Почему текут жаротрубные котлы?
Опубликовано: 29 апреля 2022 г.
5140
Андрей Колосов, директор ООО «Инновации и Сервис»
В статье продолжаем рассказывать о причинах течи жаротрубных котлов. Приводим новые данные, полученные при промывке котлов за последние три года.
Жаротрубный котел потек. Что делать?
К сожалению, нас очень часто приглашают на химическую промывку жаротрубных котлов уже после того, как передней или задней трубной доске появились течи. Посмотрите на эти фотографии – рис. 1, 2.
Рис. 1, 2. Жаротрубные котлы, нуждающиеся в промывке
А теперь, давайте попробуем разобраться причинах этого явления. Почему прогорают и текут жаротрубные котлы?
Конструкция жаротрубного котла
Начнем с конструкции котла. Как вы знаете, жаротрубный котел представляет собой цилиндр, внутри которого находится жаровая труба.
Рис. 3. Конструкция жаротрубного котла
Для улучшения теплоотдачи котел содержит еще и дымогарные трубы (1-го, 2-го хода, а иногда и с 3-м ходом), по которым также идут дымовые газы.
Обечайка котла, жаровая и дымогарные трубы ввариваются в трубные доски – переднюю и заднюю, создавая, таким образом, конструкцию котла, заполненную внутри водой.
Толщина трубной доски – 13-16 мм. Технологически, чтобы вставить в нее дымогарную трубу, в трубной доске делается отверстие, с диаметром чуть большим, чем внешний диаметр дымогарной трубы. Установленную дымогарную трубу приваривают к трубной доске с лицевой части.
Образование накипи в жаротрубном котле
Во время эксплуатации жаротрубного котла мельчайшие частицы накипи забиваются в зазор и снижают теплопередачу в местах сварки. Вообще, распределение накипи в жаротрубных котлах неравномерно.
По этой причине сварочный шов перегревается и охрупчивается (рис. 4). Через некоторое время это приводит к течи котла именно в местах сварки. Очень редко из-за термических напряжений лопается трубная доска.
Рис. 4. Перегревание и охрупчивание сварочного шва. Красной стрелкой обозначена трубная доска, синей стрелкой – дымогарная труба
Почему жаротрубные котлы не приспособлены к промывке?
А теперь рассмотрим схему химической промывки жаротрубного котла от накипи и увидим, почему котлы некоторых производителей не совсем приспособлены для этих целей.
Не будем называть конкретные марки котлов, просто разберем их на схеме. Вот жаротрубный котел в разрезе – см. рис. 5.
Рис. 5. Схема жаротрубного котла
Котел имеет только один выход в нижней части. Как правило, с тыла котла, куда обычно подключается подача промывочного насоса. По крайней мере, так делаем мы, позже объясним почему.
В верхней части котла, обратный трубопровод или выход из котла, можно сделать либо на предохранительных клапанах, либо на фланцах, где установлены датчики уровня. Однако в редких марках котлов есть фланцы Dу 80 или Dу 100 в верхней передней части котла, над горелкой.
Чтобы химическая промывка проводилась эффективно, необходимо создать гидродинамический поток, омывающий переднюю и заднюю трубные доски котла.
Как уже говорилось выше, в редких марках котла можно создать такую, идеальную схему промывки, поскольку нет фланца в передней верхней части котла. Вы спросите: а зачем это нужно? Ведь котел и так заполнен промывочным раствором и накипь должна растворяться везде?
