- Производство водорода с помощью машины на дровах
- Как получают водород в промышленности: способы выделения
- Alfa Laval — Производство водорода
- Установка производства водорода, назначение, технология, схема
- Водород, получение водяного пара — Справочник химика 21
- Паровая конверсия
- (PDF) НАЦИОНАЛЬНАЯ АКАДЕМИЯ НАУК УКРАИНЫ ИНСТИТУТ ПРОБЛЕМ МАШИНОСТРОЕНИЯ
- Улучшение цикла и водородный перегрев пара на Мутновской геотермальной электростанции
- Альфа Лаваль — Производство водорода
- Текущее состояние и будущие разработки
- 1. Введение
- 2. Водород из ископаемого топлива
- 2.1. Паровой риформинг
- 2.2. Частичное окисление
- 2.3. Автотермический риформинг
- 2.4. Сдвиг вода-газ, предпочтительное окисление и метанирование
- 2,5. Десульфуризация
- 2.6. Плазменный риформинг
- 3. Водород из возобновляемых источников
- 3.1. Газификация биомассы
- 3.2. Пиролиз и копиролиз
- 3.3. Риформинг в водной фазе
- 3.4. Электролиз
- 3.5. Фотоэлектролиз
- 3.6. Термохимическое расщепление воды
- 4. Экономические аспекты производства водорода
- 5. Выводы
- Номенклатура
- Благодарности
- Лучший способ получить водород из воды
- Образование сероводорода в процессе термического повышения нефтеотдачи в условиях перегретого пара
- Водород дешевеет — pv magazine International
- Способ получения водорода и кислорода из воды
Производство водорода с помощью машины на дровах
Известно — производство водорода из воды это энергозатратный процесс. На выделение водорода нужно потратить в 3–4 раза больше энергии чем мы потом получим с выделенного водорода. По этой причине машины на топливных элементах сложны и дороги ($60 000), а производство и хранение водорода целая индустрия которая врядли станет массовой ближайшие десятилетия.
Здесь хочу рассказать о возможном способе получения водорода с помощью автомобильного газогенератора и попутного его использования для езды машины на дровах — увеличивая тем самым мощность двигателя и уменьшая расход дров.
Откуда взять энергию на расщепление воды
При работе автомобильного газогенератора выделяется очень много тепла. В среднем при горении 1кг дров (данные усредненные) выделяется 4кВт энергии. Четверка жигули за час сжигает от 20кг дров, газ 24 — от 35кг.
Температура газа после реактора около 900 градусов, на выходе из бункера 100–400 (бункер развеивает жар в атмосферу).
От себя скажу, что во время испытания своей четверки на дровах за метр от газогенератора жар стоял как возле раскаленной буржуйки. В общем тепла сбрасывается в атмосферу много. Плюс мы обязаны охлаждать газ по максимуму тоже вынужденно сбрасывая киловатты тепла в атмосферу.
Можно попробовать эту энергию использовать с пользой — производя с её помощью водород.
В этом нам поможет железная стружка или старые метизы (гвозди, болты, гайки).
Снимая жар с стенок газогенератора (это можно делать как извне, так и изнутри) мы делаем 2 полезных дела — охлаждаем конечный газ который должен поступать в двигатель как можно более холодным (для наполнения цилиндров более богатой смесью) и одновременно увеличиваем процентное содержание полезного газа в смеси.
Нагревая воду до состояния перегретого пара (испытания в СССР для газогенераторов с подачей воды показали что оптимальная температура 300 градусов) мы пропускаем её через любое железо. Желательно чтобы оно было мелко нарублено — оптимальный размер «щепа».
Кислород обожает железо, пропуская через него перегретый пар мы осаждаем кислород на железе и получаем большое количество оторвавшегося водорода. Водород идет по трубам в карбюратор автомобиля смешиваясь с газом сделанным из древесины.
Ржавчина осаждается очень просто — во время езды автомобиль трясет и ящик с ржавыми метизами трясется осаждая ржавчину на дне — все что нужно сделать это вварить шаровый кран в днище для осыпания ржавчины или промывки.
Даже незначительное повышение полезного газа в составе древесного газа значительно увеличит мощность двигателя.
Вот такой состав полезного газа из того что засасывает двигатель.
- Метан 1–4%
- Водород 13%
- Остальное балластовые газы — недореагировавший углекислый газ около 5%, азот 50–60%.
Мы видим, что полезного газа около 30%, остальные 70% впустую заходят двигатель занимая ненужное пространство.
По этой причине машины на дровах (в статье идет речь именно о дровах как топливе не беря в расчет древесный уголь или каменный там все по другому) теряют до 35% мощности от бензиновой.
Теперь мы можем увеличить число полезного газа.
Но опять же есть некоторые «но». Дело в том что большое количество водорода вредно для поршней. Водород это газ с очень быстрым фронтом распространения пламени в 5–6 раз быстрее чем у метана. Метан «медленно» загорается по этой причине при переводе машины на метан нужно выставлять еще более раннее зажигание чем на бензине на как минимум на 10 градусов в противном случае часть метана будет гореть не в цилиндрах, а в выхлопной трубе.
Водород же напротив хорош для создания водородной бомбы с быстрым разрушительным эффектом, а вот на двигатель он влияет плохо — могут возникнуть микротрещины в поршнях и других деталях.
Я подымал этот вопрос в общении с отечественными академиками и они навели меня на мысль о покрытии двигателя наноматериалами изнутри. Некоторые из них разрабатывали смеси, которые покрывали детали двигателя защитной пленкой которая могла бы помочь в защите ДВС от разрушительного свойства водорода. Но это пока теория не проверенная практикой — если кто либо из читателей знает о применяющихся способах защиты от такого эффекта — напишите.
Жду полезных советов. [пост на geektimes.ru, NNN]
Как получают водород в промышленности: способы выделения
Водород считается одним из наиболее ценных видов сырья для синтеза аммиака и производства полимеров и нефтехимии. Он используется для получения твердых жиров из масел растительного происхождения. Из-за высокой химической активности вещество в чистом виде практически не встречается в природе. Основные источники для получения водорода в промышленности — метан, содержащийся в природном газе, и вода. Специалисты отмечают также перспективность разделения попутных газов коксового производства, которые на большинстве предприятий сжигаются.
Способы выделения водорода из соединений
Самые распространенные способы получения водорода в промышленности:
- паровая конверсия метана и его гомологов;
- газификация кокса;
- электролитическое разложение воды.
Особенности работы оборудования для получения водорода
Метановый конвертор
Оборудование для получения водорода в промышленности методом паровой конверсии имеет сложную конструкцию и компоновку. В его состав входят парогенератор, компрессорная станция, подогревающая установка, конверторы метана и угарного газа. Система подключена к подающей магистрали и потребителям. Извлечение водорода происходит при температуре до 1000° C под избыточным давлением и в присутствии катализатора. Перед этим сырье подогревается, очищается от серосодержащих примесей и перемешивается с водяным паром.
Восстановление водорода происходит в два этапа.
- После первой ступени конверсии продукт содержит до 10% метана, для разложения которого в смесь вводят атмосферный воздух.
- В конце процесса водород очищают от кислорода и оксидов углерода, а избыточное тепло направляют в котел-утилизатор для производства водяного пара.
Процесс полностью замкнут и энергетически независим, но требует применения сложных схем контроля. Несмотря на недостатки, большую часть водорода в промышленности получают как раз этим способом.
Установка газификации кокса
Технология заключается в пропускании перегретого водяного пара через слой кокса, каменного или бурого углей при температуре свыше 1000° C без доступа кислорода.Полученная смесь водорода и окиси углерода обрабатывается водяным паром. Один из наиболее перспективных способов применения продуктов газификации угля — сжигание на тепловых электростанциях, поскольку современные установки отчаются высокой производительностью, сравнительно низкой себестоимостью конечного продукта и способны работать в непрерывном режиме.
Электролизеры
При помощи электролитических установок водород получают как в промышленности, так и для коммерческого использования. На рынке присутствует оборудование разной производительности, а сырьем служит обычная вода. Установка представляет собой сосуд с раствором щелочи или средней соли, в который погружены два электрода. При пропускании постоянного тока на катоде выделяется водород. Вторичный продукт реакции — кислород — также используется для решения технологических задач. Доочистка позволяет получить на выходе технически и химически чистый водород. Электролизер с вспомогательным оборудованием для водоподготовки и осушения размещается на небольшой площади. Многие производители предлагают мобильные моноблочные и контейнерные установки.
Среди всех способов получения водорода в промышленности электролитический считается наиболее экологичным. Единственный его условный недостаток — зависимость от качества сети питания.
Alfa Laval — Производство водорода
Оптимизация процессов производства водорода на НПЗВысокие рабочие температуры, давления и высокое содержание водорода предъявляют жесткие требования к качеству и надежности оборудования, используемого для производства водорода. Альфа Лаваль предлагает свой опыт, проверенные технологии и широкий спектр услуг для удовлетворения этих потребностей.
Избыточное тепло технологического процесса используется для выработки перегретого пара высокого давления в котле-утилизаторе.
К этой системе предъявляются очень жесткие требования. Она должна обеспечить утилизацию максимального количества энергии технологического газа для увеличения выработки пара. Кроме того, высокие температуры и расходы технологических газов подвергают оборудование большой нагрузке и создают опасность возникновения отказов.
Котлы-утилизаторы Альфа Лаваль OLMI обеспечивают максимальные срок службы и надежность. Запатентованная конструкция перепускного газового канала OLMI сводит к минимуму опасность металлического запыливания. Правильные конструкция и выбор материалов также сводят к минимуму риск поломок трубной решетки и искривления трубного пучка.
Кроме того, все механические конструкции проверяются с помощью анализа методом конечных элементов (FEA).
Повышенная производительностьДля максимального увеличения производства пара вся система котла-утилизатора должна быть оптимизирована с точки зрения конструкции котла-утилизатора, а также компоновки и высоты стояков и барабана.
Альфа Лаваль оптимизирует эффективность котла, обеспечивая максимальную площадь теплопередающей поверхности в отдельных котлах, а также сводя к минимуму опасность неравномерного распределения во впускной газовой камере.
Полный комплект поставкиАльфа Лаваль может поставить не только предварительные нагреватели питательной воды котла, котел-утилизатор, паровой барабан и пароперегреватель. Мы также предоставляем инжиниринговые услуги, обеспечиваем поставку и монтаж всей системы котла-утилизатора.
Оборудование Альфа Лаваль OLMI используется в установках производства водорода во всем мире. Комплект поставки может варьироваться от отдельных охладителей технологического газа или котлов-утилизаторов до полностью завершенных систем.
Кроме того, теплообменники Альфа Лаваль Compabloc и DuroShell обычно используются для окончательного охлаждения синтетического газа в установках парового риформинга или адсорбции при переменном давлении для сведения к минимуму общей стоимости монтажа оборудования, а также для сокращения занимаемой площади и снижения требований к системе водяного охлаждения.
Установка производства водорода, назначение, технология, схема
Назначение
Установка производства водорода предназначена для обеспечения техническим водородом вновь вводимых установок:
- изомеризации,
- гидроочистки,
- гидрокрекинга,
- каталитического риформинга.
Строительство установки производства водорода позволит:
- ликвидировать недостающую потребность в водороде на НПЗ
- производить водород высокой чистоты (не менее 99,5 % об.), что сокращает объём газа в последующих схемах потребления водорода;
- улучшить экологические условия на территории предприятия за счёт применения в качестве топлива обессеренного газа с блока КЦА.
Методы производства водорода
- паровая конверсия метана и природного газа;
- газификация угля;
- электролиз воды;
- пиролиз;
- частичное окисление;
- биотехнологии.
Сырье и продукты
На российских НПЗ наиболее распространенным методом получения водорода является паровая конверсия углеводородов (СУГ, нафты, природного газа).
Продуктами являются чистый водород с концентрацией >99% об., а также отдувочный газ, который чаще всего используется в качестве топлива для печей.
Катализаторы
Наиболее часто используемыми в промышленности катализаторами для процесса паровой конверсии являются катализаторы на основе никеля, однако в ряде специфических процессов допускается использование благородных металлов платиновой группы.
Технологическая схема
В состав установки производства водорода входят следующие блоки и узлы:
- блок подготовки и очистки сырья;
- блок предриформинга;
- блок парового риформинга;
- блок конверсии и охлаждения конвертированного газа;
- блок очистки водородсодержащего газа по технологии КЦА;
- блок утилизации тепла продуктовых потоков и дымовых газов.
Очистка сырья
Природный газ поступает в подогреватель, нагревается до температуры 40 °С. Для гидрирования сернистых соединений, содержащихся в сырье, до сероводорода, требуется небольшое количество водорода.
С этой целью часть водорода, полученного на установке, подается в качестве рециркуляционного водорода в поток сырья. Смесь сырья и рециркулирующего водорода, последовательно поступая в теплообменники, нагревается до температуры 380 °С, необходимой для предварительной очистки сырья.
Подогретая газосырьевая смесь поступает в реактор гидрообессеривания, где происходит гидрирование соединений серы до H2S. Газосырьевая смесь из реактора последовательно проходит через адсорберы, где происходит улавливание хлоридов (НСl) и сернистых соединений (H2S). В каждом из этих реакторов имеется три слоя катализатора:
- модифицированный оксид алюминия для удаления НСl,
- оксид цинка,
- слой специального катализатора для эффективного и глубокого удаления H2S.
Предриформинг
Очищенная газосырьевая смесь смешивается с перегретым паром высокого давления. Соотношение расходов регулируется с поддержанием заданного мольного соотношения водяного пара и углерода. Величина значения этого соотношения зависит от типа сырья, подаваемого на установку.
Далее парогазовая смесь нагревается до температуры реакции 475 °С – 500 °С, в змеевике подогрева сырья предриформинга, расположенном в конвекционной секции печи парового риформинга и направляется в реактор предриформинга.
Предриформинг служит для превращения тяжелых углеводородов, содержащихся в сырье, в метан, а также для частичного проведения реакций риформинга, при этом эффективность процесса повышается.
В зависимости от типа перерабатываемого сырья, может наблюдаться увеличение или снижение общей температуры по реактору. Так при переработке бензинов увеличивается общая температура по реактору, за счет преобладания протекания реакций с экзотермическим эффектом, а при переработке природного газа температура по реактору падает, за счет протекания реакций с эндотермическим эффектом.
