- труба Henco металлопластиковая Бельгия
- Топ 5 термостойких пластиков | Быстрый радиус
- Top 5 Термостойкие пластмассы – Чтение Обработка и производство пластмасс
труба Henco металлопластиковая Бельгия
Страна производитель: Бельгия
Металлопластиковые трубы HENCO соединяют в себе лучшие качества металлических и пластиковых труб и в то же время лишены большинства их недостатков. Уникальные свойства этих труб открывают широчайшие возможности для их применения в самых различных областях техники: в строительстве, кораблестроении, машиностроении, на железнодорожном транспорте и т.д.
Металлопластиковые трубы HENCO предназначены для создания систем центрального и индивидуального отопления и водоснабжения в жилых, общественных, административных и промышленных зданиях. Благодаря исключительной пластичности и техническим параметрам они незаменимы при проведении ремонта и реконструкции. Эти трубы применяют в системах как горячего и холодного водоснабжения, так и центрального кондиционирования, в технологических трубопроводах и системах водоподготовки, а также для подогрева открытых площадок и лестничных сходов, стадионов, бассейнов, грунта в теплицах и оранжереях.
Фирма HENCO имеет достаточно короткую историю, но история делается людьми и по этой причине будет несправедливо не сказать о тех, кто творит эту историю. Владельцем и руководителем завода HENCO является господин Луи Хендрикс. В 1965 году Луи Хендрикс основал фирму по производству газовых плит, а немного позднее, в 1968 году он открыл фирму DURA, занимающуюся производством стальных трубчатых радиаторов. В то время были достигнуты максимальные показатели производства: 44000 штук радиаторов в день. В 1976 году – было открыто новое направление: производство радиаторов HENRAD. Насколько это крупное производство можно судить по тому факту, что завод HENRAD перерабатывал 350 тонн стали в день. Уровень годового производства радиаторов достигал 2 миллиона штук. Сердечное недомогание, а также крайне выгодное предложение одной Британской группы компаний заставляют владельца продать в 1988 году эту фирму. В 1992-1993 годах Луи Хендрикс открывает фирму HENCO по производству ныне всемирно известной многослойной металлопластиковой трубы. В 1995 году производство начинает выпускать металлопластиковую трубу. Сбытом руководит коллега Луи Хендрикса – Вим Верховен. В апреле 1997 года к работе на фирме подключаются оба сына Луи Хендрикса чтобы обеспечить дальнейшую стабильную работу фирмы HENCO. В 1998 объем продаж HENCO составил 1 миллиард бельгийских франков. Инвестиционный проект выглядел следующем образом: 1988 год – пуск в эксплуатацию третьей производственной линии 1999-2001 год – пуск в эксплуатацию еще трех производственных линий. Производством трубы спектр деятельности фирмы HENCO не ограничивается. В области фитингов, фирма HENCO предлагает универсальную систему, способную обеспечить любые мыслимые соединения. Все фитинги и трубы прошли испытания в лабораториях Штуттгартского университета (Германия) на предмет соответствия стандартам ДИН. Продукция HENCO также удостоена следующими сертификатами: DVGW (Германия), KIWA (Нидерланды), WRC (Великобритания), SCTB (Бельгия), а также сертификатами других стран. Бесспорно, ключом к успеху фирмы HENCO послужил предпринимательский талант господина Луи Хендрикса и его неиссякаемый энтузиазм, умноженный на желание во всем процессе сначала разобраться самому, а потом научить других
Предлагаемая фирмой HENCO производственная концепция позволяет решить все проблемы монтажа систем отопления и сантехники. Металлопластиковые трубы HENCO просты в монтаже (при этом используется один стандартный тип фитингов), легко гнутся и сохраняют изогнутую форму. Металлопластиковые трубы дают возможность обходиться без ремонта систем не менее 50 лет. Эти трубы абсолютно не подвержены коррозии, химическим и электрохимическим воздействиям, не засоряются, в них не образуются отравляющие воду оксиды, как в медных трубах, или ржавая грязь, как в стальных (даже из нержавеющей стали). Их гидравлическое сопротивление значительно ниже, чем у труб иных видов, из-за низкой шероховатости. Металлопластиковые трубопроводы не издают и не проводят шум, электробезопасны. Для их прокладки не нужны сварочные аппараты, трубогибы, сгоны, муфты, уголки и т.д. Вы не увидите их торчащими из стен, их никогда не придется менять, красить и т.д.