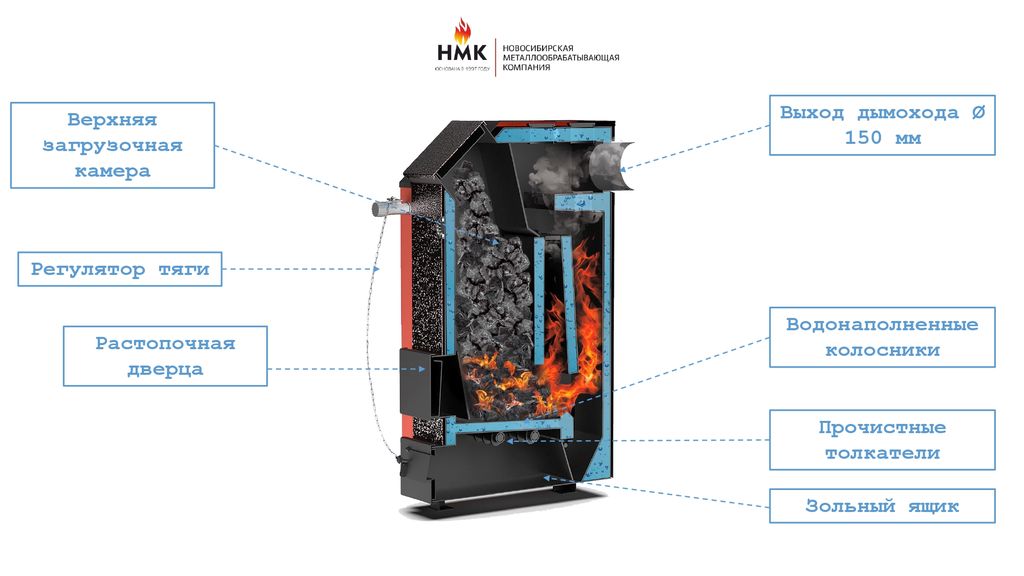
В неподвижной среде, без циркуляции, промывочный раствор срабатывается у стенок котла и не перемешивается. В результате реакция прекращается и накипь не растворяется. Именно поэтому не допускается промывка жаротрубных котлов методом травления, без циркуляции.
Как правильно промывать жаротрубные котлы?
Возвращаясь к теме статьи отметим, что неправильный процесс химической промывки жаротрубного котла приводит к тому, что накипь остается на трубных досках, вызывает перегрев мест сварки и котлы начинают течь. Чтобы избежать этого, необходимо тщательно соблюдать правила промывки жаротрубного котла и тогда проблемы можно избежать. Этих правил немного, перечислим их:
2. Параметры насоса: напор – не менее 50 метров, подача – 6-8 водяных объемов котла.
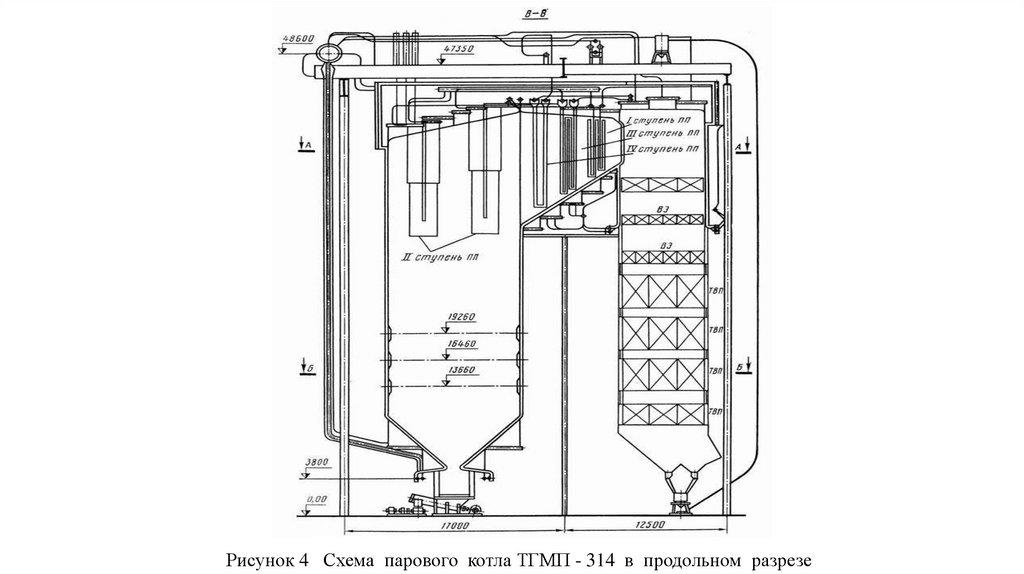
3. Для паровых котлов увеличивать время промывки до двух-трех суток, так как накипь в паровом котле более прочная и адгезированная к поверхности металла.
