналогии с когенерационными электростанциями, базирующимися на газопоршневых двигателях). Такие системы называются теплоэлектроцентралями (ТЭЦ). Электрическая мощность, развиваемая турбоагрегатом с такой паровой турбиной, зависит от фактической нагрузки производства или его потребности в паре. Поэтому ТЭЦ обычно работает параллельно с электросетью, которые покрывают возникающий дефицит в электроэнергии.
- Транспортные паровые турбины применяются как главные и дополнительные двигатели на кораблях и судах. В отличие от большинства стационарных турбин, транспортные паровые турбины работают с переменной частотой вращения, зависящей от требуемой скорости судна.
Основные отличия турбины от поршневого двигателя.
Паровые турбины и поршневые двигатели имеют ряд существенных отличий, связанных с конструкционными особенностями. Эти отличия существенно влияют на выбор того или иного принципа работы приводного двигателя в разных системах:
- Электрический КПД в электростанциях. Наивысший электрический КПД – до 34% у турбины и 42% и более у газопоршневого двигателя – достигается при работе со 100%-ной нагрузкой. При снижении нагрузки до 50 % электрический КПД газовой турбины снижается почти в 2 раза (50%). Для газопоршневого двигателя такое же изменение режима нагрузки приведет к снижению КПД всего на 4-5%.
- Номинальный выход мощности, и поршневого двигателя, и турбины зависит от высоты площадки над уровнем моря и температуры окружающего воздуха. При повышении температуры от –30 °С до +30 °С электрический КПД у турбины снижается на 15–20 %. В отличие от турбины, поршневой двигатель практически не меняет электрический КПД в данном интервале температур.
- Количество пусков: турбину, из-за резких изменений термических напряжений, возникающих в наиболее ответственных узлах и деталях горячего тракта при пусках агрегата из холодного состояния, предпочтительнее использовать для покрытия базовой нагрузки, не предусматривающей остановы и пуски, так как каждый пуск ведет к снижению назначенного ресурса.
- Поршневой двигатель может запускаться и останавливаться неограниченное число раз, что не отражается на его моторесурсе. Поэтому поршневой двигатель лучше приспособлен для покрытия пиковых нагрузок.
- Ресурс до капитального ремонта у турбины — порядка 30 000 рабочих часов (около 4 лет), у поршневого двигателя этот показатель равен 60 000 рабочих часов (около 8 лет).
- Стоимость капитального ремонта турбины с учётом затрат на запчасти и материалы несколько выше, чем ремонт поршневой установки — он требует значительно меньше финансовых и людских ресурсов.
- Капитальный ремонт может проводиться только на специально подготовленном стенде (обычно – на заводе производителе), в отличие от газопоршневого двигателя, который может ремонтироваться на месте.
- Эксплуатационные затраты на ТЭЦ с поршневыми машинами ниже, чем на ТЭЦ с турбинами. Резкие скачки на графике ГТД — капитальные ремонты двигателя. У эксплуатационных затрат ГПД таких скачков нет.
- Строительство ТЭЦ на базе поршневых двигателей электрической мощностью до 15 МВт, как правило, ниже чем на базе турбин. Это связано с более сложной монтажной и технологической частью, требующей применение пара.
www.esist.ru
История изобретения паровой турбины | Великие открытия человечества
Паровая турбина — это тепловой двигатель, тепловая энергия пара в котором преобразуется в механическую работу. Вместе с гидротурбинами огромное значение для развития мировой энергетики имело изобретение и широкое применение паровых турбин, которые являются основным двигателем тепловых (ТЭС) и атомных электростанций (АЭС). Принцип действия паровых турбин схож с гидравлическими, разница лишь в том, что в первом случае турбину приводила в действие струя разогретого пара, во втором — струя воды. Паровая турбина оказалась проще, экономичнее и удобнее, чем паровая машина Уатта. Изобретатели давно пытались создать машину (паровую турбину), где струя пара напрямую бы вращала рабочее колесо. При этом, скорость вращения колеса должна быть очень высокой за счет большой скорости струи пара.
