- Радиаторы отопления чугунные вес одной секции
- Вес секции чугунной батареи старого образца
- Сколько весит секция чугунной батареи
- Классические батареи
- Современные отопительные радиаторы из чугуна
- Заключение
- Сколько весит батарея чугунная. Вес одной секции
- Преимущества чугуна
- Особенности монтажа чугунных батарей
- Технические характеристики батарей из чугуна
- Расчет необходимого количества секций в батареях
- Размеры чугунного радиатора
- Срок службы чугунных батарей отопления
- Вес секции батареи из чугуна
- Сколько квт в 1 секции чугунного радиатора: преимущества, расчеты
- Обход огромных объемных деформаций в анодах сплавов литиевых батарей
- Морфология после первоначального литирования в различные металлы
- Достижение гомогенного и однонаправленного литирования
- Механизм из металлургического понимания
- Практическое применение к литиевой батарее с анодом из сплава
- Подготовка материалов
- Электрохимические испытания
- Наблюдение за морфологией
- Твердость по Виккерсу
- Рентгеновская дифракция
- Расчет свободной энергии
- -2. [CrossRef] [Google Scholar]
- Инвентаризация литого и кованого железа
- Снижение использования кобальта для литий-ионных аккумуляторов
Радиаторы отопления чугунные вес одной секции
Главная » Отопление » Радиаторы отопления чугунные вес одной секции
Чугунные радиаторы: вес одной секции
Радиаторы из чугуна потеснились на рынке под наплывом современных разработок в сфере отопительных приборов, но продолжают составлять серьезную конкуренцию новинкам. При выборе важно учитывать вес чугунной батареи, поскольку этот параметр влияет на сложность монтажа и принципы установки.
У классического секционного радиатора вес 1 элемента составляет 7,5 кг, то есть, стандартная конструкция из 7 элементов будет весить более 50 кг.
Классический чугунный радиатор
В связи с этим возникают две проблемы:
- надежное настенное крепление сложно смонтировать, если стены выполнены из пористых легких блоков или представляют собой каркасную конструкцию — потребуется устанавливать прибор отопления на пол;
- переносить батарею необходимо вдвоем и очень аккуратно, поскольку от ударов в хрупком чугуне появляются микротрещины, которые расширяются под воздействием нагретого теплоносителя – со временем это провоцирует разгерметизацию прибора отопления.
Преимущества чугуна
Если не учитывать, сколько весит чугунная батарея, можно отметить целый спектр преимуществ отопительных приборов данного типа, в число которых входит:
- устойчивость к коррозии;
- стойкость к химически агрессивным средам – материал нетребователен к характеристикам теплоносителя;
- долговечность;
- высокие показатели теплового излучения – чем больше количество секций, тем выше теплоотдача прибора отопления.
Внешний вид стандартных батарей из чугуна прост и лаконичен, но сегодня производители предлагают и радиаторы, выполненные под старину. К преимуществам таких моделей относится стильный и респектабельный внешний вид.
Различные варианты радиаторов
Технические характеристики
Мощность прибора отопления – показатель его теплоэффективности. При расчете системы отопления учитываются потребности дома в тепле. Важно знать мощность 1 секции чугунного радиатора, чтобы определить размер батарей для каждого отапливаемого помещения. Неправильные расчеты приводят к тому, что помещение не будет качественно прогреваться либо наоборот – придется его часто проветривать, удаляя излишки тепла.
У рядового стандартного радиатора из чугуна мощность 1 звена составляет 170 Вт. Чугунные батареи выдерживают нагрев свыше 100°С и успешно функционируют при рабочем давлении 9 атм. Это позволяет использовать изделия данного типа в составе центральных и автономных отопительных сетей.
Современные модели
Производители предлагают облегченные варианты батарей из серого чугуна. Если вес 1 звена советского радиатора МС140 составляет 7,12 кг, то 1 секция модели Viadrus STYL 500 чешского производства весит 3,8 кг, и ее внутренний объем составляет 0,8 л. Это означает, что заполненный теплоносителем чешский радиатор из 10 звеньев будет иметь массу (3,8 + 0,8) × 10 = 46 кг. Это на 40% меньше, чем масса заполненной батареи МС 140, состоящей из аналогичного количества элементов.
В России также производятся чугунные отопительные приборы облегченного образца. Под брендом EXEMET выпускаются батареи MODERN, 1 секция которых весит 3,3, а ее внутренний объем составляет 0,6 л. Эти трубчатые чугунные радиаторы характеризуются относительно невысокой теплоотдачей, что требует увеличения количества звеньев. Отопительные приборы рассчитаны на напольную установку.
Растущей популярностью пользуются винтажные радиаторы из чугуна. Это напольные модели, изготовленные по технологии художественного литья. Из-за объемных сложных узоров вес секции чугунного радиатора значительно увеличен, он достигает 12 и более килограммов.
Винтажный напольный радиатор из чугуна
Срок службы
В домах, построенных до революции, до сих пор работают радиаторы из чугуна, установленные более 100 лет назад. Современные приборы отопления из этого материала также рассчитаны на десятки лет безремонтной эксплуатации.
Долговечность объясняется прочностью чугуна, устойчивостью к нагреву и давлению. Отопительные приборы из чугуна не ржавеют в период, когда из сети слит теплоноситель и внутренняя поверхность батарей контактирует с воздухом.
Габариты
Вес секции чугунного радиатора зависит от ее высоты, конфигурации и толщины стенок.
Производители предлагают модели с различными характеристиками:
- глубина батареи составляет от 70 до 140 мм в стандартном исполнении;
- ширина звена варьируется от 35 до 93 мм;
- объем секции – от 0,45 до 1,5 л в зависимости от габаритов;
- высота отопительного прибора в стандартном исполнении — 370-588 мм;
- межосевое расстояние – 350 либо 500 мм.
Классические батареи: базовые параметры
Классической считается советская батарея МС140 со следующими параметрами:
- высота 388/588 мм;
- глубина 140 мм;
- ширина 93 мм;
- объем одного звена высотой 588 мм – 1,5 л;
- масса одного звена высотой 588 мм – 7,12 кг.
Зная, сколько весит одна секция радиатора и ее объем, можно рассчитать массу прибора отопления МС140, заполненную теплоносителем. Общая масса заполненной секции составит 8,62 кг, батарея из 10 звеньев будет весить около 86 кг.
Богатый выбор разнообразной стилистики батарей
Основные расчеты
Проектируя систему отопления, требуется рассчитать вес радиатора и необходимое количество секций в батареях. Расчеты ведутся на основании мощности одной секции отопительного прибора (для классического изделия из чугуна это 170 Вт) и теплового расчета помещения.
Чтобы подсчитать необходимое количество секций и итоговый вес чугунного радиатора, следует учесть площадь и теплопотери помещения, которые зависят от характеристик материалов, из которых возведены стены, наличия утепления. Также требуется обратить внимание на количество окон и вид оконных систем.
Для панельного дома оптимальная величина теплового потока составляет 0,041 кВт/м3, для кирпичного – 0,034 кВт/м3, для зданий с утепленными стенами (независимо от материала, из которого они возведены) – 0,02 кВт/м3.
Учитывая немалый вес одной секции чугунной батареи, количество звеньев в стандартном радиаторе варьируется от 4 до 10. В большом помещении удобнее установить два-три прибора отопления по 4-5 секций вместо того, чтобы монтировать один крайне тяжелый радиатор с числом звеньев более 10-ти.
Из этого следует
Чтобы правильно выбрать принцип крепления, необходимо узнать, сколько весит секция чугунной батареи, заполненная теплоносителем. Для приборов отопления из чугуна важно подобрать подходящее количество кронштейнов для настенного монтажа. Если стены выполнены из пористых блоков или дом возведен из СИП-панелей, число точек крепежа увеличивают с целью более равномерно распределить нагрузку.
Правильный расчет радиаторов и надежный монтаж – гарантия бесперебойного функционирования системы отопления.
Видео по теме:
profiteplo.com
Сколько весит батарея чугунная. Вес одной секции
Чугунные батареи существуют уже более века. И сегодня этот вид отопительных радиаторов продолжает обогревать человеческие жилища, ничуть не уступая более современным компактным конвекторам и аллюминиевым аналогам.
Преимущества чугуна
Чугун имеет массу неоспоримых достоинств. Он долговечен, стоек к коррозии, обладает высокой теплоэффективностью. Выпускаемые чугунные батареи в ретро-стиле поражают своей красотой. Да и современные обычные чугунные батареи выглядят очень привлекательно, выгодно отличаясь эффектным дизайном.
У чугунных батарей есть один недостаток — их вес. Сколько весит чугунная батарея, можно понять, приняв во внимание, что вес одной только секции колеблется от 7 до 7,5 кг. Среди современных разработок есть и более легкие модификации. У них вес секции составляет всего 5,7 кг.
Особенности монтажа чугунных батарей
Поскольку монтаж производится на стенки и перегородки, а они часто бывают выполнены из непрочного материала, то важно знать точно, сколько весит одна секция чугунной батареи. Это нужно для того, чтобы расчитать вес общей нагрузки. Если окажется, что расчетная нагрузка выше норматива, то от такой установки придется отказаться полностью, либо нужно будет делать специальные крепления, чтобы батарея не сломала стену, либо установить отопительную батарею на полу.
Обычно стандартные чугунные батареи состоят из нескольких секций — секционных элементов. Как правило, их количество колеблется от 4 до 10. Но иногда встречаются и батареи с 20 и более секциями. Но использовать такие громоздкие радиаторы неудобно, поэтому на практике обычно устанавливают несколько батарей, по 5-7 секций в каждой. Обычно габариты современной секции чугунной батареи составляют 140 х 500 мм. Рассчитать массу всей батареи несложно, зная точный вес одной секции.
К примеру, нужно определить, сколько весит батарея. Чугунная секция весит 7,5 кг. Следовательно, набор из семи секций будет весить 49-52,5 кг. Такая же батарея, но уже из десяти секций, окажется весом около 75 кг. Необходимо учитывать и то, что это вес батареи без учета веса теплоносителя.
Средний объем одной секции чугунной батареи составляет около 1,5 литра жидкости. Есть и более экономичные модели, с объемом от 1 литра. При решении вопроса о том, сколько весит старая чугунная батарея, необходимо знать, что в старых образцах чугунных батарей объем жидкости достигал 1,7 литра на секцию. Поэтому после запуска системы вес приборов увеличивается.
Технические характеристики батарей из чугуна
Чтобы правильно определить необходимое количество секций в источнике тепла, важно учитывать и другие характеристики чугунных батарей. Главным показателем эффективности радиатора отопления является мощность. Если точно знать мощность одного радиатора, то несложно определить и общее количество, которое требуется для обеспечения жилья теплом.
При неверном расчете нужного количества радиаторов отопления в помещении появится излишняя сухость воздуха, а это не менее неприятно, чем недостаток тепла. На радиаторах будет нагреваться осевшая пыль, из-за необходимости частого проветривания увеличатся сквозняки.
Номинальная тепловая мощность одной секции чугунного радиатора рядовой модификации составляет 160 Вт. При расчете размера каждого устанавливаемого радиатора необходимо сначала узнать, сколько весит чугунная батарея. 1 секция берется за стандарт. Затем нужно определить, какова величина теплового потока отапливаемого жилья. Эта характеристика во многом зависит от того, из какого материала выполнены стены, какова теплоизоляция дома, насколько профессионально установлены окна в здании.
Так, в панельных домах тепловой поток составляет около 0,041 кВт/м3. В кирпичных строениях этот показатель уже составляет 0,034 кВт/м3. А при качественно выполненной теплоизоляции — 0.02 кВт/м3. В последнем примере не имеет значения, из чего построены стены.
Расчет необходимого количества секций в батареях
После определения того, сколько весит батарея чугунная, необходимо расчитать необходимое число звеньев в радиаторе либо количество приборов, которое нужно установить в отдельно взятом помещении. Ту цифру, которая обозначает объем комнаты, умножаем на величину теплового потока помещения, полученную цифру делим на тепловой поток одной секции. Его величина составляет 0,160 кВт.
Полученную в результате вычислений цифру нужно округлить до целого — это и будет количество требуемых секций. При этом нет необходимости соединять все секции в один радиатор. Лучше распределить их в нескольких приборах, установив по одному под каждым оконным проемом. Вычислим таким образом, сколько весит батарея. Чугунная весит намного больше, это мы уже выяснили. Осталось определиться с местом для установки радиатора.
Размер оконного проема также влияет на выбираемое количество секций в устанавливаемом радиаторе. Чтобы использовать всю мощность отопительного прибора, его длина должна быть шире окна не менее чем на 70-75 %. При этом сам радиатор должен быть расположен на расстоянии от 8 до 12 см от подоконника.
Размеры чугунного радиатора
Отдавая дань традициям, радиаторы выпускают общепринятых размеров, обеспечивая этим еще и эффективную работу и безопасность отопления. Ширина одной секции составляет, как правило, от 30 до 60 сантиметров. Это объясняется тем, что конкурирующие производители стремятся выпускать как можно более уникальную продукцию. Кроме того, различные модели также могут иметь разные габаритные размеры. Типовые же изделия обычно имеют глубины 92, 99 и 110 мм.
На современном рынке можно встретить и множество дизайнерских модификаций. Высота чугунных батарей всегда больше межосевого расстояния и всегда может быть увеличена, если прибор планируется устанавливать на пол. Площадь одной секции чугунной батареи составляет около 0,25 кв. м.
Срок службы чугунных батарей отопления
Чугунные радиаторы служат десятилетиями, зачастую без ремонта. Поэтому, установив такие обогреватели, можно в ближайшие лет 20-25 не думать о замене батарей. Давление, которое считается рабочим для чугунных батарей, составляет 9 атмосфер, это дает возможность устанавливать их и в автономных, и в центральных системах отопления.
В домах дореволюционной постройки такие батареи исправно служат и по сей день. А ведь они были отлиты более 100 лет назад.