4. Химическую промывку производить специализированным реагентом, разработанным именно для промывки промышленных котлов от накипи.
5. Реагент должен иметь в своем составе ингибиторы, обеспечивающие реальную скорость коррозии не более 0,2 г·м2/ч, при температуре 50-60°С.
6. После химической промывки обязательно делать фото- и видеосъемку трубных досок котла на предмет отсутствия накипи.
Данные рекомендации помогут правильно промыть жаротрубный котел от накипи и эксплуатировать его длительное время без ремонта.
ООО «Инновации и Сервис»
144000, Московская область,
г. Электросталь, ул. Николаева, 9, пом. 17
Тел.: +7 (916) 868-61-88, +7 (903) 726-96-98
е-mail: innova@inev. ru
Поделиться:
вернуться назад
Серии балансировочных клапанов Giacomini
Электроэнергия из низкотемпературного бросового тепла с применением ОЦР
ВОДОПОДГОТОВКА
2.5. Паровые котлы энергоблоков ТЭС
В середине ХХ века развитие тепловых электростанций шло по пути увеличения единичной мощности и экономичности энергетического оборудования. При этом в 50-е годы ХХ века в СССР начали строить ТЭС с энергоблоками 100, 150 и 200 МВт, а в 60-е годы вводить в эксплуатацию на электростанциях энергоблоки мощностью 300, 500 и 800 МВт. Введен в эксплуатацию также один энергоблок мощностью 1200 МВт. В этих блоках установлены котлы на сверхкритические параметры пара.
Переход котлов на сверхкритические параметры пара диктовался экономической целесообразностью, которая определялась оптимальным балансом экономии топлива за счёт повышения термического к. п.д. цикла и удорожания оборудования и эксплуатации. Отказ от применения в мощных блоках барабанных котлов на докритические параметры пара определялся значительным ростом стоимости котла в результате увеличения массы барабана, которая для котла блока 500 МВт достигала 200 т. Монтаж и эксплуатация такого котла значительно усложняются, поэтому оптимальная мощность энергоблоков с барабанными котлами, несущими базовую нагрузку, не превышает 400 МВт. В связи с этим при создании блоков большой мощности было принято решение о переходе на прямоточные котлы сверхкритического давления.
Первые прямоточные котлы для энергоблоков 300 МВт моделей ТПП-110 и ПК-39 и котлы для энергоблоков 800 МВт моделей ТПП-200, ТПП-200-1 были изготовлены в начале 60-х годов XX века. Исполнялись они двухкорпусными. Паровые котлы ТПП-110 и ПК-39 были изготовлены с несимметричным расположением поверхностей нагрева в каждом корпусе (моноблоке).
В котле ТПП-110 в одном корпусе размещена основная часть первичного пароперегревателя, во втором корпусе – остальная
часть этого пароперегревателя и вся поверхность нагрева промежуточного пароперегревателя. При таком расположении пароперегревателей температура пара в каждом из них регулируется путем изменения соотношения «питательная вода – топливо». Дополнительно температура промежуточного пара регулируется в газопаровом теплообменнике.
Перераспределение тепловой нагрузки между корпусами, которое имеет место при регулировании температуры пара, нежелательно, поскольку при сжигании антрацитового штыба и других видов низкореакционного топлива происходит снижение температуры горячего воздуха, что приводит к увеличению потерь теплоты от недожога топлива.
В двухкорпусном паровом котле модели ПК-39, изготовленном по Т-образной схеме, первичный и промежуточный пароперегреватели расположены в четырех конвективных шахтах корпусов несимметрично к вертикальной оси котла. При изменении количества продуктов сгорания в правой и левой конвективной шахте каждого корпуса происходит перераспределение тепловосприятия первичным и промежуточным пароперегревателями, что приводит к изменению температуры пара. В двухкорпусном паровом котле с симметричными корпусами моделей ТПП-200, ТПП-200-1 конвективные шахты каждого корпуса разделены на три части вертикальными перегородками. В средней части конвективной шахты размещаются пакеты водяного экономайзера, в двух крайних – пакеты конвективного пароперегревателя высокого давления и промежуточного.