В 1883 году Лавалю удалось создать первую паровую машину, которая представляла легкое колесо с лопатками. Через поставленные под углом сопла на лопатки направляли пар, который давил на них и раскручивал колесо. В 1889 году Лаваль усовершенствовал конструкцию, применив сопло, которое расширялось на выходе. Благодаря этому увеличилась скорость пара и, соответственно, скорость вращения ротора. Полученная струя направлялась на один ряд лопаток, которые были насажены на диск. Давление пара и число сопел определяли мощность турбины, работающей по активному принципу. Если отработанный пар не попадал в воздух, а направлялся в конденсатор, где при пониженном давлении сжижался, то мощность турбины оказывалась наивысшей. Турбина Лаваля получила всеобщее признание, она давала большие выгоды при соединении с машинами, имеющими высокую скорость (сепараторы, пилы, центробежные насосы). Использовали ее и в качестве привода для электрогенератора, правда, только через редуктор (из-за ее высокой скорости).
В 1884 году английский изобретатель Парсонс запатентовал многоступенчатую реактивную турбину, специально созданную им для приведения в действие электрогенератора. При меньшей скорости вращения энергия пара здесь использовалась максимально благодаря тому, что пар, проходя через 15 ступеней, расширялся постепенно. Каждая ступень имела пару венцов лопаток. Неподвижным был один венец с направляющими лопатками, которые крепились на корпусе турбины. Второй — подвижный с рабочими лопатками на диске, который был насажен на вращающийся вал. Лопатки венцов (неподвижных и подвижных) сориентированы в противоположных направлениях. Это была первая паровая турбина, которая начала с успехом применяться в промышленности.
В 1889 году уже 300 турбин применяли для получения электроэнергии, в 1899 году появилась первая электростанция с турбинами Парсонса. В 1894 году был спущен на воду первый пароход «Turbinia» с приводом от паровой турбины. Вскоре паровые турбины начали устанавливать на быстроходных судах. Французский ученый Рато вывел комплексную теорию турбомашин на основе имевшегося опыта. Со временем турбина Парсонса уступила место компактным активно-реактивным турбинам. Хотя и сегодня паровые турбины в основном сохранили черты турбины Парсонса.
mirnovogo.ru
Паровая турбина — доклад
ПАРОВАЯ ТУРБИНА, первичный паровой двигатель с вращательным движением рабочего органа — ротора и непрерывным рабочим процессом; служит для преобразования тепловой энергии пара водяного в механическую работу. Поток водяного пара поступает через направляющие аппараты на криволинейные лопатки, закреплённые по окружности ротора, и, воздействуя на них, приводит ротор во вращение. В отличие от поршневой паровой машины, Паровая турбина использует не потенциальную, а кинетическую энергию пара.
Попытки создать Паровую турбину делались очень давно. Известно описание примитивной Паровой турбины, сделанное Героном Александрийским (1 в. до н. э.). Однако только в кон. 19 в., когда термодинамика, машиностроение и металлургия достигли достаточного уровня, К. Г. П. Лавалъ (Швеция) и Ч. А. Парсоне (Великобритания) независимо друг от друга в 1884-89 создали промышленно пригодные Паровые турбины. Лаваль применил расширение
пара в конических неподвижных соплах в один приём от начального до конечного давления и полученную струю, (со сверхзвуковой скоростью истечения) направил на один ряд рабочих лопаток, насаженных на диск. Паровой турбины, работающие по этому принципу, получили название активных Паровых турбин. Парсонс создал многоступенчатую реактивную Паровую турбину, в к-рой расширение пара осуществлялось в большом числе
последовательно расположенных ступеней не только в каналах неподвижных (направляющих) лопаток, но и между подвижными (рабочими) лопатками. Паровая турбина оказалась очень удобным двигателем для привода ротативных механизмов (генераторы электрического тока, насосы, воздуходувки) и судовых винтов; она была более быстроходной, компактной, лёгкой, экономичной и уравновешенной, чем поршневая паровая машина. Развитие Паровой турбины шло чрезвычайно быстро как в направлении улучшения экономичности и повышения единичной мощности, так и по пути создания
специализированных Паровых турбин различного назначения. Невозможность получить большую агрегатную мощность и очень высокая частота вращения одноступенчатых Паровых турбин. Лаваля (до 30 000 об/мин у первых образцов) привели к тому, что они сохранили своё значение только для привода вспомогательных механизмов. Активные Паровые турбины развивались в направлении создания многоступенчатых конструкций, в к-рых расширение пара осуществлялось в ряде последовательно расположенных ступеней. Это позволило значительно увеличить единичную мощность Паровых турбин, сохранив
умеренную частоту
вращения, необходимую для
Реактивная Паровая турбина Парсонса нек-рое время применялась (в основном на воен. кораблях), но постепенно уступила место более компактным комбинированным активно-реактивным Паровым турбинам, у к-рых реактивная часть высокого давления заменена одно- или двухвенчатым активным диском. В результате уменьшились потери на утечки пара через зазоры в лопаточном аппарате, турбина стала проще и экономичнее.