Помимо всего прочего, чугунные батареи спокойно переносят летний слив теплоносителя и не теряют своих свойств до следующего отопительного сезона.
Зная технические характеристики и то, сколько весит батарея чугунная, из соображений практичности лучше доверить расчет и монтаж специалистам, чем пытаться самому выполнять работу. Тогда не придется расстраиваться из-за совершенных ошибок.
fb.ru
Вес одной секции чугунной батареи
Чугунные радиаторы — немного общей информации
Чугунные радиаторы, или, как их ещё называют, батареи отопления, применяются для отопления помещений около ста лет. Они были изобретены в 1857 году Францем Сан-Галли. Их используют как для обогрева жилых квартир, так и в производственных помещениях, складах, офисах и тому подобное. Такая популярность этого вида обогревателей объясняется свойствами чугуна в первую очередь.
Рассмотрим их подробнее:
- Долговечность в использовании;
- Устойчивость к коррозии;
- Нетребовательность к условиям внешней среды и эксплуатации;
- Нетребовательность к выбору обогревающей жидкости;
- Высокая теплопередача.
Все эти факторы являются причиной того, что человечество уже дольше века использует для отопления чугунные батареи.
Однако, чугун имеет серьёзный недостаток – это достаточно хрупкий материал. Случайный удар может привести к образованию микроповреждений и в дальнейшем – к утечкам воды и разрушению радиатора, если учесть, что в момент эксплуатации он находится под давлением изнутри.
К недостаткам можно также отнести сложность домашнего ухода – поверхность батареи ребриста, имеет много неровностей и закутков, где скапливается пыль, которую сложно вытереть. Ну и совершенно неэстетичный внешний вид, что немаловажно для многих владельцев квартир.
Конструкция батареи отопления из чугуна
Устроен радиатор довольно несложно – его собирают из составляющих, количество которых может варьироваться от 4 до 10, в зависимости от размеров помещения и того, насколько интенсивного обогрева требует помещение. Секции соединяются между собой ниппелями, а в качестве прокладок между ними используют, как правило термостойкую резину или паронит. Секции расположены вертикально, что увеличивает площадь нагревательного элемента и его теплоотдачу.
По секциям происходит циркуляция теплоносителя – обогревающей жидкости. Чугун тем хорош, что не предъявляет особых требований к теплоносителю – а это в наших условиях очень важно, поскольку теплоноситель идёт по длиннейшим подземным коммуникациям, несёт в себе кусочки шлака, окалины, различного мусора, что способно изнутри повреждать каналы в радиаторах.
Этому виду обогревателей свойственна очень высокая инертность – они чрезвычайно медленно нагреваются и медленно остывают. По этой причине регулировка температуры просто не имеет смысла.
Из положительных характеристик следует также отметить низкое гидравлическое сопротивление – чугун не создаёт внутри секции трения с водой, соответственно не возникает помех для циркуляции. Поэтому часто отпадает потребность в принудительной циркуляции воды.
Радиаторы делятся на одноканальные и двухканальные. До сих пор они являются очень эффективным средством обогрева помещений.
Монтаж радиаторов отопления в помещениях
Отопительные батареи в помещениях монтируются на стену. К стене крепятся кронштейны, на которые фиксируется радиатор. Чугун – это материал с чрезвычайно большой массой, что создаёт определённые трудности при монтаже.
Совершенно очевидно, что вес всей батареи будет зависеть от того, скольковесит одна секция. Очень важно знать, скольковесит радиатор для того, чтобы правильно рассчитать нагрузку на крепления при монтаже.
Сколько весит одна секция радиатора из чугуна
Вес одной секции стандартной батареи МС 140 составляет 7,12 кг. Соответственно, при среднем количестве секций, равном 7, получаем, что общий вес батареи составит 50 кг.
Однако, сегодня предлагаются более современные модели иностранных производителей с более удобными характеристиками. Например, весоднойсоставляющей чешской батареи Viadrus STYL 500 равен 3,8 кг. Для того, чтобы обеспечить нагревательный эффект, равный эффекту семисекционной МС 140, нам нужно будет установить 14 секций, масса которыхвместе с водой будет равна 64, 4 кг.
Можно рассмотреть также радиаторы MODERN марки EXEMET – здесь масса одной составляющей равна 3,2 кг. Для создания обогрева, аналогичного марке МС 140, нам нужно смонтировать 22 секции, масса которых составит 70,4 кг.
Следует отметить, что в современных постройках из пористых материалов прочность стен гораздо ниже. Поэтому крепление радиаторов на стенах подстраховывается наличием ножек, которыми система упирается в пол, снижая нагрузку на стену здания.
Заключение
Таким образом, мы приходим к выводу, что в наших условиях рано ещё отказываться от обогрева посредством чугунных батарей отопления. Их свойства делают их самым удобным средством обогрева помещений в наших условиях. Несмотря, на большую массу чугуна и некоторые неудобства в использовании, на сегодняшний день чугунные элементы отопления являются одними из самых широко используемых. Их стойкая репутация является свидетельством надёжности и эффективности.
mynovostroika.ru
Вес секции батареи из чугуна
Чугунная батарея считается одним из самых выгодных устройств для отопления дома, ведь кроме отличной теплопередачи, она радует высокой стойкостью к коррозии, длительным сроком службы (50 лет и старше) и нетребовательностью к качеству носителя тепла. Эти факторы стимулируют многих людей включать ее в свою индивидуальную систему отопления. При этом во время создания отопительной системы они вынуждены учитывать ее особенности. Одной из них является вес чугунной батареи.
Этот показатель является очень важным, поскольку позволяет:
- подобрать оптимальное крепление;
- выбрать нужный вид батареи в зависимости от конструктивных особенностей дома.
Классические батареи
К ним относят батарею МС 140. Она известна всем, ведь свое наибольшее распространение получила во времена Советского Союза. Сегодня ее также активно покупают. Она имеет несколько модификаций, но одна секция наиболее применяемого варианта весит 7,12 кг. Она рассчитана на 1,5 л воды. Поэтому общая масса одного сектора батареи составляет 8,62 кг. Именно эту цифру нужно учитывать при расчете массы, которую должно выдерживать крепление. Если же брать во внимание только вес самой батареи, то крепление, получив дополнительное давление от массы воды, может не выдержать.
Чтобы отопить комнату площадью в 20 м², нужно установить батарею с 12 секциями. А это значит, что вес пустого устройства отопления будет составлять 85,4 кг, а радиатора с водой — 103,4 кг.
Такая батарея должна устанавливаться на крепление, зафиксированное в стене. То есть получается, что стена должна выдержать дополнительную нагрузку в почти 104 килограммов. Если стену построили из кирпича или бетона, то такой чугунный радиатор можно спокойно вешать на стену.
Однако, если владелец решил сэкономить на строительстве дома и построил его из пенобетона, газобетона или SIP-панелей, наполненных пенопластом, то классическое подвешивание на такие стены 100-килограммовой конструкции является весьма плохой идеей.
Классический способ установки предусматривает фиксацию на стене горизонтальных кронштейнов с крючками на конце. На последние вешают батарею. Стены из пористых материалов или SIP-панелей просто не выдержат большое давление, и радиатор упадет на пол.
Конечно, выход в такой ситуации есть. Их даже три:
- Нужно использовать специальное крепление, которое следует фиксировать во многих точках. Это лишние затраты своих сил и времени. Однозначно такой вариант — не по душе каждому хозяину.
- Нужно устанавливать чугунные батареи современных модификаций. Они легче и эффективнее в плане обмена тепла.
- Выбирать модели с возможностью установки на пол.
Современные варианты радиаторов из чугуна
Они состоят из более легких секторов. Так, один из чешских производителей предлагает радиатор, одна секция которого весит 3,8 кг. При этом в ней может поместиться 0,8 литра воды. В результате общая масса сектора равняется 4,6 кг.
Для отопления вышеупомянутой комнаты нужно взять радиатор с 14 секциями. Он будет весить 64,4 кг. Эта цифра включает массу чугуна и воды.
Такой радиатор все еще будет тяжелым для стен из пористого материала, однако если его разбить на две части и разместить их на разных стенах, то о необходимости в дополнительных креплениях можно забыть.
Отечественные производители предлагают радиаторы с более легким сектором. Его характеристики таковы:
- Вес — 3,3 кг
- Объем — 0,6 л.
- Общий вес с водой — 3,9 кг.
Алгоритм расчета веса радиатора
Стоит сказать, что современные производители предлагают много модификаций чугунных радиаторов. Поэтому, чтобы во время оценки каждого варианта дать ответ на вопрос, сколько весит чугунная батарея, нужно выполнить действия:
- Узнать вес самой секции.
- Добавить вес воды, которая может поместиться в секции.
- Проанализировать теплоотдачу и, отталкиваясь от нее, определить необходимое количество секций.
- Умножить количество секций на общую массу одного сектора.
(3 голосов, рейтинг: 5,00 из 5) Загрузка…
poluchi-teplo.ru
Смотрите также
- Монтаж систем отопления и водоснабжения
- Нагревательный котел для отопления электрический
- Радиатор отопления биметалиический стал подтикать краска вспучилась
- Монтаж автономного отопления
- Схема подключения буферной емкости в систему отопления
- Газовое отопление загородного дома
- Монтаж двухтрубной системы отопления в частном доме своими руками
- Клапан подпитки системы отопления
- Радиаторы отопления стальные трубчатые
- Гелиосистема для отопления дома
- Гидроразделитель в системе отопления своими руками
Вес секции чугунной батареи старого образца
Содержание
- Сколько весит секция чугунной батареи
- Классические батареи
- Современные отопительные радиаторы из чугуна
- Заключение
- Рекомендуем:
- Сколько весит батарея чугунная.
Вес одной секции
- Преимущества чугуна
- Особенности монтажа чугунных батарей
- Технические характеристики батарей из чугуна
- Расчет необходимого количества секций в батареях
- Размеры чугунного радиатора
- Срок службы чугунных батарей отопления
- Вес секции батареи из чугуна
- Классические батареи
- Современные варианты радиаторов из чугуна
- Алгоритм расчета веса радиатора
- Похожие статьи:
Сколько весит секция чугунной батареи
Когда заходит речь о приобретении и установке отопительных приборов из чугуна, то первая же ассоциация – это тяжеленный советский радиатор и все трудности перемещения и монтажа, что с этим связаны. В действительности разновидностей этих приборов появилось очень много, их масса варьируется в широком диапазоне. Нашей целью стоит донести, сколько весит секция чугунной батареи различной конфигурации и решение проблем, связанных с этим.
Классические батареи
И правда, 1 секция классической советской батареи МС 140, имеющейся в продаже и по сей день, отличается немалой массой – 7. 12 кг. Если учесть тот факт, что объем одной секции чугунной батареи МС 140 составляет 1.5 л воды, то общая масса получится 8.62 кг. Зная, что тепловая мощность каждой секции ориентировочно равна 170 Вт, то для помещения средней площади 20 м2 потребуется 12 таких секций, это по массе составит 85.4 кг, а вместе с водой – 103.4 кг.
Примечание: здесь и далее для лучшего понимания вопроса приводится пример укрупненного расчета тепловой мощности и количества секций.
Вы можете сказать, что необязательно ставить один большой прибор, можно же разделить его на два, и будете правы. Тем не менее чистый вес чугунных батарей старого образца тогда будет составлять 43 кг. что по правилам охраны труда не допускается поднимать одному человеку, потребуется помощник.
Вторая проблема заключается в том, что классические радиаторы предназначены только для настенного крепления, а подавляющее большинство современных домов строится из пористых материалов, в лучшем случае из газобетона или пенобетона, в худшем – из SIP-панелей с наполнением из пенопласта. К таким стенам потребуется специальное крепление для чугунных радиаторов сложной конструкции с фиксацией во многих точках, что вряд ли вам понравится.
Современные отопительные радиаторы из чугуна
Для настенного крепления существуют новые изделия из серого чугуна от различных производителей, чья масса гораздо меньше традиционных МС 140. Например, чешский радиатор отопления Viadrus STYL 500, изображенный на рисунке.
Его характеристики таковы: масса 1 секции – 3.8 кг, вместительность по воде – 0.8 л, итого выходит 4.6 кг. При располагаемом тепловом потоке 140 Вт на нашу комнату 20 м2 потребуется 14 шт, что по весу будет 64.4 кг вместе с водой. Данный показатель на 40% меньше, чем у МС 140, а разделив его на 2 части (по 32 кг каждый прибор), становится ясно, что возможна установка чугунных радиаторов на стены из пористого бетона без специальных дополнительных придумок.
Еще более легкую конструкцию предлагает российский производитель, продающий свои отопительные приборы под брендом EXEMET, а именно модель MODERN.
Здесь одна секция радиатора весит всего 3.2 кг при теплоотдаче 93 Вт, в помещение 20 м2 необходимо 22 секции общей массой 70.4 кг. Этот показатель тоже достаточно хороший, особенно если учитывать, что фирма изготавливает эти батареи с возможностью напольной установки.
Нельзя не сказать несколько слов о таком продукте, как винтажная чугунная батарея, чей вес еще больше советской МС 140 и в некоторых случаях достигает 14 кг. Эти отопительные приборы своим внешним видом напоминают старинные, устанавливаемые в резиденциях и усадьбах в далеком XIX веке.
Изображенная на рисунке модель EXEMET FIDELIA имеет вес 12 кг при теплоотдаче 156 Вт, что делает общий вес чугунного радиатора для нашего примера просто чудовищным – 154 кг. Но как видно на изображении, здесь вопрос установки решается иначе: первая и последняя секции имеют ножки для размещения нагревателя на полу.
Заключение
В наше время есть возможность подобрать чугунный прибор отопления применительно к разным условиям монтажа, в том числе и по весу. Благодаря напольной установке слишком тяжелым винтажным батареям даже не нужны кронштейны для крепления, разве что в качестве дополнительной фиксации к стене.