Опыт эксплуатации котлов ТПП-110 подтвердил возможность регулирования температуры первичного и промежуточного пара путем изменения соотношения «питательная вода–топливо» в каждом из корпусов. Вместе с тем при эксплуатации этих котлов наблюдалось повышенное количество их аварийных остановок. Существенно усложнялась эксплуатация котлов. Аналогичная картина наблюдалась при опытной эксплуатации котла ПК-39.
Рис. 2.13. Конструктивная схема парового котла ТПП-312А
В дальнейшем вместо этих котлов производились двухкорпусные агрегаты, но с симметричным расположением поверхностей нагрева в корпусах – дубль-блоки (ТПП-210, ТПП-210А, ТГМП-114, ПК-41, ПК-49, П-50).
Применение двухкорпусных котлов с симметричным расположением поверхностей нагрева повышает надёжность работы энергоблока. При аварийной остановке одного из корпусов энергоблок может работать с пониженной нагрузкой на другом корпусе. Однако работа с одним корпусом менее экономична. К недостаткам двухкорпусных котлов относится также сложность схемы трубопроводов, большое количество арматуры, повышенная стоимость.
Опыт эксплуатации энергоблоков с котлами сверхкритического давления показал, что коэффициент использования агрегатов с одним корпусом не ниже, чем с двумя. Кроме того, вследствие уменьшения количества пароводяной арматуры и приборов автоматического регулирования упрощается обслуживание энергоблоков с однокорпусными котлами. Эти обстоятельства обусловили переход к производству однокорпусных котлов сверхкритического давления.
Паровой котел ТПП-312А паропроизводительностью 1000 т/ч (рис. 2.13) предназначен для работы на каменном угле в блоке с турбиной 300 МВт. Он вырабатывает перегретый пар с давлением 25 МПа и температурой 545°С и имеет к. п.д. 92%. Котел – однокорпусный, с промперегревом, П-образной компоновки с открытой призматической топочной камерой. Экраны по высоте топочной камеры разделены на четыре части: нижнюю радиационную часть, среднюю, состоящую из двух частей, и верхнюю радиационную часть. Нижняя часть топочной камеры экранирована ошипованными, покрытыми карборундом, трубами. Шлакоудаление – жидкое. На выходе из топочной камеры расположен ширмовый пароперегреватель, в конвективной шахте – конвективные пароперегреватели высокого и низкого давления. Температура пара высокого давления регулируется впрыском питательной воды, а пара низкого давления – паропаровым теплообменником. Подогрев воздуха осуществляется в регенеративных воздухоподогревателях.
Разработаны и находятся в эксплуатации следующие однокорпусные котлы сверхкритического давления: пылеугольные ТПП-312, П-57, П-67, газомазутные ТГМП-314, ТГМП324, ТГМП-344, ТГМП-204, ТГМП-1204. В 2007 году на ТКЗ «Красный котельщик» изготовлены котлы ТПП-660 паропроизводительностью 2225 т/ч и давлением пара на выходе 25 МПа для энергоблоков ТЭС «Бар» (Индия). Срок службы котлов – 50 лет.
На последнем энергоблоке ТЭС «Hemweg» в Нидерландах (см. раздел 4) установлен паровой двухпроходной котел по технологии Бенсона (рис. 2.14) паропроизводительностью при полной нагрузке 1980 т/ч, спроектированный фирмой «Mitsui Babcock Energy» и предназначенный для работы на каменном угле (как основном виде топлива) и газе в блоке с турбиной мощностью 680 МВт.
Этот радиационный прямоточный котел сверхкритического давления вырабатывает пар с давлением 26 МПа и температурой 540/568°С.
Он работает в режиме модифицированного скользящего давления, при котором давление турбины на входе регулируется до уровня, меняющегося вместе с нагрузкой энергоблока.