Классификация паровых турбин. В зависимости от характера теплового процесса Паровые турбины обычно подразделяют на 3 осн. группы: чисто конденсационные, теплофикационные и специального назначения. Чисто конденсационные Паровые турбины служат для превращения максимально возможной части теплоты пара в механич. работу. Эти Паровые турбины работают с выпуском отработавшего пара в конденсатор, где поддерживается вакуум. Чисто конденсационные Паровые турбины могут быть стационарными или транспортными.
Стационарные Паровые турбины в соединении с генераторами переменного электрического тока (турбогенераторы)- осн. оборудование конденсационных электростанций. Чем больше мощность турбогенератора, тем он экономичнее и тем ниже
стоимость 1 кет установленной мощности. Поэтому мощность Паровых турбин растёт из года в год.
Транспортные Паровые турбины используются в качестве главных и вспомогательных двигателей на кораблях и судах. Неоднократно делались попытки применить Паровые турбины на локомотивах, однако паротурбовозы распространения не получили. Для соединения быстроходных Паровых турбин с гребными винтами, требующими невысокой частоты вращения, применяют зубчатые редукторы. В отличие от стационарных Паровых турбин (кроме турбовоздуходувок), судовые Паровые турбины работают с переменной частотой вращения, определяемой необходимой скоростью хода судна.
Теплофикационные Паровые турбины служат для одновременного получения электрической и тепловой энергии. К ним относятся Паровые турбины с противодавлением, с регулируемым отбором пара, а также с отбором и противодавлением.
У Паровых турбин с противодавлением весь отработавший пар используется для технологических целей (варка, сушка, отопление). Электрич. мощность, развиваемая турбоагрегатом с такой Паровой турбиной, зависит от потребности производства или отопит. системы в греющем паре и меняется вместе с ней.
Паровые турбины специального назначения обычно работают на отбросном тепле металлургич., маш.-строит. и хим. предприятий. К ним относятся Паровые турбины мятого пара, двух давлений и предвключённые.
Паровые турбины мятого пара используют отработавший пар поршневых машин, паровых молотов и прессов, имеющий давление
немного выше атмосферного. Паровые турбины двух давлений работают как на свежем, так и на отработавшем паре паровых механизмов, подводимом в одну из промежуточных ступеней.
Предвключённые Паровые турбины представляют
собой турбины с высоким начальным давлением и высоким противодавлением; весь отработавший пар этих Паровых турбин направляют в другие Паровые турбины с более низким начальным давлением пара. Необходимость в предвключённых Паровых турбин возникает при модернизации электростанций, связанной с установкой паровых
котлов более высокого давления, на к-рое не рассчитаны ранее установленные на электростанции Паровых турбин.
Паровые турбины спец. назначения не строят сериями, как конденсационные и теплофикационные Паровые турбины, а в большинстве случаев изготовляют по отд. заказам.
