- Обмуровка
- Обмуровочно-футеровочные работы
- Профессионально выполняем , обмуровку промышленных, паровых и водогрейных котлов с соблюдением всех технологий
- Обмуровка котлов, паровых, водогрейных, стационарных, обмуровочные, футеровочные работы. ООО «Промприбор плюс» тел.8(3854)437221
- Что такое обмуровка котла
- Конструкция обмуровки
- КАРКАС И ОБМУРОВКА КОТЛОВ — Мегаобучалка
- Ремонт обмуровки котлов — РосТепло Энциклопедия теплоснабжения
Обмуровка
Главная / ОбмуровкаОбмуровка парового и водогрейного котла служит для ограждения топочной камеры и газоходов от окружающей среды. Обмуровка паровых и водогрейных котлов работает при достаточно высоких температурах и резком их изменении, а также под химическим воздействием газов, золы и шлаков.
Конструкция обмуровки должна обеспечивать минимальные потери теплоты в окружающую среду, быть плотной, противостоять длительному воздействию высоких температур, химическому воздействию продуктов сгорания, золы и шлаков, быть механически прочной, легкой, простой, дешевой и доступной для ремонта, способствовать выполнению блочного монтажа парового или водогрейного котла.
Паровые и водогрейные котлы имеют довольно разнообразную по конструкции обмуровку. Однако независимо от конструкции агрегата и его мощности некоторые узлы и элементы являются общими. К ним относятся: стенки, арки, перекрытия, своды, амбразуры, поды, зажигательные пояса, места прохода труб через обмуровку и т. д.
Обмуровку котлов принято условно разделять на тяжелую, облегченную и легкую. Тяжелая обмуровка применялась в парогенераторах старых конструкции и в настоящее время еще применяется в парогенераторах малой мощности (например, парогенераторах ДКВР). В новых конструкциях парогенераторов и водогрейных котлов применяют облегченные и легкие обмуровки. Масса 1 м3 тяжелых обмуровок доходит до 1800 кг, а легких — не превышает 1000 кг.
Разрушение обмуровки прежде всего зависит от температуры, при которой она работает. С увеличением температуры интенсивность разрушения обмуровки возрастает. Чем больше неровностей на обмуровке, обращенной внутрь газохода, и чем толще ее швы, тем больше она изнашивается и истирается. Химическое воздействие шлаков приводит к размягчению, оплавлению н нарушению структуры обмуровки.
Вертикальные стены обмуровки топочной камеры и газоходов могут выполняться из различных материалов: огнеупорного, строительного и теплоизоляционного кирпича, огнеупорных, жароупорных и теплоизоляционных бетонов, температуроустойчивой изоляции и т. д. Обмуровка обычно состоит из двух слоев: внутреннего, обращенного к газоходу, и наружного. Внутренний слой называют футеровкой, а наружный — облицовочным слоем. Футеровка выполняется из огнеупорного материала, а облицовка из материала низкой теплопроводности.
Тяжелая обмуровка опирается на фундамент и имеет высоту не более 8-10 м. Существенное влияние па надежность работы обмуровки оказывает толщина швов между кирпичами. Толщина швов при выполнении кладки из огнеупорного кирпича не должна превышать 3 мм, а из красного кирпича — 5 мм. Для свободного расширения обмуровки (внутренней и наружной) всегда предусматривается устройство горизонтальных и вертикальных температурных швов с таким расчетом, чтобы колонны и каркас не препятствовали свободному расширению облицовочной кладки.
На рис. показаны узлы облегченной обмуровки парогенератора ДЕ-16-14ГМ. Футеровка парогенератора выполнена с применением легковесного шамотного кирпича, огнеупорного бетона, огнеупорной хромомагнезитовой обмазки. В качестве изоляции применен диатомитовый кирпич и асбестовермикулитовые плиты. Снаружи обмуровка обшита металлическим листом.
Огнеупорная футеровка выполнена из шамотобетона, а изоляционный слой — из минераловатных матрацев, на которые нанесена магнезиальная обмазка. Шамотобетон наносится и а металлическую плетеную сетку, которая натягивается на штыри с резьбой на конце. Штыри привариваются к шайбам, которые приварены к экранным трубам.
Минераловатный матрац изготовляют следующим образом. В ящик определенного размера сначала укладывают раскроенную сетку, затем лист крафтбумаги и набивают минеральную вату до плотности примерно 400 кг/м 3. Края сетки подгибают, сверху накладывают еще одну сетку и прошивают матрац скобами. Шаг между скобами около 150 мм. Затяжка скоб должна производиться тщательно во избежание оседания минеральной ваты при эксплуатации. Матрацы прижимаются к шамотобетону квадратными шайбами, надеваемыми на штыри и затягиваемыми гайками. Уплотнительная обмазка наносится на матрацы.
На верхнем рисунке показана одна из конструкций легких обмуровок. Обмуровка выполняется из торкретной массы, закрепленной на металлической сетке. Изоляция осуществлена двумя слоями: слоем жаростойкой изоляции из диатомита и слоем из нескольких асбоцементных плит. Поверх плит на металлическую сетку наносится штукатурка, окрашенная масляной краской в два слоя. Сетка закрепляется на балках поясов жесткости каркаса и на штырях, приваренных к трубам. Обмуровка, показанная на рис., называется натрубной. Для парогенераторов производительностью 50-75 т/ч применяют обмуровку, называемую накаркасной. Пример накаркасной обмуровки для вертикальных стен топочной камеры парогенератора производительностью 75 т/ч показан на рис. Она состоит из слоя огнеупорного кирпича и изоляции, выполненной из диатомитового кирпича и совелитовых плит. Через каждые 2,5-3 м установлены разгрузочные кронштейны, на которые опирается обмуровка. Такая конструкция уменьшает напряжения от собственной массы обмуровки и обеспечивает возможность ремонта любого пояса. Крепление обмуровки производится стяжными крюками, которые с одной стороны зацепляются за трубу, приваренную к обшивке каркаса, а с другой свободно входят в пазы фасонного огнеупорного кирпича. Снаружи накаркасная обмуровка обшита металлическим листом, что обеспечивает необходимую плотность.
При выполнении тяжелых обмуровок широко применяются арки и своды, предназначенные для перекрытия проемов, потолка топочной камеры или газохода.
В сводах под действием собственного веса и теплового расширения возникают распорные усилия. Своды выполняются из специального клинового кирпича и опираются на пяты, выкладываемые из специальных фасонных камней. Иногда кладку свода выполняют по толщине отдельными кольцами. При этом нижний свод является основным, а верхний разгрузочным. В настоящее время широко применяются подвесные своды и перекрытия.
Благодаря отсутствию распирающих усилий подвесные своды могут выполняться из малопрочных материалов. Подвесные своды изготовляются из специального фасонного кирпича, подвешиваемого к металлическим конструкциям каркаса при помощи балок, брусков и подвесок.
Важным узлом обмуровки паровых и водогрейных котлов является амбразура пневмо-механического забрасывателя и горелок.
Уплотнение температурных швов производится шнуровым асбестом несколько большего диаметра, чем ширина шва. Поверхность асбестового шнура, обращенную к топке, промазывают жидким раствором огнеупорной глины или графитом.
Внешняя температура обмуровки не должна превышать температуру окружающего воздуха более чем на 25-30 °С.
Текущее состояние обмуровок котлоагрегатов
В настоящее время в генерирующих компаниях применяется большое количество различных марок котлоагрегатов с устаревшей конструкцией обмуровки, а в некоторых случаях и неремонтопригодной, которая представляет собой щитовые конструкции, разработанные в прошлом веке для котлоагрегатов заводами — изготовителями котлов ТКЗ и ЗиО исключительно под капитальное строительство без учета текущих ремонтов обмуровки.
Во многих генерирующих компаниях текущее состояние обмуровок котлоагрегатов, организация и производство работ по капитальному и текущему ремонту обмуровки приводит (может привести) к следующему:
— производство работ по капитальному и текущему ремонту обмуровки ведется без наличия соответствующей проектно-конструкторской документации и проектов производства работ, что само по себе грубейшее нарушение правил эксплуатации и ремонта котлоагрегатов;
— отсутствие проектно-конструкторской документации и проектов производства работ, как следствие — низкое качество ремонта обмуровки и нарушение планируемых для этого сроков;
— использование давно устаревших и неэффективных, и соответственно трудоемких конструкций обмуровок;
— аварийному состоянию обмуровки и сравнительно низкому КПД котлоагрегата за счет повышенных присосов воздуха в топку;
— ненормативным тепловым потерям после капитального и текущего ремонта;
— производство работ по капитальному и текущему ремонту обмуровки выполняется без соответствующего авторского надзора со стороны проектных организаций;
— выбор материалов и конструкций обмуровки без соответствующего теплового расчета;
— без согласования с проектными и конструкторскими организациями самостоятельно вносятся изменения в заводскую конструкцию обмуровки.
Исходя из выше изложенного, результаты ремонта обмуровки котлоагрегата, как правило, неэффективны и с коротким межремонтным циклом.
Описание современной и эффективной конструкции обмуровки
Предлагается облегченная сборно-разборная конструкция обмуровки котлоагрегатов с применением современных обмуровочных материалов и ремонтопригодной конструкцией обмуровки по ее жаростойкой части.
В жаростойкой части применяются обмуровочные плиты размером 1000х250х50 из корундошпинельного бетона или шамотобетона, весом не более 19 – 25 кг. Конструкция рассчитана и применяется для замены щитовой обмуровки некаркасного типа, а также обмуровки, выполненной кладкой шамотного кирпича. Обмуровочные плиты армированы жаростойкой или теплоустойчивой сталью в зависимости от температуры применения и крепятся на вторичном каркасе котла при помощи опорных полос 5х40 из теплоустойчивой стали.
Один конец полосы приваривается к закладной пластине плиты, другой к уголку, который приварен вертикально внутри обмуровки на каркасе котла. Армировочный каркас плиты имеет две закладные пластины, соответственно к двум пластинам привариваются две опорные полосы, которые также привариваются к двум вертикальным уголкам.
В теплоизоляционной части обмуровки котлоагрегата применяются современные теплоизоляционные плиты из керамического волокна объемным весом не более 200 кг/м3 и муллитокремнеземистый войлок, которые обеспечивают постоянство теплофизических свойств на весь период эксплуатации обмуровки котлоагрегата.
Преимущества предлагаемой конструкции обмуровки
Применение данной конструкции обеспечит общее направление технической политике по ремонту обмуровок котлов, индустриальные методы монтажа обмуровки и приведет к следующему эффекту:
— снижение нагрузок на каркас до 25% по отношению к расчетным;
— снижение потерь тепла за счет увеличения толщины теплоизоляционной части обмуровки до 30 мм для заводской щитовой конструкции (шамотобетон на щитах имеет толщину до 80мм) и до 64мм для кирпичной кладки без изменения заданной толщины обмуровки котлоагрегата;
— снижение присосов воздуха и потерь тепла за счет применения современных теплоизоляционных материалов повышает КПД котлоагрегата;
— достижение необходимого качества, планируемых сроков и производительности работ при капитальных и текущих ремонтах обмуровки;
— повышение надежности и долговечности эксплуатации котлоагрегатов за счет применения современных и эффективных обмуровочных материалов, технических и конструктивных решений;
— и, наконец, снижение стоимости обмуровочных материалов и работ при капитальных и текущих ремонтах обмуровки, в том числе, за счет увеличения межремонтного цикла обмуровки котла и времени простоя в ремонте, и в том числе за счет вторичного использования обмуровочных материалов и унификации обмуровочных конструкций.
shamot.su
Обмуровочно-футеровочные работы
Профессионально выполняем , обмуровку промышленных, паровых и водогрейных котлов с соблюдением всех технологий
. Большой опыт работ компании «ПромАвтоматика» позволяет выполнить обмуровку, футеровку с отменным качеством!
Мы выполняем все виды обмуровок:
- Тяжелую обмуровка паровых котлов
- Облегченную обмуровка котла
- Натрубную обмуровка котлов
- Обмуровка котла из теплоизоляционных плит
ООО «ПромАвтоматика» производит обмуровку котлов ПТВМ. КВ-ГМ , ДКВр, ДЕ, КЕ, Е, ДСЕ, УСШ, КПС .
Все работы по обмуровке котлов выполняются высококлассными специалистами в короткие сроки.
Компания комплектует и поставляет все виды обмуровочно-футеровочных материалов на объект заказчика.
Обмуровка паровых, водогрейных, стационарных котлов по конструкции подразделяется на четыре основных вида:
- 1. Натрубная обмуровка, прикрепляемая непосредственно к поверхностям нагрева котла и выполняемая из жароупорных бетонов (первый слой), теплоизоляционных бетонов или перлитоцементных плит (второй слой) и газонепроницаемой обмазки (третий уплотнительный слой).