Рекомендуем:
Технические характеристики чугунных радиаторов МС 140 Как сложить печь для бани из кирпича Обзор радиаторов отопления: какие батареи лучше поставить?
Сколько весит батарея чугунная. Вес одной секции
November 28, 2016
Чугунные батареи существуют уже более века. И сегодня этот вид отопительных радиаторов продолжает обогревать человеческие жилища, ничуть не уступая более современным компактным конвекторам и аллюминиевым аналогам.
Преимущества чугуна
Чугун имеет массу неоспоримых достоинств. Он долговечен, стоек к коррозии, обладает высокой теплоэффективностью. Выпускаемые чугунные батареи в ретро-стиле поражают своей красотой. Да и современные обычные чугунные батареи выглядят очень привлекательно, выгодно отличаясь эффектным дизайном.
У чугунных батарей есть один недостаток — их вес. Сколько весит чугунная батарея, можно понять, приняв во внимание, что вес одной только секции колеблется от 7 до 7,5 кг. Среди современных разработок есть и более легкие модификации. У них вес секции составляет всего 5,7 кг.
Особенности монтажа чугунных батарей
Поскольку монтаж производится на стенки и перегородки, а они часто бывают выполнены из непрочного материала, то важно знать точно, сколько весит одна секция чугунной батареи. Это нужно для того, чтобы расчитать вес общей нагрузки. Если окажется, что расчетная нагрузка выше норматива, то от такой установки придется отказаться полностью, либо нужно будет делать специальные крепления, чтобы батарея не сломала стену, либо установить отопительную батарею на полу.
Обычно стандартные чугунные батареи состоят из нескольких секций — секционных элементов. Как правило, их количество колеблется от 4 до 10. Но иногда встречаются и батареи с 20 и более секциями. Но использовать такие громоздкие радиаторы неудобно, поэтому на практике обычно устанавливают несколько батарей, по 5-7 секций в каждой. Обычно габариты современной секции чугунной батареи составляют 140 х 500 мм. Рассчитать массу всей батареи несложно, зная точный вес одной секции.
К примеру, нужно определить, сколько весит батарея. Чугунная секция весит 7,5 кг. Следовательно, набор из семи секций будет весить 49-52,5 кг. Такая же батарея, но уже из десяти секций, окажется весом около 75 кг. Необходимо учитывать и то, что это вес батареи без учета веса теплоносителя.
Средний объем одной секции чугунной батареи составляет около 1,5 литра жидкости. Есть и более экономичные модели, с объемом от 1 литра. При решении вопроса о том, сколько весит старая чугунная батарея, необходимо знать, что в старых образцах чугунных батарей объем жидкости достигал 1,7 литра на секцию. Поэтому после запуска системы вес приборов увеличивается.
Технические характеристики батарей из чугуна
Чтобы правильно определить необходимое количество секций в источнике тепла, важно учитывать и другие характеристики чугунных батарей. Главным показателем эффективности радиатора отопления является мощность. Если точно знать мощность одного радиатора, то несложно определить и общее количество, которое требуется для обеспечения жилья теплом.
При неверном расчете нужного количества радиаторов отопления в помещении появится излишняя сухость воздуха, а это не менее неприятно, чем недостаток тепла. На радиаторах будет нагреваться осевшая пыль, из-за необходимости частого проветривания увеличатся сквозняки.
Номинальная тепловая мощность одной секции чугунного радиатора рядовой модификации составляет 160 Вт. При расчете размера каждого устанавливаемого радиатора необходимо сначала узнать, сколько весит чугунная батарея. 1 секция берется за стандарт. Затем нужно определить, какова величина теплового потока отапливаемого жилья. Эта характеристика во многом зависит от того, из какого материала выполнены стены, какова теплоизоляция дома, насколько профессионально установлены окна в здании.
Так, в панельных домах тепловой поток составляет около 0,041 кВт/м 3. В кирпичных строениях этот показатель уже составляет 0,034 кВт/м 3. А при качественно выполненной теплоизоляции — 0.02 кВт/м 3. В последнем примере не имеет значения, из чего построены стены.
Расчет необходимого количества секций в батареях
После определения того, сколько весит батарея чугунная, необходимо расчитать необходимое число звеньев в радиаторе либо количество приборов, которое нужно установить в отдельно взятом помещении. Ту цифру, которая обозначает объем комнаты, умножаем на величину теплового потока помещения, полученную цифру делим на тепловой поток одной секции. Его величина составляет 0,160 кВт.
Полученную в результате вычислений цифру нужно округлить до целого — это и будет количество требуемых секций. При этом нет необходимости соединять все секции в один радиатор. Лучше распределить их в нескольких приборах, установив по одному под каждым оконным проемом. Вычислим таким образом, сколько весит батарея. Чугунная весит намного больше, это мы уже выяснили. Осталось определиться с местом для установки радиатора.
Размер оконного проема также влияет на выбираемое количество секций в устанавливаемом радиаторе. Чтобы использовать всю мощность отопительного прибора, его длина должна быть шире окна не менее чем на 70-75 %. При этом сам радиатор должен быть расположен на расстоянии от 8 до 12 см от подоконника.
Размеры чугунного радиатора
Отдавая дань традициям, радиаторы выпускают общепринятых размеров, обеспечивая этим еще и эффективную работу и безопасность отопления. Ширина одной секции составляет, как правило, от 30 до 60 сантиметров. Это объясняется тем, что конкурирующие производители стремятся выпускать как можно более уникальную продукцию. Кроме того, различные модели также могут иметь разные габаритные размеры. Типовые же изделия обычно имеют глубины 92, 99 и 110 мм.
На современном рынке можно встретить и множество дизайнерских модификаций. Высота чугунных батарей всегда больше межосевого расстояния и всегда может быть увеличена, если прибор планируется устанавливать на пол. Площадь одной секции чугунной батареи составляет около 0,25 кв. м.
Срок службы чугунных батарей отопления
Чугунные радиаторы служат десятилетиями, зачастую без ремонта. Поэтому, установив такие обогреватели, можно в ближайшие лет 20-25 не думать о замене батарей. Давление, которое считается рабочим для чугунных батарей, составляет 9 атмосфер, это дает возможность устанавливать их и в автономных, и в центральных системах отопления.
В домах дореволюционной постройки такие батареи исправно служат и по сей день. А ведь они были отлиты более 100 лет назад.
Помимо всего прочего, чугунные батареи спокойно переносят летний слив теплоносителя и не теряют своих свойств до следующего отопительного сезона.
Зная технические характеристики и то, сколько весит батарея чугунная, из соображений практичности лучше доверить расчет и монтаж специалистам, чем пытаться самому выполнять работу. Тогда не придется расстраиваться из-за совершен ных ошибок.
Вес секции батареи из чугуна
Чугунная батарея считается одним из самых выгодных устройств для отопления дома, ведь кроме отличной теплопередачи, она радует высокой стойкостью к коррозии, длительным сроком службы (50 лет и старше) и нетребовательностью к качеству носителя тепла. Эти факторы стимулируют многих людей включать ее в свою индивидуальную систему отопления. При этом во время создания отопительной системы они вынуждены учитывать ее особенности. Одной из них является вес чугунной батареи.
Этот показатель является очень важным, поскольку позволяет:
- подобрать оптимальное крепление ;
- выбрать нужный вид батареи в зависимости от конструктивных особенностей дома.
Классические батареи
К ним относят батарею МС 140. Она известна всем, ведь свое наибольшее распространение получила во времена Советского Союза. Сегодня ее также активно покупают. Она имеет несколько модификаций, но одна секция наиболее применяемого варианта весит 7,12 кг. Она рассчитана на 1,5 л воды. Поэтому общая масса одного сектора батареи составляет 8,62 кг. Именно эту цифру нужно учитывать при расчете массы, которую должно выдерживать крепление. Если же брать во внимание только вес самой батареи, то крепление, получив дополнительное давление от массы воды, может не выдержать.
Чтобы отопить комнату площадью в 20 м², нужно установить батарею с 12 секциями. А это значит, что вес пустого устройства отопления будет составлять 85,4 кг, а радиатора с водой — 103,4 кг.
Такая батарея должна устанавливаться на крепление, зафиксированное в стене. То есть получается, что стена должна выдержать дополнительную нагрузку в почти 104 килограммов. Если стену построили из кирпича или бетона, то такой чугунный радиатор можно спокойно вешать на стену.
Однако, если владелец решил сэкономить на строительстве дома и построил его из пенобетона, газобетона или SIP-панелей, наполненных пенопластом, то классическое подвешивание на такие стены 100-килограммовой конструкции является весьма плохой идеей.
Классический способ установки предусматривает фиксацию на стене горизонтальных кронштейнов с крючками на конце. На последние вешают батарею. Стены из пористых материалов или SIP-панелей просто не выдержат большое давление, и радиатор упадет на пол.
Конечно, выход в такой ситуации есть. Их даже три:
- Нужно использовать специальное крепление, которое следует фиксировать во многих точках. Это лишние затраты своих сил и времени. Однозначно такой вариант — не по душе каждому хозяину.
- Нужно устанавливать чугунные батареи современных модификаций. Они легче и эффективнее в плане обмена тепла.
- Выбирать модели с возможностью установки на пол.
Современные варианты радиаторов из чугуна
Они состоят из более легких секторов. Так, один из чешских производителей предлагает радиатор, одна секция которого весит 3,8 кг. При этом в ней может поместиться 0,8 литра воды. В результате общая масса сектора равняется 4,6 кг.
Для отопления вышеупомянутой комнаты нужно взять радиатор с 14 секциями. Он будет весить 64,4 кг. Эта цифра включает массу чугуна и воды.
Такой радиатор все еще будет тяжелым для стен из пористого материала, однако если его разбить на две части и разместить их на разных стенах, то о необходимости в дополнительных креплениях можно забыть.
Отечественные производители предлагают радиаторы с более легким сектором. Его характеристики таковы:
- Вес — 3,3 кг
- Объем — 0,6 л.
- Общий вес с водой — 3,9 кг.
Алгоритм расчета веса радиатора
Стоит сказать, что современные производители предлагают много модификаций чугунных радиаторов. Поэтому, чтобы во время оценки каждого варианта дать ответ на вопрос, сколько весит чугунная батарея, нужно выполнить действия:
- Узнать вес самой секции.
- Добавить вес воды, которая может поместиться в секции.
- Проанализировать теплоотдачу и, отталкиваясь от нее, определить необходимое количество секций.
- Умножить количество секций на общую массу одного сектора.
Похожие статьи:
Чугунные или биметаллические батареи Подбор батареи отопления по площади квартиры Количество кВт одного сегмента радиатора из чугуна Как рассчитать теплоотдачу радиаторов из чугуна
Источники: http://cotlix. com/skolko-vesit-sekciya-chugunnoj-batarei, http://fb.ru/article/279785/skolko-vesit-batareya-chugunnaya-ves-odnoy-sektsii, http://poluchi-teplo.ru/radiatoryi/chugun/ves-sektsii-batarei-iz-chuguna.html
Как вам статья?
Сколько квт в 1 секции чугунного радиатора: преимущества, расчеты
Чтобы правильно определить число чугунных батарей, устанавливаемых в доме, потребуется ознакомиться с техническими характеристиками этих изделий. Одним из важнейших показателей эффективности их работы является тепловая мощность в кВт в 1 секции чугунного радиатора. При известном значении этого параметра нахождение количества звеньев, требуемых для обогрева конкретного помещения, не представляет особой сложности.
Содержание
- Достоинства чугунных батарей
- Отличие импортных батарей от отечественных
- Параметры некоторых образцов батарей
- Тепловая отдача современных моделей
- Простой расчет
- Сложный способ
- Специфика расчета
Достоинства чугунных батарей
Чугунные радиаторы не подвержены коррозии, поэтому служат дольше алюминиевых или стальныхК достоинствам чугунных батарей относят следующие свойства:
- стойкость к коррозии, совершенно не опасной для чугуна;
- высокий показатель по тепловой инертности;
- приемлемая цена и возможность увеличения количества секций;
- долговечность изделий.
При взаимодействии с теплоносителем внутренние поверхности чугуна покрываются особым налетом типа «сухой ржавчины», препятствующим коррозии. Особенности материала и достаточная толщина стенок позволяют использовать в чугунных радиаторах теплоносители любого качества. Чугун практически не изнашивается со временем от разрушающего воздействия химических примесей и агрессивных сред.
Чугунные батареи привлекательны тем, что имеют свойство аккумулировать тепло, а затем отдавать его при отключении отопления или снижении температуры теплоносителя. К достоинствам изделий из чугуна также относят возможность наращивания или снятия несколько рабочих секций, простоту обслуживания и установки.
Чугунные изделия при условии регулярного ухода за ними способны прослужить своим владельцам довольно долгое время – не менее 30-40 лет.
Отличие импортных батарей от отечественных
Радиаторы нового типа отдают больше энергии, чем старые при одинаковых размерахЧугунные радиаторы, выпускаемые еще во времена СССР, имели широкий разброс параметров и размеров. Независимо от этого тепловая мощность была примерно одинакова, что позволяло устанавливать их в разных по площади помещениях. Зарубежные чугунные батареи имеют меньшие габариты с той же тепловой отдачей.
При рассмотрении материала чугуна, используемого в том и другом случае, наблюдается небольшая разница в химическом составе и структуре рабочих поверхностей. У отечественных батарей она сильно шероховатая, что создает значительное по величине сопротивление перемещению теплоносителя и снижает показатели тепловой отдачи. Зарубежные аналоги обладают абсолютно гладкой поверхностью стенок, гарантирующей беспрепятственное передвижение жидкости по внутренним полостям. Поэтому импортные устройства пропускают больший объем нагретой воды в единицу времени и отдают больше тепловой энергии. В итоге показатель мощности повышается, что допускает их использование в помещениях со значительной площадью (до 30 м2 и более).