Одноступенчатые активные турбины применяют только для привода быстроходных
вспомогат. механизмов, экономичность к-рых не имеет решающего значения. Хорошая экономичность Паровых турбин, работающей с умеренными окружными скоростями при большом теплопадении, достигается применением ступеней давления.
«Все мои помыслы,– писал Уатт одному из своих друзей,– направлены на паровую машину, я не могу ни о чём другом думать». Признание великого мастера лаконично, но точно определяет главное содержание его жизни, интересов, дел. Уже в раннем детстве, по воспоминаниям тётки, маленький Джемс мог часами заворожённо наблюдать за кипящим чайником, прыгающей крышкой, водяными брызгами и струйками пара. О чём думал мальчуган? Может быть, в эти часы уединений и раздумий закладывались основы личности будущего учёного и инженера? Не будем гадать. Отметим лишь очевидное и главное.
Всю свою долгую
и переполненную событиями
«Уатт оказался нужным человеком, на нужном месте, в нужное время», – написал однажды известный российский исследователь его творчества И.Я. Конфедератов. Случайны или закономерны успех и слава изобретателя? Что это: улыбка фортуны, счастливое стечение обстоятельств или проявление удивительного сплава таланта и трудолюбия? Почему из многочисленных конструкторов и изобретателей теплового двигателя – предшественников и современников Уатта именно он вошёл в историю как создатель паровой машины? Для ответа необходимо обратиться к XVIII веку, той переломной эпохе, которая вошла в историю как «промышленная революция».
Зарождение и развитие паровых машин связано с кризисом средневековой гидроэнергетики (энергетики водяного колеса), достигшей критической черты на рубеже XVII–XVIII вв. В наибольшей степени этот кризис проявился в горнорудном деле.
С развитием производства и ростом потребностей в орудиях труда увеличивались добыча железной руды и выплавка железа. В качестве привода водооткачивающих насосов, дробильных установок, мехов домниц и мо-лотов кузниц на смену биологическим источникам энергии пришло водяное колесо. Выросли производственные возможности агрегатов и их единичные мощности.
Но характер
горнорудного производства делал необходимым
наличие в одном месте
Так энергетика
водяного колеса начинала вступать в
конфликт с вызванными ею же новыми
производственными
Из гидроэнергетической практики был вынесен значительный технический опыт. Разработка элементов привода, передаточных систем, оптимальных конфигураций лопаток водяных колёс закладывала основы конструктивно-технологического знания. Следовательно, наряду с потребностью в новом виде энергии, что вытекало из локальности гидроэнергетики, и возможностью реализации этой потребности, базировавшейся на естественно-научных открытиях XVII в., имелся значительный опыт конструирования различных механизмов. Слияние воедино всех трёх факторов и положило начало развитию теплоэнергетики.
Начальный этап развития паровых двигателей связан с именами таких учёных и изобретателей, как Ворчестер, Лейбниц, Севери, Папен, Дезголье, Леупольд, Ньюкомен, Ползунов, Кюньо, Вастру. Этой плеядой предшественников и современников Уатта были решены многие важные конструкторские проблемы, что позволило создать ряд достаточно работоспособных паровых двигателей. Однако установки первого поколения, преодолевшие локальность энергетики водяного колеса, не отвечали новым условиям, складывывшимся в процессе развития машинно-фабричного производства.
Наиболее ярко
промышленная революция проявилась
в Англии, в текстильном производстве.
Обострившееся до предела несоответствие
между возраставшей потребностью в
тканях и возможностью её удовлетворения
методами ручного мануфактурного производства
обратило конструкторские умы к
разработке прядильных и ткацких
машин. Навсегда в историю английской
цивилизации вошли имена
Заслуги Уатта
в построении паровой машины велики
и разнообразны. Отметим лишь основные
узлы его конструктивно-
Эти и другие
нововведения решили проблему как собственно
универсальности двигателя, так
и резкого повышения его
Для развития поточного
производства машин изобретателем
были разработаны специальные
student.zoomru.ru