- 2. Щитовая обмуровка котлов, прикрепляемая к каркасу котла или каркасу блоков поверхности нагрева и выполняемая в виде щитов или панелей, также состоящих из трех слоев – огнезащитного, теплоизоляционного и уплотнительного. В ряде случаев рационально заменять уплотнительную обмазку обшивкой из стального листа.
- 3. Облегченная обмуровка, прикрепляемая к каркасу котла из штучных огнеупорно-теплоизоляционных изделий. Эта конструкция обмуровки может иметь обшивку из стального листа.
- 4. Натрубная обмуровка в газоплотных котлах, прикрепляемая к газоплотным поверхностям нагрева котла и выполняемая из теплоизоляционных перлитоцементных или известково-кремнеземистых плит (первый теплоизоляционный слой) и газонепроницаемой обмазки (второй уплотнительный слой).
В обмуровках паровых и водогрейных котлов применяют жаростойкий на бетон связующем из глиноземистого цемента или портландцемента. Для теплоизоляционного бетона рименяют диатомовую крошку, асбест V–VI сорта распушенный и связующее – портландцемент. В некоторых случаях в теплоизоляционном бетоне применяют крошку из вспученного перлита вместо диатомовой. Газонепроницаемая (уплотнительная) обмазка состоит, в зависимости от состава, из асбеста Vсорта распушенного, шамотного порошка, огнеупорной глины и связующего – каустического магнезита, жидкого стекла или портландцемента (см. раздел 10).
Для огнеупорной кладки применяют нормальный и легковесный огнеупорный кирпич, а для теплоизоляционной кладки – кирпич плотностью не более 600 кг/м3. Для устройства теплоизоляционного слоя применяют перлитоцементные или известково-кремнеземистые плиты или маты минераловатные прошивные марки 150 (см. раздел 10).
При обмуровке газоплотных котлов для теплоизоляционного слоя, прикрепляемого к панелям, применяют известково-кремнеземистые плиты.
В табл. 9.14. приведена характеристика конструкций обмуровок.
Не допускается смешивание цементов разных видов и марок, а также цементов, выпускаемых разными заводами.
Таблица 9.14. Характеристики конструкций обмуровок
Конструкция обмуровки | Толщина слоя, мм | Общая толщина обмуровки, мм | Масса 1 м2 обмуровки, кг | ||||
Жаростойкий бетон или огнеупорный кирпич |
Теплоизоляционный бетон |
Теплоизоляционный слой | Уплотнительная обмотка | Обшивка | |||
Натрубная | 20–25 | 0–50 | 80–125 | 15–20 | 4 | 115–180 | 95–150 |
Щитовая | 40–80 | 0–126 | 125–150 | 15–20 | 4 | 165–350 | 170–340 |
Облегченная | 113 | 65–195 | 70–100 | — | 4 | 265–415 | 215–400 |
Натрубная газоплотных котлов | — | — | 150 | 15 | 4 | 170 | 95 |
Некоторая часть конструктивных узлов обмуровки котла в процессе эксплуатации разрушается и требует восстановления. Ремонт обмуровки котлов заключается в полной разборке разрушенного участка, подготовке участка и укладке новой обмуровки.
Арматурные и опалубочные работы
Арматура, стальная сетка, детали крепления обмуровки перед установкой очищают от грязи, пленочной коррозии, налипшего раствора и т. п. Пересечение проволоки арматуры сваривают электросваркой или перевязывают вязальной проволокой диаметром 1,6–2 мм. Перевязка арматуры медной или алюминиевой проволокой не допускается.
Детали крепления обмуровки и арматуру диаметром более 8 мм, находящиеся в жароупорном и теплоизоляционном бетонах, покрывают слоем битума толщиной до 2 мм. Сетку для армирования жароупорного бетона натрубной обмуровки и сетку для армирования уплотнительной обмазки натягивают без слабины и провисания и крепят крючками с шагом не более 1 × 1 м.
Деревянную опалубку изготавливают из хвойных пород дерева (кроме лиственницы), из пиломатериала толщиной 20–30 мм. Поверхность, соприкасающуюся с укладываемым бетоном, остругивают. Вторично используемая опалубка должна быть очищена от грязи и застывшего бетона.
Для заделки щелей в опалубке с целью предотвращения вытекания цементного молока разрешается применять пластичную глину или плотную бумагу. При укладке бетона в конструкции обмуровки, расположенные вертикально или под углом более 40° к горизонтальной плоскости, применяют двойную опалубку. В этом случае наружную стенку опалубки передвигают по мере укладки бетона. При возможности в качестве внутренней стенки опалубки нужно использовать не разобранный слой обмуровки.
Опалубку для выполнения отверстий диаметром до 200 мм изготавливают из круглого лесоматериала, для больших диаметров делают опалубку из узких досок или из фанеры. Для предотвращения сцепления бетона с опалубкой внутреннюю ее поверхность покрывают смазкой, состоящей из 12 частей минерального масла, 1 части цемента и 0,5 части воды. Можно применять отработанное минеральное масло. Применять для смазки опалубки известковые растворы нельзя.
Приготовление и укладка набивных масс на поверхности экранов
Для укладки на экранные поверхности котлов применяют набивные массы: хромитовые, хромитомагнезитовые, карборундовые и корундовые.
В карборундовых массах в качестве связующего применяют жидкое стекло, шликер огнеупорной глины, триполифосфат натрия и алюмофосфатное связующее на основе ортофосфорной кислоты.
Наилучшие эксплуатационные свойства имеет карборундовая масса на фосфатном связующем.
Составы и свойства набивных масс приведены в табл. 9.15.
Таблица 9.15. Составы и свойства набивных масс.
Наименование массы | Состав массы | Максимальная температура применения, оС | Плотность, кг/м3 | Коэффициент линейного расширения (при температуре 20 – 800оС) | Коэффициент теплопроводности (при температуре 300 – 700оС), Вт/ м×оС |
1 | 2 | 3 | 4 | 5 | 6 |
Хромитовая | Хромитовая смесь СХ-1 или СХ-2, жидкое стекло плотностью 1,4 – 1,5 г/см3, 7% к хромитовой смеси | 1350 | 2500 – 3200 | (7,0 – 8,0)×10– 6 | 1,1 – 1,3 |
Карборундовая | Карбид кремния черный № 160-63 – 40%, № 50-12 – 30%, шлам карбид кремния – 30%, связка сверх 100%: жидкое стекло плотностью 1,3 г/см3 – 6%, водная суспензия огнеупорной глины плотностью 1,13 г/см3 – 5% | 1500 | 2100 – 2300 | 5,5×10– 6 | 4,0 – 4,5 |
Карборундовая на фосфатном связующем | Карбид кремния черный № 160-63 – 40%, № 50-12 – 30%, шлам карбид кремния – 30%, связка сверх 100%: алюмофосфатное связующее – 18%, огнеупорная глина – 6% | 1700 | 2100 – 2300 | 8,9×10– 6 | 2,0 – 3,0 |
Карборундовая на фосфатном связующем | Карбид кремния черный № 160-63 – 40%, № 50-12 – 30%, шлам карбид кремния – 30%, связка сверх 100%: огнеупорная глина – 5%, триполифосфат – 3% | 1600 | 2300 – 2500 | 5,5×10– 6 | 5,5 – 7,2 |
Карборундовая на фосфатном связующем | Карбид кремния черный № 160-63 – 40%, № 50-12 – 30%, шлам карбид кремния – 30%, связка сверх 100%: ортофосфорная кислота – 15%, электрокорунд – 10%, огнеупорная глина – 6% | 1500 | 2100 – 2300 | 4,1×10– 6 | 4,0 – 6,0 |
Корундовая на алюмофосфатном связующем | Корунд № 400-100 –25%, огнеупорная глина – 25 – 35%; связка сверх 100%: ортофосфорная кислота 75-процентная – 15% | 1650 | 2100 – 2400 | 7,6×10– 6 | 0,8 – 1,2 |
Хромомагнезитовая | Хромомагнезит зернового состава: зерно от 7 до 3 мм – 40%, от 1 до 0,09 мм – 30%, меньше 0,09 мм – 30%; связка сверх 100%: жидкое стекло плотностью 1,4 – 1,5 г/см3 – 10%, кремнефтористый натрий – 1%, огнеупорная глина – 6% | 1500 | 2600 – 2800 | 10,3×10– 6 | 1,0 – 1,5 |
Составы и свойства жаростойких бетонов приведены в разделе 10.
Перед приготовлением набивных масс необходимо:
- — жидкое стекло разбавить водой и довести до заданной плотности;
- — огнеупорную глину высушить, размолоть и просеять через сито с отверстиями не более 1 мм;
- — растворить огнеупорную глину в воде;
- — плотность глиняной суспензии должна составлять 1,13–1,15 г/см3.
Разрешается приготовление карборунда мелкого зернового состава путем размола более крупных зерен в шаровых мельницах со стальными мелющими телами.
Массы приготавливают в лопастных смесителях. Сухие компоненты засыпают в смеситель и перемешивают 3 мин, затем без остановки смесителя загружают жидкие компоненты в любой последовательности. После загрузки в смеситель всех компонентов массу перемешивают 10 мин.
Приготовленные набивные массы, особенно хромитовая и карборундовая, употребляются в дело в течение 1,5 ч с момента приготовления. Для предохранения от высыхания и твердения массы следует хранить в закрытых емкостях. Повторное применение схватившейся массы не допускается.
Перед укладкой набивных масс ошипованные и гладкие экранные трубы, камеры и другие стальные поверхности должны быть пропескоструены. На зажигательных поясах массу набрасывают на ошипованные трубы сразу достаточно большой площадью и набивают таким образом, чтобы слой уплотненной массы над шипами составлял 3–5 мм. Необходимо учитывать, что набивка массы в несколько слоев с некоторыми промежутками времени вызывает ее расслоение.
Массу уплотняют пневмомолотками через стальную плиту размером 200×200 мм, толщиной 12–15 мм. Массу набивают плотно, без пустот между трубами и шипами. Степень уплотнения проверяют нажатием большого пальца руки с усилием 10–15 кг. При этом на поверхности массы не должен остаться заметный след.
При укладке массы на под котлов с жидким шлакоудалением, амбразуры горелок и т. п. рекомендуется массы укладывать слоями толщиной не более 100 мм. Массу уплотняют пневмолопатками или вручную деревянными трамбовками. При необходимости укладки второго слоя поверхность ранее уложенного слоя нарезают квадратами 80×80 мм на глубину 7–8 мм. Укладку масс, особенно при большой толщине слоя, желательно выполнять без перерыва. Целесообразно высушивать массу сразу же после укладки, пропуская через экраны горячую воду с температурой 60 °С.
Приготовление и нанесение уплотнительных обмазок
Уплотнительные обмазки приготавливают в смесителе принудительного действия. В смеситель засыпают сухие компоненты и затем при работающем смесителе заливают в любой последовательности жидкие компоненты. Компоненты обмазки перемешивают 8–10 мин до получения однородной массы. Уплотнительные обмазки готовят в количестве, которое может быть уложено в дело в течение 1 ч после приготовления. Затвердевшие обмазки применять не разрешается.
Перед нанесением обмазки сетку очищают от грязи и проверяют надежность ее закрепления. Обмазку набрасывают на сетку небольшими порциями, хорошо уплотняют деревянными трамбовками и заглаживают мастерком или полутеркой. При необходимости густота раствора может быть уменьшена прибавлением раствора хлористого магния с тщательным перемешиванием. Применение воды для уменьшения густоты раствора не разрешается. Нельзя увлажнять уплотнительные обмазки в процессе твердения.
В табл. 9.16. приводятся составы обмазок и мастик.