Котел оборудован тремя пароперегревателями с промежуточными впрыскивающими пароохладителями и двумя блоками промежуточных пароперегревателей (хотя это цикл с однократным промежуточным перегревом). Экономайзер представляет собой горизонтальный змеевик из труб с ребристой поверхностью. Первичный пароперегреватель устроен в виде одного горизонтального и одного вертикального блока. Вторичный ширмовый пароперегреватель представляет собой подвесной одноконтурный блок, а последняя ступень пароперегревателя также выполнена в виде одноконтурного подвесного блока. Температура острого пара на выходе котла 540°С. Система промежуточного пароперегревателя котла имеет две ступени – первичную и конечную. Первичная ступень включает два горизонтальных блока, конечная ступень промперегрева представлена вертикальным блоком в виде сложенного контура, расположенного в газоходе котла. На выходе котла температура перегретого пара составляет 568°С.
Рис. 2.15. Общая схема современного газомазутного парового котла ТГМП-805С3 (в разрезе)
Рис. 2.14. Котел сверхкритического давления ТЭС «Hemweg» (Нидерланды) в разрезе: 1 – горелки с низким выделением NO x ; 2 – отверстия острого дутья; 3 – перегреватели высокого давления; 4 – промпароперегреватель; 5 – насос; 6 – корпус сепаратора
Система сажеобдувки котла состоит из 107 воздуходувок, приводимых в действие программируемым логическим контроллером. Удаление зольного остатка осуществляется скребковым конвейером, проходящим под топкой, и гидравлическим транспортом до резервуара-фильтра для зольного остатка.
Температура дымовых газов на выходе составляет около 350°С. Далее они охлаждаются до 130°С во вращающихся регенеративных воздухоподогревателях.
Конструкция котла предусматривает минимизацию выбросов NO x за счет использования горелок с низким выделением NO x и острого дутья. Достижению хороших экологических показателей способствует десульфуризация дымовых газов, позволяющая удалять SO 2 из отработанных газов.
Современный газомазутный паровой котел ТГМП-805СЗ (рис.2.15) паропроизводительностью 2650 т/ч предназначен для выработки перегретого пара с рабочим давлением 25,5 МПа и температурой 545 °C для паровой турбины мощностью 800 МВт. Котел прямоточный, газомазутный, однокорпусный, подвешен на хребтовых балках, опирающихся на колонны здания котельного отделения, и может устанавливаться в районах с сейсмичностью 8 баллов. Он имеет открытую топочную камеру призматической формы. Она образована цельносварными трубчатыми панелями, в нижней части которых размещается цельносварной горизонтальный подовый экран, а в верхней части – горизонтальный газоход, закрытый сверху цельносварным трубчатым потолочным экраном. Экраны топочной камеры разделены по высоте на нижнюю и верхнюю радиационные части.
На фронтовой и задней стенах топочной камеры котла размещены 36 газомазутных горелок. В горизонтальном газоходе последовательно по ходу газов размещены пять вертикальных конвективных поверхностей нагрева – парогенерирующая поверхность нагрева, включенная в пароводяной тракт котла до встроенной задвижки, три части пароперегревателя высокого давления, выходная ступень пароперегревателя низкого давления.
Регулирование температуры вторичного пара осуществляется с помощью рециркулирующих газов. В опускном газоходе, экранированном цельносварными трубчатыми панелями, последовательно по ходу газов размещены входная ступень пароперегревателя низкого давления и водяной экономайзер.
Одним из самых значительных достижений теплоэнергетики конца ХХ века в мире стало внедрение суперсверхкритических котлов, которые в настоящее время способны работать при давлении пара на выходе 30 МПа и температуре 600/650°С. Это стало возможным благодаря разработкам в области технологии материалов, которые могут выдерживать условия высоких температур и давлений. В «большой энергетике» уже работают котлы (их чаще называют «парогенераторами») производительностью более 4000 т/ч. Такие котлы обеспечивают паром энергоблоки 1000–1300 МВт на электростанциях в США, России, Японии и в некоторых странах Европы.