И что особенно важно — они остаются безупречны с точки зрения гигиены вне зависимости от срока службы.
Металлопластиковая труба представляет собой пятислойную конструкцию из трех основных и двух связующих слоев. Внутренний слой трубы произведен из сшитого полиэтилена (РЕ-Хс) методом экструзии гранулированного полиэтилена высокой прочности (HDPE). Максимальная рабочая температура для данного материала 95°С, кратковременная температурная нагрузка до 110°С. У полиэтиленов средней (MD) и низкой (LD) прочности максимальная рабочая температура ниже 70°С.
Топ 5 термостойких пластиков | Быстрый радиус
Производители, как правило, используют такие металлы, как никель и нержавеющая сталь, для высокопроизводительных приложений, поскольку они обладают высокой термостойкостью. Сплавы на основе никеля, например, сохраняют свою прочность в условиях высоких температур, циклического термического воздействия и высокого уровня углерода. Несмотря на то, что металл имеет тенденцию быть более термостойким, чем пластик, во многих случаях инженерам было бы выгодно использовать термостойкие пластики вместо этого для своих высокопроизводительных приложений.
Термостойкие пластики делятся на две большие категории — термореактивные и термопласты. Термореактивные пластмассы — это пластмассы, которые затвердевают под воздействием тепла и не могут быть изменены после отверждения. Термопласты с высокими эксплуатационными характеристиками — это пластмассы, которые при нагревании плавятся, при охлаждении затвердевают и могут быть переплавлены после охлаждения. На структурную целостность термопластов влияют такие факторы, как температура стеклования (Tg) и температура плавления, присущая каждому материалу. Существуют варианты высокоэффективных термопластов, которые сохраняют свои структурные свойства при температурах выше 150°C и кратковременно при температурах выше 250°C.
Помимо термостойкости, эти материалы обладают химической стойкостью, коррозионной стойкостью и превосходными электрическими и тепловыми изоляторами. Общие высокопроизводительные применения включают поршневые компоненты в автомобильной промышленности, кабельные каналы в аэрокосмической промышленности, подводные соединители в полупроводниковой промышленности и многое другое. При разработке деталей, которые будут контактировать с чрезвычайно высокими температурами, командам разработчиков следует рассмотреть возможность производства с использованием этих пяти лучших термостойких пластиков.
Топ-5 термостойких пластиков
Термопласты обладают термостойкостью благодаря своей молекулярной структуре. Когда к смоле добавляются жесткие ароматические кольца вместо алифатических групп, основная цепь молекулярной цепи ограничивается и укрепляется таким образом, что для разрыва цепи необходимо разорвать два химических звена. С этой новой структурой химическая и термостойкость термопласта может быть такой же или лучше, чем у термореактивного материала.
Вот пять пластиков, которые могут выдерживать высокую температуру.
1. Полиэфиримид (ПЭИ)
ULTEM®, торговая марка полиэфиримида (PEI), является одним из немногих коммерчески доступных аморфных термопластов на современном рынке. Он прочный, химически стойкий и огнестойкий и уже более 35 лет является основным продуктом в обрабатывающей промышленности.
Этот материал имеет чрезвычайно высокую температуру плавления 219°C и максимальную температуру непрерывной эксплуатации 170°C, что делает его идеальным для изготовления печатных плат, оборудования для стерилизации пищевых продуктов и особенно деталей самолетов. ULTEM — одна из немногих смол для использования в коммерческой аэрокосмической промышленности — она превосходит другие термопласты по сопротивлению ползучести и хорошо выдерживает воздействие различных видов топлива и охлаждающих жидкостей. Однако он имеет тенденцию к растрескиванию в присутствии полярных хлорированных растворителей. Этот материал можно найти в противопожарных материалах и чехлах для сидений самолетов.
Пример детали, изготовленной с помощью ULTEM, которая несовместима с настольными принтерами. ULTEM довольно дорог, как и многие другие пластмассы в этом списке. Кроме того, он имеет более низкую ударную вязкость и температуру использования, чем PEEK.