Таблица 9.16. Составы обмазок и мастик
Наименование | Состав и расход на 1 м3 | Область применения | |
Материалы | Количество | ||
1 | 2 | 3 | 4 |
Уплотнительная магнезиальная обмазка | Каустический магнезит II класса | 300 кг | Наружный уплотнительный слой обмуровок без металлической обшивки |
Асбест распушенный V–VI сорта | 800 кг | ||
Раствор хлористого магния плотностью 1,2 г/см3 | 450 л | ||
Уплотнительная обмазка ОРГРЭС |
Портландцемент марки 300 |
70 кг | Наружный уплотнительный слой обмуровок без металлической обшивки |
Глина огнеупорная | 210 кг | ||
Шамотный порошок, зерно до 2 мм | 560 кг | ||
Асбест распушенный V–VI сорта | 560 кг | ||
Жидкое стекло плотностью 1,4–1,5 г/см3 | 150 кг | ||
Уплотнительная асбестодиато-мовая обмазка |
Диатомовая крошка, размер зерна до 5 мм |
360 кг | Уплотнение кладки из шамотного кирпича. Предельная температура применения 800°С |
Асбест распушенный V–VI сорта | 300 кг | ||
Жидкое стекло плотностью 1,38–1,40 г/см3 | 120 кг | ||
Огнеупорный кладочный раствор | Мертель алюмосиликатный | 1370 кг | Кладка из огнеупорного кирпича |
Вода | 450–550 л | ||
Диатомо-цементный кладочный раствор |
Диатомит молотый |
520 кг | Кладка из диатомового кирпича в местах, предусмотренных проектом. Кладка из диатомового кирпича, в основном выполняется «всухую». |
Портландцемент марки 400 | 180 кг | ||
Вода | 450–550 л | ||
Мастика для подмазки и промазки швов перлитовая | Состав по массе | Для подмазки и промазки швов в перлитоцементных изделиях | |
Перлитовый песок, размер зерна до 1,5 мм | 20% | ||
Асбест V сорта | 20% | ||
Жидкое стекло плотностью 1,40 г/см3 | 57% | ||
Кремнефтористый натрий Вода |
3% В количестве, соответствующем погружению конуса в раствор на 10–12 см |
||
Мастика для промазки швов в известково-кремнеземистых изделиях № 2 |
Жидкое стекло натриевое плотностью 1,40–1,43 г/см3 |
1 часть | — — — |
Диатомит молотый, зерно до 1,5 мм | 0,4 части | ||
Глина огнеупорная молотая | 0,04 части |
Дополнительные сведения о составах защитных и уплотнительных обмазок приведены в разделе 10.5.2.
Ремонт обмуровки из штучных огнеупорных и теплоизоляционных изделий
Классификация огнеупорных растворов по консистенции для кладки из шамотного кирпича приведена в табл. 9.17. Более подробно составы огнеупорных растворов, твердеющих при нагревании, и составы воздушно-твердеющих шамотных растворов, как и способы их приготовления, приведены в разделе 10.5.2.
Таблица 9.17. Классификация огнеупорных растворов (консистенция растворов)
Раствор | Тонкость помола мертеля | Пределы осадки конуса, см | Толщина шва, мм, не более |
Жидкий Полугустой Густой |
Тонкий Крупный Крупный |
6–9 5–6 3–5 |
1–2 3 5 |
Разборку разрушенного или разбираемого с целью ремонта участка кладки обмуровки следует выполнять с учетом максимального сохранения изделий для вторичного использования при условии лабораторных испытаний (шамотные изделия). Для уменьшения пыления участки разбираемой кладки увлажняют. Все оголенные элементы крепления кладки очищают от остатков раствора и соответствующим образом ремонтируют.
Сопряжение новой кладки с неразбираемым участком следует выполнять перевязкой по штробе, выполненной «с убегом». Толщина кладки, способ укладки кирпича должны быть такими же, как это было предусмотрено заводской конструкцией. Кладку огнеупорного кирпича начинают с углов и ведут к середине. При кладке подов котлов с жидким шлакоудалением верхний ряд огнеупорного кирпича укладывают на ребро поперек движения шлака.
Неровности и искривления (в переделах допусков) металлоконструкций, обшивки пода и экранных труб, на которые опирается кладка, следует выравнивать теплоизоляционным слоем с тем, чтобы обеспечить ровную поверхность под кладку из огнеупорного кирпича.
Кладку амбразур горелок производят с обязательной предварительной подгонкой фасонного или клинового кирпича. Толщина шва не более 1 мм. Технологические отверстия (лазы, лючки и др.) должны выполняться огнеупорным кирпичом на всю толщину обмуровки. Кладку в местах прохода труб через обмуровку и в местах подвижных опор и креплений экранных труб следует выполнять особо тщательно, не допуская защемления указанных узлов в обмуровке. Манжеты в местах прохода труб через обмуровку перед укладкой бетона должны быть надежно закреплены на трубах.
Длина манжет должна быть на 40 мм больше толщины слоя бетона. При кладке мест сопряжения обмуровки вертикальной стены с потолком должен быть выполнен температурный зазор 20 мм.
Укладку теплоизоляционных известково-кремнеземистых или перлитоцементных плит производят насухо с зазором между плитами не более 3 мм с перекрытием швов на ширину не менее 50 мм. В теплоизоляционном слое не должно быть пустот. Разрешается заделывать пустоты кусками теплоизоляционных плит.
Зазор между наружной поверхностью теплоизоляционного слоя и металлической обшивкой котла должен соответствовать проектным данным. Зазор проверяют при восстановлении металлической обшивки контрольной рейкой.
При выполнении теплоизоляционного слоя из матов минераловатных с обкладкой металлической сеткой необходимо сшивать края сеток матов мягкой углеродистой проволокой. Пустоты в местах стыков матов заделывают минеральной ватой. Поверхность изоляционного слоя должна быть ровной.
Допускаемые отклонения от проектных размеров при выполнении обмуровки не должны превышать данных, приведенных в табл. 9.18.
Таблица 9.18. Допускаемые отклонения от проектных размеров при выполнении обмуровки
Наименование | Допускаемые отклонения от проектных размеров , мм |
Расстояние между осями экранных труб и обмуровкой Расстояние между осями крайних труб змеевиков пароперегревателей, экономайзеров и обмуровкой Ширина температурного шва Впадины, выпучины, выступающие кирпичи на поверхности обмуровки на длине 1 м То же для наружной поверхности на длине 1 м |
± 10 ± 10 ± 5 ± 3 ± 4 |
promplus.ru
Обмуровка котлов, паровых, водогрейных, стационарных, обмуровочные, футеровочные работы. ООО «Промприбор плюс» тел.8(3854)437221
Компания ООО «Промприборплюс», имеющая огромный опыт, профессионально выполнит , обмуровку промышленных, паровых и водогрейных котлов с соблюдением всех технологий .
Мы выполняем все виды обмуровок:
- Тяжелую обмуровка паровых котлов
- Облегченную обмуровка котла
- Натрубную обмуровка котлов
- Обмуровка котла из теплоизоляционных плит
ООО «Промприборплюс» производит обмуровку котлов ПТВМ. КВ-ГМ , ДКВр, ДЕ, КЕ, Е, ДСЕ, УСШ, КПС .
Все работы по обмуровке котлов выполняются высококлассными специалистами в короткие сроки.
Компания комплектует и поставляет все виды обмуровочно-футеровочных материалов на объект заказчика.
Обмуровка паровых, водогрейных, стационарных котлов по конструкции подразделяется на четыре основных вида:
1. Натрубная обмуровка, прикрепляемая непосредственно к поверхностям нагрева котла и выполняемая из жароупорных бетонов (первый слой), теплоизоляционных бетонов или перлитоцементных плит (второй слой) и газонепроницаемой обмазки (третий уплотнительный слой).
2. Щитовая обмуровка котлов, прикрепляемая к каркасу котла или каркасу блоков поверхности нагрева и выполняемая в виде щитов или панелей, также состоящих из трех слоев – огнезащитного, теплоизоляционного и уплотнительного. В ряде случаев рационально заменять уплотнительную обмазку обшивкой из стального листа.
3. Облегченная обмуровка, прикрепляемая к каркасу котла из штучных огнеупорно-теплоизоляционных изделий. Эта конструкция обмуровки может иметь обшивку из стального листа.
4. Натрубная обмуровка в газоплотных котлах, прикрепляемая к газоплотным поверхностям нагрева котла и выполняемая из теплоизоляционных перлитоцементных или известково-кремнеземистых плит (первый теплоизоляционный слой) и газонепроницаемой обмазки (второй уплотнительный слой).
В обмуровках паровых и водогрейных котлов применяют жаростойкий на бетон связующем из глиноземистого цемента или портландцемента. Для теплоизоляционного бетона рименяют диатомовую крошку, асбест V–VI сорта распушенный и связующее – портландцемент. В некоторых случаях в теплоизоляционном бетоне применяют крошку из вспученного перлита вместо диатомовой. Газонепроницаемая (уплотнительная) обмазка состоит, в зависимости от состава, из асбеста Vсорта распушенного, шамотного порошка, огнеупорной глины и связующего – каустического магнезита, жидкого стекла или портландцемента (см. раздел 10).
Для огнеупорной кладки применяют нормальный и легковесный огнеупорный кирпич, а для теплоизоляционной кладки – кирпич плотностью не более 600 кг/м3. Для устройства теплоизоляционного слоя применяют перлитоцементные или известково-кремнеземистые плиты или маты минераловатные прошивные марки 150 (см. раздел 10).
При обмуровке газоплотных котлов для теплоизоляционного слоя, прикрепляемого к панелям, применяют известково-кремнеземистые плиты.
В табл. 9.14. приведена характеристика конструкций обмуровок.
Не допускается смешивание цементов разных видов и марок, а также цементов, выпускаемых разными заводами.
Таблица 9.14. Характеристики конструкций обмуровок
Конструкция обмуровки | Толщина слоя, мм | Общая толщина обмуровки, мм | Масса 1 м2 обмуровки, кг | ||||
Жаростойкий бетон или огнеупорный кирпич |
Теплоизоляционный бетон |
Теплоизоляционный слой | Уплотнительная обмотка | Обшивка | |||
Натрубная | 20–25 | 0–50 | 80–125 | 15–20 | 4 | 115–180 | 95–150 |
Щитовая | 40–80 | 0–126 | 125–150 | 15–20 | 4 | 165–350 | 170–340 |
Облегченная | 113 | 65–195 | 70–100 | — | 4 | 265–415 | 215–400 |
Натрубная газоплотных котлов | — | — | 150 | 15 | 4 | 170 | 95 |
Некоторая часть конструктивных узлов обмуровки котла в процессе эксплуатации разрушается и требует восстановления. Ремонт обмуровки котлов заключается в полной разборке разрушенного участка, подготовке участка и укладке новой обмуровки.
Арматурные и опалубочные работы
Арматура, стальная сетка, детали крепления обмуровки перед установкой очищают от грязи, пленочной коррозии, налипшего раствора и т. п. Пересечение проволоки арматуры сваривают электросваркой или перевязывают вязальной проволокой диаметром 1,6–2 мм. Перевязка арматуры медной или алюминиевой проволокой не допускается.
Детали крепления обмуровки и арматуру диаметром более 8 мм, находящиеся в жароупорном и теплоизоляционном бетонах, покрывают слоем битума толщиной до 2 мм. Сетку для армирования жароупорного бетона натрубной обмуровки и сетку для армирования уплотнительной обмазки натягивают без слабины и провисания и крепят крючками с шагом не более 1 × 1 м.
Деревянную опалубку изготавливают из хвойных пород дерева (кроме лиственницы), из пиломатериала толщиной 20–30 мм. Поверхность, соприкасающуюся с укладываемым бетоном, остругивают. Вторично используемая опалубка должна быть очищена от грязи и застывшего бетона.
Для заделки щелей в опалубке с целью предотвращения вытекания цементного молока разрешается применять пластичную глину или плотную бумагу. При укладке бетона в конструкции обмуровки, расположенные вертикально или под углом более 40° к горизонтальной плоскости, применяют двойную опалубку. В этом случае наружную стенку опалубки передвигают по мере укладки бетона. При возможности в качестве внутренней стенки опалубки нужно использовать не разобранный слой обмуровки.
Опалубку для выполнения отверстий диаметром до 200 мм изготавливают из круглого лесоматериала, для больших диаметров делают опалубку из узких досок или из фанеры. Для предотвращения сцепления бетона с опалубкой внутреннюю ее поверхность покрывают смазкой, состоящей из 12 частей минерального масла, 1 части цемента и 0,5 части воды. Можно применять отработанное минеральное масло. Применять для смазки опалубки известковые растворы нельзя.
Приготовление и укладка набивных масс на поверхности экранов
Для укладки на экранные поверхности котлов применяют набивные массы: хромитовые, хромитомагнезитовые, карборундовые и корундовые.
В карборундовых массах в качестве связующего применяют жидкое стекло, шликер огнеупорной глины, триполифосфат натрия и алюмофосфатное связующее на основе ортофосфорной кислоты.
Наилучшие эксплуатационные свойства имеет карборундовая масса на фосфатном связующем.
Составы и свойства набивных масс приведены в табл. 9.15.
Таблица 9.15. Составы и свойства набивных масс.