Риформинг
Парогазовая смесь нагревается до температуры 650 °С в змеевике подогрева сырья риформинга, расположенном в конвекционной секции печи парового риформинга, и затем поступает в коллектор, расположенный в радиантной секции печи парового риформинга.
В радиантной секции печи парового риформинга смесь сырья и пара поступает в катализаторные трубы, находящиеся в радиантной секции печи парового риформинга Н-1, проходит сверху вниз катализаторные трубы. В результате реакции, протекающей на катализаторе, загруженном в катализаторные трубы, получается равновесная смесь, состоящая из Н2, СО, СO2, СН4 и Н2O.
Для предотвращения образования кокса и отложения его на катализаторе технологический пар подается в избытке, превышая стехиометрическое количество, требуемого на реакцию.
Полученный конвертированный газ (парогазопродуктовая смесь) выходит из печи парового риформинга при температуре 888 °С и далее направляется в теплообменник. В теплообменнике происходит охлаждение питательной воды до температуры 320-343 °С, регенерированное тепло используется для генерирования насыщенного пара высокого давления.
Общий тепловой эффект реакций парового риформинга является в сильной степени эндотермическим, поэтому для достижения требуемой степени конверсии необходим подвод тепла.
Конструкция печи парового риформинга
Печь парового риформингаПечь имеет сложную конструкцию, разработанную с учетом технологических требований процесса с целью обеспечения безопасной эксплуатации и хорошими технико-экономическими показателями. Для обеспечения расчетной степени конверсии без перегрева внешней поверхности поддерживается необходимая температура газа в катализаторных трубах. Благодаря небольшому диаметру труб увеличивается площадь теплообменной поверхности и улучшается перемешивание газа в слое катализатора. В результате печи риформинга работают при максимальных давлениях и температурах.
По конструкции печь состоит из двух одинаковых радиантных камер, работающих параллельно, и расположенной над ними общей конвекционной камеры. Процесс паровой конверсии метана осуществляется в реакционных трубах при температуре 780-888 °С за счет внешнего обогрева.
Конверсия окиси углерода и охлаждение синтез-газа
Водородсодержащий газ после парового риформинга и охлаждения поступает в реактор высокотемпературной конверсии, где избыточный пар превращает большую часть СО в С02 и Н2 при прохождении через слой катализатора.
Синтез-газ, подвергнутый конверсии, охлаждается, отдавая тепло потокам системы выработки водяного пара. Далее частично охлажденный синтез-газ поступает в воздушный, а затем на доохлаждение в водяной холодильник, где охлаждается до температуры 35 °С и поступает в сепаратор для разделения смеси на неочищенный водород и технологический конденсат.
Технологический конденсат смешивается с химочищенной водой, поступающей из сетей завода и направляется в деаэратор, а неочищенный водород подается в блок короткоцикловой адсорбции.
Короткоцикловая адсорбция водородсодержащего газа
Поток неочищенного водородсодержащего газа поступает в блок короткоцикловой адсорбции (КЦА), где происходит удаление примесей в процессе циклической адсорбции. Для выполнения заданной степени концентрирования водорода и удаления примесей в процессе используются многочисленные адсорбционные слои. Принятая схема блока позволяет извлечь водород с концентрацией 99,5 % (об.) из конвертированного газа, а сбросной газ направляется в качестве топлива в реакторную печь.
В блоке КЦА происходит очистка конвертированного водородсодержащего газа от примесей метана, окислов углерода путем адсорбции загрязнений на адсорбенте при высоком давлении и десорбции при низком давлении.
Блок утилизации тепла дымовых газов
В блоке утилизации тепла дымовых газов и продуктовых потоков производится водяной пар высокого давления за счет охлаждения дымовых газов и продуктовых потоков. Одновременно с этим предусмотрено использование тепла дымовых газов для нагрева питательной воды, перегрева производимого водяного пара и подогрева воздуха, подаваемого к горелкам печи.
Материальный баланс
Наименование продукта | Измерение | Сутки | |
един.![]() | итого | % | |
Входы | |||
Сырьевой газ | т | 276,00 | 22,30 |
Расход пара ВД в предриформинг | т | 633,60 | 51,20 |
Расход пара ВД в риформинг | т | 327,90 | 26,50 |
Сумма сырья | т | 1 237,50 | 100,00 |
Выходы | |||
Водород с установки | т | 89,70 | |
Расход отдувочного газа с блока КЦА на печь | т | 605,10 | |
Расход технологического конденсата | т | 542,70 | |
Сумма продуктов | т | 1 237,50 |
Достоинства и недостатки
Недостатки
- Высокие выбросы дымовых газов в атмосферу
- Высокие капитальные затраты
- Высокая стоимость перегретого водяного пара
Достоинства
- Наиболее проработанный и распространенный вид производства водорода в нефтехимической промышленности
- Относительно низкие температуры процесса
- Вариативность проекта установки в зависимости от требований заказчика
Существующие установки
Спрос на водород растет в связи с переходом на потребление более чистых и легких нефтяных топлив, в то время как нефтяное сырье становится все тяжелее. В связи с этим трудно представить современный НПЗ без установки производства водорода. УПВ может отсутствовать только в составе НПЗ, работающих по профилю первичной переработки нефти. Стоит отметить, что для производств, обладающих развитой архитектурой вторичных процессов, ресурсов одной УПВ может быть недостаточно.
Водород, получение водяного пара — Справочник химика 21
В связи с уменьшением запасов углеводородного сырья большой интерес приобретает метод получения водорода восстановлением водяного пара раскаленным углем [c.274] Контактное производство серной кислоты. Первая операция — первичная переработка сырья — представляет собой обжиг колчедана в потоке воздуха или сжигание серы с получением газа, содержащего 7—10% 50г, 8—11% Ог, азот и незначительные по объему примеси огарковой пыли, водяных паров, серного ангидрида, окиси мышьяка, селена и, возможно, фтористого водорода. Тепло реакции используют в котлах-утилизаторах для получения водяного пара, стоимость которого с избытком компенсирует себестоимость обжига. [c.12]
Конверсионный способ получения водорода заключается в восстановлении водорода из водяного пара окисью углерода, содержащейся в продуктах газификации топлива или в продуктах конверсии газообразных углеводородов. [c.165]
Получение водорода из водяного пара и окиси углерода, взятых в отношении 1,5 I, над катализатором температура выше 300° [c.229]
В трубчатых аппаратах, применяемых для проведения сильно экзотермических процессов гидрирования (восстановление нитро-соедипений, гидрирование ароматических соединений), катализатор помещают в трубах диаметром 25—50 мм (рис. 151, а). Парогазовую смесь водорода с органическим реагентом обычно подают сверху (иногда снизу), и реакция протекает в трубах на зернах контакта. Выделяющееся тепло снимается хладоагентом, циркулирующим в межтрубном пространстве. В качестве хладоагента особенно подходит кипящий водный конденсат в этом случае можно утилизировать тепло реакции для получения водяного пара. [c.519]
Реакции гидродеалкилирования, сопровождающиеся отрывом метильных групп от моноциклических и бициклических ароматических углеводородов, в интервале температур 227—627°С протекают практически нацело [79, с. 245]. В качестве сырья для получения этим методом бензола широко используется толуол, ресурсы которого во многих странах превышают спрос на него, а также алкилароматические углеводороды жидких продуктов пиролиза. Деалкилирование с получением бензола осуществляется как на катализаторах, так и чисто термическим путем в присутствии водорода или водяного пара [79, с. 244—268 149, 150]. [c.193]
Передача полученного при электролизе водорода на большие расстояния может быть осуществлена лишь по трубопроводам, что не нашло широкого распространения. Поэтому водород используют, как правило, на месте производства в процессах гидрирования органических продуктов, синтеза хлорида водорода, для получения водяного пара, применяемого для нагрева различных технологических растворов. [c.46]
Вторая ступень конверсии протекает с выделением тепла. В результате получают поток горячих газов, тепло которого используется для получения водяного пара. Охлажденный газ поступает в конвертор СО, где окись углерода реагирует в присутствии катализатора с водяным паром, образуя дополнительное количество водорода и двуокиси углерода. [c.32]
Водород после очистки может быть выброшен в атмосферу либо использован в реакциях синтеза хлорида водорода, гидрирования, для получения водяного пара. [c.91]
Среди других методов, описанных в литературе для получения бромистых алкилов, можно упомянуть присоединение бромистого водорода к этиленовым углеводородам в присутствии абсорбента, состоящего из геля гидроокиси металла нагревание спирта или его сернокислого эфира с бромистоводородной кислотой в водном растворе при ИО—180° и под давлением для предотвращения образования паровой фазы обработку диалкилсульфата бромистым водородом в паровой фазе нагревание спирта, насыщенного бромистым водородом, вместе с бромистоводородной солью азотсодержащего гетероциклического соединения, например бромистоводородного пиридина расщепление алифатических простых эфиров бромистым водородом и водяным паром в Присутствии дегидратирующего катализатора . Алкилбромиды были получены также из высокомолекулярных спиртов насыщением спирта бромистым водородом при 100° . [c.122]
Водород получают тремя методами — химическим, электрохимическим и физическим. К химическим методам относятся получение водорода из водяного пара при взаимодействии с углеродом или с железом, из газообразных углеводородов [c.81]
После охлаждения газовую смесь, содержащую сероводород (до 80 %), углекислый газ, цианистый водород и водяные пары, подают на установку мокрого катализа для переработки сероводорода в серную кислоту. На рис. 6.7 показана технологическая схема установки для сжигания Н З и получения концентрированной серной кислоты. Установка работает следующим образом. Газовая смесь поступает в печь, в которой сероводород сжигается при температуре 700-800 С [c.172]
С и времени пребывания 0,005 —0,007 с получены следующие выходы продуктов (на мазут) 30—34% этилена, 11—13% пропилена, 3—4% бутадиена, 6—8% пироконденсата ч 25—32% тяжелой смолы пиролиза. С целью повышения технико-экономических показателей процесса высокотемпературного пиролиза мазута проводится усовершенствование технологической схемы пилотной установки и оснащение ее плазмотроном с электродуговым нагревателем для получения теплоносителя с температурой до 2500—3000 °С. В результате исследований по процессу высокотемпературного пиролиза на пилотной установке и анализа литературных данных разработана альтернативная схема высокоскоростного гидропиролиза, отличительными чертами которой являются давление — до 4 МПа, температура — до 1 000°С, малое (0,001—0,0002 с) время смешения и контакта высоконагретой смеси и теплоносителя, в качестве которого рекомендуются смеси оксида углерода и водорода или водяного пара н водорода, нагрев теплоносителя в высокотемпературном регенеративном нагревателе [430] или плазмотроне, использование газотурбинных установок [c.200]
Образец тщательно очищают ацетоном, прополаскивают в бензине и помещают в сухой воздух, где и взвешивают. Затем помещают в кварцевой лодочке в графитовый тигельный реактор и вдвигают в индукционную печь. Предварительно аргон очищают в течение 5 мин, нагревают систему до температуры 1100—1150°С (в случае ниобия). Затем нагревают в течение 20 мин в присутствии текущего аргона, скорость пропускания аргона 80 мл[мин. Полученный водород пропускают вместе с аргоном иад окисью меди при 650° С до количественного превращения водорода в водяные пары, которые впоследствии собираются в адсорбционной трубке, содержащей перхлорат магния. [c.20]
На блоках АТ в качестве отпаривающего агента обычно применяют перегретый водяной пар. Существенное преимущество его — полная конденсация в емкости верхнего продукта колонны, что исключает унос легких фракций продукта с отпаривающим агентом. Однако на получение водяного пара требуются большие затраты энергии, а тепло его конденсации не. используется. Кроме того, конденсация водяного пара приводит к обводнению продуктов разделения и необходимости их дополнительной обработки, В присутствии сероводорода и хлористого водорода водяной пар вызывает коррозию аппаратуры. [c.21]
Дегидрирование циклогексиламина в имин по термодинамическим характеристикам аналогично дегидрированию вторичных спиртов. Однако при наличии водяного пара равновесие непрерывно смещается вправо, поскольку имин почти необратимо превращается в циклогексанон. Часть циклогексанона гидрируется водородом в циклогексанол, а циклогексиламин может частично дегидрироваться в анилин. Селективными катализаторами реакции являются металлы V—VIII групп периодической системы, их окислы, а также медь, эффективные при 160—220 °С. С никелем на окиси хрома процесс осуществляют в паровой фазе при 160—200 °С и отношении амина к воде, равном 1 4. Полученный после конденсации паров и сепарации органический слой состоит из 80% циклогексанона, 10% циклогексиламина, 0,5% анилина и фенола, 9,5% циклогексанола, дициклогексиламина и других продуктов. Циклогексанон выделяют из смеси методами экстракции и ректификации, возвращая циклогексиламин на контактирование. В данном процессе можно исходить и непосредственно из анилина, пропуская его вместе с водородом и водяным паром (при мольном отношении 10 75 15) через те же контакты при температуре около 200°С. [c.661]
Окисление метана для получения водорода употребляют водяной пар, кислород или углекислый газ Смесь железа, никеля или кобальта с соединениями алюминия, содержащими кислород, кремний, углерод, бор, фосфор например каолин или боксит 1064 [c.189]
Продукты реакции охлаждают и затем разделяют водород и газы реакции возвращаются в цикл, а жидкие продукты (бензин гидроформинга) подвергаются ректификации. Регенерация катализатора осуществляется так же, как и на установках каталитического крекинга [18, 78] выжигом отложенного кокса в струе воздуха остаточный воздух вместе с газообразными продуктами горения (двуокись углерода, окись углерода, азот и др.) нагретыми до 600° С и применяют для получения водяного пара. В качестве сырья используется фракция бензина прямой гонки. [c.131]
Получение водорода действием водяного пара на предельные углеводороды рассматривается в гл. 10. [c.908]
При газификации иод нормальным давлением, как известно, в газ переходит не только весь водород разложенного водяного пара, но частично и водород органической массы топлива. При повышенном давлении этот водород топлива переходит в газообразное состояние главным образом в виде СН4. Кроме того, часть водорода, полученного в результате разложения водяного пара, связывается в углеводороды. Таким образом, повышение давления при газификации натуральных топлив способствует образованию углеводородов не только в результате реакций синтеза метана, но и вследствие процесса термического разложения органической массы топлива. [c.156]