В настоящее время продолжается разработка новых моделей паровых котлов для энергоблоков ТЭС. При этом котлы конструируются как на суперсверхкритические, сверхкритические, так и докритические параметры пара. К примеру, на 2 энергоблоках ТЭС «Нейвели» (Индия) мощностью по 210 МВт каждый установлены паровые котлы Еп-690-15,4-540 ЛТ, предназначенные для работы на низкокалорийных индийских лигнитах. Это барабанные котлы с естественной циркуляцией, докритического давления с промперегревом, однокорпусные, с твердым шлако-удалением, башенного типа. Паропроизводительность такого котла 690 т/ч, параметры пара – давление 15,4 МПа на выходе из котла и 3,5 МПа на выходе из промпароперегревателя, температура пара 540°С.
ТЭС «Нейвели» (Индия) – 2×210 МВт – с котлами башенного типа Еп-690-15,4-540 ЛТ
Топочная камера котла открытая и оборудована 12 спаренными прямоточными многоканальными горелками, установленными на всех стенах топки в два яруса. Для очистки поверхностей нагрева установлены аппараты водяной и паровой обдувки.
Необходимо отметить, что энергетика стран СНГ базируется на применении двух типов паровых котлов – прямоточных и котлов с естественной циркуляцией. В зарубежной практике наравне с прямоточными котлами широко используются котлы с принудительной циркуляцией.
Кроме основных – паровых котлов высокого и сверхкритического давления – на ТЭС в настоящее время используются и другие типы котлов: пиковые водогрейные котлы, котлы для сжигания углей в кипящем слое, котлы с циркуляционным кипящим слоем и котлы-утилизаторы. Некоторые из них и станут прообразом котлов для будущего развития теплоэнергетики.
Детализированная модель котла Бэбкока и Уилкокса из анодированной латуни и имитации кирпича в разрезе масштаба 1½ дюйма: 1 фут 1885 года
Детали
Детализированная модель котла Бэбкока и Уилкокса из анодированной латуни и имитации кирпича в разрезе 1½ дюймов: 1 фут примерно 1885 года
с приклепанным верхним барабаном с фитингами, включая двойные водомеры, манометр, грузоподъемный предохранительный клапан, дренажный и главный запорные клапаны и задний грязевой люк с перемычками, установленными над наклонным блоком из шестидесяти трех водопроводных труб с имитацией огнеупорного кирпича и кирпичным кожухом с люками для доступа , противопожарные и зольниковые дверцы, решетку и зольник, установленные на деревянной подставке с латунной пластиной с гравировкой

См. цветную иллюстрацию
Особое примечание
НДС по ставке 5% уплачивается по цене с молотка плюс премия покупателя.
Этот лот, если он не будет очищен до 13:00 следующего рабочего дня после продажи, будет отправлен на склад: Cadogan Tate Ltd., Fine Art Services Cadogan House, 2 Relay Road, London W12 7SJ. Тел.: 44(0)20 8735 3700. Факс: 44(0)20 8735 3701. Лоты будут доступны для сбора после передачи в Cadogan Tate, каждый будний день с 9до 17:00. Первоначальный сбор за передачу и администрирование в размере 3,20 фунтов стерлингов (картины) или 18,50 фунтов стерлингов (мебель/предметы) и плата за хранение в размере 1,60 фунтов стерлингов (картины) или 3,20 фунтов стерлингов (мебель/предметы) за лот в день подлежат оплате Cadogan Tate.
Ньюкомен и другие первые разработчики паровых двигателей и котлов не были просто вдохновленными механиками, делавшими открытия более или менее случайно. Они хорошо знали свой предмет, и каждый шаг вперед в области давления, температуры и сгорания был основан на сознательном поиске большей эффективности и большей выходной мощности от меньших машин. Это привело к постоянному совершенствованию двигателей. Паровые котлы также улучшились, но достигли плато в середине девятнадцатого века из-за ограничений широко используемого жаротрубного котла по давлению, температуре, единичной мощности и безопасности.