Наименование массы | Состав массы | Максимальная температура применения, оС | Плотность, кг/м3 | Коэффициент линейного расширения (при температуре 20 – 800оС) | Коэффициент теплопроводности (при температуре 300 – 700оС), Вт/ м×оС |
1 | 2 | 3 | 4 | 5 | 6 |
Хромитовая | Хромитовая смесь СХ-1 или СХ-2, жидкое стекло плотностью 1,4 – 1,5 г/см3, 7% к хромитовой смеси | 1350 | 2500 – 3200 | (7,0 – 8,0)×10– 6 | 1,1 – 1,3 |
Карборундовая | Карбид кремния черный № 160-63 – 40%, № 50-12 – 30%, шлам карбид кремния – 30%, связка сверх 100%: жидкое стекло плотностью 1,3 г/см3 – 6%, водная суспензия огнеупорной глины плотностью 1,13 г/см3 – 5% | 1500 | 2100 – 2300 | 5,5×10– 6 | 4,0 – 4,5 |
Карборундовая на фосфатном связующем | Карбид кремния черный № 160-63 – 40%, № 50-12 – 30%, шлам карбид кремния – 30%, связка сверх 100%: алюмофосфатное связующее – 18%, огнеупорная глина – 6% | 1700 | 2100 – 2300 | 8,9×10– 6 | 2,0 – 3,0 |
Карборундовая на фосфатном связующем | Карбид кремния черный № 160-63 – 40%, № 50-12 – 30%, шлам карбид кремния – 30%, связка сверх 100%: огнеупорная глина – 5%, триполифосфат – 3% | 1600 | 2300 – 2500 | 5,5×10– 6 | 5,5 – 7,2 |
Карборундовая на фосфатном связующем | Карбид кремния черный № 160-63 – 40%, № 50-12 – 30%, шлам карбид кремния – 30%, связка сверх 100%: ортофосфорная кислота – 15%, электрокорунд – 10%, огнеупорная глина – 6% | 1500 | 2100 – 2300 | 4,1×10– 6 | 4,0 – 6,0 |
Корундовая на алюмофосфатном связующем | Корунд № 400-100 –25%, огнеупорная глина – 25 – 35%; связка сверх 100%: ортофосфорная кислота 75-процентная – 15% | 1650 | 2100 – 2400 | 7,6×10– 6 | 0,8 – 1,2 |
Хромомагнезитовая | Хромомагнезит зернового состава: зерно от 7 до 3 мм – 40%, от 1 до 0,09 мм – 30%, меньше 0,09 мм – 30%; связка сверх 100%: жидкое стекло плотностью 1,4 – 1,5 г/см3 – 10%, кремнефтористый натрий – 1%, огнеупорная глина – 6% | 1500 | 2600 – 2800 | 10,3×10– 6 | 1,0 – 1,5 |
Составы и свойства жаростойких бетонов приведены в разделе 10.
Перед приготовлением набивных масс необходимо:
- — жидкое стекло разбавить водой и довести до заданной плотности;
- — огнеупорную глину высушить, размолоть и просеять через сито с отверстиями не более 1 мм;
- — растворить огнеупорную глину в воде;
- — плотность глиняной суспензии должна составлять 1,13–1,15 г/см3.
Разрешается приготовление карборунда мелкого зернового состава путем размола более крупных зерен в шаровых мельницах со стальными мелющими телами.
Массы приготавливают в лопастных смесителях. Сухие компоненты засыпают в смеситель и перемешивают 3 мин, затем без остановки смесителя загружают жидкие компоненты в любой последовательности. После загрузки в смеситель всех компонентов массу перемешивают 10 мин.
Приготовленные набивные массы, особенно хромитовая и карборундовая, употребляются в дело в течение 1,5 ч с момента приготовления. Для предохранения от высыхания и твердения массы следует хранить в закрытых емкостях. Повторное применение схватившейся массы не допускается.
Перед укладкой набивных масс ошипованные и гладкие экранные трубы, камеры и другие стальные поверхности должны быть пропескоструены. На зажигательных поясах массу набрасывают на ошипованные трубы сразу достаточно большой площадью и набивают таким образом, чтобы слой уплотненной массы над шипами составлял 3–5 мм. Необходимо учитывать, что набивка массы в несколько слоев с некоторыми промежутками времени вызывает ее расслоение.
Массу уплотняют пневмомолотками через стальную плиту размером 200×200 мм, толщиной 12–15 мм. Массу набивают плотно, без пустот между трубами и шипами. Степень уплотнения проверяют нажатием большого пальца руки с усилием 10–15 кг. При этом на поверхности массы не должен остаться заметный след.
При укладке массы на под котлов с жидким шлакоудалением, амбразуры горелок и т. п. рекомендуется массы укладывать слоями толщиной не более 100 мм. Массу уплотняют пневмолопатками или вручную деревянными трамбовками. При необходимости укладки второго слоя поверхность ранее уложенного слоя нарезают квадратами 80×80 мм на глубину 7–8 мм. Укладку масс, особенно при большой толщине слоя, желательно выполнять без перерыва. Целесообразно высушивать массу сразу же после укладки, пропуская через экраны горячую воду с температурой 60 °С.
Приготовление и нанесение уплотнительных обмазок
Уплотнительные обмазки приготавливают в смесителе принудительного действия. В смеситель засыпают сухие компоненты и затем при работающем смесителе заливают в любой последовательности жидкие компоненты. Компоненты обмазки перемешивают 8–10 мин до получения однородной массы. Уплотнительные обмазки готовят в количестве, которое может быть уложено в дело в течение 1 ч после приготовления. Затвердевшие обмазки применять не разрешается.
Перед нанесением обмазки сетку очищают от грязи и проверяют надежность ее закрепления. Обмазку набрасывают на сетку небольшими порциями, хорошо уплотняют деревянными трамбовками и заглаживают мастерком или полутеркой. При необходимости густота раствора может быть уменьшена прибавлением раствора хлористого магния с тщательным перемешиванием. Применение воды для уменьшения густоты раствора не разрешается. Нельзя увлажнять уплотнительные обмазки в процессе твердения.
В табл. 9.16. приводятся составы обмазок и мастик.
Таблица 9.16. Составы обмазок и мастик
Наименование | Состав и расход на 1 м3 | Область применения | |
Материалы | Количество | ||
1 | 2 | 3 | 4 |
Уплотнительная магнезиальная обмазка | Каустический магнезит II класса | 300 кг | Наружный уплотнительный слой обмуровок без металлической обшивки |
Асбест распушенный V–VI сорта | 800 кг | ||
Раствор хлористого магния плотностью 1,2 г/см3 | 450 л | ||
Уплотнительная обмазка ОРГРЭС |
Портландцемент марки 300 |
70 кг | Наружный уплотнительный слой обмуровок без металлической обшивки |
Глина огнеупорная | 210 кг | ||
Шамотный порошок, зерно до 2 мм | 560 кг | ||
Асбест распушенный V–VI сорта | 560 кг | ||
Жидкое стекло плотностью 1,4–1,5 г/см3 | 150 кг | ||
Уплотнительная асбестодиато-мовая обмазка |
Диатомовая крошка, размер зерна до 5 мм |
360 кг | Уплотнение кладки из шамотного кирпича. Предельная температура применения 800°С |
Асбест распушенный V–VI сорта | 300 кг | ||
Жидкое стекло плотностью 1,38–1,40 г/см3 | 120 кг | ||
Огнеупорный кладочный раствор | Мертель алюмосиликатный | 1370 кг | Кладка из огнеупорного кирпича |
Вода | 450–550 л | ||
Диатомо-цементный кладочный раствор |
Диатомит молотый |
520 кг | Кладка из диатомового кирпича в местах, предусмотренных проектом. Кладка из диатомового кирпича, в основном выполняется «всухую». |
Портландцемент марки 400 | 180 кг | ||
Вода | 450–550 л | ||
Мастика для подмазки и промазки швов перлитовая | Состав по массе | Для подмазки и промазки швов в перлитоцементных изделиях | |
Перлитовый песок, размер зерна до 1,5 мм | 20% | ||
Асбест V сорта | 20% | ||
Жидкое стекло плотностью 1,40 г/см3 | 57% | ||
Кремнефтористый натрий Вода |
3% В количестве, соответствующем погружению конуса в раствор на 10–12 см |
||
Мастика для промазки швов в известково-кремнеземистых изделиях № 2 |
Жидкое стекло натриевое плотностью 1,40–1,43 г/см3 |
1 часть | — — — |
Диатомит молотый, зерно до 1,5 мм | 0,4 части | ||
Глина огнеупорная молотая | 0,04 части |
Дополнительные сведения о составах защитных и уплотнительных обмазок приведены в разделе 10.5.2.
Ремонт обмуровки из штучных огнеупорных и теплоизоляционных изделий
Классификация огнеупорных растворов по консистенции для кладки из шамотного кирпича приведена в табл. 9.17. Более подробно составы огнеупорных растворов, твердеющих при нагревании, и составы воздушно-твердеющих шамотных растворов, как и способы их приготовления, приведены в разделе 10.5.2.
Таблица 9.17. Классификация огнеупорных растворов (консистенция растворов)
Раствор | Тонкость помола мертеля | Пределы осадки конуса, см | Толщина шва, мм, не более |
Жидкий Полугустой Густой |
Тонкий Крупный Крупный |
6–9 5–6 3–5 |
1–2 3 5 |
Разборку разрушенного или разбираемого с целью ремонта участка кладки обмуровки следует выполнять с учетом максимального сохранения изделий для вторичного использования при условии лабораторных испытаний (шамотные изделия). Для уменьшения пыления участки разбираемой кладки увлажняют. Все оголенные элементы крепления кладки очищают от остатков раствора и соответствующим образом ремонтируют.
Сопряжение новой кладки с неразбираемым участком следует выполнять перевязкой по штробе, выполненной «с убегом». Толщина кладки, способ укладки кирпича должны быть такими же, как это было предусмотрено заводской конструкцией. Кладку огнеупорного кирпича начинают с углов и ведут к середине. При кладке подов котлов с жидким шлакоудалением верхний ряд огнеупорного кирпича укладывают на ребро поперек движения шлака.
Неровности и искривления (в переделах допусков) металлоконструкций, обшивки пода и экранных труб, на которые опирается кладка, следует выравнивать теплоизоляционным слоем с тем, чтобы обеспечить ровную поверхность под кладку из огнеупорного кирпича.
Кладку амбразур горелок производят с обязательной предварительной подгонкой фасонного или клинового кирпича. Толщина шва не более 1 мм. Технологические отверстия (лазы, лючки и др.) должны выполняться огнеупорным кирпичом на всю толщину обмуровки. Кладку в местах прохода труб через обмуровку и в местах подвижных опор и креплений экранных труб следует выполнять особо тщательно, не допуская защемления указанных узлов в обмуровке. Манжеты в местах прохода труб через обмуровку перед укладкой бетона должны быть надежно закреплены на трубах.
Длина манжет должна быть на 40 мм больше толщины слоя бетона. При кладке мест сопряжения обмуровки вертикальной стены с потолком должен быть выполнен температурный зазор 20 мм.
Укладку теплоизоляционных известково-кремнеземистых или перлитоцементных плит производят насухо с зазором между плитами не более 3 мм с перекрытием швов на ширину не менее 50 мм. В теплоизоляционном слое не должно быть пустот. Разрешается заделывать пустоты кусками теплоизоляционных плит.
Зазор между наружной поверхностью теплоизоляционного слоя и металлической обшивкой котла должен соответствовать проектным данным. Зазор проверяют при восстановлении металлической обшивки контрольной рейкой.
При выполнении теплоизоляционного слоя из матов минераловатных с обкладкой металлической сеткой необходимо сшивать края сеток матов мягкой углеродистой проволокой. Пустоты в местах стыков матов заделывают минеральной ватой. Поверхность изоляционного слоя должна быть ровной.
Допускаемые отклонения от проектных размеров при выполнении обмуровки не должны превышать данных, приведенных в табл. 9.18. Таблица 9.18. Допускаемые отклонения от проектных размеров при выполнении обмуровки
Наименование | Допускаемые отклонения от проектных размеров , мм |
Расстояние между осями экранных труб и обмуровкой Расстояние между осями крайних труб змеевиков пароперегревателей, экономайзеров и обмуровкой Ширина температурного шва Впадины, выпучины, выступающие кирпичи на поверхности обмуровки на длине 1 м То же для наружной поверхности на длине 1 м |
± 10 ± 10 ± 5 ± 3 ± 4 |
prompriborplus.ru
Что такое обмуровка котла
Котлы, используемые в крупных отопительных системах, как правило, выпускаются без экранизирующего покрытия. Это вызвано тем, что они изготавливаются в соответствии с параметрами котельной. Обмуровка котла выполняет функции защитного покрытия и производится из материалов, обеспечивающих необходимые характеристики.