ДИТСЯ быстрое охлаждение газов до 450 °С ( закалка ) путем впрыскивания воды на выходе их из контактного аппарата. Дальнейшее использование тепла реакционных газов существенно сказывается на повышении экономичности производства. Поэтому газы пропускают последовательно через перегреватель 3 и испаритель 2 для испарения и нагревания смеси, поступающей в реактор, и через котел-утилизатор 1 для получения водяного пара (его тоже применяют в процессе). Из котла-утилизатора газо-паровая смесь, направляется в холодильник 5, охлаждаемый водой. Часть паров конденсируется, а несконденсировавшийся газ, содержащий пары этилбензола и стирола, охлаждается дополнительно в рассольном холодильнике 6, после чего водород с примешанными к нему низшими углеводородами выводится в линию топливного газа. Конденсат из холодильников 5 VI 6 поступает в сепаратор 7 непрерывного действия, где органический слой отстаивается и отделяется от воды. Он стекает в промежуточную емкость 8 и направляется на дальнейшее разделение. В нем содержится около 37% стирола,, 61% этилбензола и 2% смеси бензола, толуола и более тяжелых продуктов. [c.667]
Схема установки для получения хлора показана на рис. 57. При проведении синтеза воздух из газометра пропускают через барботер, наполненный 20%-ной соляной кислотой. В случае достаточно малой скорости пропускания воздуха можно считать, что в выходящем газе парциальные давления хлорида водорода и водяного пара соответствуют равновесным давлениям Ph i и Рн,о- Равновесные давления НС1 и Н2О над раствором 20 %-ной [c. 126]
Основные условия и показатели работы контакта 4 при его восстановлении водяными и генераторными газами и окислении водяным паром приведены в табл. 31. Данные получены при стационарном процессе, когда контакт 4 восстанавливается и окисляется на 25%. Полученные показатели позволяют разработать технологические основы метода получения водорода из водяного пара на контакте 4 при низких температурах. [c.118]
Изучение физико-химических основ восстановления и окисления различных контактов позволило установить, что контакты на основе сплавных 1 атализаторов синтеза аммиака могут быть использованы для получения водорода из водяного пара при температурах порядка 900°С. При этих же температурах аммиачные контакты как мы их будем называть, после окисления могут быть восстановлены не только водородом, окисью углерода и их смесями, но и такими малореакционноспособными топливами, как ископаемые угли, коксы и метан. Для изучения физико-химических условий длительного попеременного восстановления ж окисления одной загрузки контактов при стационарных условиях было исследовано четыре аммиачных контакта, приготовленных на основе катализаторов синтеза аммиака типа ХТЗ-53, ГК-Звт, ч-5 и ГК-2. После предварительных испытаний катализатор ГК-2, показавший наименьшую производительность по водороду, подробно не исследовался. [c.118]
Для процессов, сопровождаемых обратимой химической реакцией между твердыми и газообразными реагентами, равновесные концентрации и равновесный выход продукта определяются при помощи константы равновесия, рассчитанной по концентрациям или парциальным давлением газообразных реагентов и газообразных продуктов реакции. При расчете константу равновесия выражают только через равновесные концентрации компонентов газовой фазы, поскольку парциальные давления насыщенных паров твердых веществ малы и почти не изменяются. Если реакция идет без изменения числа молей газа, равновесие зависит только от температуры. Примером могут служить обе стадии производства водорода железопаровым способом — восстановление водорода из водяного пара железом и регенерация железа восстановлением его из оксидов водородом и оксидом углерода (водяным газом газификации твердого топлива). При получении водорода протекают реакции [c.172]
Микроструктурные и электронографические исследования показали, что поверхность между чистым железом, полученным зонным методом, и слоем окисла, который его покрывает (слой получен действием смеси водорода и водяного пара в соответствующих пропорциях), является совершенно упорядоченной, в то время как в случае менее чистого железа наблюдают сег [c.366]
При современной технике возможно превращение метана в водород (конверсией водяных паров) непосредственным пиролизом или электрокрекингом либо переработкой его в разнообразные продукты хлорированием (с получением хлористого метила, хлористого метилена, хлороформа и четыреххлористого углерода), окислением (с получением формальдегида) или нитрацией с получением веществ, обладающих той же взрывчатой силой, что и нитроглицерин [26]. [c.294]
Промыщленным источником ЦПД являются жидкие продукты пиролиза фракций нефти, проводимого с целью получения этилена. В связи с этим необходимо было изучить влияние на. селективность и скорость гидрирования ЦПД примесей нециклических пентадиенов указанного сырья, а также разработать способ мономеризации ЦПД. В известных способах превращения дициклопентадиена в мономер теплоносителем служит или водород, или водяной пар, которые осложняют работу мембранного катализатора. Найдено [62], что эффективным теплоносителем, не снижающим активности катализатора и селективности гидрирования ЦПД в ЦПЕ, является доступный метан, а подача водорода через мембранный катализатор обеспечивает гораздо большую селективность по ЦПЕ при высоких конверсиях ЦПД, чем гидрирование в смеси с водородом при тех же условиях (см. кривые рис. 4.4). Даже большой избыток водорода в [c.109]
В настоящее время развивается новый метод проведения реакций, так называемый плазмоструйный, или метод п дазмотро-нов. В этом случае получают высокотемпературную плазму (например, водородную или пароводяную), быстро пропуская водород или водяные пары через сильноточную дугу. Благодаря большой скорости протока газа удается вытянуть плазму из зоны разряда. Вне разряда эта плазма смешивается со струей холодного реагирующего вещества, например, предельного углеводорода. При смешении происходит быстрое охлаждение плазмы, но при этом молекулы углеводорода подвергаются крекингу, т. е. разлагаются. Затем, благодаря вторичным процессам образуются продукты реакции. Таким способом удается, например, провести крекинг природных газов (метана и др.). В результате реакции получается главным образом ацетилен. Этот способ экономически выгоднее других способов получения ацетилена. [c.306]
Ниже на основании данных отечественной и зарубежной практики кратко описаны способы газификации твердых топлив для получения водяного, паро-воздушного, полуводяного (смесь водяного и паро-воздушного газов), паро-кислородного и паро-воздушпо-кислородного (полуводяного) газов. Перечисленные газы принято называть технологическими газами или синтез-газом, так как их используют в производстве аммиака, спиртов и водорода. [c.172]
При температуре ввода циркулирующего теплоносителя 1850°С и времени реакции 0,8 с происходит глубокое разложение исходного газа, в результате чего концентрация водорода в подученном газе составляет 95-96%. Тепло водорода и горячих газов регенерации используется для получения водяного пара. Науглерожввный теплоноситель при температуре 670 0 с понощью пвевмоподьемвпса направляется в печь-регенератор, где идет выжигание углерода и нагрев теплоносителя до температуры 1350-1400 с. Данный метод может быть использован для переработки как предельного, так и вевредель-ного сырья (табл. 14). [c.64]
Коксование нефтяных остатков идет преимущественно в кипящем слое. Кокс используется, главным образом, как энергетическое топливо для получения водяного пара. По мнению специалистов гидрогенизацйонные процессы для переработки нефтяных остатков получили бы распространение лишь при более дешевом водороде. [c.13]
Образование паров перекиси водорода из водяного пара и кислорода является сильно эндотермической реакцией по наиболее точным современным термодинамическим данным, образованию перекиси водорода соответствуют ккал1г-моль и Р1,, = 29,38 ккал г-моль. Хотя образованию перекиси водорода по этой реакции благоприятствуют высокие температуры и давления, все же, например даже при 1500° К и 1000 ат, смесь, содержащая сначала 1 моль воды на 0,5 моля кислорода, образует лишь 2,1 10″ моля перекиси водорода в равновесных условиях. Таким образом, очевидно, что перекись водорода, полученная из воды, в опытах, подобных описанному, возникает за счет ряда реакций, протекающих в условиях, далеких от равновесия. Начальной стадией, безусловно, является диссоциация молекулы воды, за которой следуют реакции с участием свободных радикалов, аналогичные некоторым реакциям, встречающимся при взаимодействии водорода и кислорода. [c.35]
Ловышенной стойкостью к водородной коррозии обладают стали с малым содержанием углерода чем ниже его содержание, тем менее заметно действие водорода. Оправдало себя применение рритной обезуглероженной стали, содержащей менее 0,02% С и полученной из стали 10 обработкой ее смесью водорода и водяного пара при температуре выше 700° С. [c.132]
Если сравнить полученные нами данные со степенями использования водорода и водяного пара при температурах выше 600° С по реакциям (5) и (6), приведенными в табл. 6, то можно видеть, что большая степень использования водорода, чем по реакции (9), может быть в том случае, если процесс восстановления проводить между фазами Гез04 FeO. [c.22]
Исследования в ИГИ и ГИАПе физико-химических закономерностей окисления и восстановления контактов позволили поставить вопрос о разработке высокопроизводительных контактных методов получения водорода из водяного пара с применением в качестве восстановителей природных и искусственных газов и твердых топлив (уголь, кокс). Между контактными и железопаровыми методами получения водорода имеется принципиальное различие, основанное на каталитическом воздействии контактов на процессы разложения водяного пара и окисление восстановителей. [c.110]
Паровая конверсия
Паровая конверсия — получение чистого водорода из лёгких углеводородов (например метана, пропан-бутановой фракции) путём каталитической конверсии углеводородов в присутствии водяного пара.
Знания специалистов нашей компании позволяют проектировать, строить и эксплуатировать установки по производству водорода для снабжения водородом Заказчика. Мы разрабатываем установки производства водорода методом парового реформинга от 300 до 200000 Нм3/час.
На рисунке показана стандартная технологическая схема для высокопроизводительной водородной установки.
Основные этапы процесса
1. Гидродесульфурация исходного сырья
2. Паровой риформинг
3. Утилизация тепла для генерации пара
4. Конверсия СО
5. Очистка водорода с помо¬щью короткоцикловой адсорбции
Описание процесса
Очистка сырья
Природный газ подается на установку, разделяясь на два потока: один служит топливом к горелкам печи риформинга, а второй служит сырьевым газом для технологического процесса. В последний поток дозируется водород из блока КЦА, после чего он подается на всас сырьевых компрессоров.
Альтернативным сырьем может служить жидкая нафта, испаренная за счет тепла технологического газа.
Гидродесульфуризация
После этого смесь сырьевого газа и водорода (сырьевой газ) проходит через секцию гидродесульфуризации. В блоке гидроочистки, с применением катализатора органические соединения серы преобразуются в h3S, с гидрогенизацией всех содержащихся олефинов. В секции десульфуризации полученный h3S оседает в виде сульфида цинка на катализаторе. h3S является ядом для катализатора риформинга.
Риформинг
Десульфурированный сырьевой газ смешивается с перегретым паром. Далее, эта смесь проходит по катализаторным трубам в печи риформинга с горелками.
В трубах печи риформинга углеводороды и пар дополнительно нагреваются в присутствии катализатора, с получением водорода, углекислого газа, угарного газа. Горячий технологический газ выходит из трубок с катализатором установки риформинга при температуре около 850°C и поступает в парогенератор отходящих продуктов установки риформинга при температуре около 820°C, где производится пар для процесса, а температура на выходе регулируется согласно заданной температуре на входе в блок конверсии СО.
Конверсия СО
Из парогенератора отходящих продуктов установки риформинга технологический газ выходит с температурой около 343°C и поступает в емкость преобразовательного конвектора. В конвертере происходит реакция пара и угарного газа в присутствии катализатора с образованием водорода и углекислого газа.
К моменту выхода из конвертера температура газа увеличивается приблизительно на 70°C; это увеличение температуры варьируется в зависимости от производительности установки. Технологический газ выходит из конвертера при температуре около 410°C; выходная температура варьируется в зависимости от производительности установки.
Выходящий из конвертера технологический газ поступает в технологическую часть подогревателя сырья, где технологический газ охлаждается, одновременно подогревая сырьевой газ. Часть синтез-газа может направляться в обход нагревателя сырья с целью поддержания заданной температуры сырья для установки гидроочистки.
Технологический газ с выхода подогревателя сырья может использоваться для испарения нафты, если таковая подается в качестве сырья в установку. Затем технологический газ пропускается парогенератором тепла продуктов конвертера и теплообменник котловой воды для рекуперации тепла. Излишки генерируемого пара могут отводиться в заводскую сеть Заказчика. Далее технологический газ охлаждается, содержащаяся в потоке влага конденсируется перед подачей в сепаратор холодного конденсата, где конденсат отделяется от потока технологического газа перед вводом технологического газа в систему КЦА.
Система очистки водорода
В системе очистки КЦА применяется процесс адсорбции для получения водорода высокой чистоты. В каждом адсорбере находится слой оксида алюминия, углерод и молекулярное сито. Система работает по повторяющемуся циклу из двух этапов: адсорбция и регенерация.
Во время адсорбции технологический газ проходит через емкость адсорбера, где адсорбенты удаляют из него примеси.
В конце этапа адсорбции адсорбент насыщается примесями, после чего начинается этап регенерации (снижение давления, продувка и восстановление давления). Полученный остаточный газ собирается в емкости остаточного газа и используются в качестве первичного топлива в установке риформинга.
Утилизация отходящего тепла
Весь получаемый пар вырабатывается за счет утилизации тепла. Пар вырабатывается парогенератором дымовых газов, парогенератором отходящих продуктов установки риформинга и парогенератором тепла продуктов конвертера, входящими в состав установки. Для защиты системы получения пара предусмотрена химическая обработка котловой воды.
Тепло дымовых газов используется также для перегрева технологического сырья и воздуха для горения для печи риформинга.
Установки производства водорода методом паровой конверсии метана широко используются в следующих отраслях промышленности
— Пищевая промышленность
— Сталелитейная промышленность
— Стекольная промышленность
— Производство удобрений
— Производство метанола
— Производства электроники
— Производство перекиси водорода
— Процессы нефтеперерабатывающих заводов
— Процессы гидрогенизации/Продукты переработки масел
(PDF) НАЦИОНАЛЬНАЯ АКАДЕМИЯ НАУК УКРАИНЫ ИНСТИТУТ ПРОБЛЕМ МАШИНОСТРОЕНИЯ
4 КИНЕТИКА ВЗАИМОДЕЙСТВИЯ СПЛАВОВ С ВОДНЫМИ
РАСТВОРАМИ ЕДКОГО НАТРА
В качестве основных водородгенерирующих сплавов приняты
(масс. %):
ФСА11 – Fe — 18.15, Si — 61.9, Al — 11.13, Ti — 0.68, Mg — 0.15, Ca — 4.0, P- 0.059,
S — 0.04;
ФСА16 – Fe — 17.5, Si — 60.4, Al — 15.8, Ti — 0.84, Mg — 0.22, Ca — 3.6, P — 0.088,
S — 0.04;
ФСА25 – Fe — 10, Si — 65, Al — 25.