Параметры некоторых образцов батарей
Сравнительная мощность 1 секции радиаторов по импортным и отечественным производителямВ далекие советские времена батареи марки МС-140 можно было встретить практически в каждой квартире, а сегодня они многими воспринимаются как пережиток прошлого. Однако некоторые пользователи до сих пор предпочитают их всем другим известным моделям. Их почитатели обычно выбирают следующие две модификации:
- у первой модели мощность 1 секции чугунного радиатора в кВт составляет 0,120 единиц;
- для второго образца этот показатель равен 0,190 киловатта.
Последние значительно больше по размерам и намного тяжелее – высота и ширина секций составляет 0,588 и 0,121 метра соответственно. Объем внутренних полостей у одного такого сегмента равен 1,5 литрам.
Тепловая отдача современных моделей
По тепловым характеристикам современные образцы изделий на основе чугуна отличаются большим разнообразием. Соответствующие модели из Чехии имеют высокие показатели по эффективности обогрева жилых пространств. Образцы под наименованием Viadrus STYL 500 состоят из секций, каждая из которых позволяет развивать тепловую мощность порядка 0,14 кВт. При этом ее сегменты почти в два раза легче и меньше по габаритам большинства известных отечественных моделей.
Секция батарей Viadrus STYL 500 вмещает в себе 0,8 литра теплового носителя. Российские аналоги с примерно тем же объемом имеют чуть меньшую отдачу, соответствующую показателю в 0,102 кВт. Они немного уступают чешским изделиям, но превосходят МС-140.
Простой расчет
Для простейшего расчета тепловой мощности батареи, в которой нуждаются помещения площадью 25 м2, потребуется вычислить объем комнаты: 25 м2 умножить на высоту 2,5 метра, получается 62,5 куб. метра. Результат вычислений умножить на удельную мощность, значение которой выбирается в зависимости от типа помещения. Для панельного дома она равен 0,041 кВт на м3. При окончательном подсчете получается: 62,5х0,041=2,562 кВт, что является показателем общей тепловой мощности, которой будет достаточно для обогрева площади в 25 м2.
Согласно простой формуле расчета далее итог вычислений делится на мощность одной секции: 2,562/0,14 кВт = 18,3. Это значение округляется до 19-ти, получается искомое число звеньев в батарее. Потребуется купить две батареи с 10 и 9 сегментами.
Во время расчета следует помнить, что выбранный в нем поправочный коэффициент принимает разные значения. Для зданий, отстроенных из кирпича, он равен 0,034 кВт/метр. Для современных блочных построек его величина составляет 0,02 кВт/метр. Ориентируясь на представленные методики, удается вычислить количество секций и цельных батарей, необходимых для отопления всех комнат в доме или квартире.
Сложный способ
Формула расчета тепловой нагрузкиЭтот метод предусматривает использование сразу двух параметров: общей потребности обогреваемого объекта в тепле и тепловой отдаче одной секции радиатора (это значение берется из технических справочников). При вычислении первого из этих показателей учитываются следующие факторы:
- площадь обогреваемого помещения;
- этажность здания;
- высота потолка в квартире;
- наличие в доме кондиционера и отопительного камина;
- количество и общая площадь окон.
Также учитывается наличие утепления на стенах, на полу и потолке.
Потребность в количестве тепла для выбранного помещения находится в следующей последовательности:
- Определяется его объем (площадь перемножается с высотой).
- Результат умножается на 41 Ватт (согласно СНИП такое количества тепла нужно для комфортного обогрева одного 1 куб. метра жилой площади).
- Полученный результат корректируется в зависимости от точного значения высоты потолка.
В зависимости от расположения комнат и высоты потолков поправочные коэффициенты принимают значения 0,8, 1,1 и 1,8. С их учетом полученный результат делят на удельную теплоотдачу секции и вычисляют требуемое число звеньев.
Специфика расчета
При расчете вводятся поправки на количество окон и дверейСовременные изготовители чугунной обвязки предлагают своим клиентам батареи с различными рабочими параметрами, определяющими широкий диапазон удельных мощностей. Известно несколько методик проведения технических расчетов, касающихся определения эксплуатационных характеристик радиаторов. Простые и более сложные алгоритмы позволяют находить нужные показатели с заданной степенью точности (погрешностью) и при необходимости корректировать их.
При введении поправочных коэффициентов учитываются многие факторы, включая количество дверей и окон в помещении. При увеличении указанных элементов конструкции хотя бы на единицу в общем случае к полученному результат добавляется одна секция. Такую же поправку приходится вводить при учете материала, из которого изготовлен оконный или дверной проем.
Обход огромных объемных деформаций в анодах сплавов литиевых батарей
- Список журналов
- Нац Коммуна
- PMC7154030
Нац. коммун. 2020; 11: 1584.
Опубликовано в сети 13 апреля 2020 г. doi: 10.1038/s41467-020-15452-0
, 1 , 2 , 2 , 3 , 3 , 1 and 1
Author information Article notes Copyright and License information Disclaimer
- Supplementary Materials
- Заявление о доступности данных
С момента выпуска литий-ионных батарей элементы (такие как кремний, олово или алюминий), которые могут быть сплавлены с литием, должны были использоваться в качестве анодных материалов из-за большей емкости. Однако их успешное применение не было осуществлено из-за резкой структурной деградации, вызванной циклическим изменением большого объема во время реакций батареи. Чтобы продлить срок службы анодов из сплава, мы должны избежать огромных объемных деформаций, сопровождающихся введением/удалением лития.
Тематические термины: Батареи, металлы и сплавы
Аккумуляторы являются незаменимыми устройствами в современном обществе, и они постоянно совершенствуются в сторону повышения плотности энергии и увеличения срока службы 1 , 2 . В литий-ионных батареях (LIB) в качестве репрезентативной перезаряжаемой батареи комбинация катода из оксида переходного металла интеркаляционного типа и углеродистых материалов анода добилась большого успеха и завоевала текущий рынок устройств накопления энергии 3 – 5 . Однако, поскольку плотность энергии обычных ЛИА постепенно достигла теоретического предела, необходимы дальнейшие подходы для разработки превосходных батарей 6 , 7 . В качестве многообещающего подхода ожидалось, что материалы анода из сплава с высокой емкостью, такие как Si, Sn или Al, для практического применения в современных литиевых батареях из-за их гораздо (в три-десять раз) большей емкости, чем у обычного графитового анода.
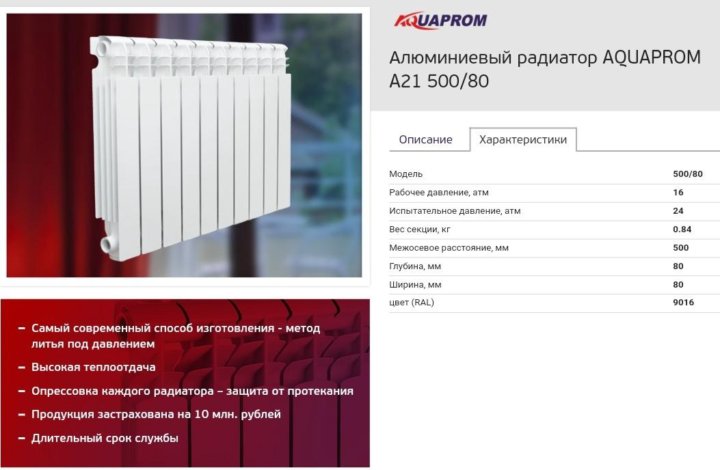
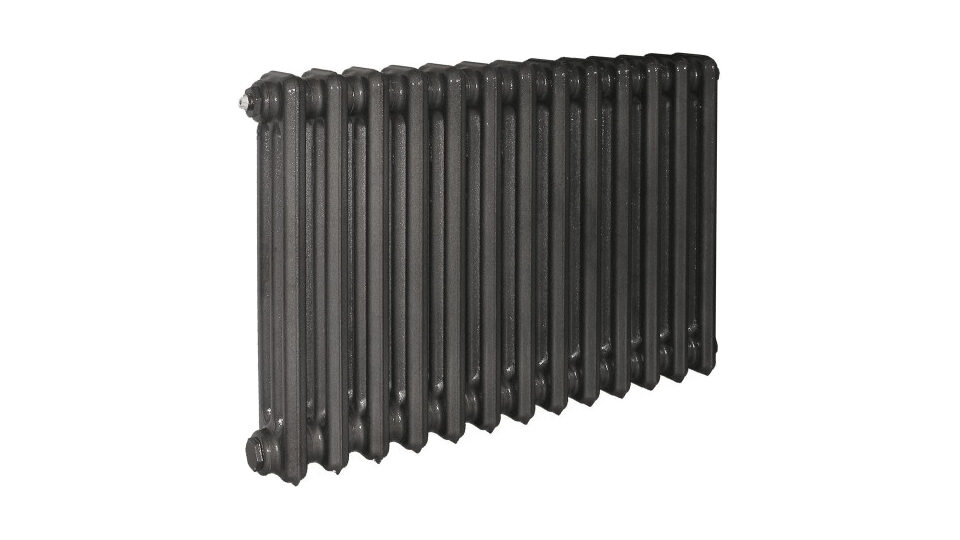
Тем не менее, применение анодов из сплавов по-прежнему остро востребовано для простой в производстве стратегии крупномасштабных ЛИА. В этой работе, чтобы установить концепцию «электрода из одного материала», который сочетает в себе активный материал и коллектор, мы показываем инновационный способ, как обойти такую огромную объемную деформацию, используя металлургические точки зрения, такие как термодинамика, упругая деформация и диффузия. . Изучая структурную стабильность различных электродов из металлической фольги во время литирования, мы демонстрируем, что алюминиевая фольга с соответствующей твердостью может использоваться в качестве автономного анода для литиевых батарей. Соответствующая твердость матрицы и определенная устойчивость к нестехиометрии образующегося интерметаллического соединения могут вызвать двумерную (в плоскости) гомогенную реакцию литирования и одномерную (вне плоскости) взаимную диффузию, чтобы удерживать Гиббс- Соотношение Дюгема, которое эффективно обходит влияние объемной деформации во время реакции батареи и фатальную проблему измельчения анодов из сплава.
Морфология после первоначального литирования в различные металлы
Для изучения структурной стабильности анодов из металлической фольги фольги Al, Zn и Sn были литированы в ячейках монетного типа с литиевым противоэлектродом, в котором электролит, состоящий из 1 M LiPF 6 и этиленкарбонат (EC) : диметилкарбонат (DMC) в эквиобъемном соотношении (50:50) использовали для всех электрохимических испытаний. В целом твердость материалов должна в значительной степени влиять на структурную стабильность после литирования. Так, что касается алюминиевых фольг, мы изготовили три типа образцов с различной твердостью, изменяя чистоту и контролируя условия прокатки и термообработки. Твердость по Виккерсу (HV) каждой фольги показана на рис. Фольги литировали до катодного заряда 5 мАч см −2 при плотности тока 0,5 мА см −2 . Как показано на рис., литированные фольги имеют совершенно разный внешний вид.
Открыть в отдельном окне
Структурная стабильность различных металлических фольг после первичного литирования.
a Фотографии различных металлических фольг после литирования 5 мАч см −2 . Средняя твердость по Виккерсу (HV) каждой фольги указана на верхнем графике. Литирование проводилось при плотности тока 0,5 мА см −2 с противоэлектродом из литиевого металла. Первоначальная толщина и процент литирования каждой фольги также указаны на фотографии лицевой стороны. Процентное значение литирования в каждом образце отображается на основе общей емкости каждого анода в зависимости от толщины фольги. Что касается Zn, процентное содержание не представлено, так как металлический Li в основном осаждается на поверхности вместо образования сплава Li-Zn; см. также дополнительный рисунок 1c . После прокатки алюминиевая фольга (99,99%) демонстрирует гомогенное литирование на лицевой стороне и достаточно устойчивую алюминиевую матрицу на обратной стороне. b Схематические иллюстрации процесса литирования, разумно сделанные из изображений СЭМ, полученных для соответствующих фольг; см. дополнительный рис. 1 .
Во-первых, интересно отметить, что мягкие металлы менее HV 30, фольга Sn (чистота 99,9%) и отожженная фольга 4N-Al (чистота 99,99%, далее именуемая «Al4N-HT») локально деформируются пластически после литирования. Волнистость матрицы, образованная сплавлением лития на лицевой стороне (обращенной к литий-металлическому противоэлектроду), распространяется на всю матрицу. Кроме того, литирование происходит неоднородно, что свидетельствует о сильном влиянии механической (упруго-пластической) деформации матрицы на процесс литирования. В отличие от мягкой фольги, жесткая прокатанная фольга 2N-Al (чистота 99,8%) демонстрирует очень разное поведение литирования. На лицевой стороне выступающие зерна AlLi растрескиваются (идентификация фаз позже показана на рис. ), что свидетельствует о том, что растущий сплав AlLi не мог деформировать алюминиевую матрицу, а наоборот, был раздавлен твердой алюминиевой матрицей. В то время как на задней стороне наблюдаются углубления, что позволяет предположить, что вязкое разрушение происходит из-за большого растягивающего напряжения, вызванного выступающими зернами AlLi на передней стороне. Детали морфологии показаны на дополнительном рисунке 9.0015 1а .
Открыть в отдельном окне
Процессы литирования-делитирования фольги Al4N-AR (чистота 99,99%, Al после прокатки) и фольги Al4N-HT (чистота 99,99%, хорошо отожженный Al).