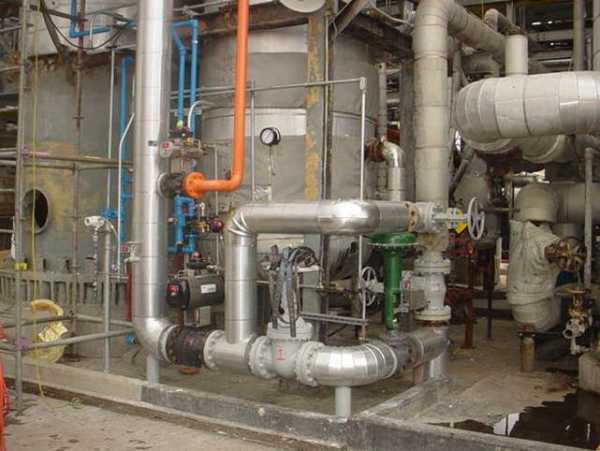
Разновидности
Главным предназначением защитного слоя является уменьшение уровня теплопотерь и риска ожогов у работников, также снижаются расходы на энергоноситель. Особое значение уделяется материалам, используемым при создании обмуровки, и технологии формирования. Существует несколько основных схем, каждая из которых подбирается индивидуально и обладает высоким уровнем эффективности:
- Натрубная обмуровка котла состоит из легкого бетона, отличающегося теплоизоляционными характеристиками. При помощи хромитовой массы и специальных плит изготавливается внешний слой.
- Накаркасная схема имеет в своем составе три слоя: минеральную вату, диатомобетон и шамотобетон.
- Тяжелая имеет ограниченную область применения и подходит только для котельных с максимальным уровнем температур в пределах 800 градусов. В качестве внешнего слоя выступает красный кирпич, внутренний представляет собой кладку огнеупорного кирпича.
Особенности
Обмуровка водогрейных котлов является трудоемким процессом, требующим соблюдения технологии и грамотного подбора материала. Набивные составы производятся на корундовой, карбундовой либо хромитовой основе. Жидкое стекло зачастую выступает в качестве связующей основы. Количество изготавливаемой массы зависит от поверхности, требующей обработки, и необходимой толщины.
Состав, нанесенный на поверхность, покрывается специальной сеткой, изготовленной из огнеупорного материала. Уплотнительная обмазка выполняется магнезитом, асбестом или шамотным порошком. Стоит отметить, что обмазка может выполняться в случае, если масса еще не застыла.
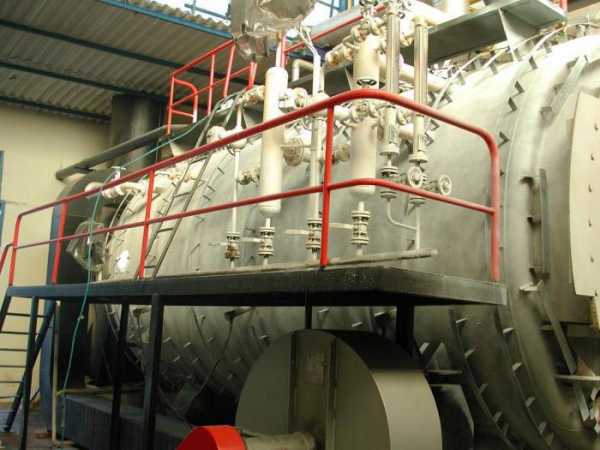
Что нужно знать
Базальтовое волокно, обладающее высокой стойкостью к воздействию температур, используется для формирования теплоизоляционных плит.
В некоторых случаях становится более рациональной частичная обмуровка котла. Снижение потерь тепловой энергии и обеспечение безопасности обслуживающего персонала возможно за счет обработки дверей конструкции. При этом необходимо обратить внимание на распределение температуры при остывании.
Ремонт обмуровки котлов начинается с демонтажа обвязки, при этом желательно сохранить основу конструкции для дальнейшего использования. При наличии неровных участков на экранах и трубах можно нанести слой теплоизолятора. Срок эксплуатации конструкции можно увеличить за счет алюминиевых красящих составов, используемых в качестве финишного покрытия.
Котлы “ДКВР”
Системы данной серии предназначены для обеспечения заготовки нагретой воды и теплоснабжения. Они позволяют получить насыщенный пар и часто применяются в вентиляционных системах. Конструкция имеет отличительные особенности в виде вертикально размещенных труб и двух барабанов. Котлы этой марки обладают множеством положительных сторон:
- широкий диапазон мощности;
- использование любого вида энергоносителя, включая мазут и газ;
- автоматизированная работа системы;
- сборка конструкции может производиться в помещении котельной, при этом не требуется демонтаж стен;
- обмуровка котлов “ДКВР” производится из любых материалов, подходящих для предполагаемого режима работы;
- надежность аэродинамической и гидравлической системы обеспечивает высокий уровень КПД.

Обмуровка котлов: технология
Обязательным этапом перед обмуровкой является гидравлическая проверка котлов. Далее выполняется футеровка поверхности котла и внешняя облицовка. Используемые материалы для футеровки должны иметь огнеупорные свойства, также необходимо тщательно просеять шамотный порошок, песок и глину перед применением. Цемент, огнеупорная и красная глина не должны иметь в своем составе посторонних вкраплений, комочков и мелкого мусора.
Перед началом работ необходимо подготовить огнеупорную смесь, инструменты и кирпичи одинакового размера. Каждый ряд кладки необходимо проверять строительным уровнем, чтобы предотвратить образование впадин и выпуклостей. Удостовериться в качестве укладки углов можно при помощи стального угольника. Как становится ясно, обмуровка паровых котлов, является достаточно сложным процессом, требующим соблюдения всех норм и правил, поэтому за работу можно браться только при наличии знаний и соответствующего опыта. В большинстве случаев лучше обратиться к специалистам, так как даже незначительный недочет может привести в дальнейшем к серьезным последствиям.

Особенности
На изоляционном слое должны отсутствовать трещины и сколы. Перед укладкой огнеупорного шамотного кирпича производится его сортировка, материал должен быть единого размера без повреждений. Применение битого или треснувшего кирпича категорически запрещено, так как это заметно снижает прочность конструкции. Неровные края также уменьшают герметичность швов.

Раствор
Не меньшее значение имеет смесь, используемая для кладки. Она должна обладать равномерной структурой без вкраплений. Для укладки шамотного кирпича подходит раствор на основе глины и шамотного порошка. Степень жирности глины определяет количество порошка. Стоит отметить, что в состав нельзя добавлять соль и речной песок, несмотря на то, что подобные ингредиенты часто встречаются в растворах для кладки печей.
Толщина смеси во время сложной обмуровки должна быть в пределах 2 мм, при обычной кладке допускается увеличение до 3 мм. Полученный результат напрямую зависит от соблюдения пропорций ингредиентов и тщательного перемешивания. Консистенция должна иметь среднюю густоту. Замешивается раствор только на чистой воде, это гарантирует отсутствие извести и других примесей. Рекомендуется готовить состав в отдельной, предварительно очищенной таре.
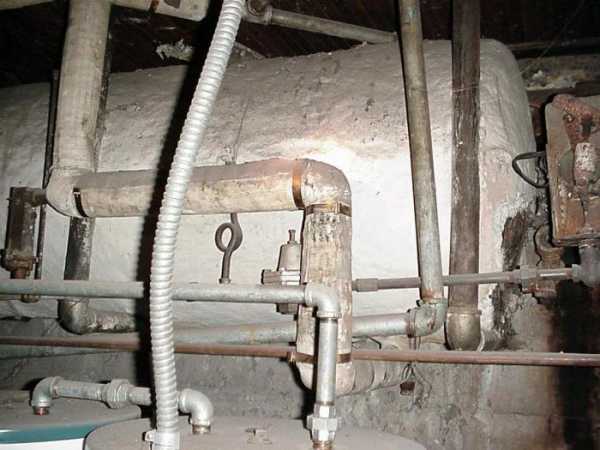
Обмуровка водогрейного котла: описание
Перед началом работ все используемые элементы должны быть очищены от капель раствора, коррозии и загрязнений. Точки соединения арматуры связываются проволокой с диаметром около 2 мм либо свариваются при помощи электросварки. Нежелательно использование алюминиевой и медной проволоки.
Битум наносится равномерным слоем на арматуру и фиксирующие элементы, необходимые для укрепления бетона.
Для изготовления опалубки применяется древесина хвойных пород, за исключением лиственницы. Тщательно обрабатываются и остругиваются стороны, прилегающие к бетонному раствору. Возможно использование бумаги или глины с высокой пластичностью для уплотнения щелей в опалубке. Двойная опалубка подходит для обмуровки вертикальной поверхности либо находящейся под углом не менее 40 градусов. Деревянную поверхность рекомендуется покрыть смазочным составом для того, чтобы избежать ее сцепления с бетоном. В качестве смазки можно использовать раствор, состоящий из воды и минерального масла.
Печи и котлы в промышленности и сегодня остаются незаменимыми объектами, поэтому часто появляется необходимость в ремонте и модернизации подобных конструкций. Кроме того, должна производиться обмуровка котла и при необходимости замена элементов, вышедших из строя.
fb.ru
Конструкция обмуровки
Котельные установки
Обмуровкой называются ограждения, отделяющие топочную камеру и газоходы от окружающей среды. Назначение обмуровки — уменьшить потерю тепла газов и препятствовать присосу воздуха в газоходы котла.
По условиям эксплуатации температура наружной поверхности не должна превышать 50 °С. Лишь в некоторых местах допускается повышенная температура до 70 °С.
Различают три основных типа конструкции обмуровки паровых котлов:
Тяжелая;
Облегченная;
Натру бная.
В пределах каждого типа имеется большое количество конструктивных решений.
Тяжелую обмуровку применяют в неэкранированных или слабо экранированных котлах малой мощности. В районе топки температура в обмуровке котла должна снизиться с 1200-1300 °С до 50-70 °С, поэтому обмуровка должна быть толстой. Для нее применяют огнеупорный шамотный кирпич (им выкладывают внутреннюю поверхность толщиной в 1 кирпич) и красный кирпич (наружная часть в 2-3 кирпича). И тот, и другой кирпич сравнительно хорошо проводит тепло, поэтому толщина обмуровки достигает 750-1000 мм. В кладке кирпичи перевязаны. Для обеспечения свободы термических расширений по углам на всю высоту обмуровки оставляют вертикальные температурные швы, которые уплотняют асбестом.
Обмуровку тяжелого типа выполняют обычно независимо от каркаса трубной системы котла. В этом случае она свободно опирается на фундамент котла. Иногда обмуровку по высоте разбивают на пояса. Нижний пояс опирают на фундамент, а верхние посредством горизонтальных балок — на каркас котла.
Тяжелая обмуровка проста по устройству, но имеет вес 1000-1200 кг на
2
В современных конструкциях котлов топочная камера сильно экранирована, поэтому температура стенки обмуровки, обращенной в топку, составляет 500-600 °С. Это позволяет упростить обмуровку. Создана так называемая облегченная обмуровка (рис. 17.4).
Рис. 17.4. Опора обмуровки на стальной кронштейн: 1 — стальной кронштейн; 2 — фасонные шамотные кирпичи; 3 — асбестовый шнур диаметром 25 мм; 4 — обшивка; 5 — температурный шов 12 мм |
Облегченную обмуровку разбивают по высоте на ряд поясов высотой 1000-1500 мм. Каждый пояс опирается на каркас через промежуточные кронштейны и балки. Таким образом, вся обмуровка держится на каркасе котла. Общая толщина обмуровки — один кирпич (250 мм).
Внутрь топки к трубам — красный кирпич (1Л кирпича), снаружи — диатомовый кирпич (Vi кирпича), который является хорошим изолятором. Плотность обмуровки достигают применением обшивки всей наружной поверхности котла железным листом толщиной 2-3 мм. Между обшивкой и диатомовым кирпичом имеется воздушный зазор 5-10 мм. Иногда облегченная обмуровка выполняется в виде плит (теплоизолирующих) толщиной 100-150 мм.
Вместо диатомового кирпича могут быть применены: совелит, вермикулит, шлаковая вата и др. Вес 1 м2 кладки облегченной обмуровки доходит до 400 кг.
Дальнейшее развитие конструкции привело к созданию натрубной обмуровки (рис. 17.5). Натрубная обмуровка состоит из нескольких слоев теплоизолирующей массы. К трубам на определенном расстоянии друг от друга приваривают прутки из углеродистой стали диаметром 10-12 мм, к которым крепят волнистую проволоку и сетки. Вначале хромитовой массой заполняют промежутки между трубами. Это образует первый слой толщиной 40 мм. Волнистая проволока оказывается внутри слоя. Затем натягивают сетку из проволоки (3 мм с величиной ячейки 20 мм) и наносят второй слой теплоизоляции толщиной 50 мм. Этот слой выполняют из легковесного бетона. Далее укладывают совелитовые плиты и укрепляют сетку. Толщина третьего слоя 50 мм. Снаружи на сетку наносят газонепроницаемую эластичную обмазку. Обмазка состоит из асбеста, глины, гудрона и минерального масла.