Основные кинетические исследования выполнены в реакторе объемом
1.13 л, обеспечивающем изохорное ведение процесса [8].
Сплавы ФСА11 и ФСА16 произведены на Запорожском производствен-
ном алюминиевом комбинате из неорганической части высокозольных углей.
Синтетический сплав ФСА25 получен в научно-исследовательском
институте металлургии (г. Челябинск) путем сплавления алюминия, кремния
и железа. Сплавы размалывали в шаровой мельнице.
При исследовании реакционной способности порошков использованы
различные фракции. Сплав ФСА11 имеет удельную площадь поверхности
0,0167 м2/г, а в некоторых опытах этот же сплав обладает удельной
площадью поверхности 0,0785 м2/г. В остальных опытах порошки сплавов
имеют размер частиц 0,5-0,8 мм, Sуд ≈ 0,035 м2/г.
Активацию реакции производили введением определенного количества
щелочи, что способствовало активному размыванию оксидного слоя сплава и
соответственно увеличению скорости вытеснения водорода.
По своей активности и полноте реакции сплавы из неорганической
части угля мало отличаются друг от друга. Так, при концентрации щелочи
30 % наблюдается следующая закономерность: при удельной площади
поверхности порошка 0,0167 м2/г полнота реакции составляет 67-86,2 %, а
при удельной площади поверхности 0,0785 м2/г — α достигает 94,8-98,4 %.
Улучшение цикла и водородный перегрев пара на Мутновской геотермальной электростанции
Основные моменты
- •
Мутновская геотермальная электростанция теряет пар из-за потребности в хозяйстве.
- •
На каждый 1% сэкономленного пара путем электролиза ежегодно может производиться 92 т H 2 .
- •
Второй процесс мгновенного испарения с водородным перегревом повышает эффективность с 10% до 12,5%.
- •
Водородный перегрев увеличивает температуру пара на 20–30 К и сухость на 2–4%.
Реферат
Настоящее исследование нацелено на возможность получения водорода и перегрева водяного пара на Мутновской геотермальной электростанции мощностью 50 МВт на 1-й стадии. Модификация путем внедрения установки низкого давления с использованием энергии. разделенной жидкости и анализируется интегрированный цикл однократного и двойного испарения. Второй процесс вспышки дает максимально возможное увеличение установленной мощности на 11,1 МВт для температуры вспышки 92 ° C и на 9 МВт для 120 ° C.В настоящее время электростанция не использует 12,3% геотермального пара для производства электроэнергии, отчасти из-за управления спросом со стороны оператора сети. Избыточная мощность может быть использована для электролиза воды, и на каждый 1% сэкономленного пара ежегодно может производиться 92 тонны H 2 . Сжигание водорода в высокотемпературном водородно-кислородном парогенераторе может использоваться для перегрева пара во втором процессе мгновенного испарения, достигая повышения температуры пара на входе в турбину низкого давления на 20–30K и увеличения осушения пара в турбине. выпуск на 2–4%.Дополнительная доступная мощность увеличивается на 5–10% (0,5–0,9 МВт), а общий тепловой КПД станции может быть увеличен с 10% до 12,5%.
Ключевые слова
Геотермальная энергия
Мутновская ГРЭС
Второй импульсный процесс
Производство водорода
Перегрев водяного пара
Водородно-кислородные парогенераторы
Рекомендуемые статьиЦитирующие статьи (0)
© 2018 Автор. Опубликовано Elsevier Ltd.
Рекомендуемые статьи
Цитирующие статьи
Альфа Лаваль — Производство водорода
Оптимизация процессов производства водорода на НПЗ Высокие рабочие температуры, высокое давление и содержание водорода предъявляют высокие требования к качеству и надежности оборудования, используемого для производства водорода. Альфа Лаваль обладает опытом, проверенными технологиями и широким спектром услуг для удовлетворения этих потребностей.
Повышение надежности производства водорода
Для производства водорода технологический газ смешивается с перегретым паром при повышенных температурах до 1000 ° C (1832 ° F) в присутствии катализатора.
Рекуперированное избыточное технологическое тепло используется для производства перегретого пара высокого давления в системе котла-утилизатора.
К этой системе предъявляются очень высокие требования.Он должен не только максимизировать рекуперацию энергии из технологического газа, чтобы максимизировать производство пара, но и высокие температуры и скорости потока технологического газа также подвергают оборудование высоким нагрузкам и риску отказа.
Установки котлов-утилизаторов Alfa Laval OLMI рассчитаны на максимальные допуски и надежность. Запатентованная конструкция OLMI для перепуска газа сводит к минимуму риск образования металлической пыли. Правильная конструкция и выбор материала также сводят к минимуму риск отказов трубной решетки и коробления трубного пучка.Более того, высококачественная сварка с полным проплавлением без трещин или сварка с внутренним отверстием сводит к минимуму риск образования трещин в сварных швах между трубами и решетками.
Кроме того, все механические конструкции проверяются методом конечных элементов (FEA).
Увеличенная мощностьДля увеличения производства пара вся система котла-утилизатора должна быть оптимизирована с точки зрения конструкции котла-утилизатора, а также расположения и высоты стояков и барабана.
Альфа Лаваль оптимизирует КПД котла, обеспечивая максимальную площадь теплопередачи в однокотловых котлах, а также сводя к минимуму риск неправильного распределения во входной камере газа.
Полный комплект Альфа Лаваль может поставить не только подогреватели питательной воды для котлов, котел-утилизатор, паровой барабан и пароперегреватель. Мы также предоставляем услуги инжиниринга и EPC для всей системы котла-утилизатора. Это включает демонтаж существующей системы, а также проектирование, поставку, монтаж и ввод в эксплуатацию новой системы.
Оборудование Alfa Laval OLMI можно найти на водородных заводах по всему миру.Объем поставки варьируется от охладителей технологического газа или котлов-утилизаторов до комплексных систем.
Более того, теплообменники Альфа Лаваль Compabloc и DuroShell обычно используются для окончательного охлаждения синтез-газа в установках парового риформинга или адсорбции с переменным давлением, чтобы минимизировать общие затраты на установку оборудования, а также уменьшить площадь участка и потребность в охлаждающей воде.
Текущее состояние и будущие разработки
Водород (H 2 ) в настоящее время используется в основном в химической промышленности для производства аммиака и метанола. Тем не менее, в ближайшем будущем ожидается, что водород станет важным топливом, которое будет в значительной степени способствовать повышению качества атмосферного воздуха. Водород как химический элемент (H) является наиболее распространенным на Земле, а молекулярный дигидроген (H 2 ) может быть получен из ряда возобновляемых и невозобновляемых источников с помощью различных процессов. До сих пор в мировом производстве водорода преобладали ископаемые виды топлива, при этом наиболее важными современными технологиями были паровой риформинг углеводородов (например,г., природный газ). Чистый водород также получают путем электролиза воды — энергоемкого процесса. В этой работе рассматриваются современные технологии, используемые для производства водорода (H 2 ) как из ископаемых, так и из возобновляемых источников биомассы, включая риформинг (пар, частичное окисление, автотермический, плазменный и водный) и пиролиз. Кроме того, обсуждаются другие методы получения водорода (например, электролиз воды) и методы очистки, такие как реакции десульфуризации и конверсии водяного газа.
1. Введение
Водород — самый простой и самый распространенный элемент на Земле. Водород легко соединяется с другими химическими элементами и всегда находится в составе другого вещества, такого как вода, углеводород или спирт. Водород также содержится в природной биомассе, в которую входят растения и животные. По этой причине он рассматривается как энергоноситель , а не как источник энергии.
Водород можно производить с использованием различных внутренних ресурсов, включая ядерную энергию, природный газ и уголь, биомассу и другие возобновляемые источники.К последним относятся солнечная, ветровая, гидроэлектрическая или геотермальная энергия. Такое разнообразие внутренних источников энергии делает водород перспективным энергоносителем и важным для энергетической безопасности. Желательно, чтобы водород производился с использованием различных ресурсов и технологических процессов или способов. Производство водорода может быть достигнуто с помощью различных технологических процессов, включая термические (реформинг природного газа, переработка возобновляемых жидкостей и бионефти, биомасса и газификация угля), электролитические (разделение воды с использованием различных энергетических ресурсов) и фотолитические (разделение воды использование солнечного света через биологические и электрохимические материалы).
Годовое производство водорода оценивается примерно в 55 миллионов тонн, при этом его потребление увеличивается примерно на 6% в год. Водород можно производить разными способами из широкого спектра исходного сырья. В настоящее время водород в основном получают путем паровой конверсии природного газа, процесса, который приводит к массовым выбросам парниковых газов [1, 2]. Около 50% мирового спроса на водород в настоящее время генерируется за счет парового риформинга природного газа, около 30% — за счет риформинга нефти / нафты из отходящих газов нефтеперерабатывающих заводов / химической промышленности, 18% — за счет газификации угля, 3.9% от электролиза воды и 0,1% от других источников [3]. Электролитические и плазменные процессы демонстрируют высокую эффективность производства водорода, но, к сожалению, они считаются энергоемкими [4].
Фундаментальный вопрос заключается в разработке технологий производства водорода, альтернативных технологиям, основанным на ископаемом топливе, особенно для его использования в качестве топлива в транспортном секторе. С этой проблемой можно столкнуться при использовании альтернативных возобновляемых ресурсов и связанных с ними методов производства, таких как газификация или пиролиз биомассы, электролитический, фотолитический и термический крекинг воды.Однако невозможно рассматривать только экологическую перспективу, поскольку, например, фотолитический крекинг воды является экологически безопасным, но его эффективность для промышленного использования очень низка. Таким образом, очевидно, что процессы, которые необходимо учитывать, должны учитывать не только экологические проблемы, но и наиболее благоприятные экономические факторы.
2. Водород из ископаемого топлива
Технологии переработки ископаемого топлива преобразуют водородсодержащие материалы, полученные из ископаемых видов топлива, таких как бензин, углеводороды, метанол или этанол, в поток газа, обогащенного водородом.Сегодня переработка метана (природного газа) в качестве топлива является наиболее распространенной коммерческой технологией производства водорода. Большинство ископаемых видов топлива содержат определенное количество серы, удаление которой является важной задачей при планировании водородной экономики. В результате будет обсужден также процесс обессеривания. Кроме того, будет представлена недавно разработанная многообещающая технология плазменного риформинга.
Водородный газ можно производить из углеводородного топлива с помощью трех основных технологий: (i) паровой риформинг (SR), (ii) частичное окисление (POX) и (iii) автотермический риформинг (ATR).Эти технологии производят большое количество оксида углерода (CO). Таким образом, на последующем этапе один или несколько химических реакторов используются для значительного превращения CO в диоксид углерода (CO 2 ) посредством реакций конверсии водяного газа (WGS) и предпочтительного окисления (PrOx) или метанирования, которые описаны ниже .
2.1. Паровой риформинг
Паровой риформинг в настоящее время является одним из наиболее распространенных и в то же время наименее дорогих процессов производства водорода [5]. Его преимущество заключается в высокой эффективности его работы и низких эксплуатационных и производственных затратах.Наиболее часто используемым сырьем являются природный газ и легкие углеводороды, метанол и другие кислородсодержащие углеводороды [6]. Схема реакций риформинга углеводородов и метанола, используемых в качестве сырья, следующая [7]:
Весь процесс состоит из двух этапов. На первом этапе углеводородное сырье смешивается с паром и подается в трубчатый каталитический реактор [8]. Во время этого процесса синтез-газ (газовая смесь H 2 / CO) производится с более низким содержанием CO 2 ((1) и (2)).Необходимая температура реакции достигается добавлением кислорода или воздуха для сжигания части исходного материала (греющего газа) внутри реактора. На втором этапе охлажденный газообразный продукт подается в каталитический нейтрализатор CO, где монооксид углерода в значительной степени преобразуется с помощью пара в диоксид углерода и водород (3). Каталитический процесс парового риформинга требует сырья, свободного от серосодержащих соединений, чтобы избежать дезактивации используемого катализатора.
Процесс SR требует умеренных температур, например, 180 ° C для метанола и кислородсодержащих углеводородов и более 500 ° C для большинства обычных углеводородов [9, 10].Используемые катализаторы можно разделить на два типа: недрагоценные металлы (обычно никель) и драгоценные металлы из элементов VIII группы (обычно платина или родий). Из-за серьезных ограничений по массе и теплопередаче обычные установки парового риформинга ограничены коэффициентом эффективности гранулированных катализаторов, который обычно составляет менее 5% [11]. Поэтому кинетика редко является ограничивающим фактором для обычных реакторов парового риформинга [12], и поэтому в промышленности используются менее дорогие никелевые катализаторы.
Важным фактором, характеризующим процесс SR, является соотношение атомов H: C в исходном материале. Чем выше это соотношение, тем меньше выделяется углекислый газ. Мембранный реактор может заменить оба реактора в обычном процессе SR для достижения общей реакции (2) [13]. Тепловая эффективность производства водорода с помощью SR процесса метана в промышленных масштабах составляет около 70–85% [14]. Ряд других видов сырья также возможно для достижения этой эффективности в ближайшем будущем, например, твердые коммунальные отходы, отходы пищевой промышленности, масла, целенаправленно выращиваемая или отработанная сельскохозяйственная биомасса, а также топливо ископаемого происхождения, такое как уголь.Недостатком является высокое производство CO 2 , ок. 7,05 кг CO 2 / кг H 2 .