Водотрубный котел был бессрочным изобретением — его разработка продолжается и по сей день — и не собирается останавливаться. Появление центральных станций для выработки электроэнергии в 1881 году открыло огромный новый рынок для котлов B&W. Оригинальный котел Babcock & Wilcox постоянно совершенствовался с 1867 года, и примерно в это же время был представлен котел, представленный этой моделью. Тысячи этих котлов были проданы, и даже сегодня некоторые продаются за границу для специального назначения. Многие из них до сих пор используются, особенно за границей. Конструкция с модификациями была стандартом B&W в течение многих лет и была заменена другими конструкциями только тогда, когда требования к высоким давлениям и температурам и значительному увеличению мощности отдельных котлов сделали изменения полезными.
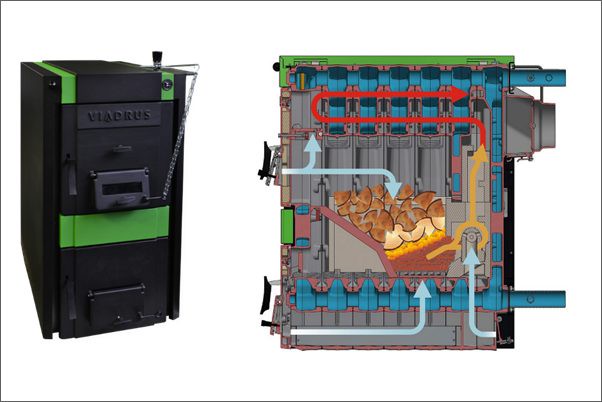
Паровые и водяные барабаны изготовлены из чугуна или стали с фланцами повышенной толщины и соединены двойными заклепками.

МОНТАЖ
При монтаже этого котла он подвешивается полностью независимо от кирпичной кладки на кованых балках, опирающихся на железные колонны. Это позволяет избежать деформации котла из-за неравномерного расширения между ним и его ограждающей стенкой и позволяет при необходимости ремонтировать или снимать кирпичную кладку, никоим образом не нарушая работу котла. Все светильники очень тяжелые и имеют аккуратный дизайн.
ЭКСПЛУАТАЦИЯ
Огонь производится под передним и верхним концом труб, а продукты сгорания проходят вверх между трубами в камеру сгорания под пароводяным барабаном; оттуда они проходят вниз между трубами, затем еще раз вверх через промежутки между трубами и выходят в дымоход. Вода внутри трубок при нагревании имеет тенденцию подниматься к верхнему концу и по мере того, как она превращается в пар, смешанный столб пара и воды имеет меньший удельный вес, чем твердая вода на заднем конце трубы. котел — поднимается по вертикальным каналам в барабан над трубами, где пар отделяется от воды, а последняя стекает назад и снова вниз по трубам в непрерывной циркуляции. Поскольку все проходы большие и свободные, эта циркуляция происходит очень быстро, выметая пар так же быстро, как он образуется, и снабжая его место водой; поглощать тепло огня с максимальной выгодой; вызывая тщательное перемешивание воды во всем котле и, как следствие, равную температуру, а также предотвращая, в значительной степени, образование отложений или накипи на поверхностях нагрева, сметая их и откладывая в грязевой барабан, откуда они выдуваются .
Пар отводится в верхнюю часть парового барабана возле задней части котла после того, как он полностью отделится от воды.
Заявленные преимущества «по сравнению с обычной конструкцией»:
1. Тонкая поверхность нагрева в печи
2. Стыки удалены от огня
3. Большая площадь тяги
4. Полное сгорание
5. Тщательное поглощение тепла
6 .Эффективная циркуляция воды
7. Быстрое пропаривание
8. Сухость пара
9. Стабильность уровня воды
10. Свобода расширения
11. Взрывобезопасность
12. Эксплуатация на полную мощность
13. Доступность для очистки
14. Наименьшая потеря эффекта от дымовой пыли
15. Долговечность
16. Легкость транспортировки
17. Отсутствие, и простота ремонта
18. Преимущества, подтвержденные практическим опытом
Копия публикации B&W HIGH PRESSURE, опубликованной в 1895 году, прилагается. Он предоставляет дополнительную информацию не только о деталях конструкции, но и иллюстрации производственных мощностей B&W и конкурентоспособных котлов того времени.