Рис. 17.5. Натрубная обмуровка стен топочной камеры парогенератора с естественной циркуляцией:
1 — экранные трубы; 2 — опускные трубы; 3 и 8 — металлическая сетка; 4 — торкрет-масса; 5 — штырь; 6 — высокотемпературная изоляционная масса; 7 — асбоцементные плиты; 8 — ; 9 — уплотиительиая штукатурка
При наличии шипов на экранах можно обойтись без волнистой проволоки. Описана одна из конструкций натрубной обмуровки. Известно много различных модификаций.
Натрубная обмуровка не связана с каркасом. Для создания жесткости по высоте топки трубы охватывают в нескольких местах поясами из проката.
При натрубной обмуровке удается уменьшить толщину стенки до 130-180 мм и вес довести до 120-200 кг/м».
Стоимость обмуровки натрубной по сравнению с облегченной в 2-2,5 раза меньше. Кроме того, отсутствует обшивка котла.
Теплоизоляционные материалы должны обладать низкой теплопроводностью, малым весом, достаточной механической прочностью, а также должны быть дешевыми.
Чем больше пористость материала, тем он легче, тем выше его теплоизоляционные свойства, но тем он менее прочен. Применяют следующие теплоизоляционные материалы.
Асбест — вводят в состав теплоизоляционного материала с целью увеличения прочности и снижения теплопроводности. При повышении температуры асбест теряет связанную влагу, ввиду чего снижается его прочность. При t = 600° влага полностью теряется и асбест превращается в порошок. Из асбеста изго-
Тавливают шнур, картон и ткань, асбестоцементные плиты используют для изоляции при температуре до 450 °С.
Диатомит — осадочная порода (в основном кремнезем). Имеет легкопористую структуру. Используют в виде порошка (засыпки) при температуре до 900-1000 °С, но чаще при более низких, ввиду низких изолирующих свойств.
Асбозурит — приготавливают из смеси доломита и асбеста с небольшой добавкой для связи извести либо цемента и воды. Применяют до температуры 450 °С. Используют в виде мастики либо плит.
Ньювель — приготавливают из смеси магнезита (85 %) с асбестом (15 %), используется в виде мастики до t = 350 °С. Магнезит (MgCO^) при обжиге выделяет ССЬ и остается порошок — магнезия.
Совелит — состоит из смеси обожженного доломита (MgCCb • СаСОз) с асбестом. Применяют в виде плит до температуры 500 °С, обладает теми же теплоизолирующими свойствами, что и ньювель.
Диатомовый пористый кирпич — изготавливают из диатомита и древесных опилок. При обжиге опилки выгорают и получаются поры.
Пористость некоторых теплоизолирующих материалов достигается набуханием изделия за счет выделения паров при нагревании. Таким путем изготавливают пеностекло — из смеси порошков стекла и угля. Хорошо поддается механической обработке при температуре 30 °С, 5 = 0,5 кДж/м • ч град.
Зонолит — пористый материал, получают при нагревании вермикулита (сорт слюды). При этом объем слюды увеличивается в 20 раз. Используют непосредственно до температуры 1000 °С.
Из обожженного вермикулита в смеси с асбестом и связанными веществами делают плиты, применяемые до температуры 600 °С.
Минеральная вата (стекловата, шлаковата) — применяют до температуры 600 °С в виде матов, войлока, плит и др.
Огнеупорные и термоизоляционные бетоны содержат гидравлически твердеющие вещества (цементы) и заполнители (огнеупорные и изоляционные материалы).
Для обмуровки паровых котлов наиболее подходят шамотобетоны. Применяют цементы: портландцемент (лучше), глиноземистый цемент (хуже) и другие марки не ниже 300. Заполнитель — шамотный порошок и дробленка (тоже шамотная).
Для обмуровки котлов применяют огнеупорные бетоны марок 100-300 (предел прочности при сжатии, кг/см»). Допустимая температура огнеупорных бетонов зависит от состава и равна 1100-1300 °С.
Торкретные массы — применяют для выполнения отдельных узлов обмуровки. Укладывают его вручную либо торкрет-пушкой. Наносят его на арматурную сетку либо на ошипованные трубы. Связующим в массе может служить цемент, глина и жидкое стекло. Заполнители — шамот или диатомит. Имеются разные рецепты приготовления (разные пропорции). Температура применения в зависимости от состава максимально 900-1200 °С.
При выборе отопительного прибора для жилого или промышленного помещения специалисты советуют обращать свое внимание на современные твердотопливные котлы. Итак, сегодняшняя тема – твердотопливные котлы, преимущества и недостатки. Основные преимущества Рассмотрим …
Собираетесь приобретать оборудование для обогрева? Присмотритесь к твердотопливным котлам – технике, работающей на самом недорогом и доступном топливе.
Без высокопроизводительных и эффективных твердотопливных отопительных котлов невозможно представить себе жизнь ни одного современного человека. В настоящее время потребительский рынок предлагает широкий ассортимент печных агрегатов например на сайте santehhaus.com.ua, использующих …
msd.com.ua
КАРКАС И ОБМУРОВКА КОТЛОВ — Мегаобучалка
Каркас.Каркасом котла называют металлическую конструкцию, которая поддерживает барабан, поверхности нагрева, обмуровку, лестницы и площадки, а также вспомогательные элементы агрегата и передает их вес на фундамент. Котлы низкого давления и малой производительности устанавливаются на раму, закрепленную непосредственно на фундаменте, или кирпичную обмуровку, и тогда основным назначением каркаса является придание обмуровке парогенератора большей устойчивости и прочности. Каркас современного котла является сложной металлической конструкцией, и на его изготовление затрачивается большое количество металла. В котлах высокого давления масса каркаса составляет 20 — 25 % всей массы металла котла, или 0,8 — 1,2 т на тонну его часовой производительности. Каркас представляет собой рамную конструкцию, выполненную из стандартных металлических профилей, изготовленных из малоуглеродистой стали марки Ст.3, и состоит из ряда основных и вспомогательных колонн и соединяющих их горизонтальных балок, воспринимающих нагрузку от барабанов, трубной системы поверхностей нагрева, а также горизонтальных и диагональных балок, служащих для придания прочности и жесткости системе каркаса.
На рис. 67 показана схема каркаса барабанного котла высокого давления.
Колонны выполняются обычно из двух стальных швеллеров или двутавровых балок, жестко соединенных между собой накладками из листовой стали; колонны передают на фундамент значительные сосредоточенные нагрузки — сотни тонн. Во избежание чрезмерных удельных давлений на фундамент колонны снабжаются башмаками (рис. 68), выполненными из листовой стали и угольников. Опорная плоскость башмаков рассчитывается на допускаемое для материала фундамента напряжение сжатия и закрепляется в фундаменте болтами или заделывается в нем. Основные горизонтальные балки привариваются к колоннам и образуют вместе с ними рамную систему. Несущие и распорные горизонтальные балки выполняются из стальных швеллеров, двутавров или угольников.
Когда сортамент прокатных профилей не обеспечивает необходимой прочности колонн и балок, их делают в виде сварной конструкции, состав- ленной из ряда профилей и листовой стали. Частью каркаса являются помосты, необходимые для обслуживания котла, которые работают как горизонтальные фермы и увеличивают жесткость каркаса. Помосты выполняются из рам прокатных профилей и приваренных к ним листов рифленой стали. Лестницы между помостами выполняются из стальных полос, между которыми приварены ступени. Угол наклона лестниц не должен превышать 50° к горизонту, а их ширина должна быть не менее 600 мм.
Рис. 67. Схема каркаса котла:
1 – колонны; 2 – несущие потолочные балки; 3 – ферма;
4 – ригель; 5 – стойки
Каркас рассчитывается как рамная конструкция, работающая под статической нагрузкой от веса элементов парогенератора и дополнительных термических напряжений, возникающих под влиянием неравномерного нагрева деталей каркаса и приваренных к ним конструкций. В целях предотвращения перегрева элементов каркаса его колонны, горизонтальные балки и фермы располагаются обычно за пределами обмуровки. При установке парогенератора вне здания должна учитываться и ветровая нагрузка на поверхности, ограничивающая парогенератор и передаваемая на каркас. Барабаны котла, коллекторы экранов пароперегревателей и водяных экономайзеров при нагревеудлиняются, и для предупреждения возникновения в них и в элементах каркаса, на которых они закрепляются, больших температурных напряжений необходимо предусмотреть возмож-ность свободного их расширения. С этой целью барабаны устанавливаются на специальных подвижных опорах, закрепленных на горизонтальных балках каркаса, или подвешиваются к этим балкам. Барабаны котлов средней и большой мощности обычно устанавливаются на двух подвижных опорах. Конструкция такой опоры показана на рис. 69.
При большой длине барабана, когда при установке на двух опорах прогиб его больше 10 мм, барабан подвешивают к каркасу в нескольких статически наивыгоднейших точках. Коллекторы экранов, пароперегревателей и водяных экономайзеров крепятся к каркасу шарнирными подвесками, а при малой их длине свободно опираются на скользящие опоры, закрепленные на каркасе.
Назначение и требования к обмуровке. Обмуровкой котла называют систему ограждений, отделяющих топочную камеру и газоходы от окружающей среды. Основным назначением обмуровки являются направление потока продуктов сгорания, а также тепловая и гидравлическая его изоляция от окружающей среды. Тепловая изоляция необходима для уменьшения потерь теплоты в окружающую среду и для обеспечения допустимой температуры наружной поверхности обмуровки, которая по условиям безопасной работы персонала не должна превышать 55 °С. Гидравлическая изоляция необходима для предотвращения присосов холодного воздуха в газоходы или выбивания продуктов сгорания при разнице давлений в газоходах и снаружи, которая имеет место при работе котла с разрежением или с давлением в газовом тракте.
Элементы обмуровки котла работают в различных условиях. Наружная поверхность обмуровки имеет низкую и относительно постоянную температуру, внутренняя ее поверхность находится в области высокой и переменной температуры, снижающейся по ходу потока газов. По направлению потока газов разрежение в газоходах увеличивается, а давление при работе парогенератора под наддувом уменьшается. Различны и нагрузки на элементы обмуровки от ее веса и внутренних напряжений, возникающих при неодинаковых температур-ных удлинениях ее частей.
В наиболее тяжелых условиях находится внутренняя часть обмуровки топки, подвергающаяся воздействию высокой температуры более 1600 °С, а при сжигании твердого топлива также химическому и механическому воздействию шлака и золы. В результате взаимодействия материала обмуровки со шлаком, а также механического износа шлаком и золой происходит разрушение обмуровки.
Конструкция обмуровки. Соответственно назначению и условиям работы к обмуровке предъявляются следующие основные требования: малая теплопроводность, герметичность, механическая прочность и термическая устойчивость. Кроме того, конструкция обмуровки должна быть простой и не требовать больших затрат труда и времени на ее изготовление и монтаж.
Ранее обмуровка парогенераторов выполнялась только из красного и огнеупорного кирпича, из которого выкладывались ее стены и своды, скрепляемые стальными балками и стяжными болтами. Обмуровка современных парогенераторов представляет собой комбинированную систему, выполненную из кирпича, огнеупорных плит, изоляционных материалов, металлических скрепляющих частей, уплотняющих обмазок, металлической обшивки и других элементов. Конструкция обмуровки изменяется и совершенствуется по мере развития парогенераторо-строения и производства огнеупорных изделий и изоляционных материалов.
Обмуровки в зависимости от конструкции и способа крепления могут быть разделены на следующие типы (рис. 70):
а) стеновая кирпичная обмуровка, опирающаяся непосредственно на фундамент;
б) облегченная обмуровка, выполняемая из огнеупорного и диатомитового кирпича, изоляционных плит и стальной обшивки, закрепленная на каркасе парогенератора с помощью металлических конструкций;
в) легкая обмуровка, выполняемая из шамотобетонных или жаростойких бетонных плит, теплоизоляционных плит и металлической обшивки или уплотнительной обмазки.
Показатели указанных типов обмуровок характеризуются следующими данными:
Стеновая обмуровка | Облегченная обмуровка | Легкая обмуровка | |
Общая толщина, мм | 500-600 | 200-500 | 100-200 |
Удельная масса, кг/м2 | 600-1000 | 200-600 | 100-200 |
Стеновая обмуровка применяется для парогенераторов малой мощности при высоте стен не более 12 м. При большей высоте обмуровка становится механически ненадежной. В этом случае она выполняется в виде наружной облицовки из красного кирпича толщиной 1-1,5 кирпича и внутренней футеровки из огнеупорного кирпича, которая в области неэкранированной топки должна иметь толщину 1-1,5 кирпича, а в газоходах с температурой 600-700 °С – не менее 0,5 кирпича (рис. 70а).