2.2. Частичное окисление
Частичное окисление (POX) и каталитическое частичное окисление (CPOX) углеводородов было предложено для производства водорода для автомобильных топливных элементов и некоторых других коммерческих приложений [15, 16]. Газифицированное сырье может представлять собой метан и биогаз, но в первую очередь тяжелые нефтяные фракции (например, вакуумные остатки, топочный мазут), дальнейшая обработка и утилизация которых затруднены [17]. POX — это некаталитический процесс, при котором сырье газифицируется в присутствии кислорода ((5) и (6)) и, возможно, пара ((7), ATR) при температурах в диапазоне 1300-1500 ° C и давлениях в диапазон 3–8 МПа. По сравнению с паровым риформингом (H 2 : CO = 3: 1) образуется больше CO (H 2 : CO = 1: 1 или 2: 1). Таким образом, процесс дополняется преобразованием CO с паром в H 2 и CO 2 . Эта реакция способствует поддержанию равновесия между отдельными продуктами реакции [18]:
Газовая смесь, образованная в результате частичного окисления, содержит CO, CO 2 , H 2 O, H 2 , CH 4 , сероводород (H 2 S) и оксисульфид углерода (COS).Часть газа сжигается, чтобы обеспечить достаточно тепла для эндотермических процессов. Сажа, образующаяся при разложении ацетилена в качестве промежуточного продукта, является нежелательным продуктом. Его количество зависит от доли H: C в исходном топливном сырье. Поэтому, как и в случае с SR, была предпринята попытка перейти на сырье с более высоким соотношением H: C, например, на природный газ. Хотя эксплуатация реактора дешевле по сравнению с паровым риформингом, последующая конверсия делает эту технологию более дорогой.Поскольку процесс не требует использования катализатора, нет необходимости удалять сернистые элементы из природного газа, что снижает эффективность катализатора. Сернистые соединения, содержащиеся в газифицированном сырье, превращаются в сероводород (около 95%) и оксисульфид углерода (около 5%) [19].
Катализаторы могут быть добавлены в систему частичного окисления (CPOX) для снижения рабочей температуры, прибл. 700–1000 ° С. Однако контроль температуры оказывается трудным из-за образования кокса и горячих точек из-за экзотермического характера реакций [10, 15, 16, 20].Для конверсии природного газа катализаторы обычно основаны на Ni или Rh. Однако никель сильно склонен к коксованию, и стоимость Rh значительно возросла. Krummenacher et al. [16] удалось использовать каталитическое парциальное окисление декана, гексадекана и дизельного топлива. Высокие рабочие температуры (> 800 ° C) [16] и соображения безопасности могут затруднить их использование в практичных и компактных портативных устройствах из-за терморегулирования [21]. Обычно тепловой КПД реакторов POX с метаном в качестве топлива находится в диапазоне 60–75% [22].
2.3. Автотермический риформинг
Как упоминалось ранее, в автотермическом риформинге (ATR) пар добавляется в процессе каталитического частичного окисления. ATR представляет собой комбинацию реакций парового риформинга (эндотермических) и частичного окисления (экзотермических) [23]. Преимущество ATR состоит в том, что он не требует внешнего тепла, а также проще и дешевле, чем SR метана.
Диапазон работы топливного процессора для производства водорода показан на рисунке 1. Выбор условий работы установки риформинга зависит от конкретной цели.Основная цель — высокий выход водорода при низком содержании окиси углерода. Для парового риформинга возможны максимальная водородная эффективность и низкое содержание окиси углерода. Однако паровой риформинг — это эндотермический процесс и, следовательно, энергоемкий. Эта энергия должна передаваться в систему извне.
Еще одно существенное преимущество ATR перед процессом SR состоит в том, что его можно остановить и запустить очень быстро, производя при этом большее количество водорода, чем только POX [23].Есть некоторые ожидания, что этот процесс станет привлекательным для отрасли «газ-жидкость» из-за благоприятного состава газа для синтеза Фишера-Тропша, относительной компактности ATR, более низких капитальных затрат и возможности экономии за счет масштаба [24]. Для риформинга метана термический КПД сопоставим с КПД POX (примерно 60–75%) и немного меньше, чем у парового риформинга. Бензин и другие высшие углеводороды могут быть преобразованы в водород на борту для использования в автомобилях с помощью автотермического процесса с использованием подходящих катализаторов [25].
2.4. Сдвиг вода-газ, предпочтительное окисление и метанирование
В процессе риформинга образуется смесь продуктового газа со значительными концентрациями окиси углерода, часто 5 об.% Или более (около 10 об.%) [10]. Чтобы увеличить количество водорода, газообразный продукт пропускают через реактор конверсии водяного газа (WGS), чтобы снизить содержание монооксида углерода и в то же время увеличить содержание водорода (3). Обычно желательна высокая температура, чтобы способствовать быстрой кинетике.Однако это приводит к высокой равновесной селективности по монооксиду углерода и снижению выхода водородного продукта. Таким образом, снижение содержания CO в синтез-газе достигается в двухстадийном процессе, который включает высоко- и низкотемпературную реакцию конверсии водяного газа, известную как процессы «HTS» и «LTS», соответственно (рис. 2). . На первом этапе, проводимом в интервале 310–450 ° C с использованием катализатора Fe 3 O 4 / Cr 2 O 3 , концентрация СО снижается с 10 до 3 об. %.На втором этапе, проводимом в диапазоне 180–250 ° C, содержание CO дополнительно снижается до низкого уровня 500 ppm с использованием катализаторов Cu / ZnO / Al 2 O 3 [26].
Для дальнейшего снижения содержания монооксида углерода в газообразном продукте используется реактор предпочтительного окисления (PrOx) или реактор селективного метанирования моноксида углерода [10, 27]. Иногда вместо предпочтительного окисления используется термин «селективное окисление». Селективное окисление относится к восстановлению моноксида углерода в топливном элементе, обычно топливном элементе с протонообменной мембраной (PEM), тогда как предпочтительное окисление происходит в реакторе вне топливного элемента [27].Реакторы PrOx и метанирования имеют свои преимущества и проблемы. Реактор первичного окисления увеличивает сложность системы, поскольку в систему необходимо добавлять точные концентрации воздуха [10, 27]. Однако эти реакторы компактны, и если вводится избыточное количество воздуха, некоторое количество водорода сгорает.
Реакторы метанирования проще в том, что не требуется воздуха. Однако на каждый прореагировавший CO расходуется три молекулы H 2 . Кроме того, CO 2 реагирует с водородом, и необходимо поддерживать тщательный контроль условий в реакторе, чтобы свести к минимуму ненужное потребление водорода.В настоящее время преимущественное окисление является основным разрабатываемым методом [27]. Катализаторы обычно представляют собой благородные металлы, такие как платина, рутений или родий, нанесенные на Al 2 O 3 [10, 27]. В то же время H 2 очищается с помощью альтернативных подходов, а именно адсорбции с переменным давлением, криогенной дистилляции и мембранных технологий, которые могут обеспечить необходимую чистоту водорода (около 98-99%). Наиболее выгодным методом очистки газов является адсорбция при переменном давлении из-за его высокой эффективности (> 99.99%) и гибкость.
2,5. Десульфуризация
Как обсуждалось ранее, в настоящее время производство водорода происходит в основном за счет переработки природного газа, хотя благодаря значительным достижениям в топливных элементах повышенное внимание уделяется другим видам топлива, таким как метанол, пропан, бензин, и топливам для логистики, таким как как Jet-A, дизель и JP8 [28]. За исключением метанола, все эти виды топлива содержат некоторое количество серы, причем конкретные серосодержащие соединения зависят от типа топлива и источника.По этой причине обессеривание считается очень важным этапом в технологиях переработки топлива.
Процессы обессеривания можно классифицировать в зависимости от характера основного физико-химического процесса, используемого для удаления серы (рис. 3). Наиболее развитыми и коммерчески доступными являются технологии каталитического превращения сероорганических соединений с удалением серы. Такие технологии каталитической конверсии включают обычную гидродесульфуризацию (HDS), гидроочистку с использованием усовершенствованных катализаторов и / или конструкции реакторов, а также комбинацию гидроочистки с некоторыми дополнительными химическими процессами для поддержания технических характеристик топлива [29, 30].Основной особенностью технологий второго типа является применение физико-химических процессов, отличных по природе от каталитического HDS, для отделения и / или преобразования сероорганических соединений из потоков нефтепереработки. Такие технологии включают, в качестве ключевого шага, дистилляцию, алкилирование, окисление, экстракцию, адсорбцию или их комбинацию [31].
2.6. Плазменный риформинг
В случае плазменного риформинга сеть реакций риформинга такая же, как и при обычном риформинге.Однако энергия и свободные радикалы, используемые для реакции риформинга, предоставляются плазмой, обычно генерируемой с помощью электричества или тепла [32–35]. Когда вода или пар впрыскиваются с топливом, в дополнение к электронам образуются радикалы H • , OH • и O • , создавая условия для протекания как восстановительных, так и окислительных реакций. . Технологии плазменного риформинга были разработаны для облегчения POX, ATR и парового риформинга, при этом большинство реакторов являются POX и ATR [35].По сути, существует две основные категории плазменного риформинга: термический и нетепловой [35].
Плазменные устройства, называемые плазмотронами, могут генерировать очень высокие температуры (примерно> 2000 ° C) с высокой степенью контроля с помощью электричества [32–35]. Вырабатываемое тепло не зависит от химического состава реакции, и оптимальные рабочие условия могут поддерживаться в широком диапазоне скоростей подачи и состава газа. Компактность установки плазменного риформинга обеспечивается высокой плотностью энергии, связанной с самой плазмой, и уменьшенным временем реакции, что приводит к короткому времени пребывания.Газовые потоки, обогащенные водородом, могут быть эффективно получены в установках плазменного риформинга из различных углеводородных топлив (например, бензина, дизельного топлива, нефти, биомассы, природного газа и реактивного топлива) с эффективностью преобразования, близкой к 100% [32, 36]. Технология плазменного риформинга имеет потенциальные преимущества перед традиционными технологиями производства водорода [32–35]. Условия плазмы (например, высокие температуры, высокая степень диссоциации и значительная степень ионизации) могут использоваться для ускорения термодинамически благоприятных химических реакций без катализатора или обеспечения энергии, необходимой для протекания процессов эндотермического риформинга.
Установки плазменного риформинга могут обеспечить ряд преимуществ, а именно компактность и малый вес (благодаря высокой удельной мощности), высокую эффективность преобразования, минимальную стоимость (простые металлические или угольные электроды и простые источники питания), быстрое время отклика (доли секунды), работа с широким спектром видов топлива, включая тяжелые углеводороды (сырье) и «грязные» углеводороды (дизельное топливо с высоким содержанием серы). Эта технология может быть использована для производства водорода для различных стационарных применений, таких как распределенное и экологически чистое производство электроэнергии для топливных элементов [32].Его также можно использовать для мобильных приложений (например, для производства водорода на борту транспортных средств с топливными элементами) и для заправки топливом (например, стационарных источников водорода для транспортных средств).
Единственными недостатками плазменного риформинга являются зависимость от электричества и сложность работы при высоком давлении (требуется для процессов высокого давления, таких как производство аммиака). Высокое давление, хотя и достижимо, увеличивает эрозию электрода из-за снижения подвижности дуги и, следовательно, сокращает срок службы электрода [33].
3. Водород из возобновляемых источников
Водород может также производиться другими методами, кроме риформинга ископаемого топлива. Краткое описание подходов на основе биомассы (например, газификации, пиролиза и реформинга водной фазы) наряду с получением водорода из воды (например, электролиз, фотоэлектролиз и термохимическое расщепление воды) описано ниже.
3.1. Газификация биомассы
Ожидается, что в ближайшем будущем биомасса станет наиболее вероятным возобновляемым органическим заменителем нефти.Биомасса доступна из широкого спектра источников, таких как отходы животноводства, твердые бытовые отходы, растительные остатки, древесные культуры с коротким севооборотом, сельскохозяйственные отходы, опилки, водные растения, виды травянистых растений с коротким оборотом (например, гренки), макулатура, кукуруза. и многие другие [37, 38].
Технология газификации, обычно используемая с биомассой и углем в качестве топливного сырья, очень зрелая и коммерчески используется во многих процессах. Это разновидность пиролиза, и поэтому он основан на частичном окислении исходного материала до смеси водорода, метана, высших углеводородов, монооксида углерода, диоксида углерода и азота, известной как «генераторный газ» [37].Процесс газификации обычно страдает низкой тепловой эффективностью, поскольку влага, содержащаяся в биомассе, также должна испаряться. Его можно проводить с катализатором или без него, а также в реакторе с неподвижным или псевдоожиженным слоем, причем последний реактор обычно имеет лучшую производительность [38]. Добавление пара и / или кислорода в процессе газификации приводит к получению «синтез-газа» с соотношением H 2 / CO 2/1, последний используется в качестве сырья для реактора Фишера-Тропша для получения высших углеводородов (синтетических бензин и дизельное топливо) или в реактор WGS для производства водорода [38]. Перегретый пар (около 900 ° C) использовался для преобразования сухой биомассы для достижения высоких выходов водорода. Однако процесс газификации дает значительные количества «смол» (сложная смесь высших ароматических углеводородов) в газообразном продукте даже при работе в диапазоне 800–1000 ° C. Вторичный реактор, в котором используется кальцинированный доломит и / или никелевый катализатор, используется для каталитической очистки и повышения качества получаемого газа [38]. В идеале на этих газификационных установках следует использовать кислород; однако установка отделения кислорода является непомерно высокой для малых предприятий.Это ограничивает газификаторы использованием воздуха, что приводит к значительному разбавлению продукта, а также к образованию NO x . Для этой технологии необходимы недорогие и эффективные кислородные сепараторы. Для производства водорода можно использовать процесс WGS для увеличения концентрации водорода с последующим процессом разделения для получения чистого водорода [39].
Обычно реакторы газификации строятся в больших масштабах и требуют непрерывной подачи огромного количества материала. Они могут достичь КПД порядка 35–50% в зависимости от более низкой теплотворной способности [4].Одна из проблем этой технологии заключается в том, что необходимо использовать огромное количество ресурсов для сбора большого количества биомассы на центральную перерабатывающую установку. В настоящее время высокие логистические затраты на установку газификации и удаление «смол» до приемлемого уровня для производства чистого водорода ограничивают коммерциализацию производства водорода на основе биомассы. В будущем для этой технологии может потребоваться разработка небольших эффективных установок распределенной газификации для рентабельного производства водорода.