Преимущества ULTEM:
- Лучшее сопротивление ползучести, чем у термопластов
- Выдерживает воздействие топлива и охлаждающих жидкостей
Недостатки ULTEM:
- Склонен к растрескиванию в присутствии полярных хлорированных растворителей
- Довольно дорого
2. Полиэфиркетон (PEEK)
PEEK, сокращение от полиэфирэфиркетон, представляет собой полукристаллический высокоэффективный конструкционный термопластик, устойчивый к химическим веществам, износу, усталости, ползучести и нагреву. Этот материал настолько прочен и адаптируется к суровым условиям, что производители используют его в качестве замены металла во многих приложениях, независимо от температуры. PEEK может выдерживать кратковременные температуры до 310°C и имеет температуру плавления более 371°C. Более того, он обладает самой высокой прочностью на растяжение и изгиб среди всех высокоэффективных полимеров.
Благодаря своей металлической прочности PEEK широко используется для различных медицинских устройств, активных компонентов автомобильных трансмиссий и внешних деталей самолетов. Его дополнительное преимущество заключается в том, что его легко обрабатывать с помощью литья под давлением или экструзии, а твердый PEEK совместим с обработкой на станках с ЧПУ.
У этого популярного термопластика есть несколько небольших недостатков, в том числе его восприимчивость к ультрафиолетовому излучению и некоторым кислотам. Тем не менее, PEEK по-прежнему является очень универсальным термопластом, который должен быть в арсенале всех инженеров.
Преимущества PEEK:
- Прочный и адаптируемый к суровым условиям окружающей среды
- Высочайшая прочность на растяжение и изгиб
- Легкие возможности литья под давлением
- Совместимость с ЧПУ
Недостатки PEEK:
- Восприимчивость к ультрафиолетовому излучению и некоторым кислотам
3.
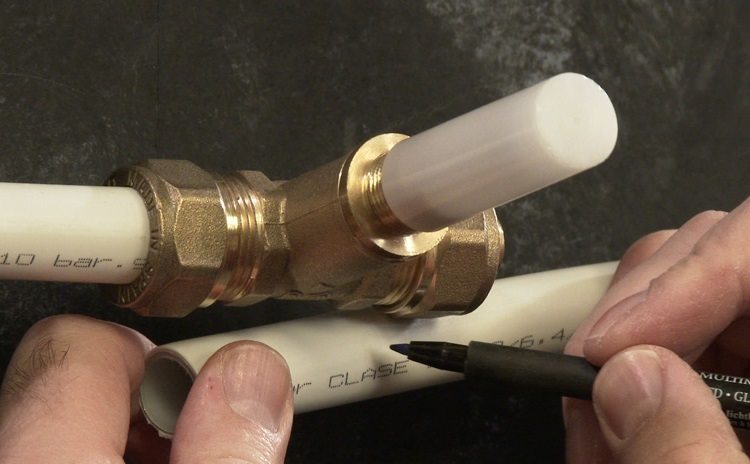
ПТФЭ, широко известный как тефлон, представляет собой мягкий, термостойкий пластик с низким коэффициентом трения и исключительной химической стойкостью. Он обладает высокой прочностью на изгиб, адекватной устойчивостью к атмосферным воздействиям и хорошими электроизоляционными свойствами как в жарких, так и во влажных условиях.
PTFE уникален тем, что он почти полностью химически инертен и плохо растворяется в большинстве растворителей, что делает его идеальным для применения при высоких температурах. ПТФЭ имеет одну из самых высоких температур плавления среди всех термопластов (327°C) и очень широкий диапазон рабочих температур. Он достаточно термически стабилен, чтобы его можно было использовать при температуре от -200°C до +260°C.
ПТФЭ широко известен благодаря своему коммерческому применению. Он также используется для защиты труб от коррозионно-активных материалов, покрытия теплообменников и изоляции электрических компонентов.
ПТФЭ превосходен при экстремально высоких и низких температурах, но его механические свойства обычно уступают сопоставимым пластикам при комнатной температуре. Он чувствителен к ползучести, истиранию и излучению, а его пары могут быть токсичными. Кроме того, стоит отметить, что обработка ПТФЭ довольно дорога.
Преимущества ПТФЭ:
- Высокая прочность на изгиб
- Достаточная устойчивость к атмосферным воздействиям
- Хорошая электроизоляционная способность как в жарких, так и во влажных средах
Недостатки ПТФЭ:
- Уступает сопоставимым пластикам при комнатной температуре
- Чувствителен к ползучести, истиранию и излучению
- Fes может быть токсичным
- Довольно дорого перерабатывать
4. Полибензимидазол (ПБИ)
Полибензимидазол (PBI) обладает самой высокой термостойкостью и износостойкостью, прочностью и стабильностью механических свойств среди всех конструкционных термопластов, представленных сегодня на рынке. Волокна PBI не имеют известной температуры плавления, не горят и не прилипают к другим пластикам. Этот материал имеет максимальную температуру непрерывной эксплуатации 398°C в инертной среде, 343°C на воздухе и возможность кратковременного воздействия до 537°C.