При относительно больших размерах топочной камеры и высокой температуре ее стенок для предотвращения нарушения связи между слоями огнеупорного и красного кирпича кладку разделяют на участки и разгружают футеровку по высоте (рис. 70б).
Для уменьшения потерь тепла через обмуровку между облицовкой и футеровкой иногда оставляют каналы, которые засыпают сыпучим изоляционным материалом — инфузорной землей, молотым шлаком и т.п. Для предупреждения возникновения разрушающих кладку внутренних температурных напряжений, возникающих в условиях ее неравномерного нагрева, в стенах кладки предусматриваются температурные швы, заполненные асбестовым шнуром, которые обеспечивают возможность ее свободного расширения.
Облегченные обмуровки ранее применялись в парогенераторах средней мощности. Конструкция облегченной обмуровки показана на рис. 70в. Обмуровка выполняется из двух или трех слоев различных материалов общей толщиной до 500 мм. Внутренний огнеупорный слой – футеровка – имеет толщину 113 мм, а при малой степени экранирования 230 мм, средний изоляционный слой из диатомитового кирпича – 113 мм, облицовочный слой из совелитовых плит 65-150 мм. Средний изоляционный слой часто выполняется из совелитовых плит толщиной 100 мм, заменяющих диатомитовый кирпич. Уменьшение толщины и массы обмуровки позволило опирать ее непосредственно на каркас, в результате чего стало возможным выполнять ее любой высоты, устанавливая через 1-1,5 м разгрузочные пояса. При этом вся стенка делится на ряд ярусов, каждый из которых опирается на чугунные или стальные кронштейны, укрепленные на каркасе парогенератора. Для обеспечения возможности свободного расширения между кронштейном и кладкой предусматриваются горизонтальные температурные швы, заполненные асбестовым шнуром.
В некоторых конструкциях для предотвращения обрушений футеровки применяются специальные крепления вертикальных ярусов к каркасу с помощью чугунных крюков. Снаружи обмуровка обшивается стальными листами или защищается газонепроницаемой штукатуркой (рис. 70 г).
Рис. 70. Конструкции обмуровок вертикальных стен:
а, б – массивная, свободно стоящая: 1 – разгрузочные пояса;
2 – футеровка; в – облегченная накаркасная: 1 – стальные или
чугунные кронштейны; 2 – фасонный шамотный кирпич;
3 – горизонтальный температурный шов; 4 – фасонный шамотный
кирпич; 5 – шамотный кирпич; 6 – фасонный шамотный кирпич;
7 – чугунный крюк; 8 – горизонтальные трубы, закрепленные на
каркасе; 9 – легковесный теплоизолирующий кирпич или
теплоизоляционная плита; 10 – наружная металлическая обшивка;
11 – разгрузочные и притягивающие пояса; г – щитовая обмуровка:
1 – первый слой щита из огнеупорного бетона; 2 – стальная сетка;
3, 4 – термоизолирующие плиты; 5 – газоплотная обмазка
Легкая обмуровка накаркасного типа выполняется из щитов, состоящих из двух слоев теплоизолирующих материалов, защищенных со стороны омывающих их газов слоем жароупорного бетона. Металлическая рамка щитов такой обмуровки крепится к каркасу парогенератора. Применяются также плиты размером 1000х500 мм и 1000х1000 м из известково-кремнеземистых материалов, покрытых со стороны газов жароупорным шамотобетоном. Плиты, предназначенные для установки в незащищенных трубами местах с более высокой температурой, имеют большую толщину и массу. Для передачи их массы на каркас предусматриваются дополнительно закладные чугунные кронштейны. Накаркасная обмуровка применяется преимущественно в области пароперегревателей, газоповоротных камер и конвективной шахты парогенераторов большой мощности. В топках накаркасную обмуровку применяют на прямых стенках. Достоинствами накаркасной конструкции обмуровки являются ее небольшая масса и существенное облегчение монтажных работ. Однако при такой обмуровке затрудняются ее ремонт и обеспечение плотности.
Натрубная обмуровка (рис. 71) выполняется в виде отдельных слоев, последовательно наносимых в пластичном состоянии на трубы экранов и других поверхностей нагрева или в виде плит-панелей с огнеупорным и теплоизоляционным слоями, устанавливаемых на балки жесткости, закрепленные на трубах.
В этом случае панели изготавливаются на заводе, а жароупорный слой может быть нанесен в пластичном состоянии на трубы экрана вручную. Для натрубной обмуровки топочной камеры несущими элементами являются трубы экранов, и в результате тепловых удлинений обмуровка перемещается вместе с ними.
Разновидностью натрубной обмуровки являются применяемые в топке зажигательные пояса.
Рис. 71. Натрубная обмуровка:
1 – слой хромитовой массы; 2 – стальная сетка;
3,4 – термоизолирующие плиты; 5 – газоплотная обмазка
ТЯГОДУТЬЕВЫЕ МАШИНЫ
Задача тягодутьевых машин – отсос дымовых газов и подача воздуха для обеспечения нормальной работы котла на всех нагрузках. Большое значение имеет обеспечение надежности их работы, ибо лопатки дымососов подвергаются износу летучей золой. Большое значение имеет также экономичная работа тягодутьевых машин. Так, от рациональной аэродинамики ротора зависит КПД (50 – 90%), а, следовательно, и расход на собственные нужды котельной установки.
В тягодутьевых установках применяются следующий машины: центробежные (радиальные) вентиляторы с лопатками, загнутыми вперед (рис. 72а), или с лопатками, загнутыми назад (рис. 72б), и осевые машины (рис. 73).
Вентиляторы и дымососы с лопатками, загнутыми вперед, нашли широкое применение благодаря тому, что даже при умеренных значениях окружной скорости они позволяют создать достаточно высокие давления. Однако эти машины имеют невысокий КПД (65–70%). Такие тягодутьевые машины распространены в котельных установках относительно небольшой мощности.
Центробежные тягодутьевые машины с лопатками, загнутыми назад, являются наиболее совершенными – КПД = 85÷90%. Однако повышение давления получается в 2 – 2,5 раза меньшим, чем у машин с лопатками, загнутыми вперед.
Поскольку развиваемое давление, пропорционально квадрату расхода на выходе из рабочего колеса, то приходится применять более высокую окружную скорость, что требует весьма тщательной балансировки ротора. Запыленность газового потока отрицательно сказывается на работе рабочего колеса.
Рис. 72. Центробежный (радиальный) вентилятор:
а – лопатки, загнутые вперед; б – лопатки, загнутые назад
Для котлов к энергоблокам мощностью 300 МВт и выше в качестве дымососов получили распространение осевые машины. В них газ движется вдоль оси.
Рис. 73. Осевая тягодутьевая машина
Осевые тягодутьёвые машины имеют достаточно высокие КПД (около 65%). Коэффициент повышения давления на ступень – невысокий, поэтому применяют несколько ступеней. На электростанциях работают двухступенчатые осевые дымососы. В связи с повышенной окружной скоростью осевые машины имеют высокий уровень шума. Большая доля динамического давления создает определенные трудности превращения его в статическое. Малый радиальный зазор между лопатками и кожухом создает дополнительные требования к монтажу и эксплуатации.
megaobuchalka.ru
Ремонт обмуровки котлов — РосТепло Энциклопедия теплоснабжения
Материал из РосТепло Энциклопедия теплоснабжении
Содержание разделаОбмуровка стационарных котлов по конструкции подразделяется на четыре основных вида:
1. Натрубная обмуровка, прикрепляемая непосредственно к поверхностям нагрева котла и выполняемая из жароупорных бетонов (первый слой), теплоизоляционных бетонов или перлитоцементных плит (второй слой) и газонепроницаемой обмазки (третий уплотнительный слой).
2. Щитовая обмуровка, прикрепляемая к каркасу котла или каркасу блоков поверхности нагрева и выполняемая в виде щитов или панелей, также состоящих из трех слоев – огнезащитного, теплоизоляционного и уплотнительного. В ряде случаев рационально заменять уплотнительную обмазку обшивкой из стального листа.
3. Облегченная обмуровка, прикрепляемая к каркасу котла из штучных огнеупорно-теплоизоляционных изделий. Эта конструкция обмуровки может иметь обшивку из стального листа.
4. Натрубная обмуровка в газоплотных котлах, прикрепляемая к газоплотным поверхностям нагрева котла и выполняемая из теплоизоляционных перлитоцементных или известково-кремнеземистых плит (первый теплоизоляционный слой) и газонепроницаемой обмазки (второй уплотнительный слой).
В обмуровках применяют жаростойкий на бетон связующем из глиноземистого цемента или портландцемента. Для теплоизоляционного бетона рименяют диатомовую крошку, асбест V–VI сорта распушенный и связующее – портландцемент. В некоторых случаях в теплоизоляционном бетоне применяют крошку из вспученного перлита вместо диатомовой. Газонепроницаемая (уплотнительная) обмазка состоит, в зависимости от состава, из асбеста V сорта распушенного, шамотного порошка, огнеупорной глины и связующего – каустического магнезита, жидкого стекла или портландцемента (см. раздел 10).
Для огнеупорной кладки применяют нормальный и легковесный огнеупорный кирпич, а для теплоизоляционной кладки – кирпич плотностью не более 600 кг/м3. Для устройства теплоизоляционного слоя применяют перлитоцементные или известково-кремнеземистые плиты или маты минераловатные прошивные марки 150 (см. раздел 10).
В газоплотных котлах для теплоизоляционного слоя, прикрепляемого к панелям, применяют известково-кремнеземистые плиты.
В табл. 9.14. приведена характеристика конструкций обмуровок.
Не допускается смешивание цементов разных видов и марок, а также цементов, выпускаемых разными заводами.
Таблица 9.14. Характеристики конструкций обмуровокКонструкция обмуровки | Толщина слоя, мм | Общая толщина обмуровки, мм | Масса 1 м2 обмуровки, кг | ||||
Жаростойкий бетон или огнеупорный кирпич | Теплоизоляционный бетон | Теплоизоля- ционный слой | Уплотни- тельная обмотка | Обшивка | |||
Натрубная Щитовая Облегченная Натрубная газоплотных котлов | 20–25 40–80 113 — | 0–50 0–126 65–195 — | 80–125 125–150 70–100 150 | 15–20 15–20 — 15 | 4 4 4 4 | 115–180 165–350 265–415 170 | 95–150 170–340 215–400 95 |
Некоторая часть конструктивных узлов обмуровки в процессе эксплуатации котла разрушается и требует восстановления. Ремонт обмуровки заключается в полной разборке разрушенного участка, подготовке участка и укладке новой обмуровки.
Арматурные и опалубочные работы[править]
Арматура, стальная сетка, детали крепления обмуровки перед установкой очищают от грязи, пленочной коррозии, налипшего раствора и т. п. Пересечение проволоки арматуры сваривают электросваркой или перевязывают вязальной проволокой диаметром 1,6–2 мм. Перевязка арматуры медной или алюминиевой проволокой не допускается.
Детали крепления обмуровки и арматуру диаметром более 8 мм, находящиеся в жароупорном и теплоизоляционном бетонах, покрывают слоем битума толщиной до 2 мм. Сетку для армирования жароупорного бетона натрубной обмуровки и сетку для армирования уплотнительной обмазки натягивают без слабины и провисания и крепят крючками с шагом не более 1 × 1 м.
Деревянную опалубку изготавливают из хвойных пород дерева (кроме лиственницы), из пиломатериала толщиной 20–30 мм. Поверхность, соприкасающуюся с укладываемым бетоном, остругивают. Вторично используемая опалубка должна быть очищена от грязи и застывшего бетона.
Для заделки щелей в опалубке с целью предотвращения вытекания цементного молока разрешается применять пластичную глину или плотную бумагу. При укладке бетона в конструкции обмуровки, расположенные вертикально или под углом более 40° к горизонтальной плоскости, применяют двойную опалубку. В этом случае наружную стенку опалубки передвигают по мере укладки бетона. При возможности в качестве внутренней стенки опалубки нужно использовать не разобранный слой обмуровки.
Опалубку для выполнения отверстий диаметром до 200 мм изготавливают из круглого лесоматериала, для больших диаметров делают опалубку из узких досок или из фанеры. Для предотвращения сцепления бетона с опалубкой внутреннюю ее поверхность покрывают смазкой, состоящей из 12 частей минерального масла, 1 части цемента и 0,5 части воды. Можно применять отработанное минеральное масло. Применять для смазки опалубки известковые растворы нельзя.
Приготовление и укладка набивных масс на поверхности экранов[править]
Для укладки на экранные поверхности котлов применяют набивные массы: хромитовые, хромитомагнезитовые, карборундовые и корундовые.