3.2. Пиролиз и копиролиз
Другим перспективным в настоящее время способом получения водорода является пиролиз или копиролиз. Сырье органическое сырье нагревается и газифицируется при давлении 0,1–0,5 МПа в диапазоне 500–900 ° C [40–43]. Процесс протекает при отсутствии кислорода и воздуха, поэтому образование диоксинов практически исключено. Поскольку вода или воздух отсутствуют, оксиды углерода (например, CO или CO 2 ) не образуются, что устраняет необходимость во вторичных реакторах (WGS, PrOx и т. Д.).). Следовательно, этот процесс обеспечивает значительное сокращение выбросов. Однако, если присутствует воздух или вода (материалы не были высушены), будут произведены значительные выбросы CO x . Среди преимуществ этого процесса — топливная гибкость, относительная простота и компактность, чистый побочный продукт углерода и сокращение выбросов CO x [40–43]. Реакцию в общем можно описать следующим уравнением: [41]
По температурному диапазону процессы пиролиза делятся на низкие (до 500 ° C), средние (500–800 ° C) и высокие (более 800 ° C).Быстрый пиролиз — один из новейших процессов преобразования органических материалов в продукты с более высоким содержанием энергии. Продукты быстрого пиролиза появляются во всех образующихся фазах (твердой, жидкой и газообразной). Одной из проблем с этим подходом является возможность загрязнения образующимся углеродом, но его сторонники утверждают, что это можно свести к минимуму с помощью соответствующей конструкции. Поскольку он имеет потенциал для более низких выбросов CO и CO 2 и может работать таким образом, чтобы извлекать значительное количество твердого углерода, который легко улавливается [41, 44], пиролиз может играть важную роль. в будущем.
Применение копролиза смеси угля с органическими отходами недавно вызвало интерес в промышленно развитых странах, так как оно должно ограничить и облегчить бремя отходов при удалении отходов (отходы и чистые пластмассы, резина, целлюлоза, бумага, текстиль, дерево) [45, 46]. Пиролиз и копиролиз — это хорошо разработанные процессы, которые можно использовать в промышленных масштабах.
3.3. Риформинг в водной фазе
Риформинг в водной фазе (APR) — это разрабатываемая технология переработки кислородсодержащих углеводородов или углеводов из возобновляемых ресурсов биомассы для производства водорода [47, 48], как показано на Рисунке 4. Реакции APR протекают при значительно более низких температурах (220–270 ° C), чем при обычном паровом риформинге алкана (около 600 ° C). Низкие температуры, при которых протекают реакции реформинга в водной фазе, сводят к минимуму нежелательные реакции разложения, обычно встречающиеся при нагревании углеводов до повышенных температур [49, 50]. Кроме того, реакция конверсии водяного газа (WGS) является благоприятной при тех же температурах, что и реакции APR, что позволяет генерировать H 2 и CO 2 в одном реакторе с низкими количествами CO.Напротив, типичные процессы парового риформинга требуют многоступенчатых или множественных реакторов для достижения низких уровней CO в получаемом газе. Другое преимущество процесса APR состоит в том, что он устраняет необходимость испарения воды, что представляет собой значительную экономию энергии по сравнению с обычными процессами парофазного риформинга с водяным паром. Большая часть исследований до настоящего времени была сосредоточена на катализаторах группы VIII на носителе, в которых Pt-содержащие твердые вещества имеют наивысшую каталитическую активность.
Катализаторы на никелевой основе, несмотря на их более низкую активность, оценивались из-за низкой стоимости никеля [47].Сторонники этой технологии заявляют, что эта технология более удобна для эффективного и избирательного преобразования сырья биомассы в водород. Для глюкозы и гликолей сообщалось о концентрациях 10-60 мас.% В воде [51]. Выбор катализатора важен, чтобы избежать метанирования, которое является термодинамически выгодным, наряду с продуктами Фишера-Тропша, такими как пропан, бутан и гексан [48, 52]. Недавно Rozmiarek [53] сообщил о способе на основе установки риформинга в водной фазе, который достиг эффективности более 55% с сырьем, состоящим из 60 мас.% Глюкозы в воде.Однако катализатор оказался нестабильным при длительных испытаниях (200 дней работы) [53]. Наконец, из-за умеренного выхода за пределы пространства-времени эти реакторы имеют тенденцию быть довольно большими. Повышение активности и долговечности катализатора — это область, в которой можно добиться значительного прогресса.
3.4. Электролиз
Перспективным методом производства водорода в будущем может стать электролиз воды. В настоящее время этим процессом производится около 4% водорода во всем мире [2].Электролиз воды или ее разложение на водород и кислород — хорошо известный метод, который начали коммерчески использовать уже в 1890 году.
Электролиз — это процесс, при котором постоянный ток, проходящий через два электрода в водном растворе, приводит к разрушению химических связей, присутствующих в молекуле воды, на водород и кислород:
Процесс электролиза происходит при комнатной температуре. Обычно при электролизе воды используется серная кислота, а электроды — из платины (Pt), которая не вступает в реакцию с серной кислотой.Этот процесс экологически чистый, поскольку не образуются парниковые газы, а производимый кислород находит дальнейшее промышленное применение. Однако по сравнению с описанными выше методами электролиз — это технология, требующая больших затрат энергии.
Энергетический КПД электролиза воды (химическая энергия, получаемая на одну поданную электрическую энергию) на практике достигает 50–70% [54]. По сути, это преобразование электрической энергии в химическую энергию в виде водорода с кислородом в качестве полезного побочного продукта.Наиболее распространенной технологией электролиза является щелочная технология, но были разработаны протонообменная мембрана (PEM) и твердооксидные электролизные ячейки (SOEC) [55, 56]. Электролизеры SOEC являются наиболее электрически эффективными, но наименее развитыми. Технология SOEC имеет проблемы с коррозией, уплотнением, термоциклированием и миграцией хрома. Электролизеры PEM более эффективны, чем щелочные, и не имеют проблем с коррозией и уплотнением, как SOEC; однако они стоят дороже, чем щелочные системы. Щелочные системы являются наиболее развитыми и имеют самые низкие капитальные затраты.У них самый низкий КПД, поэтому у них самая высокая стоимость электроэнергии.
3.5. Фотоэлектролиз
Фотоэлектролиз — один из возобновляемых способов производства водорода, демонстрирующий многообещающую эффективность и стоимость, хотя он все еще находится в стадии экспериментальной разработки [57]. В настоящее время это наименее затратный и наиболее эффективный способ получения водорода из возобновляемых источников. Фотоэлектрод — это полупроводниковый прибор, поглощающий солнечную энергию и одновременно создающий необходимое напряжение для прямого разложения молекулы воды на кислород и водород.В фотоэлектролизе используется фотоэлектрохимическая (PEC) система сбора света для проведения электролиза воды. Если полупроводниковый фотоэлектрод погружен в водный электролит, подвергающийся воздействию солнечного излучения, он будет генерировать достаточно электроэнергии, чтобы поддерживать возникающие реакции водорода и кислорода. При генерации водорода электроны выделяются в электролит, тогда как для генерации кислорода требуются свободные электроны. Реакция зависит от типа полупроводникового материала и от интенсивности солнечного излучения, которая обеспечивает плотность тока 10–30 мА / см 2 .При этих плотностях тока напряжение, необходимое для электролиза, составляет примерно 1,35 В.
Фотоэлектрод состоит из фотоэлектрических (полупроводниковых), каталитических и защитных слоев, которые можно моделировать как независимые компоненты [58]. Каждый слой влияет на общую эффективность фотоэлектрохимической системы. Фотогальванический слой изготовлен из светопоглощающих полупроводниковых материалов. Поглощение света полупроводниковым материалом прямо пропорционально характеристикам фотоэлектрода.Полупроводники с широкими полосами обеспечивают необходимый потенциал для расщепления воды [54].
Каталитические слои фотоэлектрохимического элемента также влияют на характеристики электролиза и требуют подходящих катализаторов для расщепления воды. Слой оболочки — еще один важный компонент фотоэлектрода, который предотвращает коррозию полупроводника внутри водного электролита. Этот слой должен быть высокопрозрачным, чтобы обеспечивать максимальную солнечную энергию, чтобы он мог достигать фотоэлектрического полупроводникового слоя.
3.6. Термохимическое расщепление воды
Термохимические циклы разрабатывались еще с 1970-х и 1980-х годов, когда они должны были внести свой вклад в поиск новых источников производства альтернативных видов топлива во время нефтяного кризиса. При термохимическом расщеплении воды, также называемом термолизом, только тепло используется для разложения воды на водород и кислород [59]. Считается, что с помощью этих процессов можно достичь общей эффективности, близкой к 50% [60].
Одноступенчатая термическая диссоциация воды описывается следующим образом:
Один из недостатков этого процесса связан с необходимостью эффективной техники разделения H 2 и O 2 , чтобы избежать образования взрывоопасной смеси.Для этого могут быть использованы полупроницаемые мембраны на основе ZrO 2 и других жаропрочных материалов. Разделение также может быть достигнуто после охлаждения газовой смеси продукта до более низких температур. Затем палладиевые мембраны можно использовать для эффективного отделения водорода.
Хорошо известно, что вода будет разлагаться при 2500 ° C, но материалы, стабильные при этой температуре, а также устойчивые источники тепла нелегко найти. Поэтому были предложены химические реагенты для понижения температуры, тогда как в литературе упоминается более 300 циклов расщепления воды [61]. Все процессы значительно снизили рабочую температуру до уровня ниже 2500 ° C, но обычно требуют более высокого давления. Однако считается, что масштабирование процессов может привести к повышению термического КПД, преодолевая одну из основных проблем, с которыми сталкивается эта технология. Кроме того, лучшее понимание взаимосвязи между капитальными затратами, термодинамическими потерями и термической эффективностью процесса может привести к снижению затрат на производство водорода [60].
4. Экономические аспекты производства водорода
В настоящее время наиболее широко используемым и дешевым методом производства водорода является паровой риформинг метана (природного газа) .Этот метод включает около половины мирового производства водорода, а цена на водород составляет около 7 долларов за ГДж. Сравнимую цену на водород обеспечивает частичное окисление углеводородов. Однако парниковые газы, образующиеся в результате термохимических процессов, необходимо улавливать и хранить, и, таким образом, следует учитывать увеличение цены на водород на 25–30% [62].
Используемые далее термохимические процессы включают газификацию и пиролиз биомассы. Цена на водород, полученный таким образом, примерно в три раза выше, чем цена на водород, полученный методом SR.Следовательно, эти процессы обычно не считаются экономически конкурентоспособными по сравнению с паровым риформингом. Цена на водород от газификации биомассы колеблется в пределах 10–14 долларов США / ГДж, а на пиролиз — 8,9–15,5 долларов США / ГДж. Это зависит от оборудования, наличия и стоимости сырья [1].
Электролиз воды — одна из самых простых технологий получения водорода без побочных продуктов. Электролитические процессы можно отнести к категории высокоэффективных. С другой стороны, стоимость входящего электричества относительно высока и играет ключевую роль в цене получаемого водорода.
К 2030 году преобладающими методами производства водорода будут паровой риформинг природного газа и катализируемая газификация биомассы . В относительно небольшой степени будут использоваться как газификация угля, так и электролиз. Использование солнечной энергии в данном контексте сомнительно, но также возможно. Вероятно, к 2050 году роль солнечной энергии возрастет [1].
5. Выводы
В настоящее время проводится огромное количество исследований по развитию технологий производства водорода (H 2 ).В настоящее время наиболее развитой и используемой технологией является риформинг углеводородов. Чтобы уменьшить зависимость от ископаемого топлива, рассматриваются важные разработки в других технологиях производства H 2 из возобновляемых ресурсов, таких как биомасса и вода. В таблице 1 представлены технологии, а также их использованное сырье и полученная эффективность. Важно отметить, что H 2 можно производить из широкого разнообразия сырья, доступного почти повсюду. В стадии разработки находится множество процессов с минимальным воздействием на окружающую среду.Развитие этих технологий может снизить зависимость мира от топлива, поступающего в основном из нестабильных регионов. «Собственное» производство H 2 может повысить как энергетическую, так и экономическую безопасность страны. Возможность производства H 2 из широкого разнообразия сырья и с использованием самых разнообразных процессов может позволить каждому региону мира производить большую часть своей собственной энергии. Очевидно, что по мере развития и развития технологий H 2 может оказаться наиболее распространенным доступным топливом.
Коммерческие углеводороды окисление
| ||||||||||||||||||||||||||||||||||||||||||||||||||
Очистка водорода не включена. |
Номенклатура
S Каталитическое парциальное окислениеS SO2APR: | Водно-фазовый риформинг |
ATR: | Автотермический риформинг |
CPOX: | |
CPOX: | |
PEC: | Фотоэлектрохимический |
PEM: | Протонообменная мембрана |
POX: | Частичное окисление |
PrOx: | Твердый электролизер |
SR: | Паровой риформинг |
WGS: | Переход водогазовый.![]() |
Благодарности
Авторы выражают признательность Исследовательскому комитету Кипрского университета и Кипрскому фонду содействия исследованиям за их финансовую поддержку в развитии фундаментальных исследований технологий каталитического производства водорода.
Лучший способ получить водород из воды
Экспериментальный подход к расщеплению воды может привести к относительно дешевому и чистому методу крупномасштабного производства водорода, не требующему ископаемого топлива.В процессе вода расщепляется на водород и кислород с использованием тепла и катализаторов из недорогих материалов.
Mark E. Davis Разделение воды с использованием тепла — это альтернатива электролизу, который является дорогостоящим и требует большого количества электроэнергии. Новый подход, разработанный профессором химического машиностроения Калифорнийского технологического института Марком Дэвисом, позволяет избежать основных проблем, связанных с предыдущими методами расщепления воды с использованием тепла. Он работает при относительно низких температурах и не производит никаких токсичных или коррозионных промежуточных продуктов.
Почти весь водород, используемый в настоящее время в промышленных процессах, таких как производство бензина, поступает из риформинга природного газа. Если автопроизводители начнут продавать большое количество автомобилей на водородных топливных элементах, как они заявили, что планируют это сделать в конечном итоге, водород для них, скорее всего, также будет поступать из природного газа, если процессы, подобные тому, что производятся в Калифорнийском технологическом институте, не будут коммерциализированы.
Основной подход к высокотемпературному разделению воды заключается в нагреве окисленного металла для удаления кислорода с последующим добавлением воды.В случае Дэвиса исходным материалом является оксид марганца, и реакции облегчаются за счет перемещения ионов натрия внутрь и наружу. «Без натрия температура поднялась бы намного выше 1000 ° C», — говорит Дэвис. С ним реакции протекают при температуре 850 ° C и ниже.
Технология, наверное, далека от коммерциализации. Он по-прежнему требует довольно высоких температур — например, на пару сотен градусов выше, чем те, которые используются для привода паровых турбин на угольных и атомных электростанциях.Для получения таких температур без использования ископаемого топлива, вероятно, потребуется одна из двух технологий, ни одна из которых в настоящее время не используется в коммерческих целях: высокотемпературные ядерные реакторы или солнечные тепловые установки высокой концентрации, которые используют кольца зеркал для более интенсивной концентрации солнечного света, чем это происходит сегодня в России. солнечные тепловые электростанции.