а Изменения морфологии (I, II, II, IV) на лицевой стороне (обращенной к Li-электроду) Al4N-AR в процессе литирования и делитирования и картина ДОЭ исходного состояния. Al4N-AR демонстрирует гомогенное литирование и сохраняет стойкий слой алюминиевой матрицы с хорошей стабильностью структуры. b Сечение голой фольги Al4N-AR. c Поперечное сечение фольги Al4N-AR с содержанием 53% лития. Между литированной фазой и алюминиевой матрицей наблюдается очень плоская граница раздела. Литированный слой становится вдвое толще, что позволяет предположить, что объемное расширение происходит в направлении нормали к алюминиевой фольге (т. е. одномерно). d Рентгеновские профили, полученные в геометрии отражения для фольги Al4N-AR до и после литирования. e Поперечное сечение фольги Al4N-AR, подвергшейся литированию на 47% и последующему делитированию на 26%. Матрица Al самоорганизуется, образуя столбчатую структуру во время делитирования. f Изменения морфологии (I, II, III, IV) на лицевой стороне Al4N-HT при литировании и делитировании, а также картина ДОЭ исходного состояния. Зерна AlLi формируются неоднородно, что приводит к их измельчению при делитировании. г Поперечное сечение фольги Al4N-HT, литированной на 26 %, где фаза AlLi проникает в фольгу, сопровождающуюся пластической деформацией. h Вид сзади на фольгу Al4N-HT, прошедшую 53% цикл литирования и делитирования. Фольга измельчается во время делитирования. Масштабные полосы на изображениях SEM составляют 20 мкм для a – f и 100 мкм для г , h .
EBSD-картины алюминиевых матриц, вставленные в a и f , указывают на заметный рост зерен при рекристаллизации Al4N-HT. Масштабные полосы на диаграммах EBSD составляют 30 мкм и 1 мм для Al4N-AR и Al4N-HT соответственно. Цифры в процентах литирования отображаются на основе общей емкости алюминиевой фольги.
Самое главное и неожиданное, фольга 4N-Al после прокатки (чистота 99,99%, известная как «Al4N-AR») достигает гомогенного литирования на лицевой стороне, а алюминиевая матрица остается неповрежденной на обратной стороне. Таким образом, представляется, что соответствующая твердость матрицы предотвратит деформацию матрицы анода и разрушение фазы сплава; в случае Al/AlLi наиболее подходящая твердость в итоге оказывается ок. HV 35. Отсутствие видимой пластической деформации в матрице означает, что объемное расширение при литировании происходит в нормальном (т. е. вне плоскости) направлении, т. е. происходит однонаправленный рост литированной фазы. Напротив, несмотря на прокат Zn (чистота 99,9%) имеет твердость матрицы, аналогичную Al4N-AR, Li практически осаждается на поверхности Zn-фольги, а не образует сплав Zn-Li. Это различие можно отнести к диффузионной способности Li в Zn и энергии активации литирования и т.д. С подробным пояснением в дополнительном примечании 1 изображения сканирующей электронной микроскопии (СЭМ), соответствующие рис., приведены на дополнительном рис. 1 , а профили потенциала показаны на дополнительном рис. 9.0015 2 для сравнения.
Достижение гомогенного и однонаправленного литирования
Чтобы понять различия в степени гомогенности реакции литирования и в характерной особенности объемного расширения, мы наблюдали изменения морфологии, сопровождаемые введением и извлечением Li, результаты которых суммированы на рис. . . На рисунке показаны изображения Al4N-AR с автоэмиссионным излучением (FE-SEM) в процессе литирования (I, II и III) и делитирования после литирования (IV), а на рисунке также показаны изображения Al4N-HT. На ранней стадии (I–II) литирования фаза AlLi образуется на поверхности и вызывает выступы из-за объемного расширения (увеличение примерно на 100% для Al до AlLi). Как установлено из карт энергодисперсионной рентгеновской спектроскопии (EDX), интенсивность Al Kα значительно снижается на выступах; поскольку элемент Li не может быть обнаружен с помощью EDX, уменьшение интенсивности Al Kα прямо указывает на более высокий состав Li в таких выступающих областях, соответствующих образованию AlLi. Следует отметить, что размеры зерен AlLi в этих двух случаях сильно различаются. Как видно из картин дифракции обратного рассеяния электронов (EBSD) на рис. , размер кристаллов в Al4N-AR намного меньше, чем в Al4N-HT; таким образом, кажется, что размер зерен AlLi в каждой фольге может отражать размер кристаллов в каждой из них на ранней стадии литирования. Сравнивая отображения EDX для Al4N-AR и Al4N-HT, можно обнаружить, что вокруг выступов (черные) в Al4N-HT есть области светлого цвета (серые), а в Al4N-HT такой области нет.
Это указывает на то, что для мягкой матрицы Al4N-HT литированные области также могут расти локально, начиная с выступающих зерен AlLi, что убедительно подтверждается появлением большого количества линий скольжения дислокаций, наблюдаемых на изображениях СЭМ.
При дальнейшем литировании (от II до III на рис. ) два образца демонстрируют принципиальное различие в морфологии. В Al4N-AR мелкие частицы AlLi формируются равномерно по всей поверхности, т. е. успешно достигается гомогенное литирование. С другой стороны, в Al4N-HT фаза AlLi растет преимущественно из уже набухших областей за счет литирования, где матрица Al пластически деформируется с большим количеством сдвигов. На рисунке показаны СЭМ-изображения поперечного сечения Al4N-AR до и после литирования соответственно. Примечательно, что очень плоская граница раздела AlLi проходит по направлению глубины от передней (т.е. обращенной к Li-электроду) стороны к задней и одновременно лицевая поверхность идет вверх, увеличивая толщину фольги. Толщина литированного слоя (~80 мкм) примерно в два раза больше толщины исходной фольги (~40 мкм), т. е. почти объемное расширение, вызванное превращением Al в AlLi, реализуется только вдоль внеплоскостной направление. Кроме того, сравнивая рис. и , можно обнаружить, что плотность тока будет влиять на частоту зародышеобразования на поверхности Al, поскольку в (III) при 0,5 мА см 9 образуется большое количество выступов AlLi.0015 -2 по сравнению с (II) при 0,05 мА см -2 . Однако на однонаправленное объемное расширение плотность тока не повлияет, если только рабочий потенциал не достигнет окислительно-восстановительного потенциала Li + /Li. На рисунке показано, что рентгенограмма (XRD) фольги Al4N-AR с 53% литием хорошо согласуется со стандартными данными для кристалла AlLi в базе данных неорганической кристаллической структуры (ICSD). При извлечении Li из литированной фольги Al4N-AR (от III до IV на рис.) матрица Al самоорганизуется, образуя столбчатую структуру со сколами и микропорами по механизму разложения пор 24 , тогда как в фольге Al4N-HT (с III по IV на рис.
) измельчение происходит с делитированием, начиная с зерен AlLi, ранее достигших тыльной стороны фольги, как показано на рис. .
Механизм из металлургического понимания
Для реализации однонаправленного образования AlLi, способного преодолеть огромную объемную деформацию, алюминиевый элемент матричного компонента должен вытекать изнутри на поверхность во время литирования. В противном случае объемная деформация неизбежно вызывается образованием соединения Li, что приводит к значительному износу электродов. Здесь, основываясь на точках зрения термодинамики, упругости и диффузии атомов, мы рассматриваем причину, по которой может происходить такое однонаправленное образование AlLi. На рисунке схематически показаны профили свободной энергии Гиббса в двойной системе Al-Li, в которых кривые свободной энергии, G ГЦК , G ОЦК и G AlLi , получены полуколичественно на основе термодинамической базы данных (ГЦК: твердый раствор Al, ОЦК: твердый раствор Li) 30015 . Согласно фазовой диаграмме Al-Li, внедрение Li в матрицу Al претерпевает двухфазную реакцию фаз ГЦК-Al/AlLi, где каждый химический потенциал в твердом растворе ГЦК Al и фазе AlLi должен быть равен в равновесном состоянии; мк LI в FCCAL = μ LI в Alli и μ AL в FCCAL = мкм AL в Alli , что указывается на желтый линия на рис. Фиг. Разность химических потенциалов Li между фазой AlLi и фазой чистого Li определяет электродвижущую силу ( эдс 0 на рис. ) реакции литирования, Al + Li = AlLi. Здесь мы хотим обсудить следующие два момента: (i) гомогенную реакцию Li на поверхности в плоскости и (ii) перенос Al к поверхности.
Открыть в отдельном окне
Механизм литирования на алюминиевом аноде.
a Кривые свободной энергии Гиббса в двойной системе Al-Li. Двухфазная реакция ГЦК-Al/AlLi Li-poor (состав Li C 2 ) происходит во время литирования. Химическая движущая сила реакции ГЦК-Al/AlLi (~ ЭДС 0 ) составляет около 0,38 эВ (желтая линия), но значение увеличивается, когда определенное количество энергии деформации накапливается за счет механической деформации (розовая линия). В принципе, рассмотрение локального равновесия ГЦК-Al/AlLi Li-poor достаточно, но вокруг поверхности во время литирования также необходим AlLi Li-rich /Al 2 Li 3 . b Схематическое изображение процессов литирования механически твердых и мягких алюминиевых фольг; (слева) Al4N-AR и (справа) Al4N-HT. Стадии (I, II, III и IV) соответствуют СЭМ-изображениям на рис. ; см. также дополнительный рис. 3 . Соответствующая твердость Al4N-AR обеспечивает однородное литирование. Поскольку коэффициент диффузии в фазе AlLi, обладающей упорядоченной решеткой, обычно ниже, чем в ГЦК-фазе Al, образование AlLi в оставшейся матрице Al является кинетически предпочтительным, тогда как уже деформированная матрица Al имеет тенденцию к термодинамической преимущественной атаке Li.
c Схематические профили градиентов электрического потенциала, состава и химических потенциалов Li и Al для иллюстрации механизма однонаправленного объемного расширения во время литирования на Al4N-AR. На вставках показано СЭМ-изображение и SIMS-картирование Li в ионно-лучевом поперечном сечении частично литированного Al4N-AR; изображения полного поля приведены на дополнительном рисунке 4 . Градиенты химического потенциала Li и Al, обусловленные градиентами соответствующих составов, вызывают взаимную диффузию Al и Li, максимальная движущая сила которой оценивается примерно в 0,25 эВ.
Давайте сначала обратимся к термину (i). Различие в твердости матрицы приводит к различным эффектам деформации при образовании соединения лития. Когда происходит пластическая деформация алюминиевой матрицы, в матрицу вводится большое количество дислокаций, так что свободная энергия Гиббса деформированной алюминиевой матрицы увеличивается, как показано G ГЦК S на рис. Тогда по соотношению Гиббса–Дюгема c Al dμ Al + c Li dμ Li = 0 двухфазное равновесное состояние должно сместиться, как показано розовой линией на рис. Следовательно, химический потенциал Li, по-видимому, снижается, а электродвижущая сила более или менее увеличивается. Этот эффект может быть основной причиной неоднородного литирования в более мягком электроде Al4N-HT. Поскольку мягкая алюминиевая матрица в электроде Al4N-HT не может выдерживать внутреннее напряжение, вызванное электрохимически растущей фазой AlLi, объемное расширение вызывает пластическую деформацию матрицы. Впоследствии Ли предпочел бы быть вставленным в такие нестабильные области, чтобы получить усиление химического потенциала. Кроме того, пластическая деформация связана с большим количеством дефектов решетки, которые облегчают диффузию Li в матрице Al. Как показано на рис. (справа), эти термодинамические и кинетические эффекты могут работать синергетически, и образование AlLi легко достигает обратной стороны, что приводит к разрушению и измельчению электрода при делитировании.
Напротив, как показано в фольге Al4N-AR на рис. , соответствующая твердость матрицы может обойти пластическую деформацию матрицы, т. е. соединение Li не может деформировать матрицу. В этом случае рост AlLi будет замедлен из-за упругих напряжений в матрице Al 17 . Кроме того, в отличие от случая более мягкой матрицы, в достаточно жесткой матрице не существует предпочтительной области для внедрения лития, так что литирование может происходить равномерно в оставшейся алюминиевой матрице на поверхности, что приводит к гомогенной реакции в плоскости.
Далее мы рассмотрим термин (ii), почему однонаправленная диффузия изнутри к поверхности компонента алюминиевой матрицы происходит после завершения гомогенного литирования на поверхности. На вставке к рис. показано СЭМ-изображение и соответствующее картирование элементов Li для поперечного сечения литированной фольги Al4N-AR, которая была приготовлена с помощью сфокусированного ионного пучка (FIB) и измерена с помощью времяпролетной масс-спектрометрии вторичных ионов (TOF). -СИМС). Интересно, что обнаружено, что состав Li в фазе AlLi несколько уменьшается от поверхности внутрь. Поскольку фаза AlLi допускает отклонение от стехиометрического состава в соответствии с фазовой диаграммой Al-Li, градиент состава может быть разрешен в одной фазе AlLi. Опять же, возвращаясь к соотношению Гиббса-Дюгема, не только химический потенциал Li, но и Al постепенно изменяется, как показано на рис. ; μ Al увеличивается, тогда как μ Li уменьшается от поверхности внутрь. Разница химического потенциала между поверхностью и внутренней частью оценивается примерно в 0,25 эВ для каждого элемента на основе термодинамической базы данных 38 . Градиент химического потенциала каждого элемента вызывает взаимную диффузию0089 Li = − M Li град μ Li , где M Al и M Li – подвижности элементов соответственно; таким образом, элемент Al течет изнутри к поверхности, тогда как элемент Li течет с поверхности внутрь.
Следовательно, граница раздела Al/AlLi постепенно перемещается внутрь матрицы Al, тогда как передняя поверхность AlLi растет в сторону противоэлектрода при перемещении поверхности. Этот одномерный механизм взаимной диффузии может обойти огромную объемную деформацию из-за литирования. Напротив, ранее мы пытались ограничить объемное расширение сплава Sn-Li (большинство интерметаллических соединений Sn-Li представляют собой линейные соединения) путем внедрения Sn в однонаправленную пористую структуру Cu 9 .0015 39 , но литирование происходило только на поверхности Sn без дальнейшей инфильтрации Li в матрицу Sn. Таким образом, разумно сделать вывод, что определенная устойчивость к нестехиометрии интерметаллических соединений лития имеет решающее значение для создания движущей силы взаимной диффузии.