В карборундовых массах в качестве связующего применяют жидкое стекло, шликер огнеупорной глины, триполифосфат натрия и алюмофосфатное связующее на основе ортофосфорной кислоты.
Наилучшие эксплуатационные свойства имеет карборундовая масса на фосфатном связующем.
Составы и свойства набивных масс приведены в табл. 9.15.
Таблица 9.15. Составы и свойства набивных масс.
Наименование массы | Состав массы | Максимальная температура применения, оС | Плотность, кг/м3 | Коэффициент линейного расширения (при температуре 20 – 800оС) | Коэффициент теплопроводности (при температуре 300 – 700оС), Вт/ м×оС |
1 | 2 | 3 | 4 | 5 | 6 |
Хромитовая | Хромитовая смесь СХ-1 или СХ-2, жидкое стекло плотностью 1,4 – 1,5 г/см3, 7% к хромитовой смеси | 1350 | 2500 – 3200 | (7,0 – 8,0)×10– 6 | 1,1 – 1,3 |
Карборундовая | Карбид кремния черный № 160-63 – 40%, № 50-12 – 30%, шлам карбид кремния – 30%, связка сверх 100%: жидкое стекло плотностью 1,3 г/см3 – 6%, водная суспензия огнеупорной глины плотностью 1,13 г/см3 – 5% | 1500 | 2100 – 2300 | 5,5×10– 6 | 4,0 – 4,5 |
Карборундовая на фосфатном связующем | Карбид кремния черный № 160-63 – 40%, № 50-12 – 30%, шлам карбид кремния – 30%, связка сверх 100%: алюмофосфатное связующее – 18%, огнеупорная глина – 6% | 1700 | 2100 – 2300 | 8,9×10– 6 | 2,0 – 3,0 |
Карборундовая на фосфатном связующем | Карбид кремния черный № 160-63 – 40%, № 50-12 – 30%, шлам карбид кремния – 30%, связка сверх 100%: огнеупорная глина – 5%, триполифосфат – 3% | 1600 | 2300 – 2500 | 5,5×10– 6 | 5,5 – 7,2 |
Карборундовая на фосфатном связующем | Карбид кремния черный № 160-63 – 40%, № 50-12 – 30%, шлам карбид кремния – 30%, связка сверх 100%: ортофосфорная кислота – 15%, электрокорунд – 10%, огнеупорная глина – 6% | 1500 | 2100 – 2300 | 4,1×10– 6 | 4,0 – 6,0 |
Корундовая на алюмофосфатном связующем | Корунд № 400-100 –25%, огнеупорная глина – 25 – 35%; связка сверх 100%: ортофосфорная кислота 75-процентная – 15% | 1650 | 2100 – 2400 | 7,6×10– 6 | 0,8 – 1,2 |
Хромомагнези-товая | Хромомагнезит зернового состава: зерно от 7 до 3 мм – 40%, от 1 до 0,09 мм – 30%, меньше 0,09 мм – 30%; связка сверх 100%: жидкое стекло плотностью 1,4 – 1,5 г/см3 – 10%, кремнефтористый натрий – 1%, огнеупорная глина – 6% | 1500 | 2600 – 2800 | 10,3×10– 6 | 1,0 – 1,5 |
Составы и свойства жаростойких бетонов приведены в разделе 10.
Перед приготовлением набивных масс необходимо:
- — жидкое стекло разбавить водой и довести до заданной плотности;
- — огнеупорную глину высушить, размолоть и просеять через сито с отверстиями не более 1 мм;
- — растворить огнеупорную глину в воде;
- — плотность глиняной суспензии должна составлять 1,13–1,15 г/см3.
Разрешается приготовление карборунда мелкого зернового состава путем размола более крупных зерен в шаровых мельницах со стальными мелющими телами.
Массы приготавливают в лопастных смесителях. Сухие компоненты засыпают в смеситель и перемешивают 3 мин, затем без остановки смесителя загружают жидкие компоненты в любой последовательности. После загрузки в смеситель всех компонентов массу перемешивают 10 мин.
Приготовленные набивные массы, особенно хромитовая и карборундовая, употребляются в дело в течение 1,5 ч с момента приготовления. Для предохранения от высыхания и твердения массы следует хранить в закрытых емкостях. Повторное применение схватившейся массы не допускается.
Перед укладкой набивных масс ошипованные и гладкие экранные трубы, камеры и другие стальные поверхности должны быть пропескоструены. На зажигательных поясах массу набрасывают на ошипованные трубы сразу достаточно большой площадью и набивают таким образом, чтобы слой уплотненной массы над шипами составлял 3–5 мм. Необходимо учитывать, что набивка массы в несколько слоев с некоторыми промежутками времени вызывает ее расслоение.
Массу уплотняют пневмомолотками через стальную плиту размером 200×200 мм, толщиной 12–15 мм. Массу набивают плотно, без пустот между трубами и шипами. Степень уплотнения проверяют нажатием большого пальца руки с усилием 10–15 кг. При этом на поверхности массы не должен остаться заметный след.
При укладке массы на под котлов с жидким шлакоудалением, амбразуры горелок и т. п. рекомендуется массы укладывать слоями толщиной не более 100 мм. Массу уплотняют пневмолопатками или вручную деревянными трамбовками. При необходимости укладки второго слоя поверхность ранее уложенного слоя нарезают квадратами 80×80 мм на глубину 7–8 мм. Укладку масс, особенно при большой толщине слоя, желательно выполнять без перерыва. Целесообразно высушивать массу сразу же после укладки, пропуская через экраны горячую воду с температурой 60 °С.
Приготовление и нанесение уплотнительных обмазок[править]
Уплотнительные обмазки приготавливают в смесителе принудительного действия. В смеситель засыпают сухие компоненты и затем при работающем смесителе заливают в любой последовательности жидкие компоненты. Компоненты обмазки перемешивают 8–10 мин до получения однородной массы. Уплотнительные обмазки готовят в количестве, которое может быть уложено в дело в течение 1 ч после приготовления. Затвердевшие обмазки применять не разрешается.
Перед нанесением обмазки сетку очищают от грязи и проверяют надежность ее закрепления. Обмазку набрасывают на сетку небольшими порциями, хорошо уплотняют деревянными трамбовками и заглаживают мастерком или полутеркой. При необходимости густота раствора может быть уменьшена прибавлением раствора хлористого магния с тщательным перемешиванием. Применение воды для уменьшения густоты раствора не разрешается. Нельзя увлажнять уплотнительные обмазки в процессе твердения.
В табл. 9.16. приводятся составы обмазок и мастик.
Таблица 9.16. Составы обмазок и мастикНаименование | Состав и расход на 1 м3 | Область применения | |
Материалы | Количество | ||
1 | 2 | 3 | 4 |
Уплотнительная магнезиальная обмазка | Каустический магнезит II класса Асбест распушенный V–VI сорта Раствор хлористого магния плотностью 1,2 г/см3 | 300 кг 800 кг 450 л | Наружный уплотнительный слой обмуровок без металлической обшивки |
Уплотнительная обмазка ОРГРЭС | Портландцемент марки 300 Глина огнеупорная Шамотный порошок, зерно до 2 мм Асбест распушенный V–VI сорта Жидкое стекло плотностью 1,4–1,5 г/см3 | 70 кг 210 кг 560 кг 560 кг 150 кг | Наружный уплотнительный слой обмуровок без металлической обшивки |
Уплотнительная асбестодиато-мовая обмазка | Диатомовая крошка, размер зерна до 5 мм Асбест распушенный V–VI сорта Жидкое стекло плотностью 1,38–1,40 г/см3 | 360 кг 300 кг 120 кг | Уплотнение кладки из шамотного кирпича. Предельная температура применения 800°С |
Огнеупорный кладочный раствор | Мертель алюмосиликатный Вода | 1370 кг 450–550 л | Кладка из огнеупорного кирпича |
Диатомо-цементный кладочный раствор | Диатомит молотый Портландцемент марки 400 Вода | 520 кг 180 кг 450–550 л | Кладка из диатомового кирпича в местах, предусмотренных проектом. Кладка из диатомового кирпича, в основном выполняется «всухую». |
Мастика для подмазки и промазки швов перлитовая | Перлитовый песок, размер зерна до 1,5 мм Асбест V сорта Жидкое стекло плотностью 1,40 г/см3 Кремнефтористый натрий Вода | Состав по массе 20% 20% 57% 3% В количестве, соответствующем погружению конуса в раствор на 10–12 см | Для подмазки и промазки швов в перлитоцементных изделиях |
Мастика для промазки швов в известково-кремнеземистых изделиях № 2 | Жидкое стекло натриевое плотностью 1,40–1,43 г/см3 Диатомит молотый, зерно до 1,5 мм Глина огнеупорная молотая | 1 часть 0,4 части 0,04 части | — — — |
Дополнительные сведения о составах защитных и уплотнительных обмазок приведены в разделе 10.5.2.
Ремонт обмуровки из штучных огнеупорных и теплоизоляционных изделий[править]
Классификация огнеупорных растворов по консистенции для кладки из шамотного кирпича приведена в табл. 9.17. Более подробно составы огнеупорных растворов, твердеющих при нагревании, и составы воздушно-твердеющих шамотных растворов, как и способы их приготовления, приведены в разделе 10.5.2.
Таблица 9.17. Классификация огнеупорных растворов (консистенция растворов)Раствор | Тонкость помола мертеля | Пределы осадки конуса, см | Толщина шва, мм, не более |
Жидкий Полугустой Густой | Тонкий Крупный Крупный | 6–9 5–6 3–5 | 1–2 3 5 |
Разборку разрушенного или разбираемого с целью ремонта участка кладки обмуровки следует выполнять с учетом максимального сохранения изделий для вторичного использования при условии лабораторных испытаний (шамотные изделия). Для уменьшения пыления участки разбираемой кладки увлажняют. Все оголенные элементы крепления кладки очищают от остатков раствора и соответствующим образом ремонтируют.
Сопряжение новой кладки с неразбираемым участком следует выполнять перевязкой по штробе, выполненной «с убегом». Толщина кладки, способ укладки кирпича должны быть такими же, как это было предусмотрено заводской конструкцией. Кладку огнеупорного кирпича начинают с углов и ведут к середине. При кладке подов котлов с жидким шлакоудалением верхний ряд огнеупорного кирпича укладывают на ребро поперек движения шлака.
Неровности и искривления (в переделах допусков) металлоконструкций, обшивки пода и экранных труб, на которые опирается кладка, следует выравнивать теплоизоляционным слоем с тем, чтобы обеспечить ровную поверхность под кладку из огнеупорного кирпича.
Кладку амбразур горелок производят с обязательной предварительной подгонкой фасонного или клинового кирпича. Толщина шва не более 1 мм. Технологические отверстия (лазы, лючки и др.) должны выполняться огнеупорным кирпичом на всю толщину обмуровки. Кладку в местах прохода труб через обмуровку и в местах подвижных опор и креплений экранных труб следует выполнять особо тщательно, не допуская защемления указанных узлов в обмуровке. Манжеты в местах прохода труб через обмуровку перед укладкой бетона должны быть надежно закреплены на трубах. Длина манжет должна быть на 40 мм больше толщины слоя бетона. При кладке мест сопряжения обмуровки вертикальной стены с потолком должен быть выполнен температурный зазор 20 мм.
Укладку теплоизоляционных известково-кремнеземистых или перлитоцементных плит производят насухо с зазором между плитами не более 3 мм с перекрытием швов на ширину не менее 50 мм. В теплоизоляционном слое не должно быть пустот. Разрешается заделывать пустоты кусками теплоизоляционных плит.
Зазор между наружной поверхностью теплоизоляционного слоя и металлической обшивкой котла должен соответствовать проектным данным. Зазор проверяют при восстановлении металлической обшивки контрольной рейкой.
При выполнении теплоизоляционного слоя из матов минераловатных с обкладкой металлической сеткой необходимо сшивать края сеток матов мягкой углеродистой проволокой. Пустоты в местах стыков матов заделывают минеральной ватой. Поверхность изоляционного слоя должна быть ровной.
Допускаемые отклонения от проектных размеров при выполнении обмуровки не должны превышать данных, приведенных в табл. 9.18.
Таблица 9.18. Допускаемые отклонения от проектных размеров при выполнении обмуровкиНаименование | Допускаемые отклонения от проектных размеров , мм |
Расстояние между осями экранных труб и обмуровкой Расстояние между осями крайних труб змеевиков пароперегревателей, экономайзеров и обмуровкой Ширина температурного шва Впадины, выпучины, выступающие кирпичи на поверхности обмуровки на длине 1 м То же для наружной поверхности на длине 1 м | ± 10 ± 10 ± 5 ± 3 ± 4 |
www.rosteplo.ru