Подход Caltech также необходимо протестировать, чтобы убедиться, что цикл разделения воды может выполняться многократно. На данный момент исследователи показали, что одни и те же материалы можно использовать повторно пять раз, но «если вы хотите, чтобы одна из этих вещей работала по-настоящему, вам пришлось бы запускать ее в течение тысяч циклов», — говорит Дэвис. Он говорит, что такое тестирование выходит за рамки его лаборатории. «Мы хорошо понимаем, что в этом цикле может быть много циклов, но пока вы этого не сделаете, вы не знаете, — говорит он. «Все, что мы здесь сделали, это доказали, что химия может работать».
Скорость производства водорода также должна быть увеличена — например, путем перехода на материалы с большей площадью поверхности. И Дэвис надеется еще больше снизить необходимую температуру. Цель состоит в том, чтобы использовать этот или аналогичный процесс для использования отходящего тепла на сталелитейных заводах и электростанциях.«Это хорошее начало, но чем ниже мы спускаемся, тем лучше», — говорит он.
Образование сероводорода в процессе термического повышения нефтеотдачи в условиях перегретого пара
Во время процесса термического повышения нефтеотдачи (МУН) опасный сероводород (H 2 S) в добываемых газах вызывает значительные трудности при разведке и разработке нефти. В этом исследовании влияние степени перегрева на образование H 2 S в результате акватермолиза тяжелой нефти было изучено посредством моделирования экспериментов.Неочищенная и остаточная нефть до и после реакции была разделена на насыщенные, ароматические, смоляные и асфальтеновые фракции (SARA). Образцы масла были проанализированы с различных точек зрения с помощью различных методов определения характеристик, включая инфракрасную спектроскопию с преобразованием Фурье (FTIR), элементный анализ и рентгеновскую фотоэлектронную спектроскопию (XPS). Результаты показали, что поколению H 2 S благоприятствовала большая степень перегрева при той же температуре, и она увеличилась с 0.178 до 0,345 мл г −1 масла с увеличением степени перегрева с 62,19 до 89,42 ° С. Содержание серосодержащих веществ, которые должны были быть основными источниками образования H 2 S, в насыщенной и ароматической фракциях существенно уменьшалось с увеличением степени перегрева; увеличение степени перегрева привело к небольшому снижению содержания метиленовой, метильной и карбоксильной / карбонильной групп.
Более того, анализ основных существующих форм серы до и после реакции предполагает, что сера в формах сульфидов, сульфонов и сульфатов с большей вероятностью будет генерировать H 2 S в условиях перегретого пара.Это исследование дает понимание механизма образования H 2 S в процессе закачки перегретого пара для извлечения тяжелой нефти.
Эта статья в открытом доступе
Подождите, пока мы загрузим ваш контент… Что-то пошло не так.
Водород дешевеет — pv magazine International
Долгое время это казалось утопическим видением — сможет ли Шмидт достичь того, что многие до него пытались и не смогли сделать? Сможет ли он создать систему, производящую водород для собственного потребления, для использования в качестве сезонного накопителя и, таким образом, достичь полной самоокупаемости энергии? Целевые затраты являются многообещающими при условии наличия дешевой экологически чистой электроэнергии для питания электролизеров.
Шмидт — не единственный, кто совершил эту революцию. В стартовых блоках находятся несколько малых и крупных компаний. Центральное и распределенное распределение — это проблема не только в производстве электроэнергии. Также ведутся оживленные дискуссии о том, какой подход более перспективен для производства зеленого водорода.
Потенциал экономии
В принципе, производство водорода простое. Электролиз применяется примерно с 1800 года. Метод, известный как щелочной электролиз, используется в коммерческих целях с середины 20 века.В нем используется ячейка с катодом, анодом и электролитом на основе раствора едких солей. При подаче напряжения вода разлагается в щелочном растворе. На катоде образуется водород, а на аноде — кислород. Между двумя электродами находится мембрана, которая пропускает только отрицательно заряженные ионы кислорода и водорода (ОН-), разделяя, таким образом, газы. Во время реакции выделяется тепло, которое, если использовать его, увеличивает ее эффективность. Затем полученный водород необходимо очистить, высушить и, при необходимости, сжать.
Электролит является жидким, это означает, что для щелочного электролизера требуется дополнительное периферийное оборудование, такое как насосы для электролита, промывка и подготовка раствора. Хотя в настоящее время это самый дешевый из всех процессов электролиза, он требует относительно высоких затрат на обслуживание.
Гораздо более современный метод электролиза, в котором используется протонообменная мембрана (PEM), отличается. Он полностью изменяет принцип топливного элемента и не требует жидкого электролита. Вода продавливается через пакет из двух электродов и полимерную мембрану.Он позволяет проходить только положительно заряженным протонам водорода. Платина обычно используется в качестве катализатора в ячейке. Тонкие ячейки, состоящие из мембраны и пары электродов, могут быть собраны в стопки для достижения лучшей производительности. По сравнению со щелочным электролизом, электролиз PEM имеет то преимущество, что он быстро реагирует на колебания, типичные для производства возобновляемой энергии. Эта технология часто используется для распределенных систем, потому что оборудование не требует обслуживания и подает высококачественный газ.
Более новый вариант — электролиз с анионообменной мембраной (АЭМ), применяемый Enapter. Как и щелочной электролиз, этот метод позволяет отрицательно заряженным ионам (ОН-) проходить через мембрану. AEM позволяет избежать использования дорогостоящих драгоценных металлов, необходимых в качестве катализаторов при электролизе PEM. Этот процесс также эффективен в меньших масштабах, что делает его подходящим для децентрализованных приложений.
Высокотемпературный электролиз использует несколько иную концепцию. Керамические мембраны, которые проводят ионы при очень высоких температурах, разделяют перегретый пар при температуре от 600 до 800 градусов Цельсия на кислород и водород.Поскольку большая часть энергии, необходимой для этого процесса, уже вырабатывается за счет тепла, потребность в электроэнергии ниже. Когда используется промышленное отходящее тепло, которое стоит мало или ничего не стоит, этот метод может быть очень эффективным. Эффективность, измеренная с точки зрения потребляемой электроэнергии, выше, чем у других методов.
Ценовая стратегия
Однако в конечном итоге эффективность важна лишь косвенно; самое главное — это стоимость. Общая стоимость включает стоимость электролизера, включая обслуживание и замену изношенных мембран, стоимость электроэнергии, используемой для процесса, и любые последующие расходы на сушку, очистку и сжатие газа, а также транспортировку.
Исследование, проведенное Fraunhofer ISE и IPA за 2018 год, оценило инвестиционные затраты на электролизер PEM, который производит один стандартный кубический метр водорода за один час, примерно в 7000 евро. Тем временем, однако, цены упали до 4500–5500 евро, говорит Том Смолинка, руководитель отдела химического хранения энергии Fraunhofer ISE и один из авторов исследования. Щелочные электролизеры, которые на момент исследования стоили от 3000 до 5500 евро, теперь считаются значительно дешевле в Китае.На момент проведения исследования практически не существовало готовых к продаже приложений для высокотемпературного электролиза.
По оценке Смолинки, производство мембранно-электродного блока — сердца электролизера из ПЭМ — составляет 60-70% от общей стоимости, в то время как чистые материальные затраты, включая дорогие драгоценные металлы, составляют всего 30-40. %. Кроме того, он добавляет, что силовая электроника, используемая в больших электролизерах, в настоящее время еще не является массовым продуктом, а скорее является единичным продуктом для конкретных клиентов. Соответственно, цены, вероятно, резко упадут, когда объемы продаж увеличатся. По словам Смолинки, до сих пор большинство электролизеров производилось в рамках рабочих процессов с небольшой автоматизацией или даже полностью вручную. «Высокоавтоматизированное производство, особенно для компонентов элементов, которое уже существует для топливных элементов с PEM, технически не будет проблемой». Однако он добавляет, что текущий низкий уровень рыночного спроса не позволяет производителям делать необходимые инвестиции.
Инвестиционные затраты
Ряд участников рынка работают над снижением инвестиционных затрат.Примером этого является совместное предприятие ITM Power и Linde, которое планирует открыть в этом году полуавтоматический завод в Шеффилде, Великобритания, для производства 1 ГВт мощности электролиза в год, в первую очередь для многомегаваттных проектов, таких как один в Кельне. Другие известные компании также заявили о крупных проектах и расширяют производство. Например, NEL в настоящее время готовится к реализации проекта мощностью 20 МВт в Дании, а Hydrogenics готовится к запуску небольшого проекта в Канаде. Наряду с размером проекта улучшается и производительность стека. В настоящее время обычно доступны стеллажи с входной электрической мощностью 400 кВт. Вскоре некоторые игроки захотят увеличить эту мощность до 1 МВт. Масштабирование размера должно снизить затраты.
Enapter использует другой подход. Итальянско-немецкая компания твердо привержена созданию небольшого стандартизованного продукта, который можно производить в еще больших количествах, а затем при необходимости устанавливать бок о бок. Основатель и генеральный директор Шмидт проводит параллели с компьютерным миром, чтобы проиллюстрировать правдоподобность концепции.Распределенные персональные компьютеры в значительной степени заменили мэйнфреймы, потому что большие объемы производства сделали их дешевле в производстве, чем небольшое количество мэйнфреймов. Аналогичным образом ожидается, что продукт Enapter снизит затраты по сравнению с большими центральными электролизерами, которые не производятся промышленным способом.
Это обсуждение о том, достигается ли цель быстрее за счет масштабирования до более крупных единиц в меньших количествах или путем масштабирования до большего количества более мелких единиц, распространено во многих отраслях. Скептики говорят, что последний подход не так перспективен для электролизеров по физическим причинам. В отличие от компьютеров, производительность электролизеров не увеличилась бы во много раз, если бы они были уменьшены в размерах. С другой стороны, с помощью электролиза AEM возможное устранение драгоценных металлов может сделать распределенную генерацию жизнеспособной для массового рынка.
При текущей цене 9 000 евро устройство подает пол кубометра водорода в час или один килограмм водорода каждые 24 часа.При целевом сроке службы 30 000 часов, агрегат в настоящее время достигает цены 6,70 евро / кг, что соответствует 0,17 евро / кВт · ч (теплотворная способность). Эти цифры, однако, не включают стоимость 54 кВт / ч электроэнергии, необходимой для производства 1 кг водорода с помощью электролиза AEM. Если мы предположим, например, что входящая электроэнергия стоит 0,05 евро / кВтч, это добавит еще 2,75 евро / кг, или 0,07 евро / кВтч водорода, к производственным затратам.
Как только автоматизированное производство на заводе в Пизе запустится, как и планировалось через четыре года, электролизер будет настолько дешевым, что запланированная цифра составит 1 евро. По словам Шмидта, будет получено 50 за килограмм без учета затрат на электроэнергию. На этом этапе разработчики надеются, что будет целесообразно не только использовать устройство для распределенной генерации, но и собрать более крупные агрегаты, как в компьютерном примере. Установка 416 блоков обеспечит выходную мощность 1 МВт.
Источник неопределенности
Срок службы устройств включен во все сметы затрат, которые, как и в случае любой новой технологии, нелегко доказать. Например, невозможно проверить, действительно ли электролизер AEM прослужит 30 000 часов, а электролизер PEM — от 60 000 до 80 000 часов, как заявляют производители.Тем не менее, Шмидт из Enapter и исследователи Тома Смолинки согласны с тем, что клетки AEM и PEM практически не стареют с течением времени. Кроме того, мало имеет значения, работает ли электролизер при полной нагрузке или только при половинной мощности.
В конечном счете, сама мембрана — не единственный фактор, определяющий срок службы. «Наибольшее влияние на срок службы оказывает качество воды», — говорит Смолинка. Загрязнения накапливаются в мелких порах мембраны, которые блокируют их или, в случае солей, образуют мостики.
Еще одним фактором, склеивающим электролизеры, является температура. Чрезмерные нагрузки приводят к повышению температуры всей системы, а электроды с неравномерным покрытием могут создавать горячие точки.
Areva h3Gen решит эту проблему в течение следующих трех лет. В исследовательском проекте Industriepark Höchst компания использует электролизер PEM мощностью 1 МВт. В дополнение к производству водорода он также будет обеспечивать первичную регулирующую мощность в будущем, а это означает, что иногда он будет работать с удвоенной мощностью, а в других случаях — только на части своей мощности 250 кВт.Если концепция окажется практически осуществимой, она не только откроет дополнительный доход операторам электролизных заводов, но также может помочь стабилизировать электросеть.
Согласно расчетам затрат, проведенным менеджером проекта Лукасом Буземейером, целевые затраты Enapter могут быть достигнуты уже сегодня с помощью централизованного подразделения Areva h3Gen. При непрерывной эксплуатации установки — 8000 рабочих часов в год в течение 20 лет — цена на водород в размере 3,60 евро / кг достижима при цене на электроэнергию 0 евро.05 / кВтч. Эта оценка предполагает, что стек PEM будет заменен один раз через 10 лет.
Значительное сокращение
Поскольку затраты на электроэнергию являются решающим фактором в общих затратах на генерацию, нельзя разделить технологию и ее использование. Любой, кто покупает зеленую электроэнергию из сети, будь то через PPA или в качестве сертифицированной зеленой электроэнергии, должен учитывать плату за подключение, сборы и надбавки к цене на электроэнергию, какими бы ни были правовые нормы. Однако электролизер можно подключать напрямую к существующей газовой или водородной сети, как в случае с Shell и Areva h3Gen в Хёхсте.
Операторы, которые производят водород с помощью небольших солнечных систем, могут использовать тепло и, таким образом, повысить экономическую эффективность, а также могут использовать топливо непосредственно для отопления или заправки автомобилей без необходимости его транспортировки. Такие производители также экономят часть сборов и надбавок на цене электроэнергии и снижают нагрузку на сеть.
В принципе, однако, инвесторы, которые планируют использовать только солнечную энергию для работы электролизера, должны будут согласиться с более длительным периодом окупаемости, поскольку энергия доступна только в течение небольшого количества часов полной нагрузки.