Практическое применение к литиевой батарее с анодом из сплава
Наконец, мы приводим в качестве примера концепцию «электрода из одного материала», сочетающего активный материал и коллектор с использованием практичного алюминиевого анода без коллектора для литиевых батарей. На рисунке сравнивается конструкция литиевой батареи с алюминиевым анодом и обычной литий-ионной батареи. Фольга Al4N-AR собрана в качестве анода вместо обычного графитового композита; оставшийся слой алюминиевой матрицы, который необходим для поддержания стабильной структуры электрода, также может играть роль токосъемника, и в этом типе электрода больше не требуется использовать тяжелую медную фольгу, что заметно упростило бы процесс изготовления аккумуляторов. Как показано на рис. , анод из алюминиевой фольги частично литирован в процессе предварительной зарядки (начальное литирование), и когда Li обратно извлекается из литированного слоя в процессе первого разряда (делитирования), оставшаяся алюминиевая матрица сжимается, образуя столбчатая структура с образованием некоторых внутренних пор. Эта столбчато-пористая структура активного материала, которая может формироваться в процессе работы в начальном цикле литирования/делитирования, играет значительную роль для последующих циклических процессов заряда/разряда.
На рисунке показаны характеристики батареи LiCoO 9.0089 2 — алюминиевая ячейка; сохраняется почти 100% кулоновская эффективность и не наблюдается явного изменения морфологии после 120-го цикла. Профили потенциальной емкости для 10-го, 40-го, 70-го, 100-го и 120-го циклов представлены на рис. , где алюминиевый анод ведет себя стабильно при рабочем потенциале при 0,3–0,4 В относительно лития, хотя наблюдается небольшая деградация на LiCoO 2 катод. Чтобы подтвердить, сохраняется ли активный слой алюминия или расходуется на фрагментацию, мы сравнили морфологию поперечного сечения двух образцов, полученных после первоначального литирования 2 мАч см −2 и последующая десятая литация. Как показано на рис. , за исключением небольшого увеличения внутренних промежутков между столбцами, активный слой практически сохраняется в виде объема без фрагментации, и не наблюдается заметной разницы как в толщине слоя активного материала (верхняя часть алюминиевого электрода), так и в толщине слоя активного материала.
токосъемный слой (нижняя часть алюминиевого электрода).
Открыть в отдельном окне
Применение и характеристики литиевой батареи с алюминиевым анодом.
a Структура литий-ионной батареи с алюминиевым анодом по сравнению с обычной литий-ионной батареей. Токосъемник медного анода не требуется при использовании алюминиевого анода. Свернутый алюминиевый анод может быть собран напрямую. b Электродная реакция алюминиевого анода. Алюминиевая матрица частично литируется во время предзаряда, а литированный слой образует столбчато-пористую структуру в разряде и работает как активный материал в дальнейших циклах. c Цикличность литиевой батареи, состоящей из алюминиевого анода и LiCoO 2 катод. На вставке СЭМ-изображения показана поверхность алюминиевого анода после 120 циклов. Свойства электрода при начальных циклах показаны на дополнительном рисунке 2e . d Возможные профили циклов 10, 40, 70, 100 и 120 в циклах испытаний. На алюминиевом аноде не наблюдается явной деградации. e Поверхности и поперечные сечения алюминиевых анодов после первоначального литирования 2 мАч см −2 и после последующего 10-го литирования. Активный слой и токосъемный слой хорошо сохраняются без расхода. Масштабные полосы на изображениях SEM составляют 100 мкм.
В настоящей работе твердость металлической фольги рассматривается как ключевой параметр для баланса прочности между матрицей и литированной фазой. Если прочности обеих фаз сравнимы друг с другом, можно сохранить высокую стабильность структуры при первом литировании, как и в случае Al4N-AR. Это связано с тем, что образующаяся литированная фаза (AlLi) не может деформировать алюминиевую матрицу и, следовательно, химический потенциал алюминия остается неизменным везде в алюминиевой матрице. Однако, если в матрице Al есть локально деформированные области, где химический потенциал Al высок (см. розовую линию на рис. ), атомы Li преимущественно атакуют и аннигилируют такие нестабильные области (как показано экспериментально на рис. ). Таким образом, локальная деформация вызывает неоднородную реакцию Li с материалом анода. Следовательно, очень важно, чтобы алюминиевая матрица не деформировалась при образовании AlLi. Затем необходимо направить диффузию алюминия из матрицы к поверхности (граница между электролитом и анодом), чтобы избежать расширения внутреннего объема. К счастью, для Al это возможно, поскольку соединение AlLi допускает нестехиометрический состав, так что в соединении AlLi может формироваться градиент состава. Состав Li вокруг поверхности выше, чем во внутренней матрице, т. е. состав Al вокруг поверхности ниже. Таким образом, можно успешно управлять диффузией алюминия к поверхности. Следовательно, объемное расширение при литировании ограничено только нормальным направлением. С точки зрения допуска нестехиометрического состава металлический алюминий больше подходит для материала сплава-анода, чем другие элементы, которые демонстрируют стехиометрический состав в соединениях лития.
Однако было бы эффективно добавить третий элемент для получения нестехиометрических характеристик за счет определенного энтропийного эффекта.
Благодаря гомогенному литированию и обходу однонаправленной объемной деформации между литированной фазой и алюминиевой матрицей образуется очень плоская граница раздела (см. рис. и ), которая концептуально разделяет частично литированную алюминиевую фольгу на слой активного материала и токовый слой. — коллекторный слой. Благодаря такой многослойной структуре однокомпонентный алюминиевый анод обладает превосходной структурной стабильностью. Кроме того, поскольку активный слой после литирования будет самоорганизовываться с образованием пористой структуры во время делитирования, расширенный объем с дополнительным пространством в столбчато-пористом слое активного материала может компенсировать расширение объема за счет последующего литирования. Это предотвращает столкновение относительно хрупких AlLi друг с другом в дальнейших реакциях и, следовательно, позволяет избежать фатального измельчения в аналогичном механизме, а также в нанопористом кремнии 24 , что обеспечивает превосходную циклируемость однокомпонентного алюминиевого анода. Следовательно, сосредоточив внимание на слое активного материала, он показывает большую емкость, близкую к теоретическому значению ~990 мАч/г Al-1 и ~2680 мА·ч/см Al-3 с довольно высокой циклируемостью. Как показано в дополнительном примечании 2 и дополнительном рисунке 5 , благодаря отсутствию относительно тяжелого медного токосъемника этот тип алюминиевого анода для литиевых батарей может обеспечить более высокую практическую емкость, чем обычный углеродистый анод, и даже чем литий-металлический анод (с медным коллектором), что позволит в будущем создать безопасные литиевые батареи с высокой плотностью энергии.
Подготовка материалов
Алюминиевая фольга, используемая в настоящем исследовании, была произведена Sumitomo Chemical Co., Ltd. Алюминиевая фольга после прокатки и отжига чистотой 99,99% и прокатанная алюминиевая фольга чистотой 99,8% были приготовлены из соответствующих алюминиевых слитков. . Zn-фольга в состоянии проката с содержанием 99,9% была приобретена у The Nilaco Corporation, а прокатанная фольга Sn с содержанием 99,9% была приобретена у Takeuchi Metal Foil and Powder Co. , Ltd. Электролит 1 M LiPF 6 в EC:DMC ( 50:50) раствор был приобретен у Sigma-Aldrich Co. LLC. LiCoO 9Порошок 0089 2 был приобретен у Toshima Manufacturing Co., Ltd. Композитный катод был приготовлен путем смешивания порошка LiCoO 2 с проводящей сажей (Super C65) и поливинилидендифторидным связующим (5% диспергированным в N -метилпирролидоне, Kureha Corporation) в весовом соотношении 8:1:1. Смесь была наклеена на алюминиевую фольгу толщиной 20 мкм с помощью регулируемого пленочного аппликатора (BEVS Industrial Co., Ltd) и достигла массовой загрузки более 15 мг см −2 LiCoO 2 . Затем пастообразную смесь сушили в вакуумной сушилке при 120 °С в течение 12 часов с получением композитного катодного листа. Металлическая литиевая фольга, используемая в качестве противоэлектрода и электрода сравнения, была приобретена у Honjo Metal Co., Ltd.
Электрохимические испытания
Электрохимические испытания проводились с помощью потенциостата ВМП-3 или ВСП-300 (Bio-Logic SAS). Трехэлектродные ячейки монетного типа (SB7, EC-frontier Co., Ltd) собирали в перчаточном боксе, заполненном атмосферой аргона высокой чистоты. Рабочие электроды и противоэлектроды имели круглую форму диаметром 16 мм. В качестве электрода сравнения использовали металлический литий-стержень диаметром 1 мм. В качестве сепаратора использовали полиэтиленовую пленку или фильтр из стекловолокна. Структура ячейки показана на дополнительном рисунке 9.0015 6 .
Наблюдение за морфологией
Образцы промывали каплями тетрагидрофурана (99,5%, FUJIFILM Wako Pure Chemical Corporation) и затем сушили в атмосфере аргона. Фотографии образцов были сделаны на iPhone Xs Max (Apple, Inc.). Микроструктуры литированных и делитированных образцов (кроме вставки на рис.) подробно наблюдали с помощью FE-SEM JSM-7200F (JEOL Ltd). Измерение EBSD было выполнено для алюминиевых фольг с помощью детектора (Symmetry, Oxford Instruments), прикрепленного к FE-SEM. Образцы готовили в атмосфере аргона и переносили в высоковакуумную камеру FE-SEM без доступа воздуха. Образцы поперечного сечения на рис. и были подготовлены с помощью обрезного резака (C-4, WISTA Co., Ltd). Образец на вставке рис. был подготовлен с использованием FIB для получения идеальной плоскости поперечного сечения. Последующее измерение состава лития методом TOF-SIMS было поручено Sumika Chemical Analysis Service, Ltd.
Твердость по Виккерсу
Твердость каждой металлической фольги измеряли с помощью тестера микро-HV (HMV-G21DT, Shimadzu Corporation). Применяли испытательную силу HV0,05 (490,3 мН) и удерживали ее в течение 15 с. Для каждого образца измеряли более шести точек с соответствующими интервалами. Среднее значение твердости представлено на рис.
Рентгеновская дифракция
Рентгенограммы получены с помощью автоматизированного многоцелевого рентгеновского дифрактометра SmartLab (Rigaku Corporation). Для литированного образца использовали герметичный столик для поддержания атмосферы аргона на протяжении всего эксперимента без воздействия воздуха.
Расчет свободной энергии
Свободные энергии Гиббса бинарных фаз Al-Li, показанные на рис., были схематически изображены в свете компьютерного расчета с использованием программного обеспечения CaTCalc SE, разработанного Национальным институтом передовых промышленных наук и технологий, Япония. , с термодинамической базой данных, предоставленной Национальным институтом материаловедения Японии.
Дополнительная информация (1.3M, pdf)
Эта работа является совместным исследовательским проектом, заключенным по контракту между Университетом Тохоку и Sumitomo Chemical Co. Ltd. Эта работа частично поддерживается Грантом в поддержку научных исследований (S) номер 18H05249и грант в помощь научному сотруднику JSPS № 18J11696 по заказу Японского общества содействия развитию науки (JSPS).
Т.И. и Т.Ю. задумал исследование. Х.Л. разработал план исследования и провел основную часть экспериментов. Х.Х. и Т.К. подготовили образцы Al. С.М. провели анализ распределения Li в образцах Al. Н.Л.О. и HL провели измерения EBSD. Х.Л. и Т.И. написал рукопись. Все авторы обсудили результаты и внесли свой вклад в рукопись.
Данные, подтверждающие результаты этого исследования, можно получить у соответствующего автора по запросу.
Т.Ю., С.М., Х.Х. и Т.К. являются сотрудниками Sumitomo Chemical Co., Ltd. Другие авторы заявляют об отсутствии конкурирующих интересов.
Информация о рецензировании Nature Communications благодарит анонимных рецензентов за их вклад в рецензирование этой работы.
Примечание издателя Springer Nature остается нейтральной в отношении юрисдикционных претензий в опубликованных картах и институциональной принадлежности.
Дополнительная информация доступна для этого документа по телефону 10.1038/s41467-020-15452-0.