При всех своих достоинствах PBI невероятно дорог и сложен в производстве. Инженерам часто приходится использовать алмазные инструменты для обработки этого материала, что еще больше увеличивает затраты. С точки зрения дизайна, одним из основных недостатков PBI является его чувствительность к вырезу. Разработчики продукта должны быть осторожны, чтобы избежать любых острых краев или углов и сгладить все поверхности.
Преимущества PBI:
- Высокая стабильность
- Чрезвычайная термостойкость – самая высокая из всех термопластов, представленных сегодня на рынке
- Волокна не имеют точки плавления – они не горят и не прилипают к другим пластикам
Недостатки PBI:
- Дорогой и сложный в производстве
- Высокая чувствительность надреза
5.
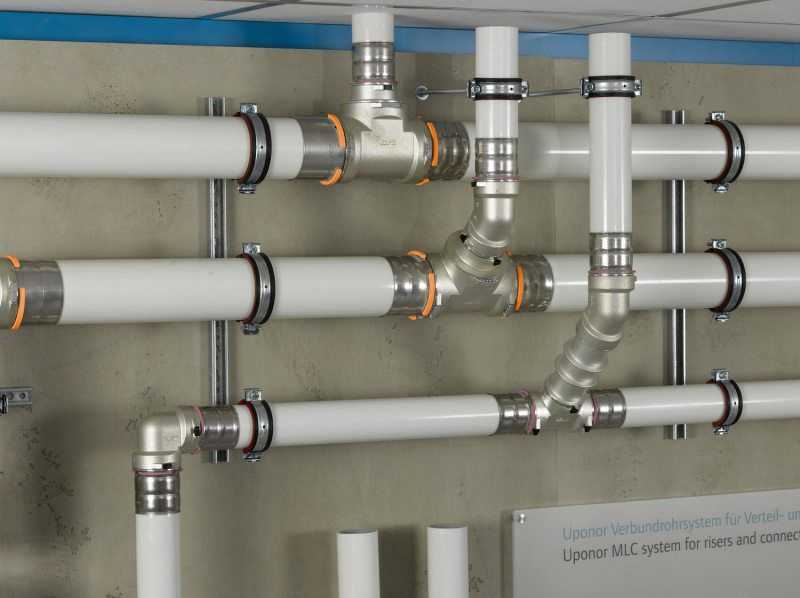
(pDCPD) представляет собой специально разработанный термореактивный полимер, разработанный для обеспечения превосходного сочетания химической, коррозионной и термостойкости, а также жесткости и ударной прочности. Этот материал сочетает в себе пластичность термореактивных материалов при формовании с высокими эксплуатационными характеристиками лучших инженерных термопластов. Он имеет температуру теплового изгиба до 120°C.
pDCPD уникален тем, что практически не имеет ограничений по размеру или весу деталей — детали с переменной толщиной стенок, формованными ребрами жесткости и т. д. не замедляют производство. pDCPD является относительно новым материалом, и его применение пока ограничено, но он показал себя многообещающим в коррозионно-стойком химическом технологическом оборудовании, септических резервуарах и оборудовании для очистки воды.
Преимущества pDCPD:
- Сочетает в себе химическую, коррозионную и термостойкость
- Отсутствие ограничений по размеру или весу детали – не замедляет производство
- Гибкость формования сочетается с высокой производительностью
Недостатки pDCPD:
- Новый материал: применение ограничено
Могут ли производители улучшить термостойкость?
Инженеры и производители могут нагревать и улучшать характеристики большинства видов пластмасс с помощью добавок и/или термостабилизаторов. Тремя наиболее распространенными типами добавок являются антиоксиданты, антипирены и технологические добавки. Каждая добавка обеспечивает различные характеристики и способствует долговечности полимера.
защищают полимер от теплового повреждения во время производства или во время нормального использования готовой детали, и сегодня они добавляются в большинство полимеров. Термостабилизаторы также могут сохранить внешний вид, прочность и эластичность полимера.