Значительного снижения потребления электроэнергии для электролиза можно достичь с помощью высокотемпературных устройств, которые имеют наивысший электрический КПД от 80% до 90%. Одним из пионеров этой технологии является Sunfire из Дрездена. Вместо 55 кВтч, как при электролизе PEM, для производства 1 килограмма водорода требуется всего 41,4 кВтч электроэнергии. Однако для этого электролизер необходимо нагреть. Поэтому рекомендуется устанавливать их там, где образуются промышленные отходы тепла, например, на сталелитейных заводах.Если производство стали не требует выбросов CO2, идеально подойдет соединение секторов, потому что произведенный водород может потребляться немедленно. С кислородной мембраной, которую использует Sunfire, можно не только расщепить воду для получения водорода, но и отделить любую молекулу, содержащую кислород, например углеводороды или даже углекислый газ, говорит Нильс Альдаг, главный операционный директор Sunfire. Полученный газ можно легко переработать в синтетическую сырую нефть, которую намного легче транспортировать, чем объемистый водород.
Вопрос о централизованном или распределенном электролизе, вероятно, в конечном итоге будет не вопросом «или-или», а «обоими / и».Задача огромная. Один только НПЗ Shell Rheinland в Кельне, который, по данным компании, является крупнейшим нефтеперерабатывающим заводом в Германии, требует 180 000 метрических тонн водорода в год. Он по-прежнему производится в основном путем паровой конверсии природного газа, который производит большое количество вредного для климата CO2. С середины 2019 года компания строит электролизный завод мощностью 10 МВт на заводе в Весселинге. По заявлению Shell, там будет установлен крупнейший в мире завод, использующий технологию протонообменных мембран. И все же для того, чтобы только эта компания перешла на экологически чистый водород, потребуется около 140 таких станций.
Способ получения водорода и кислорода из воды
(57) Реферат:
Изобретение предназначено для энергетики и может быть использовано для получения дешевых и экономичных источников энергии. Получают в открытом космосе перегретый пар с температурой 500-550 o С. Перегретый пар пропускают через постоянное электрическое поле высокого напряжения (6000 В) для получения водорода и кислорода.Метод прост по аппаратной части, экономичен, пожаро- и взрывобезопасен, высокопроизводителен. 3 ил. Водород в сочетании с окислением кислорода занимает первое место по калорийности на 1 кг топлива среди всего горючего, используемого для изучения электричества и тепла. Но водород с высокой теплотворной способностью по-прежнему не используется для электричества и тепла и не может конкурировать с углеводородным топливом. Препятствием к использованию водородной энергии является его дорогостоящий метод, который экономически не оправдан.
— невозможность получения водорода в больших количествах;
— энергоемкость;
— сложность устройства и использование дорогих материалов;
— невозможность проведения способа при использовании технической воды, так как при температуре насыщенного пара на стенках устройства и на катализаторе будут образовываться отложения и накипь, что приведет к быстрому выходу из строя;
— для сбора образующегося водорода и кислорода используются специальные бригады мощностей, благодаря которым они являются легковоспламеняющимися и взрывоопасными.
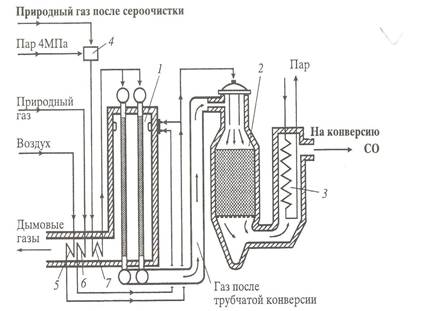

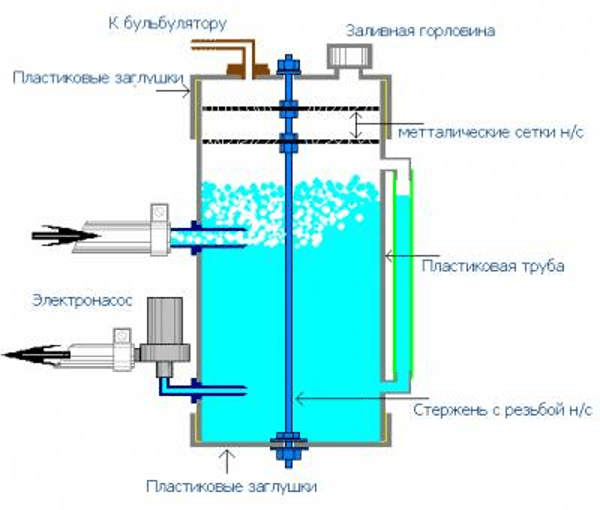

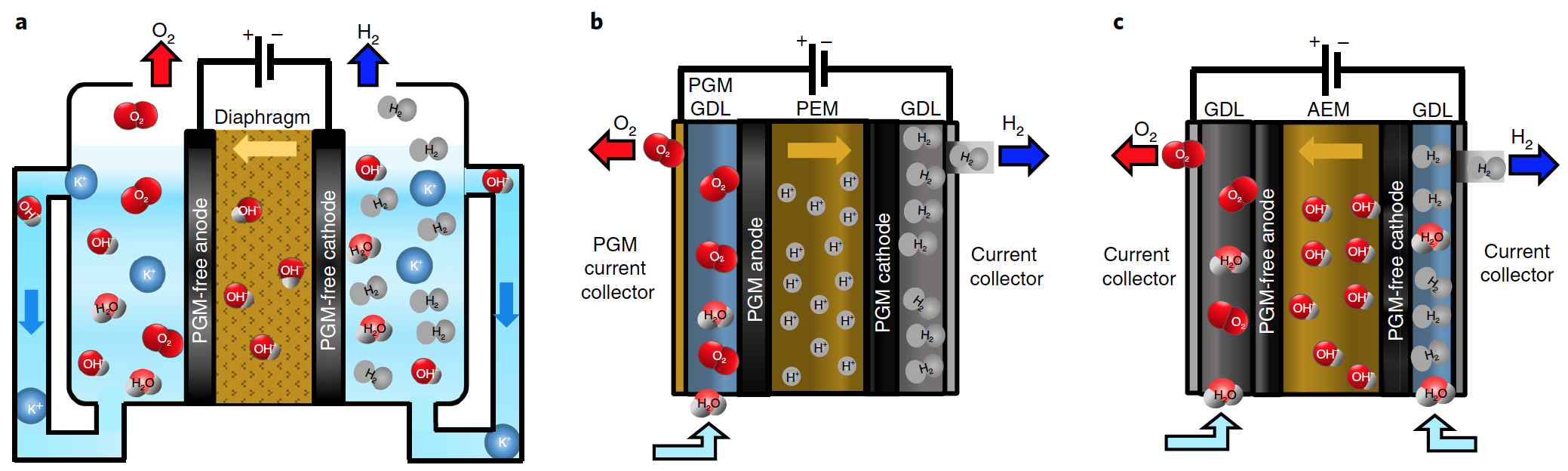

2H 2 + O 2 = 2H 2 O + тепло
В результате окисления газов рекуперируются вода и тепло. Это тепло в установке собирают котлы № 1 и № 2, преобразовывая это тепло в рабочий пар высокого давления. А восстановленная вода с высокой температурой поступает в следующий теплообменник, в следующую камеру разложения. Эта последовательность перехода воды из одного состояния в другое продолжается столько раз, сколько вы хотите получить от этой собранной тепловой энергии в виде рабочей пары продуктов, придаст контур расчетной энергии и оставит последнюю. В контуре котла 2 перегретый пар по патрубку направляется в коммутатор, пара смонтирована на пускателе.Пара переключателя положения «пуск» переводится в положение «работа», после чего он попадает в стартер. Отключен стартер / подогрев воды /. Из стартера перегретый пар поступает в первый теплообменник и оттуда в камеру разложения.
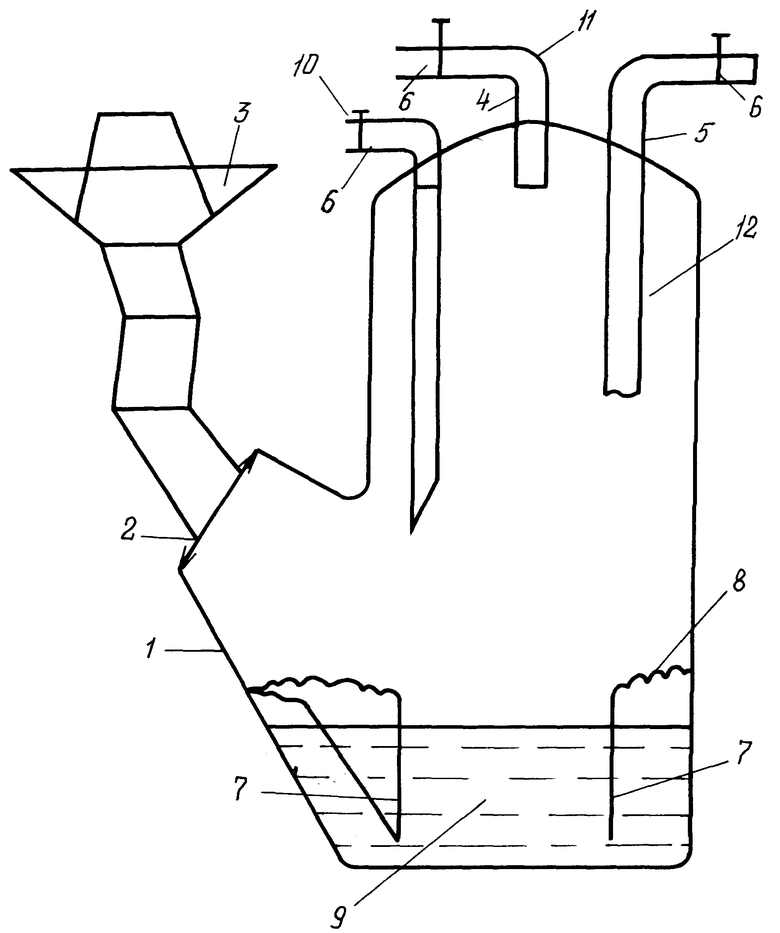

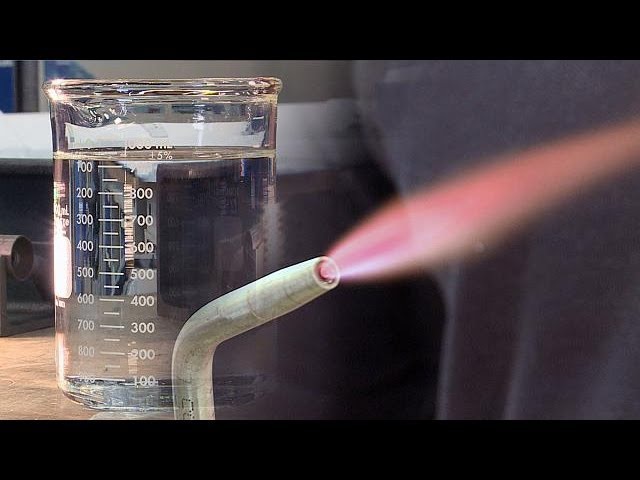
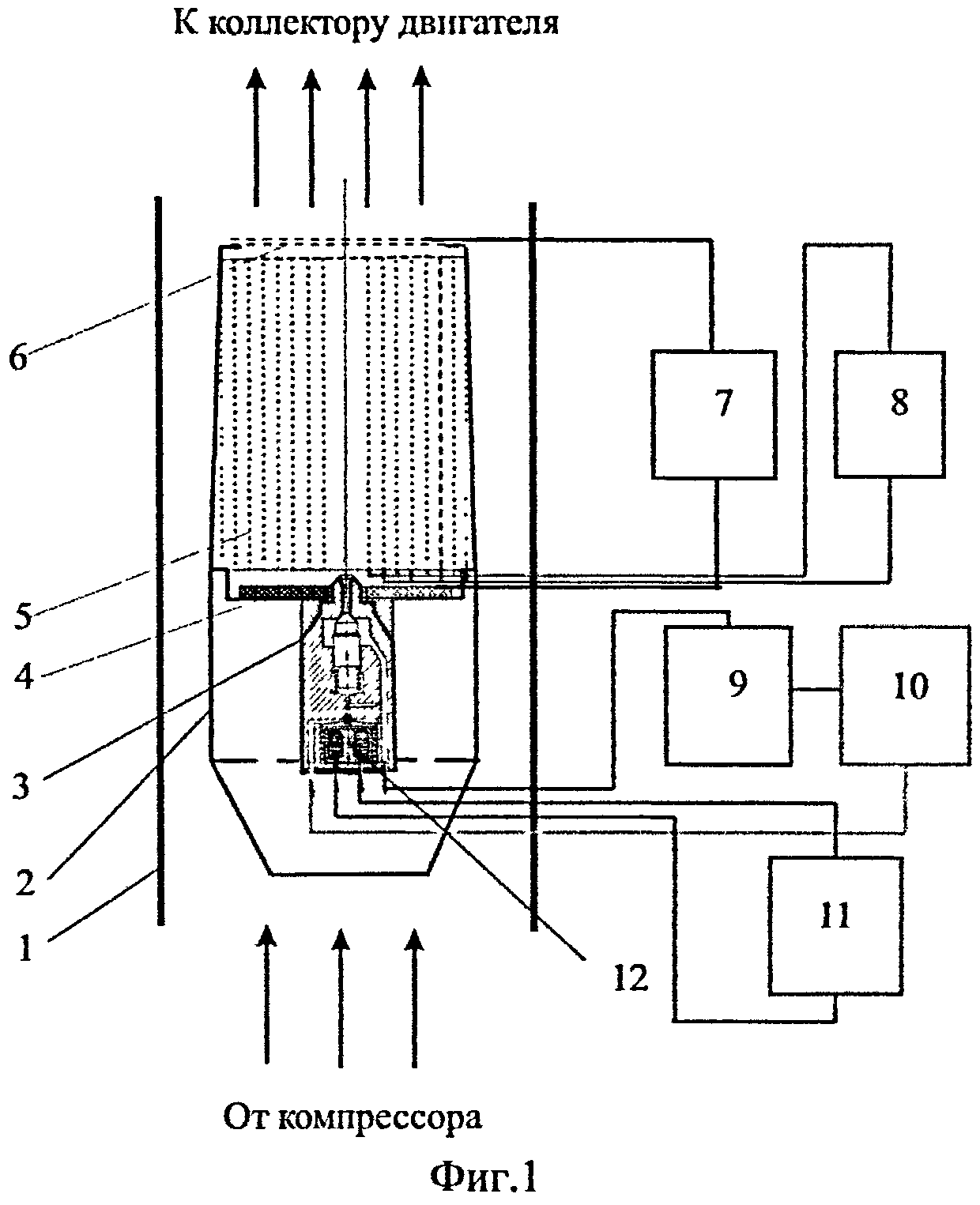