1. Чу С., Маджумдар А. Возможности и проблемы для устойчивого энергетического будущего. Природа. 2012; 488: 294–303. doi: 10.1038/nature11475. [PubMed] [CrossRef] [Google Scholar]
2. Larcher D, Tarascon JM. На пути к более экологичным и устойчивым батареям для хранения электроэнергии. Нац. хим. 2015;7:19–29. doi: 10.1038/nchem.2085. [PubMed] [CrossRef] [Академия Google]
3. Гуденаф Дж.Б., Парк К.С. Литий-ионная аккумуляторная батарея: перспектива. Варенье. хим. соц. 2013; 135:1167–1176. дои: 10.1021/ja3091438. [PubMed] [CrossRef] [Google Scholar]
4. Whittingham MS. Литиевые батареи и катодные материалы. хим. 2004; 104:4271–4302. doi: 10.1021/cr020731c. [PubMed] [CrossRef] [Google Scholar]
5. Йошино А. Рождение литий-ионного аккумулятора. Ангью. хим. Междунар. Эд. 2012;51:5798–5800. doi: 10.1002/anie.201105006. [PubMed] [CrossRef] [Академия Google]
6. Tarascon JM, Armand M. Проблемы и проблемы, связанные с перезаряжаемыми литиевыми батареями. Природа. 2001; 414: 359–367. doi: 10.1038/35104644. [PubMed] [CrossRef] [Google Scholar]
7. Armand M, Tarascon JM. Создание лучших аккумуляторов. Природа. 2008; 451: 652–657. doi: 10.1038/451652a. [PubMed] [CrossRef] [Google Scholar]
8. Besenhard JO, Yang J, Winter M. Будут ли перспективные аноды из литиевых сплавов в литий-ионных батареях? J. Источники питания. 1997; 68: 87–90. дои: 10.1016/S0378-7753(96)02547-5. [CrossRef] [Google Scholar]
9. Hamon Y, et al. Алюминиевый отрицательный электрод в литий-ионных батареях. J. Источники питания. 2001; 97–98: 185–187. doi: 10.1016/S0378-7753(01)00616-4. [CrossRef] [Google Scholar]
10. Park CM, Kim JH, Kim H, Sohn HJ. Анодные материалы на основе литиевых сплавов для литиевых вторичных аккумуляторов. хим. соц. 2010; 39:3115–3141. doi: 10.1039/b919877f. [PubMed] [CrossRef] [Google Scholar]
11. Обровац М.Н., Шеврие В.Л. Отрицательные электроды из сплава для литий-ионных аккумуляторов. хим. 2014; 114:11444–11502. doi: 10.1021/cr500207g. [PubMed] [CrossRef] [Академия Google]
12. Фонг Р., Фонсакен У., Дан Дж.Р. Исследования интеркаляции лития в углероды с использованием неводных электрохимических ячеек. Дж. Электрохим. соц. 1990;137:2009–2013. doi: 10.1149/1.2086855. [CrossRef] [Google Scholar]
13. Dahn JR, Zheng T, Liu Y, Xue JS. Механизмы внедрения лития в углеродистые породы. Матер. науч. 1995; 270: 590–593. [Google Scholar]
14. Винтер М., Безенхард Дж.О. Электрохимическое литирование олова и интерметаллидов и композитов на основе олова. Электрохим. Акта. 1999;45:31–50. doi: 10.1016/S0013-4686(99)00191-7. [CrossRef] [Google Scholar]
15. McDowell MT, Lee SW, Nix WD, Cui Y. Статья, посвященная 25-летию: понимание литирования кремниевых и других легирующих анодов для литий-ионных аккумуляторов. Доп. Матер. 2013;25:4966–4985. doi: 10.1002/adma.201301795. [PubMed] [CrossRef] [Google Scholar]
16. Hirai K, et al. Влияние объемной деформации из-за образования соединения Li–Sn на потенциал электрода в литий-ионных батареях. Acta Mater. 2008;56:1539–1545. doi: 10.1016/j.actamat.2007.12.002. [CrossRef] [Google Scholar]
17. Ichitsubo T, et al. Влияние механической деформации на электрохимическое литирование электродных материалов на основе алюминия. Дж. Электрохим. соц. 2011;159:A14–A17. doi: 10.1149/2.038201jes. [CrossRef] [Google Scholar]
18. Liu XH, et al. Разрушение наночастиц кремния в зависимости от размера при литировании. АКС Нано. 2012; 6: 1522–1531. doi: 10.1021/nn204476h. [PubMed] [CrossRef] [Академия Google]
19. Chan CK, et al. Высокопроизводительные аноды литиевых батарей с использованием кремниевых нанопроволок. Нац. нанотехнологии. 2008; 3:31–35. doi: 10.1038/nnano.2007.411. [PubMed] [CrossRef] [Google Scholar]
20. Yu Y, Gu L, Zhu C, van Aken PA, Maier J. Наночастицы олова, инкапсулированные в пористые многоканальные углеродные микротрубки: получение методом электроформования с одним соплом и применение в качестве анодного материала для высокопроизводительных аккумуляторов на основе лития. Варенье. хим. соц. 2009; 131:15984–15985. doi: 10.1021/ja1c. [PubMed] [CrossRef] [Академия Google]
21. Герцберг Б., Алексеев А., Юшин Г. Деформации Si-Li анодов при электрохимическом сплавлении в наноограниченном пространстве. Варенье. хим. соц. 2010; 132:8548–8549. doi: 10.1021/ja1031997. [PubMed] [CrossRef] [Google Scholar]
22. Wu H, et al. Стабильное циклирование анодов батарей с двойными стенками из кремниевых нанотрубок посредством межфазного контроля твердого электролита. Нац. нанотехнологии. 2012;7:310–315. doi: 10.1038/nnano.2012.35. [PubMed] [CrossRef] [Google Scholar]
23. Wang C, et al. Самовосстанавливающаяся химия обеспечивает стабильную работу анодов из микрочастиц кремния для высокоэнергетических литий-ионных аккумуляторов. Нац. хим. 2013;5:1042–1048. doi: 10.1038/nchem.1802. [PubMed] [CrossRef] [Академия Google]
24. Вада Т. и др. Отрицательный электрод из объемного нанопористого кремния с чрезвычайно высокой циклируемостью для литий-ионных аккумуляторов, изготовленный с использованием нисходящего процесса. Нано Летт. 2014;14:4505–4510. дои: 10.1021/nl501500g. [PubMed] [CrossRef] [Google Scholar]
25. Lin D, et al. Вторичный кремниевый анод с высокой плотностью отводов, изготовленный путем масштабируемого механического прессования для литий-ионных аккумуляторов. Энергетическая среда. науч. 2015;8:2371–2376. doi: 10.1039/C5EE01363A. [Перекрестная ссылка] [Академия Google]
26. An Y, et al. Экологически чистое, масштабируемое и контролируемое производство нанопористого кремния из коммерческих прекурсоров сплавов для высокоэнергетических литий-ионных аккумуляторов. АКС Нано. 2018;12:4993–5002. doi: 10.1021/acsnano.8b02219. [PubMed] [CrossRef] [Google Scholar]
27. Ли Х. Эволюция кристаллической структуры нано-кремниевого анода, вызванная введением и экстракцией лития при комнатной температуре. Твердотельный ион. 2000; 135:181–191. doi: 10.1016/S0167-2738(00)00362-3. [Перекрестная ссылка] [Академия Google]
28. Li X, Dhanabalan A, Gu L, Wang C. Трехмерные пористые композитные аноды Sn@Carbon с пористым ядром и оболочкой для высокопроизводительных литий-ионных аккумуляторов. Доп. Энергия Матер. 2012;2:238–244. doi: 10.1002/aenm.201100380. [CrossRef] [Google Scholar]
29. Meschini I, et al. Высокоэффективный нанокомпозитный анод Sn@carbon для литиевых аккумуляторов. J. Источники питания. 2013; 226: 241–248. doi: 10.1016/j.jpowsour.2012.11.004. [CrossRef] [Google Scholar]
30. Kim H, Cho J. Превосходные литиевые электроактивные мезопористые нанопровода Si@Carbon с ядром и оболочкой для материала анода литиевой батареи. Нано Летт. 2008; 8: 3688–369.1. doi: 10.1021/nl801853x. [PubMed] [CrossRef] [Google Scholar]
31. Медури П., Пендьяла С., Кумар В., Суманасекера Г.У., Сункара М.К. Гибридные нанопроволоки оксида олова в качестве стабильных и высокоемких анодов для литий-ионных аккумуляторов. Нано Летт. 2009; 9: 612–616. doi: 10.1021/nl802864a. [PubMed] [CrossRef] [Google Scholar]
32. Wu H, Cui Y. Разработка наноструктурированных кремниевых анодов для высокоэнергетических литий-ионных аккумуляторов. Нано сегодня. 2012;7:414–429. doi: 10.1016/j.nantod.2012.08.004. [Перекрестная ссылка] [Академия Google]
33. Ji J, et al. Инкапсулированный графеном кремний на ультратонкой графитовой пене в качестве анода для литий-ионных аккумуляторов большой емкости. Доп. Матер. 2013; 25:4673–4677. doi: 10.1002/adma.201301530. [PubMed] [CrossRef] [Google Scholar]
34. Liu Y, Zhang N, Jiao L, Tao Z, Chen J. Сверхмалые наночастицы олова, встроенные в углерод, в качестве высокопроизводительного анода для натрий-ионных аккумуляторов. Доп. Функц. Матер. 2015;25:214–220. doi: 10.1002/adfm.201402943. [CrossRef] [Google Scholar]
35. Qin J, et al. Графеновые сети, закрепленные с помощью sn@graphene в качестве анода литий-ионного аккумулятора. АКС Нано. 2014; 8: 1728–1738. doi: 10.1021/nn406105n. [PubMed] [CrossRef] [Академия Google]
36. Ван Дж., Кинг П., Хаггинс Р. Исследования бинарных сплавов литий-цинк, литий-кадмий и литий-свинец в качестве отрицательных электродов в электролите на основе органических растворителей. Твердотельный ион. 1986; 20: 185–189. doi: 10.1016/0167-2738(86)
-2. [CrossRef] [Google Scholar]
37. Chen C, Yang Y, Shao H. Повышение способности к циклированию лития с использованием подложки из литий-цинкового сплава для литий-металлических батарей. Электрохим. Акта. 2014; 137:476–483. doi: 10.1016/j.electacta.2014.06.006. [Перекрестная ссылка] [Академия Google]
38. Hallstedt B, Kim O. Термодинамическая оценка системы Al-Li. Междунар. Дж. Матер. Рез. 2007; 98: 961–969. дои: 10.3139/146.101553. [CrossRef] [Google Scholar]
39. Ichitsubo T, et al. Механико-энергетические воздействия на электрохимические явления в литий-ионных батареях. Дж. Матер. хим. 2011;21:2701–2708. doi: 10.1039/c0jm02893b. [CrossRef] [Google Scholar]
Статьи из Nature Communications предоставлены здесь с разрешения Nature Publishing Group
Инвентаризация литого и кованого железа
Отчеты
Инвентаризация открывается в новом окне и содержит три отчета о каждом состоянии литой или кованой трубы.
В первом отчете можно ранжировать штаты либо по протяжённости магистральных газораспределительных сетей, либо по количеству линий обслуживания. Распределительные магистрали — это распределительные трубопроводы природного газа, которые служат общим источником снабжения для более чем одной сервисной линии. Линии обслуживания — это трубопроводы, по которым газ транспортируется к счетчику или трубопроводу потребителя. Таблица изначально отсортирована по количеству километров литой или кованой газораспределительной магистрали, но может быть отсортирована по любому из столбцов.
Второй отчет показывает изменение количества основных миль и маршрутов обслуживания за несколько лет. С 2005 по 2020 год основной пробег по распределению литого и кованого железа на национальном уровне сократился на 50 процентов. Количество сервисных линий из литого или кованого железа сократилось примерно на 80 процентов за тот же период времени. В третьем отчете показаны данные для каждого оператора, сообщающего о железных конвейерах с 2005 года.
Все отчеты можно ограничить одним состоянием, используя подсказку состояния вверху. В любом штате, не включенном в раскрывающийся список, либо никогда не было литых и кованых распределительных газопроводов, либо все они были удалены до 2005 г. 24 государства и 1 территория полностью ликвидировали чугунные и кованые газораспределительные трубопроводы: AK, AZ, AR, CO, GA, HI, IA, ID, KS, MN, MT, NM, NC, ND, NV, OK, OR , PR, SC, SD, UT, VT, WA, WI и WY .
Отчеты об инвентаризации чугунных газораспределительных трубопроводов
Недавние инциденты, связанные с чугунными трубопроводами
Несмотря на то, что количество чугунных трубопроводов сокращается, в последнее время произошел ряд инцидентов, вызванных чугунными газораспределительными трубопроводами. отказов, вновь привлекая внимание к рискам, связанным с литыми и коваными трубопроводами.
- 10 января 2020 г. — Пожар и взрыв газа на частной собственности в Джерси-Сити, штат Нью-Джерси, привели к травме, потребовавшей госпитализации пациента. Компания Public Service Electric & Gas Co обнаружила утечки в стыках 36-дюймовой чугунной магистрали, установленной в 1952 году, которые мигрировали через 4-дюймовый электрический трубопровод, идущий с улицы, и простирались в подвал здания.
- 19 декабря 2019 г. – Бригады Philadelphia Gas Works (PGW) прибыли на три горящих объекта на юге 8 -я улица в Филадельфии, Пенсильвания.
6-дюймовый чугунный газопровод имел разрыв по окружности, где большая подземная полость вызвала движение грунта и привела к разрыву магистрали, установленной в 1928 году. Погибло 2 человека. Во время происшествия PGW эвакуировала около 60 человек.
- 16 июня 2018 г. — Бригада подрядчика по укладке дорожного покрытия Baltimore Gas and Electric (BGE) была ранена, и ей потребовалась ночная госпитализация во время установки термопластичных маркеров линий дорожного движения с использованием тепловой горелки в Балтиморе, штат Мэриленд. Обнаружена утечка магистрального газопровода и 1903 установленный чугунный стык был отремонтирован.
- 20 января 2018 г. — В результате пожара газа в двухэтажном жилом доме в Бруклине, штат Нью-Йорк, четыре человека получили ранения, одному человеку потребовалась ночная стационарная госпитализация. Здание получило умеренные структурные повреждения. Чугунная основная труба диаметром 6 дюймов была установлена примерно в 1927 году и работала под давлением 0,3 фунта на кв.
дюйм. Предположительной причиной инцидента стало морозное пучение.
- 31 июля 2016 г. — Выброс из чугунной магистрали привел к 1 смертельному исходу и 1 травме в жилом доме в Шривпорте, штат Луизиана. Определенной причины инцидента нет, но сочетание размыва/эрозии, утечки жидкости из канализационного люка, неправильной обратной засыпки и уплотнения способствовало перегрузке, которая даже привела к утечке газа. 4-дюймовая труба была установлена в 1911 и работал при манометрическом давлении 0,5 фунта на кв. дюйм.
- 5 марта 2015 г. — Получив уведомление об утечке газа в жилом доме в Детройте, штат Мичиган, коммунальные службы обнаружили кольцевую трещину в 6-дюймовой чугунной магистрали. Глубина промерзания составляла 48 дюймов, в результате чего магистраль сломалась. Последствия: 1 погибший и 1 травмированный. Чугунная магистраль была установлена в 1923 году и работала под давлением 2 фунта на кв. дюйм.