;
Бойлеры ~ Подводное плавание с аквалангом в Нью-Джерси
Бойлеры
Типичный шотландский котел (в разрезе) Бойлеры являются одним из наиболее распространенных признаков кораблекрушения, которые можно найти почти на всех судах с двигателями. Задача котла — производить пар высокого давления для двигателя, который приводит в движение судно. Паровые котлы используются с начала 1800-х годов до наших дней.
Большинство морских котлов относятся к одному из двух типов: жаротрубные и водотрубные. В жаротрубном котле внешний сосуд высокого давления содержит воду, а горячие дымовые газы направляются через маленькие трубы — «жаротрубные трубы» — внутрь, как показано выше. Преимущество этого типа котлов заключалось в том, что им было легче управлять, но в то же время большой объем воды и пара под давлением означал, что выход из строя котла приводил к огромному и обычно катастрофическому взрыву. Они распространены в первых морских приложениях и почти универсальны в локомотивах.
Позже стали использовать водотрубные котлы. В них использовались резервуары для воды гораздо меньшего размера, соединенные между собой водяными трубами, которые нагревались в дымоходе печи. Обычно требуется заключительная стадия «перегрева», чтобы получить пар с пригодной для использования температурой и давлением. Водотрубные котлы более сложны в эксплуатации, но также быстрее «запариваются» в холодном состоянии и менее подвержены катастрофическим взрывам. Меньший размер и меньший вес делают их полезными в мобильных приложениях. Хотя они полностью заменили старые технологии в морском использовании, водотрубные котлы не пользовались успехом в локомотивах и редко использовались.
Из-за высоких давлений котлы были очень прочно изготовлены из железа и стали. Котлы обычно имеют цилиндрическую форму снаружи, с множеством небольших трубок и ребер внутри. На более ранних судах, как правило, было несколько небольших котлов, а на более поздних — только один или два больших. Котлы могли работать либо на угле, либо, на более поздних судах, на нефти. Котел часто является последней частью крушения, которая поддается разрушительной силе моря.
Многие более поздние парусные суда, баржи и шхуны также несли небольшие котлы, хотя и не для движения. Известные как «ослиные котлы» и обычно устанавливаемые в носовой части судна, они использовались для питания паровых лебедок и другого оборудования на судне, заменяя рабочую силу для таких задач, как подъем якоря.
Жаротрубный котел В жаротрубном котле горячие газы из камеры сгорания проходят через трубы, соединяющие перфорированные концевые плиты. Затем газы попадают в «дымовой ящик» и проходят в дымовую трубу. Такая конструкция типична для ранних морских установок для лодок и котлов паровозов. В водотрубном котле вода перегревается в трубах, подвергающихся воздействию горячих газов. Существенным преимуществом этого типа является то, что вероятность катастрофического отказа меньше, так как в котле нет большого количества воды, а также нет крупных механических элементов, подверженных выходу из строя.
Котлы на затонувших кораблях девятнадцатого века, таких как Delaware , как правило, разрушаются или прогибаются, обнажая дымовые трубы и другие внутренние компоненты. Те, что на более поздних обломках, таких как Mohawk , скорее всего, будут целыми и выглядят как большие, а иногда и огромные железные цилиндры.
Котлы на Делавэр . На переднем плане целая. Рядом с этим находится разрушенный; всего их четыре. На заднем плане — двигатель. Небольшой ослиный котел на затонувшем корабле «Биг Хэнкинс». Верх исчез, видны дымовые трубы внутри. Задняя (южная) сторона оставшегося котла на Mohawk с крышками для дымогарных труб. Передняя часть котла сплошная. Обратите внимание на большую трещину в углу. Противоположность котла — конденсатор Такой конденсатор использовался для охлаждения отработанного пара двигателя морской водой. Это преследовало две цели: во-первых, восстановить пресную воду для повторного использования в котле, а во-вторых, создать вакуум на стороне выпуска двигателя, увеличив его мощность.