Выберите опытного производителя, который поможет с выбором материала
Для высокотемпературных применений любой из этих высокоэффективных пластиков действительно может выдерживать тепло. Однако подойдет не любой материал. Инженеры должны провести исследование, чтобы убедиться, что они выбирают термостойкий пластик, который лучше всего подходит для их конкретного применения. Если инженеры выбирают неправильный материал, они рискуют поставить под угрозу функциональность своей детали, и им придется начинать с нуля.
Опытный партнер-производитель, такой как Fast Radius, может упростить процесс выбора материала благодаря нашим экспертным инженерно-консультационным услугам. Мы можем помочь любой группе разработчиков выбрать правильный материал для своей детали и уникальных требований.
Помимо выбора материалов, наша команда опытных инженеров и дизайнеров готова оптимизировать процесс разработки продукции и поставлять детали высочайшего качества по доступным ценам и в кратчайшие сроки, поэтому каждый клиент может быть уверен, что получает лучший продукт за лучшее. иметь дело. Свяжитесь с нами сегодня для цитаты.
Дополнительные руководства по материалам и информацию о производстве из пластмасс можно найти в ресурсном центре Fast Radius.
Готовы создавать детали с помощью Fast Radius?
Начать предложение
Top 5 Термостойкие пластмассы – Чтение Обработка и производство пластмасс
Для высокотемпературных применений вам нужны пластмассы, которые могут противостоять термическому разложению, сохраняя при этом достаточную прочность и жесткость при рабочей температуре. Введите термостойкие пластмассы , материалы, температура которых может превышать 300ºF при постоянной рабочей температуре без ухудшения их механических свойств. Выбор подходящего термостойкого пластика для работы часто включает в себя больше соображений, чем просто рабочая температура, таких как химическая стойкость материала, характеристики трения и износа, а также прочность на растяжение. Вот 5 самых эффективных термостойких пластиков для тяжелых условий эксплуатации:
- Тефлон® (ПТФЭ) – Тефлон® наиболее широко известен своими антипригарными свойствами, так как у него один из самых низких коэффициентов трения по отношению к любому твердому телу, известному человеку. Но он также имеет широкий диапазон рабочих температур с достаточной термической стабильностью, чтобы его можно было использовать в диапазоне от -328ºF до +500ºF без ухудшения характеристик. ПТФЭ также обладает высокой прочностью на изгиб, высоким электрическим сопротивлением и диэлектрической прочностью, а также является гидрофобным.
Одной из других уникальных особенностей Teflon® является то, что он почти полностью химически инертен и плохо растворяется в большинстве растворителей или химикатов. Это невероятное сочетание свойств делает его идеальным полимером для целого ряда высокотемпературных применений.
- Vespel® – этот термостойкий пластик может работать при температурах до 550ºF и даже может выдерживать температуры до 900ºF в течение ограниченного периода времени без изменения своих термических или механических свойств. Это делает Vespel® популярным выбором для таких применений, как реактивные двигатели, автомобили, грузовики и промышленное оборудование. Vespel® также обладает высокой устойчивостью к химической коррозии, высокой ударопрочностью и ударной вязкостью, а также низким коэффициентом трения и превосходными характеристиками износа. Этот легкий материал может быть легко обработан для получения сложной геометрии и жестких допусков, что позволяет создавать конструкции, которые были бы невозможны с меньшими материалами.
- Torlon® – Torlon® представляет собой полиамид-имид, обеспечивающий исключительную долговременную прочность и жесткость при постоянной температуре эксплуатации 500ºF. Это делает его эффективной альтернативой металлу для высокотемпературного трения и износа. Torlon® прочнее при 400ºF, чем другие инженерные смолы при комнатной температуре. Обладая выдающейся стойкостью к ползучести, износу и химическим веществам, включая сильные кислоты и большинство органических химикатов, Torlon® идеально подходит для тяжелых условий эксплуатации.
- PEEK – Обладая температурой плавления более 700ºF, постоянной рабочей температурой 500ºF и превосходной твердостью, PEEK может работать в условиях высоких нагрузок и температур без потери размерных свойств. PEEK также устойчив ко многим агрессивным химическим веществам и способен противостоять износу даже в жестких физических и химических условиях. Обладая самой высокой прочностью на растяжение и изгиб из всех высокоэффективных полимеров, PEEK идеально подходит для применений, требующих долговечности, подобной металлу.