- 27 января 2015 г.
— Дом взорвался на улице МакКрори в Кордове, штат Алабама, когда сотрудники газовой службы реагировали на утечку природного газа. В результате один погибший и трое раненых. Движение земли возле чугунной магистрали привело к растрескиванию трубы. Чугунная распределительная магистраль была установлена в 1952 и работал под давлением 22 фунта на кв. дюйм.
- 9 января 2012 г. — Взорвался дом на Пейн-авеню в Остине, штат Техас, в результате чего один человек погиб и один был ранен. Утечка возникла в результате прорыва четырехдюймового чугунного газопровода, установленного в 1950 году. Прорыв чугунного газопровода произошел после дождя, последовавшего за продолжительной засухой.
- 9 февраля 2011 г. – Трагический взрыв произошел на 13-й Северной улице в Аллентауне, штат Пенсильвания. Местные аварийно-спасательные службы пытались ограничить распространение огня, в то время как оператор прорезал железобетон, чтобы получить доступ к газопроводу.
Предварительное расследование выявило трещину в 12-дюймовой чугунной магистрали, установленной в 1928 и на момент инцидента работал под давлением менее 1 фунта на кв. дюйм. В результате взрыва и последовавшего за ним пожара пять человек погибли, трем потребовалась стационарная госпитализация, восемь жилых домов были разрушены.
- 18 января 2011 г. — В результате взрыва и пожара один сотрудник газовой компании погиб и несколько других получили ранения, когда бригады газовой компании реагировали на утечку природного газа в Филадельфии, штат Пенсильвания. Предварительное расследование выявило кольцевой разрыв на 12-дюймовой чугунной распределительной магистрали, которая была установлена в 1942 и работал под давлением 17 фунтов на квадратный дюйм.
Анализ происшествий и последствий
Правила PHMSA требуют, чтобы операторы газораспределения представляли отчеты об инцидентах, когда утечка приводит к травмам или летальному исходу, ущерб имуществу превышает нормативный порог в соответствии с §191. 3 или непреднамеренный выпуск трех миллионов стандартных кубических футов или более газа. Отчеты об инцидентах в системе газораспределения (за исключением утечек за пределами счетчика потребителя) за 2005–2020 годы показывают следующее:
- 9 процентов происшествий на газораспределительных магистральных сетях были связаны с чугунными магистралями. Однако только 2% распределительных сетей выполнены из чугуна.
- 39 процентов несчастных случаев на литейных/кованых железных дорогах привели к гибели людей или травмам, по сравнению с 21 процентом несчастных случаев на других типах сетей.
- 36 процентов всех смертельных случаев и 16 процентов всех травм на газораспределительных магистральных трубопроводах, связанных с литыми или коваными трубопроводами.
Что вызывает протечки железных труб?
Самой большой угрозой для литых или кованых труб является движение грунта. Если эти трубопроводы будут нарушены земляными работами, сезонными морозными пучениями или изменениями уровня грунтовых вод, может возникнуть утечка.
Другая серьезная угроза, называемая графитизацией, представляет собой естественный процесс, при котором железо разлагается на более мягкие элементы, что делает железные трубопроводы более восприимчивыми к растрескиванию. Степень графитизации зависит от многих факторов, но газ может просачиваться из соединений или через трещины в трубе, если графитизация произошла.
При возникновении утечек в системах низкого давления с распределительными трубопроводами из литого или кованого железа объем газа, выходящего через место отказа, намного меньше, чем тот, который мог бы выйти из-за отказа того же размера в системе, работающей при более высоких давлениях. Однако даже относительно небольшой объем утечки природного газа может иметь катастрофические последствия.
История
Трубопроводы из чугуна и кованого железа были первоначально построены для транспортировки промышленного газа, начиная с 1870-х и 1880-х годов, а чугун стал более популярным в начале 1900с.
В 1970 году PHMSA начала собирать данные о пробеге газопроводов с разбивкой по типу материала труб. В 1983 году операторы газораспределительных трубопроводов сообщили о 61 536 милях чугунных и 4 371 милях кованых труб. С 1984 года операторы начали представлять объединенные данные по этим двум направлениям.
Трубопроводы из кованого железа соединялись встык с помощью резьбовых или компрессионных муфт, в то время как трубопроводы из чугуна соединялись с помощью раструбных и втулочных соединений с уплотняющим материалом, набитым в раструб, чтобы образуют газонепроницаемое уплотнение. Поскольку по этим трубопроводам транспортировался влажный промышленный газ, упаковочный материал впитывал влагу и, как правило, не имел утечек.
Поскольку в середине 20-го века сухой природный газ начал вытеснять искусственный газ, уплотнительный материал, герметизирующий соединения, высох, что привело к утечкам. На протяжении многих лет для восстановления суставов применялись различные методы зажима и инкапсуляции.
Программы управления целостностью распределительных сетей
В конце 2009 года PHMSA внедрила правила безопасности трубопроводов для управления целостностью газораспределительных трубопроводов. Операторы должны были создать и внедрить программы управления целостностью распределения (DIMP) к августу 2011 года. Операторы должны знать конкретные характеристики своей системы и операционной среды, чтобы выявлять угрозы, оценивать риски и принимать меры по их снижению.
В частности, при работе с литым/кованым чугуном операторы должны знать специфические характеристики трубы и условия окружающей среды, в которых графитизация может быть серьезной. Оценка прошлой истории утечек и мониторинг литых/кованых труб во время раскопок также являются ключевыми компонентами поддержания целостности.
Рекомендации Национального совета по безопасности на транспорте
Национальный совет по безопасности на транспорте — это независимое федеральное агентство, которое проводит расследования для определения вероятных причин транспортных происшествий.
В 1986 году NTSB расследовал взрыв в ресторане в Дерби, штат Коннектикут, в результате которого шесть человек погибли и 12 получили ранения. NTSB дал рекомендации по корректирующим действиям только оператору трубопровода. В 1990 году в результате взрыва природного газа и пожара один человек погиб, девять получили ранения, были разрушены два дома и повреждены два соседних дома в Аллентауне, штат Пенсильвания. В отчете NTSB было обнаружено, что утечка водопровода разрушила опору под 4-дюймовым чугунным газопроводом. . Это нарушение грунта приводит к кольцевой трещине в газопроводе. Природный газ мигрировал через почву в подвал одного из домов, где воспламенился, взорвался и сгорел. Чугунный газопровод был значительно ослаблен графитизацией.
В 1991 году NTSB рекомендовал PHMSA, которая тогда называлась Управлением по исследованиям и специальным программам, потребовать от операторов трубопроводов реализации программы по выявлению и замене чугунных трубопроводов, которые могут угрожать общественной безопасности. PHMSA выпустила два консультативных бюллетеня, касающихся программ замены чугуна.
Оповещение RSPA 91-02 Призывает операторов разрабатывать процедуры для определения сегментов чугунных труб, которые могут нуждаться в замене. Напоминает операторам о том, что правила безопасности трубопроводов требуют, как правило, замены труб из графитированного чугуна и защиты выкопанных чугунных труб от повреждений.
Оповещение RSPA 92-02 Напоминает операторам о том, что правила безопасности трубопроводов требуют, чтобы операторы имели процедуру постоянного наблюдения за трубопроводными объектами для выявления проблем и принятия соответствующих мер в отношении отказов, истории утечек, коррозии и других необычных условий эксплуатации и обслуживания. Эта процедура должна также включать наблюдение за чугуном для выявления проблем и принятия соответствующих мер в отношении графитизации.
Консультативный бюллетень PHMSA ADB-2012-05 В 2012 году PHMSA дополнила два предупреждающих уведомления RSPA с просьбой к операторам и представителям штата по безопасности трубопроводов контролировать программы замены чугуна, организовать ускоренные исследования утечек, сосредоточить усилия по обеспечению безопасности на трубах с высоким риском, стимулировать восстановление трубопровода. , программы ремонта и замены, усилить инспекцию, расследование несчастных случаев и правоприменительные меры, а также установить домашнюю сигнализацию газа метана.
Снижение использования кобальта для литий-ионных аккумуляторов
Управление транспортных технологий
6 апреля 2021 г.
Справочная информация
Литий-ионные аккумуляторы (LiB) являются повсеместным источником питания во всей бытовой электронике, во всех электроинструментах и, поскольку многие компании и страны стремятся сократить выбросы парниковых газов, составляют растущую долю мировых автомобильный парк. Чтобы работать, у этих накопителей энергии должно быть место для перемещения ионов лития, когда батарея работает. Это катод, а также место, откуда берутся ионы лития, когда аккумулятор заряжается. Чтобы получить достаточно энергии от батарей, катоды LiB изготавливаются из различных комбинаций переходных металлов и кислорода в определенном порядке. Наилучшая комбинация для многих потребностей в хранении энергии включает структуру катода, которая в основном состоит из ионов кобальта (Co). Даже с ростом использования сотовых телефонов эта зависимость от кобальта не была серьезной помехой, поскольку для этих устройств требовалось лишь небольшое количество Co. Однако электрификация мирового автомобильного парка LiB существенно меняет ситуацию.
Кобальт считается материалом с самым высоким риском в цепочке поставок электромобилей (EV) в краткосрочной и среднесрочной перспективе. Аккумуляторы электромобилей могут содержать до 20 кг Co в каждой упаковке на 100 киловатт-часов (кВтч). Сейчас Co может составлять до 20% веса катода в ионно-литиевых батареях электромобилей. Существуют экономические, социальные и социальные факторы, способствующие снижению содержания Co. Кобальт добывается как вторичный материал из смешанных никелевых (Ni) и медных руд. Это означает, что поставка не является независимой от других сырьевых предприятий, а внедрение новых проектов восстановления обходится дорого. Более того, в США нет больших запасов Co, а добыча и переработка на ранних стадиях сосредоточены в небольшом числе стран за пределами США. Поэтому Соединенные Штаты стремятся обезопасить источники Co, резко снизить содержание Co в LiB или и то, и другое.
Три различных переходных металла — Co, марганец (Mn) и Ni — могут справиться с основной тяжестью сдвигов накопления заряда, а также многие другие металлы, включая алюминий (Al), титан (Ti), железо (Fe) и магний ( Мг) помогите. Однако простой оксид кобальта предлагает наилучшее сочетание обеспечения высокого напряжения, очень хорошей плотности энергии и легкого перемещения ионов Li+. Отказ от высокого содержания Со означает, что новые катодные материалы должны быть оптимизированы для всех этих рабочих характеристик за счет незначительных изменений в расположении переходных металлов и их относительном составе. Несмотря на то, насколько хорошими стали катоды на основе оксидов переходных металлов, обычно обозначаемые аббревиатурой NMC для трех основных переходных металлов, за которыми следует соотношение Ni/Mn/Co, для аккумуляторов электромобилей, существует общепризнанная необходимость уменьшить зависимость от Co без ущерба для производительности. .
Исследования и разработки Министерства энергетики США в области аккумуляторов с низким содержанием/отсутствием кобальта
Промышленность осознала риски, связанные с зависимостью от кобальта, и многие производители аккумуляторов и конечные пользователи поставили амбициозные цели по переходу на катоды с низким содержанием кобальта или без него. Существует множество технологических препятствий, и Министерство энергетики США (DOE) через Управление транспортных средств взяло на себя обязательство по реализации многолетней многоцелевой программы для решения всех научных и инженерных проблем с устранением большей части Co из аккумуляторов электромобилей. .
Многие исследовательские проекты сосредоточены на материалах с высоким содержанием никеля, которые обладают очень хорошей плотностью энергии. На сегодняшний день проблема использования катодных материалов с высоким содержанием никеля заключается в том, что они, как правило, страдают от быстрого снижения емкости и повышения импеданса из-за вредных реакций между атомами никеля на поверхности катода и электролитом элемента. Многие проекты работают над стабилизацией или защитой этой поверхности, чтобы свести к минимуму эти реакции. Ниже приведены проекты, финансируемые Министерством энергетики, которые продемонстрировали ранний успех.
Исследовательская группа под руководством Национальной лаборатории Ок-Риджа (ORNL) при содействии XALT Energy и технического центра Nissan разрабатывает новый класс катодных материалов, не содержащих Co, с маркировкой NFA, состоящих из Ni, Fe и Al. На рис. 1 показаны результаты циклирования полных элементов, изготовленных с использованием катодного материала ORNL-NFA (LI 1,0 Ni 0,85 Fe 0,052 Al 0,091 O 2 ). Большинство элементов, использующих катоды NMC с концентрацией Ni выше 80%, испытают гораздо более быстрое снижение емкости, чем показано здесь.
Рис. 1. Результаты циклов для литий-ионного элемента без кобальта с катодом NFA.
Группа под руководством Техасского университета в Остине совместно с Национальной лабораторией возобновляемых источников энергии и Tesla Inc. разрабатывает ряд катодных материалов с низким содержанием или отсутствием кобальта. На рис. 2 полностью показаны результаты циклирования некоторых из этих катодных материалов. карманные клетки. Светло-голубая линия показывает хорошую цикличность коммерческого NMC622 (20% Co), которая превосходит или равна цикличности клеток, использующих NMA (90% Ni, 5% Mn, 5% Al, 0% Co) (серая линия) и материалы NMCAM (90% Ni, 4% Mn, 4% Co, 1% Al и 1% Mg) (зеленая линия). Вывод здесь состоит в том, что катодные примеси (Al, Mg) могут стабилизировать эти материалы при циклировании под высоким напряжением.
Рис. 2. Полная циклическая обработка ячеек с низким содержанием кобальта и без кобальта.
Катодный материал без кобальта, синтезированный с использованием поверхностного/объемного легирования Ti/Mg, помеченный NTM (LiNi 0,96 Ti 0,02 Mg 0,02 O 2 ), показал более высокие результаты с точки зрения срока службы и многообещающие результаты с точки зрения срока службы ограничения по напряжению (рис.